Preparation of Papers for AIAA Technical Conferences
Total Page:16
File Type:pdf, Size:1020Kb
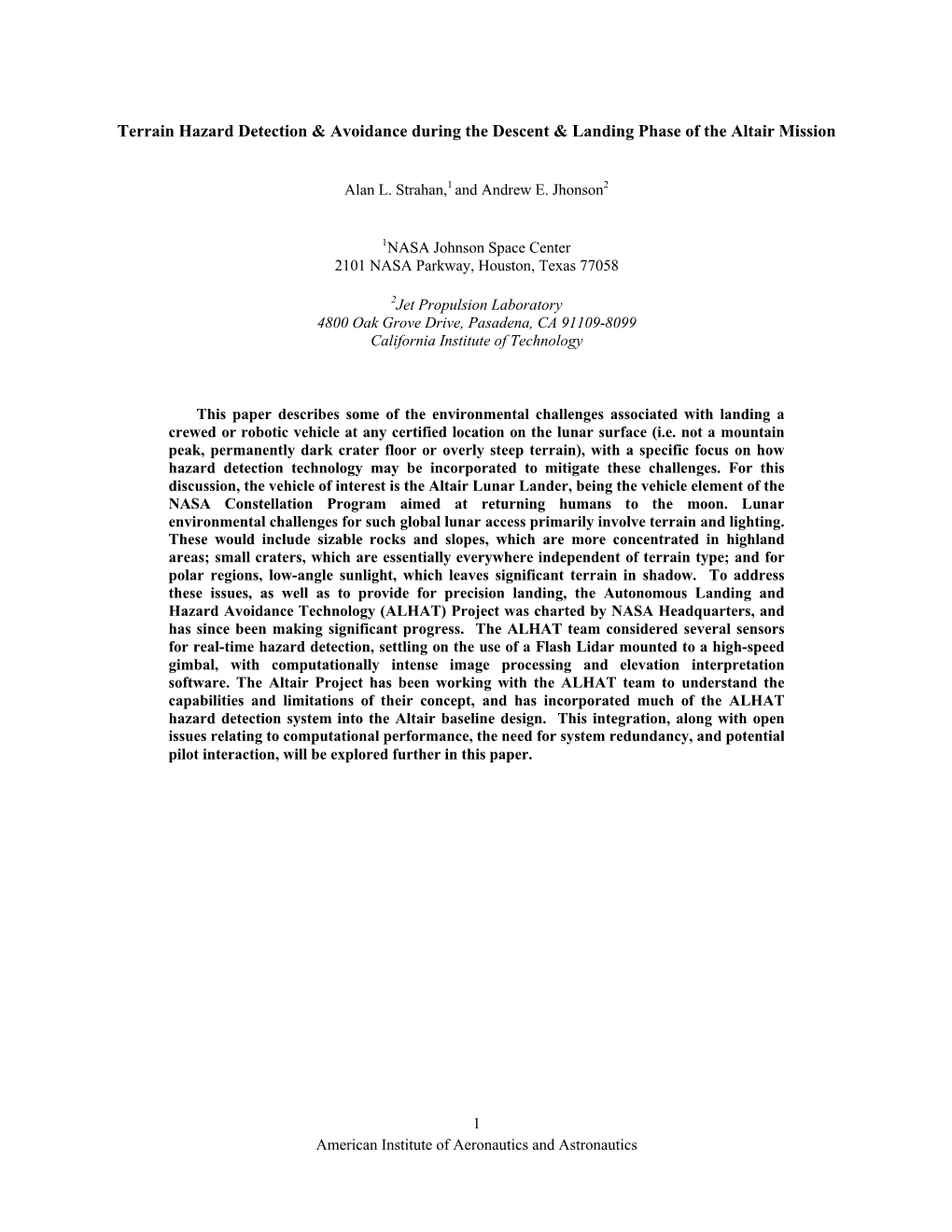
Load more
Recommended publications
-
Gryphon: a Flexible Lunar Lander Design to Support a Semi-Permanent Lunar Outpost
AIAA SPACE 2007 Conference & Exposition AIAA 2007-6169 18 - 20 September 2007, Long Beach, California The Gryphon: A Flexible Lunar Lander Design to Support a Semi-Permanent Lunar Outpost Dale Arney1, Joseph Hickman,1 Philip Tanner,1 John Wagner,1 Marc Wilson,1 and Dr. Alan Wilhite2 Georgia Institute of Technology/National Institute of Aerospace, Hampton, VA, 23666 A lunar lander is designed to provide safe, reliable, and continuous access to the lunar surface by the year 2020. The NASA Exploration System Architecture is used to initially define the concept of operations, architecture elements, and overall system requirements. The design evaluates revolutionary concepts and technologies to improve the performance and safety of the lunar lander while minimizing the associated cost using advanced systems engineering capabilities and multi-attribute decision making techniques. The final design is a flexible (crew and/or cargo) lander with a side-mounted minimum ascent stage and a separate stage to perform lunar orbit insertion. Nomenclature ACC = Affordability and Cost Criterion AFM = Autonomous Flight Manager AHP = Analytic Hierarchy Process ALHAT = Autonomous Landing and Hazard Avoidance Technology ATP = Authority to Proceed AWRS = Advanced Air & Water Recovery System CDR = Critical Design Review CER = Cost Estimating Relationship CEV = Crew Exploration Vehicle CH4 = Methane DDT&E = Design, Development, Testing and Evaluation DOI = Descent Orbit Insertion DSM = Design Structure Matrix ECLSS = Environmental Control & Life Support System -
Extending NASA™S Exploration Systems Architecture Towards Long
SpaceOps 2006 Conference AIAA 2006-5746 Extending NASA’s Exploration Systems Architecture towards Long - term Crewed Moon and Mars Operations Wilfried K. Hofstetter *, Paul D. Wooster †, Edward F. Crawley ‡ Massac husetts Institute of Technology 77 Massachusetts Avenue , Cambridge, MA, 02139 This pape r presents a baseline strategy for extending lunar crew transportation system operations as outlined in NASA’s Exploration Systems Architecture Study (ESAS) report towards longer -stay lunar surface operations and conjunction class Mars missions. The analys is of options for commonality between initial lunar sortie operations and later Moon and Mars exploration missions is essential for reducing life -cycle cost and pr oviding low - investment / high -return options for extending exploration capabilities soon afte r the 7 th human lunar landing . The analysis is also intended to inform the development of the human lunar lander and other exploration system elements by identifying enabling requirements for extension of the lunar crew tr ansportation system. The baseline strategy outlined in this paper was generated using a three -step process : the analysis of exploration objectives and scenarios, identification of functional and operational extension options , and the conceptual design of a set of preferred extension option s. Extension options include (but are not limited to) the use of the human lunar lander as outpost for extended stays, and Mars crew transportation using evolved Crew Exploration Vehicle ( CEV ) and human lander crew compartments. Although t he results presen ted in this paper are based on the ES AS elements , the conclusions drawn in this paper are generally applicable provided the same l unar transportation mode (lunar orbit rendezvous) is used . -
4. Lunar Architecture
4. Lunar Architecture 4.1 Summary and Recommendations As defined by the Exploration Systems Architecture Study (ESAS), the lunar architecture is a combination of the lunar “mission mode,” the assignment of functionality to flight elements, and the definition of the activities to be performed on the lunar surface. The trade space for the lunar “mission mode,” or approach to performing the crewed lunar missions, was limited to the cislunar space and Earth-orbital staging locations, the lunar surface activities duration and location, and the lunar abort/return strategies. The lunar mission mode analysis is detailed in Section 4.2, Lunar Mission Mode. Surface activities, including those performed on sortie- and outpost-duration missions, are detailed in Section 4.3, Lunar Surface Activities, along with a discussion of the deployment of the outpost itself. The mission mode analysis was built around a matrix of lunar- and Earth-staging nodes. Lunar-staging locations initially considered included the Earth-Moon L1 libration point, Low Lunar Orbit (LLO), and the lunar surface. Earth-orbital staging locations considered included due-east Low Earth Orbits (LEOs), higher-inclination International Space Station (ISS) orbits, and raised apogee High Earth Orbits (HEOs). Cases that lack staging nodes (i.e., “direct” missions) in space and at Earth were also considered. This study addressed lunar surface duration and location variables (including latitude, longi- tude, and surface stay-time) and made an effort to preserve the option for full global landing site access. Abort strategies were also considered from the lunar vicinity. “Anytime return” from the lunar surface is a desirable option that was analyzed along with options for orbital and surface loiter. -
A Review of Nasa's Exploration
A REVIEW OF NASA’S EXPLORATION PROGRAM IN TRANSITION: ISSUES FOR CONGRESS AND INDUSTRY HEARING BEFORE THE SUBCOMMITTEE ON SPACE AND AERONAUTICS COMMITTEE ON SCIENCE, SPACE, AND TECHNOLOGY HOUSE OF REPRESENTATIVES ONE HUNDRED TWELFTH CONGRESS FIRST SESSION MARCH 30, 2011 Serial No. 112–8 Printed for the use of the Committee on Science, Space, and Technology ( Available via the World Wide Web: http://science.house.gov U.S. GOVERNMENT PRINTING OFFICE 65–305PDF WASHINGTON : 2011 For sale by the Superintendent of Documents, U.S. Government Printing Office Internet: bookstore.gpo.gov Phone: toll free (866) 512–1800; DC area (202) 512–1800 Fax: (202) 512–2104 Mail: Stop IDCC, Washington, DC 20402–0001 COMMITTEE ON SCIENCE, SPACE, AND TECHNOLOGY HON. RALPH M. HALL, Texas, Chair F. JAMES SENSENBRENNER, JR., EDDIE BERNICE JOHNSON, Texas Wisconsin JERRY F. COSTELLO, Illinois LAMAR S. SMITH, Texas LYNN C. WOOLSEY, California DANA ROHRABACHER, California ZOE LOFGREN, California ROSCOE G. BARTLETT, Maryland DAVID WU, Oregon FRANK D. LUCAS, Oklahoma BRAD MILLER, North Carolina JUDY BIGGERT, Illinois DANIEL LIPINSKI, Illinois W. TODD AKIN, Missouri GABRIELLE GIFFORDS, Arizona RANDY NEUGEBAUER, Texas DONNA F. EDWARDS, Maryland MICHAEL T. MCCAUL, Texas MARCIA L. FUDGE, Ohio PAUL C. BROUN, Georgia BEN R. LUJA´ N, New Mexico SANDY ADAMS, Florida PAUL D. TONKO, New York BENJAMIN QUAYLE, Arizona JERRY MCNERNEY, California CHARLES J. ‘‘CHUCK’’ FLEISCHMANN, JOHN P. SARBANES, Maryland Tennessee TERRI A. SEWELL, Alabama E. SCOTT RIGELL, Virginia FREDERICA S. WILSON, Florida STEVEN M. PALAZZO, Mississippi HANSEN CLARKE, Michigan MO BROOKS, Alabama ANDY HARRIS, Maryland RANDY HULTGREN, Illinois CHIP CRAVAACK, Minnesota LARRY BUCSHON, Indiana DAN BENISHEK, Michigan VACANCY SUBCOMMITTEE ON SPACE AND AERONAUTICS HON. -
Lunar Science Workshop
National Aeronautics and Space Administration LUNAR SCIENCE WORKSHOP NASA ADVISORY COUNCIL WORKSHOP ON SCIENCE ASSOCIATED WITH THE LUNAR EXPLORATION ARCHITECTURE FEBRUARY 27–MARCH 2, 2007 • TEMPE, ARIZONA TABLE OF CONTENTS Foreword . 3 Organizing Committee . 7 Executive Summary and Key Assessments . 9 Introduction and Overview of the Workshop . 17 The Vision for Space Exploration and the Role of Science . 21 The Global Exploration Strategy . 23 The Lunar Exploration Architecture . 27 Assessment of Potential Science Activities . 31 Findings of the Workshop . 35 Astrophysics . 36 Earth Science . 39 Heliophysics . 41 Planetary Protection . 43 Planetary Science . 46 Outreach Messages and Highlights of the Workshop . 53 Concluding Statement . 57 Appendices: Science Subcommittee Workshop Findings . 59 Appendix 1: Astrophysics . 59 Appendix 2: Earth Science . 67 Appendix 3: Heliophysics . 83 Appendix 4: Planetary Protection . 91 Appendix 5: Planetary Science . 99 Appendix 6: Detailed Program . 119 Appendix 7: List of Acronyms Used in the Report . 131 2 FOREWORD From February 27 through March 2, 2007, the NASA Advisory Council Science Committee conducted the “Workshop on Science Associated with the Lunar Exploration Architecture” at the Fiesta Inn Resort in Tempe, Arizona . The workshop was planned and timed to feed into ongoing efforts by NASA’s Lunar Architecture Team (LAT) to develop an exploration architecture for the return of humans to the Moon by 2020 in accordance with the Vision for Space Exploration (VSE) and the NASA Authorization Act of 2005 . The goals of the workshop were to: (1) ensure that NASA’s exploration strategy, architecture, and hardware development enable the best and appropriately integrated science activities in association with the return of humans to the Moon and subsequent exploration of Mars; (2) bring diverse constituencies together to hear, discuss, and assess science activities and priorities for science enabled by the exploration architecture; and (3) identify needed science programs and technology developments. -
Paper Number
https://ntrs.nasa.gov/search.jsp?R=20080013530 2019-08-30T04:06:05+00:00Z View metadata, citation and similar papers at core.ac.uk brought to you by CORE provided by NASA Technical Reports Server 08ICES-0132 Life Support Systems for Lunar Landers Molly Anderson NASA Copyright © 2008 SAE International ABSTRACT exploration work. This mission could deliver crewmembers to many different locations on the lunar Engineers designing life support systems for NASA’s surface for the maximum range of exploration activities next Lunar Landers face unique challenges. As with any and support intravehicular activity (IVA) and vehicle that enables human spaceflight, the needs of the extravehicular activity (EVA) for the crew. The second crew drive most of the lander requirements. The lander mission is a delivery of crew to the lunar Outpost, is also a key element of the architecture NASA will sometimes referred to as a “Down and Out” mission for implement in the Constellation program. Many the lander. The lander again delivers the crew to the requirements, constraints, or optimization goals will be lunar surface, but in this case they almost immediately driven by interfaces with other projects, like the Crew transfer to the lunar Outpost or some other transport Exploration Vehicle, the Lunar Surface Systems, and the vehicle. For current design work, this mission is Extravehicular Activity project. Other challenges in the assumed to go to a polar location. The lander is left life support system will be driven by the unique location unmanned in a dormant state until it is time for the crew of the vehicle in the environments encountered to return home, which could be up to 210 days. -
Lunar Outpost the Challenges of Establishing a Human Settlement on the Moon Erik Seedhouse Lunar Outpost the Challenges of Establishing a Human Settlement on the Moon
Lunar Outpost The Challenges of Establishing a Human Settlement on the Moon Erik Seedhouse Lunar Outpost The Challenges of Establishing a Human Settlement on the Moon Published in association with Praxis Publishing Chichester, UK Dr Erik Seedhouse, F.B.I.S., As.M.A. Milton Ontario Canada SPRINGER±PRAXIS BOOKS IN SPACE EXPLORATION SUBJECT ADVISORY EDITOR: John Mason, M.Sc., B.Sc., Ph.D. ISBN 978-0-387-09746-6 Springer Berlin Heidelberg New York Springer is part of Springer-Science + Business Media (springer.com) Library of Congress Control Number: 2008934751 Apart from any fair dealing for the purposes of research or private study, or criticism or review, as permitted under the Copyright, Designs and Patents Act 1988, this publication may only be reproduced, stored or transmitted, in any form or by any means, with the prior permission in writing of the publishers, or in the case of reprographic reproduction in accordance with the terms of licences issued by the Copyright Licensing Agency. Enquiries concerning reproduction outside those terms should be sent to the publishers. # Praxis Publishing Ltd, Chichester, UK, 2009 Printed in Germany The use of general descriptive names, registered names, trademarks, etc. in this publication does not imply, even in the absence of a speci®c statement, that such names are exempt from the relevant protective laws and regulations and therefore free for general use. Cover design: Jim Wilkie Project management: Originator Publishing Services, Gt Yarmouth, Norfolk, UK Printed on acid-free paper Contents Preface ............................................. xiii Acknowledgments ...................................... xvii About the author....................................... xix List of ®gures ........................................ xxi List of tables ........................................ -
Human Spaceflight Health Systems for the Constellation Project Richard (Rick) A
Send information for publication on this page to: Mark Campbell, M.D. 420 N. Collegiate Dr., #300 Paris, TX 75460 SPACE MEDICINE ASSOCIATION NEWS [email protected] Human Spaceflight Health Systems for the Constellation Project Richard (Rick) A. Scheuring, DO, MS, FAAFP, small, mini-medical kit will be flown to handle medical equipment will need interfaces for Jeffrey (Jeff) A. Jones, MD, MS, FACS, FACPM, the usual expected physiological adaptation to power, data, and pressurized breathing gas and James D. (JD) Polk, DO, MS, FACOEP microgravity, and any minor contingencies. (with or without oxygen concentration) for Historically, the Apollo medical kit certain medical conditions or for environmen- The Constellation Program Office has weighed 3.8 pounds. However, the Apollo kits tal contingencies (depressurization, fire, toxic been tasked with developing the exploration were based on 3 male crewmembers for a total release). The crew will don Personal Protective vehicular architecture. NASA, with the prime mission duration of less than 2 weeks. Orion is Equipment (PPE) during a toxic spill clean up contractor Lockheed-Martin, will build The based on mixed-gender crews of 4-6 for much or a dust-ridden activity. A crewmember with Crew Exploration Vehicle or CEV (Orion) over longer missions. Apollo was a "best guess," a significant illness or injury will be stabilized the next 5 years. The architecture includes ini- based on limited space medical knowledge using lunar lander-based medical equipment tial flights of the CEV to ISS and allows 3-6 and would be insufficient to meet even in preparation for ascent and transfer to the crewmembers to be rotated to the station, be- Constellation Level 1 Medical Care. -
From Apollo LM to Altair: Design, Environments, Infrastructure, Missions, and Operations
AIAA SPACE 2009 Conference & Exposition AIAA 2009-6404 14 - 17 September 2009, Pasadena, California From Apollo LM to Altair: Design, Environments, Infrastructure, Missions, and Operations Marc M. Cohen∗ Northrop Grumman Corporation, El Segundo, CA 90245 Abstract This essay presents a comparison between the Apollo Lunar Module (LM) and the current concepts and requirements for the Altair Lunar Lander. The basis of comparison reflects the difference between the Apollo Program, pursuing a Cold War era “Flag and Footsteps” mission, and the Constellation Program creating a more expansive program of exploration leading to a permanent human presence on the moon. The specific areas of comparison derive largely from the changes in mission philosophy and exploration strategy – not from technology or engineering. These factors illuminate the differences in the current design drivers for the Altair compared to the Apollo LM. Nomenclature ALARA As Low As Reasonably Achievable, refers to radiation exposure. ALHAT Autonomous Lander Hazard Avoidance Technology. Altair NASA’s Lunar Lander to return crew and cargo to the moon. Ascent Module The Altair module with the flight crew station where the crew pilot the vehicle; the Ascent Module launches from the surface to return the crew to the Orion in LLO, leaving the DM behind. Ascent Stage The Apollo LM module with the flight crew station where the crew pilot the vehicle. The Ascent Stage launches from the surface to return the crew to the CSM in LLO, leaving the Descent Stage behind. BFO Blood forming organs. CARD Constellation Architecture Requirements Document, NASA CxP-70000. CEV Crew Exploration Vehicle. CM The Apollo Command Module, also the Orion Crew Module. -
4. Lunar Architecture
4. Lunar Architecture 4.1 Summary and Recommendations As defined by the Exploration Systems Architecture Study (ESAS), the lunar architecture is a combination of the lunar “mission mode,” the assignment of functionality to flight elements, and the definition of the activities to be performed on the lunar surface. The trade space for the lunar “mission mode,” or approach to performing the crewed lunar missions, was limited to the cislunar space and Earth-orbital staging locations, the lunar surface activities duration and location, and the lunar abort/return strategies. The lunar mission mode analysis is detailed in Section 4.2, Lunar Mission Mode. Surface activities, including those performed on sortie- and outpost-duration missions, are detailed in Section 4.3, Lunar Surface Activities, along with a discussion of the deployment of the outpost itself. The mission mode analysis was built around a matrix of lunar- and Earth-staging nodes. Lunar-staging locations initially considered included the Earth-Moon L1 libration point, Low Lunar Orbit (LLO), and the lunar surface. Earth-orbital staging locations considered included due-east Low Earth Orbits (LEOs), higher-inclination International Space Station (ISS) orbits, and raised apogee High Earth Orbits (HEOs). Cases that lack staging nodes (i.e., “direct” missions) in space and at Earth were also considered. This study addressed lunar surface duration and location variables (including latitude, longi- tude, and surface stay-time) and made an effort to preserve the option for full global landing site access. Abort strategies were also considered from the lunar vicinity. “Anytime return” from the lunar surface is a desirable option that was analyzed along with options for orbital and surface loiter. -
Executive Summary
Preface The National Aeronautics and Space Administration’s (NASA’s) Exploration Systems Architecture Study (ESAS) Final Report documents the analyses and findings of the 90-day Agencywide study. Work on this study began in May 2005 and was completed in July 2005. The purpose of the study was to: • Assess the top-level Crew Exploration Vehicle (CEV) requirements and plans that will enable the CEV to provide crew transport to the International Space Station (ISS) and will accelerate the development of the CEV and crew launch system to reduce the gap between Shuttle retirement and CEV Initial Operational Capability (IOC); • Define the top-level requirements and configurations for crew and cargo launch systems to support the lunar and Mars exploration programs; • Develop a reference exploration architecture concept to support sustained human and robotic lunar exploration operations; and • Identify key technologies required to enable and significantly enhance these reference exploration systems and a reprioritization of near-term and far-term technology investments. The ESAS Final Report presents analysis and recommendations concerning technologies and potential approaches related to NASA’s implementation of the Vision for Space Explora- tion. Project and contract requirements will likely be derived, in part, from the ESAS analysis and recommendations. However, the analysis and recommendations contained herein do not represent a set of project or contract requirements and are not binding on the U.S. Government unless and until they are formally and expressly adopted as such. Details of any recommendations offered by the ESAS Final Report will be translated into implementation requirements. Moreover, the report represents the assessments and projections of the report’s authors at the time it was prepared. -
Lunar Surface Mission Operations Scenario and Considerations Larissa S. Arnold, Susan E. Torney, John D. (Doug) Rask, and Scott
Lunar Surface Mission Operations Scenario and Considerations Larissa S. Arnold, Susan E. Torney, John D. (Doug) Rask, and Scott A. Bleisath of Lyndon B. Johnson Space Center National Aeronautics and Space Administration 2101 NASA Parkway Houston, TX 77058-3696 June 1, 2006 ABSTRACT Planetary surface operations have been studied since the last visit of humans to the Moon, including conducting analog missions. Mission Operations lessons from these activities are summarized. Characteristics of forecasted surface operations are compared to current human mission operations approaches. Considerations for future designs of mission operations are assessed. INTRODUCTION National Aeronautics and Space Administration’s (NASA) efforts in human space flight are currently focused on the Space Shuttle and International Space Station (ISS) programs, with efforts beginning on the Constellation Program, in accordance with the President’s “Vision for Space Exploration” (Bush 2004). The lunar phase of the Constellation Program begins with lunar “sortie” missions that consist of up to seven days on the lunar surface. The “sortie” missions are followed by the establishment of a lunar outpost. Both the Space Shuttle and ISS programs are important to the development of a capability for human exploration beyond Low Earth Orbit (LEO). The ISS provides extensive research capabilities to determine how the human body reacts to long duration stays in space. Also, the ISS and Shuttle can serve as a limited testbed for equipment or entire systems that may be used on missions to the Moon, Mars, or to a near-Earth asteroid. It has been nearly 35 years since the Apollo astronauts visited the Moon. Future space explorers will have to re-learn how to work and live on planetary surfaces, and how to do that for extended periods of time.