US 2012/0082610 A1 Channon (43) Pub
Total Page:16
File Type:pdf, Size:1020Kb
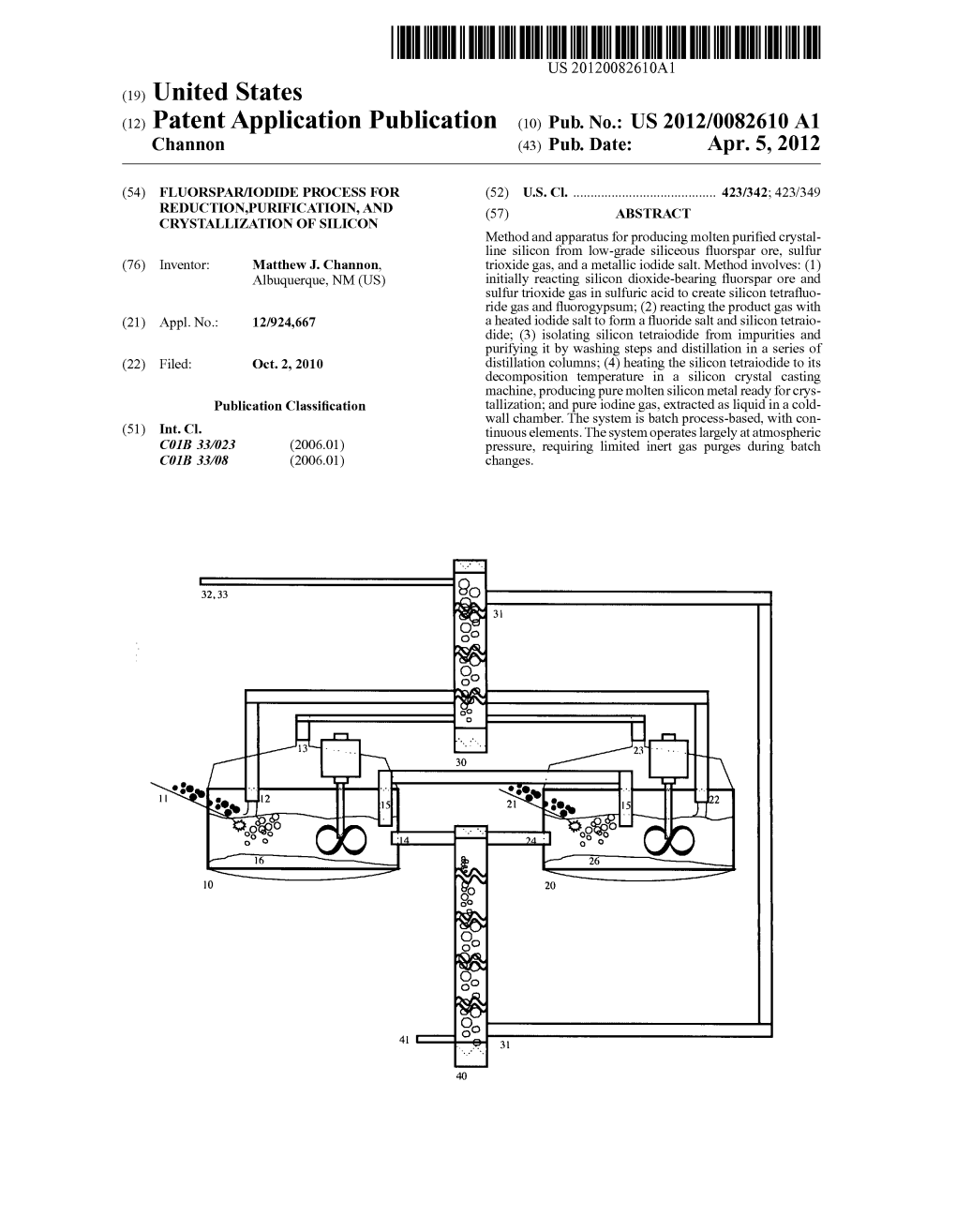
Load more
Recommended publications
-
Pp-03-25-New Dots.Qxd 10/23/02 2:41 PM Page 778
pp-03-25-new dots.qxd 10/23/02 2:41 PM Page 778 778 PRAESODYMIUM PRAESODYMIUM [7440–10–0] Symbol Pr; atomic number 59; atomic weight 140.908; a lanthanide–series rare earth element; belongs to the cerium group of rare earths; electron con- figuration [Xe] 4f36s2; partially filled f subshell; valence states +3, +4; most 3+ stable oxidation state +3; electrode potential E°/V (aq) for Pr + 3e¯ ↔ Pr is –2.35 V; atomic radius 1.828 Å; first ionization potential 5.46 eV; one natu- rally–occurring isotope, Pr–141; twenty–nine artificial radioactive isotopes known in the mass range 124, 126–140 and 142–154; the longest–lived isotope Pr–143, t1/2 13.57 day, and the shortest–lived isotope Pr–124, t1/2 1.2 second. History, Occurrence, and Uses Mosander extracted from the mineral lanthana a rare earth fraction, named didymia in 1841. In 1879, Boisbaudran separated a rare earth oxide called samaria (samarium oxide) from the didymia fraction obtained from the mineral samarskite. Soon after that in 1885, Baron Auer von Welsbach iso- lated two other rare earths from didymia. He named them as praseodymia (green twin) and neodymia (new twin) after their source didymia (twin). The name praseodymium finally was assigned to this new element, derived from the two Greek words, prasios meaning green and didymos meaning twin. Praseodymium occurs in nature associated with other rare earths in a rel- atively high abundance. It is more abundant than some common metals such as silver, gold, or antimony. The average concentration of this metal in the earth’s crust is estimated to be 8.2 mg/kg. -
The Preparation and Reactions of the Lower Chlorides and Oxychlorides of Silicon Joseph Bradley Quig Iowa State College
Iowa State University Capstones, Theses and Retrospective Theses and Dissertations Dissertations 1926 The preparation and reactions of the lower chlorides and oxychlorides of silicon Joseph Bradley Quig Iowa State College Follow this and additional works at: https://lib.dr.iastate.edu/rtd Part of the Inorganic Chemistry Commons Recommended Citation Quig, Joseph Bradley, "The preparation and reactions of the lower chlorides and oxychlorides of silicon " (1926). Retrospective Theses and Dissertations. 14278. https://lib.dr.iastate.edu/rtd/14278 This Dissertation is brought to you for free and open access by the Iowa State University Capstones, Theses and Dissertations at Iowa State University Digital Repository. It has been accepted for inclusion in Retrospective Theses and Dissertations by an authorized administrator of Iowa State University Digital Repository. For more information, please contact [email protected]. INFORMATION TO USERS This manuscript has been reproduced from the microfilm master. UlVli films the text directly from the original or copy submitted. Thus, some thesis and dissertation copies are in typewriter face, while others may be from any type of computer printer. The quality of this reproduction is dependent upon the quality of the copy submitted. Broken or indistinct print, colored or poor quality illustrations and photographs, print bleedthrough, substandard margins, and impiroper alignment can adversely affect reproduction. In the unlikely event that the author did not send UMI a complete manuscript and there are missing pages, these will be noted. Also, if unauthorized copyright material had to be removed, a note will indicate the deletion. Oversize materials (e.g., maps, drawings, charts) are reproduced by sectioning the original, beginning at the upper left-hand corner and continuing from left to right in equal sections with small overiaps. -
(12) Patent Application Publication (10) Pub. No.: US 2016/0115593 A1 KUCHENBESER Et Al
US 2016O115593A1 (19) United States (12) Patent Application Publication (10) Pub. No.: US 2016/0115593 A1 KUCHENBESER et al. (43) Pub. Date: Apr. 28, 2016 (54) AMINO(IODO)SILANE PRECURSORS FOR HOIL 2/3 II (2006.01) ALDACVD SILICON-CONTAINING FILM C23C I6/34 (2006.01) APPLICATIONS AND METHODS OF USING C23C I6/56 (2006.01) THE SAME (52) U.S. Cl. CPC ......... C23C 16/45553 (2013.01); C23C 16/345 (71) Applicant: American Air Liquide, Inc., Fremont, (2013.01); C23C I6/45536 (2013.01); C23C CA (US) I6/56 (2013.01); HOIL 21/31 III (2013.01); HOIL 21/02211 (2013.01); HOIL 21/02274 (72) Inventors: Glenn KUCHENBEISER, Newark, DE (2013.01); HOIL 2L/0228 (2013.01); HOIL (US); Bastien LEFEVRE, Wilmington, 21/0217 (2013.01) DE (US) (21) Appl. No.: 14/984,866 (57) ABSTRACT (22) Filed: Dec. 30, 2015 Publication Classification Disclosed are amino(iodo)silane precursors, methods of syn thesizing the same, and methods of using the same to deposit (51) Int. Cl. silicon-containing films using vapor deposition processes. C23C I6/455 (2006.01) The disclosed amino(iodo)silane precursors include SiHI(N HOIL 21/02 (2006.01) (iPr)) or SiHI(N(iBu)). Patent Application Publication Apr. 28, 2016 Sheet 1 of 6 US 2016/O115593 A1 FG Patent Application Publication Apr. 28, 2016 Sheet 2 of 6 US 2016/O115593 A1 100 T - - - - 90 - SiH(NMe2)2 atmoc 44mg 80 - - - - SiH(NMe2)2 closed cup 70 - 50 - 30 - 10 - O 1 OO 2OO 300 400 500 Temperature (°C) FIG. 3 - - SiH2(NEt2) atmoc 41 mg SiH2(NEt2) closed Cup 22mg s s cus s 9 CD 8 300 Temperature (°C) FIG. -
Dec. 12, 1961 H
Dec. 12, 1961 H. W. LNG 3,012,861 PRODUCTION OF SILICON Filed Jan. 15, 1960 zzzzz INVENTOR HARRY W. LING ATTORNEY 3,012,861 United States Patent Office Patented Dec. 12, 1961 1. 2 3,012,861 . Referring now to this drawing, there is shown a ver PRODUCTION OF SELICON tically disposed cylindrical or tubular reactor 1 with a Harry W. Ling, Wilmington, Del assignor to E. I. du conical bottom 3 provided with inlet 4 for entrance of Pont de Nemours and Company, Wilmington, Dei, a reactant fluidizing gas. The reactor 1 is sufficiently high corporation of Delaware to provide for a 2-3 times expansion of the bed 6 and also Filed Jan. 15, 1960, Ser. No. 3,708. a disengaging space 7 above the bed 6 to reduce solids 9. Claims. (C. 23-223.5) blowover to a minimum. A valved inlet 8 is provided for introduction of silicon bed particles. The reaction This invention relates to the production of elemental by-product gases are removed from the reactor through silicon. More particularly, it relates to a new and im 10 the outlet 9 and cyclone 13 which can be kept hot by a proved method of thermally decomposing volatile silicon furnace (not shown). These gases then pass to a con compounds. densing system 10 and cold trap (not shown) through Silicon can be produced by thermally decomposing sili which the vacuum pumping system (not shown) is con con iodide at a reduced pressure -on an electrically nected. The reactor 1 is maintained at the desired reactor heated, incandescent metal filament. -
WO 2013/089962 Al 20 June 2013 (20.06.2013) W P O P C T
(12) INTERNATIONAL APPLICATION PUBLISHED UNDER THE PATENT COOPERATION TREATY (PCT) (19) World Intellectual Property Organization International Bureau (10) International Publication Number (43) International Publication Date WO 2013/089962 Al 20 June 2013 (20.06.2013) W P O P C T (51) International Patent Classification: (81) Designated States (unless otherwise indicated, for every B01J 31/04 (2006.01) B01J 31/18 (2006.01) kind of national protection available): AE, AG, AL, AM, B01J 31/14 (2006.01) B01J 31/22 (2006.01) AO, AT, AU, AZ, BA, BB, BG, BH, BN, BR, BW, BY, BZ, CA, CH, CL, CN, CO, CR, CU, CZ, DE, DK, DM, (21) Number: International Application DO, DZ, EC, EE, EG, ES, FI, GB, GD, GE, GH, GM, GT, PCT/US20 12/065285 HN, HR, HU, ID, IL, IN, IS, JP, KE, KG, KM, KN, KP, (22) International Filing Date: KR, KZ, LA, LC, LK, LR, LS, LT, LU, LY, MA, MD, 15 November 2012 (15.1 1.2012) ME, MG, MK, MN, MW, MX, MY, MZ, NA, NG, NI, NO, NZ, OM, PA, PE, PG, PH, PL, PT, QA, RO, RS, RU, (25) Filing Language: English RW, SC, SD, SE, SG, SK, SL, SM, ST, SV, SY, TH, TJ, (26) Publication Language: English TM, TN, TR, TT, TZ, UA, UG, US, UZ, VC, VN, ZA, ZM, ZW. (30) Priority Data: 13/323,328 12 December 201 1 (12. 12.201 1) US (84) Designated States (unless otherwise indicated, for every kind of regional protection available): ARIPO (BW, GH, (71) Applicant (for all designated States except US): CHEV¬ GM, KE, LR, LS, MW, MZ, NA, RW, SD, SL, SZ, TZ, RON PHILLIPS CHEMICAL COMPANY LP UG, ZM, ZW), Eurasian (AM, AZ, BY, KG, KZ, RU, TJ, [US/US]; 10001 Six Pines Drive, The Woodlands, Texas TM), European (AL, AT, BE, BG, CH, CY, CZ, DE, DK, 77380 (US). -
Silicon Semiconductor Technology
Runyan TEXAS INSTRUMENTS INCORPORATED Semiconductor·Components Division EXAS INSTRUMENTS INCORPORATED Silicon Semiconductor Technology W. R. Runyan Texas Instruments Electronics Series McGraw·HiII McGraw-Hili Beok Company 54276 Silicon Semiconductor Technology The Engineering Staff of Texas Instruments Incorporated • TRANSISTOR CIRCUIT DESIGN Runyan • SILICON SEMICONDUCTOR TECHNOLOGY Sevin • FIELD-EFFECT TRANSISTORS Silicon Semiconductor Technology w. R. Runyan Semiconductor Research and Development Laboratory Texas Instruments Incorporated McGRAW-HILL BOOK COMPANY New York San Francisco Toronto London Sydney SILICON SEMICONDUCTOR TECHNOLOGY Copyright © 1965 by Texas Instruments Incorporated. All Rights Reserved. Printed in the United States of America. This book, or parts thereof, may not be reproduced in any form without permission of Texas Instru ments Incorporated. Library of Congress Catalog Card Number 64-24607. Information contained in this book is believed to be accurate and reliable. However, responsibility is assumed neither for its use nor for any infringement of patents or rights of others which may result from its use. No license is granted by implication or otherwise under any patent or patent right of Texas Instruments or others. 54276 345678 9-MP-9 8 7 6 Preface The purposes of this book are to provide in a single reference the properties of silicon important to those who would use it as a semiconductor and to discuss at length several of the more important semiconductor technologies, such as crystal growing and diffusion. It had its beginning in a set of notes I began compiling shortly after starting work in the semiconductor industry. Since most of my activ ities were with silicon, these notes were restricted to information pertaining to that material. -
N FIG. I Azawad "Wiiw4
July 10, 1962 B, MANNING 3,043,667 PRODUCTION OF ULTRA-PURE SELICON OR GERMANIUM Filed Oct. 31, 1960 3 Sheets-Sheet N 220 eaded sao 162 o o F.G. 6 3. 1. | 6ao.4%726/24a/ s. 77%WG/ ape/a/ay1 9/4 /64 Gaa. 404A2/V FIG. I azawad "WiiW4 B%0/.-- 2.2 77(42.45 Oag A/AX-S July 10, 1962 B. MANNING 3,043,667 PRODUCTION OF ULTRA-PURE SILICON OR GERMANIUM Filed Oct. 31, 1960 3. Sheets-Sheet 2 in SS INVENTOR, ABAA/WAAA M/4///////4 2AMWAS July 10, 1962 B, MANNING 3,043,667 PRODUCTION OF ULTRA-PURE SILICON OR GERMANIUM Filed Oct. 3l, 1960 3. Sheets-Sheet 3 2 4. 8 as7 s i.\ \ INVENTOR. AtAA/VAAA) M/4//W/WG B 'cC-4- 2. 92 - . Z 775"/0231. a Maas 3,043,667 United States Patent Office Patiented July 10, 1962 2 adsorbing impurities from the tetrahalide by passing a 3,043,667 solution thereof through purified silica gel, recovering PRODUCTION OF ULTRA-PURE SELICON the tetrahalide from the solution, Zone purifying the OR GERMANUM tetrahalide by passing a mass thereof slowly past alternate Bernard Manning, Waltham, Mass, assignor to the melting and cooling zones, and reducing the tetrahalide to United States of America as represented by the Secre elemental silicon or germanium by passing hydrogen gas tary of the Air Force into a retort containing the halide heated to an elevated Filed Oct. 3, 1960, Ser. No. 66,369 temperature, said gas and halide vapor passing into a 2 Claims. -
Signature Redacted 0'10
A STUDY OF THE REACTION 0'10 OF HYDROGEN IODIDE WITH SILICON v193 ARY THESIS by CAROLYN H. KLEIN S.B. Simmons College, 1933. Submitted in Partial Fulfillment of the Requirements for the Degree of MASTER OF SCIENCE from the Massachusetts Institute of Technology 1934 Signature Redacted Signature of Author. .. .. Department of Chemistry. Date Professor in Charge of Research . Signature Redacted Chairman of Departmental Commltee on Graduate Students . Signature Rected Signature Redacted Head of Deartment . it * - Acknowledgement The author wishes to express her most sincere appreciation to Professor Walter C. Schumb for the active interest which he has at all times shown in this research, and for the many helpful suggestions which he has offered. The author should also like to extend her thanks to the many other members of the Research Laboratory of Inorganic Chemistry, for the helpful advice which they have given. N I 197618 K j\> Table of Contents Page I Previous Wiork on the Preparation of the Iodides of Silicon . .... .. 1 II Introauction .. .... ..... 3 III Preparation of Hydrogen Iodide . 4 IV Figure I. Apparatus Used in the Reaction between Silicon and HI .. ... .. 6 V The Reaction of Silicon withHI ....... 7 VI Figure II. Revised Apparatus for the Reaction of Silicon with HI . .. .10 VII General Conclusions from the Reaction between Silicon and HI ..... .... 13 VIII Reaction of Calcium Silicide with HI .. ... 14 IX Figure III. Arparatus Used for the Reaction of Calcium Silicide with HI .. 15 X Figure IV. Apparatus for Distillation of the Crude Product of the Reaction .. 19 XI The Purification of Silicon Tetra-iodide .. -
Molar Heat Capacity and Heat of Fusion of Silicon Tetraiodide*
229 Molar Heat Capacity and Heat of Fusion of Silicon Tetraiodide* By Toshio Kurosawa**, Ryosuke Hasegawa** and Tetsuo Yagihashi** The molar heat capacity of silicon tetraiodide, SiI4, used as a source material in the iodide process of silicon prepara- tion was measured by means of an adiabatic calorimeter which can be used for continuous measurement. The molar heat capacities of solid and liquid silicon tetraiodide obtained were Cp=19.59+0.0209T eal/mol deg and Cp=35.25+0.00987Tcal/mol deg, respectively. The melting point was 120.5℃, and the heat of fusion and the entropy of fusion were 4.70kcal/mol and 11.9cal/mol deg, respectively. The heat contents, free energy functions and standard entropy of S298=43.7cal/mol deg were derived for silicon tetraiodide from the experimental values and thermochemical data. Moreover, the molar heat capacities of pure chromium, fused quartz and highly pure silicon were also measured, the values of which were in good agreement with those in the previous literature. (Received April 26, 1965) helices. The sampling capsule was also made of quartz I. Introduction and theshape is shown in Fig.1(A). Thiscapsule was hprevious reports(1)~(4), various processes relating COnlleCted With the diStilation column and filled with to the hydrogen reduction of silicon tetraiodide have been the main fraction of silicon tetraiodide in argon atmos- described as a part of the research program on the pre- phere. After separated from the column, it was sealed parationof pure silicon.In regardto thermochemicalhy a ball joint①, and then two capillaries ② were fused off under evacuation from the capsule. -
Nitrogen Tribromide Polar Or Nonpolar
Nitrogen tribromide polar or nonpolar Continue Nitrogen Tribromid Names IUPAC Name Nitrogen Tribromid Identifiers CAS Number 15162-90-0 3D Model (JSmol) Interactive Image ChemSpider 20480821 PubChem CID 3082084 CompTox Dashboard (EPA) DTXSID901648 In22 InChI InChIBrH.N/h3'1H;/p-3 SMILES N(Br)(Br)Br Properties Chemical Formula NBr3 Molar Mass 253.7187 g/mol Appearance Deep-red solid melting point explodes at -100 degrees Celsius, except when otherwise noted, the data is given for materials in their standard state (at 25 degrees Celsius), 100 kPa). Infobox links nitrogen tribromid is a chemical compound with the NBr3 formula. It is extremely explosive in its purest form, even at 100 degrees Celsius, and was not isolated until 1975. It's deep-red and volatile solid. The drug NBr3 was first prepared by the reaction of bistrimetligrilbramamin (bis (trimethylsil)amin bromide) with bromine monochloride (with trimethylylyl chloride as a by-product) at 87 degrees on the following equations: (Me3Si)2NBr2 BrCl → NBr3 and 2 Me3SiCl, Where Me is He instantly reacts with ammonia in a dichloromethane solution at 87 degrees Celsius to give NBrH2. Links - Lide, David R. (1998), Handbook on Chemistry and Physics (87 Ed.), Boca-Raton, Florida: CRC Press, p. 4-73, ISBN 0-8493-0594-2 Greenwood, Norman N.; Earnshaw, Alan (1997). Chemistry of elements (2nd st. Butterworth-Keinmann. page 439. ISBN 978-0-08-037941-8. vteSalts and covalent derivatives of nitrid ion NH3N2H4 He (N2)11 Li3N Be3N2 BN β-C3N4g- C3N4CxNy N2 NxOy NF3 Ne Na3N Mg3 NN2 AlN Si3N4 PNP3N5 SxNySNS4N4 NCl3 Ar K3N Ca3N2 ScN VN CrNCr2N MnxNy FexNy Ni3N CuN n3N2 GaN Ge3N4 as Se NBr3 Kr Rb3 Yn Sr3N2 yn srn NbN β-Mo2N Tc Ru Rh PdN AgN CdN InN Sb Te NI3 Xe Cs3N Ba3N2 Hf3N4 TaN WN Re Os Au Hg3N2 TlN Pb BiN Po At At Rn Fr3N Ra3N2 Rf Db Sg Bh Hs Mt D rg Cn Nh Fl Mc Lv Ts Og s La CeN Pr Nd Pm Sm Eu GdN Tb Dy Er Tm Yb Lu Ac Th Pa UN Np Pu Am Cm Bk Cf Es Fm No Lr Lr Extracted from the Is NBr3 (Nitrogen Tribromid) polar or non-polar? NBr3 (Nitrogen Tribromid) is a polar I'll tell you the polar or nonpolar list below. -
United States Patent 0 " IC€ Patented Jan
3,299?-l7 United States Patent 0 " IC€ Patented Jan. 17, 1967 1 2 amount of a norbornadiene. As determined by infrared 3,299,017 analysis, the product obtained from this polymerization COlPOLYMlERS OF 1,3-BUTADIENE AND A NORBORNADHENE reaction is a copolymer of 1,3-butadiene and a norborna Robert P. Zelinski and Floyd E. Naylor, lliartlesville, diene in which at least 85 percent, e.g., from 85 to 98 Okla, assignors to Phillips Petroleum Company, a cor percent and higher, of the butadiene units have a cis 1,4 poration of Delaware con?guration. This novel copolymer has a greatly re No Drawing. Filed Apr. 29, 1963, Ser. No. 276,166 duced tendency to cold flow while still retaining the desir 12 ‘Claims. (Cl. 26tl—82.l) able physical properties of conventional cis-polybutadi ene. Furthermore, the copolymer of this invention pos This invention relates to novel polymers of 1,3-butadi sesses improved processing characteristics. For example, ene. In one aspect, it relates to a method for producing in the compounding of the copolymers, shorter mixing a polymer of 1,3-butadiene having a reduced tendency to times are required. This results from the fact that there cold ?ow. In another aspect, it relates to a method for is a more rapid heat buildup during mixing as compared improving the processability of polymers of 1,3-butadi to conventional cis-polybutadiene, which facilitates the ene. 15 incorporation of compounding ingredients. Further A great deal of research work has been conducted dur more, the novel copolymers have better extrusion and ing the last few years with the object of producing im milling characteristics and exhibit a considerably longer proved rubbery polymers. -