Electro Fuels
Total Page:16
File Type:pdf, Size:1020Kb
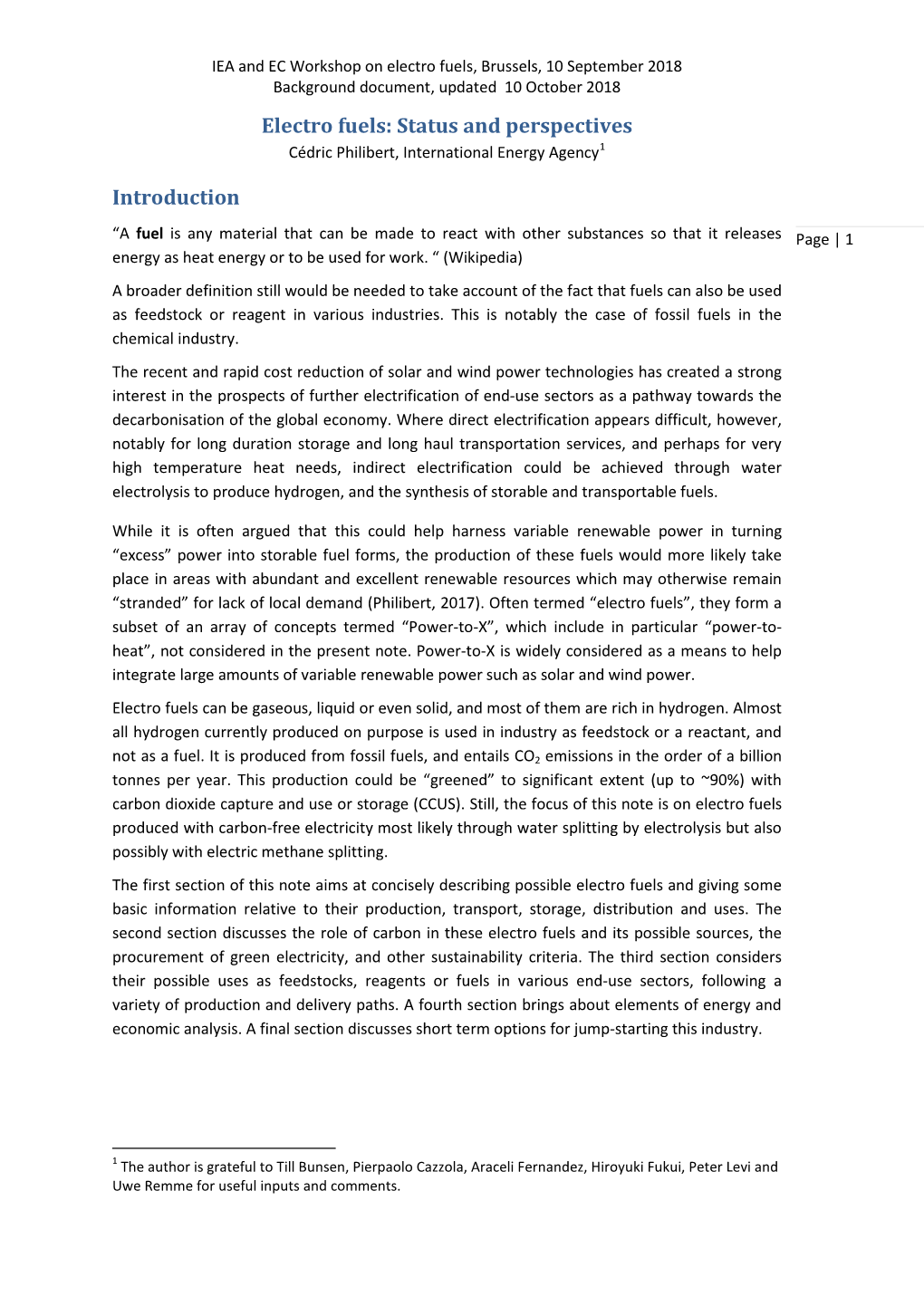
Load more
Recommended publications
-
A Comparative Study on the Prospects of Sustainable Aviation Fuels in Sweden
A comparative study on the prospects of sustainable aviation fuels in Sweden Daniel Katebi Olle Hoffman Carlsson Kandidatexamensarbete KTH – Skolan för Industriell Teknik och Management Energiteknik EGI-2020) Bachelor of Science Thesis KTH School of Industrial Engineering and Management Energy Technology EGI-2020 TRITA-ITM-EX 2020:220 SE-100 44 STOCKHOLM Bachelor of Science Thesis EGI-2020 TRITA-ITM-EX 2020:220 Approved Examiner Supervisor Dilip Khatiwada Dilip Khatiwada Commissioner Contact person -2- Sammanfattning Flygplansindustrin behöver röra sig mot en mer hållbar framtid för att nå Europeiska Unionens klimatmål (att nå en klimatneutral ekonomi senast 2050), och under de senaste åren har intresset för hållbara flygplansbränslen ökat markant. I denna rapport sammanställde och jämförde vi olika produktionsvägar och råmaterial utifrån ekonomiskt-, tekniskt- och klimatperspektiv för långsiktig implementation. En litteraturstudie utfördes för att samla information om hållbara flygplansbränslen. Det finns ett flertal sätt att producera hållbara flygplansbränslen och denna rapport jämför tre olika produktionsvägar: Hydroprocessed Esters and Fatty Acids (HEFA), hydrotermisk förvätskning (HTL) och elektrobränslen. Av dessa har enbart HEFA godkänts för användning som flygbränsle (april 2020). Rapporten jämförde även tre olika råmaterial: biomassa från skogen, matlagningsolja samt matavfall ur ett svenskt perspektiv. Jämförelsen utfördes med en Pugh-matris som var baserad på: minskning i växthusgasutsläpp, teknisk mognadsgrad (hur långt i utvecklingen har produktionsväggen kommit), kostnaden för bränslet, effektivitet och potentiell bränslemängd (hur stor del av svenska jetbränslekonsumtionen kan vardera produktionsväg täcka). För att sätta jämförelsen i ett långsiktigt perspektiv vägdes jämförelseparameterna till: potentiell bränslemängd - 30%, minskning i växthusgasutsläpp - 30%, pris – 20%, avkastning – 10% och bränslet mognadsgrad – 10% av total 100 poäng. -
Capture and Reuse of Carbon Dioxide (CO2) for a Plastics Circular Economy: a Review
processes Review Capture and Reuse of Carbon Dioxide (CO2) for a Plastics Circular Economy: A Review Laura Pires da Mata Costa 1 ,Débora Micheline Vaz de Miranda 1, Ana Carolina Couto de Oliveira 2, Luiz Falcon 3, Marina Stella Silva Pimenta 3, Ivan Guilherme Bessa 3,Sílvio Juarez Wouters 3,Márcio Henrique S. Andrade 3 and José Carlos Pinto 1,* 1 Programa de Engenharia Química/COPPE, Universidade Federal do Rio de Janeiro, Cidade Universitária, CP 68502, Rio de Janeiro 21941-972, Brazil; [email protected] (L.P.d.M.C.); [email protected] (D.M.V.d.M.) 2 Escola de Química, Universidade Federal do Rio de Janeiro, Cidade Universitária, CP 68525, Rio de Janeiro 21941-598, Brazil; [email protected] 3 Braskem S.A., Rua Marumbi, 1400, Campos Elíseos, Duque de Caxias 25221-000, Brazil; [email protected] (L.F.); [email protected] (M.S.S.P.); [email protected] (I.G.B.); [email protected] (S.J.W.); [email protected] (M.H.S.A.) * Correspondence: [email protected]; Tel.: +55-21-3938-8709 Abstract: Plastic production has been increasing at enormous rates. Particularly, the socioenvi- ronmental problems resulting from the linear economy model have been widely discussed, espe- cially regarding plastic pieces intended for single use and disposed improperly in the environment. Nonetheless, greenhouse gas emissions caused by inappropriate disposal or recycling and by the Citation: Pires da Mata Costa, L.; many production stages have not been discussed thoroughly. Regarding the manufacturing pro- Micheline Vaz de Miranda, D.; Couto cesses, carbon dioxide is produced mainly through heating of process streams and intrinsic chemical de Oliveira, A.C.; Falcon, L.; Stella transformations, explaining why first-generation petrochemical industries are among the top five Silva Pimenta, M.; Guilherme Bessa, most greenhouse gas (GHG)-polluting businesses. -
Implementation of Electrofuel Production at a Biogas Plant Case Study at Borås Energi & Miljö Master’S Thesis Within the Sustainable Energy Systems Programme
Biogas Digester Rawgas Gas upgrade Gas CO2 Biogas Organic waste Sabatier reactor Implementation of electrofuel production at a biogas plant Case study at Borås Energi & Miljö Master’s Thesis within the Sustainable Energy Systems programme TOBIAS JOHANNESSON Department of Energy and Environment Division of Physical Resource Theory Chalmers University of Technology Göteborg, Sweden 2016 FRT 2016:03 master’s thesis Implementation of electrofuel production at a biogas plant Case study at Borås Energi & Miljö Master’s Thesis within the Sustainable Energy Systems programme tobias johannesson supervisors: Stavros Papadokonstantakis & Camilla Ölander Examiner Maria Grahn Department of Energy and Environment Division of Physical Resource Theory chalmers university of technology Göteborg, Sweden 2016 Implementation of electrofuel production at a biogas plant Case study at Borås Energi & Miljö Master’s Thesis within the Sustainable Energy Systems programme TOBIAS JOHANNESSON FRT 2016:03 © TOBIAS JOHANNESSON, 2016 Department of Energy and Environment Division of Physical Resource Theory Chalmers University of Technology SE-412 96 Göteborg Sweden Telephone: + 46 (0)31-772 10 00 Cover: Schematic picture over a simplified biogas process with an implemented Sabatier reactor. Chalmers Reproservice Göteborg, Sweden 2016 Implementation of electrofuel production at a biogas plant Case study at Borås Energi & Miljö Master’s Thesis within the Sustainable Energy Systems programme TOBIAS JOHANNESSON Department of Energy and Environment Division of Physical Resource Theory Chalmers University of Technology Abstract One way to decrease the emissions of greenhouse gases is to use a renewable vehicle fuel, such as biogas. By separating methane from carbon dioxide in raw gas in a gas upgrading system, biogas is produced. -
Biofuels, Electrofuels, Electric Or Carbon-Free?: a Review of Current
1Biofuels, Electrofuels, Electric or Carbon-free?: A review of current and emerging Sustainable 2Energy Sourcing for Aviation (SESA) 3Pimchanok Su-ungkavatin1*, Ligia Barna1, Lorie Hamelin1 41 Toulouse Biotechnology Institute (TBI), INSA, INRAE UMR792, and CNRS UMR5504, Federal University of Toulouse, 135 5Avenue de Rangueil, F-31077, Toulouse, France 6* Corresponding author e-mail address: [email protected] 7Abstract 8Climate neutrality is becoming a core long-term competitiveness factor within the aviation industry, as demonstrated 9by the several innovations and targets set within that sector, prior to and especially after the COVID-19 crisis. 10Ambitious timelines are set, involving important investment decisions to be taken in a 5-years horizon time. Here, 11we provide an in-depth review of alternative energy sourcing technologies for aviation revealed to date, which we 12classified into three main categories, namely liquid fuels (biofuels, electrofuels), electric aviation (all electric and 13hybrid), and carbon-free options (hydrogen-based, solar-powered). For liquid fuels, 10 pathways were reviewed, for 14which we supply the detailed process flow picturing all input, output, and co-products generated. The market uptake 15and use of these co-products were also investigated, along with the overall international regulations and targets for 16future aviation. As most of the inventoried pathways require hydrogen, we further reviewed six existing and 17emerging carbon-free hydrogen production technologies. Our review also details the five key battery technologies 18available (lithium-ion, advanced lithium-ion, solid-state battery, lithium-sulfur, lithium-air) for aviation, as well as 19the possible configuration schemes for electric propulsion (parallel electric hybrid, series electric hybrid, all electric, 20partial turboelectric and full turboelectric) and reflects upon the inclusion of hydrogen-powered fuel cells with these 21configurations. -
The Role of E-Fuels in the Transport System in Europe (2030–2050) (Literature Review)
A look into the role of e-fuels in the transport system in Europe (2030–2050) (literature review) Introduction As part of Concawe’s Low Carbon Pathways project, this In December 2015, Parties to the United Nations Framework Convention on Climate Change convened article presents a literature in Paris for the 21st Conference of Parties (COP21). The conference was an important step towards review on e-fuels, which aims to addressing the risks posed by climate change through an agreement to keep the global temperature build a better understanding of increase ‘well below 2°C above pre-industrial levels’ and drive efforts to limit it to 1.5°C above pre- e-fuel production technologies industrial levels. To achieve these goals, the European Union (EU) is exploring different mid-century and implications in terms of scenarios leading to a low-carbon EU economy by 2050. efficiency, greenhouse gas reduction, technology readiness level, environmental impact, In line with the EU’s low-emissions strategy, Concawe’s cross-sectoral Low Carbon Pathways (LCP) investment, costs and potential programme is exploring opportunities and challenges presented by different low-carbon technologies to demand. It is a summary of the achieve a significant reduction in carbon dioxide (CO2) emissions associated with both the manufacture exhaustive literature review and use of refined products in Europe over the medium (2030) and longer term (2050). which is due to be published by the end of 2019. In the scenarios considered by the Commission (P2X, COMBO, 1.5 TECH and 1.5 LIFE) e-fuels are presented as a potential cost-effective technology that could be used to achieve the objectives of the Paris Agreement, i.e. -
AD-MARTEM-OFFICIAL-2.Pdf
Odysseus II Space Contest The TEAM INTERSTELLAR Giulia Bassani & Nicola Timpano Liceo M. Curie Collegno Italy presents… Odysseus II Space Contest AD MARTEM “How to build an autonomous space station on Mars?” Odysseus II Space Contest EARTH MARS 23.44° YEAR 25,19° 365 days 686 days(667 sols) GRAVITY 9.81 m/s² 3.71 m/s² SOLAR LIGHT 24 h 40 m 1.37*10³ W/m² 6.1*10² W/m² 24 h ATMOSPHERE 1013 mbar 7.6 mbar 0.039% CO2 95% 78% N2 2.6% 0.4% H2O 0.03% 0.93% Ar 1.6% 20.9% O2 0.13% Odysseus II Space Contest Odysseus II Space Contest Geodesic Dome Semi-spherical structure made up of a network of beams lying on great circles (geodesics). It becomes proportionally more resistant with increasing size. In the picture→ Artistic view of our base made by us with 3D Studio Max. Resistant against the strong Martian sand-storms. This shape avoids the accumulation of sand and other debris on its surface. Odysseus II Space Contest Materials Multilayered-walls are built with regolith and water (obtained from the permafrost) using a 3D printer. If water freezes, the protection against the cosmic rays is improved. The Ad Martem Program Mission 1 – Cargo •Robotic 3D Printer •Nuclear reactor •Inflatable module Mission 2 – Setup Short human mission •Life Support System •Water and food •Rovers Mission 3 – Stay Human mission Odysseus II Space Contest The Main Base Made with Geogebra Odysseus II Space Contest Made with Geogebra The Main Base Odysseus II Space Contest No windows! Because they would let in the radiations. -
Volume 64, Issue 3, July 2020 Published by Johnson Matthey © Copyright 2020 Johnson Matthey
ISSN 2056-5135 Johnson Matthey’s international journal of research exploring science and technology in industrial applications Volume 64, Issue 3, July 2020 Published by Johnson Matthey www.technology.matthey.com © Copyright 2020 Johnson Matthey Johnson Matthey Technology Review is published by Johnson Matthey Plc. This work is licensed under a Creative Commons Attribution-NonCommercial-NoDerivatives 4.0 International License. You may share, copy and redistribute the material in any medium or format for any lawful purpose. You must give appropriate credit to the author and publisher. You may not use the material for commercial purposes without prior permission. You may not distribute modifi ed material without prior permission. The rights of users under exceptions and limitations, such as fair use and fair dealing, are not aff ected by the CC licenses. www.technology.matthey.com www.technology.matthey.com Johnson Matthey’s international journal of research exploring science and technology in industrial applications Contents Volume 64, Issue 3, July 2020 234 Guest Editorial: Johnson Matthey Technology Review Special Edition on Clean Mobility By Andy Walker 236 Powering the Future through Hydrogen and Polymer Electrolyte Membrane Fuel Cells By Bo Ki Hong, Sae Hoon Kim and Chi Myung Kim 252 Exploring the Impact of Policy on Road Transport in 2050 By Huw Davies 263 Sustainable Aviation Fuels By Ausilio Bauen, Niccolò Bitossi, Lizzie German, Anisha Harris and Khangzhen Leow 279 Hydrogen Fuel Cell Vehicle Drivers and Future Station Planning By Scott Kelley, Michael Kuby, Oscar Lopez Jaramillo, Rhian Stotts, Aimee Krafft and Darren Ruddell 287 Battery Materials Technology Trends and Market Drivers for Automotive Applications By Sarah Ball, Joanna Clark and James Cookson 298 Adaptable Reactors for Resource- and Energy-Efficient Methane Valorisation (ADREM) By Emmanouela Korkakaki, Stéphane Walspurger, Koos Overwater, Hakan Nigar, Ignacio Julian, Georgios D. -
Assessing the Sustainability Implications of Alternative Aviation Fuels
WORKING PAPER 2021-11 © 2021 INTERNATIONAL COUNCIL ON CLEAN TRANSPORTATION MARCH 2021 Fueling flight: Assessing the sustainability implications of alternative aviation fuels Authors: Nikita Pavlenko, Stephanie Searle Keywords: Aviation, biofuels, low-carbon fuels Aviation faces large technical barriers to making a transition to hydrogen or electricity- powered airframes, so the industry will probably have to rely on liquid fuels through 2050. That is particularly true for the medium- and long-haul flights that generate two- thirds of aviation emissions. If the industry is to meet its long-term climate goal of cutting greenhouse gas (GHG) emissions 50% by 2050 without curbing traffic growth or using out-of-sector carbon offsets, sustainable aviation fuels (SAFs) will need to play a key role. SAFs can be used to generate in-sector GHG reductions when they supplant conventional petroleum jet fuel. In 2018, less than 0.01% of aviation fuel came from alternative sources (Hupe, 2019; Graver, Zhang, & Rutherford, 2019). While reducing petroleum consumption in aviation is an important objective for decarbonization, the specific types of alternative fuels used to displace petroleum will determine the net climate impact of any alternative fuels policy. A fuel’s feedstock and its conversion process—together called the fuel pathway—determine the fuel’s life-cycle GHG emissions. The European Union’s recently announced Green New Deal framework calls for a clear regulatory roadmap for the decarbonization of aviation, to be achieved using a combination of new technology, SAFs, modal shift, and improved efficiency (European Parliament, 2020). As part of this effort, the European Commission announced the ReFuelEU initiative to deploy SAFs to decarbonize EU aviation (European Commission, n.d.). -
Power to Gas – Bridging Renewable Electricity to the Transport Sector
POWER TO GAS – BRIDGING RENEWABLE ELECTRICITY TO THE TRANSPORT SECTOR Abstract Globally, transport accounts for a significant part of the total energy utilization and is heavily dominated by fossil fuels. The main challenge is how the greenhouse gas emissions in road transport can be addressed. Moreover, the use of fossil fuels in road transport makes most countries or regions dependent on those with oil and/or gas assets. With that said, the question arises of what can be done to reduce the levels of greenhouse gas emissions and furthermore reduce dependency on oil? One angle is to study what source of energy is used. Biomass is considered to be an important energy contributor in future transport and has been a reliable energy source for a long time. However, it is commonly known that biomass alone cannot sustain the energy needs in the transport sector by far. This work presents an alternative where renewable electricity could play a significant role in road transport within a relatively short time period. Today the amount of electricity used in road transport is negligible but has a potential to contribute substantially. It is suggested that the electricity should be stored, or “packaged” in a chemical manner, as a way of conserving the electrical energy. One way of doing so is to chemically synthesize fuels. It has been investigated how a fossil free transport system could be designed, to reach high levels of self- sufficiency. According to the studies, renewable electricity could have the single most important role in such a system. Among the synthetic fuels, synthetic methane (also called synthetic biogas) is the main focus of the thesis. -
Extracellular Electron Transfer from Cathode to Microbes: Application for Biofuel Production Okkyoung Choi and Byoung‑In Sang*
Choi and Sang Biotechnol Biofuels (2016) 9:11 DOI 10.1186/s13068-016-0426-0 Biotechnology for Biofuels REVIEW Open Access Extracellular electron transfer from cathode to microbes: application for biofuel production Okkyoung Choi and Byoung‑In Sang* Abstract Extracellular electron transfer in microorganisms has been applied for bioelectrochemical synthesis utilizing microbes to catalyze anodic and/or cathodic biochemical reactions. Anodic reactions (electron transfer from microbe to anode) are used for current production and cathodic reactions (electron transfer from cathode to microbe) have recently been applied for current consumption for valuable biochemical production. The extensively studied exoelectro‑ genic bacteria Shewanella and Geobacter showed that both directions for electron transfer would be possible. It was proposed that gram-positive bacteria, in the absence of cytochrome C, would accept electrons using a cascade of membrane-bound complexes such as membrane-bound Fe-S proteins, oxidoreductase, and periplasmic enzymes. Modification of the cathode with the addition of positive charged species such as chitosan or with an increase of the interfacial area using a porous three-dimensional scaffold electrode led to increased current consumption. The extracellular electron transfer from the cathode to the microbe could catalyze various bioelectrochemical reductions. Electrofermentation used electrons from the cathode as reducing power to produce more reduced compounds such as alcohols than acids, shifting the metabolic pathway. Electrofuel could be generated through artificial photosynthe‑ sis using electrical energy instead of solar energy in the process of carbon fixation. Keywords: Bioelectrochemical synthesis, Extracellular electron transfer, Cathodic electron, Electrofuel Background and/or cathodic reactions. BES has two categories An eventual replacement of fossil energy source with according to the direction of electron flow, microbial fuel sustainable energy system is unavoidable. -
State of NASA Oxygen Recovery
48th International Conference on Environmental Systems ICES-2018-48 8-12 July 2018, Albuquerque, New Mexico State of NASA Oxygen Recovery Zachary W. Greenwood1, Morgan B. Abney2, Brittany R. Brown3, Eric T. Fox4, and Christine Stanley5 NASA, George C. Marshall Space Flight Center, Huntsville, Alabama, 35812, USA Life support is a critical function of any crewed space vehicle or habitat. One of the key elements of the life support system is the provision of oxygen to the crew. For missions close to Earth, oxygen may be resupplied from the ground, but as we look at exploring further out into the solar system for longer periods of time oxygen recovery from metabolic carbon dioxide (CO2) becomes a priority to minimize resupply requirements and enable feasible mission architectures. For more than half a century NASA has pursued the development of technology to enable oxygen recovery from metabolic CO2. Development work has included Bosch, Sabatier, and CO2 electrolysis systems and more recently plasma reactors, ionic liquids, and other exotic processes. NASA’s historical oxygen recovery work as well as the current state of oxygen recovery work currently going on within the agency is presented and discussed. Nomenclature IL = Ionic Liquid AR = Atmosphere Revitalization ISS = International Space Station C2H2 = Acetylene MSFC = Marshall Space Flight Center C2H4 = Ethylene OGA = Oxygen Generation Assembly C2H6 = Ethane PPA = Plasma Pyrolysis Assembly C = Carbon PSI = Pounds per Square Inch CM = Crew Member PSIG = Pounds per Square Inch Gauge CDRA = Carbon Dioxide Removal Assembly RGA = Residual Gas Analyzer CFR = Carbon Formation Reactor RTV = Room Temperature Vulcanizing CH4 = Methane RWGS = Reverse Water-Gas Shift CORTS = Carbon Dioxide Reduction Test Stand SBIR = Small Business Innovation Research CRA = Carbon Dioxide Reduction Assembly SCOR = Spacecraft Oxygen Recovery ECLSS = Environmental Control and Life SDU = Sabatier Development Unit Support Systems SI = Sustainable Innovations, Inc. -
Fischer–Tropsch Synthesis As the Key for Decentralized Sustainable Kerosene Production †
energies Article Fischer–Tropsch Synthesis as the Key for Decentralized Sustainable Kerosene Production † Andreas Meurer * and Jürgen Kern Department of Energy Systems Analysis, Institute of Networked Energy Systems, German Aerospace Center (DLR), Curiestraße 4, 70563 Stuttgart, Germany; [email protected] * Correspondence: [email protected]; Tel.: +49-711-6862-8100 † This paper is an extended version of our conference paper from 15th SDEWES Conference, Cologne, Germany, 1–5 September 2020. Abstract: Synthetic fuels play an important role in the defossilization of future aviation transport. To reduce the ecological impact of remote airports due to the long-range transportation of kerosene, decentralized on-site production of synthetic paraffinic kerosene is applicable, preferably as a near- drop-in fuel or, alternatively, as a blend. One possible solution for such a production of synthetic kerosene is the power-to-liquid process. We describe the basic development of a simplified plant layout addressing the specific challenges of decentralized kerosene production that differs from most of the current approaches for infrastructural well-connected regions. The decisive influence of the Fischer–Tropsch synthesis on the power-to-liquid (PtL) process is shown by means of a steady-state reactor model, which was developed in Python and serves as a basis for the further development of a modular environment able to represent entire process chains. The reactor model is based on reaction kinetics according to the current literature. The effects of adjustments of the main operation parameters on the reactor behavior were evaluated, and the impacts on the up- and downstream Citation: Meurer, A.; Kern, J.