Lecture 2: Paper and Paperboard Based Ki Packaging
Total Page:16
File Type:pdf, Size:1020Kb
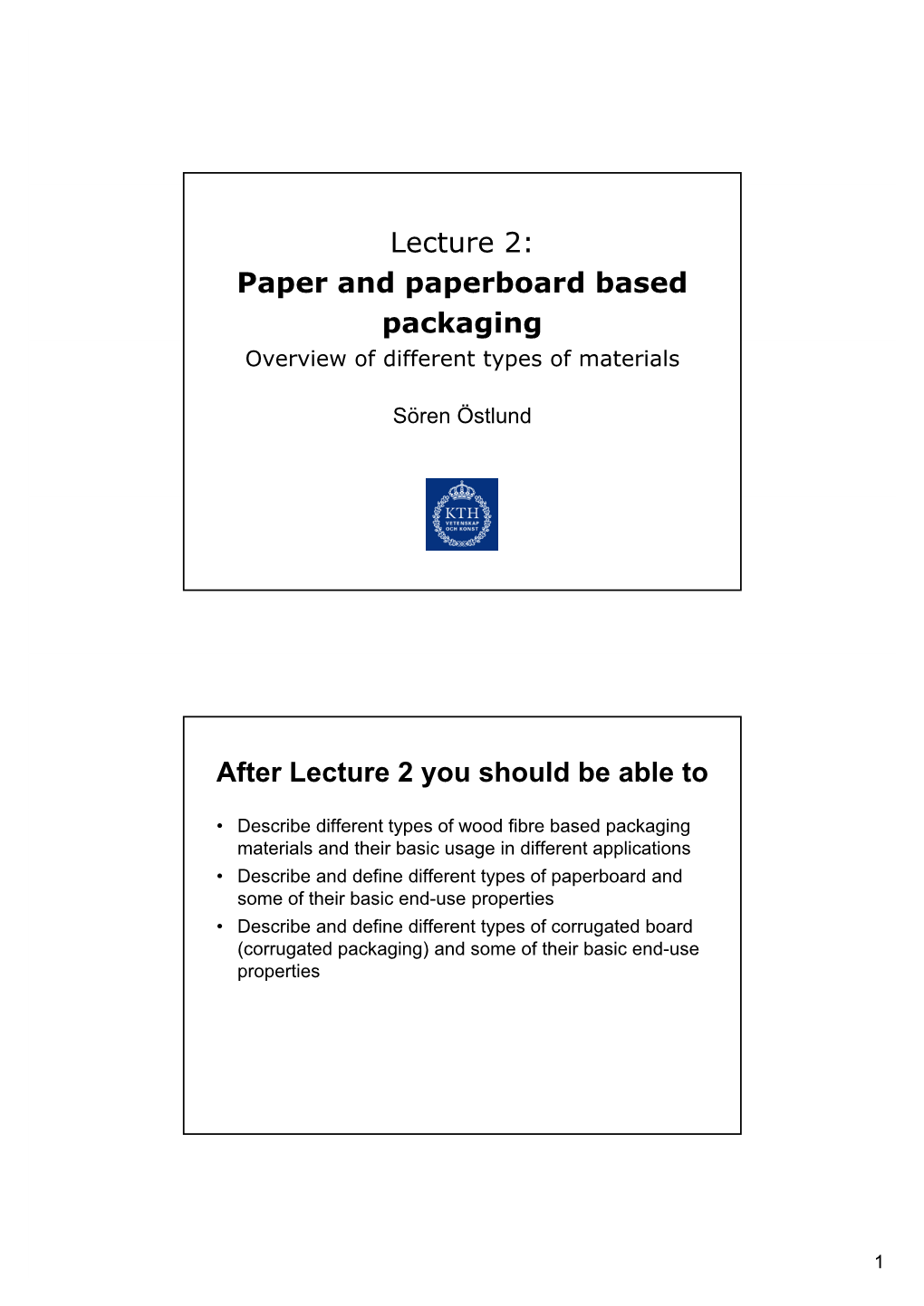
Load more
Recommended publications
-
Effects of Moisture on the Biaxial Strength of Wood-Based Composites
EFFECTS OF MOISTURE ON THE BIAXIAL STRENGTH OF WOOD-BASEDCOMPOSITES J. C. Suhling* J.M. Considine ** K. C. Yeh* * Department of Mechanical Engineering Auburn University Auburn, AL36849-5341 ** U.S.D.A. Forest Products Laboratory One Gifford Pinchot Drive Madison,WI 53705-2398 ABSTRACT applications such as corrugated containers where it is subjected to complicated biaxial stress states, In the present work, the effects of moisture on including shear. At present, lack of accurate the biaxial strength of wood-based composite materials constitutive relations and reliable strength has been examined. Experiments have been performed on predictions under biaxial loading and variable paperboard to measure the uniaxial and biaxial input environments hampers analysis of such problems. parameters of the tensor polynomial criterion at Therefore, it has been common practice in the paper several levels of relative humidity. With these data, industry to use trial and error, and empirical the dependence of the zero shear biaxial failure approaches for optimizing the designs of paperboard envelope on humidity level has been predicted and products. The current lack of technology limits trends have been observed. creative design improvements which could curtail the excess use of materials and energy. Accurate predictions of material strength under 1. INTRODUCTION general biaxial normal loading plus shear are needed by the design engineer when considering typical Unlike laminated fiber-reinforced composite structural applications of paperboard. Examples of materials, paper (paperboard) is a multiphase important current applications where biaxial stress composite composed of moisture, fibers, voids, and states exist in paperboard include the quality control possibly chemical additives. The fibers in paperboard burst test (bulged plate), material handling are typically organic with cellulose fibers from wood operations during the papermaking process, and stacked being the chief material. -
Cardboard and Brown Paper Bags Office Paper, Newspaper, Junk Mail, Magazines, and Catalogs
Recycling Center 801 Diamond Valley Drive Open: Daily to the public during daylight hours This guide will help you properly prepare your recyclable materials for drop-off at the Town of Windsor Recycle Center. This is a drop-off facility. It does not have a buy-back option and is for use by residents and small businesses. Following this information will help maintain the facility and the recycling program for the benefit of the community. IMPORTANT… • Do not leave your recyclables in plastic bags. Plastic bags are NOT recyclable! • The plastic item must be a BOTTLE or JAR. with a #1 or #2 on the bottom. • 99 percent of these will have a screw-on plastic lid (which isn’t recyclable). • Plastic containers with a #3 - #7 on the bottom are NOT acceptable. • Tubs, buckets, deli plates, microwave/fast food trays, wrappers, Styrofoam, toys, patio furniture, etc. are NOT acceptable. • Plastic bottles larger than 2.5 gallons are NOT acceptable. • Syringes and other medical supplies are NOT acceptable. Cardboard and Brown Paper Bags Corrugated cardboard is easy to recognize. It is made of paper and has an arched layer called “fluting” between smooth sheets called “liners”. The drop-off site has two 40-yard hydraulic compactor units for collecting corrugated cardboard and brown paper bags. The compaction system is self-activated by depositing the prepared materials into a six-inch tall slot. Flatten boxes. Cut or tear large boxes into sections no larger than 4 feet by 4 feet to prevent jamming the machine. No wet, waxed-coated or food-contaminated boxes. -
26 the Carton Packaging Fact File CARTONBOARD
26 The Carton Packaging Fact File CARTONBOARD 5 The Carton Packaging Fact File 27 KEY FACTS Cartonboard is a multilayered material. The main types of cartonboard are solid bleached board, solid unbleached board, folding boxboard and white lined chipboard. Cartonboard usually has a white, pigmented coating on one or both surfaces Cartonboard specifications Cartonboard can be vary with respect to the pulp combined with other composition of the various materials to vary the visual layers and by the grammage appearance and to extend (weight per sq. metre in the protective properties grammes) and thickness (microns or 0.001 millimetre) Laminations, coatings and impregnations can be added to extend the range of carton applications 28 The Carton Packaging Fact File CARTONBOARD COMMON ABBREVIATIONS SBB Solid Bleached Board SUB Solid Unbleached Board FBB Folding Box Board WLC White Lined Chipboard Different types and grades the range 200-600g/m 2 for grammage product aroma, flavour and hygiene are of cartonboard and their and 350-800µm for thickness. critical. Examples of cartons where abbreviations. The principles SBB is used are perfumes, cosmetics, of cartonboard manufacture, What are the main characteristics chocolates, pharmaceuticals, frozen developments and treatments of cartonboard? foods and cigarettes. Cartonboard is mechanically strong. What is cartonboard? Its stiffness, rigidity and toughness SBB is sometimes referred to as SBS Cartonboard is a multilayer material provide compression strength to protect or GZ. with, usually, three or more layers, or products in distribution and use. It can plies, of cellulose fibre (pulp) derived be cut, creased, folded and glued, giving What is Solid Unbleached Board? from wood. -
The EMA Guide to Envelopes and Mailing
The EMA Guide to Envelopes & Mailing 1 Table of Contents I. History of the Envelope An Overview of Envelope Beginnings II. Introduction to the Envelope Envelope Construction and Types III. Standard Sizes and How They Originated The Beginning of Size Standardization IV. Envelope Construction, Seams and Flaps 1. Seam Construction 2. Glues and Flaps V. Selecting the Right Materials 1. Paper & Other Substrates 2. Window Film 3. Gums/Adhesives 4. Inks 5. Envelope Storage 6. Envelope Materials and the Environment 7. The Paper Industry and the Environment VI. Talking with an Envelope Manufacturer How to Get the Best Finished Product VII. Working with the Postal Service Finding the Information You Need VIII. Final Thoughts IX. Glossary of Terms 2 Forward – The EMA Guide to Envelopes & Mailing The envelope is only a folded piece of paper yet it is an important part of our national communications system. The power of the envelope is the power to touch someone else in a very personal way. The envelope has been used to convey important messages of national interest or just to say “hello.” It may contain a greeting card sent to a friend or relative, a bill or other important notice. The envelope never bothers you during the dinner hour nor does it shout at you in the middle of a television program. The envelope is a silent messenger – a very personal way to tell someone you care or get them interested in your product or service. Many people purchase envelopes over the counter and have never stopped to think about everything that goes into the production of an envelope. -
FAQ About Recycling Cartons
FREQUENTLY ASKED QUESTIONS ABOUT CARTONS WHAT IS A CARTON? » Cartons are a type of packaging for food and beverage products you can purchase at the store. They are easy to recognize and are available in two types—shelf-stable and refrigerated. Shelf-stable cartons (types of products) Refrigerated (types of products) » Juice » Milk » Milk » Juice » Soy Milk » Cream » Soup and broth » Egg substitutes » Wine You will find these You will find these products in the chilled products on the shelves sections of grocery stores. in grocery stores. WHAT ARE CARTONS MADE FROM? » Cartons are mainly made from paper in the form of paperboard, as well as thin layers of polyethylene (plastic) and/or aluminum. Shelf-stable cartons contain on average 74% paper, 22% polyethylene and 4% aluminum. Refrigerated cartons contain about 80% paper and 20% polyethylene. ARE CARTONS RECYCLABLE? » Yes! Cartons are recyclable. In fact, the paper fiber contained in cartons is extremely valuable and useful to make new products. WHERE CAN I RECYCLE CARTONS? » To learn if your community accepts cartons for recycling, please visit RecycleCartons.com or check with your local recycling program. HOW DO I RECYCLE CARTONS? » Simply place the cartons in your recycle bin. If your recycling program collects materials as “single- stream,” you may place your cartons in your bin with all the other recyclables. If your recycling program collects materials as “dual-stream” (paper items together and plastic, metal and glass together), please place cartons with your plastic, metal and glass containers. WAIT, YOU JUST SAID CARTONS ARE MADE MAINLY FROM PAPER. Don’t I WANT TO PUT THEM WITH OTHER PAPER RECYCLABLES? » Good question. -
Tall Oil Rosin (TOR) Version Number: 8 Issued: 2021-03-15 Replaces SDS: 2019-01-16
SAFETY DATA SHEET According to Regulation (EC) No 1907/2006 Tall Oil Rosin (TOR) Version number: 8 Issued: 2021-03-15 Replaces SDS: 2019-01-16 SECTION 1: Identification of the substance/mixture and of the company/undertaking 1.1. Product identifier Trade name Tall Oil Rosin (TOR) CAS No. 8050-09-7 UFI code 5SDP-7PGU-G604-3JPD EC number 232-475-7 REACH registration number 01-2119480418-32 Index No. 650-015-00-7 1.2. Relevant identified uses of the substance or mixture and uses advised against Use Manufacture rosin Rubber production Binders and release agents Coatings Production of paper and cardboard 1.3. Details of the supplier of the safety data sheet Supplier SunPine AB Street address Box 76 941 22 Piteå Sweden Telephone 0911-23 28 00 Email [email protected] Web site www.sunpine.se 1.4. Emergency telephone number NHS 111 1 / 15 SAFETY DATA SHEET According to Regulation (EC) No 1907/2006 Tall Oil Rosin (TOR) Version number: 8 Issued: 2021-03-15 Replaces SDS: 2019-01-16 Available outside office hours Yes SECTION 2: Hazards identification 2.1. Classification of the substance or mixture Classification according to Regulation (EC) No 1272/2008 Danger classes Skin sensitisation, hazard category 1 Hazard statements H317 2.2. Label elements Labelling according to Regulation (EC) No 1272/2008 Hazard pictograms Signal word Warning Hazard statements H317 May cause an allergic skin reaction. Precautionary statements P261 Avoid breathing smoke/fog/vapors/spray. P280 Wear protective gloves/protective clothing/eye protection/face protection. P302 + P352 IF ON SKIN: Wash with plenty of water/soap. -
Different Perspectives for Assigning Weights to Determinants of Health
COUNTY HEALTH RANKINGS WORKING PAPER DIFFERENT PERSPECTIVES FOR ASSIGNING WEIGHTS TO DETERMINANTS OF HEALTH Bridget C. Booske Jessica K. Athens David A. Kindig Hyojun Park Patrick L. Remington FEBRUARY 2010 Table of Contents Summary .............................................................................................................................................................. 1 Historical Perspective ........................................................................................................................................ 2 Review of the Literature ................................................................................................................................... 4 Weighting Schemes Used by Other Rankings ............................................................................................... 5 Analytic Approach ............................................................................................................................................. 6 Pragmatic Approach .......................................................................................................................................... 8 References ........................................................................................................................................................... 9 Appendix 1: Weighting in Other Rankings .................................................................................................. 11 Appendix 2: Analysis of 2010 County Health Rankings Dataset ............................................................ -
Technical Drawing: Selecting Your Paper
Published on L'atelier Canson (https://www.lateliercanson.com) Accueil > Technical drawing: Selecting your paper Retour à la liste d'articles [1] Technical drawing: Selecting your paper [2] Le matériel [5] Notez cet article Give Technical drawing: ? Selecting your paper 3/5 Taux Texture, format, thickness, grid: a wide range of paper, tracing paper and transparent film readily adapts to all your creations. 1. Grammage It conditions the paper's thickness and is measured as grams per square meter: fine papers (under 90 g/m²) are appropriate for sketching, intermediate (up to 200 g/m²), adapt to most kinds of work, thick (300 g and more) are designed for wet media such as watercolor. 2. Format It is standardized and comes in six formats: from A0 (1 (m)2), up to A5 (the smallest one). Each format represents half of the previous one. Most used are the two classics, A3 and A4. 3. Texture The quality of a technical drawing relies on perfect lines: opt for slightly textured paper, whether fine grained or satin finish, and even completely smooth, such as Bristol board. Memo: There?s a paper for every medium Graphite: white or slightly tinted (beige, ocher, gray?). Color pencils: fine grained to make the pigments hold. Markers: paper known as "layout" paper holds ink and limits smudges. 4. Graph paper Technical drawing implies high precision. Choose it taking your subject's constraints into account. White drawing paper and Bristol board are available as graph paper. The covers of "to scale" pads of tracing paper come as 5 mm grid charts. -
Nanofibrillated Cellulose Applied As Reinforcement for Short-Fiber Paper
NANOFIBRILLATED CELLULOSE APPLIED AS REINFORCEMENT FOR SHORT-FIBER PAPER Daniele Cristina Potulski1*, Lívia Cássia Viana2, Ana Namikata da Fonte3 Mayara Elita Carneiro4, Graciela Ines Bolzon de Muniz5, Umberto Klock6 Universidade Federal do Paraná. Curitiba, Paraná, Brasil – [email protected]* ; [email protected] ; [email protected] ; [email protected] ; [email protected] 2 Universidade Federal do Tocantins. Gurupi, Tocantins, Brasil – e-mail: [email protected] Received for publication: 02/05/2018 - Accepted for publication: 31/10/2019 __________________________________________________________________________________________________ Resumo Nanocelulose aplicada como reforço para papel de fibra curta. Este trabalho teve como objetivo avaliar a influência da adição de diferentes porcentagens de celulose nanofibrilada sobre as propriedades mecânicas e físicas do papel feito a partir da polpa de fibras curtas. A celulose nanofibrilada foi obtida a partir de polpa Kraft de Eucalyptus sp. branqueada, submetida a três diferentes passes no moinho: 2, 10 e 20 passes. Os papéis foram produzidos com a adição de celulose nanofibrilada nas porcentagens de 3, 6 e 9%. Os resultados mostraram que a adição de celulose nanofibrilada aumentou as propriedades mecânicas: índice de tração, índice de arrebentamento e índice de rasgo. A porosidade e a densidade aparente diminuíram. A adição de 9% de celulose nanofibrilada, obtida a partir de 2 passes, proporcionou os melhores resultados com aumento da resistência à tração, arrebentamento e rasgo de 111, 114 e 70%, respectivamente, em comparação aos papéis normais. A melhoria das propriedades mecânicas do papel está relacionada à rede muito densa de ligações de hidrogênio, resultando em maior área de superfície obtida após a desfibrilação. -
Corrugated Board Structure: a Review M.C
ISSN: 2395-3594 IJAET International Journal of Application of Engineering and Technology Vol-2 No.-3 Corrugated Board Structure: A Review M.C. Kaushal1, V.K.Sirohiya2 and R.K.Rathore3 1 2 Assistant Prof. Mechanical Engineering Department, Gwalior Institute of Information Technology,Gwalior, Assistant Prof. Mechanical Engineering 3 Departments, Gwalior Engineering College, Gwalior, M. Tech students Maharanapratap College of Technology, Gwalior, [email protected] [email protected] [email protected] ABSTRACT Corrugated board is widely used in the packing industry. The main advantages are lightness, recyclability and low cost. This makes the material the best choice to produce containers devoted to the shipping of goods. Furthermore examples of structure design based on corrugated boards can be found in different fields. Structural analysis of paperboard components is a crucial topic in the design of containers. It is required to investigate their strength properties because they have to protect the goods contained from lateral crushing and compression loads due to stacking. However in this paper complete and detailed information are presented. Keywords: - corrugated boards, recyclability, compression loads. Smaller flutes offer printability advantages as well as I. INTRODUCTION structural advantages for retail packaging. Corrugated board is essentially a paper sandwich consisting of corrugated medium layered between inside II. HISTORY and outside linerboard. On the production side, corrugated In 1856 the first known corrugated material was patented is a sub-category of the paperboard industry, which is a for sweatband lining in top hats. During the following four sub-category of the paper industry, which is a sub-category decades other forms of corrugated material were used as of the forest products industry. -
Tensile Properties of Paper and Paperboard (Using Constant Rate of Elongation Apparatus) (Revision of T 494 Om-01)
WI 050808.09 T 494 DRAFT NO. 2 DATE June 13, 2006 TAPPI WORKING GROUP CHAIRMAN D Muchorski SUBJECT CATEGORY Physical Properties RELATED METHODS See “Additional Information” CAUTION: This Test Method may include safety precautions which are believed to be appropriate at the time of publication of the method. The intent of these is to alert the user of the method to safety issues related to such use. The user is responsible for determining that the safety precautions are complete and are appropriate to their use of the method, and for ensuring that suitable safety practices have not changed since publication of the method. This method may require the use, disposal, or both, of chemicals which may present serious health hazards to humans. Procedures for the handling of such substances are set forth on Material Safety Data Sheets which must be developed by all manufacturers and importers of potentially hazardous chemicals and maintained by all distributors of potentially hazardous chemicals. Prior to the use of this method, the user must determine whether any of the chemicals to be used or disposed of are potentially hazardous and, if so, must follow strictly the procedures specified by both the manufacturer, as well as local, state, and federal authorities for safe use and disposal of these chemicals. Tensile properties of paper and paperboard (using constant rate of elongation apparatus) (Revision of T 494 om-01) (Underlines indicated changes/corrections since last draft) 1. Scope 1.1 This test method describes the procedure, using constant-rate-of-elongation equipment, for determining four tensile breaking properties of paper and paperboard: tensile strength, stretch, tensile energy absorption, and tensile stiffness. -
Tyvek Graphics Technical Data Sheet
DuPont ™ Tyvek ® for Graphics DURABLE – ECO-FRIENDLY – RECYCLABLE Available in sheets or rolls; usable for nearly all print technolo gies DuPont Tyvek a is a tough, durable, eco-friendly and 100% recyclable material available in sheets and rolls for all print technologies. DuPont Tyvek ® products are used for long-lasting signs, banners, flags, displays, visual merchandising, map and book printing, packaging, credit card sleeves, envelopes, shopping bags, wallets, wall coverings, drapery, and promotional apparel. Tyvek ® is also gaining use as a template material for signs because it is lightweight, durable, and is unaffected by moisture. Conventional laser printing is not recommended on Tyvek ® because of the temperatures involved in the printing units. For the same reason, Tyvek ® should not be used in electrostatic copiers. PRODUCT TYPE OF PRINTING USED FOR COATED MILS OZ. [GSM] CORE NOTES IDEAL USES STOCK WIDTHS Black Tyvek Flexography, Gravure, Offset Uncoated 5 mil 1.25 oz 2” Paper-like. Banners & Signs 36", 45" Lithography, Screen Process, UV-cure [42 gsm] Hard Structure Custom sizes available Inkjet (w/ testing due to lighter weight) Available in 10-yard rolls 1085D Digital on Demand, Flexography, Uncoated 10.3 mil 3.2 oz 3” Paper-like. Banners & Signs. Extra body 48.25", 57.125", 114.25" Gravure, Offset Lithography, Screen [109 gsm] Hard Structure for shape development. Custom sizes available Process, UV-cure Inkjet Available in 10-yard rolls 1079 Digital on Demand, Flexography, Uncoated 7.9 mil 2.85 oz 3” Paper-like. Tags & Labels 48" Gravure, Offset Lithography, Screen [97 gsm] Hard Structure Custom sizes available Process, Thermal Transfer, UV-cure Available in 10-yard rolls Inkjet 1073D Digital on Demand, Flexography, Uncoated 7.5 mil 2.2 oz 3” Paper-like.