Case Study Engineering Plastics By
Total Page:16
File Type:pdf, Size:1020Kb
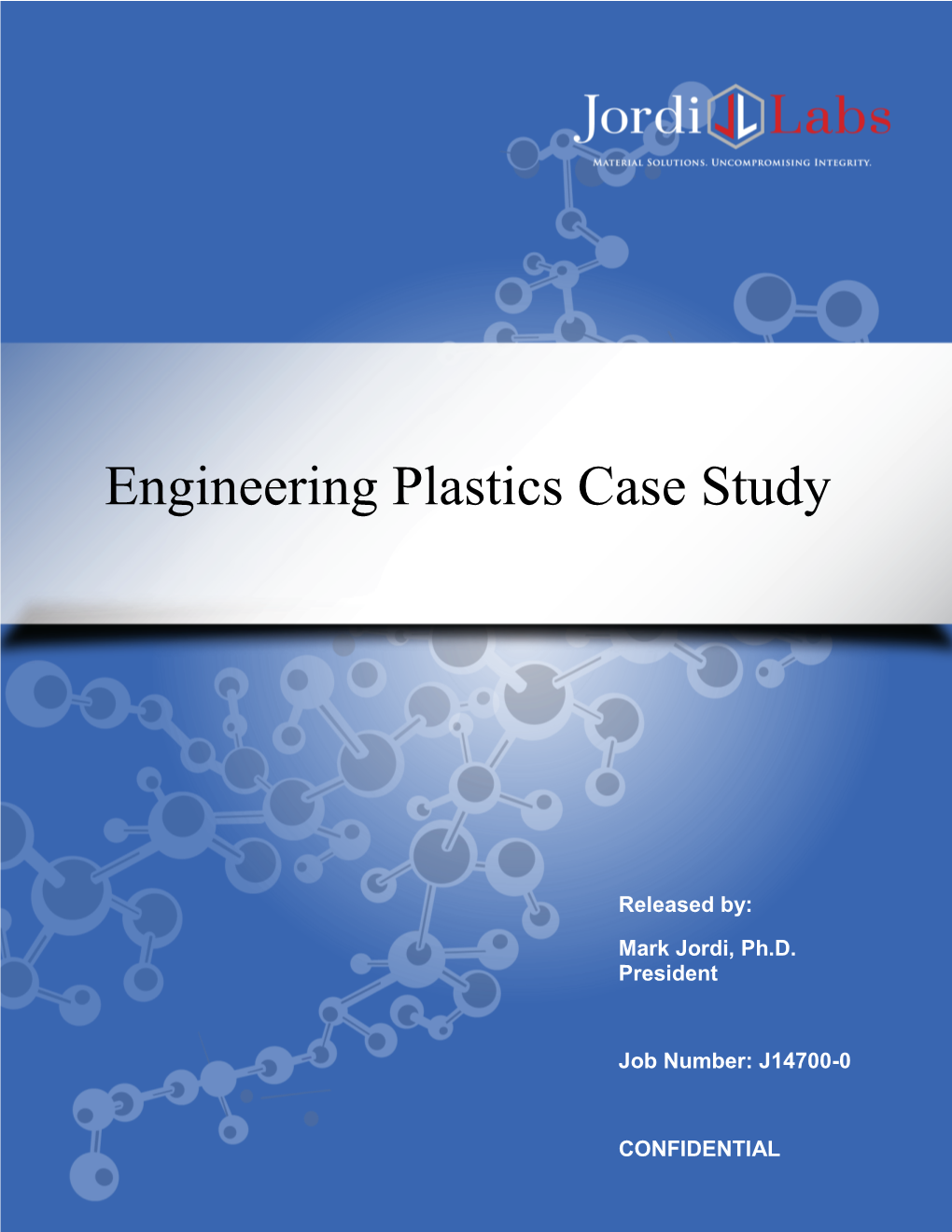
Load more
Recommended publications
-
Polycarbonate Lenses
Polycarbonate Lenses The most impact resistant of all lens materials is polycarbonate. Children, athletes, anyone working at a job or hobby where they might get hit in the face and need safety glasses, people with only one eye, those who fall a lot, are natural candidates for polycarbonate lenses. If safety is a prime concern, choose polycarbonate lenses. Advantages of polycarbonate lenses : 1. Polycarbonate has four to five times the impact resistance of glass or plastic. When glass or plastic lenses break, they do not break into harmless granules, but can break into sharp shards that can enter your eye and destroy your vision. Poly- carbonate is far and away the safest of all the lenses made. 2. Polycarbonate is the lightest lens material made. 3. Polycarbonate lenses naturally provide protection against ultra-violet light, at no additional charge. 4. Polycarbonate lenses come with a scratch resistant coating (not scratch proof) at no additional charge. 5. Polycarbonate is a high index material, so the lenses will be thinner than if made with glass or plastic. Disadvantages of polycarbonate lenses : 1. People in prescriptions with higher powers sometimes have trouble seeing out the edges of the lenses--your clear field of vision is not as wide as with glass or plas- tic lenses. The lenses are made with different curves than are used to make the same pre- scription power in glass or plastic, so you will see out of these lenses a little dif- ferently. People with prescriptions up to plus or minus three diopters (most people) usually have no problem adjusting to polycarbonate lenses. -
Quadrant EPP Cestilene™ HD 1000 Polyethylene Datasheet
www.lookpolymers.com email : [email protected] Quadrant EPP Cestilene™ HD 1000 Polyethylene Category : Polymer , Thermoplastic , Polyethylene (PE) , HDPE , High Density Polyethylene (HDPE), Injection Molded Material Notes: Data provided by Quadrant Engineering Plastic Products for polymers in their European product line. Order this product through the following link: http://www.lookpolymers.com/polymer_Quadrant-EPP-Cestilene-HD-1000-Polyethylene.php Physical Properties Metric English Comments Density 0.930 g/cc 0.0336 lb/in³ ISO 1183 Water Absorption 0.010 % 0.010 % immersion Mechanical Properties Metric English Comments Hardness, Shore D 60 60 after 15 sec.; ISO 868 62 62 after 3 sec.; ISO 868 Ball Indentation Hardness 36.0 MPa 5220 psi ISO 2039-1 Tensile Strength, Yield 19.0 MPa 2760 psi ISO 527 Elongation at Break >= 50 % >= 50 % ISO 527 Elongation at Yield 15 % 15 % ISO 527 Tensile Modulus 0.750 GPa 109 ksi ISO 527 Compressive Yield Strength 4.50 MPa 653 psi at 1% nominal strain; ISO 604 8.00 MPa 1160 psi at 2% nominal strain; ISO 604 14.0 MPa 2030 psi at 5% nominal strain; ISO 604 Charpy Impact Unnotched NB NB ISO 179/1eU Charpy Impact, Notched 11.0 J/cm² 52.4 ft-lb/in² Partial Break; ISO 179/1eA Abrasion 100 100 Relative loss per DSM internal test (CESTILENE HD 1000 = 100) Thermal Properties Metric English Comments 175 - 225 µm/m-°C 97.2 - 125 µin/in-°F CTE, linear @Temperature 20.0 °C @Temperature 68.0 °F Thermal Conductivity 0.400 W/m-K 2.78 BTU-in/hr-ft²-°F Melting Point 130 - 135 °C 266 - 275 °F ISO 3146; DSC, 10°C/min -
Engineered-Plastics.Pdf
PLASTIC PLASTICS REFERENCE HANDBOOK REGAL PLASTIC SUPPLY COMPANY PLASTICS REFERENCE HANDBOOK Copyright 1999—2000 Regal Plastic Supply Company, a division of Regal Supply Company INTRODUCTION Established in 1954, Regal Plastic Supply Company is considered one of the foremost pioneers in the plastic distribution industry. Throughout the years, the innovative “customer- oriented plan for success” thinking has become a credible trademark our customers rely on. Fortifying that philosophy, Regal introduced its Plastic Materials Reference Guide in 1984. As products and industries continue to evolve, so does this compilation of technical data. We view providing our customers with tools for effective planning and purchasing as important as meeting product “supply and demand”. You will find this guide an invaluable reference source for researching or finding the answer pertaining to your plastic application. The product information contained herein covers the most commonly used materials; it does not reflect our total capacity. True customer service is a thought process not developed overnight. Our experience and stability in the industry gives Regal the opportunity to assist you in your plastics endeavors as you utilize staff who are accessible, knowledgeable and resourceful with regard to all inquiries. We invite you to visit the Regal Plastic Supply Company location in your vicinity. All locations maintain generous inventories of plastic sheet, rod, tube, film, and numerous finished products. Regal Plastic Supply Company thanks all of our customers for their patronage over the years. We will continue in our efforts to provide the best in JIT inventory and personal service. Plastic is in your future and Regal Plastic Supply Company is your best source. -
Dispersity in Polymer Science
Pure Appl. Chem., Vol. 81, No. 2, pp. 351–353, 2009. doi:10.1351/PAC-REC-08-05-02 © 2009 IUPAC INTERNATIONAL UNION OF PURE AND APPLIED CHEMISTRY POLYMER DIVISION SUBCOMMITTEE ON POLYMER TERMINOLOGY* DISPERSITY IN POLYMER SCIENCE (IUPAC Recommendations 2009) Prepared by a Working Group consisting of R. G. GILBERT (AUSTRALIA), M. HESS (GERMANY), A. D. JENKINS (UK), R. G. JONES (UK), P. KRATOCHVÍL (CZECH REPUBLIC), AND R. F. T. STEPTO (UK) Prepared for publication by R. F. T. STEPTO‡ Polymer Science and Technology Group, Manchester Materials Science Centre, School of Materials, The University of Manchester, Grosvenor Street, Manchester, M1 7HS, UK *Membership of the Subcommittee on Polymer Terminology† during the preparation of this report (2003–2008) was as follows: M. Barón (Argentina, Secretary until 2003); M. Hess (Germany, Chairman to 2005, Secretary, 2006–2007); R. G. Jones (UK, Secretary 2003–2005, Chairman, from 2006); T. Kitayama (Japan, Secretary, from 2008); G. Allegra (Italy); T. Chang (Korea); C. dos Santos (Brazil); A. Fradet (France); K. Hatada (Japan); J. He (China); K.-H. Hellwich (Germany); R. C. Hiorns (France); P. Hodge (UK); K. Horie (Japan); A. D. Jenkins (UK); J.-I. Jin (Korea); J. Kahovec (Czech Republic); P. Kratochvíl (Czech Republic); P. Kubisa (Poland); I. Meisel (Germany); W. V. Metanomski (USA); V. Meille (Italy); I. Mita (Japan); G. Moad (Australia); W. Mormann (Germany); C. Ober (USA); S. Penczek (Poland); L. P. Rebelo (Portugal); M. Rinaudo (France); I. Schopov (Bulgaria); M. Schubert (USA); F. Schué (France); V. P. Shibaev (Russia); S. Słomkowski (Poland); R. F. T. Stepto (UK); D. Tabak (Brazil); J.-P. -
Migration of Bisphenol a from Polycarbonate Plastic of Different Qualities
Migration of bisphenol A from polycarbonate plastic of different qualities Environmental project No. 1710, 2015 [Series Title and year] Title: Editing: Migration of Bisphenol A from polycarbonate Gitte Alsing Pedersen, DTU National Food Institute, plastic of different qualities Søren Hvilsted, DTU Danish Polymer Centre, Department of Chemical and Biochemical Engineering and Jens Højslev Petersen, DTU National Food Institute Technical University of Denmark Published by: The Danish Environmental Protection Agency Strandgade 29 1401 Copenhagen K Denmark www.mst.dk/english Year: ISBN no. 2015 978-87-93352-24-7 Disclaimer: When the occasion arises, the Danish Environmental Protection Agency will publish reports and papers concerning research and development projects within the environmental sector, financed by study grants provided by the Danish Environmental Protection Agency. It should be noted that such publications do not necessarily reflect the position or opinion of the Danish Environmental Protection Agency. However, publication does indicate that, in the opinion of the Danish Environmental Protection Agency, the content represents an important contribution to the debate surrounding Danish environmental policy. Sources must be acknowledged. 2 Migration of Bisphenol A from polycarbonate plastic of different qualities Contents Foreword .................................................................................................................. 5 Conclusion and Summary ......................................................................................... -
Blends of Polycarbonate Containing Fluorinated-Bisphenol-A and Polyvinyl Chloride
Europaisches Patentamt European Patent Office © Publication number: 0 576 057 A1 Office europeen des brevets EUROPEAN PATENT APPLICATION © Application number: 93201533.2 int. Ci.5; C08L 69/00, C08L 27/06, C08G 64/10, //(C08L69/00, @ Date of filing: 28.05.93 27:06),(C08L27/06,69:00) © Priority: 01.06.92 US 891032 © Applicant: ENICHEM S.p.A. Piazza della Repubblica, 16 @ Date of publication of application: 1-20124 Milano(IT) 29.12.93 Bulletin 93/52 @ Inventor: Drzewinski, Michael A. © Designated Contracting States: 371 Clarksville Road, Princeton Junction AT BE CH DE DK ES FR GB GR IE IT LI LU MC New Jersey 08850(US) NL PT SE © Representative: Roggero, Sergio et al Ing. Barzano & Zanardo Milano S.p.A. Via Borgonuovo 10 1-20121 Milano (IT) © Blends of polycarbonate containing fluorinated-bisphenol-A and polyvinyl chloride. © Bisphenol A polycarbonate containing at least 15 mole % of 2,2-bis-(4-hydroxyphenyl)hexafluoropropane (6F-Bisphenol A) can be blended with polyvinyl chloride (PVC) to form a thermodynamically miscible, transpar- ent, single phase blend at all compositions. Such blends are flame resistant as well as resistant to attack by acids, bases and many organic solvents. CO Rank Xerox (UK) Business Services (3. 10/3.6/3.3. 1) EP 0 576 057 A1 BACKGROUND OF THE INVENTION Field of the Invention: 5 This invention pertains to mixtures of polyvinyl chloride (PVC) and polycarbonates which contain at least 15 mole % of fluorinated bisphenol monomer units (F-PC) such as 2,2-bis-(4-hydroxyphenyl)- hexafluoropropane (6F-bisphenol A), herein referred to as 6F-PC. -
Brominated Polystyrene(BPS) FR
Brominated Polystyrene(BPS) FR Description Product Name : Brominated Polystyrene(BPS) Equivalent Name : Albermarle Saytex HP3010 ; Albermarle Saytex HP7010 ; Dead Sea FR‐803P Cas No. : 88497‐56‐7 Application It provides outstanding thermal stability and electrical performance. It is particularly suitable for engineering plastic applications such as polyesters (PET, PBT, PCT) and PA (nylons).it has outstanding thermal stability. It is an ideal choice for high temperature applications such as engineering plastics. Due to its stability, it can often be used where other flame retardants fail to survive. Due toits polymeric structure, it is non‐blooming in all applications. Excellent electrical properties provide yet another reason to choose this flame retardant for demanding engineering plastic applications. Benefits and Features Excellent Flow In Resin,Superior Color,Excellent Thermal Stability, Excellent Melt Stability, Excellent Non Blistering Performance, Improved Mechanical Properties,Low Loading Typical Properties BPS 3010 Appearance .............................................................................................................................................................. White grain/ yellowish powder. Content % ..........................................................................................................................................................................................................66 min. Melting point °C ............................................................................................................................................................................................. -
The Recent Developments in Biobased Polymers Toward
polymers Review The Recent Developments in Biobased Polymers toward General and Engineering Applications: Polymers that Are Upgraded from Biodegradable Polymers, Analogous to Petroleum-Derived Polymers, and Newly Developed Hajime Nakajima, Peter Dijkstra and Katja Loos * ID Macromolecular Chemistry and New Polymeric Materials, Zernike Institute for Advanced Materials, University of Groningen, Nijenborgh 4, 9747 AG Groningen, The Netherlands; [email protected] (H.N.); [email protected] (P.D.) * Correspondence: [email protected]; Tel.: +31-50-363-6867 Received: 31 August 2017; Accepted: 18 September 2017; Published: 18 October 2017 Abstract: The main motivation for development of biobased polymers was their biodegradability, which is becoming important due to strong public concern about waste. Reflecting recent changes in the polymer industry, the sustainability of biobased polymers allows them to be used for general and engineering applications. This expansion is driven by the remarkable progress in the processes for refining biomass feedstocks to produce biobased building blocks that allow biobased polymers to have more versatile and adaptable polymer chemical structures and to achieve target properties and functionalities. In this review, biobased polymers are categorized as those that are: (1) upgrades from biodegradable polylactides (PLA), polyhydroxyalkanoates (PHAs), and others; (2) analogous to petroleum-derived polymers such as bio-poly(ethylene terephthalate) (bio-PET); and (3) new biobased polymers such as poly(ethylene 2,5-furandicarboxylate) -
GPC - Gel Permeation Chromatography Aka Size Exclusion Chromatography- SEC
GPC - Gel Permeation Chromatography aka Size Exclusion Chromatography- SEC Wendy Gavin Biomolecular Characterization Laboratory Version 1 May 2016 1 Table of Contents 1. GPC Introduction………………………………………………………. Page 3 2. How GPC works………………………………………………………... Page 5 3. GPC Systems…………………………………………………………… Page 7 4. GPC/SEC Separations – Theory and System Considerations… Page 9 5. GPC Reports……………………………………………………………. Page 10 6. Calibrations of GPC systems………………………………………... Page 14 7. GPC preparation……………………………………………………….. Page 16 8. Alliance System………………………………………………………… Page 17 9. GPC columns…………………………………………………………… Page 18 2 1. GPC Introduction Gel permeation chromatography (GPC) is one of the most powerful and versatile analytical techniques available for understanding and predicting polymer performance. It is the most convenient technique for characterizing the complete molecular weight distribution of a polymer. Why is GPC important? GPC can determine several important parameters. These include number average molecular weight (Mn), weight average molecular weight(Mw) Z weight average molecular weight(Mz), and the most fundamental characteristic of a polymer its molecular weight distribution(PDI) These values are important, since they affect many of the characteristic physical properties of a polymer. Subtle batch-to-batch differences in these measurable values can cause significant differences in the end-use properties of a polymer. Some of these properties include: Tensile strength Adhesive strength Hardness Elastomer relaxation Adhesive tack Stress-crack resistance Brittleness Elastic modules Cure time Flex life Melt viscosity Impact strength Tear Strength Toughness Softening temperature 3 Telling good from bad Two samples of the same polymer resin can have identical tensile strengths and melt viscosities, and yet differ markedly in their ability to be fabricated into usable, durable products. -
Study of Surface Mechanical Characteristics of ABS/PC Blends Using Nanoindentation
processes Article Study of Surface Mechanical Characteristics of ABS/PC Blends Using Nanoindentation Saira Bano 1, Tanveer Iqbal 2, Naveed Ramzan 3 and Ujala Farooq 4,* 1 Department of Chemical & Polymer Engineering, University of Engineering & Technology, FSD Campus, Lahore 38000, Pakistan; [email protected] 2 Department of Chemical, Polymer & Composite Materials Engineering, University of Engineering & Technology, KSK Campus, Lahore 54890, Pakistan; [email protected] 3 Department of Chemical Engineering, University of Engineering & Technology, KSK Campus, Lahore 54890, Pakistan; [email protected] 4 Faculty of Aerospace Engineering, Aerospace Manufacturing Technologies, Delft University of Technology, Kluyverweg 1, 2629 HS Delft, The Netherlands * Correspondence: [email protected] Abstract: Acrylonitrile butadiene styrene (ABS) and polycarbonate (PC) are considered a well-known class of engineering thermoplastics due to their efficient use in automotive, 3D printing, and elec- tronics. However, improvement in toughness, processability, and thermal stability is achieved by mixing together ABS and PC. The present study focuses on the understanding of surface mechani- cal characterization of acrylonitrile butadiene styrene (ABS) and polycarbonate (PC) blends using nano-indentation. Polymer blends sheets with three different proportions of ABS/PC (75:25, 50:50, and 25:75) were fabricated via melt-processing and thermal press. Fourier transform infrared (FTIR) spectroscopy was performed to analyze the intermolecular interactions between the blends’ compo- nents. To understand the surface mechanical properties of ABS and PC blends, a sufficient number Citation: Bano, S.; Iqbal, T.; Ramzan, of nano-indentation tests were performed at a constant loading rate to a maximum load of 100 mN. N.; Farooq, U. -
Environmental Biodegradability of Recombinant Structural Protein
www.nature.com/scientificreports OPEN Environmental biodegradability of recombinant structural protein Yuya Tachibana1,2*, Sunita Darbe3, Senri Hayashi1, Alina Kudasheva3, Haruna Misawa1, Yuka Shibata1 & Ken‑ichi Kasuya1,2* Next generation polymers needs to be produced from renewable sources and to be converted into inorganic compounds in the natural environment at the end of life. Recombinant structural protein is a promising alternative to conventional engineering plastics due to its good thermal and mechanical properties, its production from biomass, and its potential for biodegradability. Herein, we measured the thermal and mechanical properties of the recombinant structural protein BP1 and evaluated its biodegradability. Because the thermal degradation occurs above 250 °C and the glass transition temperature is 185 °C, BP1 can be molded into sheets by a manual hot press at 150 °C and 83 MPa. The fexural strength and modulus of BP1 were 115 ± 6 MPa and 7.38 ± 0.03 GPa. These properties are superior to those of commercially available biodegradable polymers. The biodegradability of BP1 was carefully evaluated. BP1 was shown to be efciently hydrolyzed by some isolated bacterial strains in a dispersed state. Furthermore, it was readily hydrolyzed from the solid state by three isolated proteases. The mineralization was evaluated by the biochemical oxygen demand (BOD)‑ biodegradation testing with soil inocula. The BOD biodegradability of BP1 was 70.2 ± 6.0 after 33 days. Many commercially available polymers have some associated environmental problems1,2. Te increase in the production and subsequent disposal of synthetic polymers causes serious environmental pollution because these polymers do not degrade in the natural environment. -
Engineering Plastic ®
ENGINEERING PLASTIC ® General Engineering Plastic ACRYLIC (PERSPEX) TECAST-T (CAST NYLON) TECADUR (PET) BAKELITE HMWPE-500 TECAMID 6 (NYLON) POLYSTONE PP NYOIL HDPE-300 TECAFORM AH (POM) POLYCARBONATE ABS UHMWPE-1000 TECAMID 66 (PA66) TEFLON EPOXY G10 High Performance Engineering Plastic G 10 ESD TECATOR- PAI PPS PPO- NORYL TAKIRON PVC ESD UHMV-PE CONDUCTIVE TECAPEI-ULTEM TAKIRON PC ESD TORLON ENSITAL- POM SD UHMV-PE ANTI STATIC TURCITE AC-350/450 TECAPEEK VESPEL DELRIN AF ENGINEERING PLASTIC ® General Engineering Plastic Nylon 6 tough, wear- resistant, good vibration-absorption Nylon 6 MoS2 tough, better wear- resistant, and non stick properties than Nylon 6 Nylon 6 Glass Reinforced high strength and rigidity high wear resistance, harder, stiffer and better dimensional stability under Nylon 66 heat than Nylon 6 Nylon 66 Glass Reinforced high rigidity and strength hard, high compressive strength and wear resistance, high degree of Nylon 6 Cast crystallisation Cast Nylon 6 MoS2 very high wear resistance, very hard and rigid high wear resistance, low coefficient of friction - recommended for bearings Cast Nylon 6 Oil Impregnated with pv-value high strength, tough, low creep, better resistance to hydrolysis than Acetal Acetal Copolymer Homopolymer Acetal Homopolymer high strength Acetal Copolymer Glass Reinforced high strength, low thermal expansion, very low water absorption ABS tough, hard, can be galvanized PVC Excellent corrosion resistance, withstands strong acids and alkalis Polycarbonate transparent, tough, low creep, good electrical properties Polycarbonate Glass Reinforced high strength, low thermal expansion PET tough, hard, stable in dimension UHMW PE Excellent wear and abrasions resistance. Low coefficient of friction HDPE Good wear and abrasions resistance.