Contact Mechanics of Multilayered Rough Surfaces in Tribology
Total Page:16
File Type:pdf, Size:1020Kb
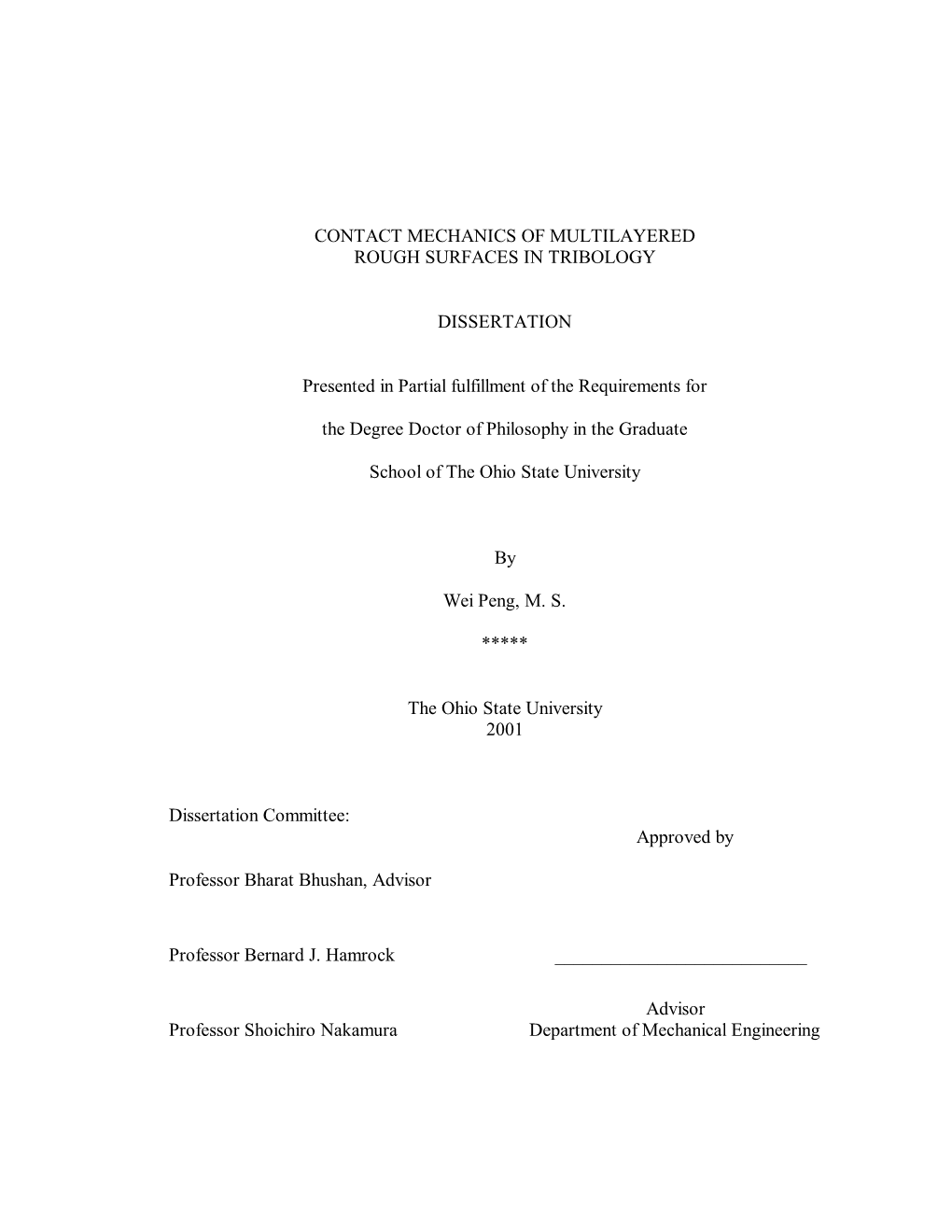
Load more
Recommended publications
-
10-1 CHAPTER 10 DEFORMATION 10.1 Stress-Strain Diagrams And
EN380 Naval Materials Science and Engineering Course Notes, U.S. Naval Academy CHAPTER 10 DEFORMATION 10.1 Stress-Strain Diagrams and Material Behavior 10.2 Material Characteristics 10.3 Elastic-Plastic Response of Metals 10.4 True stress and strain measures 10.5 Yielding of a Ductile Metal under a General Stress State - Mises Yield Condition. 10.6 Maximum shear stress condition 10.7 Creep Consider the bar in figure 1 subjected to a simple tension loading F. Figure 1: Bar in Tension Engineering Stress () is the quotient of load (F) and area (A). The units of stress are normally pounds per square inch (psi). = F A where: is the stress (psi) F is the force that is loading the object (lb) A is the cross sectional area of the object (in2) When stress is applied to a material, the material will deform. Elongation is defined as the difference between loaded and unloaded length ∆푙 = L - Lo where: ∆푙 is the elongation (ft) L is the loaded length of the cable (ft) Lo is the unloaded (original) length of the cable (ft) 10-1 EN380 Naval Materials Science and Engineering Course Notes, U.S. Naval Academy Strain is the concept used to compare the elongation of a material to its original, undeformed length. Strain () is the quotient of elongation (e) and original length (L0). Engineering Strain has no units but is often given the units of in/in or ft/ft. ∆푙 휀 = 퐿 where: is the strain in the cable (ft/ft) ∆푙 is the elongation (ft) Lo is the unloaded (original) length of the cable (ft) Example Find the strain in a 75 foot cable experiencing an elongation of one inch. -
Lubrication Chemistry Viewed from DFT-Based Concepts and Electronic Structural Principles
Int. J. Mol. Sci. 2004, 5, 13-34 International Journal of Molecular Sciences ISSN 1422-0067 © 2004 by MDPI www.mdpi.org/ijms/ Lubrication Chemistry Viewed from DFT-Based Concepts and Electronic Structural Principles Li Shenghua*, Yang He and Jin Yuansheng State Key Laboratory of Tribology, Tsinghua University, Beijing 100084, P.R. China Tel.: +86 (10) 62772509, Fax: +86 (10) 62784691, E-mail: [email protected] URL: http://www.pim.tsinghua.edu.cn/sklt/sklt.html *Author to whom correspondence should be addressed. Received: 16 April 2003 / Accepted: 16 October 2003 / Published: 26 December 2003 Abstract: Fundamental molecular issues in lubrication chemistry were reviewed under categories of solution chemistry, contact chemistry and tribochemistry. By introducing the Density Functional Theory(DFT)-derived chemical reactivity parameters (chemical potential, electronegativity, hardness, softness and Fukui function) and related electronic structural principles (electronegativity equalization principle, hard-soft acid-base principle, and maximum hardness principle), their relevancy to lubrication chemistry was explored. It was suggested that DFT, theoretical, conceptual and computational, represents a useful enabling tool to understand lubrication chemistry issues prior to experimentation and the approach may form a key step in the rational design of lubrication chemistry via computational methods. It can also be optimistically anticipated that these considerations will gestate unique DFT-based strategies to understand sophisticated tribology themes, such as origin of friction, essence of wear, adhesion in MEMS/NEMS, chemical mechanical polishing in wafer manufacturing, stress corrosion, chemical control of friction and wear, and construction of designer tribochemical systems. Keywords: Lubrication chemistry, DFT, chemical reactivity indices, electronic structural principle, tribochemistry, mechanochemistry. -
Crack Tip Elements and the J Integral
EN234: Computational methods in Structural and Solid Mechanics Homework 3: Crack tip elements and the J-integral Due Wed Oct 7, 2015 School of Engineering Brown University The purpose of this homework is to help understand how to handle element interpolation functions and integration schemes in more detail, as well as to explore some applications of FEA to fracture mechanics. In this homework you will solve a simple linear elastic fracture mechanics problem. You might find it helpful to review some of the basic ideas and terminology associated with linear elastic fracture mechanics here (in particular, recall the definitions of stress intensity factor and the nature of crack-tip fields in elastic solids). Also check the relations between energy release rate and stress intensities, and the background on the J integral here. 1. One of the challenges in using finite elements to solve a problem with cracks is that the stress field at a crack tip is singular. Standard finite element interpolation functions are designed so that stresses remain finite a everywhere in the element. Various types of special b c ‘crack tip’ elements have been designed that 3L/4 incorporate the singularity. One way to produce a L/4 singularity (the method used in ABAQUS) is to mesh L the region just near the crack tip with 8 noded elements, with a special arrangement of nodal points: (i) Three of the nodes (nodes 1,4 and 8 in the figure) are connected together, and (ii) the mid-side nodes 2 and 7 are moved to the quarter-point location on the element side. -
The Use of Artificial Intelligence in Tribology—A Perspective
lubricants Perspective The Use of Artificial Intelligence in Tribology—A Perspective Andreas Rosenkranz 1,*, Max Marian 2,* , Francisco J. Profito 3, Nathan Aragon 4 and Raj Shah 4 1 Department of Chemical Engineering, Biotechnology and Materials, University of Chile, Santiago 7820436, Chile 2 Engineering Design, Friedrich-Alexander-University Erlangen-Nuremberg (FAU), 91058 Erlangen, Germany 3 Department of Mechanical Engineering, Polytechnic School, University of São Paulo, São Paulo 17033360, Brazil; fprofi[email protected] 4 Koehler Instrument Company, Holtsville, NY 11742, USA; [email protected] (N.A.); [email protected] (R.S.) * Correspondence: [email protected] (A.R.); [email protected] (M.M.) Abstract: Artificial intelligence and, in particular, machine learning methods have gained notable attention in the tribological community due to their ability to predict tribologically relevant pa- rameters such as, for instance, the coefficient of friction or the oil film thickness. This perspective aims at highlighting some of the recent advances achieved by implementing artificial intelligence, specifically artificial neutral networks, towards tribological research. The presentation and discussion of successful case studies using these approaches in a tribological context clearly demonstrates their ability to accurately and efficiently predict these tribological characteristics. Regarding future research directions and trends, we emphasis on the extended use of artificial intelligence and machine learning concepts in the field of tribology including the characterization of the resulting surface topography and the design of lubricated systems. Keywords: artificial intelligence; machine learning; artificial neural networks; tribology 1. Introduction and Background Citation: Rosenkranz, A.; Marian, M.; There have been very recent advances in applying methods of deep or machine Profito, F.J.; Aragon, N.; Shah, R. -
Contact Mechanics in Gears a Computer-Aided Approach for Analyzing Contacts in Spur and Helical Gears Master’S Thesis in Product Development
Two Contact Mechanics in Gears A Computer-Aided Approach for Analyzing Contacts in Spur and Helical Gears Master’s Thesis in Product Development MARCUS SLOGÉN Department of Product and Production Development Division of Product Development CHALMERS UNIVERSITY OF TECHNOLOGY Gothenburg, Sweden, 2013 MASTER’S THESIS IN PRODUCT DEVELOPMENT Contact Mechanics in Gears A Computer-Aided Approach for Analyzing Contacts in Spur and Helical Gears Marcus Slogén Department of Product and Production Development Division of Product Development CHALMERS UNIVERSITY OF TECHNOLOGY Göteborg, Sweden 2013 Contact Mechanics in Gear A Computer-Aided Approach for Analyzing Contacts in Spur and Helical Gears MARCUS SLOGÉN © MARCUS SLOGÉN 2013 Department of Product and Production Development Division of Product Development Chalmers University of Technology SE-412 96 Göteborg Sweden Telephone: + 46 (0)31-772 1000 Cover: The picture on the cover page shows the contact stress distribution over a crowned spur gear tooth. Department of Product and Production Development Göteborg, Sweden 2013 Contact Mechanics in Gears A Computer-Aided Approach for Analyzing Contacts in Spur and Helical Gears Master’s Thesis in Product Development MARCUS SLOGÉN Department of Product and Production Development Division of Product Development Chalmers University of Technology ABSTRACT Computer Aided Engineering, CAE, is becoming more and more vital in today's product development. By using reliable and efficient computer based tools it is possible to replace initial physical testing. This will result in cost savings, but it will also reduce the development time and material waste, since the demand of physical prototypes decreases. This thesis shows how a computer program for analyzing contact mechanics in spur and helical gears has been developed at the request of Vicura AB. -
TRIBOLOGY Lecture 3: FRICTION
Video Course on Tribology Prof. Dr Harish Hirani Department of Mechanical Engineering Indian institute of Technology, Delhi Lecture No. # 03 Friction Welcome to the third lecture of video course on Tribology. Topic of this lecture is friction. It is interesting. We experience friction in day to day life when you walk we experience friction, when we cycle we experience friction, when we drive we experience friction. This is very common mode which we experience every day. TRIBOLOGY Lecture 3: FRICTION And often when you go to mall, we find this kind of signal or warning that slippery when the floor is wet. So, you need to be careful when you walk resending the water place as lubricant layer. Some Typical Values of Coefficient of Friction for Metals sliding on themselves Metals Sliding on themselves µ Aluminum 1.5 Copper 1.5 Copper((oxide film not penetrated) 0.5 Gold 2.5 Iron 1.2 Platinum 3 Silver 1.5 Steel(mild steel) 0.8 Steel(tool steel) 0.4 Observations: 1. μ > 1.0 2. Mild steel vs Tool steel 3. μ depends on environment. And it reduces the friction. So, we need to walk with more force. So, the overall the friction force turn out to be same. I have gone through number of books and found number of variation in coefficient of friction. So, I am just showing on the first slide of this course that typical value of coefficient friction which is often quoted in books. We say these values are static coefficient of friction or this value belongs to static coefficient of friction. -
AC Fischer-Cripps
A.C. Fischer-Cripps Introduction to Contact Mechanics Series: Mechanical Engineering Series ▶ Includes a detailed description of indentation stress fields for both elastic and elastic-plastic contact ▶ Discusses practical methods of indentation testing ▶ Supported by the results of indentation experiments under controlled conditions Introduction to Contact Mechanics, Second Edition is a gentle introduction to the mechanics of solid bodies in contact for graduate students, post doctoral individuals, and the beginning researcher. This second edition maintains the introductory character of the first with a focus on materials science as distinct from straight solid mechanics theory. Every chapter has been 2nd ed. 2007, XXII, 226 p. updated to make the book easier to read and more informative. A new chapter on depth sensing indentation has been added, and the contents of the other chapters have been completely overhauled with added figures, formulae and explanations. Printed book Hardcover ▶ 159,99 € | £139.99 | $199.99 The author begins with an introduction to the mechanical properties of materials, ▶ *171,19 € (D) | 175,99 € (A) | CHF 189.00 general fracture mechanics and the fracture of brittle solids. This is followed by a detailed description of indentation stress fields for both elastic and elastic-plastic contact. The discussion then turns to the formation of Hertzian cone cracks in brittle materials, eBook subsurface damage in ductile materials, and the meaning of hardness. The author Available from your bookstore or concludes with an overview of practical methods of indentation. ▶ springer.com/shop MyCopy Printed eBook for just ▶ € | $ 24.99 ▶ springer.com/mycopy Order online at springer.com ▶ or for the Americas call (toll free) 1-800-SPRINGER ▶ or email us at: [email protected]. -
Static Friction at Fractal Interfaces
Dorian Hanaor, Yixiang Gan and Itai Einav (2016). Static friction at fractal interfaces. Tribology International, 93, 229-238. DOI: 10.1016/j.triboint.2015.09.016 Static friction at fractal interfaces Dorian A. H. Hanaor, Yixiang Gan, Itai Einav School of Civil Engineering, University of Sydney, NSW 2006, Australia https://doi.org/10.1016/j.triboint.2015.09.016 Abstract: Tribological phenomena are governed by combined effects of material properties, topology and surface- chemistry. We study the interplay of multiscale-surface-structures with molecular-scale interactions towards interpreting static frictional interactions at fractal interfaces. By spline-assisted-discretization we analyse asperity interactions in pairs of contacting fractal surface profiles. For elastically deforming asperities, force analysis reveals greater friction at surfaces exhibiting higher fractality, with increasing molecular-scale friction amplifying this trend. Increasing adhesive strength yields higher overall friction at surfaces of lower fractality owing to greater true-contact-area. In systems where adhesive-type interactions play an important role, such as those where cold-welded junctions form, friction is minimised at an intermediate value of surface profile fractality found here to be in the regime 1.3-1.5. Our results have implications for systems exhibiting evolving surface structures. Keywords: Contact mechanics, friction, fractal, surface structures 1 Dorian Hanaor, Yixiang Gan and Itai Einav (2016). Static friction at fractal interfaces. Tribology -
Tribology of Polymer Blends PBT + PTFE
materials Article Tribology of Polymer Blends PBT + PTFE Constantin Georgescu 1,* , Lorena Deleanu 1,*, Larisa Chiper Titire 1 and Alina Cantaragiu Ceoromila 2 1 Department of Mechanical Engineering, Faculty of Engineering, “Dunarea de Jos” University of Galati, 800008 Galati, Romania; [email protected] 2 Department of Applied Sciences, Cross-Border Faculty, “Dunarea de Jos” University of Galati, 800008 Galati, Romania; [email protected] * Correspondence: [email protected] (C.G.); [email protected] (L.D.); Tel.: +40-743-105-835 (L.D.) Abstract: This paper presents results on tribological characteristics for polymer blends made of polybutylene terephthalate (PBT) and polytetrafluoroethylene (PTFE). This blend is relatively new in research as PBT has restricted processability because of its processing temperature near the degradation one. Tests were done block-on-ring tribotester, in dry regime, the variables being the PTFE concentration (0%, 5%, 10% and 15% wt) and the sliding regime parameters (load: 1, 2.5 and 5 N, the sliding speed: 0.25, 0.5 and 0.75 m/s, and the sliding distance: 2500, 5000 and 7500 m). Results are encouraging as PBT as neat polymer has very good tribological characteristics in terms of friction coefficient and wear rate. SEM investigation reveals a quite uniform dispersion of PTFE drops in the PBT matrix. Either considered a composite or a blend, the mixture PBT + 15% PTFE exhibits a very good tribological behavior, the resulting material gathering both stable and low friction coefficient and a linear wear rate lower than each component when tested under the same conditions. Keywords: polybutylene terephthalate (PBT); polytetrafluoroethylene (PTFE); blend PBT + PTFE; block-on-ring test; linear wear rate; friction coefficient Citation: Georgescu, C.; Deleanu, L.; Chiper Titire, L.; Ceoromila, A.C. -
1 Classical Theory and Atomistics
1 1 Classical Theory and Atomistics Many research workers have pursued the friction law. Behind the fruitful achievements, we found enormous amounts of efforts by workers in every kind of research field. Friction research has crossed more than 500 years from its beginning to establish the law of friction, and the long story of the scientific historyoffrictionresearchisintroducedhere. 1.1 Law of Friction Coulomb’s friction law1 was established at the end of the eighteenth century [1]. Before that, from the end of the seventeenth century to the middle of the eigh- teenth century, the basis or groundwork for research had already been done by Guillaume Amontons2 [2]. The very first results in the science of friction were found in the notes and experimental sketches of Leonardo da Vinci.3 In his exper- imental notes in 1508 [3], da Vinci evaluated the effects of surface roughness on the friction force for stone and wood, and, for the first time, presented the concept of a coefficient of friction. Coulomb’s friction law is simple and sensible, and we can readily obtain it through modern experimentation. This law is easily verified with current exper- imental techniques, but during the Renaissance era in Italy, it was not easy to carry out experiments with sufficient accuracy to clearly demonstrate the uni- versality of the friction law. For that reason, 300 years of history passed after the beginning of the Italian Renaissance in the fifteenth century before the friction law was established as Coulomb’s law. The progress of industrialization in England between 1750 and 1850, which was later called the Industrial Revolution, brought about a major change in the production activities of human beings in Western society and later on a global scale. -
Cross-Linked Polymers and Rubber Elasticity Chapter 9 (Sperling)
Cross-linked Polymers and Rubber Elasticity Chapter 9 (Sperling) • Definition of Rubber Elasticity and Requirements • Cross-links, Networks, Classes of Elastomers (sections 1-3, 16) • Simple Theory of Rubber Elasticity (sections 4-8) – Entropic Origin of Elastic Retractive Forces – The Ideal Rubber Behavior • Departures from the Ideal Rubber Behavior (sections 9-11) – Non-zero Energy Contribution to the Elastic Retractive Forces – Stress-induced Crystallization and Limited Extensibility of Chains (How to make better elastomers: High Strength and High Modulus) – Network Defects (dangling chains, loops, trapped entanglements, etc..) – Semi-empirical Mooney-Rivlin Treatment (Affine vs Non-Affine Deformation) Definition of Rubber Elasticity and Requirements • Definition of Rubber Elasticity: Very large deformability with complete recoverability. • Molecular Requirements: – Material must consist of polymer chains. Need to change conformation and extension under stress. – Polymer chains must be highly flexible. Need to access conformational changes (not w/ glassy, crystalline, stiff mat.) – Polymer chains must be joined in a network structure. Need to avoid irreversible chain slippage (permanent strain). One out of 100 monomers must connect two different chains. Connections (covalent bond, crystallite, glassy domain in block copolymer) Cross-links, Networks and Classes of Elastomers • Chemical Cross-linking Process: Sol-Gel or Percolation Transition • Gel Characteristics: – Infinite Viscosity – Non-zero Modulus – One giant Molecule – Solid -
Chapter 10: Elasticity and Oscillations
Chapter 10 Lecture Outline 1 Copyright © The McGraw-Hill Companies, Inc. Permission required for reproduction or display. Chapter 10: Elasticity and Oscillations •Elastic Deformations •Hooke’s Law •Stress and Strain •Shear Deformations •Volume Deformations •Simple Harmonic Motion •The Pendulum •Damped Oscillations, Forced Oscillations, and Resonance 2 §10.1 Elastic Deformation of Solids A deformation is the change in size or shape of an object. An elastic object is one that returns to its original size and shape after contact forces have been removed. If the forces acting on the object are too large, the object can be permanently distorted. 3 §10.2 Hooke’s Law F F Apply a force to both ends of a long wire. These forces will stretch the wire from length L to L+L. 4 Define: L The fractional strain L change in length F Force per unit cross- stress A sectional area 5 Hooke’s Law (Fx) can be written in terms of stress and strain (stress strain). F L Y A L YA The spring constant k is now k L Y is called Young’s modulus and is a measure of an object’s stiffness. Hooke’s Law holds for an object to a point called the proportional limit. 6 Example (text problem 10.1): A steel beam is placed vertically in the basement of a building to keep the floor above from sagging. The load on the beam is 5.8104 N and the length of the beam is 2.5 m, and the cross-sectional area of the beam is 7.5103 m2.