Chapter Iii Cadmium Zinc Telluride Wafer Processing
Total Page:16
File Type:pdf, Size:1020Kb
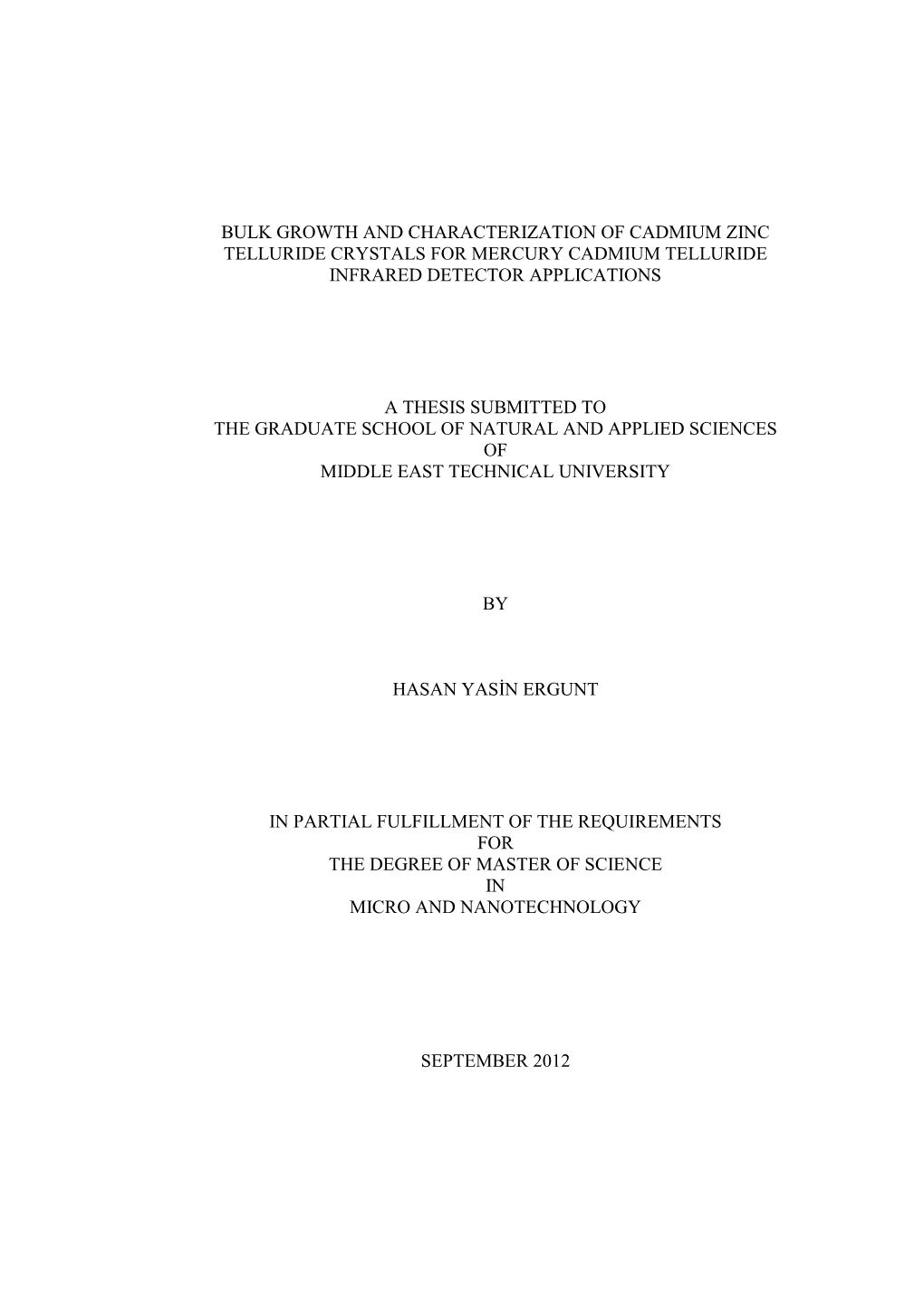
Load more
Recommended publications
-
Progress in the Development of Cdte and Cdznte Semiconductor Radiation Detectors for Astrophysical and Medical Applications
Sensors 2009, 9, 3491-3526; doi:10.3390/s90503491 OPEN ACCESS sensors ISSN 1424-8220 www.mdpi.com/journal/sensors Review Progress in the Development of CdTe and CdZnTe Semiconductor Radiation Detectors for Astrophysical and Medical Applications Stefano Del Sordo 1,*, Leonardo Abbene 1,2,*, Ezio Caroli 3, Anna Maria Mancini 4, Andrea Zappettini 5 and Pietro Ubertini 6 1 INAF/IASF Palermo, Via Ugo La Malfa 153, 90146 Palermo, Italy 2 Dipartimento di Fisica e Tecnologie Relative, Università di Palermo,Viale delle Scienze, 90128 Palermo, Italy 3 INAF/IASF Bologna, Via Gobetti 101, 40129 Bologna, Italy; E-Mail: [email protected] (E.C.) 4 Dipartimento di Ingegneria dell’Innovazione, Università del Salento, Via Arnesano, 73100 Lecce, Italy; E-Mail: [email protected] (A.M.M.) 5 IMEM-CNR, Parco Area delle Scienze 37/A, 43100 Parma, Italy; E-Mail: [email protected] (A.Z.) 6 INAF/IASF Roma, Via del Fosso del Cavaliere 100, 00133 Roma, Italy; E-Mail: [email protected] (P.U.) * Authors to whom correspondence should be addressed; E-Mails: [email protected]; (S.D.S.); [email protected] (L.A.); Tel. +39-091-6809563; Fax: +39-091-6882258 (S.D.S.); Tel. +39-091-6615053; Fax: +39-091-6615063 (L.A.) Received: 26 March 2009; in revised form: 5 May 2009 / Accepted: 8 May 2009 / Published: 12 May 2009 Abstract: Over the last decade, cadmium telluride (CdTe) and cadmium zinc telluride (CdZnTe) wide band gap semiconductors have attracted increasing interest as X-ray and gamma ray detectors. -
Two Cadmium Zinc Telluride (CZT) Semiconductor Detectors, a Lacl3(Ce) Scintillator, and an Nai(Tl) Scintillator
Performance comparison of four compact room- temperature detectors – two cadmium zinc telluride (CZT) semiconductor detectors, a LaCl3(Ce) scintillator, and an NaI(Tl) scintillator John K. Hartwell, Member IEEE, Robert J. Gehrke, and Michael E. Mc Ilwain measurement scenarios where portability, compact design, Abstract— The performance characteristics of four compact, and freedom from cryogenics are primary considerations. room-temperature detectors – two scintillators and two A recent publication provided performance comparison semiconductor detectors – were studied. All are commercially- data on three detectors including a ∅10 cm X 10 cm NaI(Tl), available detectors. The two scintillators were a ∅13 mm X a ∅55 mm X 54 mm HPGe detector, and a ∅9 mm X 2 mm 13 mm lanthanum chloride [LaCl3(Ce)] detector and a ∅25 mm X 25 mm sodium iodide [NaI(Tl)] detector. The two CdTe detector [1]. Our work, reported in this paper, provides semiconductor detectors were a 10 mm X 10 mm X 3 mm complimentary assessment data on a different suite of four cadmium zinc telluride (CZT) detector with a coplanar gridded highly portable detectors, including work with the promising anode and a 5 mm X 5 mm X 5 mm CZT detector with an new scintillator LaCl3(Ce). extended cathode. The efficiency, resolution, and peak shape of these devices are compared. Since LaCl (Ce) is a relatively new 3 II. EXPERIMENTAL METHOD commercial scintillator material, additional information on the performance of this detector is presented. Specifically, the The electronics system used for these evaluations consisted impact of naturally-occurring radioactive 138La and additional of a preamplifier, a linear amplifier (Tennelec TC244 or Ortec contamination from alpha-emitting radionuclides on the 460), and an multichannel analyzer (Amptek MCA8000A) background measured with this detector are discussed. -
Characterization of Cadmium Zinc Telluride Solar Cells by RF Sputtering Senthilnathan Subramanian University of South Florida
University of South Florida Scholar Commons Graduate Theses and Dissertations Graduate School 6-24-2004 Characterization of Cadmium Zinc Telluride Solar Cells by RF Sputtering Senthilnathan Subramanian University of South Florida Follow this and additional works at: https://scholarcommons.usf.edu/etd Part of the American Studies Commons Scholar Commons Citation Subramanian, Senthilnathan, "Characterization of Cadmium Zinc Telluride Solar Cells by RF Sputtering" (2004). Graduate Theses and Dissertations. https://scholarcommons.usf.edu/etd/1261 This Thesis is brought to you for free and open access by the Graduate School at Scholar Commons. It has been accepted for inclusion in Graduate Theses and Dissertations by an authorized administrator of Scholar Commons. For more information, please contact [email protected]. Characterization of Cadmium Zinc Telluride Solar Cells by RF Sputtering by Senthilnathan Subramanian A thesis submitted in partial fulfillment of the requirements for the degree of Master of Science in Electrical Engineering Department of Electrical Engineering College of Engineering University of South Florida Major Professor: Christos S. Ferekides, Ph.D. Don L. Morel, Ph.D. Yun L. Choiu, Ph.D Date of Approval: June 29, 2004 Keywords: czt, thin films, wide bandgap semiconductors, tandem solar cells © Copyright 2004 , Senthilnathan Subramanian DEDICATION This thesis is dedicated to my family and friends for their love and support. ACKNOWLEDGEMENT I would like to express my gratitude to my Major Professor Dr. Chris Ferekides for his invaluable guidance and support during the course of this work. He has been a great source of inspiration during my work here. I also thank Dr.Don L. Morel and Dr. -
Research Progress on Ultra-Precision Machining Technologies for Soft-Brittle Crystal Materials
Front. Mech. Eng. 2017, 12(1): 77–88 DOI 10.1007/s11465-017-0411-8 REVIEW ARTICLE Hang GAO, Xu WANG, Dongming GUO, Yuchuan CHEN Research progress on ultra-precision machining technologies for soft-brittle crystal materials © The Author(s) 2017. This article is published with open access at link.springer.com and journal.hep.com.cn 2017 Abstract Soft-brittle crystal materials are widely used in Mercury cadmium telluride (HgCdTe, MCT) single crystal many fields, especially optics and microelectronics. is the most significant material for infrared optoelectronic However, these materials are difficult to machine through devices and MCT-based high performance infrared traditional machining methods because of their brittle, soft, devices, and is widely used in the fields of aeronautics and anisotropic nature. In this article, the characteristics and astronautics [4]. Cadmium zinc telluride (CdZnTe, and machining difficulties of soft-brittle and crystals are CZT) single crystal is the most promising material for the presented. Moreover, the latest research progress of novel fabrication of room temperature radiation detectors [5,6] machining technologies and their applications for soft- and is also widely used as the perfect substrates for brittle crystals are introduced by using some representative growing epitaxial layers of MCT crystal [7]. CaF2 single materials (e.g., potassium dihydrogen phosphate (KDP), crystal is extensively applied in deep ultraviolet photo- cadmium zinc telluride (CZT)) as examples. This article lithography, solid-state lasers, and high-energy radiation reviews the research progress of soft-brittle crystals detection [8]. BaF2 single crystal with high transparency processing. for infrared and visible light is often used in CO2 laser hatch and infrared optical systems [9]. -
Journal of Materials Chemistry C Rscpublishing COMMUNICATION
Journal of Materials Chemistry C RSCPublishing COMMUNICATION The room temperature phosphine-free organometallic synthesis of near-infrared emitting Cite this: DOI: 10.1039/x0xx00000x HgSe quantum dots H. Mirzai,a M. N. Nordin,b,c R. J. Curry,b J.-S. Bouillard,a A. V. Zayats,a M. a Received 00th January 2012, Green* Accepted 00th January 2012 DOI: 10.1039/x0xx00000x Luminescent mercury selenide (HgSe) quantum dots have been synthesised by a phosphine- free method using oleic acid as a capping agent. The modification of experimental conditions www.rsc.org/ such as temperature resulted in particles of various sizes (15 - 100 nm) and morphologies not previously seen in HgSe, with emission tuneable between 1000 nm and 1350 nm. The popularity of semiconductor quantum dots (QDs) and b Advanced Technology Institute, Department of Electronic Engineering, their association with next-generation opto-electronic devices University of Surrey, Guildford, Surrey.UK GU2 7XH c and biomedical applications has grown rapidly over the last Present address: Medical Engineering Technology Department, University Kuala Lumpur, 53100, Gombak, Malaysia. years. Current research focuses on various synthetic routes as a means to modify QD characteristics to satisfy specific due to the lack of obvious and safe precursors (despite the optical and magnetic requirements for applications such as fact that many early routes to nano-dispersed semiconductors biological imaging,1 telecommunications,2 photodetection3 4 were based on mercury chalcogenides). We have focused on and solar energy. Quantum dots have provided a new source mercury chalcogenides due to their low reaction temperatures of electromagnetic radiation on the nano-scale. -
Properties of Sputtered Mercury Telluride Contacts on P-Type Cadmium Telluride A
Properties of sputtered mercury telluride contacts on p-type cadmium telluride A. Zozime, C. Vermeulin To cite this version: A. Zozime, C. Vermeulin. Properties of sputtered mercury telluride contacts on p-type cadmium telluride. Revue de Physique Appliquée, Société française de physique / EDP, 1988, 23 (11), pp.1825- 1835. 10.1051/rphysap:0198800230110182500. jpa-00246011 HAL Id: jpa-00246011 https://hal.archives-ouvertes.fr/jpa-00246011 Submitted on 1 Jan 1988 HAL is a multi-disciplinary open access L’archive ouverte pluridisciplinaire HAL, est archive for the deposit and dissemination of sci- destinée au dépôt et à la diffusion de documents entific research documents, whether they are pub- scientifiques de niveau recherche, publiés ou non, lished or not. The documents may come from émanant des établissements d’enseignement et de teaching and research institutions in France or recherche français ou étrangers, des laboratoires abroad, or from public or private research centers. publics ou privés. Revue Phys. Appl. 23 (1988) 1825-1835 NOVEMBRE 1988, 1825 Classification Physics Abstracts 73.40 - 79.20 Properties of sputtered mercury telluride contacts on p-type cadmium telluride A. Zozime and C. Vermeulin Laboratoire de Physique des Matériaux, CNRS, 1 place A. Briand, 92195 Meudon Cedex, France (Reçu le 12 avril 1988, révisé le 29 juillet 1988, accepté le 16 août 1988) Résumé. 2014 La valeur élevée du travail de sortie du composé semi-métallique HgTe (q03A6m ~ 5.9 eV) a conduit à utiliser ce matériau pour réaliser des contacts ohmiques de faible résistance spécifique 03C1c (03A9 cm2) sur le composé semi-conducteur II-VI CdTe de type p, dans la gamme des résistivités 70 03A9 cm 03C1B 45 k03A9 cm. -
Trends in Performance Limits of the HOT Infrared Photodetectors
applied sciences Review Trends in Performance Limits of the HOT Infrared Photodetectors Antoni Rogalski 1, Piotr Martyniuk 1,*, Małgorzata Kopytko 1 and Weida Hu 2 1 Faculty of Advanced Technologies and Chemistry, Institute of Applied Physics, Military University of Technology, 2 Kaliskiego St., 00-908 Warsaw, Poland; [email protected] (A.R.); [email protected] (M.K.) 2 State Key Laboratory of Infrared Physics, Shanghai Institute of Technical Physics, Chinese Academy of Sciences, 500 Yu Tian Road, Shanghai 200083, China; [email protected] * Correspondence: [email protected]; Tel.: +48-26-183-92-15 Abstract: The cryogenic cooling of infrared (IR) photon detectors optimized for the mid- (MWIR, 3–5 µm) and long wavelength (LWIR, 8–14 µm) range is required to reach high performance. This is a major obstacle for more extensive use of IR technology. Focal plane arrays (FPAs) based on thermal detectors are presently used in staring thermal imagers operating at room temperature. However, their performance is modest; thermal detectors exhibit slow response, and the multispectral detection is difficult to reach. Initial efforts to develop high operating temperature (HOT) photodetectors were focused on HgCdTe photoconductors and photoelectromagnetic detectors. The technological efforts have been lately directed on advanced heterojunction photovoltaic HgCdTe detectors. This paper presents the several approaches to increase the photon-detectors room-temperature performance. Various kinds of materials are considered: HgCdTe, type-II AIIIBV superlattices, two-dimensional materials and colloidal quantum dots. Keywords: HOT IR detectors; HgCdTe; P-i-N; BLIP condition; 2D material photodetectors; colloidal quantum dot photodetectors Citation: Rogalski, A.; Martyniuk, P.; Kopytko, M.; Hu, W. -
Fabrication of Small-Pixel Cdznte Sensors and Characterization with X-Rays
sensors Article Fabrication of Small-Pixel CdZnTe Sensors and Characterization with X-rays Stergios Tsigaridas 1,∗,† , Silvia Zanettini 2 , Manuele Bettelli 3 , Nicola Sarzi Amadè 3 , Davide Calestani 3 , Cyril Ponchut 1 and Andrea Zappettini 3 1 European Synchrotron Radiation Facility (ESRF), 71 Avenue des Martyrs, F-38043 Grenoble, France; [email protected] 2 Due2lab s.r.l., via Paolo Borsellino 2, 42019 Scandiano, Italy; [email protected] 3 IMEM-CNR, Istituto Materiali per l’Elettronica e il Magnetismo, Consiglio Nazionale delle Ricerche, Parco Area delle Scienze 37/A, 43124 Parma, Italy; [email protected] (M.B.); [email protected] (N.S.A.); [email protected] (D.C.); [email protected] (A.Z.) * Correspondence: [email protected] † Current address: TRIUMF, 4004 Wesbrook Mall, Vancouver, BC V6T 2A3, Canada. Abstract: Over the past few years, sensors made from high-Z compound semiconductors have attracted quite some attention for use in applications which require the direct detection of X-rays in the energy range 30–100 keV. One of the candidate materials with promising properties is cadmium zinc telluride (CdZnTe). In the context of this article, we have developed pixelated sensors from CdZnTe crystals grown by Boron oxide encapsulated vertical Bridgman technique. We demonstrate the successful fabrication of CdZnTe pixel sensors with a fine pitch of 55 µm and thickness of 1 mm and 2 mm. The sensors were bonded on Timepix readout chips to evaluate their response to X-rays Citation: Tsigaridas, S.; Zanettini, S.; provided by conventional sources. Despite the issues related to single-chip fabrication procedure, Bettelli, M.; Sarzi Amadè, N.; reasonable uniformity was achieved along with low leakage current values at room temperature. -
Bandgap-Engineered Hgcdte Infrared Detector Structures for Reduced Cooling Requirements
Bandgap-Engineered HgCdTe Infrared Detector Structures for Reduced Cooling Requirements by Anne M. Itsuno A dissertation submitted in partial fulfillment of the requirements for the degree of Doctor of Philosophy (Electrical Engineering) in The University of Michigan 2012 Doctoral Committee: Associate Professor Jamie D. Phillips, Chair Professor Pallab K. Bhattacharya Professor Fred L. Terry, Jr. Assistant Professor Kevin P. Pipe c Anne M. Itsuno 2012 All Rights Reserved To my parents. ii ACKNOWLEDGEMENTS First and foremost, I would like to thank my research advisor, Professor Jamie Phillips, for all of his guidance, support, and mentorship throughout my career as a graduate student at the University of Michigan. I am very fortunate to have had the opportunity to work alongside him. I sincerely appreciate all of the time he has taken to meet with me to discuss and review my research work. He is always very thoughtful and respectful of his students, treating us as peers and valuing our opinions. Professor Phillips has been a wonderful inspiration to me. I have learned so much from him, and I believe he truly exemplifies the highest standard of teacher and technical leader. I would also like to acknowledge the past and present members of the Phillips Research Group for their help, useful discussions, and camaraderie. In particular, I would like to thank Dr. Emine Cagin for her constant encouragement and humor. Emine has been a wonderful role model. I truly admire her expertise, her accom- plishments, and her unfailing optimism and can only hope to follow in her footsteps. I would also like to thank Dr. -
Experimental Stability of Tellurium and Its Implications for the Venusian Radar Anomalies
44th Lunar and Planetary Science Conference (2013) 2951.pdf EXPERIMENTAL STABILITY OF TELLURIUM AND ITS IMPLICATIONS FOR THE VENUSIAN RADAR ANOMALIES. E. Kohler1, V. Chevrier1, P. Gavin1, N. Johnson2. 1Arkansas Center for Space and Plane- tary Sciences, University of Arkansas, Fayetteville, AR, 72701; 2National Aeronautics and Space Administration (NASA) Goddard Space Flight Center, Greenbelt, MD, 20771. [email protected] Introduction: Evidence of radar anomalies on Ve- portant aspect of determining the source, thus, it was nus has sparked debate about potential atmospheric chosen for this experiment. One gram of each were interactions with the surface. These high reflectivity heated to average Venusian surface conditions, and (low emissivity) anomalies have been found on the then to highland conditions (460°C and 90 bar, 380°C Venusian surface between altitudes of 2.5-4.75km and 55 bar respectively). The latter conditions are the using radar mapping [1-5]. There have been several anticipated temperature and pressure at the anomalies theoretical studies on the source of these anomalies altitude. After each run, the samples were weighed to including increased surface roughness, materials with determine stability and/or reactivity. Each compound higher dielectric constants or surface-atmospheric in- was also tested in a Lindberg tube oven at the Univer- teractions [1, 6]. Additionally, the literature suggests sity of Arkansas and heated to both 460°C and 380°C several possibilities of metal compound frosts or low at ambient pressure. The oven experiment isolated the lying clouds/fog. Evidence from Venera 13 and 14 effects of temperature. The samples were then ana- indicates a low layer cloud deck at an altitude of 1- lyzed using X-Ray Diffraction (XRD) and Scanning 2km that could consist of tellurium, bismuth, or lead Electron Microscope (SEM). -
Cd,-,Zn,Te Materials
Source of Acquisition NASA Goddard Space Flight Center Temperature Evolution of Excitonic Absorptions in Cd,-,Zn,Te Materials Manuel A. Quijada and Ross Henry Goddard Space Flight Center, Code 551, Greenbelt, MD 20771, USA ABSTRACT The studies consist of measuring the frequency dependent transmittance (T) and reflectance (R) above and below the optical band-gap in the W/Visible and infrared frequency ranges for Cdl-,Zn,Te materials for x=O and XI-0.04. Measurements were also done in the temperature range from 5 to 300 K. The results show that the optical gap near 1.49 eV at 300 K increases to 1.62 eV at 5 K. Finally, we observe sharp absorption peaks near this gap energy at low temperatures. The close proximity of these peaks to the optical transition threshold suggests that they originate from the creation of bound electron-hole pairs or excitons. The decay of these excitonic absorptions may contribute to a photoluminescence and transient background response of these back-illuminated HgCdTe CCD detectors. Keywords: Keywords: CdZnTe, UV/Vis infrared, transmittance, reflectance, semiconducting gap, photolumi- nescence, exciton 1. INTRODUCTION The ternary compound Cdl-,Zn,Te (CdZnTe) is a semiconducting alloy that is widely used as a base material for x-ray and infrared detectors. In particular, single crystals of CdZnTe wafers are the principal material on which HgCdTe epitaxial layers have been recently grown for the fabrication of infrared sensors on lattice matched CdZnTe substrate.l This has been possible due to recent advances through use of new detector growth technologies2 which involve p/n double layer planar heterostructure arrays grown by Molecular Beam Epitaxy (MBE). -
Molecular Beam Epitaxy of Cdxhg12xte
12 Molecular Beam Epitaxy of CdxHg12xTe Yu.G. Sidorov1, A.P. Anciferov1, V.S. Varavin1, S.A. Dvoretsky1, N.N. Mikhailov1, M.V. Yakushev1, I.V. Sabinina1, V.G. Remesnik1, D.G. Ikusov1, I.N. Uzhakov1, G.Yu. Sidorov1, V.D. Kuzmin1, S.V. Rihlicky1, V.A. Shvets1, A.S. Mardezov1, E.V. Spesivcev1, A.K. Gutakovskii1, A.V. Latyshev1,2 1 RZHANOV INSTITUTE OF SEMICONDUCTOR PHYSICS OF THE SIBERIAN BRANCHOF THE RUSSIAN ACADEMY OF SCIENCES, NOVOSIBIRSK, RUSSIA 2 NOVOSIBIRSK STATE UNIVERSITY, NOVOSIBIRSK, RUSSIA Infrared imaging systems are required for applications in medicine, agriculture, the chemical industry, ferrous and nonferrous metals metallurgy, the fuel industry, and other areas of the economy. Due to high quantum efficiency, tunable absorption wavelength, and a wide oper- ating temperature range, HgCdTe (mercury cadmium telluride, MCT)-based infrared focal plane arrays are a good choice for the fabrication of high-performance infrared imaging sys- tems. Creating arrays and matrices of photodetectors with a large number of elements imposes stringent requirements for narrow-band MCT. What is wanted is a large area plate MCT with highly uniform properties and low cost. MCT technology over the past 20 years has evolved from the production of relatively small (diameter ,10 mm) volume bars to large (up to 150 mm in diameter) epitaxial layers on alternative substrates. The electrical properties of solid solutions MCT are largely deter- mined by the intrinsic point defects and residual impurities associated with the growing method. MCT is characterized by a high rate of diffusion of point defects. Therefore, a low growth temperature is need.