An Engineering Analysis On
Total Page:16
File Type:pdf, Size:1020Kb
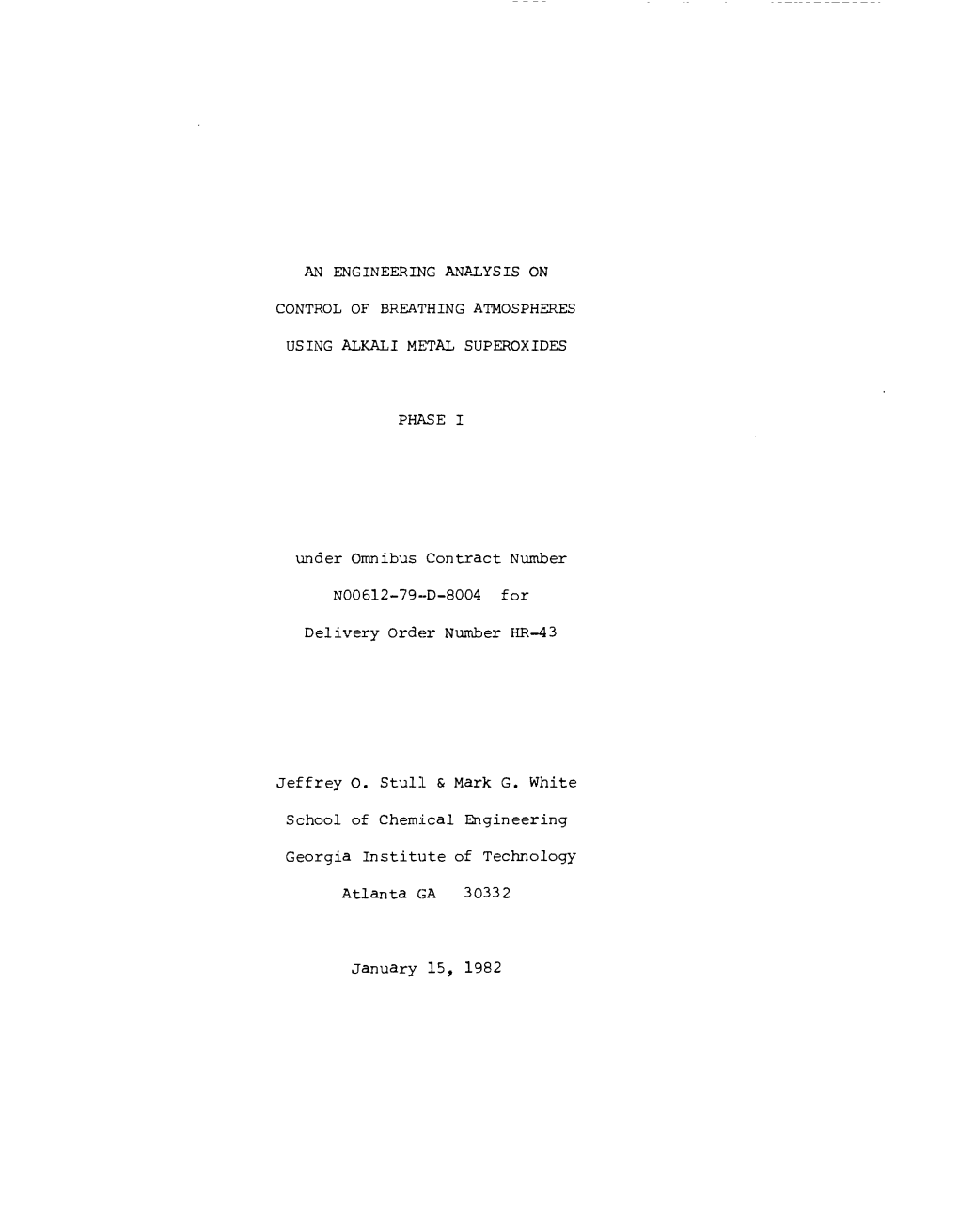
Load more
Recommended publications
-
Portable Oxygen Dispensing Device
CIKITUSI JOURNAL FOR MULTIDISCIPLINARY RESEARCH ISSN NO: 0975-6876 Portable Oxygen Dispensing Device Mr. Pritaj Yadav, Dept. of Computer Science and Engineering Rabindranath Tagore University, Bhopal Abstract A portable oxygen dispensing device, comprises a body which comprises of six chambers to generate oxygen, and a wearable mask attached to the body , a first chamber consists of a micro-capsule comprising a sodium superoxide, a second chamber is connected to the first chamber for storing solid carbon di-oxide, a third chamber is connected with the first chamber and second chamber, and contains a solution of solution of hydrogen peroxide and non-ionic surfactant such as ethoxylated aliphatic alcohol and a and a fourth chamber is connected with the first chamber and the third chamber, consists of a hydrogen peroxide and ethoxylated aliphatic alcohol to feed the first chamber, a fifth chamber consists of a zeolite for absorbing noxious gases and a sixth chamber consists of an anti-oxidant to prevent the body from harmful reactions [1], [2]. Key words: micro-capsule, chamber, non-ionic surfactant, hydrogen peroxide. Introduction In the present scenario, environment is threatened by air pollution due to addition of harmful substances, poisonous gases and smoke that are released in the surrounding air from industries which are working on chemicals such as nitrogen dioxide, sulphur dioxide etc. To live a healthy life, fresh air is very important that is free from various poisonous gasses and other pollutants. Many devices like respirators and rebreathers are used to provide oxygen by absorbing carbon di-oxide and protect the user from respiratory problems but these devices are limited by the rate at which they provide oxygen and the conditions under which they are used. -
Chemistry Lab Hygiene Plan
UNIVERSITY OF MAINE Department of Chemistry CHEMICAL HYGIENE PLAN October, 2001 Contents I. Personal Protective Equipment .. 3 II. Storage of Chemicals .. 6 III. Disposal of Chemicals .. 16 IV. Reading MSDS .. 19 V. Emergencies and the Emergency Action Plan .. 26 VI. Standard Operating Guidelines .. 33 VII. General Housekeeping and Prudent Practices .. 40 2 I. Laboratory Clothing and Personal Protective Equipment A. Dressing for safety in the laboratory Individuals should prepare for a safe laboratory experience by dressing appropriately for laboratory work. Appropriate clothing includes the following: • Shoes should fully cover the feet to protect against spills; no open-toed shoes or sandals are permitted, and shoes with mesh inserts (such as athletic shoes) are not recommended. One may choose to keep a pair of sturdy leather shoes in the laboratory to change into upon arrival. • Trousers or skirts falling below the knee are preferred; if shorter garments are worn, a lab coat or apron of below knee length is required. Preferred materials are resistant polyester, cotton or wool, since ordinary polyester and acrylics may be dissolved by common laboratory solvents. • Neckties, if worn, should be firmly clipped to the shirt or confined inside a lab coat or apron. • Loose, flowing garments and scarves should be avoided; they may easily pick up spills or trail through a burner flame. • In a laboratory where open flames may be used, long hair should be confined. • Loose jewelry should be avoided, since it may catch on equipment. Also avoid ornate rings that can damage protective gloves or make wearing or removing gloves difficult B. Protective Equipment Every laboratory must have available, and workers must be trained in the use of, safety goggles, face masks, lab coats or aprons, gloves, and reaction shields. -
Standardal /Z<-Z
Hamilton Ui StandardAl HANL1r0N STNTVI) Bi;.TVGircr1h VP0FT SVHCA, 5712 1 0 L 'K-KY-o LaIUI P~FrcX.-19F TEST2 ?i0&at CONrxyhCT NO. TIAS 9-8159 NASA Aid!,zj.. SACECAFT CF.CErR ,_eb-r 1970 Prepared Byi/kA / 70 L.A. Wilis, axrer.mwtal Enineer Pae Aproved ByA1"" /Z<-Z -;' W. A. Blezhcr0 Chiet Pa tc Advanced -nginee.rin ONUMBE) AHRU) U NASA CR OR ?MX OR AD NUMBER) (CATEGORY) Hamilton L Standard cnisni _ This report contairs test results defining the operating chsractcristics of lithin peroxide to the extcnt required to quantify system level ponalties. The effects of chemical caulysts, bed cooling, che.,ical Panufacturing tech uiques, opera ing conditions, and cheaica) handling jroc Curea are evaluated. ii! StandardHamilton i5U TAlBLE OF CO_&E!PS Section me No. 1.0 SUMM4ARY 1 2 .0 INTRODUCTION 3 3.0 PROGRAM DEFINITION 3.1 Program Objectives 4 3.2 Test Objectives 4 3.3 Program Description 5 3.4 Test Conitions T 3.5 Test Facility 7 3.6 - Test Hardware 12 3.7 Planned Test Sequence 18 3.8 Test.Results 21 ho TEST DATA PRESENTATION 22 4.1 Performance Data 22 4.2 Chemical Analysis Data 1o6 5.0 PERFOrd4ICE ANALYSIS 109 5.1 Catalyst Evaluation 109 5.2 Bed Cooling Evaluation 134 5.3 Procedural Test Evaluation 0h5 5.4 Off Design Test Evaluation 153 5.5 End Item Canister Evaluation 157 5.6 Li 2O2 System Penalty Evaluation 163 6.0 RECOM ENDED FUTURE EFFORT 165 7.0 APPENDIX 167 7.1 Specification for Lithium Peroxide 167 Manufacturing 7.2 Specification for Lithium Peroxide Storage a68 7.3 Specification for Lithium Peroxide 170 Cartridge Loading iv Standard 5712 LIST OP TABLFS Table No. -
Transport of Dangerous Goods
ST/SG/AC.10/1/Rev.16 (Vol.I) Recommendations on the TRANSPORT OF DANGEROUS GOODS Model Regulations Volume I Sixteenth revised edition UNITED NATIONS New York and Geneva, 2009 NOTE The designations employed and the presentation of the material in this publication do not imply the expression of any opinion whatsoever on the part of the Secretariat of the United Nations concerning the legal status of any country, territory, city or area, or of its authorities, or concerning the delimitation of its frontiers or boundaries. ST/SG/AC.10/1/Rev.16 (Vol.I) Copyright © United Nations, 2009 All rights reserved. No part of this publication may, for sales purposes, be reproduced, stored in a retrieval system or transmitted in any form or by any means, electronic, electrostatic, magnetic tape, mechanical, photocopying or otherwise, without prior permission in writing from the United Nations. UNITED NATIONS Sales No. E.09.VIII.2 ISBN 978-92-1-139136-7 (complete set of two volumes) ISSN 1014-5753 Volumes I and II not to be sold separately FOREWORD The Recommendations on the Transport of Dangerous Goods are addressed to governments and to the international organizations concerned with safety in the transport of dangerous goods. The first version, prepared by the United Nations Economic and Social Council's Committee of Experts on the Transport of Dangerous Goods, was published in 1956 (ST/ECA/43-E/CN.2/170). In response to developments in technology and the changing needs of users, they have been regularly amended and updated at succeeding sessions of the Committee of Experts pursuant to Resolution 645 G (XXIII) of 26 April 1957 of the Economic and Social Council and subsequent resolutions. -
Data Sheet According to 1907/2006/EC, Article 31 Printing Date 19.07.2021 Revision: 19.07.2021
Page 1/8 Safety data sheet according to 1907/2006/EC, Article 31 Printing date 19.07.2021 Revision: 19.07.2021 SECTION 1: Identification of the substance/mixture and of the company/undertaking · 1.1 Product identifier · Trade name: Sodium peroxide, min. 93% (ACS) · Item number: 93-1050 · CAS Number: 1313-60-6 · EC number: 215-209-4 · Index number: 011-003-00-1 · 1.2 Relevant identified uses of the substance or mixture and uses advised against No further relevant information available. · 1.3 Details of the supplier of the safety data sheet · Manufacturer/Supplier: Strem Chemicals, Inc. 7 Mulliken Way NEWBURYPORT, MA 01950 USA [email protected] · Further information obtainable from: Technical Department · 1.4 Emergency telephone number: EMERGENCY: CHEMTREC: + 1 (800) 424-9300 During normal opening times: +1 (978) 499-1600 SECTION 2: Hazards identification · 2.1 Classification of the substance or mixture · Classification according to Regulation (EC) No 1272/2008 d~ GHS03 flame over circle Ox. Sol. 1 H271 May cause fire or explosion; strong oxidiser. d~ GHS05 corrosion Skin Corr. 1A H314 Causes severe skin burns and eye damage. · 2.2 Label elements · Labelling according to Regulation (EC) No 1272/2008 The substance is classified and labelled according to the CLP regulation. · Hazard pictograms d~d~ GHS03 GHS05 · Signal word Danger · Hazard-determining components of labelling: sodium peroxide · Hazard statements H271 May cause fire or explosion; strong oxidiser. (Contd. on page 2) GB 44.1.1 Page 2/8 Safety data sheet according to 1907/2006/EC, Article 31 Printing date 19.07.2021 Revision: 19.07.2021 Trade name: Sodium peroxide, min. -
The History of Dräger Johann Heinrich Dräger (1847–1917) Dr
D The History of Dräger Johann Heinrich Dräger (1847–1917) Dr. Bernhard Dräger (1870–1928) Dr. Heinrich Dräger (1898–1986) Contents 04 The Early Years: From Inventor’s Workshop to Medical and Safety Technology Specialist 10 Turbulent Times: Between Innovation Challenges and Political Constraints 20 New Beginnings: Transformation to a Modern Technology Group 30 Globalization: Realignment as a Global Technology Leader Dr. Christian Dräger (*1934) Theo Dräger (*1938) Stefan Dräger (*1963) Technology for Life for over 120 years Dräger is technology for life. Every day we take on the responsibility and put all our passion, know-how and experience into making life better: With outstanding, pioneering technology which is 100 percent driven by life. We do it for all the people around the world who entrust their lives to our technology, for the environment and for our common future. The key to the continued success of the Company, based in Lübeck, Germany, is its clear focus on the promising growth industries of medical and safety technology, its early expansi- on to international markets, and above all, the trust it has built and maintains with custo- mers, employees, shareholders, and the general public. The Company has always been managed by entrepreneurial members of the Dräger family, who have responsibly met new challenges while never losing sight of the vision: Johann Heinrich Dräger, Dr. Bernhard Dräger, Dr. Heinrich Dräger, Dr. Christian Dräger, Theo Dräger, and now Stefan Dräger. Healthy growth has consistently remained the main objective of the family business and shapes decisions within the Company even now. Founded in 1889 by Johann Heinrich Dräger, the family business has been headed in the fifth generation by CEO Stefan Dräger since 2005. -
(10) Patent No.: US 6458183 B1
USOO6458183B1 (12) United States Patent (10) Patent No.: US 6,458,183 B1 Phillips et al. (45) Date of Patent: Oct. 1, 2002 (54) METHOD FOR PURIFYING RUTHENIUM FOREIGN PATENT DOCUMENTS AND RELATED PROCESSES JP 5-177137 * 7/1993 (75) Inventors: James E. Phillips, Somerville, NJ JP 10-273327 * 10/1999 (US); Len D. Spaulding, Newark, DE OTHER PUBLICATIONS (US) Translation of Japan 5-177137, Jul. 20, 1993.* Z. Naturforsch, A Method for the Preparation of Anhydrous (73) Assignee: Colonial Metals, Inc., Elkton, MD Ruthenium (VIII) Oxide, Journal of Science, 36b, 395 (US) (1981), no month. (*) Notice: Subject to any disclaimer, the term of this * cited by examiner patent is extended or adjusted under 35 Primary Examiner Steven Bos U.S.C. 154(b) by 0 days. (74) Attorney, Agent, or Firm- Pillsbury Winthrop, LLP (57) ABSTRACT (21) Appl. No.: 09/655,307 The present invention provides a method for purifying (22) Filed: Sep. 5, 2000 ruthenium Sources to obtain high purity ruthenium metal without the need for high temperature processing, expensive Related U.S. Application Data reagents, complex Series of wet processes, or expensive (60) Provisional application No. 60/152,342, filed on Sep. 7, equipment. According to the present invention, a gas Stream 1999. including OZone (O) is brought into contact with a ruthe (51) Int. Cl. ................................................ C01G 55/00 nium Source, Such as a commercial ruthenium metal Sponge, (52) U.S. Cl. ............................................ 75/631; 75/710 in one or more reaction vessels. The OZone reacts with the (58) Field of Search .......................... 75/363, 369, 631, ruthenium present in the ruthenium Source to form ruthe 75/710 nium tetraoxide (RuO), a compound that is a gas at the reaction conditions. -
Notable Reactivity of Acetonitrile Towards Li2o2/Lio2 Probed By
Topics in Catalysis https://doi.org/10.1007/s11244-018-1072-5 ORIGINAL ARTICLE Notable Reactivity of Acetonitrile Towards Li2O2/LiO2 Probed by NAP XPS During Li–O2 Battery Discharge Tatiana K. Zakharchenko1 · Alina I. Belova1 · Alexander S. Frolov1 · Olesya O. Kapitanova1 · Juan‑Jesus Velasco‑Velez2 · Axel Knop‑Gericke2,5 · Denis Vyalikh3,4 · Daniil M. Itkis1 · Lada V. Yashina1 © Springer Science+Business Media, LLC, part of Springer Nature 2018 Abstract One of the key factors responsible for the poor cycleability of Li–O2 batteries is a formation of byproducts from irreversible reactions between electrolyte and discharge product Li 2O2 and/or intermediate LiO2. Among many solvents that are used as electrolyte component for Li–O2 batteries, acetonitrile (MeCN) is believed to be relatively stable towards oxidation. Using near ambient pressure X-ray photoemission spectroscopy (NAP XPS), we characterized the reactivity of MeCN in the Li–O2 battery. For this purpose, we designed the model electrochemical cell assembled with solid electrolyte. We discharged it first in O2 and then exposed to MeCN vapor. Further, the discharge was carried out in O2 + MeCN mixture. We have dem- onstrated that being in contact with Li–O2 discharge products, MeCN oxidizes. This yields species that are weakly bonded to the surface and can be easily desorbed. That’s why they cannot be detected by the conventional XPS. Our results suggest that the respective chemical process most probably does not give rise to electrode passivation but can decrease considerably the Coulombic efficiency of the battery. Keywords Li–O2 battery · In situ NAP XPS · Acetonitrile · Side reactions 1 Introduction Li–O2 batteries promise extraordinary high specific energy that makes them interesting for the next generation power technologies [1, 2]. -
United States Patent Office Patented May 26, 964 1
3,134,646 United States Patent Office Patented May 26, 964 1. 2 3,134,646 anhydrous lithium peroxide. The rapid drying step PREPARATION 6Fiff UM PEROXIDE. serves not only to effect the removal of water added Ricardo O. Bach, Gastonia, N.C., assignor to Lithium through the water solutions of the reactants and, addi Corporation of America, inc., New York, N.Y., a cor tionally, formed in the course of the reaction, but serves, poration of Minnesota also, and quite surprisingly, to bring about the important No Drawing, Filed Jan. 5, 1962, Set. No. 166,395 function of effecting rapid transfer of the active oxygen 10 Claims. (CI. 23-184) of the hydrogen peroxide to the lithium hydroxide to consummate formation of the desired lithium peroxide. This invention relates to an improved method of pro The lithium hydroxide (which term also includes ducing substantially anhydrous lithium peroxide, and to O lithium hydroxide hydrates such as lithium hydroxide the product produced thereby. monohydrate) is most advantageously used in the form Methods for the production of substantially anhydrous of a strong to substantially saturated aqueous solution, lithium peroxide have long been known in the art. More for instance, from about 8 or 10 to 12% concentration. recently, improvements in such methods have been pro In those instances where the resulting lithium hydroxide posed as disclosed, for instance, in U.S. Patents Nos. 5 solutions contain insoluble impurities as, for instance, 2,448,485 and 2,962,358. However, each of the methods lithium carbonate, it is desirable to filter the solutions disclosed in these patents has certain significant disad to remove said impurities so as to bring about greater vantages, particularly from an economic standpoint, purity of the final substantially anhydrous lithium which make their utilization in commercial operations peroxide. -
Potassium Superoxide (KO2) 1
Potassium Superoxide (KO2) 1. OTHER NAMES a. Potassium Dioxide b. Potassium hyperoxide 2. CAS NO. 12030-88-5 3. FORMULA WEIGHT 71.10 gm/mole 4. SPECIFICATION Sr SPECIFICATION POWDER SHEET GRANULES I GRANULES II No. 1. Appearance Pale Yellow Pale Yellow Pale Yellow Pale Yellow 2. KO2 content (%) min 96 90 82.5 96 3. Copper content (%) -- 0.25 0.25 0.25 4. CO2 Evolution (ml/gm) 220 Min 170 Min 190 -200 220-230 5. CO2 Evolution (ml/gm) max 6 12 12 6 6. Sizes (mm) NA L:313-318/B:216-221 / T:5.5-6 3.5-5.6 3.5-5.6 7. Weight (gm) 380-400 --- --- --- 8. Dust content (passing through 125 μ sieve ---- NA 0.5 0.5 (%) max SUPARNA CHEMICALS LTD 54 A Mittal Tower, Nariman Point, Mumbai India. Phone No: 022-22027446/7/8/9 Email Id: [email protected] [email protected] Potassium Superoxide (KO2) 5. REACTIVITY Potassium superoxide is a strong oxidizing agent and reacts explosively with organic materials. 6. SOLUBILITY Potassium superoxide is soluble in ethers and hydrocarbons. 7. STABILITY Potassium superoxide reacts readily with atmospheric moisture to form potassium hydroxide and oxygen is liberated. It should be stored in hermetically sealed condition under dry nitrogen. 8. PACKAGING a. 20 kgs in steel drums b. Other custom packing available SUPARNA CHEMICALS LTD 54 A Mittal Tower, Nariman Point, Mumbai India. Phone No: 022-22027446/7/8/9 Email Id: [email protected] [email protected] Potassium Superoxide (KO2) 9. SHIPPING INFORMATION a. -
Material Safety Data Sheet
MSDS003 Oxygen-Generating Canister MATERIAL SAFETY DATA SHEET 1. Product and Company Identification LABEL IDENTIFIER: Oxygen–Generating Canister PRODUCT IDENTIFIER: P/N 92908 Canister, Navy Oxygen Breathing Apparatus, Type ll Quick Starting P/N 95710 Canister, One Hour Oxygen Breathing Apparatus, Chemox®, Quick Starting P/N 10012477 Canister, One Hour Quick Starting with One Candle for MSA Canada P/N 10065537 Canister, Chemox® International PRODUCT DESCRIPTION: This device is an oxygen generating escape breathing apparatus containing potassium superoxide and a chlorate candle for ignition. COMPANY IDENTIFICATION: MINE SAFETY APPLIANCES 1100 Cranberry Woods Drive Cranberry Township, PA 16066 CUSTOMER SERVICE: 1-800-MSA-2222 (8:30 am – 5:00 pm, local US time) EMERGENCY: 1-800-255-3924 (CHEM-TEL, INC.) 2. Composition/Information on Ingredients % Synonym(s) Canister Body Contents: Approx. 1100 grams Potassium superoxide (CAS 12030-88-5) 100 KO2 Oxygen Candle (In lower part of canister): 50 grams Sodium chlorate (CAS 7775-09-9) <90 NaClO3 Barium peroxide (CAS 1304-29-6) <10 BaO2 Flash Powder (CAS 7778-74-7) <0.1 KClO4 OSHA REGULATORY STATUS: Hazardous by definition of Hazard Communication Standard, 29 CFR 1910.1200. 3. Hazards Identification EMERGENCY OVERVIEW: Canister is kidney shaped, approximately 8.72 inches high, 6.88 inches wide and 2.75 inches thick, weighing about 4.5 pounds with no odor. Material in canister is a strong oxidizer, contact with combustible material may cause fire. Material reacts vigorously with water generating heat, oxygen and corrosive solution. Material causes eye and possible skin burns. PHYSICAL HAZARD: KO2: Strong water reactive oxidizer, reacts violently with water generating oxygen heat and caustic potassium hydroxide solution. -
The ABC's of the Reactions Between Nitric Oxide, Superoxide
Oxygen'99 Sunrise Free Radical School 1 The ABC’s of the Reactions between Nitric Oxide, Superoxide, Peroxynitrite and Superoxide Dismutase Joe Beckman Department of Anesthesiology The University of Alabama at Birmingham [email protected] The interplay between nitric oxide and superoxide to form peroxynitrite is a major biological process that competes in a remarkably subtle fashion with superoxide dismutase in vivo. The complex interactions between superoxide, nitric oxide reveals some extraordinary features about the difficulties of effectively scavenging of superoxide in a biological system. The discovery of dominant mutations in the cytosolic Cu,Zn SOD leading to the selective death of motor neurons in ALS highlights how subtle the scavenging of superoxide can be in the presence of low concentrations of nitric oxide. In the 1980’s, the following reaction became the dominant explanation for how superoxide was toxic in vivo. While the Haber-Weiss reaction became a commonly accepted mechanism of oxidant injury, it suffers many limitations. The reduction step with superoxide is slow and can easily Joe Beckman 1 Oxygen'99 Sunrise Free Radical School 2 be substituted by other reductants such as ascorbate. The source of catalytic iron in vivo is still uncertain, and many forms of chelated iron do not catalyze this reaction. The reaction of ferrous iron with hydrogen peroxide is slow and once formed, hydroxyl radical is too reactive to diffuse more than a few nanometers. Finally, the toxicity of hydroxyl radical is far from certain. While it is a strong oxidant, it may be too reactive to be generally toxic.