Instrumentation and Control Qualification Standard
Total Page:16
File Type:pdf, Size:1020Kb
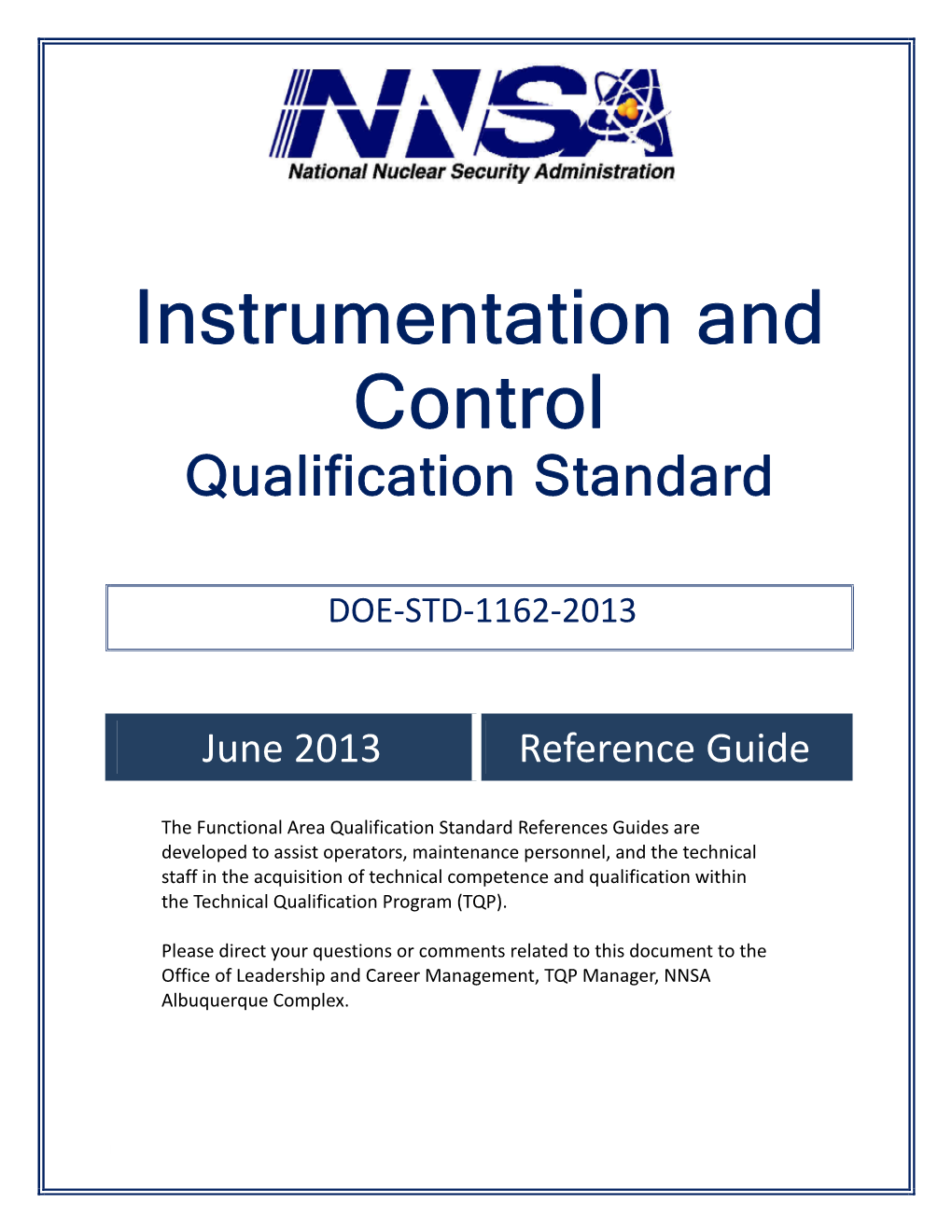
Load more
Recommended publications
-
A Novel Solid State Ultracapacitor
National Aeronautics and NASA/TM—2017–219686 Space Administration IS02 George C. Marshall Space Flight Center Huntsville, Alabama 35812 A Novel Solid State Ultracapacitor A.Y. Cortés-Peña Johnson Space Center, Houston, Texas T.D. Rolin and S.M. Strickland Marshall Space Flight Center, Huntsville, Alabama C.W. Hill CK Technologies, Meridianville, Alabama August 2017 The NASA STI Program…in Profile Since its founding, NASA has been dedicated to the • CONFERENCE PUBLICATION. Collected advancement of aeronautics and space science. The papers from scientific and technical conferences, NASA Scientific and Technical Information (STI) symposia, seminars, or other meetings sponsored Program Office plays a key part in helping NASA or cosponsored by NASA. maintain this important role. • SPECIAL PUBLICATION. Scientific, technical, The NASA STI Program Office is operated by or historical information from NASA programs, Langley Research Center, the lead center for projects, and mission, often concerned with NASA’s scientific and technical information. The subjects having substantial public interest. NASA STI Program Office provides access to the NASA STI Database, the largest collection of • TECHNICAL TRANSLATION. aeronautical and space science STI in the world. English-language translations of foreign The Program Office is also NASA’s institutional scientific and technical material pertinent to mechanism for disseminating the results of its NASA’s mission. research and development activities. These results are published by NASA in the NASA STI Report Specialized services that complement the STI Series, which includes the following report types: Program Office’s diverse offerings include creating custom thesauri, building customized databases, • TECHNICAL PUBLICATION. Reports of organizing and publishing research results…even completed research or a major significant providing videos. -
Maintenance in Instrumentation Maintenance with Concept and Technology Focusing on Results
Maintenance in instrumentation Maintenance with concept and technology focusing on results www.andritz.com Specific knowledge for reliable instruments. Analytical instrumentation Due to its close relation with operation and process control, Instrumentation is a fundamental discipline to In Analytical Instrumentation, Maintenance continued process industries. Maintenance Solutions Division of ANDRITZ offers to Clients maintenance Solutions Division of ANDRITZ offers ser- contracts, as assuming the responsibility of managing and implementing conventional Instrumentation, as vices ranging from factory’s analyzers to managing specialized modules, such as analytics, metrology, automation and valves. a complete maintenance structure. MS Division can also assume full responsibili- Conventional instrumentation ty of the function, from the management of analyzers’ performance to the purchase Differentials and importation of spares. The purpose is to provide even more reliability to analytical ▪ Active in the management of contracts since 1993 process and environmental variables. ▪ Experience in major projects: “greenfield” and “brownfield“ Scope of the function ▪ Large specific instrumentation training bank ▪ Control loops in general ▪ Technologies integration capacity, ranging from pneumatic ▪ Field instrumentation and accessories nstrumentation through Fieldbus ▪ Primary measuring elements: sensors, Differentials ▪ Technological exchange between the diverse hired contracts Scope of the function detectors and meters ▪ Pioneer in Brazil in analytical -
INSTRUMENTATION and CONTROL Module 3 Level Detectors
Department of Energy Fundamentals Handbook INSTRUMENTATION AND CONTROL Module 3 Level Detectors Level Detectors TABLE OF CONTENTS TABLE OF CONTENTS LIST OF FIGURES .................................................. ii LIST OF TABLES ................................................... iii REFERENCES ..................................................... iv OBJECTIVES ...................................................... v LEVEL DETECTORS ................................................ 1 Gauge Glass .................................................. 1 Ball Float .................................................... 4 Chain Float ................................................... 5 Magnetic Bond Method .......................................... 6 Conductivity Probe Method ....................................... 6 Differential Pressure Level Detectors ................................. 7 Summary ................................................... 10 DENSITY COMPENSATION .......................................... 11 Specific Volume .............................................. 11 Reference Leg Temperature Considerations ............................ 12 Pressurizer Level Instruments ..................................... 13 Steam Generator Level Instrument .................................. 13 Summary ................................................... 14 LEVEL DETECTION CIRCUITRY ...................................... 15 Remote Indication ............................................. 15 Environmental Concerns ........................................ -
Programmable Logic Controller
Revised 10/07/19 SPECIFICATIONS - DETAILED PROVISIONS Section 17010 - Programmable Logic Controller C O N T E N T S PART 1 - GENERAL ....................................................................................................................... 1 1.01 DESCRIPTION .............................................................................................................. 1 1.02 RELATED SECTIONS ...................................................................................................... 1 1.03 REFERENCE STANDARDS AND CODES ............................................................................ 2 1.04 DEFINITIONS ............................................................................................................... 2 1.05 SUBMITTALS ............................................................................................................... 3 1.06 DESIGN REQUIREMENTS .............................................................................................. 8 1.07 INSTALLED-SPARE REQUIREMENTS ............................................................................. 13 1.08 SPARE PARTS............................................................................................................. 13 1.09 MANUFACTURER SERVICES AND COORDINATION ........................................................ 14 1.10 QUALITY ASSURANCE................................................................................................. 15 PART 2 - PRODUCTS AND MATERIALS......................................................................................... -
Instrumentation and Control Systems
Whole Number 216 Instrumentation and Control Systems Lifecycle total solution Integrate latest leading hardware and software and application know-how, future-oriented system development with evolution. This is the lifecycle concept of MICREX-NX. MICREX-NX realizes optimal plant operation in all phases of system design, commissioning, operation and maintenance. At renewal phase, MICREX-NX provides maximum effect with minimum capital investment. The MICREX-NX lifecycle total solution offers cost reduction and long-term stable operation with constant evolution and variety of solution know-how. The new process control system Instrumentation and Control Systems CONTENTS Present Status and Fuji Electric’s Involvement with 2 Instrumentation and Control Systems New Process Control System for a Steel Plant 8 New Process Control Systems in the Energy Sector 13 Cover photo: Instrumentation and control sys- Network Wireless Sensor for Remote Monitoring of Gas Wells 17 tems are anticipated to become sys- tems capable of considering carefully the comfort and safety of society and the global environment while contrib- uting to the stable manufacture of high quality products with the desired productivity. Fuji Electric strives to provide a total optimal system with vertically and horizontally integrated solutions Fuji Electric’s Latest High Functionality Temperature Controllers 21 that link seamlessly various compo- PXH, PXG and PXR, and Examples of their Application nents and solutions required on the shop fl oor. The cover photograph represents an image of instrumentation and con- trol system organized by the MICREX- NX new process control system, fi eld devices, receivers, and the like. Head Office : No.11-2, Osaki 1-chome, Shinagawa-ku, Tokyo 141-0032, Japan http://www.fujielectric.co.jp/eng/company/tech/index.html Present Status and Fuji Electric’s Involvement with Instrumentation and Control Systems Yuji Todaka Toshiyuki Sasaya Ken Kakizakai 1. -
Instrumentation and Controls Engineer DUTIES
TITLE: Instrumentation and Controls Engineer DUTIES: Responsible for designing, developing and maintaining instrumentation and controls systems for biorefinery manufacturing plant including selection, construction and installation of I&C equipment. Develop process control and alarm logic diagrams/SAMA diagrams/cause and effect matrices. Responsible for control system architecture, DCS and PLC specification and configuration, SCADA systems, Instrument index, Instrument specifications, data sheets and selection, instruction loop diagrams, and motor elementaries. Troubleshoot motors, instruments and valves. Update control system programming and documentation. Review vendor drawings. Interface with third party I&C companies. Participate in HAZOP. Serve as technical expert support to field engineers, technicians and plant staff. Review PIDs for project engineering. Field interfacing with contractors for instrumentation and controls installation and QC. Checkout, commission, start-up and troubleshoot support. Stay current on control theory research and instrumentation advances and recommend changes as needed. SCHEDULE: 40 hours per week, Monday through Friday, 8:00 AM to 5:00 PM LOCATION: American Process, Inc., 300 McIntosh Parkway, Thomaston, GA 30286. REQUIREMENTS: Master's degree in manufacturing, controls & automation or electronics engineering. 3 years of experience in related instrumentation and controls engineering position. Will also accept a Bachelor's in stated fields and 5 years of stated experience. (foreign equivalent degree acceptable). Also requires at least 3 years of experience in the following (which may have been obtained concurrently): Selecting, constructing and installing I&C equipment. Developing P&IDs and control narratives. Designing control systems including PLC/DCS specification and HMI configuration. Developing and troubleshooting Motor, Instruments and Valves specifications. Planning and developing the layout of control system network and I/O architecture. -
Iot LSP Standard Framework Concepts 2015
AIOTI ALLIANCE FOR INTERNET OF THINGS INNOVATION IoT LSP Standard Framework Concepts Release 2.0 AIOTI WG03 – loT Standardisation 2015 AIOTI ALLIANCE FOR INTERNET OF THINGS INNOVATION Executive Summary This deliverable introduces IoT Standards Developing Organisation (SDO), Alliance and Open Source Software (OSS) landscapes to be used as input for the recommendations for Large Scale Pilots (LSPs) standard framework and gap analysis. The LSPs can play an important role in investigating and solving specific challenges for the IoT industry and promoting innovation that is related to specific activities such as 1) the applied standards framework, 2) deployments, 3) technological and business model validation and 4) acceptability. The main objective of this deliverable is to briefly present the global dynamics and landscapes of IoT SDO, Alliance and OSS initiatives, which can be used: 1) to leverage on existing IoT standardization, industry promotion and implementation of standards and protocols, 2) as input for LSP standards framework and gap analysis and 3) to provide a guideline for the proponents of future project proposals associated with future IoT related calls financed by the EC on the positioning of these initiatives within these landscapes. AIOTI – Restricted 2 AIOTI ALLIANCE FOR INTERNET OF THINGS INNOVATION Table of Contents 1. GOAL AND MOTIVATION............................................................................................................................. 4 2. IOT SDO AND ALLIANCE INITIATIVES LANDSCAPE.......................................................................... -
TION GALVANOMETERS in the Vibration Galvanorneter
A paper to be presented at the 29th Annual Con* vention of the American Institute of Electrical Engineers, Boston, Mass., June 25, 1912. Copyright, 1912. By Α. I. Ε. E. (Subject to final revision for the Transactions.) CHARACTERISTICS AND APPLICATIONS OF VIBRA- TION GALVANOMETERS BY FRANK WENNER In the vibration galvanorneter we have a type of synchronous motor which is distinctly different from all the ordinary types of dynamo electric machines. Further it does not have any of the characteristics of any of the ordinary galvanometers and except for the fact that it is used in the detection or measure ment of small currents and voltages, it should not be called a galvanometer. In galvanometers, except when used in the measurement of transient currents or quantity of electricity, the moving system is displaced until we have an equality of static couples acting on it. In the vibration galvanometer the equilibrium condition is an equality between integral values of the product of the current and generated voltage and the mechanical power dissipated in various ways as in ordinary electric motors when operated without a load. It therefore behaves more like an electric motor than like a galvanometer. Further, since it is used only with alternating currents and op erates in synchronism with the current it must necessarily have some of the characteristics of a synchronous motor. As a motor the efficiency of conversion was found in a particular case to be as high as 97J per cent while the power required to maintain an easily discernable amplitude of vibration was of the order of 10-11 watts. -
HOW the SCIO TECHNOLOGY WORKS Many Have Asked What Is
HOW THE SCIO TECHNOLOGY WORKS Many have asked what is measured by the SCIO/QXCI medical device. This incredible advancement in medicine measures subtle electrical factors of the body. The history of alternative medicine has been dominated by old style resistance measuring devices. These antique devices depended on the operator to apply the probe to the acupuncture point. By subtle changing the speed of probe delivery (not the pressure), the operator could influence the outcome. This prevented true results. The other complication was the limits of just resistance testing. The body is much more complicated than just resistance. The electrical factors of the body include voltage, amperage, capacitance, inductance, frequency, and many others. The basics of bio-electrical medicine lie in the voltage, amperage, and resistance. The only thing that can truly be measured in electricity is the voltage and amperage. Everything else is a mathematical variation of voltage and amperage. So the QXCI device starts by measuring multiple channels of this information. Multiple channels are needed so that we can see variations in the electrical potential and flow of the body total. So we measure the extremities and the head. This direct measurement is of four channels of voltage, four of amperage, and four of resistance. These come into the computer for amplification and the computer acts as a frequency counter for receiving this data. This makes an active twelve channel measuring device. Other calculations are made mathematically. Resistance cannot be measured directly. It must be calculated from an amperage or voltage meter. Same as that any capacitance meters cannot directly measure capacitance it must do a mathematical adjustment of voltage and amperage flow. -
Arxiv:1708.02856V1 [Cond-Mat.Mes-Hall] 9 Aug 2017 Systems Close to Equilibrium
Probing the energy reactance with adiabatically driven quantum dots Mar´ıaFlorencia Ludovico,1, 2 Liliana Arrachea,1, 3 Michael Moskalets,4 and David S´anchez5 1International Center for Advanced Studies, UNSAM, Campus Miguelete, 25 de Mayo y Francia, 1650 Buenos Aires, Argentina 2The Abdus Salam International Centre for Theoretical Physics, Strada Costiera 11, I-34151 Trieste, Italy 3Dahlem Center for Complex Quantum Systems and Fachbereich Physik, Freie Universit¨atBerlin, 14195 Berlin, Germany 4Department of Metal and Semiconductor Physics, NTU "Kharkiv Polytechnic Institute", 61002 Kharkiv, Ukraine 5Institute for Cross-Disciplinary Physics and Complex Systems IFISC (UIB-CSIC), E-07122 Palma de Mallorca, Spain The tunneling Hamiltonian describes a particle transfer from one region to the other. While there is no particle storage in the tunneling region itself, it has associated certain amount of energy. We name the corresponding flux energy reactance since, like an electrical reactance, it manifests itself in time-dependent transport only. Noticeably, this quantity is crucial to reproduce the universal charge relaxation resistance for a single-channel quantum capacitor at low temperatures. We show that a conceptually simple experiment is capable of demonstrating the existence of the energy reactance. PACS numbers: 73.23.-b, 72.10.Bg, 73.63.Kv, 44.10.+i Motivation. A very exciting experimental activity is lately taking place in search of controlling on-demand quantum coherent charge transport in the time domain. The recent burst of activity started with the experimen- Floating contact tal realization of quantum capacitors in quantum dots under ac driving [1], single particle emitters [2], and was followed by the generation of quantum charged solitons over the Fermi sea (levitons) [3]. -
Standards Publications
IRISH STANDARDS PUBLISHED BASED ON CEN/CENELEC STANDARDS 1. I.S. 178:1973 Date published 28 SEPTEMBER 2005 Extruded Rigid PVC Corrugated Sheeting 2. I.S. EN 60835-1-2:1993 Date published 1 JUNE 2005 Methods of measurement for equipment used in digital microwave radio transmission systems -- Part 1: Measurements common to terrestrial radio-relay systems and satellite earth stations -- Section 2: Basic characteristics (IEC 60835-1-2:1992 (EQV)) 3. I.S. EN 160000:1993/A1:1996 Date published 1 JUNE 2005 Generic Specification: Modular electronic units 4. I.S. EN 61595-1:1999 Date published 1 JUNE 2005 Multichannel digital audio tape recorder (DATR), reel-to-reel system, for professional use -- Part 1: Format A (IEC 61595-1:1997 (EQV)) 5. I.S. EN 1990:2002+NA:2010 Date published 24 MARCH 2005 Eurocode - Basis of structural design (including Irish National Annex) 6. I.S. EN ISO 14122-4:2004 Date published 23 FEBRUARY 2005 Safety of machinery - Permanent means of access to machinery - Part 4: Fixed ladders (ISO 14122-4:2004) 7. I.S. EN 13877-1:2004 Date published 23 SEPTEMBER 2005 Concrete pavements - Part 1: Materials 8. I.S. EN 13877-2:2004 Date published 23 SEPTEMBER 2005 Concrete pavements - Part 2: Functional requirements for concrete pavements 9. I.S. EN 12843:2004 Date published 4 MARCH 2005 Precast concrete products - Masts and poles 10. I.S. EN 13225:2005 Date published 4 MARCH 2005 Precast concrete products - Linear structural elements 11. I.S. EN 13693:2004 Date published 4 MARCH 2005 Precast concrete products - Special roof elements 12. -
COUNTRIES MAPS and METADATA REPORT Deliverable 3.1.1
SIMONA D 3.1.1 COUNTRIES MAPS AND METADATA REPORT Deliverable 3.1.1 1 Programme co-funded by the European Union funds (ERDF, IPA, ENI) SIMONA D 3.1.1 Project title Sediment-quality Information, Monitoring and Assessment System to support transnational cooperation for joint Danube Basin water management Acronym SIMONA Project duration 1st June 2018 to 1st May 2021, 36 months Date of preparation 30/04/2019 Compiled by: Veronica Alexe, Anca-Marina Vijdea Authors (in alphabetical order): Veronica Alexe (IGR), Jasminka Alijagić (GEOZS), Albert Baltres (IGR), Sonja Cerar (GEOZS), Gheorghe Damian (TUCN), Neda Dević (GSM), Katalin Mária Dudás (NAIC), Petyo Filipov (GI-BAS), Edith Haslinger (AIT), Zuzana Hiklová (SWME), Atanas Hikov (GI-BAS), Pavel Hucko (WRI-VUVH), Gheorghe Iepure (TUCN), Danijel Ivanišević (HGI-CGS), Ana Čaić Janković (HGI-CGS), Gyozo Jordan (SZIE), Paul Kinner (AIT), Volodymyr Klos (UGC), Jozef Kordík (SGIDS), Aleksandra Kovacevic (JUVS), Zsófia Kovács (OVF), Tanja Knoll (GBA), Zlatka Milakovska (GI-BAS), Ivan Mišur (HGI-CGS), Tatjana Mitrović (UB-FMG), Daniel Nasui (TUCN), Igor Nicoară (IGS-ASM), Jarmila Nováková (SGIDS), Irena Peytcheva (GI-BAS), Sebastian Pfleiderer (GBA), Vladimír Roško (WRI-VUVH), Robert Šajn (GEOZS), Manfred Sengl (LfU), Ajka Šorša (HGI-CGS), Igor Stríček (SGIDS), Zsolt Szakacs (TUCN), Ľudmila Tokarčíková (SGIDS), Milena Vetseva (GI-BAS), Jelena Vicanovic (JUVS), Anca- Marina Vijdea (IGR), Dragica Vulić (JCI). Responsible(s) of the deliverable: Anca-Marina Vijdea (IGR) Co-responsible(s) of the deliverable: Gyozo Jordan (SZIE) 2 Programme co-funded by the European Union funds (ERDF, IPA, ENI) SIMONA D 3.1.1 Contents Contents ....................................................................................................................................................................................... 3 1. INTRODUCTION ........................................................................................................................................................... 9 2.