Hydrotalcite-Like Compounds: a Way to Recover A
Total Page:16
File Type:pdf, Size:1020Kb
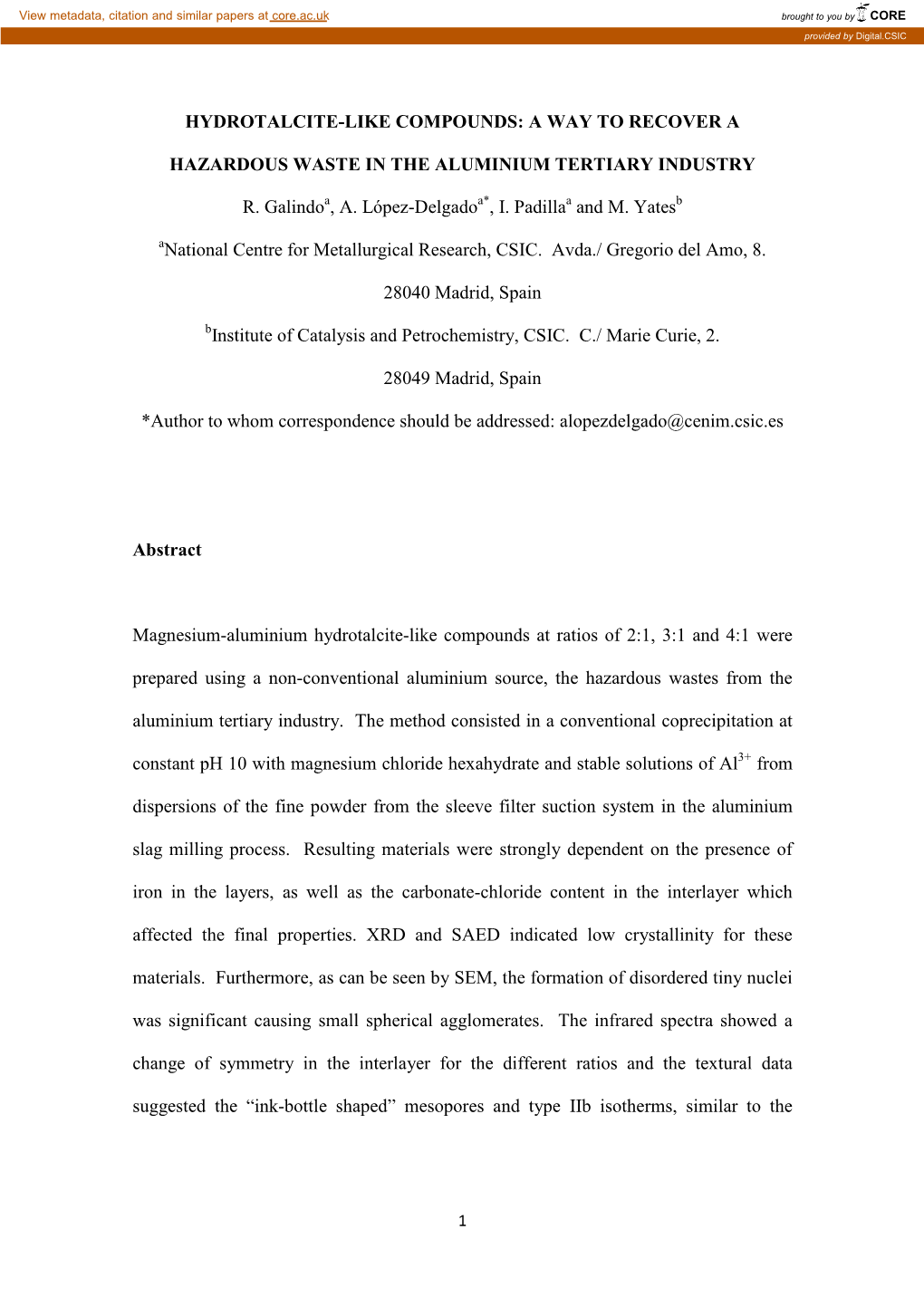
Load more
Recommended publications
-
Minerals of the Hydrotalcite Group in Metasomatically Altered Carbonate Rocks from Zawiercie, S Poland
MINERALOGIA POLONICA Vol. 32, No 1, 2001 PL ISSSN 0032-6267 Ewa KOSZOWSKA1, Dorota SAŁATA1 MINERALS OF THE HYDROTALCITE GROUP IN METASOMATICALLY ALTERED CARBONATE ROCKS FROM ZAWIERCIE, S POLAND A b s t a c t . Minerals of the hydrotalcite-manasseite group were identified in samples from two borehols in Zawiercie (ZMZ-9, RK-1). The minerals were found in calciphire bodies (RK-1) and in one small, metasomatic veinlet (ZMZ-9) formed in Middle Devonian dolomites. Alteration of dolomitic sediments was genetically connected with infiltration fluids that caused formation of a gamet-pyroxene skam. Inves tigations have revealed the presence of both hydrotalcite and manasseite. Besides, in few places of the veinlet there occurs a mineral, which has been recognized as iowaite. Key-words: hydrotalcite-manasseite group, calciphires, ska ms, metasomatic veins, Zawiercie, S Poland INTRODUCTION The hydrotalcite group minerals belong to a large group of natural and synthetic dihydroxides named also as "layered double hydroxides" or "anionic clays". Their general formula can be written as: M |2XM (0 H)2 (Am“)x/mn H 2 0 (where M+2, M +3 are cations in the hydroxide layers and Am_ is the interlayer anion) and is based on positively charged brucite-like layers with C 03-like anions and water molecules in interlayer positions (Drits et al. 1987) (Fig. la). Within the group, depending on the composition of the octahedral brucite-type cationic layers, three subgroups can be distinguished in which the cations are: a) M g +2 + Al+3, b) Mg +2 + Fe+3 , c) M g + 2 + C r+3. -
Infrare D Transmission Spectra of Carbonate Minerals
Infrare d Transmission Spectra of Carbonate Mineral s THE NATURAL HISTORY MUSEUM Infrare d Transmission Spectra of Carbonate Mineral s G. C. Jones Department of Mineralogy The Natural History Museum London, UK and B. Jackson Department of Geology Royal Museum of Scotland Edinburgh, UK A collaborative project of The Natural History Museum and National Museums of Scotland E3 SPRINGER-SCIENCE+BUSINESS MEDIA, B.V. Firs t editio n 1 993 © 1993 Springer Science+Business Media Dordrecht Originally published by Chapman & Hall in 1993 Softcover reprint of the hardcover 1st edition 1993 Typese t at the Natura l Histor y Museu m ISBN 978-94-010-4940-5 ISBN 978-94-011-2120-0 (eBook) DOI 10.1007/978-94-011-2120-0 Apar t fro m any fair dealin g for the purpose s of researc h or privat e study , or criticis m or review , as permitte d unde r the UK Copyrigh t Design s and Patent s Act , 1988, thi s publicatio n may not be reproduced , stored , or transmitted , in any for m or by any means , withou t the prio r permissio n in writin g of the publishers , or in the case of reprographi c reproductio n onl y in accordanc e wit h the term s of the licence s issue d by the Copyrigh t Licensin g Agenc y in the UK, or in accordanc e wit h the term s of licence s issue d by the appropriat e Reproductio n Right s Organizatio n outsid e the UK. Enquirie s concernin g reproductio n outsid e the term s state d here shoul d be sent to the publisher s at the Londo n addres s printe d on thi s page. -
Crystal Structure and Comparative Crystal Chemistry of AI2M~(OH)12(C03) · 3H20, a New Mineral from the Hydrotalcite-Manasseite Group A
Crystallography,Repons, Vol. 41, No.6, 1996, pp. 972-981. Transltnedfrom Kristallograjiya, VoL 41, No.6, 1996, pp. 1024-1034. @ Original Russian Text Copyright 1996 by Aralccheeva, Pushcharovskii, Rastwetaeva, Atencio, Luhman. Crystal Structure and Comparative Crystal Chemistry of AI2M~(OH)12(C03) · 3H20, a New Mineral from the Hydrotalcite-Manasseite Group A. v. Arakcheeva*, D. Yu. Pushcharovskii**, R. K. Rastsvetaeva***, D. Atencio****, and G. U. Lubman* Baikov Institute of Metallurgy, Russian Academy of Sciences, Leninskii pro 49, Moscow, 117334 Russia * Moscow State University, Moscow, 119899 Russia ** *** Shubnikov Institute of Crystallography, Russian Academy of Sciences, Leninskii pro 59, Moscow, //7333 Russia **** University of Sao Paulo, Sao Paulo, Brazil Received April 9, 1996 . 3H~O from Ihe Abstract-The crystal structure of a new mineral of the composition AI2Mg4(OH)12(C03) hydrotalcite-manasseite group has been determined by X-ray structure analysis. The parameters of Ihe hexag- onal unit cell are a =5.283(3), c = 15.150(9) A; sp. gr. P6 2m. The structure was refined over 52 cryslallograph- ically nonequivalent reflections up to R =0.039. The hydrogen atoms of hydroxyl groups are localized. The new mineral differs from otherrepresentatives oHhis group by the complete order of all the atoms, which is rctkl'!ed in a lower structure symmetry. The variety of minerals within the group is considered and interpreled in lerms of polytypism, the atomic order in the structure of sublattices, and isomorphous substitutions. INTRODUCTION Later on, one more mineral-chlormagaluminite (Mg, Fe)4A12(OH)dCI, (C03)o.sh 2H:O-w~ Depending on the composition of the octahedral included into the hydrotalcite-manasseite ..ubgroup. -
A Specific Gravity Index for Minerats
A SPECIFICGRAVITY INDEX FOR MINERATS c. A. MURSKyI ern R. M. THOMPSON, Un'fuersityof Bri.ti,sh Col,umb,in,Voncouver, Canad,a This work was undertaken in order to provide a practical, and as far as possible,a complete list of specific gravities of minerals. An accurate speciflc cravity determination can usually be made quickly and this information when combined with other physical properties commonly leads to rapid mineral identification. Early complete but now outdated specific gravity lists are those of Miers given in his mineralogy textbook (1902),and Spencer(M,i,n. Mag.,2!, pp. 382-865,I}ZZ). A more recent list by Hurlbut (Dana's Manuatr of M,i,neral,ogy,LgE2) is incomplete and others are limited to rock forming minerals,Trdger (Tabel,l,enntr-optischen Best'i,mmungd,er geste,i,nsb.ildend,en M,ineral,e, 1952) and Morey (Encycto- ped,iaof Cherni,cal,Technol,ogy, Vol. 12, 19b4). In his mineral identification tables, smith (rd,entifi,cati,onand. qual,itatioe cherai,cal,anal,ys'i,s of mineral,s,second edition, New york, 19bB) groups minerals on the basis of specificgravity but in each of the twelve groups the minerals are listed in order of decreasinghardness. The present work should not be regarded as an index of all known minerals as the specificgravities of many minerals are unknown or known only approximately and are omitted from the current list. The list, in order of increasing specific gravity, includes all minerals without regard to other physical properties or to chemical composition. The designation I or II after the name indicates that the mineral falls in the classesof minerals describedin Dana Systemof M'ineralogyEdition 7, volume I (Native elements, sulphides, oxides, etc.) or II (Halides, carbonates, etc.) (L944 and 1951). -
Layered Double Hydroxides with Intercalated Permanganate and Peroxydisulphate Anions for Oxidative Removal of Chlorinated Organic Solvents Contaminated Water
minerals Article Layered Double Hydroxides with Intercalated Permanganate and Peroxydisulphate Anions for Oxidative Removal of Chlorinated Organic Solvents Contaminated Water Karen Maria Dietmann 1 , Tobias Linke 2, Miguel del Nogal Sánchez 3 , José Luis Pérez Pavón 3 and Vicente Rives 1,* 1 Grupo de Investigación Reconocido—Química del Estado Sólido, Materiales y Catálisis Heterogénea (GIR-QUESCAT), Departamento de Química Inorgánica, Universidad de Salamanca, 37008 Salamanca, Spain; [email protected] 2 Institute of Earth Sciences, University of Iceland, Sturlugata 7, 101 Reykjavík, Iceland; [email protected] 3 Departamento de Química Analítica, Nutrición y Bromatología, Universidad de Salamanca, 37008 Salamanca, Spain; [email protected] (M.d.N.S.); [email protected] (J.L.P.P.) * Correspondence: [email protected] Received: 9 April 2020; Accepted: 18 May 2020; Published: 20 May 2020 Abstract: The contamination by chlorinated organic solvents is a worldwide problem as they can deeply penetrate aquifers, accumulating in the sub-surface as lenses of highly hazardous pollutants. In recent years, so called in situ oxidation processes have been developed to remediate chlorinated organic solvents from groundwater and soil by injecting solutions of oxidising agents such as permanganate or peroxydisulphate. We here present modified layered double hydroxides (LDHs) with intercalated oxidising agents that might serve as new reactants for these remediation strategies. LDHs might serve as support and stabiliser materials for selected oxidising agents during injection, as the uncontrolled reaction and consumption might be inhibited, and guarantee that the selected oxidants persist in the subsurface after injection. In this study, LDHs with hydrotalcite- and hydrocalumite-like structures intercalated with permanganate and peroxydisulphate anions were synthesised and their efficiency was tested in batch experiments using trichloroethene or 1,1,2-trichloroethane as the target contaminants. -
12Cl23h2o, a New Gibbsite-Based Hydrotalcite Supergroup
minerals Article Dritsite, Li2Al4(OH)12Cl2·3H2O, a New Gibbsite-Based Hydrotalcite Supergroup Mineral Elena S. Zhitova 1,2,* , Igor V. Pekov 3, Ilya I. Chaikovskiy 4, Elena P. Chirkova 4, Vasiliy O. Yapaskurt 3, Yana V. Bychkova 3, Dmitry I. Belakovskiy 5, Nikita V. Chukanov 6, Natalia V. Zubkova 3, Sergey V. Krivovichev 1,7 and Vladimir N. Bocharov 8 1 Department of Crystallography, St. Petersburg State University, Universitetskaya nab. 7/9, St. Petersburg 199034, Russia 2 Laboratory of Mineralogy, Institute of Volcanology and Seismology, Russian Academy of Sciences, Bulvar Piypa 9, Petropavlovsk-Kamchatsky 683006, Russia 3 Faculty of Geology, Moscow State University, Vorobievy Gory, Moscow 119991, Russia 4 Mining Institute, Ural Branch of the Russian Academy of Sciences, Sibirskaya str., 78a, Perm 614007, Russia 5 Fersman Mineralogical Museum, Russian Academy of Sciences, Leninsky Prospekt 18-2, Moscow 119071, Russia 6 Institute of Problems of Chemical Physics, Russian Academy of Sciences, Akad. Semenova 1, Chernogolovka, Moscow Region 142432, Russia 7 Nanomaterials Research Centre, Kola Science Centre, Russian Academy of Sciences, Fersman Street 14, Apatity 184209, Russia 8 Resource Center Geomodel, St. Petersburg State University, Universitetskaya nab. 7/9, St. Petersburg 199034, Russia * Correspondence: [email protected]; Tel.: +7-924-587-51-91 Received: 2 August 2019; Accepted: 14 August 2019; Published: 17 August 2019 Abstract: Dritsite, ideally Li Al (OH) Cl 3H O, is a new hydrotalcite supergroup mineral formed 2 4 12 2· 2 as a result of diagenesis in the halite carnallite rock of the Verkhnekamskoe salt deposit, Perm Krai, − Russia. Dritsite forms single lamellar or tabular hexagonal crystals up to 0.25 mm across. -
Hydrotalcites in Construction Materials
applied sciences Review Hydrotalcites in Construction Materials Anna-Marie Lauermannová 1 , Iva Paterová 2, Jan Patera 2, Kryštof Skrbek 1, OndˇrejJankovský 1 and Vilém Bart ˚unˇek 1,* 1 Department of Inorganic Chemistry, Faculty of Chemical Technology, University of Chemistry and Technology, Prague, Technická 5, 166 28 Prague, Czech Republic; [email protected] (A.-M.L.); [email protected] (K.S.); [email protected] (O.J.) 2 Department of Organic Technology, Faculty of Chemical Technology, University of Chemistry and Technology, Prague, Technická 5, 166 28 Prague, Czech Republic; [email protected] (I.P.); [email protected] (J.P.) * Correspondence: [email protected]; Tel.: +42-022-0443-765 Received: 25 September 2020; Accepted: 9 November 2020; Published: 11 November 2020 Featured Application: In this contribution, the applications of the hydrotalcites and hydrotalcite-like materials in the building materials, cements, mortars, and concretes are summarized. Abstract: Hydrotalcites are layered double hydroxides displaying a variety of stoichiometry caused by the different arrangement of the stacking of the layers, ordering of the metal cations, as well as the arrangement of anions and water molecules, in the interlayer galleries. The compounds of the hydrotalcite group show a wide range of the possible applications due to their specific properties, such as their large surface area, ion exchange ability, the insolubility in water and most of the organic sorbents, and others. Affordability, wide possibilities of manufacturing, and presence of sufficient natural deposits make hydrotalcites potentially very useful for the construction industry, as either a building material itself or an additive in mortars, concrete or in polymers composites used in constructions. -
Pauloabibite, Trigonal Nanbo3, Isostructural with Ilmenite, from the Jacupiranga Carbonatite, Cajati, São Paulo, Brazil
American Mineralogist, Volume 100, pages 442–446, 2015 Pauloabibite, trigonal NaNbO3, isostructural with ilmenite, from the Jacupiranga carbonatite, Cajati, São Paulo, Brazil LUIZ A.D. MENEZES FILHO1,†, DANIEL ATENCIO2,*, MARCELO B. ANDRADE3, ROBERT T. DOWNS4, MÁRIO L.S.C. CHAVES1, ANTÔNIO W. ROMANO1, RICARDO SCHOLZ5 AND ABA I.C. PERSIANO6 1Instituto de Geociências, Universidade Federal de Minas Gerais, Avenida Antônio Carlos, 6627, 31270-901, Belo Horizonte, Minas Gerais, Brazil 2Instituto de Geociências, Universidade de São Paulo, Rua do Lago 562, 05508-080, São Paulo, São Paulo, Brazil 3Instituto de Física de São Carlos, Universidade de São Paulo, Caixa Postal 369, 13560-970, São Carlos, São Paulo, Brazil 4Department of Geosciences, University of Arizona, Tucson, Arizona 85721-0077, U.S.A. 5Departamento de Geologia da Escola de Minas da Universidade Federal de Ouro Preto, Campus Morro do Cruzeiro, Ouro Preto, 35400-000, Minas Gerais, Brazil 6Departamento de Física do Instituto de Ciências Exatas da Universidade Federal de Minas Gerais, Avenida Antônio Carlos, 6627, 31279-901, Belo Horizonte, Minas Gerais, Brazil ABSTRACT Pauloabibite (IMA 2012-090), trigonal NaNbO3, occurs in the Jacupiranga carbonatite, in Cajati County, São Paulo State, Brazil, associated with dolomite, calcite, magnetite, phlogopite, pyrite, pyr- rhotite, ancylite-(Ce), tochilinite, fluorapatite, “pyrochlore”, vigezzite, and strontianite. Pauloabibite occurs as encrustations of platy crystals, up to 2 mm in size, partially intergrown with an unidentified Ca-Nb-oxide, embedded in dolomite crystals, which in this zone of the mine can reach centimeter sizes. Cleavage is perfect on {001}. Pauloabibite is transparent and displays a sub-adamantine luster; it is pinkish brown and the streak is white. -
A Novel Route for the Preparation of Hydrotalcite and Synthesis of Intercalated Reversible Dioxygen-Carrying Cobalt (II) Complexes
A Novel Route for the Preparation of Hydrotalcite and Synthesis of Intercalated Reversible Dioxygen-Carrying Cobalt (II) Complexes M. ZIKMUND, К. PUTYERA, and K. HRNCIAROVÁ Institute of Inorganic Chemistry, Slovak Academy of Sciences, SK-842 36 Bratislava Received 17 May 1996 Reacting a solid MgCC>3-3H20 or Mg5(C03)4(OH)2 • 5H2O (nesquehonite, hydromagnesite, dypingite) with an aqueous solution of sodium aluminate and sodium hydroxide is a novel pro cedure to synthesize solid solutions with desired stoichiometric Mg/Al ratios in the hydrotalcite series [Мёз-*А1(ОН)8-2хЫ(СОз)(Н20)4-х] (0 < x < 1). By mixing of an intermediate solid solution of magnesium aluminium oxide obtained by thermal decomposition of hydrotalcite with an aqueous solution of mono- or a, u-dicarboxylates which con tain N-donor atom in the presence of ethylene glycol as a swelling agent pillared aminocarboxylate derivatives of hydrotalcite are produced. Nitrogen donor atoms of aminocarboxylate pillars may react with cobalt(II) complexes to form coordinatively unsaturated cobalt(II) chelates. The synthe sized model Co(salen) and Co(salophen) complexes immobilized in the interlayer region of anionic clays reversibly bind dioxygen and enjoy high stability in the course of oxygenation-deoxygenation cycles. A relatively scarce natural mineral of the chemi tion of divalent cations (e.g. Mn = Mg, Zn, Fe, Co, Ni, 111 cal composition ranged from [Mg6Al2(OH)i6][(C03) Cu) and trivalent cations (e.g. M = AI, Fe, Co, Mn, (H20)4] to [Mg4Al2(OH)12][(C03)(H20)3] occurs in Cr, V) into the brucite-like layers; replacing of anions 71 2 2 two polytype modifications, C03-hydrotalcite-3ič (hy (e.g. -
Nickel Speciation, Microbial Community Structure, And
University of Kentucky UKnowledge Theses and Dissertations--Plant and Soil Sciences Plant and Soil Sciences 2020 NICKEL SPECIATION, MICROBIAL COMMUNITY STRUCTURE, AND CHEMICAL ATTRIBUTES IN THE RHIZOSPHERE OF NICKEL HYPERACCUMULATING AND NON-ACCUMULATING PLANTS GROWING IN SERPENTINE SOILS James W. Morris University of Kentucky, [email protected] Digital Object Identifier: https://doi.org/10.13023/etd.2020.154 Right click to open a feedback form in a new tab to let us know how this document benefits ou.y Recommended Citation Morris, James W., "NICKEL SPECIATION, MICROBIAL COMMUNITY STRUCTURE, AND CHEMICAL ATTRIBUTES IN THE RHIZOSPHERE OF NICKEL HYPERACCUMULATING AND NON-ACCUMULATING PLANTS GROWING IN SERPENTINE SOILS" (2020). Theses and Dissertations--Plant and Soil Sciences. 131. https://uknowledge.uky.edu/pss_etds/131 This Doctoral Dissertation is brought to you for free and open access by the Plant and Soil Sciences at UKnowledge. It has been accepted for inclusion in Theses and Dissertations--Plant and Soil Sciences by an authorized administrator of UKnowledge. For more information, please contact [email protected]. STUDENT AGREEMENT: I represent that my thesis or dissertation and abstract are my original work. Proper attribution has been given to all outside sources. I understand that I am solely responsible for obtaining any needed copyright permissions. I have obtained needed written permission statement(s) from the owner(s) of each third-party copyrighted matter to be included in my work, allowing electronic distribution (if such use is not permitted by the fair use doctrine) which will be submitted to UKnowledge as Additional File. I hereby grant to The University of Kentucky and its agents the irrevocable, non-exclusive, and royalty-free license to archive and make accessible my work in whole or in part in all forms of media, now or hereafter known. -
Eprints.Qut.Edu.Au
View metadata, citation and similar papers at core.ac.uk brought to you by CORE provided by Queensland University of Technology ePrints Archive QUT Digital Repository: http://eprints.qut.edu.au/ This is the author version published as: This is the accepted version of this article. To be published as : This is the author version published as: Frost, Ray L. and Palmer, Sara J. and Grand, Laure-Marie (2010) Synthesis and thermal stability of hydrotalcites containing manganese. Journal of Thermal Analysis and Calorimetry, 100(3). pp. 981-985. Copyright 2010 Akadémiai Kiadó/Springer Science+Business Media B.V. 1 Synthesis and thermal stability of hydrotalcites containing manganese 2 3 Laure-Marie Grand, 1, 2 Sara J. Palmer 1 and Ray L. Frost 1 4 5 1 Inorganic Materials Research Program, School of Physical and Chemical Sciences, 6 Queensland University of Technology, GPO Box 2434, Brisbane Queensland 4001, 7 Australia. 8 9 2 ENSICAEN, 6 Boulevard Marechal Juin, 14050 CAEN Cedex 4, France 10 11 ABSTRACT 12 13 The hydrotalcite based upon manganese known as charmarite 14 Mn4Al2(OH)12CO3·3H2O has been synthesised with different Mn/Al ratios from 4:1 to 2:1. 15 Impurities of manganese oxide, rhodochrosite and bayerite at low concentrations were also 16 produced during the synthesis. The thermal stability of charmarite was investigated using 17 thermogravimetry. The manganese hydrotalcite decomposed in stages with mass loss steps at 18 211, 305 and 793°C. The product of the thermal decomposition was amorphous material 19 mixed with manganese oxide. A comparison is made with the thermal decomposition of the 20 Mg/Al hydrotalcite. -
Stichtite Mg6cr2(CO3)(OH)16 • 4H2O C 2001-2005 Mineral Data Publishing, Version 1
Stichtite Mg6Cr2(CO3)(OH)16 • 4H2O c 2001-2005 Mineral Data Publishing, version 1 Crystal Data: Hexagonal. Point Group: 32/m. As aggregates of fibers or plates, commonly matted, contorted; as cross-fiber veinlets and micaceous scales. Physical Properties: Cleavage: Perfect on {0001}. Tenacity: Laminae flexible, not elastic; greasy feel. Hardness = 1.5–2 D(meas.) = 2.16 D(calc.) = 2.11 Optical Properties: Transparent. Color: Lilac to rose-pink; lilac to rose-pink in transmitted light. Streak: Very pale lilac to white. Luster: Waxy to resinous, somewhat pearly. Optical Class: Uniaxial (–); may be anomalously biaxial. Pleochroism: Weak; O = dark rose-pink to lilac; E = light rose-pink to lilac. ω = 1.545(3) = 1.518(3) 2V(meas.) = Small. Cell Data: Space Group: R3m. a = 3.09 c = 23.19 Z = 3/8 X-ray Powder Pattern: Dundas, Tasmania, Australia. (ICDD 14-330). 7.8 (100), 3.91 (90), 2.60 (40), 2.32 (30), 1.97 (30), 1.54 (20), 1.51 (20) Chemistry: (1) (2) Al2O3 2.30 Fe2O3 4.18 Cr2O3 14.15 23.24 MgO 37.72 36.98 H2O 34.14 33.05 CO2 7.15 6.73 Total [100.00] 100.00 (1) Dundas, Tasmania, Australia; probably intermixed with barbertonite, original total given as 99.27%, recalculated to 100% after deduction of SiO2 2.09%, FeO 0.28% as chromite. • (2) Mg6Cr2(CO3)(OH)16 4H2O. Polymorphism & Series: Dimorphous with barbertonite. Mineral Group: Hydrotalcite group. Occurrence: An alteration product of chromite in serpentinite. Association: Barbertonite, chromite, antigorite. Distribution: From Stichtite Hill, near the Adelaide mine, Dundas, Tasmania, Australia.