Filed Aug. 28, 1968
Total Page:16
File Type:pdf, Size:1020Kb
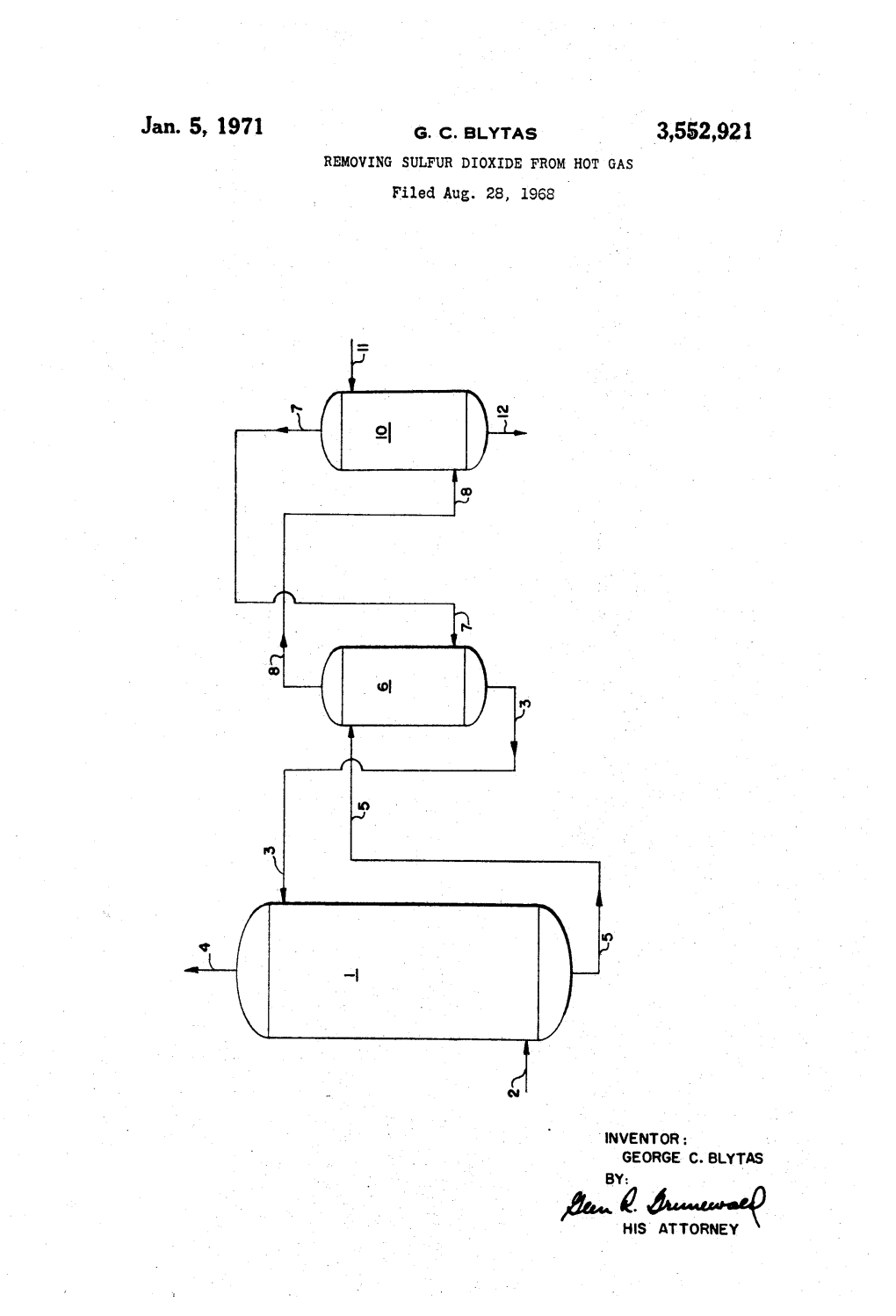
Load more
Recommended publications
-
DRY ACID Safety Data Sheet (SDS No
Safety Data Sheet (SDS No. 207) HASA DRY ACID HASA DRY ACID Safety Data Sheet Emergency 24 Hour Telephone: CHEMTREC 800.424.9300 Corporate Headquarters: Hasa Inc. P. O. Box 802736 Santa Clarita, CA 91355 Telephone 661.259.5848 Fax 661.259.1538 SECTION 1: CHEMICAL PRODUCT AND COMPANY IDENTIFICATION 1.1 Product Identification: 1.1.1 Product Name: HASA DRY ACID 1.1.2 CAS # : (Chemical Abstract Service) 7681-38-1 1.1.3 RTECS : (Registry of Toxic Effects VZ1860000 of Chemical Substances) 1.1.4 EINECS : (European Inventory of 231-665-7 Existing Commercial Substances) 1.1.5 Chemical Name: Sodium bisulfate 1.1.6 Chemical Formula: NaHSO 4 1.1.7 Chemical Family: Inorganic acid salt 1.1.8 Synonym: Sodium Acid Sulfate, Sodium Hydrogen Sulfate, Sodium Pyrosulfate. 1.2 Recommended Uses: It is used primarily to lower the pH of water for effective chlorination, including swimming pools and spas. 1.3 Company Identification: Hasa Inc. P. O. Box 802736 Santa Clarita, CA 91355 1.4 Emergency Assistance: CHEMTREC : 1-800-424-9300 (24 Hour Emergency Telephone) 1.5 Non -Emergency Assistance : 661-259-5848 (8 AM – 5 PM PST / PDT) Revision Date: 01/01/2015 (Supersedes previous revisions) Page 1 of 9 SECTION 2: HAZARD(S) IDENTIFICATION Safety Data Sheet (SDS No. 207) HASA DRY ACID Hazard Category Skin corrosion / irritation: Category 1 Acute Toxicity (oral): Category 4 Acute Toxicity (inhalation): Category 4 Symbol Signal Word DANGER Haza rd Statements Causes severe skin burns and eye damage. Harmful if inhaled. Harmful if swallowed. Precautionary Prevention Statements Do not breathe dusts or mists. -
Purification Method of Pemetrexed Salts,Sodium Salts and Disodium Salts
(19) & (11) EP 2 213 674 A1 (12) EUROPEAN PATENT APPLICATION published in accordance with Art. 153(4) EPC (43) Date of publication: (51) Int Cl.: 04.08.2010 Bulletin 2010/31 C07D 487/04 (2006.01) A61K 31/519 (2006.01) A61P 35/00 (2006.01) (21) Application number: 08844190.2 (86) International application number: (22) Date of filing: 21.10.2008 PCT/CN2008/072758 (87) International publication number: WO 2009/056029 (07.05.2009 Gazette 2009/19) (84) Designated Contracting States: • LIN, Meng AT BE BG CH CY CZ DE DK EE ES FI FR GB GR Chongqing 400061 (CN) HR HU IE IS IT LI LT LU LV MC MT NL NO PL PT • LIN, Bo RO SE SI SK TR Chongqing 400061 (CN) Designated Extension States: • YE, Wenrun AL BA MK RS Chongqing 400061 (CN) • QIN, Yongmei (30) Priority: 24.10.2007 CN 200710092879 Chongqing 400061 (CN) •DENG,Jie (71) Applicant: Chongqing Pharmaceutical Chongqing 400061 (CN) Research Institute Co., Ltd. Chongqing 400-061 (CN) (74) Representative: Epping - Hermann - Fischer Patentanwaltsgesellschaft mbH (72) Inventors: Ridlerstrasse 55 •LUO,Jie 80339 München (DE) Chongqing 400061 (CN) (54) PURIFICATION METHOD OF PEMETREXED SALTS,SODIUM SALTS AND DISODIUM SALTS + + (57) A method of purifying a salt of pemetrexed have a structure of formula (III) by salting-out, wherein if M 3 is H , + + + + + + + + + + then each of M1 and M2 is independently H , Li , Na or K , provided that both of them are not H ; if M3 is Li , Na + + + + + + or K , then each of M1 and M2 is independently Li , Na or K . -
SMALL-SCALE SYNTHESIS of LABORATORY REAGENTS with Reaction Modeling
SMALL-SCALE SYNTHESIS of LABORATORY REAGENTS with Reaction Modeling © 2011 by Taylor and Francis Group, LLC SMALL-SCALE SYNTHESIS of LABORATORY REAGENTS with Reaction Modeling LEONID LERNER Boca Raton London New York CRC Press is an imprint of the Taylor & Francis Group, an informa business © 2011 by Taylor and Francis Group, LLC CRC Press Taylor & Francis Group 6000 Broken Sound Parkway NW, Suite 300 Boca Raton, FL 33487-2742 © 2011 by Taylor and Francis Group, LLC CRC Press is an imprint of Taylor & Francis Group, an Informa business No claim to original U.S. Government works Printed in the United States of America on acid-free paper 10 9 8 7 6 5 4 3 2 1 International Standard Book Number: 978-1-4398-1312-6 (Hardback) This book contains information obtained from authentic and highly regarded sources. Reasonable efforts have been made to publish reliable data and information, but the author and publisher cannot assume responsibility for the validity of all materials or the con- sequences of their use. The authors and publishers have attempted to trace the copyright holders of all material reproduced in this publication and apologize to copyright holders if permission to publish in this form has not been obtained. If any copyright material has not been acknowledged please write and let us know so we may rectify in any future reprint. Except as permitted under U.S. Copyright Law, no part of this book may be reprinted, reproduced, transmitted, or utilized in any form by any electronic, mechanical, or other means, now known or hereafter invented, including photocopying, microfilming, and record- ing, or in any information storage or retrieval system, without written permission from the publishers. -
Screening Assessment for the Challenge Quartz 14808-60-7
Screening Assessment for the Challenge Quartz Chemical Abstracts Service Registry Number 14808-60-7 Cristobalite Chemical Abstracts Service Registry Number 14464-46-1 Environment Canada Health Canada June 2013 Screening Assessment CAS RN 14808-60-7, 14464-46-1 Synopsis Pursuant to section 74 of the Canadian Environmental Protection Act, 1999 (CEPA 1999), the Ministers of the Environment and of Health have conducted a screening assessment of quartz, Chemical Abstracts Service Registry Number1 14808-60-7 and cristobalite, Chemical Abstracts Service Registry Number 14464-46-1. These substances were identified as a high priority for screening assessment and included in the Challenge initiative under the Chemicals Management Plan. Quartz and cristobalite were identified as high priorities as they were considered to pose greatest potential for exposure of individuals in Canada and their respirable forms are classified by the International Agency for Research on Cancer as carcinogenic to humans (quartz and cristobalite) and by the National Toxicology Program as known human carcinogens (crystalline silica). These substances met the ecological categorization criteria for persistence, but not for bioaccumulation potential or inherent toxicity to aquatic organisms. According to information reported under Section 71 of CEPA 1999 for the year 2006, over 10 000 000 kg of quartz were manufactured, imported and used in Canada. Based on the results of the same survey, over 10 000 000 kg of cristobalite were manufactured and between 1 000 000 and 10 000 000 kg were imported and used in the year 2006. It should be noted that this quantity does not represent the total quantities of quartz and cristobalite in the market in Canada because response to the mandatory section 71 Notice was required only if the substance or product, mixture or manufactured item containing the substance, was composed of more than 5% respirable crystalline silica and was intended for use within a residence. -
Dry Acid 25Kg
Safety Data Sheet May 2019 1. Identification of the Substance and Supplier Product Name: SODIUM BISULPHATE Other Names: Sodium Bisulfate; Sodium Pyrosulfate; Sodium Hydrogen Sulfate; Sodium Acid Sulfate. Amtrade product Sodium Bisulphate 25kg, Bag [407097] description [& code]: Sodium Bisulphate (GW) 25kg, Bag [417343] Recommended Use: Raw material; Flux for decomposing minerals. Substitute for Sulfuric Acid in dyeing. Disinfectant. Manufacture of: Sodium Hydrosulfide; Sodium Sulfate; Soda alum. Liberating Carbon Dioxide in Carbonic Acid containing baths. Carbonizing wool. Manufacture of: magnesia cements; paper; soap; perfumes; industrial cleaners; metal pickling compounds. Animal feed additive. Supplier: Amtrade International Pty Ltd (ABN 49 006 409 936) Level 8 580 St Kilda Road Melbourne VIC 3004 Australia Tel: +61 3 9229 9229 Melbourne +61 2 9805 4200 Sydney Email: [email protected] Emergency Contact: 1800 033 111 (Australia - all hours) +61 3 9663 2130 (Australia - at Sea) 2. Hazards Identification Hazard classification: Eye Damage/Irritation: Category 1 Corrosive to Metals: Category 1 PICTOGRAM: CORROSION GHS Hazardous Yes No Chemical (AU): Signal Word: DANGER Hazard Statement: H318 Causes serious eye damage. H290 May be corrosive to metals. Prevention: P234 Keep only in original container. P260 Do not breathe dusts / mists. P280 Wear eye protection / face protection. P264 Wash hands and skin thoroughly after handling. Response: P302+352 IF ON SKIN: Wash with plenty of soap and water. P332+313 If skin irritation occurs: Get medical advice/attention. P305+351+338 IF IN EYES: Rinse cautiously with water for several minutes. Remove contact lenses, if present and easy to do. Continue rinsing. Amtrade BC26BW-0 SODIUM BISULPHATE Safety Data Sheet Page 1 of 7 P310 Immediately call a POISONS CENTER or doctor/physician. -
General Disclaimer One Or More of the Following Statements May Affect
General Disclaimer One or more of the Following Statements may affect this Document This document has been reproduced from the best copy furnished by the organizational source. It is being released in the interest of making available as much information as possible. This document may contain data, which exceeds the sheet parameters. It was furnished in this condition by the organizational source and is the best copy available. This document may contain tone-on-tone or color graphs, charts and/or pictures, which have been reproduced in black and white. This document is paginated as submitted by the original source. Portions of this document are not fully legible due to the historical nature of some of the material. However, it is the best reproduction available from the original submission. Produced by the NASA Center for Aerospace Information (CASI) FINAL REPORT on the project Molecular Orbital Studies in Oxidation: Sulfate Formation and Metal-Metal Oxide Adhesion NASA Grant No. NAG 3-341 i Covering the period 10-30-82 through 7-31-85 by Alfred B. Anderson (P.I.) Chemistry Department, Case Western Reserve University Cleveland, OH 44106 av fi r" ti p NE5-321 i4 (N ASI-Cji-'176070) MCLECULIR OBEITAL STUDIES IN OXIDATION: 5OLZAIE FORNAIICN AND SETAL-118TII OX:LE IDBES;UN Final R eport, 30 Oct. 1982 - 31 Jul. 1585 (Cafe hesteL.o UnclaE CSCL 11P G3/26 21933 Reserve UD iV-) 5 F HC &02 /!!P X01 • ^ ^ ^ 1^saf ^ ' Tht purpose of this project. was two-fold. The first was to %1 termine the chemical mechanisms for sulfate formation from sodium chloride and s^.ilfur trioxide, which is a produc` of jet fuel combustion. -
United States Patent Office Patented Feb
3,232,955 United States Patent Office Patented Feb. 1, 1966 2 oxygen oxidation of o-xylene or naphthalene which has 3,232,955 PRODUCTION OF PHTHALIC ANHYDRDE BY little or no sensitivity to sulfur. CATALYTEC OXDATION These and other objects are achieved by carrying out Helialist Nonnenmacher, Konstantin Andrussow, Max the oxydation of o-xylene or naphthalene to phthalican Appl, Anton Feinauer, and Juergen Haag, Ludwigs 5 hydride with oxygen or inert gases containing molecular hafen (Rhine), Alfred Helms, Ludwigshafen (Rhine)- Oxygen at a temperature of 250 to 420° C. by the use Edigheim, and Klaus Wiebusch, Ludwigshafen (Rhine), of a fluidized catalyst which comprises a highly porous car Germany, assignors to Badische Anilin- & Soda. rier material, especially silica gel having an inner sur Fabrik Aktiengesellschaft, Ludwigshafen (Rhine), Germany face of 200 to 400 m. per gram and a grain size of 10 NoDrawing. Filed Apr. 24, 1962, Ser. No. 189,701 O to 3,000 microns and which contains an active substance Clains priority, application Germany, Apr. 28, 1961, mixture of vanadium pentoxide, sodium pyrosulfate and Bg2,399; $62,310; Sept. 28, 1961, B 64,169; Nov.30, potassium pyrosulfate, the melting point of the mixture 1961, B 64,993 of sodium and potassium pyrosulfate being lower than - 9 Claims. (C. 260-346.4) that of potassium pyrosulfate and the said active sub 5 stance mixture being present in the pores of the carrier in This invention relates to the production of phthalic fused form under the reaction conditions. The total anhydride. More specifically it relates to the use of amount of vanadium pentoxide-pyrosulfate melt should catalysts which have not heretofore been used for the preferably be between 10 and 60% by weight of the Oxidation of naphthalene or xylene by means of air. -
Sodium Metabisulfite in Food Pdf
Sodium metabisulfite in food pdf Continue Sodium Metabisulfite Food Class Application of sodium metabisulfite in the sodium food industry Metabisulfite is widely used in the food industry. In addition to the bleaching effect, sodium metabisulfite also has the following functions: 1) Sodium metabisulfite in food has an anti-brown effect. Ensimatic browning often occurs in fruits, potato food. Sodium metabisulfite is a kind of reducing agent, has a strong inhibitory effect on the activity of oxidase polyphenols. 0.0001% sulfur dioxide can reduce 20% of enzyme activity, 0.001% sulfur dioxide can completely inhibit enzyme activity and can prevent enzyme browning; It can also consume oxygen in a food organization and has a decontamination effect. In addition, sulfitis and glucose can have additional effects, preventing glucose and amino acids in ammonia's reaction to ammonia to master the anti-browning function. 2) Sodium metabisulfite in food has an antiseptic effect. Sodium metabisulfite can play the role of an acidic preservative, nondiscipline sulphuric acid is thought to inhibit yeast, mold and bacteria. Inhibition of non-disciplined sulphuric acid for the colon bacillus is 1000 times stronger than hydrogen sulfide, 100 to 500 times stronger than beer yeast, 100 times stronger than a sheet of mold. The sulfur dioxide in acid has the most powerful anti-microorganism effects. 3) Sodium metabisulfite in food has the effect of weakening the machine, sodium metabisulfite can be used as a component of the weakening machine. 4) Sodium metabisulfite in food has an effect of resistance to oxidation. Sodium metabisulfite has a distinctive resistance effect. Sulphuric acid is a strong reducing agent, it can consume oxygen in the organization of fruits and vegetables, inhibit the activity of the oxidative enzyme, is effective to prevent oxidation and disturbance of vitamin C in fruits and vegetables. -
Safety Data Sheet CS: 1.7.2
Safety Data Sheet CS: 1.7.2 Page : 1 of 5 Infosafe No ™ 1CHBK Issue Date : November 2016 RE-ISSUED by CHEMSUPP Product Name : SODIUM BISULFATE Anhydrous Classified as hazardous 1. Identification GHS Product SODIUM BISULFATE Anhydrous Identifier Company Name CHEM-SUPPLY PTY LTD (ABN 19 008 264 211) Address 38 - 50 Bedford Street GILLMAN SA 5013 Australia Telephone/Fax Tel: (08) 8440-2000 Number Fax: (08) 8440-2001 Recommended use Flux for decomposing minerals ; substitute for sulfuric acid in dyeing ; disinfectant ; liberating CO2 in of the chemical and carbonic acid baths, in thermophores ; carbonizing wool ; to reduce alkalinity and pH in swimming pools ; restrictions on use manufacture of magnesia cements, paper, soap, perfumes, industrial and household cleaners, foods, silver and metal pickling compounds, sodium hydrosulfide, sodium sulfate and soda alum and laboratory reagent. Other Names Name Product Code SODIUM BISULFATE LR SL010 Sodium hydrogen sulfate, Sodium pyrosulfate, Sodium acid sulfate Other Information EMERGENCY CONTACT NUMBER: +61 08 8440 2000 Business hours: 8:30am to 5:00pm, Monday to Friday. Chem-Supply Pty Ltd does not warrant that this product is suitable for any use or purpose. The user must ascertain the suitability of the product before use or application intended purpose. Preliminary testing of the product before use or application is recommended. Any reliance or purported reliance upon Chem-Supply Pty Ltd with respect to any skill or judgement or advice in relation to the suitability of this product of any purpose is disclaimed. Except to the extent prohibited at law, any condition implied by any statute as to the merchantable quality of this product or fitness for any purpose is hereby excluded. -
MARLAP Manual Volume II: Chapter 13, Sample Dissolution (Pdf)
13 SAMPLE DISSOLUTION 13.1 Introduction The overall success of any analytical procedure depends upon many factors, including proper sample preparation, appropriate sample dissolution, and adequate separation and isolation of the target analytes. This chapter describes sample dissolution techniques and strategies. Some of the principles of dissolution are common to those of radiochemical separation that are described in Chapter 14 (Separation Techniques), but their importance to dissolution is reviewed here. Sample dissolution can be one of the biggest challenges facing the analytical chemist, because most samples consist mainly of unknown compounds with unknown chemistries. There are many factors for the analyst to consider: What are the measurement quality objectives of the program? What is the nature of the sample; is it refractory or is there only surface contamination? How effective is the dissolution technique? Will any analyte be lost? Will the vessel be attacked? Will any of the reagents interfere in the subsequent analysis or can any excess reagent be removed? What are the safety issues involved? What are the labor and material costs? How much and what type of wastes are generated? The challenge for the analyst is to balance these factors and to choose the method that is most applicable to the material to be analyzed. The objective of sample dissolution is to mix a solid or nonaqueous liquid sample quantitatively with water or mineral acids to produce a homogeneous aqueous solution, so that subsequent separation and analyses may be performed. Because very few natural or organic materials are water-soluble, these materials routinely require the use of acids or fusion salts to bring them into solution. -
United States Patent Office Patented Oct
3,281,225 United States Patent Office Patented Oct. 25, 1966 2 One such material that has been commonly used is METHOD oF INCREASNG3,281.225 iHE DURABILITY OF sulfur trioxide gas, usually introduced into or formed GLASSWARE within an annealing lehr wherein the glassware is being James J. Hazdra, Joliet, and Arthur S. Gunderson, Lock treated so as to create an acid gas atmosphere therein. port, Ill., assignors to Brockway Glass Company, Inc., 5 However, with this method of utilizing sulfur trioxide Brockway, Pa. gas, it has been very difficult to effectively reach the in No Drawing. Filed Sept. 30, 1965, Ser. No. 491,902 terior surfaces of glass containers, since the containers 8 Claims. (C. 65-30) enter the lehr filled with air which must be displaced. A further practical consideration is that the gas is ex This application is a continuation-in-part of applica 0 tremely hazardous and difficult to confine in plant opera tion Serial No. 157,839 filed December 7, 1961, and now tional equipment, which limits its commercial use in the abandoned. above form. Sometimes, when small glassWare con The present invention relates to a method of treating tainers for which the interior surfaces must have their glassware so as to remove surface alkalinity therefrom. alkalinity reduced, sulfur either in the form of pellets The invention is more particularly related to an im or powder has been introduced therein. The sulfur upon proved method of removing surface alkalinity from the heating and in the presence of oxygen will react to form interior surfaces of glass containers such as are to be sulfur trioxide. -
Danh Mục Số Cas A
CÔNG TY CỔ PHẦN CÔNG NGHIỆP VIỆT XUÂN NHÀ CUNG CẤP KHÍ HELI, KHÍ METAN, KHÍ SF6, KHÍ PROPAN Số 80B Nguyễn Văn Cừ - Long Biên - Hà Nội - Việt Nam www.vietxuangas.com.