(10) Patent No.: US 6458183 B1
Total Page:16
File Type:pdf, Size:1020Kb
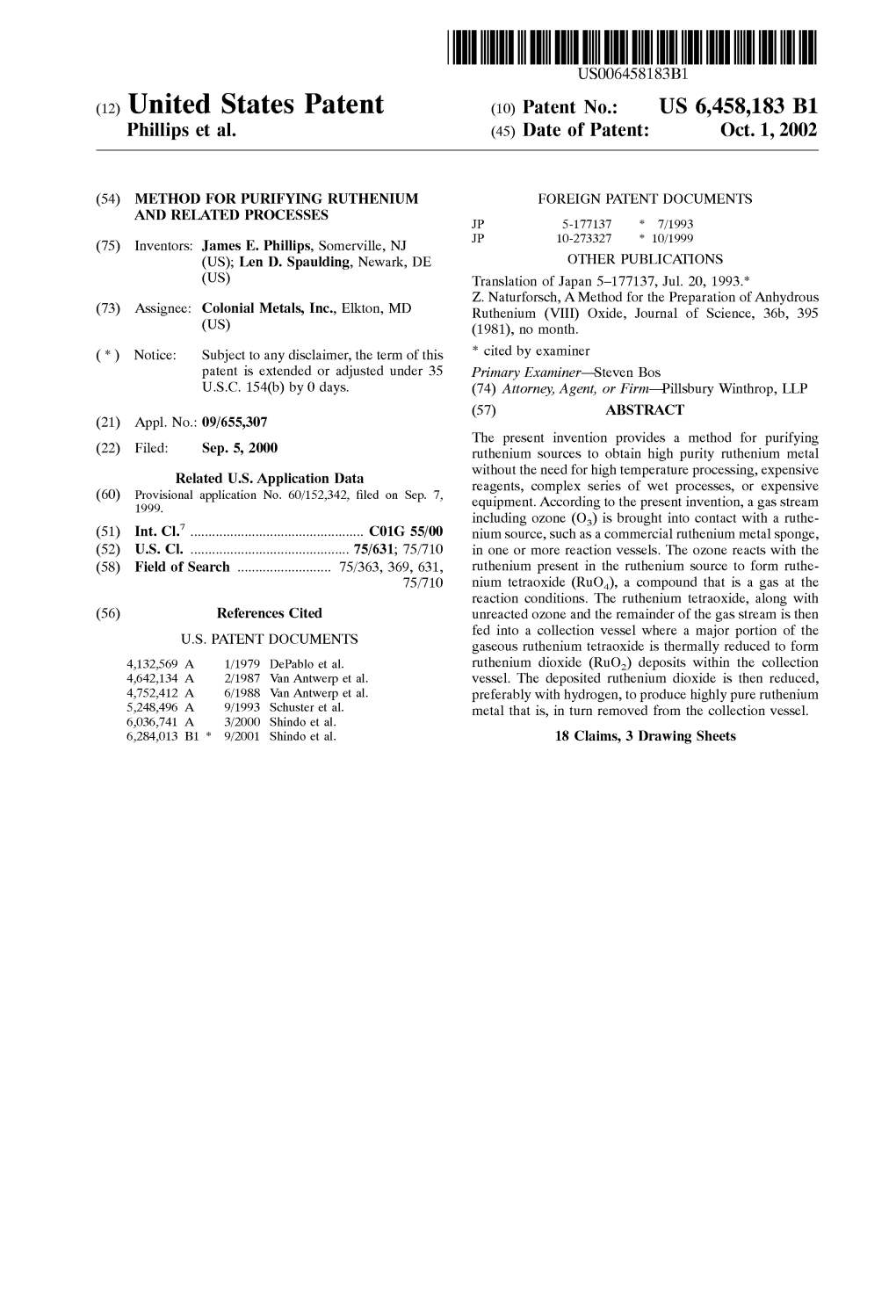
Load more
Recommended publications
-
Data Sheet According to 1907/2006/EC, Article 31 Printing Date 19.07.2021 Revision: 19.07.2021
Page 1/8 Safety data sheet according to 1907/2006/EC, Article 31 Printing date 19.07.2021 Revision: 19.07.2021 SECTION 1: Identification of the substance/mixture and of the company/undertaking · 1.1 Product identifier · Trade name: Sodium peroxide, min. 93% (ACS) · Item number: 93-1050 · CAS Number: 1313-60-6 · EC number: 215-209-4 · Index number: 011-003-00-1 · 1.2 Relevant identified uses of the substance or mixture and uses advised against No further relevant information available. · 1.3 Details of the supplier of the safety data sheet · Manufacturer/Supplier: Strem Chemicals, Inc. 7 Mulliken Way NEWBURYPORT, MA 01950 USA [email protected] · Further information obtainable from: Technical Department · 1.4 Emergency telephone number: EMERGENCY: CHEMTREC: + 1 (800) 424-9300 During normal opening times: +1 (978) 499-1600 SECTION 2: Hazards identification · 2.1 Classification of the substance or mixture · Classification according to Regulation (EC) No 1272/2008 d~ GHS03 flame over circle Ox. Sol. 1 H271 May cause fire or explosion; strong oxidiser. d~ GHS05 corrosion Skin Corr. 1A H314 Causes severe skin burns and eye damage. · 2.2 Label elements · Labelling according to Regulation (EC) No 1272/2008 The substance is classified and labelled according to the CLP regulation. · Hazard pictograms d~d~ GHS03 GHS05 · Signal word Danger · Hazard-determining components of labelling: sodium peroxide · Hazard statements H271 May cause fire or explosion; strong oxidiser. (Contd. on page 2) GB 44.1.1 Page 2/8 Safety data sheet according to 1907/2006/EC, Article 31 Printing date 19.07.2021 Revision: 19.07.2021 Trade name: Sodium peroxide, min. -
CHEMICAL STORAGE SEGREGATION GUIDELINES Incompatible Chemicals Should Always Be Handled and Stored So That They Do Not Accidentally Come in Contact with Each Other
Laboratory Safety Reminders January 2007 ♦ Mount Holyoke College – Environmental Health and Safety CHEMICAL STORAGE SEGREGATION GUIDELINES Incompatible chemicals should always be handled and stored so that they do not accidentally come in contact with each other. This list is not complete, nor are all compatibilities shown. These materials can react to produce excessive heat, harmful vapors, and/or other deadly reactions. Always know the hazards and incompatibilities of a chemical before using it. Chemicals Avoid Accidental Contact With Acetic acid Chromic acid, nitric acid, permanganates, peroxides Hydroxyl-containing compounds such as perchloric acid, Acetic anhydride ethylene glycol Concentrated nitric acid and sulfuric acid mixtures, peroxides (i.e. Acetone peracetic acid solution, hydrogen peroxide) Acetylene Chlorine, bromine, copper, silver, fluorine, mercury Alkali, alkaline earth and strongly electropositive metals (powered Carbon dioxide, carbon tetrachloride and other chlorinated aluminum, magnesium, sodium, hydrocarbons potassium) Mercury, chlorine, calcium hypochlorite, iodine, bromine, hydrogen Ammonia (anhydrous) fluoride Acids, metal powders, flammable liquids, chlorates, nitrates, sulfur, Ammonium nitrate finely divided organics, combustibles Aniline Nitric acid, hydrogen peroxide Arsenical compounds Any reducing agent Azides Acids Ammonia, acetylene, butadiene, butane, other petroleum gases, Bromine sodium carbide, turpentine, benzene, finely divided metals Calcium oxide Water Carbon activated Calcium hypochlorite, other -
Chemical Name Federal P Code CAS Registry Number Acutely
Acutely / Extremely Hazardous Waste List Federal P CAS Registry Acutely / Extremely Chemical Name Code Number Hazardous 4,7-Methano-1H-indene, 1,4,5,6,7,8,8-heptachloro-3a,4,7,7a-tetrahydro- P059 76-44-8 Acutely Hazardous 6,9-Methano-2,4,3-benzodioxathiepin, 6,7,8,9,10,10- hexachloro-1,5,5a,6,9,9a-hexahydro-, 3-oxide P050 115-29-7 Acutely Hazardous Methanimidamide, N,N-dimethyl-N'-[2-methyl-4-[[(methylamino)carbonyl]oxy]phenyl]- P197 17702-57-7 Acutely Hazardous 1-(o-Chlorophenyl)thiourea P026 5344-82-1 Acutely Hazardous 1-(o-Chlorophenyl)thiourea 5344-82-1 Extremely Hazardous 1,1,1-Trichloro-2, -bis(p-methoxyphenyl)ethane Extremely Hazardous 1,1a,2,2,3,3a,4,5,5,5a,5b,6-Dodecachlorooctahydro-1,3,4-metheno-1H-cyclobuta (cd) pentalene, Dechlorane Extremely Hazardous 1,1a,3,3a,4,5,5,5a,5b,6-Decachloro--octahydro-1,2,4-metheno-2H-cyclobuta (cd) pentalen-2- one, chlorecone Extremely Hazardous 1,1-Dimethylhydrazine 57-14-7 Extremely Hazardous 1,2,3,4,10,10-Hexachloro-6,7-epoxy-1,4,4,4a,5,6,7,8,8a-octahydro-1,4-endo-endo-5,8- dimethanonaph-thalene Extremely Hazardous 1,2,3-Propanetriol, trinitrate P081 55-63-0 Acutely Hazardous 1,2,3-Propanetriol, trinitrate 55-63-0 Extremely Hazardous 1,2,4,5,6,7,8,8-Octachloro-4,7-methano-3a,4,7,7a-tetra- hydro- indane Extremely Hazardous 1,2-Benzenediol, 4-[1-hydroxy-2-(methylamino)ethyl]- 51-43-4 Extremely Hazardous 1,2-Benzenediol, 4-[1-hydroxy-2-(methylamino)ethyl]-, P042 51-43-4 Acutely Hazardous 1,2-Dibromo-3-chloropropane 96-12-8 Extremely Hazardous 1,2-Propylenimine P067 75-55-8 Acutely Hazardous 1,2-Propylenimine 75-55-8 Extremely Hazardous 1,3,4,5,6,7,8,8-Octachloro-1,3,3a,4,7,7a-hexahydro-4,7-methanoisobenzofuran Extremely Hazardous 1,3-Dithiolane-2-carboxaldehyde, 2,4-dimethyl-, O- [(methylamino)-carbonyl]oxime 26419-73-8 Extremely Hazardous 1,3-Dithiolane-2-carboxaldehyde, 2,4-dimethyl-, O- [(methylamino)-carbonyl]oxime. -
Sodium Peroxide Hazard Summary Identification Reason for Citation How to Determine If You Are Being Exposed Workpla
Common Name: SODIUM PEROXIDE CAS Number: 1313-60-6 RTK Substance number: 1718 DOT Number: UN 1504 Date: January 1987 Revision: May 2002 ------------------------------------------------------------------------- ------------------------------------------------------------------------- HAZARD SUMMARY WORKPLACE EXPOSURE LIMITS * Sodium Peroxide can affect you when breathed in. No occupational exposure limits have been established for * Contact can severely irritate and burn the skin and eyes Sodium Peroxide. This does not mean that this substance is with possible eye damage. not harmful. Safe work practices should always be followed. * Breathing Sodium Peroxide can irritate the nose, throat and lungs causing coughing, wheezing and/or shortness of WAYS OF REDUCING EXPOSURE breath. * Where possible, enclose operations and use local exhaust * Sodium Peroxide is a REACTIVE CHEMICAL and an ventilation at the site of chemical release. If local exhaust EXPLOSION HAZARD. ventilation or enclosure is not used, respirators should be worn. IDENTIFICATION * Wear protective work clothing. Sodium Peroxide is a yellowish-white powder. It is used as a * Wash thoroughly immediately after exposure to Sodium bleaching agent, disinfectant, laboratory chemical, and in the Peroxide. production of other chemicals. * Post hazard and warning information in the work area. In addition, as part of an ongoing education and training REASON FOR CITATION effort, communicate all information on the health and * Sodium Peroxide is on the Hazardous Substance List safety hazards of Sodium Peroxide to potentially exposed because it is cited by DOT and NFPA. workers. * This chemical is on the Special Health Hazard Substance List because it is REACTIVE. * Definitions are provided on page 5. HOW TO DETERMINE IF YOU ARE BEING EXPOSED The New Jersey Right to Know Act requires most employers to label chemicals in the workplace and requires public employers to provide their employees with information and training concerning chemical hazards and controls. -
MSDS Material Safety Data Sheet
For RICCA, SpectroPure, Red Bird, and Solutions Plus Brands Emergency Contact(24 hr) -- CHEMTREC® Domestic: 800-424-9300 International: 703-527-3887 (SODIUM) ACETATE BUFFER SOLUTIONS, IRON BUFFER MSDS Material Safety Data Sheet Section 1: Chemical Product and Company Identification Catalog Number: 50, 51, 52, A-107, A000070, AX-1032, AX-1062, IX-919, R0056000, SA000070, SA000080 Product Identity: (SODIUM) ACETATE BUFFER SOLUTIONS, IRON BUFFER Manufacturer's Name: Emergency Contact(24 hr) -- CHEMTREC® RICCA CHEMICAL COMPANY LLC Domestic: 800-424-9300 International: 703-527-3887 CAGE Code: 4TCW6, 0V553, 4XZQ2 Address: Telephone Number For Information: 448 West Fork Dr 817-461-5601 Arlington, TX 76012 Date Prepared: 8/13/99 Revision: 11 Last Revised: 07/16/2013 Date Printed: 04/09/2015 5:05:40 pm Section 2. Composition/Information on Ingredients Component CAS Registry # Concentration ACGIH TLV OSHA PEL 6 - 42% (w/v) Not Available Not Available Sodium Acetate Trihydrate 6131-90-4 Not Available Not Available 10 - 50% (v/v) 10 ppm 10 ppm Acetic Acid 64-19-7 25 mg/m3 25 mg/m3 Balance Not Available Not Available Water, Deionized 7732-18-5 Not Available Not Available Section 3: Hazard Identification Emergency Overview: Danger! Corrosive liquid. May be fatal if swallowed. Causes severe burns to all areas of contact. Harmful if inhaled. Inhalation may cause lung and tooth damage. Immediately wash areas of contact with plenty of water for at least 15 minutes. If ingested, give large quantity of water. Do not induce vomiting. Target Organs: eyes, skin, respiratory system, teeth. Eye Contact: Eye contact may cause severe eye damage followed by loss of sight. -
Acutely / Extremely Hazardous Waste List
Acutely / Extremely Hazardous Waste List Federal P CAS Registry Acutely / Extremely Chemical Name Code Number Hazardous 4,7-Methano-1H-indene, 1,4,5,6,7,8,8-heptachloro-3a,4,7,7a-tetrahydro- P059 76-44-8 Acutely Hazardous 6,9-Methano-2,4,3-benzodioxathiepin, 6,7,8,9,10,10- hexachloro-1,5,5a,6,9,9a-hexahydro-, 3-oxide P050 115-29-7 Acutely Hazardous Methanimidamide, N,N-dimethyl-N'-[2-methyl-4-[[(methylamino)carbonyl]oxy]phenyl]- P197 17702-57-7 Acutely Hazardous 1-(o-Chlorophenyl)thiourea P026 5344-82-1 Acutely Hazardous 1-(o-Chlorophenyl)thiourea 5344-82-1 Extemely Hazardous 1,1,1-Trichloro-2, -bis(p-methoxyphenyl)ethane Extemely Hazardous 1,1a,2,2,3,3a,4,5,5,5a,5b,6-Dodecachlorooctahydro-1,3,4-metheno-1H-cyclobuta (cd) pentalene, Dechlorane Extemely Hazardous 1,1a,3,3a,4,5,5,5a,5b,6-Decachloro--octahydro-1,2,4-metheno-2H-cyclobuta (cd) pentalen-2- one, chlorecone Extemely Hazardous 1,1-Dimethylhydrazine 57-14-7 Extemely Hazardous 1,2,3,4,10,10-Hexachloro-6,7-epoxy-1,4,4,4a,5,6,7,8,8a-octahydro-1,4-endo-endo-5,8- dimethanonaph-thalene Extemely Hazardous 1,2,3-Propanetriol, trinitrate P081 55-63-0 Acutely Hazardous 1,2,3-Propanetriol, trinitrate 55-63-0 Extemely Hazardous 1,2,4,5,6,7,8,8-Octachloro-4,7-methano-3a,4,7,7a-tetra- hydro- indane Extemely Hazardous 1,2-Benzenediol, 4-[1-hydroxy-2-(methylamino)ethyl]- 51-43-4 Extemely Hazardous 1,2-Benzenediol, 4-[1-hydroxy-2-(methylamino)ethyl]-, P042 51-43-4 Acutely Hazardous 1,2-Dibromo-3-chloropropane 96-12-8 Extemely Hazardous 1,2-Propylenimine P067 75-55-8 Acutely Hazardous 1,2-Propylenimine 75-55-8 Extemely Hazardous 1,3,4,5,6,7,8,8-Octachloro-1,3,3a,4,7,7a-hexahydro-4,7-methanoisobenzofuran Extemely Hazardous 1,3-Dithiolane-2-carboxaldehyde, 2,4-dimethyl-, O- [(methylamino)-carbonyl]oxime 26419-73-8 Extemely Hazardous 1,3-Dithiolane-2-carboxaldehyde, 2,4-dimethyl-, O- [(methylamino)-carbonyl]oxime. -
Safety Data Sheet: Sodium Peroxide
safety data sheet according to Regulation (EC) No. 1907/2006 (REACH), amended by 2015/830/EU Sodium peroxide ≥95 %, p.a., ACS, granulated article number: 4412 date of compilation: 09.01.2017 Version: 1.0 en SECTION 1: Identification of the substance/mixture and of the company/undertaking 1.1 Product identifier Identification of the substance Sodium peroxide Article number 4412 Registration number (REACH) This information is not available. Index No 011-003-00-1 EC number 215-209-4 CAS number 1313-60-6 1.2 Relevant identified uses of the substance or mixture and uses advised against Identified uses: laboratory chemical 1.3 Details of the supplier of the safety data sheet Carl Roth GmbH + Co KG Schoemperlenstr. 3-5 D-76185 Karlsruhe Germany Telephone: +49 (0) 721 - 56 06 0 Telefax: +49 (0) 721 - 56 06 149 e-mail: [email protected] Website: www.carlroth.de Competent person responsible for the safety data : Department Health, Safety and Environment sheet e-mail (competent person) : [email protected] 1.4 Emergency telephone number Emergency information service Poison Centre Munich: +49/(0)89 19240 SECTION 2: Hazards identification 2.1 Classification of the substance or mixture Classification according to Regulation (EC) No 1272/2008 (CLP) Classification acc. to GHS Section Hazard class Hazard class and cat- Hazard egory state- ment 2.14 oxidising solid (Ox. Sol. 1) H271 3.2 skin corrosion/irritation (Skin Corr. 1A) H314 3.3 serious eye damage/eye irritation (Eye Dam. 1) H318 Malta (en) Page 1 / 12 safety data sheet according to Regulation (EC) No. -
A New Method of Determination for the Trace Ruthenium in High Purity P이 Ladium by Neutron Activation Analysis
DAEHAN HWAHAK HWOEJEE (Journal of the Korean Chemical Society) Vol. 15, Number 4, 1971 Printed in Republic of Korea 방사화 분석에 의한 고순도 팔라듐 금속중의 미량 루테늄에 관한 새로운 정량법 원자력 연구소 화학 연구실 이 철 • 임영창 • 엄경자 서강대학교 이공대학 화학과 정구순 (1971. 5.11 接受 ) A New Method of Determination for the Trace Ruthenium in High Purity P이 ladium by Neutron Activation Analysis Chui Lee, * Yung Chang Yim, * Kyung Ja Uhm* and Koo Soon Chung** ^Chemistry Division, Atomic Energy Research Institute, Seoul, Korea. ** Department of Chemistry^ Sogang University, Seoul, Korea. (Received May 11, 고 971) 요약 고 순도 팔라듐 금속 (99.9%)에 함유된 루테늄 함량을 K4RuS7部 -) 105Rh 의 핵반응에 의하 여 생성된 N5Rh 의 방사능을 계축하므 로써 결정하였다 . 원자 로에 서 조사된 팔라듐 시료와 루테늄 표준시료를 각각 왕수 처리 및 과산화나트 륨으로 용융 시 킨다 음 如 5Rh 을 음이 온 및 양이 온 교환수지로 분리 하였다 . 팔라 듐 시 료로 부터 얻 은 KRh 의 방사능을 루테 늄 표준시료로 부터 얻 은 l^Rh 의 방사능과 비 교 하므로서 루테늄의 함량올 결정하였다 . 본 방법 으로 구한 루테 늄의 검 출한계 는 팔라듐 10 mg을 시 료로 하였을 때 약 1 ppm 이 었으며 이 검 출 감도는 102RU(偽7)103Ru의 핵반응을 사용한 종래의 방사화 분석에 비해 약 40배 더 예민하였다 . Abstract Ruthenium content in highly purified palladium metal (99.9%) was determined by counting 105Rh nuclide which was produced by 104Ru (n, 105Rh nuclear reaction. Palladium sample and ruthenium standard were irradiated by neutron with the Pneumatic Transfer System of TRIGA MARK H reactor. Palladium and ruthenium were dissolved by treating with aqua-regia and by fusing with sodium peroxide flux respectively. -
Environmental Health & Safety
Environmental Health & Safety Chemical Safety Program Chemical Segregation & Incompatibilities Guidelines Class of Recommended Incompatible Possible Reaction Examples Chemical Storage Method Materials If Mixed Corrosive Acids Mineral Acids – Separate cabinet or storage area Flammable Liquids Heat Chromic Acid away from potential water Flammable Solids Hydrogen Chloride sources, i.e. under sink Bases Hydrochloric Acid Oxidizers Gas Generation Nitric Acid Poisons Perchloric Acid Violent Phosphoric Acid Reaction Sulfuric Acid Corrosive Bases/ Ammonium Hydroxide Separate cabinet or storage area Flammable Liquids Heat Caustics Sodium Hydroxide away from potential water Flammable Solids Sodium Bicarbonate sources, i.e. under sink Acids Gas Generation Oxidizers Poisons Violent Reaction Explosives Ammonium Nitrate Secure location away from Flammable Liquids Nitro Urea other chemicals Oxidizers Picric Acid Poisons Explosion Hazard Trinitroaniline Acids Trinitrobenzene Bases Trinitrobenzoic Acid Trinitrotoluene Urea Nitrate Flammable Liquids Acetone Grounded flammable storage Acids Fire Hazard Benzene cabinet of flammable storage Bases Diethyl Ether refrigerator Oxidizers Methanol Poisons Heat Ethanol Toluene Violent Glacial Acetic Acid Reaction Flammable Solids Phosphorus Separate dry cool area Acids Fire Hazard Magnesium Bases Heat Oxidizers Violent Poisons Reaction Sodium Hypochlorite Spill tray that is separate from Reducing Agents Fire Oxidizers Benzoyl Peroxide flammable and combustible Flammables Hazard Potassium Permanganate materials Combustibles -
Chemical Incompatibilities
Chemical Incompatibilities Incompatibilities Chromic acid, nitric acid, hydroxyl compounds, ethylene glycol, Acetic acid perchloric acid, peroxides, permanganates Acetylene Chlorine, bromine, copper, fluorine, silver, mercury Acetone Concentrated nitric and sulfuric acid mixtures Alkali and alkaline earth metals (such as Water, carbon tetrachloride or other chlorinated hydrocarbons, powdered aluminum or magnesium, calcium, carbon dioxide, halogens lithium, sodium, potassium) Mercury (in manometers, for example), chlorine, calcium Ammonia (anhydrous) hypochlorite, iodine, bromine, hydrofluoric acid (anhydrous) Acids, powdered metals, flammable liquids, chlorates, nitrites, Ammonium nitrate sulfur, finely divided organic combustible materials Aniline Nitric acid, hydrogen peroxide Arsenical materials Any reducing agent Azides Acids Bromine See chlorine Calcium oxide Water Carbon (activated) Calcium hypochlorite, all oxidizing agents Carbon tetrachloride Sodium Ammonium salts, acids, powdered metals, sulfur, finely divided Chlorates organic or combustible materials Acetic acid, naphthalene, camphor, glycerol, alcohol, flammable Chromic acid and chromium liquids in general Ammonia, acetylene, butadiene, butane, methane, propane (or Chlorine other petroleum gases), hydrogen, sodium carbide, benzene, finely divided metals, turpentine Chlorine dioxide Ammonia, methane, phosphine, hydrogen sulfide Copper Acetylene, hydrogen peroxide Cumene hydroperoxide Acids (organic or inorganic) Cyanides Acids Ammonium nitrate, chromic acid, hydrogen peroxide, -
Sample Digestion Methods for the Determination of Traces of Precious Metals by Spectrometric Techniques
ANALYTICAL SCIENCES JULY 2002, VOL. 18 737 2002 © The Japan Society for Analytical Chemistry Reviews Sample Digestion Methods for the Determination of Traces of Precious Metals by Spectrometric Techniques Maria BALCERZAK Department of Analytical Chemistry, Warsaw University of Technology, Noakowskiego 3, 00-664 Warsaw, Poland Recent advances in digestion methods used in the analysis of precious metal samples by spectrometric techniques are reviewed. The applicability of a fire assay, a wet acid treatment, chlorination and alkaline oxidizing fusion to a quantitative recovery of metals from various materials is discussed. Data on the precious metal contents obtained by using particular digestion methods as well as UV-VIS spectrophotometry, atomic absorption spectrometry, atomic emission spectrometry and inductively coupled plasma mass spectrometry in the examination of various samples are tabulated. (Received November 26, 2001; Accepted April 4, 2002) 1 Introduction 737 5 Oxidizing Fusion 746 2 Fire Assay 738 6 Conclusions 748 3 Wet Acid Treatment 739 7 References 748 4 Chlorination 741 sensitivity, selectivity and reliability have been carried out. 1 Introduction Spectrometric techniques, ultra-violet visible (UV-VIS) spectrophotometry, atomic absorption spectrometry (both flame The members of the platinum group metals (PGM) (ruthenium, (FAAS) and graphite furnace (GFAAS) techniques), inductively rhodium, palladium, osmium, iridium and platinum) and gold coupled plasma combined with atomic emission spectrometry are called “precious” or “noble” metals. These names have (ICP-AES) or mass spectrometry (ICP-MS), are widely applied roots in the unique physical and chemical properties of the in the analysis of a variety of samples containing noble metals metals, owing to their low abundance and high economic value. -
Defect Chemistry in Alkali Peroxides and Superoxides
Defect Chemistry in Alkali Peroxides and Superoxides Von der Fakultät Chemie der Universität Stuttgart zur Erlangung der Würde eines Doktors der Naturwissenschaften (Dr. rer. nat.) genehmigte Abhandlung Vorgelegt von Oliver Gerbig aus Darmstadt Hauptberichter: Prof. Dr. J. Maier Mitberichter: Prof. Dr. J. Bill Prüfungsvorsitzender: Prof. Dr. J. van Slageren Tag der Einreichung: 28. Februar 2014 Tag der mündlichen Prüfung: 7. Mai 2014 Max-Planck-Institut für Festkörperforschung Stuttgart 2014 Erklärung Die vorliegende Doktorarbeit wurde vom Autor selbst in der Abteilung von Prof. J. Maier am Max- Planck-Institut für Festkörperforschung im Zeitraum von Januar 2010 bis März 2014 angefertigt. Der Inhalt ist die eigene Arbeit des Autors, Ausnahmen sind gekennzeichnet und wurden noch nicht zur Erlangung einer Qualifizierung oder eines Titels an der einer akademischen Institution eingereicht. Stuttgart, den 28. Februar 2014 Oliver Gerbig Declaration The work described in this thesis was carried out by the author in the Department of Prof. J. Maier at the Max Planck Institute for Solid State Research from January 2010 to March 2014. The content is the original work of the author except where indicated otherwise and has not been previously submitted to obtain any other degree or qualification at any academic institution. Stuttgart, 28th February 2014 Oliver Gerbig Table of Contents 1 Introduction and Motivation ........................................................................................................... 1 1.1 Inorganic Peroxides and