United States Patent Office Patented May 1, 1962 2 Event, a Test Run Suffices to Indicate a Time Sufficient to 3,032,389 Solubilize the Lithium Content
Total Page:16
File Type:pdf, Size:1020Kb
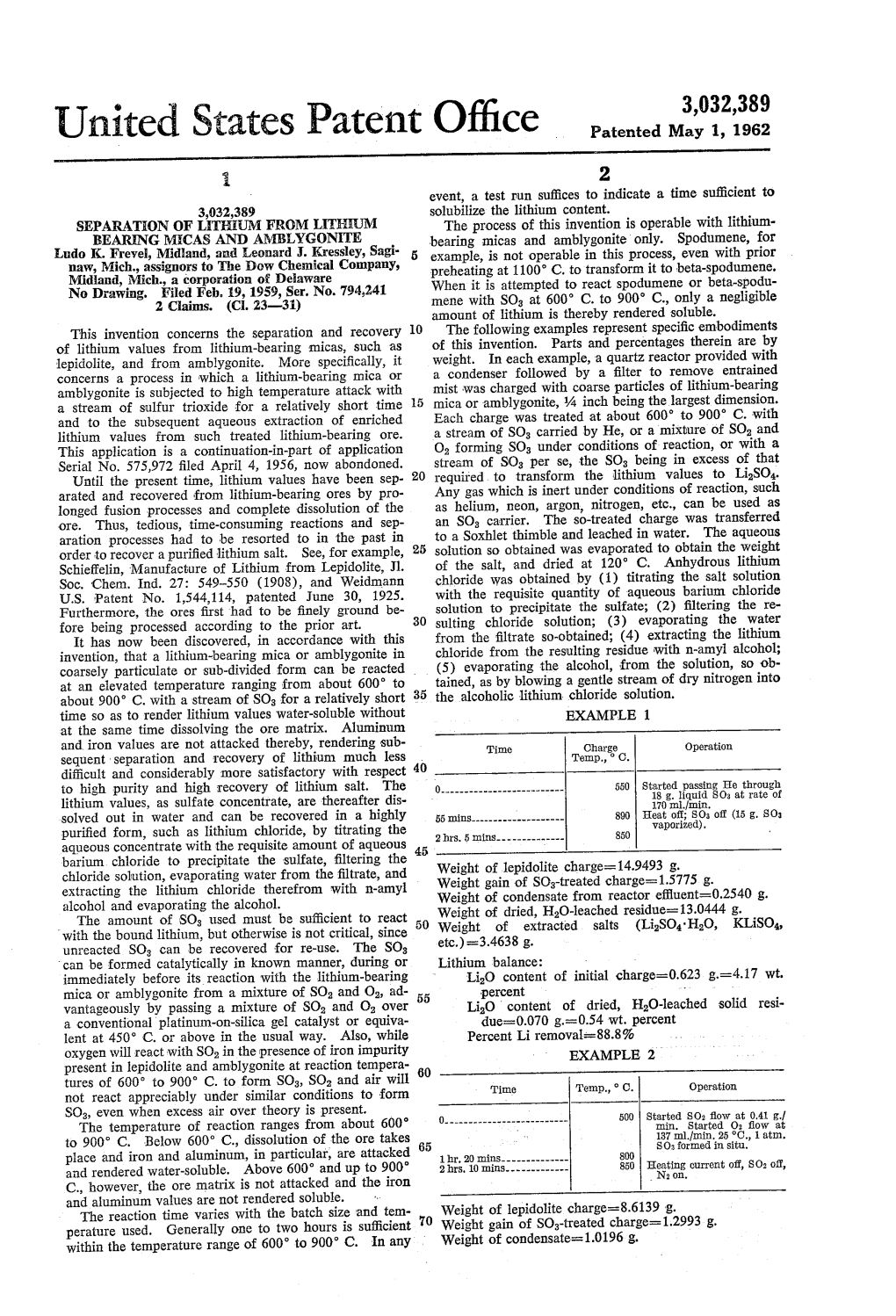
Load more
Recommended publications
-
Presentation Materials
Annual General Meeting 25 November 2016 Creative Resources Leadership Overview § Lepidico is a well funded ASX-listed lithium exploration and development company with an experienced management team § Lepidico’s strategic objective is to become a sustainable lithium producer with a portfolio of assets and pipeline of projects § Lepidico’s exploration initiatives largely focus on hard rock minerals that prior to L-Max® were not traditional sources of lithium § Lepidico is differentiated by having successfully produced lithium carbonate and a suite of by-products from non-traditional hard rock lithium bearing minerals using its patented L-Max® process technology § Lepidico provides exposure to a portfolio of lithium exploration assets through its wholly owned properties, JV’s and IP licence agreements in Asia, Australia, Canada, Europe and South America § At 30 September 2016 Lepidico had A$3.0M in cash and no debt 2 New sources of lithium § Micas and phosphates have been largely overlooked as a source of lithium as no commercially viable process was available to extract the lithium and process through to lithium chemicals prior to L-Max® § Lithium bearing micas Lepidolite and Zinnwaldite contain up to 5% Li2O and like spodumene, are hosted in pegmatites § Lepidolite and Zinnwaldite often occur with tin and tantalum bearing minerals as well as with spodumene § Lithium phosphates such as Amblygonite contain up to 10% Li2O Lepidolite (light purple) Zinnwaldite (dArk grey) Ambygonite/MontebrAsite K(Li,Al,Rb)3(Al,Si)4O10(F,OH)2 KLiFeAl(AlSi3)O10(OH,F)2 -
Lithium 2017
2017 Minerals Yearbook LITHIUM [ADVANCE RELEASE] U.S. Department of the Interior September 2020 U.S. Geological Survey Lithium By Brian W. Jaskula Domestic survey data and tables were prepared by Annie Hwang, statistical assistant. In the United States, one lithium brine operation with an cobalt oxide and 2,160 kg of lithium-nickel-cobalt-aluminum associated lithium carbonate plant operated in Silver Peak, oxide (Defense Logistics Agency Strategic Materials, 2017). At NV. Domestic and imported lithium carbonate, lithium yearend 2017, the NDS held 540 kg of lithium-cobalt oxide and chloride, and lithium hydroxide were consumed directly 1,620 kg of lithium-nickel-cobalt-aluminum oxide. in industrial applications and used as raw materials for downstream lithium compounds. In 2017, lithium consumption Production in the United States was estimated to be equivalent to The U.S. Geological Survey (USGS) collected domestic 3,000 metric tons (t) of elemental lithium (table 1) [16,000 t production data for lithium from a voluntary canvass of the of lithium carbonate equivalent (LCE)], primarily owing to only U.S. lithium carbonate producer, Rockwood Lithium Inc. demand for lithium-based battery, ceramic and glass, grease, (a subsidiary of Albemarle Corp. of Charlotte, NC). Production pharmaceutical, and polymer products. In 2017, the gross weight and stock data collected from Rockwood Lithium were withheld of lithium compounds imported into the United States increased from publication to avoid disclosing company proprietary data. by 7% and the gross weight of exports increased by 29% from The company’s 6,000-metric-ton-per-year (t/yr) Silver Peak those in 2016. -
A Review of Lithium Occurrences in Africa
A Review of Lithium occurrences in Africa Paul Nex, Kathryn Goodenough, Richard Shaw and Judith Kinnaird Lithium occurrences and exploration activity in Africa are dominated by pegmatite occurrences . Greenbushes, Australia No known brine resources as yet, Mineral Formula although Spodumene LiAl(SiO3)2 Botswana is Petalite LiAlSi4O10 being Eucryptite LiAlSiO4 investigated: Amblygonite (Li,Na)AlPO (F,OH) (by Lithium 4 Consolidated Mineral Lepidolite K(Li,Al)3(Al,Si,Rb)4O10(F,OH) Exploration Ltd-ASX) Pegmatites:typically granitic, enriched in incompatible elements, occurrences correlate with times of collisional orogeny and supercontinent assembly. Pegmatite classification needs reworking, however two types of interest - LCT: Lithium-caesium-tantalum NYF: Niobium-yttrium-fluorine Rubicon (Namibia) Bikita (Zimbabwe) Two dominant genetic models: 1. Products of the fractionation of a parental granite. 2. Products of low volume partial melting of metasediments during post-collisional orogenic collapse associated with decompression Nigeria: Pegmatites are ~probably younger than 560 Ma. Contenders for parental granites are 640-600 Ma Recent research in Norway (Muller et al 2017, or 60-580 Ma “thousands of pegmatites without parental granites”), NW Scotland, Nigeria and Namibia suggests that the low volume partial melting model for the genesis of granitic pegmatites is more prevalent than previously appreciated. In Namibia, potential parental granites are ~25 Ma older than the pegmatites and are deformed while the pegmatites are undeformed Most -
~Ui&£R5itt! of J\Rij!Oua
Minerals and metals of increasing interest, rare and radioactive minerals Authors Moore, R.T. Rights Arizona Geological Survey. All rights reserved. Download date 06/10/2021 17:57:35 Link to Item http://hdl.handle.net/10150/629904 Vol. XXIV, No.4 October, 1953 ~ui&£r5itt! of J\rij!oua ~ul1etiu ARIZONA BUREAU OF MINES MINERALS AND METALS OF INCREASING INTEREST RARE AND RADIOACTIVE MINERALS By RICHARD T. MOORE ARIZONA BUREAU OF MINES MINERAL TECHNOLOGY SERIES No. 47 BULLETIN No. 163 THIRTY CENTS (Free to Residents of Arizona) PUBLISHED BY ~tti£ll~r5itt! of ~rh!Omt TUCSON, ARIZONA TABLE OF CONTENTS INTRODUCTION 5 Acknowledgments 5 General Features 5 BERYLLIUM 7 General Features 7 Beryllium Minerals 7 Beryl 7 Phenacite 8 Gadolinite 8 Helvite 8 Occurrence 8 Prices and Possible Buyers ,........................................ 8 LITHIUM 9 General Features 9 Lithium Minerals 9 Amblygonite 9 Spodumene 10 Lepidolite 10 Triphylite 10 Zinnwaldite 10 Occurrence 10 Prices and Possible Buyers 10 CESIUM AND RUBIDIUM 11 General Features 11 Cesium and Rubidium Minerals 11 Pollucite ..................•.........................................................................., 11 Occurrence 12 Prices and Producers 12 TITANIUM 12 General Features 12 Titanium Minerals 13 Rutile 13 Ilmenite 13 Sphene 13 Occurrence 13 Prices and Buyers 14 GALLIUM, GERMANIUM, INDIUM, AND THALLIUM 14 General Features 14 Gallium, Germanium, Indium and Thallium Minerals 15 Germanite 15 Lorandite 15 Hutchinsonite : 15 Vrbaite 15 Occurrence 15 Prices and Producers ~ 16 RHENIUM 16 -
A Review of Rare-Element (Li-Cs-Ta) Pegmatite Exploration Techniques for the Superior Province, Canada, and Large Worldwide Tantalum Deposits
Exploration and Mining Geology, Vol. 14, Nos. 1-4, pp. 1-30, 2005 © 2006 Canadian Institute of Mining, Metallurgy and Petroleum. All rights reserved. Printed in Canada. 0964-1823/00 $17.00 + .00 A Review of Rare-Element (Li-Cs-Ta) Pegmatite Exploration Techniques for the Superior Province, Canada, and Large Worldwide Tantalum Deposits JULIE B. SELWAY, FREDERICK W. BREAKS Precambrian Geoscience Section, Ontario Geological Survey 933 Ramsey Lake Road, Sudbury, ON P3E 6B5 ANDREW G. TINDLE Department of Earch Sciences, Open University Milton Keynes, Buckinghamshire, UK MK7 6AA (Received February 16, 2004; accepted September 20, 2004) Abstract — Rare-element pegmatites may host several economic commodities, such as tantalum (Ta- oxide minerals), tin (cassiterite), lithium (ceramic-grade spodumene and petalite), and cesium (pollucite). Key geological features that are common to pegmatites in the Superior province of Ontario and Manitoba, Canada, and in other large tantalum deposits worldwide, can be used in exploration. An exploration project for rare-element pegmatites should begin with an examination of a regional geology map. Rare-element pegmatites occur along large regional-scale faults in greenschist and amphibolite facies metamorphic terranes. They are typically hosted by mafic metavolcanic or metasedimentary rocks, and are located near peraluminous granite plutons (A/CNK > 1.0). Once a peraluminous granite pluton has been identified, then the next step is to determine if the pluton is barren or fertile. Fertile granites have elevated rare element contents, Mg/Li ratio < 10, and Nb/Ta ratio < 8. They commonly contain blocky K-feldspar and green muscovite. Key fractionation indicators can be plotted on a map of the fertile granite pluton to determine the fractionation direction: presence of tourmaline, beryl, and ferrocolumbite; Mn content in garnet; Rb content in bulk K-feldspar; and Mg/Li and Nb/Ta ratios in bulk granite samples. -
Global Lithium Sources—Industrial Use and Future in the Electric Vehicle Industry: a Review
resources Review Global Lithium Sources—Industrial Use and Future in the Electric Vehicle Industry: A Review Laurence Kavanagh * , Jerome Keohane, Guiomar Garcia Cabellos, Andrew Lloyd and John Cleary EnviroCORE, Department of Science and Health, Institute of Technology Carlow, Kilkenny, Road, Co., R93-V960 Carlow, Ireland; [email protected] (J.K.); [email protected] (G.G.C.); [email protected] (A.L.); [email protected] (J.C.) * Correspondence: [email protected] Received: 28 July 2018; Accepted: 11 September 2018; Published: 17 September 2018 Abstract: Lithium is a key component in green energy storage technologies and is rapidly becoming a metal of crucial importance to the European Union. The different industrial uses of lithium are discussed in this review along with a compilation of the locations of the main geological sources of lithium. An emphasis is placed on lithium’s use in lithium ion batteries and their use in the electric vehicle industry. The electric vehicle market is driving new demand for lithium resources. The expected scale-up in this sector will put pressure on current lithium supplies. The European Union has a burgeoning demand for lithium and is the second largest consumer of lithium resources. Currently, only 1–2% of worldwide lithium is produced in the European Union (Portugal). There are several lithium mineralisations scattered across Europe, the majority of which are currently undergoing mining feasibility studies. The increasing cost of lithium is driving a new global mining boom and should see many of Europe’s mineralisation’s becoming economic. The information given in this paper is a source of contextual information that can be used to support the European Union’s drive towards a low carbon economy and to develop the field of research. -
Mineralogy of Pegmatites
University of New Hampshire University of New Hampshire Scholars' Repository New England Intercollegiate Geological NEIGC Trips Excursion Conference Collection 1-1-1960 Mineralogy of Pegmatites Peacor, D.R. Follow this and additional works at: https://scholars.unh.edu/neigc_trips Recommended Citation Peacor, D.R., "Mineralogy of Pegmatites" (1960). NEIGC Trips. 40. https://scholars.unh.edu/neigc_trips/40 This Text is brought to you for free and open access by the New England Intercollegiate Geological Excursion Conference Collection at University of New Hampshire Scholars' Repository. It has been accepted for inclusion in NEIGC Trips by an authorized administrator of University of New Hampshire Scholars' Repository. For more information, please contact [email protected]. TRIP E MINERALOGY OP PEGMATITES OP THE NEWRY HILL AREA, NEWRY, MAINE Leader: D. R. Peacor Meet at 8:15 A.M., Sunday, October 9, at the base of Plumbago Mountain, on Route 5. The meeting place is easily recognized through the Abbott farmhouse on the east side of the road, and the ore hopper and pas ture on the west side. The one mile long dirt road up to the mines was passable by car on July l6. If it has been washed out by October we will arrange for jeeps to ferry those few who are unable to walk to the top of the hill. INTRODUCTION There are five major quarries in the area (Pig. 1) and many smaller prospect pits. The mineral suites from three of these quarries are different and a unique opportunity to study a wide range of pegmatite minerals is available. -
Local Peralkalinity in Peraluminous Granitic Pegmatites. I. Evidence
This is the peer-reviewed, final accepted version for American Mineralogist, published by the Mineralogical Society of America. The published version is subject to change. Cite as Authors (Year) Title. American Mineralogist, in press. DOI: https://doi.org/10.2138/am-2021-7790. http://www.minsocam.org/ Revision 1 1 Local peralkalinity in peraluminous granitic pegmatites. I. Evidence 2 from whewellite and hydrogen carbonate in fluid inclusions 3 YONGCHAO LIU1,2, CHRISTIAN SCHMIDT2,*, AND JIANKANG LI1 4 1MNR Key Laboratory of Metallogeny and Mineral Assessment, Institute of Mineral Resources, 5 Chinese Academy of Geological Sciences, Beijing 100037, China 6 2GFZ German Research Centre for Geosciences, Telegrafenberg, 14473 Potsdam, Germany 7 *Corresponding author: [email protected] 8 9 ABSTRACT 10 Fluid inclusions in pegmatite minerals were studied using Raman spectroscopy to 11 determine the carbon species. Carbon dioxide is very abundant in the aqueous liquid and vapor − 12 phases. Occasionally, CH4 was found in the vapor. In the aqueous liquid, HCO3 was detected in 13 fluid inclusions in tantalite-(Mn) from the Morrua Mine and in late-stage quartz from the Muiâne 14 pegmatite and the Naipa Mine, all in the Alto Ligonha District, Mozambique. Moreover, we 15 observed a carbonate (calcite group) in fluid inclusions in garnet from the Naipa Mine and in 16 beryl from the Morrua Mine, both in the Alto Ligonha District, Mozambique, and a calcite-group 17 carbonate and whewellite [CaC2O4∙H2O] in fluid inclusions in topaz from Khoroshiv, Ukraine. 18 The occurrence of oxalate is interpreted to be due to a reaction of some form of carbon (possibly 19 CO or bitumen) with a peralkaline fluid. -
UNIVERSITY of LATVIA FACULTY of CHEMISTRY Doctoral Thesis
UNIVERSITY OF LATVIA FACULTY OF CHEMISTRY Doctoral thesis Artūrs Zariņš FORMATION, ACCUMULATION AND ANNIHILATION OF RADIATION-INDUCED DEFECTS AND RADIOLYSIS PRODUCTS IN ADVANCED TWO-PHASE CERAMIC TRITIUM BREEDER PEBBLES Supervisor: Leading researcher, Dr. chem. Gunta Ķizāne Scientific advisors: Dr. chem. Arnis Supe Dr. rer. nat. Regina Knitter RIGA 2018 ABSTRACT Advanced lithium orthosilicate (Li4SiO4) pebbles with additions of lithium metatitanate (Li2TiO3) as a secondary phase are suggested as a potential candidate for the tritium breeding in future nuclear fusion reactors. In this doctoral thesis, for the first time the formation, accumulation and annihilation of radiation-induced defects (RD) and radiolysis products (RP) in the Li4SiO4 pebbles with various contents of Li2TiO3 are analysed and described under the simultaneous action of 5 MeV accelerated electrons and high temperature. To exclude the effects from technological factors, which could affect the formation and accumulation of RD and RP in the Li4SiO4 pebbles during irradiation, the influence of the noble metals, the pebble diameter, the grain size and the chemisorption products on the radiolysis is analysed and evaluated. Key words: Nuclear fusion, tritium breeding, lithium orthosilicate, lithium metatitanate, radiation-induced defects, radiolysis products. 2 TABLE OF CONTENT ABBREVIATIONS ......................................................................................................................... 5 INTRODUCTION .......................................................................................................................... -
Initiation of Coverage
28 November 2018 CORPORATE SPONSORED - MARKETING COMMUNICATION MINING Corporate European Lithium Share Price 6.5p Initiation - One of Europe’s most advanced lithium projects European Lithium is seeking to develop the Wolfsberg lithium deposit in Austria. The company has a simple plan to produce a high-value, battery-grade lithium hydroxide Reuters/BBG NEX / ASX:EUR product which will have an immediate market in the industrial heart of Europe. The European Union and the car industry in Europe is well aware of its over reliance on Sector Mining lithium battery imports from Asia; and with environmental and business development Market Cap £31m plans combining with a massive expansion of Electric Vehicle (EV) production (and Shares in Issue 514m use) in Europe, will be keen, in our opinion, to secure supply from a domestic source. NAV p Wolfsberg is well-located and significantly advanced to benefit as one of the first-to- Gearing NA market lithium projects in the region. We see the biggest risk as access to capital, Interest Cover NA but are of the opinion that a strategic partner from regional industry might help as the project approaches final funding. We see fair value at 13p (AUD23c) using an Performance All-Share Sector appropriately risked discounted cash flow analysis. 1 month: 3 months: An investment in European Lithium provides investors with: 12 months: Exposure to the lithium market. We see strong fundamentals for the lithium High/Low high / low market. The supply response may be insufficient to fulfil the obvious growing demand. Long lead times to develop projects and the associated downstream conversion capacity together with difficult capital markets may keep the lithium price volatile and relatively high. -
Optimisation of Spodumene Flotation
The European Journal of Mineral Processing and Environmental Protection Vol.4, No.2, 1303-0868, 2004, pp. 130-135 Optimisation of spodumene flotation M. Menéndez*, A. Vidal, J. Toraño, M. Gent Escuela Técnica Superior de Ingenieros de Minas, Universidad de Oviedo C/ Independencia, 13, 33004 Oviedo, Spain Received 10 December 2002; accepted 15 March 2004 ABSTRACT Results of investigations into the optimum conditions for concentration of spodumene by anionic froth flotation are presented. Parameters investigated include: collector dosage; cell rotor velocity; feed pH, conditioning period, temperature, solids content, and reprocessing steps required to yield an optimum product. Results are based upon sequential testing of various values for each parameter while maintaining all others constant. These show that optimum conditions are attained with: the pulp at a pH of 7.5 to 9.8, 18% solids, 15°C and a 10min conditioning period; a cell rotor velocity of 1040rpm; and that an oleic acid concentration of 1.4kg/t as a collector is adequate. It was also found that under these operating conditions, no significant increase in grade could be achieved with more than two passes through cleaner cells. Analysis of these tests indicates that a product with an optimum lithia content and a calculated recovery of 96.24% may be achieved by the cleaning the rougher concentrate twice in conventional sub-aeration flotation cells. © 2004 SDU. All rights reserved. Keywords: Froth flotation; Operating parameters; Spodumene 1. INTRODUCTION Spodumene is an important mineral in the production of vitreous products. It is valued for reducing firing temperature and flux consumption, decreasing melt viscosity, increasing furnace throughput, improving forming characteristics, increasing product thermal shock resistance while serving as a bulk source of alumina and silica. -
Synthesis and Fluorine.Hydfoxyl Exchange in the Amblygonite Series
Caiwdian Mineralogist Vol. 14, pp. 357-363 (1976) SYNTHESISAND FLUORINE.HYDFOXYLEXCHANGE IN THE AMBLYGONITESERIES SPENCER E. LOH,|, ^rxn WLLIAM S. WISE Departmentof Geologicalsciences, university of california, santa Barbara, ca 9|106 ABSTRACT Souurernr, The amblygonite series includes the solid solution La s6rieamblygonite consiste en une solution solide between the end members, amblygonite, LiAIPO;F, entre les p6les extr6mes,I'amblygonite (LiAlpO4F) and montebrasite, LiAIPO4OH. The moit comrrion et la mont6brasite (LiAIPO4OH). La compositionla composition range. is between Ambl6 and Amb5o, plus courante que I'on retrouve dans les pqmatites where this series occurs in Li-rich pegmatites. richesen Li se situe entre Amble et Ambrol Ih com- The end members and four intermediate composi- positions limifss st quatre compositions interm6_ tions were synthesized by standard hydrothermal diaires ont 6t6 synttr6tis6espar voie hydrothermale d tochniques at 600'C and 2 kbar water pressure. All 6@'C et 2 kbar de pressiond'eau. Tous les six para_ six ell param€ters vary linearly across the com- mdtresde l4 maills varient de fagon linGaire. positional I-es ai_ range. Amblygonite cell dimensions arg mensionsde la maille de I'amblygonite sont, a 8.103, a p 5.103, b 7.221, c 5.5064, a L14"22" 98.54'. b7.22L,c 5.506[, aLl422t, p 98.b4',^y 6ZTfz'iww t 67'02'; and montebrasite, a 5.185, b 7.161, c mont6brasite,a 5.185,b Z.t6I, c 5.OOA, 5.040A, a ll2"I8" B 97"51" .t 67"52'. These !t c 112"18r, cell P 97%It, Les paramOtresae cescomposGs dimensions indicate that the unit cells of the pure purement!.97"52'.