Patented Aug. 18, 1959 2 the Closed Reaction Vessel Is Then Brought to the De Sired Operating Temperature
Total Page:16
File Type:pdf, Size:1020Kb
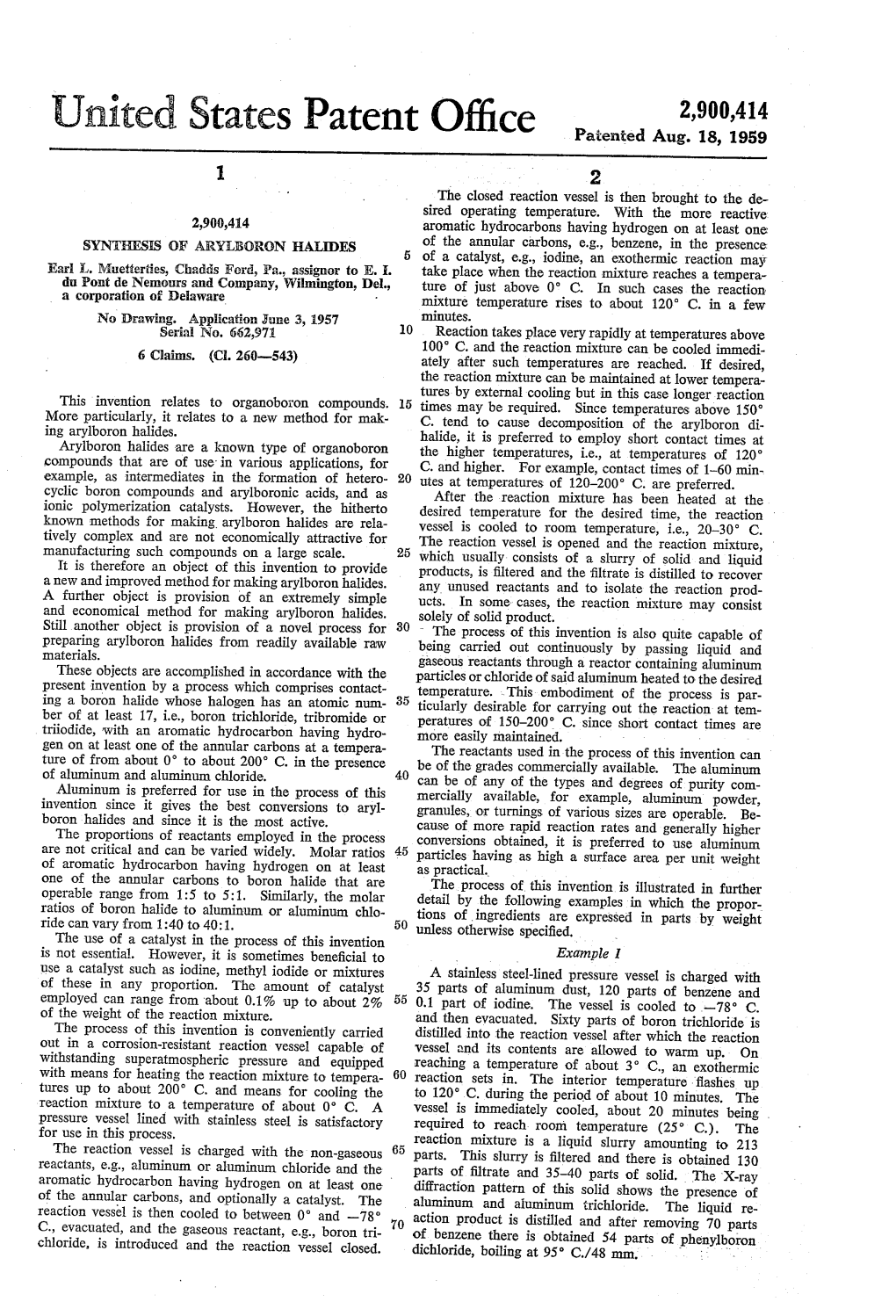
Load more
Recommended publications
-
United States Patent (19) (11) 4,161,571 Yasui Et Al
United States Patent (19) (11) 4,161,571 Yasui et al. 45 Jul. 17, 1979 (54) PROCESS FOR PRODUCTION OF THE 4,080,493 3/1978 Yasui et al. .......................... 260/879 MALE CANHYDRDE ADDUCT OF A 4,082,817 4/1978 Imaizumi et al. ...................... 526/46 LIQUID POLYMER 4,091,198 5/1978 Smith ..................................... 526/56 75 Inventors: Seimei Yasui, Takarazuka; Takao FOREIGN PATENT DOCUMENTS Oshima, Sonehigashi, both of Japan 2262677 2/1975 France ....................................... 526/56 73) Assignee: Sumitomo Chemical Company, 44-1989 1/1969 Japan ......................................... 526/56 Limited, Osaka, Japan Primary Examiner-William F. Hamrock Attorney, Agent, or Firm-Birch, Stewart, Kolasch and 21 Appl. No.: 843,311 Birch 22 Filed: Oct. 18, 1977 57 ABSTRACT Related U.S. Application Data A process for production of the maleic anhydride ad duct of a liquid polymer having a maleic anhydride 62 Division of Ser. No. 733,914, Oct. 19, 1976, Pat, No. addition amount of 2 to 70% by weight, which com 4,080,493. prises reacting a liquid polymer having a molecular 51 Int. C.’................................................ CO8F 8/46 weight of 150 to 5,000 and a viscosity of 2 to 50,000 cp (52) U.S. C. ...................................... 526/90; 526/192; at 30 C. in the presence of at least one compound, as a 526/209; 526/213; 526/193; 526/195; 526/226; gelation inhibitor, selected from the group consisting of 526/233; 526/237; 526/238; 526/272; 525/285; imidazoles, thiazoles, metallic salts of mercapto 525/249; 525/251; 525/255; 525/245; 525/248 thiazoles, urea derivatives, naphthylamines, nitrosa (58) Field of Search ................ -
Aldrich Organometallic, Inorganic, Silanes, Boranes, and Deuterated Compounds
Aldrich Organometallic, Inorganic, Silanes, Boranes, and Deuterated Compounds Library Listing – 1,523 spectra Subset of Aldrich FT-IR Library related to organometallic, inorganic, boron and deueterium compounds. The Aldrich Material-Specific FT-IR Library collection represents a wide variety of the Aldrich Handbook of Fine Chemicals' most common chemicals divided by similar functional groups. These spectra were assembled from the Aldrich Collections of FT-IR Spectra Editions I or II, and the data has been carefully examined and processed by Thermo Fisher Scientific. Aldrich Organometallic, Inorganic, Silanes, Boranes, and Deuterated Compounds Index Compound Name Index Compound Name 1066 ((R)-(+)-2,2'- 1193 (1,2- BIS(DIPHENYLPHOSPHINO)-1,1'- BIS(DIPHENYLPHOSPHINO)ETHAN BINAPH)(1,5-CYCLOOCTADIENE) E)TUNGSTEN TETRACARBONYL, 1068 ((R)-(+)-2,2'- 97% BIS(DIPHENYLPHOSPHINO)-1,1'- 1062 (1,3- BINAPHTHYL)PALLADIUM(II) CH BIS(DIPHENYLPHOSPHINO)PROPA 1067 ((S)-(-)-2,2'- NE)DICHLORONICKEL(II) BIS(DIPHENYLPHOSPHINO)-1,1'- 598 (1,3-DIOXAN-2- BINAPH)(1,5-CYCLOOCTADIENE) YLETHYNYL)TRIMETHYLSILANE, 1140 (+)-(S)-1-((R)-2- 96% (DIPHENYLPHOSPHINO)FERROCE 1063 (1,4- NYL)ETHYL METHYL ETHER, 98 BIS(DIPHENYLPHOSPHINO)BUTAN 1146 (+)-(S)-N,N-DIMETHYL-1-((R)-1',2- E)(1,5- BIS(DI- CYCLOOCTADIENE)RHODIUM(I) PHENYLPHOSPHINO)FERROCENY TET L)E 951 (1,5-CYCLOOCTADIENE)(2,4- 1142 (+)-(S)-N,N-DIMETHYL-1-((R)-2- PENTANEDIONATO)RHODIUM(I), (DIPHENYLPHOSPHINO)FERROCE 99% NYL)ETHYLAMIN 1033 (1,5- 407 (+)-3',5'-O-(1,1,3,3- CYCLOOCTADIENE)BIS(METHYLD TETRAISOPROPYL-1,3- IPHENYLPHOSPHINE)IRIDIUM(I) -
Ep 2508506 A1
(19) & (11) EP 2 508 506 A1 (12) EUROPEAN PATENT APPLICATION (43) Date of publication: (51) Int Cl.: 10.10.2012 Bulletin 2012/41 C07C 67/343 (2006.01) C07C 227/08 (2006.01) C07F 5/02 (2006.01) C07C 229/34 (2006.01) (21) Application number: 11161611.6 (22) Date of filing: 08.04.2011 (84) Designated Contracting States: (72) Inventor: The designation of the inventor has not AL AT BE BG CH CY CZ DE DK EE ES FI FR GB yet been filed GR HR HU IE IS IT LI LT LU LV MC MK MT NL NO PL PT RO RS SE SI SK SM TR (74) Representative: Kunic Tesovic, Barbara Designated Extension States: Lek Pharmaceuticals d.d. BA ME Sandoz Development Center Slovenia - Patents Verovskova 57 (71) Applicant: LEK Pharmaceuticals d.d. 1526 Ljubljana (SI) 1526 Ljubljana (SI) (54) Preparation of sitagliptin intermediates (57) The invention relates to the preparation of chiral compounds, in particular to the preparation of chiral compounds which may be used as intermediates for the preparation of anti-diabetic agents, preferably sitagliptin. EP 2 508 506 A1 Printed by Jouve, 75001 PARIS (FR) EP 2 508 506 A1 Description Field of the Intention 5 [0001] The present invention relates to the preparation of chiral compounds, in particular to the preparation of chiral compounds which may be used as intermediates for the preparation of anti-diabetic agents, preferably sitagliptin. Background prior art 10 [0002] Type II diabetes mellitus (T2DM) is a global epidemic. Therefore, the research is oriented in the development of selective inhibitors of the enzyme DPP-IV as a promising new treatment for the type II diabetes. -
Chapter 2 Atoms, Molecules and Ions
Chapter 2 Atoms, Molecules and Ions PRACTICING SKILLS Atoms:Their Composition and Structure 1. Fundamental Particles Protons Electrons Neutrons Electrical Charges +1 -1 0 Present in nucleus Yes No Yes Least Massive 1.007 u 0.00055 u 1.007 u 3. Isotopic symbol for: 27 (a) Mg (at. no. 12) with 15 neutrons : 27 12 Mg 48 (b) Ti (at. no. 22) with 26 neutrons : 48 22 Ti 62 (c) Zn (at. no. 30) with 32 neutrons : 62 30 Zn The mass number represents the SUM of the protons + neutrons in the nucleus of an atom. The atomic number represents the # of protons, so (atomic no. + # neutrons)=mass number 5. substance protons neutrons electrons (a) magnesium-24 12 12 12 (b) tin-119 50 69 50 (c) thorium-232 90 142 90 (d) carbon-13 6 7 6 (e) copper-63 29 34 29 (f) bismuth-205 83 122 83 Note that the number of protons and electrons are equal for any neutral atom. The number of protons is always equal to the atomic number. The mass number equals the sum of the numbers of protons and neutrons. Isotopes 7. Isotopes of cobalt (atomic number 27) with 30, 31, and 33 neutrons: 57 58 60 would have symbols of 27 Co , 27 Co , and 27 Co respectively. Chapter 2 Atoms, Molecules and Ions Isotope Abundance and Atomic Mass 9. Thallium has two stable isotopes 203 Tl and 205 Tl. The more abundant isotope is:___?___ The atomic weight of thallium is 204.4 u. The fact that this weight is closer to 205 than 203 indicates that the 205 isotope is the more abundant isotope. -
WO 2013/089962 Al 20 June 2013 (20.06.2013) W P O P C T
(12) INTERNATIONAL APPLICATION PUBLISHED UNDER THE PATENT COOPERATION TREATY (PCT) (19) World Intellectual Property Organization International Bureau (10) International Publication Number (43) International Publication Date WO 2013/089962 Al 20 June 2013 (20.06.2013) W P O P C T (51) International Patent Classification: (81) Designated States (unless otherwise indicated, for every B01J 31/04 (2006.01) B01J 31/18 (2006.01) kind of national protection available): AE, AG, AL, AM, B01J 31/14 (2006.01) B01J 31/22 (2006.01) AO, AT, AU, AZ, BA, BB, BG, BH, BN, BR, BW, BY, BZ, CA, CH, CL, CN, CO, CR, CU, CZ, DE, DK, DM, (21) Number: International Application DO, DZ, EC, EE, EG, ES, FI, GB, GD, GE, GH, GM, GT, PCT/US20 12/065285 HN, HR, HU, ID, IL, IN, IS, JP, KE, KG, KM, KN, KP, (22) International Filing Date: KR, KZ, LA, LC, LK, LR, LS, LT, LU, LY, MA, MD, 15 November 2012 (15.1 1.2012) ME, MG, MK, MN, MW, MX, MY, MZ, NA, NG, NI, NO, NZ, OM, PA, PE, PG, PH, PL, PT, QA, RO, RS, RU, (25) Filing Language: English RW, SC, SD, SE, SG, SK, SL, SM, ST, SV, SY, TH, TJ, (26) Publication Language: English TM, TN, TR, TT, TZ, UA, UG, US, UZ, VC, VN, ZA, ZM, ZW. (30) Priority Data: 13/323,328 12 December 201 1 (12. 12.201 1) US (84) Designated States (unless otherwise indicated, for every kind of regional protection available): ARIPO (BW, GH, (71) Applicant (for all designated States except US): CHEV¬ GM, KE, LR, LS, MW, MZ, NA, RW, SD, SL, SZ, TZ, RON PHILLIPS CHEMICAL COMPANY LP UG, ZM, ZW), Eurasian (AM, AZ, BY, KG, KZ, RU, TJ, [US/US]; 10001 Six Pines Drive, The Woodlands, Texas TM), European (AL, AT, BE, BG, CH, CY, CZ, DE, DK, 77380 (US). -
Safety Data Sheet Acc
Page 1/6 Safety Data Sheet acc. to OSHA HCS Printing date 01/23/2014 Reviewed on 01/07/2010 1 Identification Product identifier Product name: Boron triiodide Stock number: 87220 CAS Number: 13517-10-7 EC number: 236-857-4 Relevant identified uses of the substance or mixture and uses advised against. Identified use: SU24 Scientific research and development Details of the supplier of the safety data sheet Manufacturer/Supplier: Alfa Aesar, A Johnson Matthey Company Johnson Matthey Catalog Company, Inc. 30 Bond Street Ward Hill, MA 01835-8099 Tel: 800-343-0660 Fax: 800-322-4757 Email: [email protected] www.alfa.com Information Department: Health, Safety and Environmental Department Emergency telephone number: During normal hours the Health, Safety and Environmental Department at (800) 343-0660. After normal hours call Carechem 24 at (866) 928-0789. 2 Hazard(s) identification Classification of the substance or mixture Classification according to Regulation (EC) No 1272/2008 GHS05 Corrosion Skin Corr. 1B H314 Causes severe skin burns and eye damage. Eye Dam. 1 H318 Causes serious eye damage. Classification according to Directive 67/548/EEC or Directive 1999/45/EC C; Corrosive R34: Causes burns. R14: Reacts violently with water. Information concerning particular hazards for human and environment: Not applicable Hazards not otherwise classified Reacts violently with water. Label elements Labelling according to Regulation (EC) No 1272/2008 The substance is classified and labeled according to the CLP regulation. Hazard pictograms GHS05 Signal word Danger Hazard statements H314 Causes severe skin burns and eye damage. Precautionary statements P280 Wear protective gloves/protective clothing/eye protection/face protection. -
Hazardous Substances (Chemicals) Transfer Notice 2006
16551655 OF THURSDAY, 22 JUNE 2006 WELLINGTON: WEDNESDAY, 28 JUNE 2006 — ISSUE NO. 72 ENVIRONMENTAL RISK MANAGEMENT AUTHORITY HAZARDOUS SUBSTANCES (CHEMICALS) TRANSFER NOTICE 2006 PURSUANT TO THE HAZARDOUS SUBSTANCES AND NEW ORGANISMS ACT 1996 1656 NEW ZEALAND GAZETTE, No. 72 28 JUNE 2006 Hazardous Substances and New Organisms Act 1996 Hazardous Substances (Chemicals) Transfer Notice 2006 Pursuant to section 160A of the Hazardous Substances and New Organisms Act 1996 (in this notice referred to as the Act), the Environmental Risk Management Authority gives the following notice. Contents 1 Title 2 Commencement 3 Interpretation 4 Deemed assessment and approval 5 Deemed hazard classification 6 Application of controls and changes to controls 7 Other obligations and restrictions 8 Exposure limits Schedule 1 List of substances to be transferred Schedule 2 Changes to controls Schedule 3 New controls Schedule 4 Transitional controls ______________________________ 1 Title This notice is the Hazardous Substances (Chemicals) Transfer Notice 2006. 2 Commencement This notice comes into force on 1 July 2006. 3 Interpretation In this notice, unless the context otherwise requires,— (a) words and phrases have the meanings given to them in the Act and in regulations made under the Act; and (b) the following words and phrases have the following meanings: 28 JUNE 2006 NEW ZEALAND GAZETTE, No. 72 1657 manufacture has the meaning given to it in the Act, and for the avoidance of doubt includes formulation of other hazardous substances pesticide includes but -
CHEM Safety Manual
Department of Chemistry Safety Manual October 2018 Safety Committee Department of Chemistry Hong Kong University of Science and Technology Table of Contents 1.0 Introduction 2.0 Safety Policy and Responsibility for Safety 2.1 Department Head 2.2 Department of Chemistry Safety Committee 2.3 Laboratory Supervisors 2.4 Researchers 2.5 HSEO 3.0 Information, Training, Safety Clearance, and Safety Clearance at Termination 3.1 Initial Training 3.2 Information on Hazardous Substances 3.3 Additional Safety Information 3.4 Safety Clearance at Termination 4.0 Personal Protective Equipment and Safety Engineering Controls 4.1 Eye Protection 4.2 Protective Apparel 4.3 Respirators 4.4 Laboratory Fume Cupboards 4.5 Fire Extinguishers, Safety Showers, and Eyewash Facilities 5.0 Standard Operating Procedures for Work with Hazardous Substances 5.1 Classes of Hazardous Substances 5.2 General Procedures for Work with Toxic Substances 5.3 General Procedures for Work with Flammable and Explosive Substances 6.0 Procedures for Work with Particularly Hazardous Substances 6.1 Identification and Classification of Particularly Hazardous Substances 6.2 Designated Areas 6.3 General Procedures for Work with Substances of Moderate to High Chronic or High Acute Toxicity 6.4 Additional Procedures for Work with Substances of Known High Chronic Toxicity 6.5 Specific Handling Procedures for Some Common Particularly Hazardous Substances 7.0 Proper Planning of Laboratory Work 7.1 Recognition and Assessment 7.2 Planning for the Unexpected: What Could Go Wrong? 7.3 Site Selection -
"Boron Halides"
138 BORON HALIDES Vol. 4 BORON HALIDES 1. Introduction The boron trihalides boron trifluoride [7637-07-2], BF3, boron trichloride [10294- 34-5], BCl3, and boron tribromide [10294-33-4], BBr3, are important industrial chemicals having increased usage as Lewis acid catalysts and in chemical vapor deposition (CVD) processes (see ELECTRONIC MATERIALS). Boron halides are widely used in the laboratory as catalysts and reagents in numerous types of organic reactions and as starting material for many organoboron and inorganic boron compounds. An exhaustive review of the literature on boron halides up to 1984 is available (1–5). Of particular interest are review articles on BCl3 (1), BBr3 (2), and boron triiodide [13517-10-7], BI3 (3). An excellent review on diboron tetrahalides and polyhedral boron halides is available (6). Kirk-Othmer Encyclopedia of Chemical Technology. Copyright John Wiley & Sons, Inc. All rights reserved. Vol. 4 BORON HALIDES 139 2. Physical Properties 2 Boron trihalides, BX3, are trigonal planar molecules which are sp hybridized. The X–B–X angles are 1208. Important physical and thermochemical data are presented in Table 1 (7–13). Additional thermodynamic and spectroscopic data may be found in the literature (1–5). Table 1. Physical Properties of the Boron Trihalides References Property BF3 BCl3 BBr3 BI3 BCl3 BBr3 BI3 BF3 mp, 8C À128.37 À107 À46 À49:977714 bp, 8C À99.9 12.5 91.3 210 7 7 7 14 a : 0 : 18 density , g/mL (liq) 1 4344 2 6434 3.35 8 9 : 11 1 3494 critical temperature, À12.25 Æ 0.03 178.8 300 7 7 14 8C critical pressure, -
SAFETY DATA SHEET Revision Date 14.09.2021 According to Regulation (EC) No
Version 6.4 SAFETY DATA SHEET Revision Date 14.09.2021 according to Regulation (EC) No. 1907/2006 Print Date 26.09.2021 GENERIC EU MSDS - NO COUNTRY SPECIFIC DATA - NO OEL DATA SECTION 1: Identification of the substance/mixture and of the company/undertaking 1.1 Product identifiers Product name : Boron triiodide Product Number : 307629 Brand : Aldrich REACH No. : A registration number is not available for this substance as the substance or its uses are exempted from registration, the annual tonnage does not require a registration or the registration is envisaged for a later registration deadline. CAS-No. : 13517-10-7 1.2 Relevant identified uses of the substance or mixture and uses advised against Identified uses : Laboratory chemicals, Manufacture of substances 1.3 Details of the supplier of the safety data sheet Company : Sigma-Aldrich Inc. 3050 SPRUCE ST ST. LOUIS MO 63103 UNITED STATES Telephone : +1 314 771-5765 Fax : +1 800 325-5052 1.4 Emergency telephone Emergency Phone # : 800-424-9300 CHEMTREC (USA) +1-703- 527-3887 CHEMTREC (International) 24 Hours/day; 7 Days/week SECTION 2: Hazards identification 2.1 Classification of the substance or mixture Classification according to Regulation (EC) No 1272/2008 Skin corrosion (Category 1B), H314 For the full text of the H-Statements mentioned in this Section, see Section 16. 2.2 Label elements Labelling according Regulation (EC) No 1272/2008 Pictogram Aldrich- 307629 Page 1 of 8 The life science business of Merck operates as MilliporeSigma in the US and Canada Signal word Danger Hazard statement(s) H314 Causes severe skin burns and eye damage. -
Material Safety Data Sheet
LTS Research Laboratories, Inc. Safety Data Sheet Boron triiodide ––––––––––––––––––––––––––––––––––––––––––––––––––––––––––––––––––––––––––––––––––––––––––––– 1. Product and Company Identification ––––––––––––––––––––––––––––––––––––––––––––––––––––––––––––––––––––––––––––––––––––––––––––– Trade Name: Boron triiodide Chemical Formula: BI3 Recommended Use: Scientific research and development Manufacturer/Supplier: LTS Research Laboratories, Inc. Street: 37 Ramland Road City: Orangeburg State: New York Zip Code: 10962 Country: USA Tel #: 855-587-2436 / 855-lts-chem 24-Hour Emergency Contact: 800-424-9300 (US & Canada) +1-703-527-3887 (International) ––––––––––––––––––––––––––––––––––––––––––––––––––––––––––––––––––––––––––––––––––––––––––––– 2. Hazards Identification ––––––––––––––––––––––––––––––––––––––––––––––––––––––––––––––––––––––––––––––––––––––––––––– Signal Word: Danger Hazard Statements: H314: Causes severe skin burns and eye damage. Precautionary Statements: P260: Do not breathe dust or mist. P264: Wash skin thoroughly after handling. P280: Wear protective gloves/ protective clothing/ eye protection/ face protection. P301+P330+P331: IF SWALLOWED: Rinse mouth. Do NOT induce vomiting. P303+P361+P353: IF ON SKIN (or hair): Remove/ Take off immediately all contaminated clothing. Rinse skin with water/ shower. P304+P340: IF INHALED: Remove victim to fresh air and keep at rest in a position comfortable for breathing. P305+P351+P338: IF IN EYES: Rinse cautiously with water for several minutes. Remove contact lenses, if present and -
(12) Patent Application Publication (10) Pub. No.: US 2006/0061017 A1 Strouse Et Al
US 2006006 1017A1 (19) United States (12) Patent Application Publication (10) Pub. No.: US 2006/0061017 A1 Strouse et al. (43) Pub. Date: Mar. 23, 2006 (54) METHOD FOR SYNTHESIS OF COLLOIDAL (22) Filed: Sep. 20, 2004 NANOPARTICLES Publication Classification (75) Inventors: Geoffrey Fielding Strouse, Tallahassee, FL (US); Jeffrey A. Gerbec, Goleta, (51) Int. Cl. CA (US); Donny Magana, Madera, CA B29C 67/00 (2006.01) (US) (52) U.S. Cl. .............................................................. 264/489 Correspondence Address: (57) ABSTRACT GATES & COOPER LLP HOWARD HUGHES CENTER A method for Synthesis of high quality colloidal nanopar 6701 CENTER DRIVE WEST, SUITE 1050 ticles using comprises a high heating rate proceSS. Irradia LOS ANGELES, CA 90045 (US) tion of Single mode, high power, microwave is a particularly well Suited technique to realize high quality Semiconductor (73) Assignee: The Regents of the University of Cali nanoparticles. The use of microwave radiation effectively fornia automates the Synthesis, and more importantly, permits the use of a continuous flow microwave reactor for commercial (21) Appl. No.: 10/945,053 preparation of the high quality colloidal nanoparticles. Patent Application Publication Mar. 23, 2006 Sheet 1 of 6 US 2006/0061017 A1 U O a O S. - 4.5mm CC Se - - - 5.5nm CC Se s D s N 500 600 Wavelength (nm) FIG. 1 Patent Application Publication Mar. 23, 2006 Sheet 2 of 6 US 2006/0061017 A1 18 2O 1 O O O. 8 9. 2. O O 6 B 2 O o f 0. 4. O 2 7. O. 5 rus 0. O O O 400 500 600 700 Wavelength (nm) FIG.