The Development of the New XJ Jaguar in Advanced Aluminium; Opportunities and Challenges
Total Page:16
File Type:pdf, Size:1020Kb
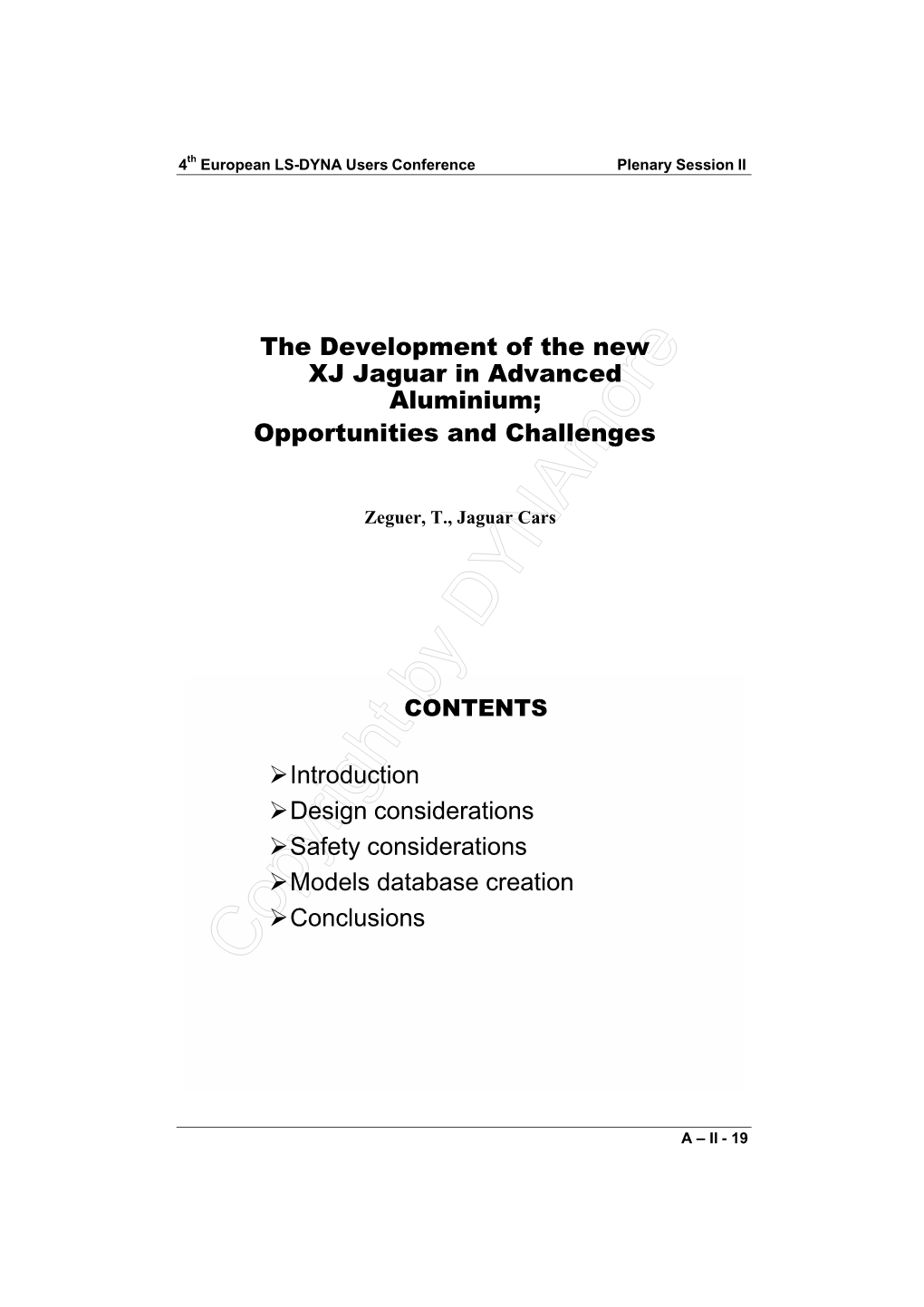
Load more
Recommended publications
-
Jaguar Xj6, Xj12, Xjs Jxj-19
JAGUAR XJ6, XJ12, XJS JXJ-19 UPGRADED VOLTAGE REGULATOR Unlike an original mechanical regulator, this is completely new, solid-state, electronic version encased in an original-style housing. It has load dump protection and adjustable voltage while retaining the original look and connections (NEG- POS-FLD). Voltage is factory-set at 14.2V. The LMAR23 keeps the battery at full charge by managing proper alternator output under changing loads and varying speeds. Maximum field current is increased from 3 to 5 amps to safely yield the most $139.99 from the alternator. XJ6 Series I w/ Butec Alternator C31526 MOSS CLASSIC JAGUAR A “bad old days” relic. Given to Al Moss by members of a local MG club, this license plate was Looking Ahead to the New Normal registered to Al’s MG YB. I used to love telling the story of how to assume or believe things would For the past year plus, we have in our pre computer days, customer materially change. As long as we do operated on a mix of reduced staffing service posted a number in the sales our jobs, the results will follow. and video conferences. The Moss room. That number was how many Then things changed. We all know team has gone all in on keeping things days until an order was likely to be what I mean. As this catalog goes to moving. I cannot say enough about processed. When things got busy, press, we are welcoming in a return the loyalty and dedication of our the number could grow to as high as to normal life. -
1 Fundamental Car Groups, 1981-2011
FUNDAMENTAL CAR GROUPS, 1981-2011 (Shared Body Platforms) 1. The first line of the definition assigns a five-digit number to the car group; the first two digits indicate the manufacturer, based on FARS codes (1=AMC, 6=Chrysler, 12=Ford, 18=GM, etc.); the last three digits are sequential and generally chronological for that manufacturer. 2. The second line assigns a name to the car group and gives the limits of the range of model years for the various make-models in the car group. Car groups are often named after the largest selling make-model with that body platform and/or the wheelbase of that platform (to the nearest inch). 3. The third line shows the wheelbase of the cars in that group, as derived from "New Car Specifications" in Automotive News or Ward’s Automotive Yearbook. 4. The remaining lines list the specific make-models included in the car group, including a five-digit make-model code, the make-model name (plus additional specifications such as "4-door" if not every car of that make-model is in that car group during the specified time period), a range of model years, and the VIN characters that identify specifically which cars belong to this car group (V3 is the 3rd character of the VIN, V34 is the 3rd and 4th character, etc.). American Motors Car Groups Car group 1008 AMC Gremlin/Spirit, 1981-1983 Wheelbase 96 1008 AMC Spirit 1981-1983 V6=4 V3=M Car group 1009 AMC Hornet/Concord, 1981-1983 Wheelbase 108 1007 AMC Concord, 1981-1983 V6=0 Car group 1011 AMC Eagle, 1981-1988 Wheelbase 109.3 1009 AMC Eagle, 1981-1988 V6=3 Car group 1012 AMC SX4, 1981-1983 Wheelbase 97.2 1010 AMC SX4/Kammback, 1981-1983 V6=5 1 Chrysler Corp. -
1976 Jaguar Xj-S Group 44
1976 JAGUAR XJ-S GROUP 44 D E T A I L S Year: 1976 Conguration: LHD Price: SOLD D E S C R I P T I O N 1976 American privateer Bob Tullius and his Group 44 organisation were loyal proponents of British Leyland, having already raced Austin Healeys, MGs and Triumphs before switching to a Jaguar E-Type in 1974. He convinced Jaguar to create a competition version of the company's new V12 engine, which he continued to use well into the 1980s, bringing Jaguar back to Le Mans in the process. Among the most successful Group 44 Jaguars was the XJ-S campaigned during the 1978 season. It had big shoes to ll as Tullius had won the 1977 Category 1 title of the Trans-Am championship from a Porsche 911. The sport's governing body were not too happy with two European cars dominating their championship and for 1978 the regulations were changed to suit the domestic Chevrolet Corvette. Jaguar did their part by supplying a brand new XJ-S body-shell, which had been acid dipped to make it as light as possible. Upon arrival in the Group 44 workshop, the shell was turned into a rolling chassis by Brian Fuerstenau and Lawton Foushee. Following the regulations, they equipped the car with stock suspension adapted to suit the massive Goodyear tyres that were tted on all four corners. Power came from the latest development of the DOHC Jaguar V12, which was run with carburettors as the fuel injection tted on the road cars was unsuitable for use on the track. -
Annual Report 2018/19 (PDF)
JAGUAR LAND ROVER AUTOMOTIVE PLC Annual Report 2018/19 STRATEGIC REPORT 1 Introduction THIS YEAR MARKED A SERIES OF HISTORIC MILESTONES FOR JAGUAR LAND ROVER: TEN YEARS OF TATA OWNERSHIP, DURING WHICH WE HAVE ACHIEVED RECORD GROWTH AND REALISED THE POTENTIAL RATAN TATA SAW IN OUR TWO ICONIC BRANDS; FIFTY YEARS OF THE EXTRAORDINARY JAGUAR XJ, BOASTING A LUXURY SALOON BLOODLINE UNLIKE ANY OTHER; AND SEVENTY YEARS SINCE THE FIRST LAND ROVER MOBILISED COMMUNITIES AROUND THE WORLD. TODAY, WE ARE TRANSFORMING FOR TOMORROW. OUR VISION IS A WORLD OF SUSTAINABLE, SMART MOBILITY: DESTINATION ZERO. WE ARE DRIVING TOWARDS A FUTURE OF ZERO EMISSIONS, ZERO ACCIDENTS AND ZERO CONGESTION – EVEN ZERO WASTE. WE SEEK CONSCIOUS REDUCTIONS, EMBRACING THE CIRCULAR ECONOMY AND GIVING BACK TO SOCIETY. TECHNOLOGIES ARE CHANGING BUT THE CORE INGREDIENTS OF JAGUAR LAND ROVER REMAIN THE SAME: RESPONSIBLE BUSINESS PRACTICES, CUTTING-EDGE INNOVATION AND OUTSTANDING PRODUCTS THAT OFFER OUR CUSTOMERS A COMPELLING COMBINATION OF THE BEST BRITISH DESIGN AND ENGINEERING INTEGRITY. CUSTOMERS ARE AT THE HEART OF EVERYTHING WE DO. WHETHER GOING ABOVE AND BEYOND WITH LAND ROVER, OR BEING FEARLESSLY CREATIVE WITH JAGUAR, WE WILL ALWAYS DELIVER EXPERIENCES THAT PEOPLE LOVE, FOR LIFE. The Red Arrows over Solihull at Land Rover’s 70th anniversary celebration 2 JAGUAR LAND ROVER AUTOMOTIVE PLC ANNUAL REPORT 2018/19 STRATEGIC REPORT 3 Introduction CONTENTS FISCAL YEAR 2018/19 AT A GLANCE STRATEGIC REPORT FINANCIAL STATEMENTS 3 Introduction 98 Independent Auditor’s report to the members -
Jaguar Xe 2019
JAGUAR XE 2019 THE ART OF PERFORMANCE Every day we push performance to its limit. Our performance. Our cars' performance. We innovate, we engineer, we design. We master rules and then break them. Only to push further. Past the limits of convention. This is when performance becomes art. Jaguar. The Art of Performance. CONTENTS INTRODUCTION ASSISTANCE AND EFFICIENCY The Concept of the XE 07 Driver Assistance 46 The XE – The Facts 08 Efficient Technologies 49 DESIGN XE LANDMARK EDITION 50 Exterior Principles 10 Exterior Detail 12 PERSONALIZATION The XE – Your Choice 52 Interior 17 Choose your Engine 54 PERFORMANCE Choose your Model 56 Engines 18 Choose your Options 58 Advanced Aerodynamics 22 Choose your Color 64 Lightweight Aluminum Architecture 25 Choose your Wheels 66 Chassis and Suspension 26 Choose your Interior 68 Choose your Jaguar Gear – 84 DRIVING TECHNOLOGY Accessories Advanced Driving Dynamics 29 Added Driver Confidence 30 TECHNICAL DETAILS 86 Advanced Drivetrain Technology 33 SPECIAL VEHICLE OPERATIONS 92 Torque Vectoring 35 Stability and Control 36 THE WORLD OF JAGUAR 94 JAGUAR INCONTROL® TECHNOLOGIES AT YOUR SERVICE 97 Infotainment 39 Connectivity 40 Audio 44 VEHICLE SHOWN: JAGUAR XE R-SPORT IN CAESIUM BLUE WITH OPTIONAL EQUIPMENT VEHICLES SHOWN ARE FROM THE JAGUAR GLOBAL RANGE. SPECIFICATIONS, OPTIONS AND AVAILABILITY MAY VARY BETWEEN MARKETS AND SHOULD BE VERIFIED WITH YOUR LOCAL JAGUAR RETAILER. INTRODUCTION THE CONCEPT OF THE XE The Jaguar XE is the foundation of the Jaguar sedan car family. A distillation of the design, luxury and technology found in the Jaguar XF and the Jaguar XJ. Inspired by the Jaguar F-TYPE sports car, with its assertive looks and agile drive. -
2013 Jaguar XJ Brochure
> Build Your Jaguar > Keep me informed Twitter Facebook 2013 JAGUAR XJ JAGUAR 2013 Information Provided by: > Build Your Jaguar > Keep me informed Twitter Facebook EXTRAORDINARY LUXURY The XJ is passion in motion, a dramatic combination of beauty, luxury and sheer exhilarating power. Outside, the sweep of its streamlined roof is fashioned to slice through air. Inside, its sensuous cabin is crafted to pamper, built for supremely comfortable driving or for a passenger to stretch out and relax. With its strong lightweight aluminum body, the XJ provides agility and superlative handling. This, combined with its anticipatory technology, allows the XJ to react to road conditions and other cars alike. The XJ drive is truly unique. XJ | PORTFOLIO | SUPERCHARGED | SUPERSPORT | ULTIMATE Information Provided by: VEHICLE SHOWN: XJL PORTFOLIO IN RHODIUM SILVER > Build Your Jaguar > Keep me informed Twitter Facebook Information Provided by: > Build Your Jaguar > Keep me informed Twitter Facebook XJ, ARRIVE IN STYLE The XJ turns heads and attracts glances. Its fusion of honed dynamic lines and sculpted elegance is designed to fulfil the core Jaguar values of beauty, purity, simplicity and consistency. The objective was never ‘merely’ to create the world’s most beautiful sporting sedan but to produce a more efficient shape where the pinnacles of aesthetics and aerodynamics work together in complete accord. You haven’t just got there in the XJ. You’ve arrived. Information Provided by: VEHICLE SHOWN: XJL PORTFOLIO IN RHODIUM SILVER 4 > Build Your Jaguar > Keep me informed Twitter Facebook Information Provided by: > Build Your Jaguar > Keep me informed Twitter Facebook DESIGN ON THE MOVE You can see and touch the opulent good looks of the XJ. -
Xf Xk 2012 Range Xj
XJ XF XK 2012 RANGE XJ XF XK J aguar raN g E Cars like no other, Jaguar combines high performance with beauty, athletic grace and finesse: the world’s most strikingly modern sports cars and sedans. Today, more than ever, Jaguar vehicles express the ultimate in state-of-the-art design, performance and technology with the sporting heritage that is their heart and soul. From the XJ flagship sedan, to the XF luxury sport sedan, the XK coupe and convertible and the heart-stopping XKR-S - the fastest ever Jaguar production sports car - every Jaguar makes a unique statement of luxury, performance and individuality. XJ 04 XF 18 XK 32 XJ Stunning design, contemporary luxurious materials and the use of intuitive technology make the XJ an outstanding full-size sedan that delivers true driving pleasure. In fact, the aesthetic beauty of the streamlined body of the XJ was a prime consideration in its creation. Its lightweight aluminum architecture utilizes techniques and alloys directly from the aerospace industry, making the XJ uncommonly light and agile, yet strong and powerful. With standard features like the panoramic glass roof, the XJ redefines how luxury sports sedans should look. Available in six models with three superb engines, to experience the XJ is to feel pure excitement. XJL Supersport in Rhodium Silver with 20D Mataiva wheels XJ PERFORMANCE MAIN FEATURES WHEELS 5.0L V8 385 HP JaguarSenseTM lighting and glovebox controls Standard 0-60 mPH SECONDS – 5.4 Virtual Instruments CITY (mPg) – 16* Color HD Touch-screen HIgHWaY (mPg) – 23* Interactive -
Download the Multimac Fitting Guide
Fitting Type SUPERCLUB SUPERCLUB Vehicle 1320 1260 1200 1000 930 A B C 1200 1100 Alfa Romeo 147 Alfa Romeo 156 Alfa Romeo 159 Alfa Romeo 166 Alfa Romeo Brera Alfa Romeo GT Alfa Romeo Guilietta Alfa Romeo Mito Aston Martin DB 5/6 Audi A1 [3 door] Audi A1 [5door] Audi A2 Audi A3 (5 door) Audi A3 (3 door) Audi A3 cabriolet Audi A4 saloon/Avant/Allroad Audi A4 Cabriolet Audi A5 3door Audi A5 5door Audi A5 Cabriolet Audi A6 saloon/Avant/Allroad Audi A7 Audi A8 Audi Q3 Audi Q5 Audi Q7 middle Audi Q7 Rear Audi TT not Cabrio Bently Flying Spur Bently GTC Bently Mulsanne BMW 1 series BMW 1 series cabriolet BMW 2 series BMW 2 series Active T third row BMW 2 series Active Tourer BMW 2 series cabriolet BMW 3 series BMW 3 series Cabriolet BMW 4 series BMW 4 series Cabriolet BMW 5 series BMW 5series GT BMW 6 series 2 door BMW 6 series cabrio BMW 7 series BMW i3 BMW X1 BMW X3 BMW X5 5seat BMW X5 7seat middle BMW X5 7seat rear BMW X6 bench seat Chevrolet Aveo Chevrolet Captiva middle row Chevrolet Captiva third row Chevrolet Cruze Chevrolet Kalos Chevrolet Lacetti Chevrolet Matiz Chevrolet Orlando middle row Chevrolet Orlando third row Chevrolet Spark Chevrolet Tacuma Chrysler 300C Chrysler Grand Voyager middle Chrysler Grand Voyager rear Chrysler neon Chrysler PT cruiser Chrysler voyager middle row Chrysler Voyager rear row Citroen -
6 June 2018 Dear Sir/Madam Freedom Of
Information Governance Coventry City Council PO Box 15 Council House Coventry CV1 5RR www.coventry.gov.uk Please contact Information Governance Direct line 024 7683 3323 [email protected] 6 June 2018 Dear Sir/Madam Freedom of Information Act 2000 (FOIA) Request ID: REQ04312 Thank you for your request for information relating to Mayoral cars in 2015/16, 2016/17 and 2017/18. How many cars your organisation has. Please also specify the make and model. 2 cars listed on the attached document. The cost of purchasing a car(s) during 2015/16, 2016/17 and 2017/18. Nil, as the vehicles are leased The cost of leasing a car(s) during 2015/16, 2016/17 and 2017/18. Please see the attached document. The cost of fuel for a car(s) during 2015/16, 2016/17 and 2017/18. Please see the attached document. The cost of purchasing a personalised number plate(s) during 2015/16, 2016/17 and 2017/18. Nil. The costs associated with maintaining a car(s) during 2015/16, 2016/17 and 2017/18. This includes, but is not limited to, MOT, general service, insurance, and new tyres and parts. Both cars are leased, so tyres, service and maintenance are included in the leasing contract. Insurance for 1COV is included in the leasing contract. Insurance for K1COV is part of the City Council’s insurance Scheme. Costs of fuel are included in the attached. If your authority has a lord mayor, chairman/woman or vice-chairman/woman, please also include this as part of your response. -
Next Generation of Jaguar Today’S Agenda
NEXT GENERATION OF JAGUAR TODAY’S AGENDA • JAGUAR LAND ROVER • THE JAGUAR BRAND • NEXT GENERATION OF JAGUAR JAGUAR LAND ROVER GLOBAL 462,678 SALES 425,006 375,773 Global sales have more than doubled in 5 years 274,280 232,839 196,226 381,108 UNITS SOLD +9% FOR 2014 81,570 UNITS SOLD +6% FOR 2014 2009 2010 2011 2012 2013 2014 FY 2014/15 $35 billion in Revenue $4 billion in Profit before tax Q1 2015 $1 billion in Profit before tax $5 BILLION ANNUAL INVESTMENT IN PRODUCTS & FACILITIES UK Coming Soon • Solihull, Castle Bromwich, • Brazil Wolverhampton China • Slovak Republic (LOI) India • Austria NEXT GENERATION OF JAGUAR 2009 2014 XF F-TYPE XJ XF XJ Instinctive All Wheel Drive™ Engines XK 2016 F-TYPE with AWD, Man. Updated XJ ALL NEW XF SEDAN XE & F-PACE TRIPLE JAGUAR U.S. MARKET POTENTIAL REACH 1,200,000 877,000 380,000 2015 + XE + F-PACE 2016 / 2017 F-TYPE XJ XF XE F-PACE Instinctive All Wheel Drive™ Ingenium Engines Diesel Engines STARTING IN 16MY JAGUAR WILL COMPETE IN THE HEART OF THE LUXURY MARKET 1. XE & F-PACE to compete in ENTRY LUXURY segments 2. Competitive entry-priced models 3. Lowered MSRP or Increased standard equipment 17MY JAGUAR XE • New aluminum intensive architecture • Double wishbone front suspension with Integral Link rear • Available with all-wheel drive • Coupe-like profile with new Jaguar family cues • XE 25t - 2.0L turbocharged four- cylinder • XE 20d - 2.0L turbocharged diesel • XE 35t - 3.0L supercharged V6 17MY JAGUAR XE • Jaguar 25t $34,900 • Jaguar 20d $36,400 • Jaguar 35t $41,700 • From a MSRP competitive position: -
1990 Gas Mileage Guide: EPA Fuel Economy Estimates
Contents Pzgs Tse rds zse;. :c eete-ine :he c&v fuei economy estinaze simulates a 7.5 mile. stop-andgc :ria with at. avenge speed 3f 2C mph. The trip Pn:w o! the Guide .................................... :=ices 23 -i:::es an5 has :E stops. A&&: :E percen: of :he :.;me is i-. i-. ..,e:io: Volume ......................................... s.n+... ,"...c.:;?:- as it. wzi:ing t: :ra4ic ti@s or in rush hour traffic. Two 3ow :he Fce: Economy Es:Ima:es Are OStainel .............. ccs3, engize sSzs z:e used-the cold whick is simiiar>?c .-acors- affecting ME............................. ,.. I... : s:eZing t czr in :be rornizg af!er i: 3% beer. -,arked a!: niski-and :>e 52: s9?, $-i:tr := :es"+;-.c8.,..~ a vehicle a%er i: Pas beer: wamed "OW to 3se:he Guide. ............................. .- ;-;vc: 2-l s:c;pi fc: a she? $me. k?.ncalFueiCoss ................................ *;-. ".. 5s:ing of 'Jehicie 3afa ............................. - index ........................................... ke :es: :z dew-lr.e :>e hiflwey fuei economy es:ina:e represeri's a Sazple Eue; Economy 'LaSei ........................ -;.... x2:e C: "nc--civ" cr:.vins. Setpen's correspcnding :c ,iifferen: k%s cf rxz; w~?sand :::erstate highways are Inciuded. The :es: b s+..!...-. t:es a :2 -iie !:i; as:! averages 4.6 mpk. The :es: is run 50%a 50: staz and has vev ?tie idlir.~::me am? no Sops (exce~ta? ?he enl Purpose of the Guide c? !be test). The Gas Mileage Guide :s ?uS::shed by :he 2.S.3epaEr: :s:J ct Energy as an a:e !o consmen conszer:r.S :ne purchase )f new vehcie. -
ALL-NEW JAGUAR XJ PRODUCT COMPARISON GUIDE XJ Vs
ALL-NEW JAGUAR XJ PRODUCT COMPARISON GUIDE XJ vs. Lexus LS 460 2 3 JAGUAR XJ vs. LEXUS LS 460 SPECIFICATIONS (Jaguar advantages in bold.) ENGINE JAGUAR XJ SEDAN LEXUS LS 460 SEDAN Displacement 5.0 liter DOHC naturally 4.6 liter DOHC V8 and type aspirated V8 – XJ/XJL 5.0 liter DOHC Supercharged V8 – Supercharged 5.0 liter DOHC Supercharged V8 – Supersport JAGUAR XJ Horsepower 385 @ 6,500 – XJ/XJL 380 @ 6,400 – RWD 470 @ 6,000–6,500 – 357 @ 6,400 – AWD vs. LEXUS LS 460 Supercharged 510 @ 6,000–6,500 Supersport LEXUS LS 460 JAGUAR XJ TRIM LEVELS ADVANTAGE Torque, lb.-ft. 380 @ 3,500–6,500 – XJ/XJL 367 @ 4,100 – RWD 424 @ 2,500–5,500 – 344 @ 4,100 – AWD AND MSRP HIGHLIGHTS Supercharged • LS 460 RWD Sedan $66,255 • More standard and available power – 461 @ 2,500-5,500 – • LS 460 AWD Sedan $69,780 up to 130 horsepower more on Supersport • LS 460 L RWD Sedan $71,800 Supersport Camshaft drive Silent chain Silent chain • LS 460 L AWD Sedan $75,325 • Lower curb weights – over 300 pounds MSRP includes destination charge. on both wheelbases Cam phasing Dual independent variable Variable Valve Timing • Longer wheelbases for interior room cam timing with intelligence LEXUS LS 460 and Electronically • Standard XJ features not available on HIGHLIGHTS controlled intake Lexus LS 460: panoramic roof, Blind (VVT-iE) • Regular (460) and extended (460 L) Spot Monitor, Media Hub, rear wheelbase models available in rear- business trays (XJL) Valve lift Cam profile switching Cam profile switching or all-wheel drive • Standard XJ features optional on Lexus • Standard