For HALIFAX Class Ships - Scoping Study
Total Page:16
File Type:pdf, Size:1020Kb
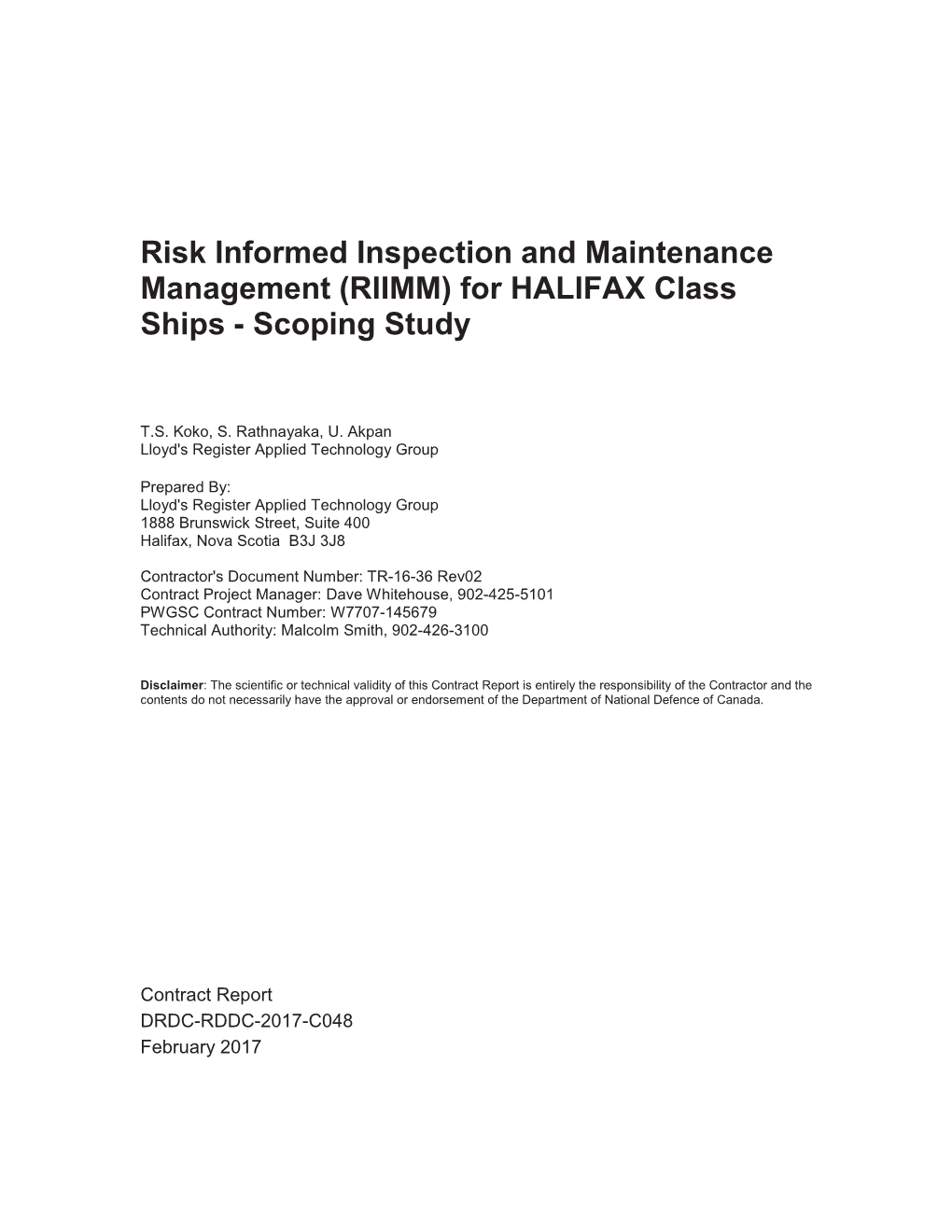
Load more
Recommended publications
-
Hmcs Ottawa Ncsm Ottawa
A-AD-267-000/AF-002 HMCS OTTAWA NCSM OTTAWA BADGE INSIGNE Description Description Gules a bend wavy Argent charged with two cotises De gueules, une bande ondée d'argent barrée de deux wavy Azure over all a beaver Or the sinister forepaw cotices ondées d'azur, brochant le tout un castor d'or, resting on a log of silver birch proper. la patte en senestre reposant sur une bûche de bouleau argenté au naturel. Significance Signification The design is derived from the unofficial pre-war and Ces armoiries sont dérivées de l'insigne non officielles war-time badge of Ottawa, a beaver on a log of wood. portées par le Ottawa avant et pendant la guerre : un The white and blue wavy bend represents the Ottawa castor sur une bûche. La bande ondée blanche et bleue River after which the ship is named. The red field is représente la rivière des Outaouais d'ou origine le nom intended to refer to those Outaouais or Ottawans who du navire. Le champ rouge se rapporte aux travelled this river and from whom the name was Amérindiens (Peaux-rouges), les Outaouais ou Ottawas derived. qui, empruntant le cours d'eau pour la navigation, ont baptisé la rivière. MOTTO DEVISE EGOR BEOFOR (Ocean beaver) EGOR BEOFOR (Castor de l'océan) 2-73 A-AD-267-000/AF-002 COLOURS COULEURS Red and White Rouge et blanc Note Nota Normal heraldic colours, the principal colours in the badge, would be Les couleurs héraldiques normales, les principales couleurs de gold and red, but the official Colours of Canada, white and red, are l'insigne, devraient être l'or et le rouge; mais les couleurs officielles used instead because the capital of Canada lies on the Ottawa River. -
Poseidon Cutlass
WWantant ttoo kknownow wwhathat yyourour BBasease Volume 62 Number 30 | July 31, 2017 Helping BC families become debt free CCommanderommander for more than 35 years. iiss uupp tto?o? WANT TO BECOME debt free? DDoo yyouou uusese newspaper.comnewwssppaaperr..com Talk to us today to see if a Consumer Proposal is right for you. FFacebook?acebook? TTwitter?witter? MARPAC NEWS CCFBFB EEsquimalt,squimalt, VVictoria,ictoria, BB.C..C Stop collection calls 778-403-4335 Follow Captain (N) Jason Boyd Stop a wage garnishment FREE CONSULTATION @LookoutNewspaperNavyNews @Lookout_news Deal with income tax debts smytheinsolvency.com on Twitter: @MayorCFBEsq And visit facebook.com/EsquimaltBase Smythe Insolvency Inc. Licensed Insolvency Trustees POSEIDON CUTLASS The crew of HMCS Winnipeg, currently on Poseidon Cutlass 17, lowers a rigid hulled inflatable boat containing Leading Seaman Anthony Berardi and Ordinary Seaman Mitchel Kathol as part of boat crew training. Photo by MCpl Carbe Orellana, MARPAC Imaging Services The goal is to Join in the 2017 Invictus We proudly serve the have a signed fl ag for each Games celebration! Canadian Forces Community competitor participating Write a message of As a military family we understand in the 2017 encouragement your cleaning needs during ongoing Invictus Games on the Supporter Flag service, deployment and relocation. www.mollymaid.ca taking place this September Monday July 31 to August 16 in Toronto. Naden Athletic Centre (250) 744-3427 [email protected] 2 • LOOKOUT July 31, 2017 Red Serge returns to HMCS Regina James Vassallo “The idea that a piece of my father will be Mess but that it had been lost while the ship Base Public Affairs immortalized with this ship for as long as she was in mid-life refit,” says LCdr Graham. -
Maritime Engineering Journal 64 Since 1982 CANADA’S NAVAL TECHNICAL FORUM Spring 2009
Maritime Engineering Journal 64 Since 1982 CANADA’S NAVAL TECHNICAL FORUM Spring 2009 The Nine Minute Writing Challenge (Part II) The Challenge Moves East CNTHA News Inside! Also in this Issue: • First Frigate Rollout of the MASIS “Deployed Solution” • Forum: The Requirement for Requirements • A Measure of Seaworthiness West Coast “whale” watching — Photo: Brian McCullough HMCS Orca (PCT-55) may look like a killer backyard building project in this October 2008 photo, but the patrol training vessel was simply in for repairs at the Point Hope Maritime Limited shipyard in Victoria’s Upper Harbour. Maritime Engineering (Established 1982) Edition No. 64 Journal SPRING 2009 DEPARTMENTS Commodore’s Corner Engineering Knowledge — Understanding the requirement is fundamental in the search for solutions by Commodore Richard Greenwood .............................................................. 2 Letters An Engineer’s Tale — Diving in the Engine Room by Commodore (Ret.) Ed Murray .................................................................. 3 Forum The Requirement for Requirements (or how to get what you want) Director General by LCdr (ret.) Gordon Forbes ........................................................................ 4 Maritime Equipment Program Management Commodore Richard W. Greenwood, OMM, CD FEATURES The East Coast’s “Short Answer” to the Nine Minute Writing Challenge Senior Editor We asked participants at the 2008 MARLANT Naval Technical Capt(N) Mike Wood DGMEPM Chief of Staff Seminar to write about their biggest technical challenge in the navy. You should read what they wrote. Project Director by 71 Worthy Contributors ............................................................................. 7 Maritime Engineering Journal Lt(N) Patrick Fortin Materiel Acquisition and Support Information System — First Frigate Rollout of the MASIS “Deployed Solution” Production Editor / Enquiries Brian McCullough by LCdr Simon Paré, CP02 Chris Tucker and Janelle Mansfield .............. -
FEATURE of the WEEK One Million Strong
133154 MND makes announcements HMCS Goose Bay on the Milestone missile shoot for Hundreds turn out for MARLANT's in Halifax Pg. 3 Great Lakes Pg. 7 HMCS Ottawa Pg. 17 Navy Bike Ride Pg. 20 Monday, June 26, 2017 Volume 51, Issue 13 www.tridentnewspaper.com Family Days Midway rides are a highlight of DND Family Days each year. Add to those the inflatable amusements, RHIB rides, face painting, and free cookies at the Sobeys display, and DND Family Days is a guaranteed good time for all. MEGHAN FASH, PSP Don’t miss out on our... Get your CFOne card! Benefits available exclusively to members of the CAF Community - offering program discounts, savings CANEX Rewards and more! One Community, FEATURE OF THE WEEK One Million Strong Une communauté, forte d’un million de membres One Community, In-store and online at CANEX.CA One Million Strong Une communauté, JOHN SMITH forte d’un million de membres 1 000 000 001 001 Family of Canadian Forces Member CF-F Famille de membre des Forces armées canadiennes Exp. 08/18 JOHN SMITH 1 000 000 001 001 Extended Security & Defence Team D Équipe de la Défense et sécurité élargie Exp. 08/18 CANEX WINDSOR PARK | 902-465-5414 CF1FC.ca 133149 2 TRIDENT NEWS JUNE 26, 2017 A new addition this year was a glider, displayed by 615 Bluenose Royal Canadian Air Cadet Squadron. Farther down the jetty is a CH-148 Cyclone helicopter from 12 Wing A static display of a CH-148 Cyclone attracts much interest from adults and children Shearwater. -
The Canadian Navy
1 | P a g e Royal Canadian Sea Cadet Corps Centurion Canadian Navy 2 | P a g e The Canadian Navy “The Sea Element of the Canadian Forces” The current resources of the Canadian Navy include: twelve Halifax class Canadian Patrol Frigates (CPFs) (multipurpose); three Iroquois class Destroyers (DDGs) (air defence and antisubmarine); two Protecteur class Auxiliary Oil Replenishers (AORs) (replenishment); twelve Kingston class Maritime Coastal Defence Vessels (MCDVs) (coastal surveillance and mine counter measures); four Victoria class submarines; aircraft – CH-124 Sea King helicopters and CP-140 Aurora long-range patrol planes (though they are operated by Air Force personnel, they act in support of naval operations); and miscellaneous auxiliary vessels (firefighting vessels, tugboats, diving tenders, etc.). The Canadian Navy also makes use of 24 Naval Reserve Divisions across Canada. The Halifax class Canadian Patrol Frigates include: Her Majesty’s Canadian Ship (HMCS) Halifax 330 HMCS Vancouver 331 HMCS Ville De Québec 332 HMCS Toronto 333 HMCS Regina 334 HMCS Calgary 335 HMCS Ottawa341 HMCS Montréal 336 HMCS Fredericton 337 HMCS Winnipeg 338 HMCS Charlottetown 339 HMCS St. John’s 340 HMCS Ottawa 341 The Iroquois class Destroyers include: HMCS Iroquois 280 HMCS Iroquios 280 HMCS Athabaskan 282 HMCS Algonquin 283 The Protecteur class includes: HMCS Preserver 510 HMCS Protecteur 509 HMCS Preserver 510 The Kingston class Coastal Defence Vessels include: HMCS Kingston 700 HMCS Glace Bay 701 HMCS Nanaimo 702 HMCS Edmonton 703 HMCS Shawinigan 704 HMCS Whitehorse 705 HMCS Brandon 710 HMCS Yellowknife 706 HMCS Goose Bay 707 HMCS Moncton 708 HMCS Saskatoon 709 HMCS Brandon 710 HMCS Summerside 711 3 | P a g e The Victoria class submarines include: HMCS Victoria 876 HMCS Windsor 877 HMCS Corner Brook 878 HMCS Chicoutimi 879 HMCS Victoria 876 Sea King Helicopter Aurora Visit the Canadian Navy Website at www.navy.gc.ca for the most up to date information on the fleet and its supporting aircraft. -
Mp-Hfm-275-22P
Suicide and Violence Perpetration Risk Assessments in the Canadian Armed Forces Health Information System: A Population-Based Analysis Robert Hawes & François Thériault Directorate of Force Health Protection Department of National Defence, Ottawa, Canada NATO HFM-275 Riga, Latvia 05 April 2017 Suicide in the Canadian Armed Forces (CAF) • 3rd leading cause of death in active-duty personnel 1983 -2007 (17%) (Tien et al. 2010) • 23.5 deaths per 100,000 person-years (Rolland-Harris et al, 2016) • 4.3% of CAF service members seriously consider suicide (Mann et al, 2005; Rusu et al, 2016) • 9% of CAF personnel with suicidal ideation attempt suicide (Rusu et al, 2016) • 93% of CAF suicide deaths (83% civilian pop.) accessed health care in previous 12 months (Mann, 2005; Rolland-Harris et al, 2016) Alert CFHIS SQL Referral / Diagnostic / Review of Care Discharge Intake Treatment Diagnostic Assessment MH Referral Periodic Case Psychosocial Review * Functioning Discharge Summary * Intake Session Note * External Screening * Provider Psychiatrist Review Progress Note Family Counselling Communication Case Consult Couple and Individual Conference Note Family Session Communication Note CFHIS Mental Health Session Note Clinical Impression Classification (CIC) 7 Clinical Impression Classifications (CIC) Addictions / Compulsive Behaviours • Classification system to Administrative categorize the MH Childhood / Upbringing assessment or narrative Education Family Circumstance • Terms based on ICD-10 Housing / Economic health status (Z-codes) Legal / Disciplinary -
Maritime Engineering Journal, Spring 2020, No.92
National Defence 92 Maritime Since 1982 Engineering Spring 2020 Journal Canada’s Naval Technical Forum CNTHA News Feature Article Inside! Is human-coded software a weak link in naval combat systems? A retired CSE speaks out. Good to go! Photo by LS Victoria Ioganov, MARPAC Imaging Services These engineering technicians from HMCS Ottawa worked with other ship’s staff and fleet maintenance subject matter experts in Esquimalt to undertake a challenging pump repair while deployed to Unalaska. see page 11 Maritime 92 Engineering (Established 1982) Journal Spring 2020 Commodore’s Corner Embracing Change by Captain (Navy) Sebastien Richard, CD .................................................................................................2 A Message from RAdm Christopher Earl .......................................................................................3 Acting Director General Forum Maritime Equipment Program Management Materiel Group – Movement at the Top .........................................................................................3 Farewell to Mr. Finn .........................................................................................................................................4 Capt(N) Sebastien Richard, CD Profile: Chief Petty Officer 1st Class Monika Quillan by Brian McCullough ............................................................................................................................5 Readership Survey Update .................................................................................................................7 -
Policy, Transformation and Shipbuilding: the Perfect Storm Threatening the Future of Canada’S Surface Combatant Fleet
Archived Content Information identified as archived on the Web is for reference, research or record-keeping purposes. It has not been altered or updated after the date of archiving. Web pages that are archived on the Web are not subject to the Government of Canada Web Standards. As per the Communications Policy of the Government of Canada, you can request alternate formats on the "Contact Us" page. Information archivée dans le Web Information archivée dans le Web à des fins de consultation, de recherche ou de tenue de documents. Cette dernière n’a aucunement été modifiée ni mise à jour depuis sa date de mise en archive. Les pages archivées dans le Web ne sont pas assujetties aux normes qui s’appliquent aux sites Web du gouvernement du Canada. Conformément à la Politique de communication du gouvernement du Canada, vous pouvez demander de recevoir cette information dans tout autre format de rechange à la page « Contactez-nous ». CANADIAN FORCES COLLEGE / COLLÈGE DES FORCES CANADIENNES JCSP / PCÉMI 33 MASTER OF DEFENCE STUDIES RESEARCH PROJECT / PROJET DE RECHERCHE DE MAÎTRISE EN ÉTUDES DE LA DÉFENSE POLICY, TRANSFORMATION AND SHIPBUILDING: THE PERFECT STORM THREATENING THE FUTURE OF CANADA’S SURFACE COMBATANT FLEET By/par LCdr/capc M.T.J. Kurtz 23 April/avril 2007 This paper was written by a student attending La présente étude a été rédigée par un the Canadian Forces College in fulfilment of stagiaire du Collège des Forces canadiennes one of the requirements of the Course of pour satisfaire à l'une des exigences du cours. Studies. The paper is a scholastic document, L'étude est un document qui se rapporte au and thus contains facts and opinions which the cours et contient donc des faits et des opinions author alone considered appropriate and que seul l'auteur considère appropriés et correct for the subject. -
HMCS Calgary As Sailors of the Quarter
Issue 25 / Numéro 25 NESOP Newsletter / Bulletin de l’OP(DEM) December 2009 The NESOP Le BULLETIN OP NEWSLETTER is (DEN) est publié par published by and NESOP Newsletter hits the Quarter-Century mark! les OP DEN de la for the NESOPs Marine canadienne of the Canadian As we find another year mark that all other occupations coming to a close there are try to meet. et à leur intention. Navy. It’s Son but : aider les purpose; to keep many of us wondering where Also on the subject of the it went. It seems like it was number 25, the NESOP militaires à connaître members current l’actualité en ce qui with items that just last month that I was occupation will be 25 years-old sailing on the PRESERVER next year and no doubt there concerne le milieu reflect the des OP DEN, en NESOP for an exercise in February. will be another special Mess Many of you out there have Dinner to mark that occasion. complétant community, by th l’information qui supplementing completed career courses this In addition to our 25 year, received another anniversary next year, the Navy provient des sources information officielles, et offrir provided by promotion and perhaps will be celebrating its completed another major centennial. There will be many une tribune où les formal sources unités peuvent and acting as a deployment. Here’s hoping events to attend over the next that whatever your year and I highly encourage all mettre en commun forum for sharing les sujets dignes unit-level items accomplishment this year that to try and get to as many as you you enjoyed yourself to the can. -
Canada's Naval Role in the Persian Gulf Before and During Iraq War, 2003
“Force Protection” for the Coalition Navy Retired Admiral Ken Summers Canada’s Naval Role confirmed in 2003, that the in the Persian Gulf Canadian Navy was then providing before and during “direct support to the war on terrorism ...and indirect support to Iraq War, 2003 the war on Iraq, in that they are Here’s what U.S. Central Command escorting through the Strait of had to say about the role of Canadian warships in the Persian Gulf during the Hormuz any allied ship that needs Iraq war and how they were “inte- to get in or out of the [Persian] gulf.” grated into a coalition formation.” More than a decade earlier, Summers Force Protection commanded Canada’s naval, air and land Heavily armed, manoeuvrable war- forces in the 1991 war against Iraq. ships, such as Canada’s destroyers and frigates, provide defensive capabilities HMCS Preserver to the more vulnerable specialized ves- sels in the multinational coalition fleet. (See pp.12-15) Fleet Support The replenishment ships HMCS Pre- server and Protecteur cruised the Ara- bian [Persian] Gulf and Arabian Sea to replenish the coalition fleet. Replenish- ment ships are crucial to sustaining coa- HMCS Protecteur lition naval operations; as well as food and essential materiel such as fuel, am- munition and replacement parts, they provide other ships of the fleet with specialized services such as health care and engineering expertise. During their time in theatre, HMCS Preserver and Protecteur conducted more than 200 replenishment operations. (See “Fleet “Fleet Support” for Coalition in the Persian -
The Royal Canadian Navy in Peace Operations
DND photo HS06-2017-0521-004 by Leading Seaman Dan Bard Leading Seaman Dan by HS06-2017-0521-004 DND photo Minister of National Defence, Harjit S. Sajjan visits the HMCS Scotian at Canadian Forces Base Halifax on 12 June 2017 to make an announcement. The Royal Canadian Navy in Peace Operations by Corey Bursey Commander C.A. Bursey, CD, BMASc, MA, has been, in of the 600 personnel are still in the planning stages by CAF his own words, “…a proud officer of the Royal Canadian Navy operational planners. Nevertheless, given that the CAF is a (RCN) since 1988.” Bursey has served operationally on several unified force made up of multiple environments – Army, Navy, HMC Ships, and on many operational deployments. Having also Air Force, and Special Forces – we ought not to assume that held numerous challenging and varied staff appointments, he is any Canadian contribution to UN PO is necessarily going to be currently the Assistant Naval Advisor of the Canadian Defence army-centric. There may very well be an impact on the other Liaison Staff in London, England. services, including the Royal Canadian Navy (RCN). Indeed, this article will describe how the RCN, or any navy for that Introduction matter, can support land and air PO, even if those forces are operating in a land-locked region. Equally, the RCN can deploy he Government of Canada, under Prime Minister independently and undertake a UN PO without it needing to Justin Trudeau, has committed to supporting be in a supporting role. The RCN can deploy rapidly, be self- international peace operations with the United sufficient if deployed with the right logistics support, remain Nations (UN) with specialized capabilities, head- outside territorial waters, and deliver multiple effects at sea. -
Corsairs in the Crosshairs: a Strategic Plan to Eliminate Modern Day Piracy
CORSAIRS IN THE CROSSHAIRS: A STRATEGIC PLAN TO ELIMINATE MODERN DAY PIRACY Alexandra Schwartz* INTRODUCTION: 1 Hijacked on the High Seas, Pirates Free Tanker After Ransom,2 Pirates Outmaneuver Warships off Somalia,3 U.S. Captain Is Hostage of Pirates,4— * J.D., 2010, New York University; B.A., 2005, Cornell University. I would like to thank my family and friends for their encouragement. I would particularly like to thank my brother Matthew Schwartz, Professor Sam Rascoff, and my friends Char- lotte Decker, Dave Baltmanis and Michelle & Michael McGovern for their helpful comments. 1 Greeta Anand & John W. Miller, Hijacked on the High Seas, WALL ST. J., Jan. 29, 2009, at A1, available at http://online.wsj.com/article/SB123335651246634995.html (detailing the hijacking and negotiation process for the ransom and return of the crew and ship of a Connecticut-based company). 2 Mohammed Ibrahim & Graham Bowley, Pirates Free Tanker After Ransom, N.Y. TIMES, Jan. 10, 2009, at A6, available at www.nytimes.com/2009/01/10/world/africa/10somalia.html (describing the release of a Saudi-owned supertanker for $3 million after approximately two months of being held hostage). 3 Jeffrey Gettleman, Pirates Outmaneuver Warships off Somalia, N.Y. TIMES, Dec. 16, 2008, at A6, available at www.nytimes.com/2008/12/16/world/africa/16pirate.html (stating that despite the addition of more than one dozen international warships to the region, pirates are not deterred and are, perhaps, actually emboldened). 4 Mark Mazzetti & Sharon Otterman, U.S. Captain Is Hostage of Pirates, N.Y. TIMES, April 9, 2009, at A6, available at www.nytimes.com/2009/04/09/world/africa/09pirates.html (marking the first time that an American-crewed ship was seized by pirates in the 500 2010] Corsairs in the Crosshairs 501 these are just a small sampling of the headlines concerning the treacherous situation created by the actions of Somali pirates in the Gulf of Aden during the final months of 2008 and the beginning of 2009.