Wearable Haptic Systems for the Fingertip and the Hand: Taxonomy, Review, and Perspectives 3
Total Page:16
File Type:pdf, Size:1020Kb
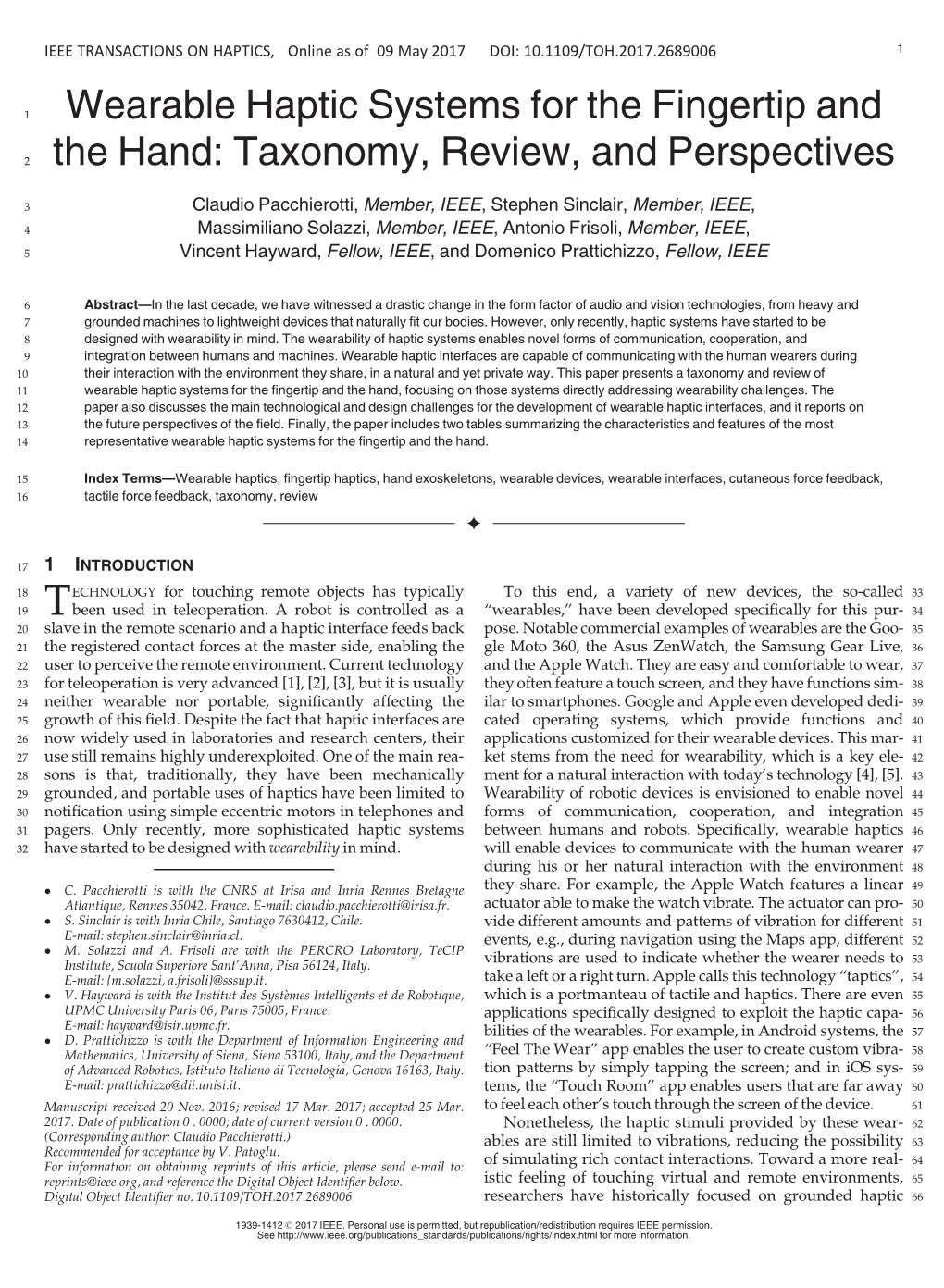
Load more
Recommended publications
-
Digital Humanities Pedagogy: Practices, Principles and Politics
To access digital resources including: blog posts videos online appendices and to purchase copies of this book in: hardback paperback ebook editions Go to: https://www.openbookpublishers.com/product/161 Open Book Publishers is a non-profit independent initiative. We rely on sales and donations to continue publishing high-quality academic works. Digital Humanities Pedagogy: Practices, Principles and Politics Edited by Brett D. Hirsch http://www.openbookpublishers.com © 2012 Brett D. Hirsch et al. (contributors retain copyright of their work). Some rights are reserved. The articles of this book are licensed under a Creative Commons Attribution-NonCommercial-NoDerivs 3.0 Unported Licence. This license allows for copying any part of the work for personal and non-commercial use, providing author attribution is clearly stated. Details of allowances and restrictions are available at: http://creativecommons.org/licenses/by-nc-nd/3.0/ As with all Open Book Publishers titles, digital material and resources associated with this volume are available from our website at: http://www.openbookpublishers.com/product/161 ISBN Hardback: 978-1-909254-26-8 ISBN Paperback: 978-1-909254-25-1 ISBN Digital (pdf): 978-1-909254-27-5 ISBN Digital ebook (epub): 978-1-909254-28-2 ISBN Digital ebook (mobi): 978-1-909254-29-9 Typesetting by www.bookgenie.in Cover image: © Daniel Rohr, ‘Brain and Microchip’, product designs first exhibited as prototypes in January 2009. Image used with kind permission of the designer. For more information about Daniel and his work, see http://www.danielrohr.com/ All paper used by Open Book Publishers is SFI (Sustainable Forestry Initiative), and PEFC (Programme for the Endorsement of Forest Certification Schemes) Certified. -
A Study of Bluetooth Low Energy Performance for Human Proximity Detection in the Workplace
CORE Metadata, citation and similar papers at core.ac.uk Provided by Apollo A Study of Bluetooth Low Energy Performance for Human Proximity Detection in the Workplace Alessandro Montanari, Sarfraz Nawaz, Cecilia Mascolo Kerstin Sailer Computer Laboratory, University of Cambridge Space Syntax Laboratory, University College London Cambridge, United Kingdom London, United Kingdom Email: [email protected] Email: [email protected] Abstract—The ability to detect and distinguish interactions in fine granularity but require dedicated hardware which hinder the workplace can shed light over productivity, team work and on adoption [11], [12], [13]. The recent interest in wearable employees’ use of space. Questionnaires and direct observations devices [14] has brought us to question if those devices are have often been used as mechanisms to identify office based interactions, however, these are either very time consuming, yield able to fulfill both needs. In particular we directed our attention coarse grained information or do not scale to large numbers of towards Bluetooth Low Energy (BLE) which is included in all people. Technology has been recently employed to cut costs and current wearables. We envision an interaction sensing system improve output, however precise interaction dynamics gathering that can be easily installed on a wearable device like a smart often requires individuals to wear custom hardware. watch thus extending its functionality to interaction sensing In this paper, we present an extensive evaluation of Bluetooth Low Energy (BLE) as a technology to monitor people proximity and offering widespread adoption. However, before this can in the workplace. We examine the key parameters that affect become a reality there are fundamental questions which need the accuracy of the detected contacts and their impact on power answers. -
A Survey of Smartwatch Platforms from a Developer's Perspective
Grand Valley State University ScholarWorks@GVSU Technical Library School of Computing and Information Systems 2015 A Survey of Smartwatch Platforms from a Developer’s Perspective Ehsan Valizadeh Grand Valley State University Follow this and additional works at: https://scholarworks.gvsu.edu/cistechlib ScholarWorks Citation Valizadeh, Ehsan, "A Survey of Smartwatch Platforms from a Developer’s Perspective" (2015). Technical Library. 207. https://scholarworks.gvsu.edu/cistechlib/207 This Project is brought to you for free and open access by the School of Computing and Information Systems at ScholarWorks@GVSU. It has been accepted for inclusion in Technical Library by an authorized administrator of ScholarWorks@GVSU. For more information, please contact [email protected]. A Survey of Smartwatch Platforms from a Developer’s Perspective By Ehsan Valizadeh April, 2015 A Survey of Smartwatch Platforms from a Developer’s Perspective By Ehsan Valizadeh A project submitted in partial fulfillment of the requirements for the degree of Master of Science in Computer Information Systems At Grand Valley State University April, 2015 ________________________________________________________________ Dr. Jonathan Engelsma April 23, 2015 ABSTRACT ................................................................................................................................................ 5 INTRODUCTION ...................................................................................................................................... 6 WHAT IS A SMARTWATCH -
Smartwatch Security Research TREND MICRO | 2015 Smartwatch Security Research
Smartwatch Security Research TREND MICRO | 2015 Smartwatch Security Research Overview This report commissioned by Trend Micro in partnership with First Base Technologies reveals the security flaws of six popular smartwatches. The research involved stress testing these devices for physical protection, data connections and information stored to provide definitive results on which ones pose the biggest risk with regards to data loss and data theft. Summary of Findings • Physical device protection is poor, with only the Apple Watch having a lockout facility based on a timeout. The Apple Watch is also the only device which allowed a wipe of the device after a set number of failed login attempts. • All the smartwatches had local copies of data which could be accessed through the watch interface when taken out of range of the paired smartphone. If a watch were stolen, any data already synced to the watch would be accessible. The Apple Watch allowed access to more personal data than the Android or Pebble devices. • All of the smartwatches we tested were using Bluetooth encryption and TLS over WiFi (for WiFi enabled devices), so consideration has obviously been given to the security of data in transit. • Android phones can use ‘trusted’ Bluetooth devices (such as smartwatches) for authentication. This means that the smartphone will not lock if it is connected to a trusted smartwatch. Were the phone and watch stolen together, the thief would have full access to both devices. • Currently smartwatches do not allow the same level of interaction as a smartphone; however it is only a matter of time before they do. -
Samsung, LG Launch Smartwatches with New Google Software 26 June 2014
Samsung, LG launch smartwatches with new Google software 26 June 2014 largest smartphone maker, respectively. A typical smartwatch allows users to make calls, receive texts and e-mails, take photos and access apps. G Watch opened Thursday for online pre-order in 12 countries including the United States, France and Japan before hitting stores in 27 more including Brazil and Russia in early July. Gear Live was also available for online pre-order Thursday. Visitors check out Samsung Gear Live watches during the Google I/O Developers Conference at Moscone Center in San Francisco, California, on June 25, 2014 South Korea's Samsung and LG on Thursday launched rival smartwatches powered by Google's new software as they jostle to lead an increasingly competitive market for wearable devices seen as the mobile industry's next growth booster. Samsung's "Gear Live" and LG's "G Watch"—both powered by Android Wear—are the first devices to adopt the new Google software specifically A LG G watch is seen on display during the Google I/O designed for wearables. Developers Conference at Moscone Center in San Francisco, California, on June 25, 2014 G Watch—LG's first smartwatch—is also equipped with Google's voice recognition service and can perform simple tasks including checking email, sending text messages and carrying out an online The launches come as global handset and software search at users' voice command. makers step up efforts to diversify from the saturated smartphone sector to wearable devices. The two devices cannot make phone calls by themselves but can be connected to many of the Samsung introduced its Android-based Galaxy latest Android-based smartphones, the South Gear smartwatch last year but it was given a Korean companies said in separate statements. -
Laval Virtual's Missions Are to Gather, Inspire and Valorize Involved in This Study
The VR/AR special edition #4 health Clinical VR Medicine Well Being #EDITORIAL How VR is changing the way women breast cancer is diagnosed, treated and managed LAURENT CHRÉTIEN DIRECTOR / LAVAL VIRTUAL ancer cells live in complex communities. They will then take all the information they Just like houses in a city, each cell in a collect about the cells in a tumour and use it tumour is different from its neighbour, to construct a 3D version that can be studied Cand relies on infrastructure to support using virtual reality. its existence. And we know that there are different neighbourhoods, some worse than Using virtual reality will allow scientists others. Where we have roads, tumours contain to immerse themselves in a tumour, blood vessels that deliver nutrients, and act meaning they can study patterns and other as highways for different cell types to move characteristics within it, in entirely new around. And when a tumour spreads, the can- ways that aren’t possible in 2D. It will also cer cells themselves use these blood ‘roads’ to allow multiple doctors and scientists to look migrate. at a tumour at the same time, meaning people at opposite ends of a country, and with different areas of expertise, can What the healthcare experts need is a Google Earth-like view work together to help diagnose and treat patients better. And of a tumour. If they could make a 3D map, they would find with the Covid19 crisis, the use of virtual reality to cooperate new targets for treatment and, eventually, could use this view remotely is even more obvious! to track what’s going on in real time, such as in response to treatment. -
Wearable Haptic Systems for the Fingertip and the Hand: Taxonomy, Review, and Perspectives
IEEE TRANSACTIONS ON HAPTICS, VOL. XX, NO. X, XX 20XX 1 Wearable Haptic Systems for the Fingertip and the Hand: Taxonomy, Review, and Perspectives Claudio Pacchierotti, Member, IEEE, Stephen Sinclair, Member, IEEE, Massimiliano Solazzi, Member, IEEE, Antonio Frisoli, Member, IEEE, Vincent Hayward, Fellow, IEEE, Domenico Prattichizzo, Fellow, IEEE Abstract—In the last decade, we have witnessed a drastic change in the form factor of audio and vision technologies, from heavy and grounded machines to lightweight devices that naturally fit our bodies. However, only recently, haptic systems have started to be designed with wearability in mind. The wearability of haptic systems enables novel forms of communication, cooperation, and integration between humans and machines. Wearable haptic interfaces are capable of communicating with the human wearers during their interaction with the environment they share, in a natural and yet private way. This paper presents a taxonomy and review of wearable haptic systems for the fingertip and the hand, focusing on those systems directly addressing wearability challenges. The paper also discusses the main technological and design challenges for the development of wearable haptic interfaces, and it reports on the future perspectives of the field. Finally, the paper includes two tables summarizing the characteristics and features of the most representative wearable haptic systems for the fingertip and the hand. Index Terms—wearable haptics, fingertip haptics, hand exoskeletons, wearable devices, wearable interfaces, cutaneous force feedback, tactile force feedback, taxonomy, review F 1 INTRODUCTION Technology for touching remote objects has typically been the Apple Watch. They are easy and comfortable to wear, used in teleoperation. A robot is controlled as a slave in they often feature a touch screen, and they have functions the remote scenario and a haptic interface feeds back the similar to smartphones. -
Haptic Augmented Reality 10 Taxonomy, Research Status, and Challenges
Haptic Augmented Reality 10 Taxonomy, Research Status, and Challenges Seokhee Jeon, Seungmoon Choi, and Matthias Harders CONTENTS 10.1 Introduction ..................................................................................................227 10.2 Taxonomies ...................................................................................................229 10.2.1 Visuo-Haptic Reality–Virtuality Continuum ...................................229 10.2.2 Artificial Recreation and Augmented Perception ............................. 232 10.2.3 Within- and Between-Property Augmentation ................................. 233 10.3 Components Required for Haptic AR ..........................................................234 10.3.1 Interface for Haptic AR ....................................................................234 10.3.2 Registration between Real and Virtual Stimuli ................................236 10.3.3 Rendering Algorithm for Augmentation ..........................................237 10.3.4 Models for Haptic AR.......................................................................238 10.4 Stiffness Modulation.....................................................................................239 10.4.1 Haptic AR Interface ..........................................................................240 10.4.2 Stiffness Modulation in Single-Contact Interaction .........................240 10.4.3 Stiffness Modulation in Two-Contact Squeezing .............................243 10.5 Application: Palpating Virtual Inclusion in Phantom -
Virtual Reality and Augmented Reality a Survey from Scania’S Perspective
EXAMENSARBETE INOM MASKINTEKNIK, AVANCERAD NIVÅ, 30 HP STOCKHOLM, SVERIGE 2019 Virtual Reality and Augmented Reality A Survey from Scania’s Perspective KARL INGERSTAM KTH SKOLAN FÖR INDUSTRIELL TEKNIK OCH MANAGEMENT Virtual Reality and Augmented Reality A Survey from Scania’s Perspective Karl Ingerstam 2019 Master of Science Thesis TPRMM 2019 KTH – Industrial Engineering and Management Production Engineering SE-100 44 Stockholm Abstract Virtual reality and augmented reality are technological fields that have developed and expanded at a great pace the last few years. A virtual reality is a digitally created environment where computer- generated elements are displayed to a user via different interfaces for the respective senses. Video is used for displaying images, creating a realistic environment, while audio is played to stimulate hearing and other sorts of feedback is used to stimulate the sense of touch in particular. Augmented reality is a sub-category of virtual reality where the user sees the real surroundings, but computer-generated imagery is displayed on top of objects in the environment. This type of technology brings a lot of new possibilities and potential use cases in all sorts of areas, ranging from personal entertainment, communication and education to medicine and heavy industry. Scania is a global manufacturer of heavy trucks and buses, and provider of related services, based in Sweden. By studying Scania’s different departments and surveying the fields of virtual reality and augmented reality, the aim of this thesis is to identify situations and use cases where there is potential for Scania to implement virtual reality and augmented reality technology. This thesis also studies what obstacles implementation of these technologies bring. -
The Law and Ethics of Virtual Sexual Assault
The Law and Ethics of Virtual Sexual Assault Forthcoming in Barflied, W. and Blitz, M. The Law of Virtual and Augmented Reality (Cheltenham, UK: Edward Elgar Publishers, 2018). By John Danaher In 1993, Julian Dibbell wrote an article in The Village Voice describing the world’s first virtual rape.1 The incident he described took place in a virtual world called LambdaMOO, which is a text-based virtual environment that still exists to this day. People in LambdaMOO create avatars (onscreen ‘nicknames’) and interact with one another through textual descriptions. Dibbell’s article described an incident in which one character (Mr. Bungle) used a “voodoo doll” program2 to take control of two other users’ avatars and force them to engage in sexual acts with both his avatar and one another. At least one of the victims found the incident extremely traumatising, with Dibbell describing her later as having ‘postraumatic tears’ streaming down her face when she spoke about it.3 In 2003, a similar incident took place in Second Life. Second Life is a well-known virtual world, created by the engineer and entrepreneur Philip Rosedale. It is visual rather than textual in nature. People create virtual avatars that can interact with other user’s avatars in a reasonably detailed visual virtual environment. In 2007, the Belgian Federal Police announced that they would be investigating a ‘virtual rape’ incident that took place in Second Life back in 2003.4 Little is known about what actually happened, and the investigation does not appear to have progressed to a charge, but taking control of another character’s avatar and forcing it to engage in sexual acts was not unheard of in Second Life. -
IMMERSIVE MEDIA a STATE of the INDUSTRY May 2017
IMMERSIVE MEDIA A STATE OF THE INDUSTRY May 2017 VR/AR Project VR/AR Project vrarproject.com [email protected] VR/AR Project New Amsterdam Media 1 VR/AR Project May 1, 2017 Rev 3.0 Editor: Seth Shapiro Deputy Editors: Bryce Paul & Andriy Pishchalenko Contributors: Perisa Brown, John Canning, Amy Dai, Xingting Gu, Hudson Leiser, Francisco Serna, Kinsey Thompson V2 Seth Shapiro 2016 Andriy Pishchalenko V1 Seth Shapiro 2015 Andriy Pishchalenko [email protected] VR/AR Project New Amsterdam Media 2 VR/AR Project [email protected] VR/AR Project New Amsterdam Media 3 VR/AR Project THIS IS AN OPEN COMMUNITY PROJECT. THIS IS A SNAPSHOT OF A RAPIDLY EVOLVING LANDSCAPE. TO OPT IN FOR FUTURE VERSIONS OF THIS PAPER, JOIN US AT VRARPROJECT.COM EMAIL US AT [email protected] [email protected] VR/AR Project New Amsterdam Media 4 VR/AR Project TABLE OF CONTENTS I 1. Preface 7 2. Overview 8 3. Enterprise Use Cases 9 Advertising & Marketing 9 Aerospace & Defense 11 Construction 12 Education 14 Entertainment 15 Fashion 18 Finance 19 Gaming 21 Healthcare 24 Live Events 26 Real Estate 28 Retail 29 Training 31 Travel & Hospitality 32 4. Computer Rendered VR 35 5. Live Action VR 37 6. Web VR 38 7. Social VR 39 8. Location-Based VR 42 Theme parks 42 VRcades 44 9. Smartphone VR/AR 46 10. VR Head Mounted Displays (HMDs) 49 11. AR/MR Head Mounted Displays (HMDs) 54 12. Spatial Audio 59 13. Haptics, Accessories, and Control Systems 63 Omnidirectional Treadmills 66 Exercise and fitness 29 Haptic Suits 64 Galvanic Vestibular Stimulation (GVS) 67 [email protected] VR/AR Project New Amsterdam Media 5 VR/AR Project TABLE OF CONTENTS II Advanced movement tracking 66 14. -
Smart Watch OS Mobile OS Supported by Komoot Tours
Tours (Link for Detailed Description) Navigation Speedometer Average & Current Speed, Time Smart Watch OS Mobile OS Supported by Komoot Smart Tour Arrows, Street Name & Saved/Offline Notifications Average & Current Speed & Distance Traveled & Progress / Recommendations Distance Updates Position on Tour Apple Watch iOS App - Video with Details 1 3 yes yes yes Android Wear Moto 360 LG G Watch R Sony Smart Watch 3 Android 4.3 App - Video with Details yes yes yes LG G Watch Samsung Gear Live ...further Android Wear Tizen 2.3 Gear S3 Android (only Gear S2 with Samsung New App with Tizen 2.3 5 3 yes yes yes yes Gear S Phone) Gear 2 OS that supports Notifications iOS & Android Notifications Pebble iOS & Android Notifications Fenix 3 iOS & Android Notifications Vivo Active iOS & Android Notifications yes (as shown on linked Forerunner 920XT iOS & Android Notifications picture during testing) Epix iOS & Android Notifications iOS Android Android Wear Notifications Wear App Other not supported Sony Smart Watch 2 Android 4.0 not supported Samsung Gear Fit (RTOS) Samsung not supported Other Devices Navigation via linked bike computer, demo video Ciclo HAC 1, HAC 2.1 iOS & Android BLE Connect via app settings linked here Navigation via linked Yamaha Display C iOS & Android Bluetooth Connect via app settings Yamaha display Navigation via linked Wahoo Elemnt, Elemnt Bolt iOS & Android Profile Connect Elemnt Navigation via linked Sigma Sigma Rox 12.0 iOS & Android komoot Profile Connect Rox COBI iOS & Android Navigation via linked COBI Garmin D2™ Charlie