PDF File Generated From
Total Page:16
File Type:pdf, Size:1020Kb
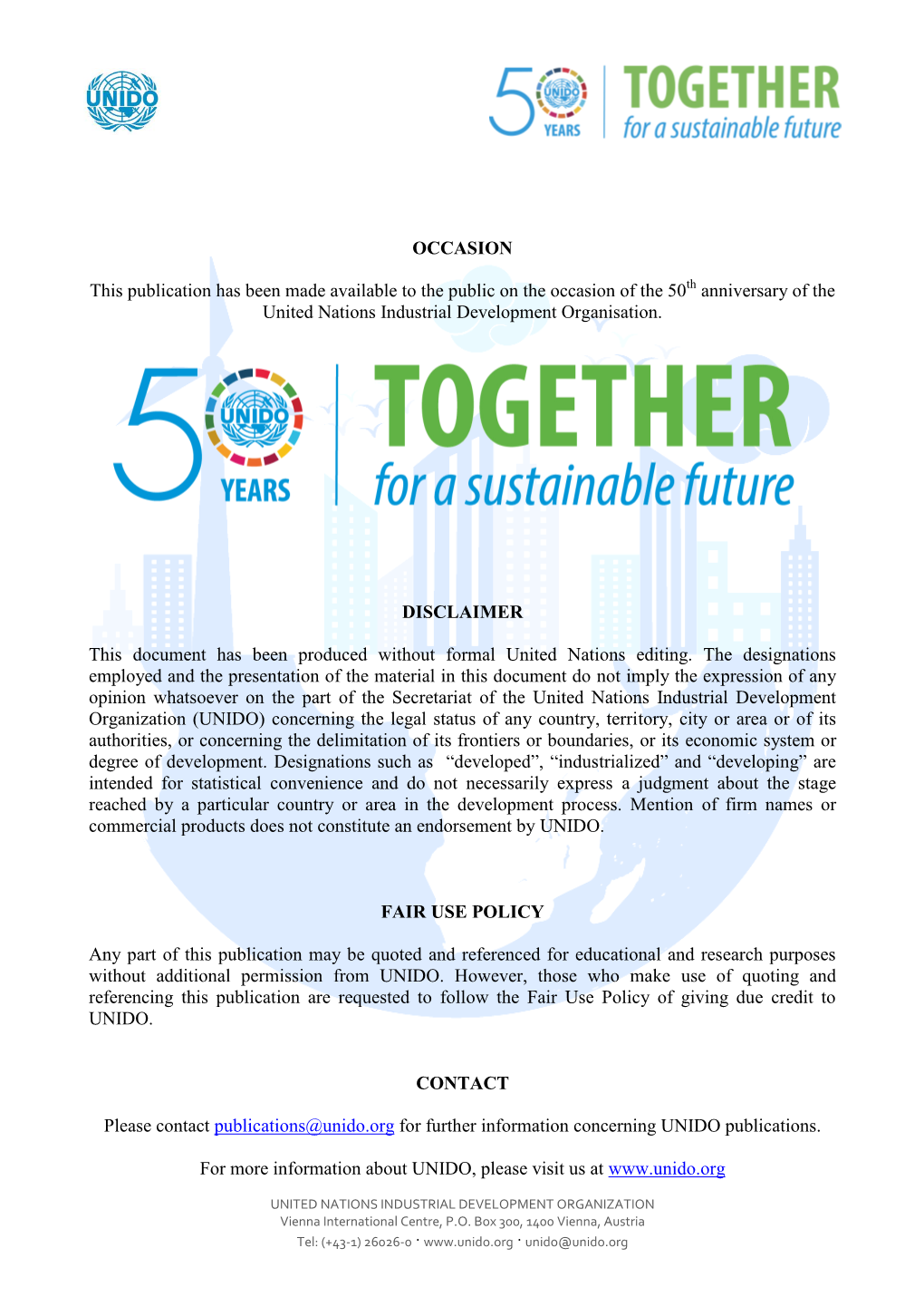
Load more
Recommended publications
-
Study on Improving the Production Rate by Rapier Looms in Textile Industry Aby Chummar, Soni Kuriakose, George Mathew
ISSN: 2277-3754 ISO 9001:2008 Certified International Journal of Engineering and Innovative Technology (IJEIT) Volume 2, Issue 7, January 2013 Study on Improving the Production Rate by Rapier Looms in Textile Industry Aby Chummar, Soni Kuriakose, George Mathew the company. It is mainly manufactured by the shuttle looms. Abstract— In India the textile industry is growing very fast. Conventional shuttle looms are mainly used during the Most of the earlier established textile industries are using weaving process in the industry. All these shuttle looms are conventional shuttle looms for the production of the cloth. But the too old. In these present conventional shuttle looms, it is advancement in the technology made the textile industry more competitive. The effective usage of the new methods of the necessary to pass a shuttle weighing around half a kilogram weaving technology, which is more energy efficient, makes the through the warp shed to insert a length of weft yarn which production more economical. It is found out that the usage of the weighs only few grams. The shuttle has to be accelerated conventional looms badly affects the cloth production. This study rapidly at the starting of picking cycle and also to be focuses on identifying the problems associated with the low decelerated, stopped abruptly at the opposite end. This production by the shuttle loom and suggesting suitable methods process creates heavy noise and shock and consumes by which these problems can be reduced. considerable energy. Beat-up is done by slay motion which again weighs a few hundred kilograms. The wear life of the Index Terms—Greige Fabric Picks, Rapier Loom, Shuttle Loom. -
Model: R880DX
(JuLiBao) HuZhou Hyundai Textile Machinery CO.,LTD OFFER Model: R880DX Tel: 0086 572 3972043 Fax: 0086 572 3979298 Website: www.hzhyundai.com Email: [email protected] Address: No.88, JingYi Road, WuXing District, HuZhou City, ZheJiang Provience, China HUZHOU HYUNDAI TEXTILE MACHINERY CO.,LTD No.88, Jing Yi Road, Wuxing Street, Huzhou city, Zhejiang Province, China TEL:+86 572-3972043 3975858 FAX:+86 572-3979298 Model: JLB-R880DX (JuLiBao) Label Weaving Machine Model: JuLiBao R880DX HUZHOU HYUNDAI TEXTILE MACHINERY CO.,LTD TEL:+86 572-3972043 3975858 FAX:+86 572-3979298 HUZHOU HYUNDAI TEXTILE MACHINERY CO.,LTD No.88, Jing Yi Road, Wuxing Street, Huzhou city, Zhejiang Province, China TEL:+86 572-3972043 3975858 FAX:+86 572-3979298 Model: JLB-R880DX Machine Configuration Base Loom --Loom:Itema R880 Rapier loom --Speed: 500rpm --Working Width:1600mm --Cycle numbers:8 repeats for taffeta(1 repeats=20cm) --Weft density adjustment:adjust in the range between 5 to 200picks/ cm --Take-up:electronic take-up --Let-off:Microprocessor control electronic let-off device with tension device --Weft tension:Double-twist electronic weft storage device adjustment --Weft searching system:Electronic automatic detecting weft finder --Weft selector:8 (up to 12) color electronic controlled color selector --Beam diameter:800mm --Cloth roller diameter:600mm(max) --Main motor Power:7.5kw(max) Jacquard --Model:STAUBLI DX --Hooks:1152 hooks(standard) --Control System:JC7 Electronic control system --Power:0.8KW --Weight:800KG --Jacquard support frame:Using double -
UPDATE November 2012
UPDATE November 2012 THE TREASURER has asked to remind you that by the time you receive this ‘UPDATE’ your affiliation fees should have been paid. By the middle of October only half the guilds had paid. Please help Jenifer to get the accounts done on time by paying now if you haven’t already done so. Many Thanks. THE COPY DATE for THE JOURNAL Spring Edition i.e. March is 9th December. Please send copy to [email protected] asap. This request has reached me so I will pass it on........ My name is Gordon MacDonald and I live on the Isle of Lewis in Scotland and would like to take up weaving Harris Tweed, but the problem is obtaining a loom, either new or second hand. I have found a company, Griffith, which manufactures a suitable loom that will weave both double width and single width fabric, but requires an order for 16 individual looms before manufacture will start.As there is a limited population on the island I am including your association in the hope that some of your members or their contacts may have an interest in purchasing a new loom. Each individual would have to contact the manufacturer directly to take the order process forward, but I am hopeful that the target can be reached and new looms produced for a new generation of weavers. I have attached the information sheet that I have received from Griffith. Could you please circulate this to any affiliated guilds of weavers Thank you for your time Gordon MacDonald 5 Lewis St Stornoway Isle of Lewis HS1 2JF Mobile: 07718898115 Home: 01851 705142 Email: [email protected] ******************************************************************************** ************************************ Dear All Please find attached brochure for the Griffith Rapier loom. -
Weaving Machine
Weaving Machine Kazuhide Chikaoka and Ryuji Shintani* *Industrial Research Institute of Ishikawa, Kanazawa 1. Introduction The 6th OTEMAS was a very impressive show. In the weaving machine, 76 machines of 18 companies were exhibited as shown in Table 1. It was very interesting that companies of Korea and Indonesia exhibited first. Table 2 Fig. 1 The change of mean loom speed shows a comparison of the exhibits with the previous OTEMAS. From these tables, it is found that features of the 6th OTEMAS are as follows. 1) The number of exhibited looms decreased by 8, but the number of companies increased by 3. 2) The air jet loom (AJL) decreased by 15, and the companies also decreased by 4. 3) The flexible rapier loom (FRL) increased by 9, and the companies also increases by 4. 4) The rigid rapier looms (RRL) decreased. 5) The companies of Korea and Indonesia first exhibited water jet loom (WJL). 6) The multi-phase looms (ML) that were very impressive Reed Width cm in the ITMA '95 were exhibited. Fig. 2 Weft insertion rate of exhibited AJLs 2. Productivity Table 3 shows the maximum values of reed width, speed and weft insertion rate (WIR) in the OTEMAS. Figure 1 indicates the change of loom speed in the International Shows. It is clear that the productivity of all kinds of weaving machines remains on the same line or show a slowdown and there is no longer the speed race of weaving machine companies. In the wide width looms, the productivity is looking up. Figures 2 and 3 show the relationships between reed width and weft insertion rate in the AJLs and the FRLs. -
Basic of Textiles
BASIC OF TEXTILES BFA(F) 202 CC 5 Directorate of Distance Education SWAMI VIVEKANAND SUBHARTI UNIVERSITY MEERUT 250005 UTTAR PRADESH SIM MOUDLE DEVELOPED BY: Reviewed by the study Material Assessment Committed Comprising: 1. Dr. N.K.Ahuja, Vice Chancellor Copyright © Publishers Grid No part of this publication which is material protected by this copyright notice may be reproduce or transmitted or utilized or store in any form or by any means now know or here in after invented, electronic, digital or mechanical. Including, photocopying, scanning, recording or by any informa- tion storage or retrieval system, without prior permission from the publisher. Information contained in this book has been published by Publishers Grid and Publishers. and has been obtained by its author from sources believed to be reliable and are correct to the best of their knowledge. However, the publisher and author shall in no event be liable for any errors, omission or damages arising out of this information and specially disclaim and implied warranties or merchantability or fitness for any particular use. Published by: Publishers Grid 4857/24, Ansari Road, Darya ganj, New Delhi-110002. Tel: 9899459633, 7982859204 E-mail: [email protected], [email protected] Printed by: A3 Digital Press Edition : 2021 CONTENTS 1. Fiber Study 5-64 2. Fiber and its Classification 65-175 3. Yarn and its Types 176-213 4. Fabric Manufacturing Techniques 214-260 5. Knitted 261-302 UNIT Fiber Study 1 NOTES FIBER STUDY STRUCTURE 1.1 Learning Objective 1.2 Introduction 1.3 Monomer, Polymer, Degree of polymerization 1.4 Student Activity 1.5 Properties of Fiber: Primary & Secondary 1.6 Summary 1.7 Glossary 1.8 Review Questions 1.1 LEARNING OBJECTIVE After studying this unit you should be able to: ● Describe the Natural Fiber. -
12.2% 122,000 135M Top 1% 154 4,800
We are IntechOpen, the world’s leading publisher of Open Access books Built by scientists, for scientists 4,800 122,000 135M Open access books available International authors and editors Downloads Our authors are among the 154 TOP 1% 12.2% Countries delivered to most cited scientists Contributors from top 500 universities Selection of our books indexed in the Book Citation Index in Web of Science™ Core Collection (BKCI) Interested in publishing with us? Contact [email protected] Numbers displayed above are based on latest data collected. For more information visit www.intechopen.com 3 The Physical Properties of Woven Fabrics for Emotional Garment According to the Weaving Loom Characteristics Seung Jin Kim and Hyun Ah Kim School of Textiles, Yeungnam University, Gyeongsan, Korea Institute for Knit Industry, Iksan, Korea 1. Introduction Many efforts for making good quality fabrics for emotional garment have been performed by SME weavers and finishers. And weaving machinery companies are researching about loom mechanism applied by low warp and filling tensions and loom mechanism for good quality fabrics. The fabric defects complained by garment manufacturers are stop marks, streaky phenomena on the warp direction, thickness variation and color differences between edges on the right and left sides of the fabrics, which are partly due to the tension variation of warp and filling directions. Therefore, many researches(Basu, 1987; Islam & Bandara, 1996, 1999) related to the fabric defects and weaving loom mechanism were carried out and many patents related to the loom were presented by loom makers. Many researches related to the warp and filling tensions during weaving were performed with relation to the fabric defects. -
Identifying Strengths of Polylon Based Woven Fabric As an Automotive Passive Restraint System Fabric
ISSN(Online) :2319-8753 ISSN (Print) : 2347-6710 International Journal of Innovative Research in Science, Engineering and Technology (An ISO 3297: 2007 Certified Organization) Vol. 4, Issue 9, September 2015 Identifying Strengths of Polylon Based Woven Fabric as an Automotive Passive Restraint System Fabric Dr. Tasnim N. Shaikh1, Dr. S. B. Chaudhari2 and Hiren Rasania3 Associate Professor, Dept. of Textile Engineering, Faculty of Technology & Engineering, The M.S. University of Baroda, Vadodara, Gujarat, India1 Assistant Professor, Dept. of Textile Engineering, Faculty of Technology & Engineering, The M.S. University of Baroda, Vadodara, Gujarat, India2 P.G. Student, Dept. of Textile Engineering, Faculty of Technology & Engineering, The M.S. University of Baroda, Vadodara, Gujarat, India3 ABSTRACT: Airbag is an automotive safety restraint system, consisting of a flexible fabric envelope designed to inflate rapidly during an automobile collision. Its purpose is to cushion occupants during a crash and provide protection to their bodies when they strike interior objects and lower the number and seriousness of injuries by reducing the force exerted at any point on the body. Important fabric characteristics needed to meet these objectives of an airbag are high impact resistance and tearing strength, low air permeability, faster unfolding of the airbag well at the time of collision and high heat resistance for preventing damage to and rupture of the airbag itself, and flexibility for reducing the impact provided to occupants. Even though costlier and difficult to manufacture, being Nylon 6, 6 possess all these desired characteristics remains the material of the choice since long. Polylon is the newly introduced composite yarn of Nylon 6 and High Tenacity Polyester in the market. -
Weaving Books and Monographs
Tuesday, September 10, 2002 Page: 1 ---. 10 Mujeres y Textil en 3d/10 Women and Textile Into 3. [Mexico City, Mexico: Universidad Nacional Autonoma de Mexico. Galeria Aristos, 1975], 1975. ---. 10 Mujeres y Textil en 3d/10 Women and Textile Into 3. [Mexico City, Mexico: Universidad Nacional Autonoma de Mexico. Galeria Aristos, 1975], 1975. ---. 100 Jahre J. Hecking; Buntspinnerei und Weberei. Wiesbaden, Verlag f?r Wirtschaftspublizistik Bartels, 1958. ---. 100 Years of Native American Arts: Six Washington Cultures. [Tacoma, Washington: Tacoma Art Museum, 1988], 1988. ---. 1000 [i.e. Mil] Años de Tejido en la Argentina: [Exposici?n] 24 de Mayo Al 18 Junio de 1978. Buenos Aires: Ministerio de Cultura y Educaci?n, Secretaría de Cultura, Instituto Nacional de Antropología, 1978. ---. 1000 Years of Art in Poland. [London, Great Britain: Royal Academy of Arts, 1970], 1970. ---. 101 Ways to Weave Better Cloth: Selected Articles of Proven Interest to Weavers Chosen from the Pages of Textile Industries. Atlanta, GA.: Textile Indistries, 1960. ---. 125 Jahre Mech. Baumwoll-Spinnerei und Weberei, Augsburg. [Augsburg, 1962. ---. 1977 HGA Education Directory. West Hartford, CT: Handweavers Guild of America, 1978. ---. 1982 Census of Manufactures. Preliminary Report Industry Series. Weaving Mills. [Washington, DC: U.S. Dept. of Commerce, Bureau of, 1984. ---. 1987 Census of Manufactures. Industry Series. Weaving and Floor Covering Mills, Industries 2211, 2221, 2231, 2241, and 2273. Washington, DC: U.S. Dept. of Commerce, Bureau of, 1990. ---. 1987 Census of Manufactures. Preliminary Report. Industry Series. Weaving and Floor Covering Mills: Industries 2211, 2221, 2241, and 2273. [Washington, DC: U.S. Dept. of Commerce, Bureau of, 1994. ---. 1992 Census of Manufactures. -
Is a Close-Fitting Sleeveless Garment Originally Designe
69134-ECF-W_409-450.qxd 8/24/2004 6:20 AM Page 409 W WAFFLE-WEAVE. See Weave, Jacquard. Double-breasted waistcoats were the most popular style during the first few decades of the eighteenth cen- tury and featured small pockets with flaps. By the mid- dle of the century, rather than following the older style WAISTCOAT The waistcoat, or vest (as it is known of having cuff-length sleeves, the majority of waistcoats in the United States), is a close-fitting sleeveless garment were sleeveless; skirts were much shorter and by 1790 originally designed for men that buttons (or occasionally were cut square to the waist. Toward 1800, decorated zips) down the front to the waist. Produced in either sin- single-breasted waistcoats with small lapels became fash- gle or double-breasted styles, the waistcoat is designed to ionable; fabrics with horizontal or vertical stripes were be worn underneath a suit or jacket, although it does not particularly favored, especially if the waistcoat was fin- necessarily have to match. Similar garments are worn by ished with a silk trim. women. By 1800, the waistcoat had become an increasingly decorative and flamboyant addition to the male wardrobe. History Through various style trends at the time, the overriding Originating in Persia, waistcoats first became fashionable principle was that as long as a waistcoat was highly con- in the middle of the seventeenth century. The new style spicuous, ostentatious, and embroidered, it was deemed was noticed by Samuel Pepys in 1666: “The King hath fashionable. Single-breasted, double-breasted, waist- … declared his resolution of setting a fashion for clothes length, square-cut, roll-collared, low stand-collared and which he will never alter,” he wrote in his diary. -
DETAILED PROJECT REPORT on AUTO LOOM / RAPIER LOOM (8 Nos.) (SOLAPUR TEXTILE CLUSTER)
DETAILED PROJECT REPORT ON AUTO LOOM / RAPIER LOOM (8 Nos.) (SOLAPUR TEXTILE CLUSTER) Bureau of Energy Efficiency Prepared By Reviewed By AUTO LOOM/RAPIER LOOM (8 Nos.) SOLAPUR TEXTILE CLUSTER BEE, 2010 Detailed Project Report on Auto Loom/Rapier Loom (8 Nos.) Textile SME Cluster, Solapur, Pune, Maharashtra (India) New Delhi: Bureau of Energy Efficiency; Detail Project Report No. : SLP/TXT/AL8/14 For more information Bureau of Energy Efficiency (BEE) Telephone +91-11-26179699 (Ministry of Power, Government of India) Fax +91-11-26178352 4th Floor, Sewa Bhawan Websites : www.bee-india.nic.in R. K. Puram, New Delhi – 110066 Email: [email protected]/[email protected] Acknowledgement We sincerely appreciate the efforts of industry, energy auditors, equipment manufacturers, technology providers, consultants and other experts in the area of energy conservation for joining hands with Bureau of Energy Efficiency (BEE), Ministry of Power, and Government of India for preparing the Detailed Project Report (DPR) under BEE SME Program in SMEs clusters. We appreciate the support of suppliers/vendors for providing the adoptable energy efficient equipments/technical details to the SMEs. We have received very encouraging feedback for the BEE SME Program in various SME Clusters. Therefore, it was decided to bring out the DPR for the benefits of SMEs. We sincerely thank the officials of BEE, Executing Agencies and ISTSL for all the support and cooperation extended for preparation of the DPR. We gracefully acknowledge the diligent efforts and commitments of all those who have contributed in preparation of the DPR. Contents List of Annexure vii List of Tables vii List of Figures viii List of Abbreviation viii Executive summary ix About BEE’S SME program x 1 INTRODUCTION ....................................................................................................... -
Rapier Loom Weaver
Contents Sr No Contents Page no. 1. Textiles terms and definitions 1 2. Weaving 1 3. Identification of parts 2 4. Control panel 5 5. Motions of loom 5 6. Identification of reason of loom stop 8 7. Weavers knot 8 8. Fabric defects 10 9. Loom patrolling 11 10. Patrol controls 13 11. Contingencies 16 12. Fabric defects 18 13. Instructions for shift change 20 14. Operations for rapier loom 22 1. Basic Textiles Terms Yarn: A continuous strand of fibers/filament, twisted /non twisted, it is basic raw material for weaving. Type of Yarns: single yarn, double or multi fold yarn, spun yarn & filament yarn etc. Yarn count: the yarn count is a numerical expression which defines it’s fineness or coarseness. Yarn count: Indirect system: English count (Ne), Worsted Count etc. i.e. Higher the yarn number , finer the yarn. Direct System: Tex, Denier i.e. Higher the yarn number , Coarser the yarn. 2. Weaving Weaving is a process of fabric production in which two distinct sets of yarns are interlaced at right angles to each other to form a fabric or cloth. The lengthwise yarns are called the warp yarn and the widthwise yarns are the weft yarn. Selvedge: The length wise running edges of woven fabric are known as selvedges. It prevents unraveling of warp yarns. Sequence of Operations In Weaving Warping Sizing Drawing in Weaving Page No 1 RSA DOCUMENT Version No.01 3. Identification of Rapier Loom Parts Page No 2 RSA DOCUMENT Version No.01 Types of Rapier Looms There are two types of Rapier loom Rigid Rapier loom Flexible Rapier Loom Single Rigid Rapier Page No 3 RSA DOCUMENT Version No.01 Double rigid Rapier Double Flexible Rapier Page No 4 RSA DOCUMENT Version No.01 Control panel: It is display panel provided on the machine to function various operations to perform and control such as; design loading, lifting of heald frames, jacquard and dobby operation, Motions of loom Primary motions: Shedding motion: Shedding separates the warp threads normally into two layers for the insertion of a pick. -
Recent Developments in Rapier Weaving Machines in Textiles
American Journal of Systems Science 2012; 1(1): 7-16 DOI: 10.5923/j.ajss.20120101.02 Recent Developments in Rapier Weaving Machines in Textiles Subhankar Maity1, Kunal Singha1,*, Mrinal Singha2 1Department of Textile Technology, Panipat Institute of Engineering & Technology, Harayana, India 2Department of Pharmaceutical Chemistry, CU Shah College of Pharmacy & Research, Gujarat, India Abstract This paper reviews the recent developments in rapier weaving and addresses the challenges that face the weaving industry. The paper sheds the light on how the weaving machine manufacturers and woven fabric producers might strengthen the weaving industry by further advanced the rapier technology with the help of electro-mechanics, electronics, microprocessors, information technology and their application to the production of woven fabrics. Keywords Rapier, Electro-Mechanics, Electronics, Microprocessors, Information Technology, Woven Technology Smith of Salford was granted a patent to eliminate the shuttle. 1. Introduction Subsequent patents were taken out by Phillippe and Maurice in 1855, W.S. Laycock in 1869, W.Glover in 1874[7]. Rigid Rapier weaving today exists in diversified forms. During rapiers were invented in 1870 and perfected by O. Hal- the last two decades the developments in rapier weaving lensleben in 1899. The main breakthrough came in 1922 have been carried out in a rapid continuous way. Rapier when John Gabler invented principle of loop transfer in the weaving machine produces top- quality fabrics from spun middle of the shed [8-10]. Flexible rapiers of the type used yarns such as cotton-wool, camel hair, silk, synthetic fibers today were proposed in 1925 by R.G.Moya of Barcelona, and fancy yarns.