Thesis Development of a Martian In-Situ Hybrid
Total Page:16
File Type:pdf, Size:1020Kb
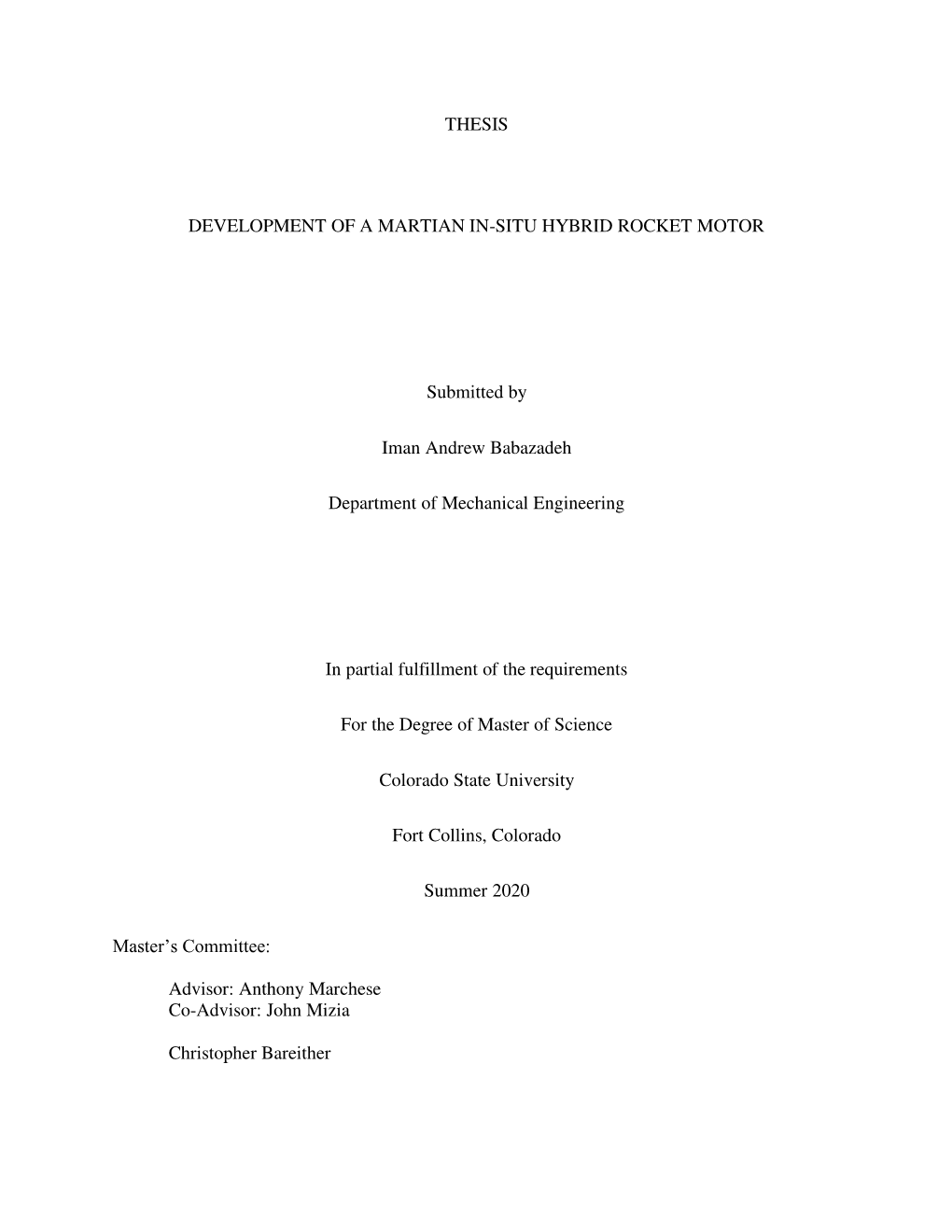
Load more
Recommended publications
-
Qualification Over Ariane's Lifetime
r bulletin 94 — may 1998 Qualification Over Ariane’s Lifetime A. González Blázquez Directorate of Launchers, ESA, Paris M. Eymard Groupe Programme CNES/Arianespace, Evry, France Introduction Similarly, the RL10 engine on the Centaur stage The primary objectives of the qualification of the Atlas launcher has been the subject of an activities performed during the operational ongoing improvement programme. About 5000 lifetime of a launcher are: tests were performed before the first flight, and – to verify the qualification status of the vehicle 4000 during the subsequent ten years. – to resolve any technical problems relating to subsystem operations on the ground or in On-going qualification activities of a similar flight. nature were started for the Ariane-3 and 4 launchers in 1986, and for Ariane-5 in 1996. Before focussing on the European family of They can be classified into two main launchers, it is perhaps informative to review categories: ‘regular’ and ‘one-off’. just one or two of the US efforts in the area of solid and liquid propulsion in order to put the Ariane-3/4 accompanying activities Ariane-related activities into context. Regular activities These activities are mainly devoted to In principle, the development programme for a launcher ends with the verification of the qualification status of the qualification phase, after which it enters operational service. In various launcher subsystems. They include the practice, however, the assessment of a launcher’s reliability is a following work packages: continuing process and qualification-type activities proceed, as an – Periodic sampling of engines: one HM7 and extension of the development programme (as is done in aeronautics), one Viking per year, tested to the limits of the over the course of the vehicle’s lifetime. -
High-Thrust In-Space Liquid Propulsion Stage: Storable Propellants
View metadata, citation and similar papers at core.ac.uk brought to you by CORE provided by Institute of Transport Research:Publications Space Propulsion 2014 – ID 2968378 High-Thrust in-Space Liquid Propulsion Stage: Storable Propellants Etienne Dumont, Alexander Kopp, Carina Ludwig, Nicole Garbers DLR, Space Launcher Systems Analysis (SART), Bremen, Germany [email protected] Abstract In the frame of a project funded by ESA, a consortium led Subscripts, Abbreviations by Avio in cooperation with Snecma, Cira, and DLR is ATV Automated Transfer Vehicle performing the preliminary design of a High-Thrust in- CDF Concurrent Design Facility Space Liquid Propulsion Stage for two different types of ECSS European Cooperation on Space manned missions beyond Earth orbit. For these missions, Standardization one or two 100 ton stages are to be used to propel a Elec assy electronic assembly manned vehicle. Three different propellant combinations; EPS Etage à propergols stockables (Ariane 5’s LOx/LH2, LOx/CH4 and MON-3/MMH are being storable propellant stage) compared. GNC Guidance Navigation and Control HTS High-Thrust Stage The preliminary design of the storable variant (MON- IF Interface 3/MMH) has been performed by DLR. The Aestus II ISS International Space Station engine with a large nozzle expansion ratio has been LEO Low Earth Orbit chosen as baseline. A first iteration has demonstrated, that LEOP Launch and Early Orbit Phase it indeed provides the best performance for the storable LH2 Liquid Hydrogen propellant combination, when considering all engines LOx Liquid Oxygen available today or which may be available in a short- to MLI Multi-Layer Insulation medium term. -
Einicke Diplom.Pdf
Zum Erlangen des akademischen Grades DIPLOMINGENIEUR (Dipl.-Ing.) Betreuer: Dr. Christian Bach Verantwortlicher Hochschullehrer: Prof. Dr. techn. Martin Tajmar Tag der Einreichung: 20.04.2021 Erster Gutachter: Prof. Dr. techn. Martin Tajmar Zweiter Gutachter: Dr. Christian Bach Hiermit erkläre ich, dass ich die von mir dem Institut für Luft-und Raumfahrttechnik der Fakultät Maschinenwesen eingereichte Diplomarbeit zum Thema Mischungsverhältnis- und Brennkammerdruckregelung eines Expander-Bleed Raketentriebwerks mit Reinforcement Learning (Mixture Ratio and Combustion Chamber Pressure Control of an Expander-Bleed Rocket Engine with Reinforcement Learning) selbstständig verfasst und keine anderen als die angegebenen Quellen und Hilfsmittel benutzt sowie Zitate kenntlich gemacht habe. Berlin, 20.04.2021 Karina Einicke Contents Nomenclature iv Acronyms vii 1. Introduction 1 1.1. Motivation . .1 1.2. Objectives and Approach . .2 2. Fundamentals of Liquid Rocket Engines 3 2.1. Control Loops . .5 2.1.1. Open-Loop Control . .5 2.1.2. Closed-Loop Control . .5 2.1.3. Reusable Liquid Rocket Engine Control . .6 2.2. Control Valves . .8 2.2.1. Flow Characteristics . .9 2.2.2. Valve Types . .9 2.3. Liquid Rocket Engine Control: Historical Background . 11 2.4. Summary . 13 3. LUMEN 15 3.1. LUMEN Components . 15 3.2. Operating Points . 17 3.3. EcosimPro/ESPSS Model . 18 3.3.1. LUMEN System Analysis . 21 3.3.2. LUMEN System Validation . 26 3.4. Summary . 27 4. Reinforcement Learning 28 4.1. Fundamentals of Reinforcement Learning . 28 4.2. Reinforcement Learning Algorithms . 31 4.2.1. Model-based and Model-free Reinforcement Learning . 31 4.2.2. Policy Optimization . -
Rocket Propulsion Fundamentals 2
https://ntrs.nasa.gov/search.jsp?R=20140002716 2019-08-29T14:36:45+00:00Z Liquid Propulsion Systems – Evolution & Advancements Launch Vehicle Propulsion & Systems LPTC Liquid Propulsion Technical Committee Rick Ballard Liquid Engine Systems Lead SLS Liquid Engines Office NASA / MSFC All rights reserved. No part of this publication may be reproduced, distributed, or transmitted, unless for course participation and to a paid course student, in any form or by any means, or stored in a database or retrieval system, without the prior written permission of AIAA and/or course instructor. Contact the American Institute of Aeronautics and Astronautics, Professional Development Program, Suite 500, 1801 Alexander Bell Drive, Reston, VA 20191-4344 Modules 1. Rocket Propulsion Fundamentals 2. LRE Applications 3. Liquid Propellants 4. Engine Power Cycles 5. Engine Components Module 1: Rocket Propulsion TOPICS Fundamentals • Thrust • Specific Impulse • Mixture Ratio • Isp vs. MR • Density vs. Isp • Propellant Mass vs. Volume Warning: Contents deal with math, • Area Ratio physics and thermodynamics. Be afraid…be very afraid… Terms A Area a Acceleration F Force (thrust) g Gravity constant (32.2 ft/sec2) I Impulse m Mass P Pressure Subscripts t Time a Ambient T Temperature c Chamber e Exit V Velocity o Initial state r Reaction ∆ Delta / Difference s Stagnation sp Specific ε Area Ratio t Throat or Total γ Ratio of specific heats Thrust (1/3) Rocket thrust can be explained using Newton’s 2nd and 3rd laws of motion. 2nd Law: a force applied to a body is equal to the mass of the body and its acceleration in the direction of the force. -
Design of a 500 Lbf Liquid Oxygen and Liquid Methane Rocket Engine for Suborbital Flight Jesus Eduardo Trillo University of Texas at El Paso, [email protected]
University of Texas at El Paso DigitalCommons@UTEP Open Access Theses & Dissertations 2016-01-01 Design Of A 500 Lbf Liquid Oxygen And Liquid Methane Rocket Engine For Suborbital Flight Jesus Eduardo Trillo University of Texas at El Paso, [email protected] Follow this and additional works at: https://digitalcommons.utep.edu/open_etd Part of the Aerospace Engineering Commons, and the Mechanical Engineering Commons Recommended Citation Trillo, Jesus Eduardo, "Design Of A 500 Lbf Liquid Oxygen And Liquid Methane Rocket Engine For Suborbital Flight" (2016). Open Access Theses & Dissertations. 767. https://digitalcommons.utep.edu/open_etd/767 This is brought to you for free and open access by DigitalCommons@UTEP. It has been accepted for inclusion in Open Access Theses & Dissertations by an authorized administrator of DigitalCommons@UTEP. For more information, please contact [email protected]. DESIGN OF A 500 LBF LIQUID OXYGEN AND LIQUID METHANE ROCKET ENGINE FOR SUBORBITAL FLIGHT JESUS EDUARDO TRILLO Master’s Program in Mechanical Engineering APPROVED: Ahsan Choudhuri, Ph.D., Chair Norman Love, Ph.D. Luis Rene Contreras, Ph.D. Charles H. Ambler, Ph.D. Dean of the Graduate School Copyright © by Jesus Eduardo Trillo 2016 DESIGN OF A 500 LBF LIQUID OXYGEN AND LIQUID METHANE ROCKET ENGINE FOR SUBORBITAL FLIGHT by JESUS EDUARDO TRILLO, B.S.ME THESIS Presented to the Faculty of the Graduate School of The University of Texas at El Paso in Partial Fulfillment of the Requirements for the Degree of MASTER OF SCIENCE Department of Mechanical Engineering THE UNIVERSITY OF TEXAS AT EL PASO December 2016 Acknowledgements Foremost, I would like to express my sincere gratitude to my advisor Dr. -
Jacques Tiziou Space Collection
Jacques Tiziou Space Collection Isaac Middleton and Melissa A. N. Keiser 2019 National Air and Space Museum Archives 14390 Air & Space Museum Parkway Chantilly, VA 20151 [email protected] https://airandspace.si.edu/archives Table of Contents Collection Overview ........................................................................................................ 1 Administrative Information .............................................................................................. 1 Biographical / Historical.................................................................................................... 1 Scope and Contents........................................................................................................ 2 Arrangement..................................................................................................................... 2 Names and Subjects ...................................................................................................... 2 Container Listing ............................................................................................................. 4 Series : Files, (bulk 1960-2011)............................................................................... 4 Series : Photography, (bulk 1960-2011)................................................................. 25 Jacques Tiziou Space Collection NASM.2018.0078 Collection Overview Repository: National Air and Space Museum Archives Title: Jacques Tiziou Space Collection Identifier: NASM.2018.0078 Date: (bulk 1960s through -
Accesso Autonomo Ai Servizi Spaziali
Centro Militare di Studi Strategici Rapporto di Ricerca 2012 – STEPI AE-SA-02 ACCESSO AUTONOMO AI SERVIZI SPAZIALI Analisi del caso italiano a partire dall’esperienza Broglio, con i lanci dal poligono di Malindi ad arrivare al sistema VEGA. Le possibili scelte strategiche del Paese in ragione delle attuali e future esigenze nazionali e tenendo conto della realtà europea e del mercato internazionale. di T. Col. GArn (E) FUSCO Ing. Alessandro data di chiusura della ricerca: Febbraio 2012 Ai mie due figli Andrea e Francesca (che ci tiene tanto…) ed a Elisabetta per la sua pazienza, nell‟impazienza di tutti giorni space_20120723-1026.docx i Author: T. Col. GArn (E) FUSCO Ing. Alessandro Edit: T..Col. (A.M.) Monaci ing. Volfango INDICE ACCESSO AUTONOMO AI SERVIZI SPAZIALI. Analisi del caso italiano a partire dall’esperienza Broglio, con i lanci dal poligono di Malindi ad arrivare al sistema VEGA. Le possibili scelte strategiche del Paese in ragione delle attuali e future esigenze nazionali e tenendo conto della realtà europea e del mercato internazionale. SOMMARIO pag. 1 PARTE A. Sezione GENERALE / ANALITICA / PROPOSITIVA Capitolo 1 - Esperienze italiane in campo spaziale pag. 4 1.1. L'Anno Geofisico Internazionale (1957-1958): la corsa al lancio del primo satellite pag. 8 1.2. Italia e l’inizio della Cooperazione Internazionale (1959-1972) pag. 12 1.3. L’Italia e l’accesso autonomo allo spazio: Il Progetto San Marco (1962-1988) pag. 26 Capitolo 2 - Nascita di VEGA: un progetto europeo con una forte impronta italiana pag. 45 2.1. Il San Marco Scout pag. -
A Pictorial History of Rockets
he mighty space rockets of today are the result A Pictorial Tof more than 2,000 years of invention, experi- mentation, and discovery. First by observation and inspiration and then by methodical research, the History of foundations for modern rocketry were laid. Rockets Building upon the experience of two millennia, new rockets will expand human presence in space back to the Moon and Mars. These new rockets will be versatile. They will support Earth orbital missions, such as the International Space Station, and off- world missions millions of kilometers from home. Already, travel to the stars is possible. Robotic spacecraft are on their way into interstellar space as you read this. Someday, they will be followed by human explorers. Often lost in the shadows of time, early rocket pioneers “pushed the envelope” by creating rocket- propelled devices for land, sea, air, and space. When the scientific principles governing motion were discovered, rockets graduated from toys and novelties to serious devices for commerce, war, travel, and research. This work led to many of the most amazing discoveries of our time. The vignettes that follow provide a small sampling of stories from the history of rockets. They form a rocket time line that includes critical developments and interesting sidelines. In some cases, one story leads to another, and in others, the stories are inter- esting diversions from the path. They portray the inspirations that ultimately led to us taking our first steps into outer space. NASA’s new Space Launch System (SLS), commercial launch systems, and the rockets that follow owe much of their success to the accomplishments presented here. -
The European Launchers Between Commerce and Geopolitics
The European Launchers between Commerce and Geopolitics Report 56 March 2016 Marco Aliberti Matteo Tugnoli Short title: ESPI Report 56 ISSN: 2218-0931 (print), 2076-6688 (online) Published in March 2016 Editor and publisher: European Space Policy Institute, ESPI Schwarzenbergplatz 6 • 1030 Vienna • Austria http://www.espi.or.at Tel. +43 1 7181118-0; Fax -99 Rights reserved – No part of this report may be reproduced or transmitted in any form or for any purpose with- out permission from ESPI. Citations and extracts to be published by other means are subject to mentioning “Source: ESPI Report 56; March 2016. All rights reserved” and sample transmission to ESPI before publishing. ESPI is not responsible for any losses, injury or damage caused to any person or property (including under contract, by negligence, product liability or otherwise) whether they may be direct or indirect, special, inciden- tal or consequential, resulting from the information contained in this publication. Design: Panthera.cc ESPI Report 56 2 March 2016 The European Launchers between Commerce and Geopolitics Table of Contents Executive Summary 5 1. Introduction 10 1.1 Access to Space at the Nexus of Commerce and Geopolitics 10 1.2 Objectives of the Report 12 1.3 Methodology and Structure 12 2. Access to Space in Europe 14 2.1 European Launchers: from Political Autonomy to Market Dominance 14 2.1.1 The Quest for European Independent Access to Space 14 2.1.3 European Launchers: the Current Family 16 2.1.3 The Working System: Launcher Strategy, Development and Exploitation 19 2.2 Preparing for the Future: the 2014 ESA Ministerial Council 22 2.2.1 The Path to the Ministerial 22 2.2.2 A Look at Europe’s Future Launchers and Infrastructure 26 2.2.3 A Revolution in Governance 30 3. -
UCLA Electronic Theses and Dissertations
UCLA UCLA Electronic Theses and Dissertations Title Minimizing hydraulic losses in additively-manufactured swirl coaxial rocket injectors via analysis-driven design methods Permalink https://escholarship.org/uc/item/7n51c078 Author Morrow, David Publication Date 2020 Peer reviewed|Thesis/dissertation eScholarship.org Powered by the California Digital Library University of California UNIVERSITY OF CALIFORNIA Los Angeles Minimizing hydraulic losses in additively-manufactured swirl coaxial rocket injectors via analysis-driven design methods A thesis submitted in partial satisfaction of the requirements for the degree Master of Science in Aerospace Engineering by David Morrow 2020 c Copyright by David Morrow 2020 ABSTRACT OF THE THESIS Minimizing hydraulic losses in additively-manufactured swirl coaxial rocket injectors via analysis-driven design methods by David Morrow Master of Science in Aerospace Engineering University of California, Los Angeles, 2020 Professor Raymond M. Spearrin, Chair Additive manufacturing (AM) has matured significantly over the past decade and become a highly attractive tool for reducing manufacturing complexity and removing traditional de- sign constraints. This is particularly desirable for rocket combustion devices which often feature hundreds of individual parts with precise tolerances. The degree to which AM can be used to improve combustion device performance, however, has been less rigorously ex- plored. In this work, hydraulic performance impacts associated with and enabled by AM are assessed for a liquid bi-propellant swirl coaxial injector. Specifically, a single-element liquid oxygen/kerosene injector based on a canonical design was manufactured from inconel using Direct Metal Laser Sintering at two different coaxial recess depths. Cold-flow testing for the as-manufactured baseline injector found a reduction in the designed discharge coefficients, which is primarily attributed to increased surface roughness inherent in the AM process. -
Desind Finding
NATIONAL AIR AND SPACE ARCHIVES Herbert Stephen Desind Collection Accession No. 1997-0014 NASM 9A00657 National Air and Space Museum Smithsonian Institution Washington, DC Brian D. Nicklas © Smithsonian Institution, 2003 NASM Archives Desind Collection 1997-0014 Herbert Stephen Desind Collection 109 Cubic Feet, 305 Boxes Biographical Note Herbert Stephen Desind was a Washington, DC area native born on January 15, 1945, raised in Silver Spring, Maryland and educated at the University of Maryland. He obtained his BA degree in Communications at Maryland in 1967, and began working in the local public schools as a science teacher. At the time of his death, in October 1992, he was a high school teacher and a freelance writer/lecturer on spaceflight. Desind also was an avid model rocketeer, specializing in using the Estes Cineroc, a model rocket with an 8mm movie camera mounted in the nose. To many members of the National Association of Rocketry (NAR), he was known as “Mr. Cineroc.” His extensive requests worldwide for information and photographs of rocketry programs even led to a visit from FBI agents who asked him about the nature of his activities. Mr. Desind used the collection to support his writings in NAR publications, and his building scale model rockets for NAR competitions. Desind also used the material in the classroom, and in promoting model rocket clubs to foster an interest in spaceflight among his students. Desind entered the NASA Teacher in Space program in 1985, but it is not clear how far along his submission rose in the selection process. He was not a semi-finalist, although he had a strong application. -
Ideas Into Hardware: a History of the Rocket Engine Test Facility
Ideas Into Hardware IDEAS INTO HARDWARE A History of the Rocket Engine Test Facility at the NASA Glenn Research Center Virginia P. Dawson National Aeronautics and Space Administration NASA Glen Research Center Cleveland, Ohio 2004 This document was generated for the NASA Glenn Research Center, in accor- dance with a Memorandum of Agreement among the Federal Aviation Administration, National Aeronautics and Space Administration (NASA), The Ohio State Historic Preservation Officer, and the Advisory Council on Historic Preservation. The City of Cleveland’s goal to expand the Cleveland Hopkins International Airport required the NASA Glenn Research Center’s Rocket Engine Test Facility, located adjacent to the airport, to be removed before this expansion could be realized. To mitigate the removal of this registered National Historic Landmark, the National Park Service stipulated that the Rocket Engine Test Facility be documented to Level I standards of the Historic American Engineering Record (HAER). This history project was initiated to fulfill and supplement that requirement. Produced by History Enterprises, Inc. Cover and text design by Diana Dickson. Library of Congress Cataloging-in-Publication Data Dawson, Virginia P. (Virginia Parker) —Ideas into hardware : a history of NASA’s Rocket Engine Test Facility / by Virginia P. Dawson. ——p.——cm. —Includes bibliographical references. —1. Rocket engines—Research—United States—History.—2.—United States. National Aeronautics and Space Administration—History.—I. Title. TL781.8.U5D38 2004 621.43'56'072077132—dc22 2004024041 Table of Contents Introduction / v 1. Carving Out a Niche / 1 2. RETF: Complex, Versatile, Unique / 37 3. Combustion Instability and Other Apollo Era Challenges, 1960s / 64 4.