Jan. 9, 1968 B. MATCHEN 3,362,787 PREPARATION of MOLYBDENUM SILICEDES Filed Feb
Total Page:16
File Type:pdf, Size:1020Kb
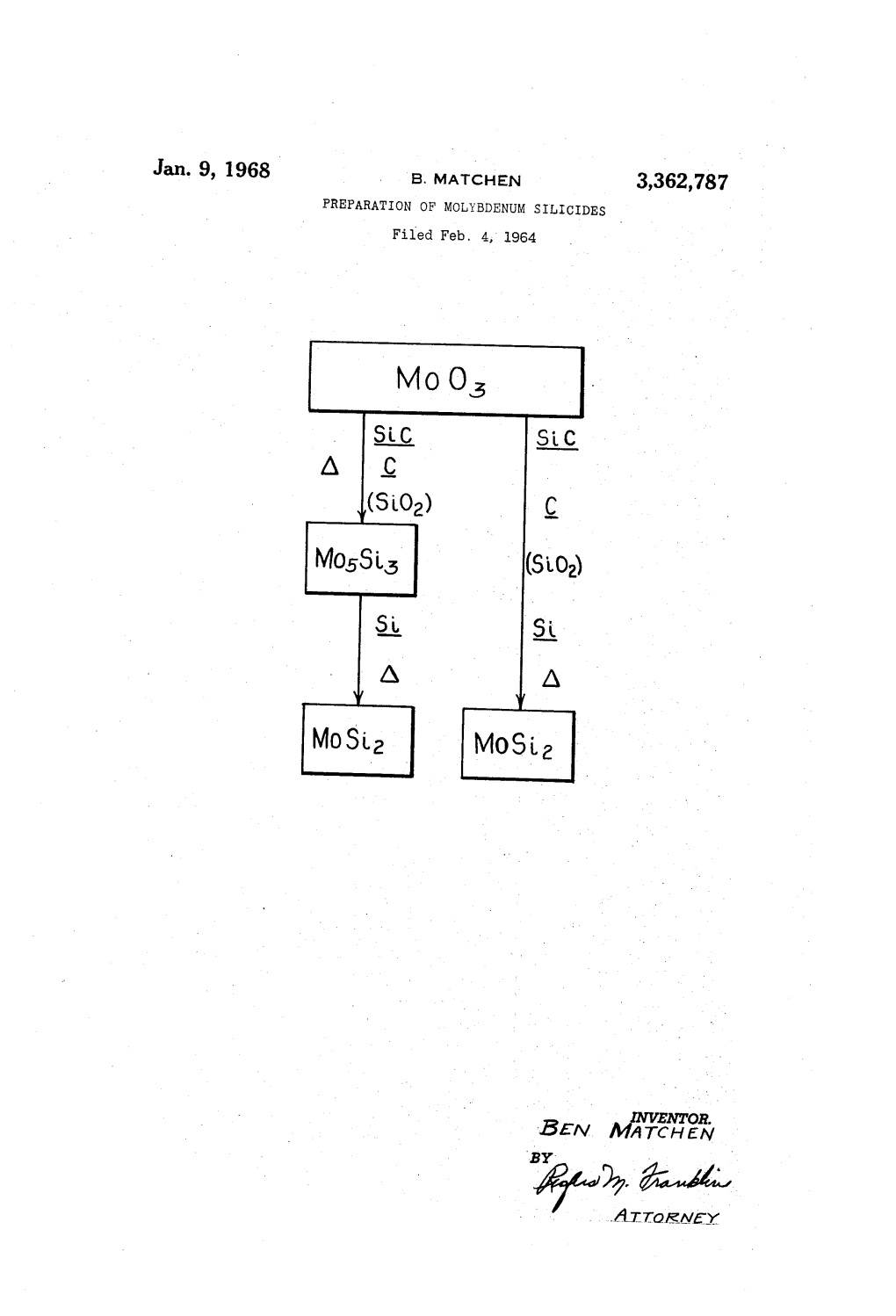
Load more
Recommended publications
-
Processing, Microstructure, and Mechanical Properties of Zirconium Diboride-Molybdenum Disilicide Ceramics and Dual Composite Architectures
Scholars' Mine Doctoral Dissertations Student Theses and Dissertations Spring 2017 Processing, microstructure, and mechanical properties of zirconium diboride-molybdenum disilicide ceramics and dual composite architectures Ryan Joseph Grohsmeyer Follow this and additional works at: https://scholarsmine.mst.edu/doctoral_dissertations Part of the Energy Systems Commons, and the Materials Science and Engineering Commons Department: Materials Science and Engineering Recommended Citation Grohsmeyer, Ryan Joseph, "Processing, microstructure, and mechanical properties of zirconium diboride- molybdenum disilicide ceramics and dual composite architectures" (2017). Doctoral Dissertations. 2561. https://scholarsmine.mst.edu/doctoral_dissertations/2561 This thesis is brought to you by Scholars' Mine, a service of the Missouri S&T Library and Learning Resources. This work is protected by U. S. Copyright Law. Unauthorized use including reproduction for redistribution requires the permission of the copyright holder. For more information, please contact [email protected]. PROCESSING, MICROSTRUCTURE, AND MECHANICAL PROPERTIES OF ZIRCONIUM DIBORIDE-MOLYBDENUM DISILICIDE CERAMICS AND DUAL COMPOSITE ARCHITECTURES by RYAN JOSEPH GROHSMEYER A DISSERTATION Presented to the Faculty of the Graduate School of the MISSOURI UNIVERSITY OF SCIENCE AND TECHNOLOGY In Partial Fulfillment of the Requirements for the Degree DOCTOR OF PHILOSOPHY in MATERIALS SCIENCE AND ENGINEERING 2017 Submitted to: Gregory Hilmas, Advisor William Fahrenholtz Jeffrey Smith David Van Aken Lokeswarappa Dharani iii PUBLICATION DISSERTATION OPTION This dissertation consists of the following five articles that will be submitted for publication as follows and have been formatted in the style of the journal Ceramics International. The manuscripts entitled, “ZrB2-MoSi2 Ceramics with Varying MoSi2 Content: Part 1. Processing and Microstructure with Varying ZrB2 Particle Size:” (Paper I, Pages 50–80), and the manuscript entitled “ZrB2-MoSi2 Ceramics with Varying MoSi2 Content: Part 2. -
Research Memorandum
RM E52B06 NACA RESEARCH MEMORANDUM SOME FACTORS AFFECTING FABRICATION AND HIGH-TEMPERATURE STRENGTH OF MOLYBDENUM DISILICIDE By W. A. Maxwell Lewis Flight Propulsion Labora tory Cleveland, Ohio NATIONAL ADVISORY COMMITTEE FOR AERONAUTICS WASHINGTON April 17 , 1952 1U NACA RM E58B06 NATIONAL ADVISORY COMMITTEE FOR AERONAUTICS RESEARCH MEMORANDUM SOME FACTORS AFFECTING FABRICATION AND HIGH-TEMPERATURE STRENGTH OF MOLYBDENUM DISILICIDE By W. A. Maxwell SUMMARY In an investigation of the properties of molybdenum disilicide, a fine-grain material having a moderately high oxygen content has been produced by cold-pressing and sintering, and a large-grain material having a lower oxygen content and a density of 99 percent of the theo retical density has been produced by hot-pressing. In a series of experiments with the fine-grain material in which the only variable was the amount of carbon added, marked increases in modulus-of-rupture strength were found at carbon contents between 0.15 and 0.3 percent. Improvements in the long-time deformation properties, as shown by the flexure-creep test, and decreased high-temperature plasticity accompanied the carbon additions. The Knoop hardness was 1160. The beneficial effects of carbon additions on strength are attri buted to partial deoxidation of the material, particularly the reduction of molybdenum oxides, and the formation of silicon carbide and other carbides. Exceptionally high short-time strengths, in comparison with other high-temperature materials, were obtained with sintered molybdenum disilicide containing from 1.0 to 1.4 percent oxygen. The effects of such oxygen contents on sintering and binding may be beneficial. The large-grain, hot-pressed molybdenum disilicide having a low oxygen content possessed superior high-temperature deformation resist ance, slightly inferior short-time strength, and decreased high temperature plasticity as compared with the fine-grain molybdenum disili cide to which carbon was added. -
The Disilicides of Tungsten, Molybdenum, Tantalum, Titanium, Cobalt, and Nickel, and Platinum Monosilicide: a Survey of Their Thermodynamic Properties
The Disilicides of Tungsten, Molybdenum, Tantalum, Titanium, Cobalt, and Nickel, and Platinum Monosilicide: A Survey of Their Thermodynamic Properties Cite as: Journal of Physical and Chemical Reference Data 22, 1459 (1993); https:// doi.org/10.1063/1.555922 Submitted: 21 December 1992 . Published Online: 15 October 2009 M. S. Chandrasekharaiah, J. L. Margrave, and P. A. G. O’Hare ARTICLES YOU MAY BE INTERESTED IN Thermodynamic considerations in refractory metal-silicon-oxygen systems Journal of Applied Physics 56, 147 (1984); https://doi.org/10.1063/1.333738 Thermal and Electrical Conductivity of Graphite and Carbon at Low Temperatures Journal of Applied Physics 15, 452 (1944); https://doi.org/10.1063/1.1707454 Formation of thin films of NiSi: Metastable structure, diffusion mechanisms in intermetallic compounds Journal of Applied Physics 55, 4208 (1984); https://doi.org/10.1063/1.333021 Journal of Physical and Chemical Reference Data 22, 1459 (1993); https://doi.org/10.1063/1.555922 22, 1459 © 1993 American Institute of Physics for the National Institute of Standards and Technology. The Disilicides of Tungsten, Molybdenum, Tantalum, Titanium, Cobalt, and Nickel, and Platinum Monosilicide: A Survey of Their Thermodynamic Properties M. s. Chandrasekharaiah and J. L. Margrave HARC, Materials Science Research Center, 4802 Research Forest Drive, The Woodlands, TX 77381 and P. A. G. O'Hare Chemical Kinetics and Thennodynamics Division, National Institute of Standards and Technology, Gaithersburg, MD 20899-0001 Received December 21, 1992; revised manuscript received February 19, 1993 A critical evaluation is presented of the thermodynamic properties of six disiIi cides and one monosilicide that are important in the manutacture ot very large scale integrated circuits. -
Research Memorandum
RESEARCH MEMORANDUM PROPERTIES OF CERTAIN INTER&UXTALLICS AS RELATtiD . TO ELEVATED-TEMPERATURE APPLICATIONS I - MOLYBDENUM DISILKXDE Ld By W. A. MaxweJ.l. Lewis l&&t Propulsion Laboratory Cleveland, Ohio .: _i. I_ -.ClASSIFICATfON CANC NATIONAL ADVISORY COMMITTEE FOR AERONAUTICS WASHINGTON October 6,1949 NACA RM E9GOl NA!KCONALADVISORYCOMKETEEFORAXRONAUTICS I -MOL~DISILIC~ By W. A. Maxwell A method for the preparation and purification of the inter- metallic, molybdenum disilicide, was developed and the following properties were determined for the sintered material: Tanperature Room 2000°F 2400°F Modulus of rupture, lb/sq in. 50,700 35,700 20,700 Total elongation calculated f4 fletietests, percent . 0.09 0.72 3.2 Plastic elongation calculated from flexure tests, percent . none 0.39 1.4 DeIlBity: Theoretioal (X-ray data), grams/cm1 . 6.24 Potiered,gramsbl........, . 6.2 Sintered,msj%l... ..5.66 Rockwell hardness (superpioial) . , . C-57 Crystal structure tetragonal body-centered Oxidation resistax.d,'s~a;le'&Z ;n'aL 200ooF' 2400°F (gnmgaFnlBqcm)fhr. -0.000ooo4 0.000005 Chemical mpertles of molybdenum disilicide were found to be: highly inert, unattadsed by boilin@; hydroohloric acid, sulfuric acid, or aqueous sodium hydroxide; elightly attacked by nitrio acid; dis- solved by molten sodium h-de. The sintered material is silvery white in co&, possesses high eleutria oonductivity, and is resistant to thermal shock. Molybdenum disilicide melts at 3500° &IL@ F with decomposition. 2 NACA FM lBGO1 Plastic deformation of the intermetallic at temperatures well below the melting point was observed although only brittle behavior wasapparentatroomtemperature. From the Investigation c&Tpropertiee of molybdenum dieilioide, it appear0 that: 1. -
Mosi2 and Other Silicides As High Temperature Structural Materials
MoSi2 AND OTHER SILICIDES AS HIGH TEMPERATURE STRUCTURAL MATERIALS DILIP M. SHAH Pratt & Whitney 400 Main St. E. Hartford, CT. 06108 Abstract There has been a revival of interest in MoSi;? and other refractory silicides, hitherto used for heating elements and coatings, as high temperature structural materials. With their high melting point and excellent high temperature oxidation resistance, silicides as a class of intermetallics, have potential for developing temperature capability beyond nickel base superalloys. Though metal like in their physical properties, silicides are in general brittle at room temperature. This drawback is being addressed through a variety of in-situ and artificial composite approaches. This paper attempts to provide a perspective on these approaches with a review of current activities. To provide a background, the development strategies for high temperature structural materials are discussed, followed by an overview on formation of silicides. The relevant mechanical and physical properties and environmental resistance of silicides are compared using superalloys as the benchmark, to help assess the risks versus benefits. Finally, the paper concludes with a brief summary of primarily fiber reinforced MoSi2 composites and ductile phase reinforced in-situ composites based on other silicides. The unavailability of suitable fibers and interface coating for conventional composites and containerless solidification for in-situ composites are identified as the principal problems. Superalloys 1992 Edited by S.D. Antolovich, R.W. Stusrud, R.A. MacKay, D.L. Anton, T. Khan, R.D. Kissinger, D.L. Klarstmm The Minerals, Metals & Materials Society, 1992 409 Introduction Since as early as 1956, molybdenum disilicide (MoSi2) based material has been commercially available as Super Kanthal [l], along with nickel-chromium based heating elements. -
Research Memorandum
RM E52A04 NACA RESEARCH MEMORANDU M OXIDATION-RESISTANCE MECHANISM AND OTHER PROPERTIES OF MOLYBDENUM DISILICIDE By W. A. Maxwell Lewis Flight Propulsion Laboratory Cleveland, Ohio NATIONAL ADVISORY COMMITTEE FOR AERONAUTICS WASHINGTON March 14, 1952 lW NACA RM E52A04 NATIONAL ADVISORY COMMITTEE FOR AERONAUTIeS RESEARCH MEMORANDUM OXIDATION-RESISTANCE MECHANISM AND OTHER PROPERTIES OF MOLYBDENUM DISILICIDE By W. A. Maxwell SUMMARY An experimental investigation was conducted to determine the oxidation-resistance mechanism, the melting characteristics, the electric resistiVity, and the modulus of elasticity of molybdenum disilicide. Molybdenum disilicide MoSi2 bodies are protected from oxidation at high temperatures by the formation of a protective siliceous coating in which ~cristobalite has been identified as the sole or principa~ constituent. In powdered form, MoSi2 is not inherently resistant to oxidation and burns in air at comparatively low temperatures. Molybdenum disilicide decomposed at the melting point with the loss of appreciable silicon. This phenomenon has so far prevented casting of satisfactory ingots. Decomposition below the melting point was indicated. The electric resistivity of MoSi2 at room temperature varies from 23 to 27 microhm-centimeters depending on the method of fabrication. The conductivity was found to be metallic in nature and to decrease with increasing temperatures to 20000 F. The room-temperature modulus of elasticity as determined by a dynamic method was 59 Xl06 pounds per square inch. Poor damping character istics are indicated for the material at room temperature. INTRODUCTION The outstanding oxidation resistance of molybdenum disilicide MoSi2 at high temperatures, as previously reported (references 1 and 2) and as summarized in table I, places it among the most resistant of materials in the temperature range from 20000 to 28500 F. -
Oxidation Behavior of Molybdenum Silicides and Their Composites K
ET/CP- 776 / 7 Oxidation Behavior of Molybdenum Silicides and Their Composites K. Natesan Energy Technology Division, Argonne National Laboratory, Argonne, IL 60439, USA and S. C. Deevi Research and Development Center, Philip Morris USA, Richmond, VA 23234 February 2000 The submitted manuscript has been created by the University of Chicago as Operator of Argonne National Laboratory ("Argonne") under Contract No. W-31-109-ENG-38 with the U.S. Department of Energy. The U.S. Government retains for itself, and others act- ing on its behalf, a paid-up, nonexclusive, irrevocable worldwide license in said article to reproduce, prepare derivative works, dis- tribute copies to the public, and perform pub- F.\ s* licly and display publicly, by or on behalf of ^HtP Cr the Government. <f{^ C A % V\ - Invited paper presented at the International Symposium on Intermetallics for the Third Millennium, ASM Materials Solutions, Cincinnati, November 1-4, 1999. *Work supported by the U.S. Department of Energy, Office of Fossil Energy, Advanced Research and Special Technologies Materials Program and Office of Energy Research, Basic Energy Sciences, Division of Materials, under Contract W-31-109-Eng-38. DISCLAIMER This report was prepared as an account of work sponsored by an agency of the United States Government. Neither the United States Government nor any agency thereof, nor any of their employees, make any warranty, express or implied, or assumes any legal liability or responsibility for the accuracy, completeness, or usefulness of any information, apparatus, product, or process disclosed, or represents that its use would not infringe privately owned rights. -
Oxidation Behaviour of Molybdenum Disilicide Coatings at 1500 °C
published at the ITSC 2004, Osaka, J, May 10th - 12th Oxidation behaviour of molybdenum disilicide coatings at 1500 °C B. Wielage, G. Reisel, A. Wank, G. Fritsche, Chemnitz / D Molybdenum disilicide (MoSi2) is a suitable material for high temperature applications especially because of its excellent high temperature oxidation resistance. For several high temperature applications MoSi2 shows high potential to be used as a protective coating. The oxidation behaviour of HVOF sprayed MoSi2 coatings is studied at 1500 °C. The oxidation tests are carried out in a simultaneous thermogravimetric device and the mass change is measured in dependence on the oxidation time. The microstructure of the coatings before and after oxidation is examined by X-ray diffraction analysis (XRD), scanning electron microscopy (SEM) and energy dispersive X-ray analysis (EDXS). The mass of the coating increases according to a parabolic function. During the oxidation test the microstructure changes significantly from a typical thermal spray coating microstructure with lamellae, pores and a phase mixture of MoSi2 and Mo5Si3 to a two phase system with sharply separated grain boundaries. On the surface of the coating a silicon dioxide layer with a thickness of less than 10 µm is formed. 1 Introduction 1.0 MoSi2 0.9 Monolithic molybdenum disilicide (MoSi2) shows an 0.8 excellent resistance against high temperature 0.7 oxidation. Other good properties of this material are 0.6 -3 the relatively low density of 6.25 g·cm , the high 0.5 melting point of 2030 °C and the high toughness 0.4 0.3 above the brittle-ductile transition at approximately Intensity fraction SiO2 800 - 1100 °C. -
Optimization of Molybdenum Electrodes for Glass Melting
Optimization of Molybdenum Electrodes for Glass Melting by WenDi Liu A Dissertation Submitted to the Faculty of WORCESTER POLYTECHNIC INSTITUTE In partial fulfillment of the requirements of the Degree of Doctor of Philosophy in Materials Science and Engineering April 2015 APPROVED: _______________________________ Dr. Diran Apelian, Advisor Alcoa-Howmet Professor of Engineering _______________________________ Dr. Richard D. Sisson Jr. Director of Manufacturing and Materials Engineering George F. Fuller Professor ABSTRACT The U.S. glass industry is a $28 billion enterprise and millions of tons of glasses are melted each day by different heating techniques, such as conventional oil fired furnaces or via electrical heating. The share of electrical heating is bound to rise steadily because it is cleaner and more energy efficient. Due to this situation molybdenum will play a significant role in electrical glass melting, since it is the most frequently used electrode material to deliver the electricity into the glass melts. Although it has a high melting point, high electrical and thermal conductivity and a low coefficient of expansion, molybdenum electrodes fail because of lack of sustainability during the glass melting process. Melt reaction with electrodes is the fundamental barrier to higher melting temperatures. Glass manufacturers have suggested that the need for better performance of molybdenum electrodes will see a rapid advancement in the use of electric heating system in the U.S. This work first focused on post-mortem analysis on used molybdenum electrodes with and without the current load in order to establish failure mechanisms for molybdenum during glass melting. It was determined that service life of molybdenum electrodes are limited by poor oxidation and corrosion resistance of molybdenum with redox reactions. -
Fermi Surface and Electrical Characteristics of Molybdenum Disilicide S
Physics of the Solid State, Vol. 45, No. 2, 2003, pp. 201–206. Translated from Fizika Tverdogo Tela, Vol. 45, No. 2, 2003, pp. 193–197. Original Russian Text Copyright © 2003 by KurganskiÏ, Pereslavtseva, Levitskaya. SEMICONDUCTORS AND DIELECTRICS Fermi Surface and Electrical Characteristics of Molybdenum Disilicide S. I. KurganskiÏ, N. S. Pereslavtseva, and E. V. Levitskaya Voronezh State University, Universitetskaya pl. 1, Voronezh, 394006 Russia e-mail: [email protected] Received April 9, 2002 Abstract—Semirelativistic self-consistent calculations of the electronic structure of MoSi2 are performed within the framework of the linearized augmented-plane-wave (APW) method in the local density functional approximation. The results of investigations of the band structure, the Fermi surface, and electrical character- istics (effective cyclotron masses, the conductivity anisotropy constant, the mean free path, and the coefficient γ of the heat capacity component linear in temperature) are reported. The Fermi surface consists of two sheets, namely, an electron sheet and a hole sheet. The extreme sectional areas of the Fermi surface agree well with the experimental data on the de Haas–van Alphen effect. The results of first-principles calculations need no addi- tional correction. © 2003 MAIK “Nauka/Interperiodica”. 1. INTRODUCTION tional approximation, specifically for the band structure [20, 21, 24], densities of states [17, 20–24], and the Molybdenum disilicide possesses high microhard- Fermi surface [22, 24]. However, none of the first-prin- ness [1], resistance to oxidation during heating both in ciples calculations of the Fermi surface [22, 24] agrees air and in an oxygen flow [1], high thermal stability [2], in full measure with the experiment [19]. -
Chapter 1 Introduction
In-situ single step synthesis of MoSi2 nano powder A Thesis Submitted in partial fulfillment of the requirements for the award of degree of MASTER OF SCIENCE by Taranpreet Kaur (Registration No. 301504036) Under the Supervision of Dr. O.P. Pandey (Senior Professor) School of Physics & Materials Science Thapar University, Patiala-147004 July, 2017 ABSTRACT Molybdenum disilicide (MoSi2) has emerged as a promising material for high temperature applications. This transition metal silicide exhibits superior temperature stability, excellent oxidation resistance, low contact resistivity and is highly resistant to electro-migration. The low temperature synthesis of molybdenum disilicide has been investigated in a specially designed autoclave. The powder blend of MoO3-Si-Mg is heated at different temperatures for various interval of time. The impact of initial composition of the formation of MoSi2 is also studied. The prepared samples are characterized through various techniques i.e. X- ray diffraction (XRD), Field emission scanning electron microscope (FE-SEM) and high-resolution transmission electron microscope (HRTEM). The best results are obtained at 900 ºC for 10 hrs. dwell time. In this case, molybdenum disilicide (MoSi2) phase is obtained along with molybdenum silicide (Mo5Si3). This study provides the complete understanding associated with the formation of MoSi2. iii LIST OF FIGURES CHAPTER 1: INTRODUCTION PAGE Fig.1.1 Three different forms of molybdenum silicide. 3 Fig.1.2 Binary phase diagram of Mo-Si system. 3 Fig.1.3 Crystal structure of molybdenum disilicide (MoSi2). 5 CHAPTER 3: EXPERIMENTAL DETAILS Fig.3.1 Flow chart of MoSi2 synthesis. 22 Fig.3.2 Schematic diagram of synthesis route for MoSi2. -
Research Memorandum
https://ntrs.nasa.gov/search.jsp?R=19930087009 2020-06-17T13:45:51+00:00Z RM E52B06 NACA RESEARCH MEMORANDUM SOME FACTORS AFFECTING FABRICATION AND HIGH-TEMPERATURE STRENGTH OF MOLYBDENUM DISILICIDE By W. A. Maxwell Lewis Flight Propulsion Labora tory Cleveland, Ohio NATIONAL ADVISORY COMMITTEE FOR AERONAUTICS WASHINGTON April 17 , 1952 1U NACA RM E58B06 NATIONAL ADVISORY COMMITTEE FOR AERONAUTICS RESEARCH MEMORANDUM SOME FACTORS AFFECTING FABRICATION AND HIGH-TEMPERATURE STRENGTH OF MOLYBDENUM DISILICIDE By W. A. Maxwell SUMMARY In an investigation of the properties of molybdenum disilicide, a fine-grain material having a moderately high oxygen content has been produced by cold-pressing and sintering, and a large-grain material having a lower oxygen content and a density of 99 percent of the theo retical density has been produced by hot-pressing. In a series of experiments with the fine-grain material in which the only variable was the amount of carbon added, marked increases in modulus-of-rupture strength were found at carbon contents between 0.15 and 0.3 percent. Improvements in the long-time deformation properties, as shown by the flexure-creep test, and decreased high-temperature plasticity accompanied the carbon additions. The Knoop hardness was 1160. The beneficial effects of carbon additions on strength are attri buted to partial deoxidation of the material, particularly the reduction of molybdenum oxides, and the formation of silicon carbide and other carbides. Exceptionally high short-time strengths, in comparison with other high-temperature materials, were obtained with sintered molybdenum disilicide containing from 1.0 to 1.4 percent oxygen. The effects of such oxygen contents on sintering and binding may be beneficial.