US2221691.Pdf
Total Page:16
File Type:pdf, Size:1020Kb
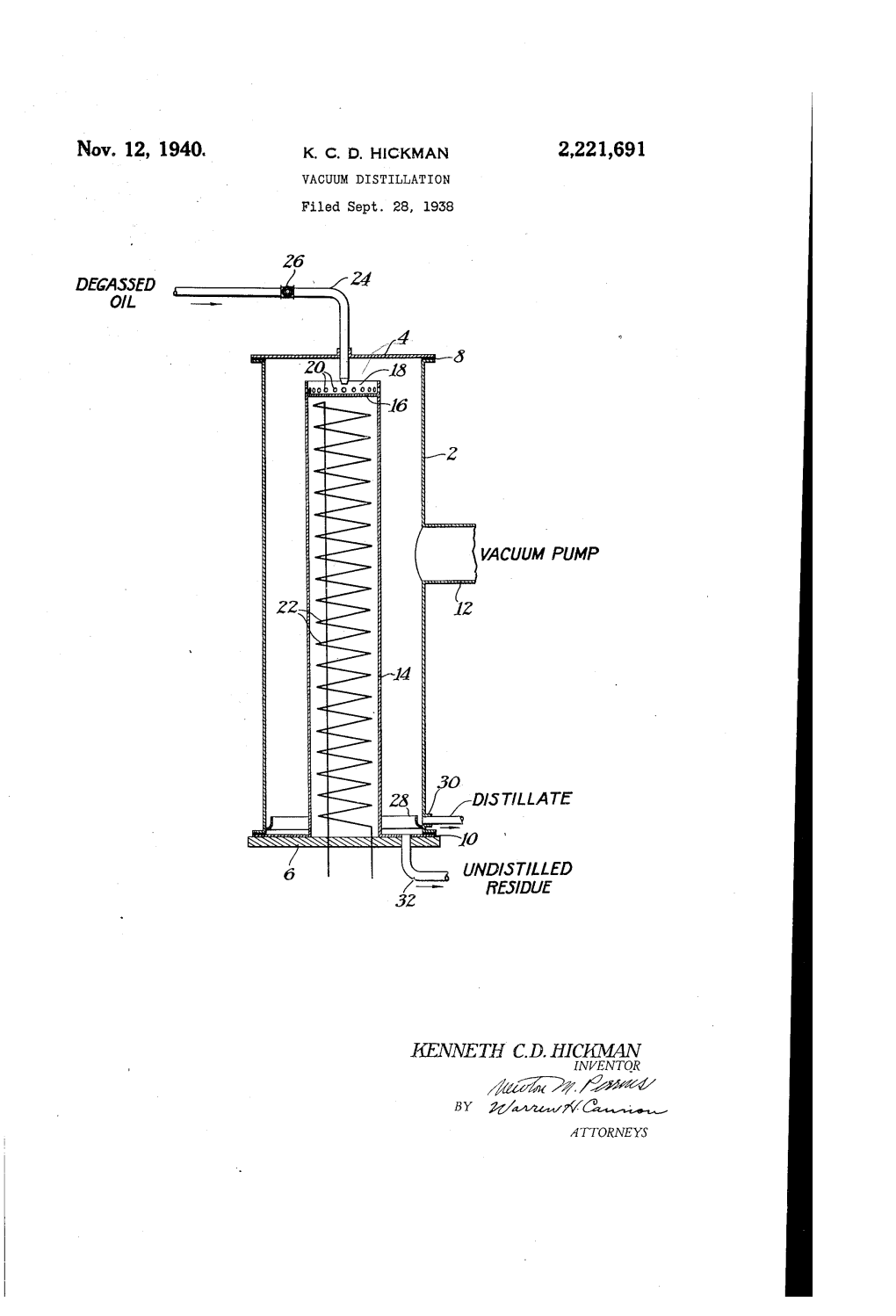
Load more
Recommended publications
-
Tailoring Diesel Bioblendstock from Integrated Catalytic Upgrading of Carboxylic Acids: a “Fuel Property First” Approach Xiangchen Huoa,B, Nabila A
Electronic Supplementary Material (ESI) for Green Chemistry. This journal is © The Royal Society of Chemistry 2019 Tailoring Diesel Bioblendstock from Integrated Catalytic Upgrading of Carboxylic Acids: A “Fuel Property First” Approach Xiangchen Huoa,b, Nabila A. Huqa, Jim Stunkela, Nicholas S. Clevelanda, Anne K. Staracea, Amy E. Settlea,b, Allyson M. Yorka,b, Robert S. Nelsona, David G. Brandnera, Lisa Foutsa, Peter C. St. Johna, Earl D. Christensena, Jon Lueckea, J. Hunter Mackc, Charles S. McEnallyd, Patrick A. Cherryd, Lisa D. Pfefferled, Timothy J. Strathmannb, Davinia Salvachúaa, Seonah Kima, Robert L. McCormicka, Gregg T. Beckhama, Derek R. Vardona* aNational Renewable Energy Laboratory, 15013 Denver West Parkway, Golden, CO, United States bColorado School of Mines, 1500 Illinois St., Golden, CO, United States cUniversity of Massachusetts Lowell, 220 Pawtucket St., Lowell, MA, United States dYale University, 9 Hillhouse Avenue, New Haven, CT, United States *[email protected] Section S1: Experimental Methods Catalyst synthesis and characterization Pt/Al2O3 catalyst was prepared by strong electrostatic adsorption method with chloroplatinic acid hexahydrate as Pt precursor. Al2O3 of 30-50 mesh and Pt precursor were added to deionized water, and solution pH was adjusted to 3 by adding HCl. After stirring overnight, the catalyst particles were recovered by filtration extensively washed with -1 deionized water. The catalyst was dried in the air and reduced in flowing H2 (200 mL min ) at 300°C for 4 h. BET surface area was determined by nitrogen physisorption using a Quadrasorb SI™ surface area analyzer from Quantachrome Instruments. Samples of ~80–120 mg were measured using a 55-point nitrogen adsorption/desorption curve at -196°C. -
Laboratory Rectifying Stills of Glass 2
» LABORATORY RECTIFYING STILLS OF GLASS 2 By Johannes H. Bruun 3 and Sylvester T. Schicktanz 3 ABSTRACT A complete description is given of a set of all-glass rectifying stills, suitable for distillation at pressures ranging from atmospheric down to about 50 mm. The stills are provided with efficient bubbling-cap columns containing 30 to 60 plates. Adiabatic conditions around the column are maintained by surrounding it with a jacket provided with a series of independent electrical heating units. Suitable means are provided for adjusting or maintaining the reflux ratio at the top of the column. For the purpose of conveniently obtaining an accurate value of the true boiling points of the distillates a continuous boiling-point apparatus is incor- porated in the receiving system. An efficient still of the packed-column type for distillations under pressures less than 50 mm is also described. Methods of operation and efficiency tests are given for the stills. CONTENTS Page I. Introduction 852 II. General features of the still assembly 852 III. Still pot 853 IV. Filling tube and heater for the still pot 853 V. Rectifying column 856 1. General features 856 2. Large-size column 856 3. Medium-size column 858 4. Small-size column 858 VI. Column jacket 861 VII. Reflux regulator 861 1. With variable reflux ratio 861 2. With constant reflux ratio 863 VIII. The continuous boiling-point apparatus 863 IX. Condensers and receiver 867 X. The mounting of the still 867 XI. Manufacture and transportation of the bubbling-cap still 870 XII. Operation of the bubbling-cap still 870 XIII. -
Building a Home Distillation Apparatus
BUILDING A HOME DISTILLATION APPARATUS A Step by Step Guide Building a Home Distillation Apparatus i BUILDING A HOME DISTILLATION APPARATUS Foreword The pages that follow contain a step-by-step guide to building a relatively sophisticated distillation apparatus from commonly available materials, using simple tools, and at a cost of under $100 USD. The information contained on this site is directed at anyone who may want to know more about the subject: students, hobbyists, tinkers, pure water enthusiasts, survivors, the curious, and perhaps even amateur wine and beer makers. Designing and building this apparatus is the only subject of this manual. You will find that it confines itself solely to those areas. It does not enter into the domains of fermentation, recipes for making mash, beer, wine or any other spirits. These areas are covered in detail in other readily available books and numerous web sites. The site contains two separate design plans for the stills. And while both can be used for a number of distillation tasks, it should be recognized that their designs have been optimized for the task of separating ethyl alcohol from a water-based mixture. Having said that, remember that the real purpose of this site is to educate and inform those of you who are interested in this subject. It is not to be construed in any fashion as an encouragement to break the law. If you believe the law is incorrect, please take the time to contact your representatives in government, cast your vote at the polls, write newsletters to the media, and in general, try to make the changes in a legal and democratic manner. -
19750010206.Pdf
AND NASA TECHNICAL NASA TM X-2932 MEMORANDUM c-v I N75-1827875827 VACUUM BY REMOVAL (NASA-TM--2932) BETTER (NASA) OF DIFFUSION-PUM1POIL CONTAMINANTS S70 -p HC $4.25 Unclas H1/14 12827 BETTER VACUUM BY REMOVAL OF . DIFFUSION-PUMP-OIL CONTAMINANTS Lewis Research Center Cleveland, Ohio 44135 AT'6ARONATIANDSPACADMINISTRATIONWASHINGTOND.1975 FEBRUARY * FEBRUARY 1975 NATIONAL AERONAUTICS AND SPACE ADMINISTRATION • WASHINGTON, D. C. 1. Report No. 2. Government Accession No. 3. Recipient's Catalog No. NASA TM X-2932 4. Title and Subtitle 5. Report Date 1975 BETTER VACUUM BY REMOVAL OF DIFFUSION-PUMP- February Organization Code OIL CONTAMINANTS 6. Performing 7. Author(s) 8. Performing Organization Report No. Alvin E. Buggele E-7583 10. Work Unit No. 9. Performing Organization Name and Address 491-01 Lewis Research Center 11. Contract or Grant No. National Aeronautics and Space Administration Cleveland, Ohio 44135 13. Type of Report and Period Covered 12. Sponsoring Agency Name and Address Technical Memorandum National Aeronautics and Space Administration 14. Sponsoring Agency Code Washington, D. C. 20546 15. Supplementary Notes Film supplement C-280 is available on request. 16. Abstract The complex problem of why large space simulation chambers do not realize true ultimate vacuum was investigated. Some contaminating factors affecting diffusion pump performance were identified and explained, and some advances in vacuum distillation-fractionation tech- nology were achieved which resulted in a two-decade-or-more lower ultimate pressure. Data are presented to show the overall or individual contaminating effects of commonly used phthalate ester plasticizers of 390 to 530 molecular weight on diffusion pump performance. -
5.1 Petroleum Refining1
5.1 Petroleum Refining1 5.1.1 General Description The petroleum refining industry converts crude oil into more than 2500 refined products, including liquefied petroleum gas, gasoline, kerosene, aviation fuel, diesel fuel, fuel oils, lubricating oils, and feedstocks for the petrochemical industry. Petroleum refinery activities start with receipt of crude for storage at the refinery, include all petroleum handling and refining operations and terminate with storage preparatory to shipping the refined products from the refinery. The petroleum refining industry employs a wide variety of processes. A refinery's processing flow scheme is largely determined by the composition of the crude oil feedstock and the chosen slate of petroleum products. The example refinery flow scheme presented in Figure 5.1-1 shows the general processing arrangement used by refineries in the United States for major refinery processes. The arrangement of these processes will vary among refineries, and few, if any, employ all of these processes. Petroleum refining processes having direct emission sources are presented on the figure in bold-line boxes. Listed below are 5 categories of general refinery processes and associated operations: 1. Separation processes a. Atmospheric distillation b. Vacuum distillation c. Light ends recovery (gas processing) 2. Petroleum conversion processes a. Cracking (thermal and catalytic) b. Reforming c. Alkylation d. Polymerization e. Isomerization f. Coking g. Visbreaking 3.Petroleum treating processes a. Hydrodesulfurization b. Hydrotreating c. Chemical sweetening d. Acid gas removal e. Deasphalting 4.Feedstock and product handling a. Storage b. Blending c. Loading d. Unloading 5.Auxiliary facilities a. Boilers b. Waste water treatment c. Hydrogen production d. -
Distillation Strategies: a Key Factor to Obtain Spirits with Specific Organoleptic Characteristics
DISTILLATION STRATEGIES: A KEY FACTOR TO OBTAIN SPIRITS WITH SPECIFIC ORGANOLEPTIC CHARACTERISTICS Pau Matias-Guiu Martí ADVERTIMENT. L'accés als continguts d'aquesta tesi doctoral i la seva utilització ha de respectar els drets de la persona autora. Pot ser utilitzada per a consulta o estudi personal, així com en activitats o materials d'investigació i docència en els termes establerts a l'art. 32 del Text Refós de la Llei de Propietat Intel·lectual (RDL 1/1996). Per altres utilitzacions es requereix l'autorització prèvia i expressa de la persona autora. En qualsevol cas, en la utilització dels seus continguts caldrà indicar de forma clara el nom i cognoms de la persona autora i el títol de la tesi doctoral. No s'autoritza la seva reproducció o altres formes d'explotació efectuades amb finalitats de lucre ni la seva comunicació pública des d'un lloc aliè al servei TDX. Tampoc s'autoritza la presentació del seu contingut en una finestra o marc aliè a TDX (framing). Aquesta reserva de drets afecta tant als continguts de la tesi com als seus resums i índexs. ADVERTENCIA. El acceso a los contenidos de esta tesis doctoral y su utilización debe respetar los derechos de la persona autora. Puede ser utilizada para consulta o estudio personal, así como en actividades o materiales de investigación y docencia en los términos establecidos en el art. 32 del Texto Refundido de la Ley de Propiedad Intelectual (RDL 1/1996). Para otros usos se requiere la autorización previa y expresa de la persona autora. En cualquier caso, en la utilización de sus contenidos se deberá indicar de forma clara el nombre y apellidos de la persona autora y el título de la tesis doctoral. -
5.1 Petroleum Refining1
5.1 Petroleum Refining1 5.1.1 General Description The petroleum refining industry converts crude oil into more than 2500 refined products, including liquefied petroleum gas, gasoline, kerosene, aviation fuel, diesel fuel, fuel oils, lubricating oils, and feedstocks for the petrochemical industry. Petroleum refinery activities start with receipt of crude for storage at the refinery, include all petroleum handling and refining operations, and they terminate with storage preparatory to shipping the refined products from the refinery. The petroleum refining industry employs a wide variety of processes. A refinery’s processing flow scheme is largely determined by the composition of the crude oil feedstock and the chosen slate of petroleum products. The example refinery flow scheme presented in Figure 5.1-1 shows the general processing arrangement used by refineries in the United States for major refinery processes. The arrangement of these processes will vary among refineries, and few, if any, employ all of these processes. Petroleum refining processes having direct emission sources are presented on the figure in bold-line boxes. Listed below are 5 categories of general refinery processes and associated operations: 1. Separation processes a. Atmospheric distillation b. Vacuum distillation c. Light ends recovery (gas processing) 2. Petroleum conversion processes a. Cracking (thermal and catalytic) b. Reforming c. Alkylation d. Polymerization e. Isomerization f. Coking g. Visbreaking 3. Petroleum treating processes a. Hydrodesulfurization b. Hydrotreating c. Chemical sweetening d. Acid gas removal e. Deasphalting 4. Feedstock and product handling a. Storage b. Blending c. Loading d. Unloading 5. Auxiliary facilities a. Boilers b. Waste water treatment c. Hydrogen production d. -
Harbauer Soil Washing/Vacuum-Distillation System
HARBAUER SOIL WASHING/VACUUM-DISTILLATION SYSTEM HARBAUER GmbH & COMPANY KG FACILITY MARKTREDWITZ, GERMANY EPA - BMBF BILATERAL SITE DEMONSTRATION INNOVATIVE TECHNOLOGY EVALUATION REPORT AUGUST 1996 Prepared for: U.S. ENVIRONMENTAL PROTECTION AGENCY NATIONAL RISK MANAGEMENT RESEARCH LABORATORY OFFICE OF RESEARCH AND DEVELOPMENT CINCINNATI, OHIO 45628 Prepared by: PRC Environmental Management Inc. 4065 Hancock Street, Suite 200 San Diego, California 92110 EPA Contract No. 68-C5-0037 Work Assignment No. 0-5 Notice The information in this document has been prepared for the U.S. Environmental Protection Agency's (EPA) Superfund Innovative Technology Evaluation (SITE) program in accordance with a bilateral agreement between EPA and the Federal Republic of German Ministry for Research and Technology (BMBF), and under Contract No. 68-C5-0037 to PRC Environmental Management, Inc. This document has been subjected to EPA's peer and administrative reviews, and has been approved for publication as an EPA document. Mention of trade names or commercial products does not constitute an endorsement or recommendation for use. i Foreword The Superfund Innovative Technology Evaluation (SITE) program was authorized by the Superfund Amendments and Reauthorization Act (SARA) of 1986. The program is administered by the U.S. Environmental Protection Agency (EPA) Office of Research and Development (ORD). The purpose of the SITE program is to accelerate the development and use of innovative remediation technologies applicable to Superfund and other hazardous waste sites. This purpose is accomplished through technology demonstrations designed to provide performance and cost data on selected technologies. This technology demonstration, conducted under the SITE program, evaluated the Harbauer soil washing/vacuum-distillation technology developed by Harbauer GmbH & Co. -
Development of a New Type of Centrifugal Vacuum Distillation System
ULVAC TECHNICAL JOURNAL (ENGLISH) No.70E 2009 Development of a New Type of Centrifugal Vacuum Distillation System Takashi Hanamoto* 1. Introduction and higher function products in conventional fi ne chemi- cal industries, including medical and cosmetic products. We have developed and launched a new type of cen- At the same time, there is demand for further cost reduc- trifugal vacuum distillation system (model, CEH-400B II). tion and development of high value added products due to Improved from conventional distillation systems in terms a higher crude oil price than ever before. of compactness and operability, this new system can be In these situations, fi ne chemical industries are required operated even by those who are unskilled in distillation to stabilize the physical properties of materials in prod- process operations. ucts, remove particular impurities and improve degrees Recently, packaging technologies and semiconductor of purity. They are forced to shift production from cost- devices have made progress and positive environmental oriented mass production to production of a wide variety measures have been introduced in the fi elds of electronic of products in small quantities focusing on added value, parts, FPD and other electronics materials. This situa- showing a tendency toward made-to-order production. tion has spurred demand for new functions and more Target components can be separated and refined from advanced performance than ever before in material fi elds chemically synthesized materials and natural materials in recent years. -
Distillation • Distillation Is a Method of Separating Mixtures Based on Differences in Their Volatilities in a Boiling Liquid Mixture
Distillation • Distillation is a method of separating mixtures based on differences in their volatilities in a boiling liquid mixture. • Distillation is a unit operation, or a physical separation process, and not a chemical reaction. • Commercially, distillation is used to separate crude oil itinto more frac tions for spec ific uses suc h as transport, power generation and heating. • Water is distilled to remove impurities, such as salt from seawater. • Air is distilled to separate its components— oxygen, nitrogen, and argon—for industrial use. • Distillation of fermented solutions has been used since ancient times to produce distilled beverages with a higher alcohol content. History • The first clear evidence of distillation comes from GkGreek alhlchem itists working in Alexan dr ia ithfitin the first century AD. Distilled water has been known since at least ca. 200 AD. Arabs learned the process from the Egyptians and used it extensively in their alchemical experiments. • The first clear evidence from the distillation of alcohol comes from the School of Salerno in the 12th century. Fractional distillation was developed by Tadeo Alderotti in the 13th century. • In 1500, German alchemist Hieronymus Braunschweig published the Book of the Art of Distillation, the first book solely dedicated to the subject of distillation. In 1651, John French published The Art of Distillation the first major English compendium of practice. This includes diagrams with people in them showing the industrial rather than bench scale of the operation. • Early forms of distillation were batch processes using one vaporization and one condensation. Purity was improved by further distillation of the condensate. Greater volumes were processed by simply repeating the dis tilla tion. -
REFINING, FUELS and PETROCHEMICALS - Petroleum: Chemistry, Refining, Fuels and Petrochemicals –Refining - James G
PETROLEUM: CHEMISTRY, REFINING, FUELS AND PETROCHEMICALS - Petroleum: Chemistry, Refining, Fuels and Petrochemicals –Refining - James G. Speight PETROLEUM: CHEMISTRY, REFINING, FUELS AND PETROCHEMICALS -REFINING James G. Speight 2476 Overland Road,Laramie, WY 82070-4808, USA Keywords: Dewatering, desalting, atmospheric distillation, vacuum distillation, azeotropic distillation, extractive distillation, thermal cracking, visbreaking, delayed coking, fluid coking, flexicoking, catalytic cracking, hydrocracking, hydrotreating, thermal reforming, catalytic reforming, isomerization, alkylation, polymerization, Contents 1. Introduction 2. Dewatering and Desalting 3. Distillation 3.1. Atmospheric Distillation 3.2. Vacuum Distillation 3.3. Azeotropic and Extractive Distillation 4. Thermal Processes 4.1. Thermal Cracking 4.2. Steam Cracking 4.3. Visbreaking 4.4. Coking 5. Catalytic Processes 5.1. Processes 5.2. Catalysts 6. Hydroprocesses 6.1. Hydrocracking 6.2. Hydrotreating 7. Reforming Processes 7.1. Thermal Reforming 7.2. Catalytic Reforming 7.3. Catalysts 8. Isomerization Processes 8.1. ProcessesUNESCO – EOLSS 8.3. Catalysts 9. Alkylation Processes 9.1. Processes SAMPLE CHAPTERS 9.2. Catalysts 10. Polymerization Processes 10.1. Processes 10.2. Catalysts 11. Extraction 11.2. Deasphalting 11.3. Dewaxing 12. Treating Processes 13. Asphalt Production ©Encyclopedia Of Life Support Systems (EOLSS) PETROLEUM: CHEMISTRY, REFINING, FUELS AND PETROCHEMICALS - Petroleum: Chemistry, Refining, Fuels and Petrochemicals –Refining - James G. Speight 14. Hydrogen Production 15. Other Refining Operations Glossary Bibliography Biographical Sketch Summary In the crude state petroleum has minimal value, but when refined it provides high-value liquid fuels, solvents, lubricants, and many other products. Refining petroleum involves subjecting the feedstock to a series of physical and chemical processes as a result of which a variety of products are generated. -
Molbank 2005, M405
(2endo)-2-Chloro-1,4,4-trimethyl-8-oxabicyclo[3.2.1]oct-6-en-3-one (2... http://www.mdpi.org/molbank/molbank2005/m405.htm Molbank 2005 , M405 (2endo )-2-Chloro-1,4,4-trimethyl-8-oxabicyclo[3.2.1]oct-6-en-3-one Jutta Oexle, Michael Buchinger, and Baldur Föhlisch * Institut für Organische Chemie der Universität Stuttgart, Pfaffenwaldring 55, D-70569 Stuttgart, Germany Fax (+49) 711/6854269; E-mail: [email protected] Received: 8 March 2004 / Accepted: 18 March 2004 / Published: 3 October 2005 1. Procedure (2 endo )-2-Chloro-1,4,4-trimethyl-8-oxabicyclo[3.2.1]oct-6-en-3-one (2) is synthesized via [4+3] cycloaddition of an oxyallyl intermediate generated from 1,3-dichloro-3-methylbutan-2-one with lithium perchlorate / diethylether / triethylamine. A. 1,3-Dichloro-3-methylbutan-2-one (Note 1). Caution: The operation must be carried out in a well-vented hood. The evolving HCl and SO 2 gas should be absorbed by passing over water. A 2-L, three-necked, round-bottomed flask, fitted with a dropping funnel, immersion thermometer, drying tube (calcium chloride) and an efficient Teflon-coated magnetic stirring bar ("Circulus"), is charged with 3-methylbutan-2-one (isopropyl methyl ketone) (430 mL, ca. 346 g, 4.0 mol) (Note 2) and chilled in an ice bath. With magnetic stirring, freshly distilled sulfuryl chloride (800 mL, ca. 1334 g, 9.9 mol) is added dropwise. The internal temperature is controlled to be between 10 and 15°C; this takes approximately 3 hours.