Low-Cost Open Source Ultrasound-Sensing Based 3 Navigational Support for Visually Impaired
Total Page:16
File Type:pdf, Size:1020Kb
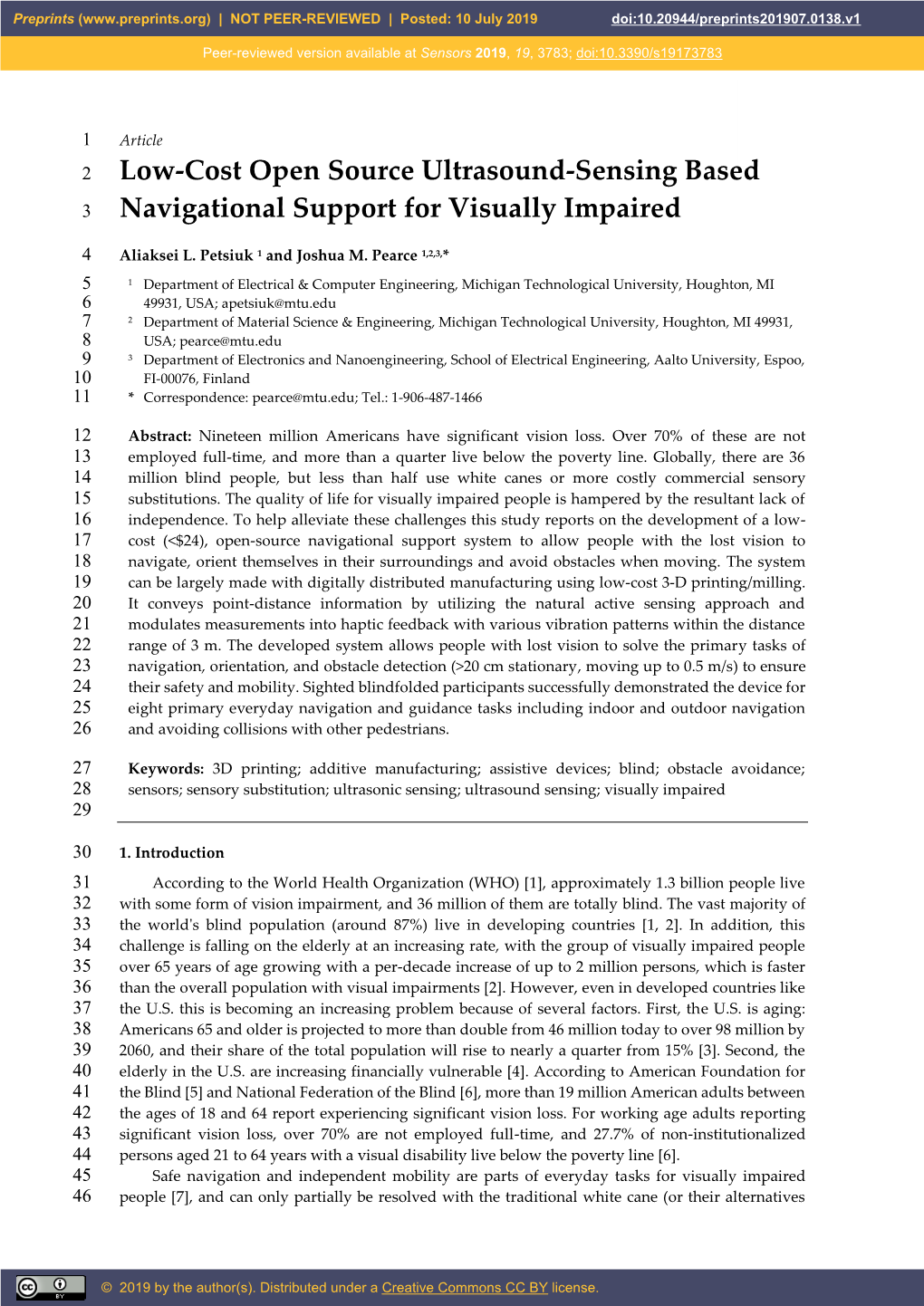
Load more
Recommended publications
-
The Effect of Contingent Music with Physical Therapy in Children Who Toe- Walk Penny Roberts
Florida State University Libraries Electronic Theses, Treatises and Dissertations The Graduate School 2002 The Effect of Contingent Music with Physical Therapy in Children Who Toe- Walk Penny Roberts Follow this and additional works at the FSU Digital Library. For more information, please contact [email protected] THE FLORIDA STATE UNIVERSITY COLLEGE OF MUSIC THE EFFECT OF CONTINGENT MUSIC WITH PHYSICAL THERAPY IN CHILDREN WHO TOE-WALK By PENNY ROBERTS A Thesis submitted to the School of Music in partial fulfillment of the Requirements for the degree of Master of Music Degree Awarded: Fall Semester, 2002 The members of the Committee approve the thesis of Penny Roberts defended on November 8, 2002. ________________________ Jayne M. Standley Professor Directing Thesis ________________________ Clifford K. Madsen Committee Member ________________________ Diane Gregory Committee Member ACKNOWLEDGEMENTS I greatly appreciate Dr. Jayne Standley for her advice, patience, and gentle prodding during this experience. I sincerely thank the Physical Therapists who allowed me access to their patients, and patiently answered my many questions: E.A., V. C., M. M., S. M., & C. S. Thank you also to the facilities for your cooperation. Thank you to those friends who listened to thesis talk almost every day. You know who you are. Many thanks to Kate & Scott for their superior accommodations, computer assistance, and general support. I very much appreciate Claudine Boussicaut’s time. Most importantly, thank you to Zac, who now knows more about toe-walking and -
Enabling People with Visual Impairments to Navigate Virtual Reality with a Haptic and Auditory Cane Simulation Yuhang Zhao1, 2, Cynthia L
Enabling People with Visual Impairments to Navigate Virtual Reality with a Haptic and Auditory Cane Simulation Yuhang Zhao1, 2, Cynthia L. Bennett1, 3, Hrvoje Benko1, Edward Cutrell1, Christian Holz1, Meredith Ringel Morris1, Mike Sinclair1 1Microsoft Research, Redmond 2Information Science, Cornell 3Computer Science & Engineering, {benko, cutrell, cholz, merrie, Tech, Cornell University University of Washington sinclair}@microsoft.com [email protected] [email protected] Figure 1. (A) A blind user wearing the gear for our VR evaluation, including a VR headset and Canetroller, our haptic VR controller. (B) The mechanical elements of Canetroller. (C) Overlays of the virtual scene atop the real scene show how the virtual cane extends past the tip of the Canetroller device and can interact with the virtual trash bin. (D) The use of Canetroller to navigate a virtual street crossing: the inset shows the physical environment, while the rendered image shows the corresponding virtual scene. Note that users did not have any visual feedback when using our VR system. The renderings are shown here for clarity. ABSTRACT Author Keywords Traditional virtual reality (VR) mainly focuses on visual Virtual reality; white cane; blindness; visual impairments; feedback, which is not accessible for people with visual haptic feedback; auditory feedback; mobility. impairments. We created Canetroller, a haptic cane ACM Classification Keywords controller that simulates white cane interactions, enabling H.5.1. Information interfaces and presentation: Multimedia people -
Sensor-Based Assistive Devices for Visually-Impaired People: Current Status, Challenges, and Future Directions
Review Sensor-Based Assistive Devices for Visually-Impaired People: Current Status, Challenges, and Future Directions Wafa Elmannai and Khaled Elleithy * Department of Computer Science and Engineering, University of Bridgeport, Bridgeport, CT 06604, USA; [email protected] * Correspondence: [email protected]; Tel.: +1-203-576-4703 Academic Editor: Panicos Kyriacou Received: 23 January 2017; Accepted: 1 March 2017; Published: 10 March 2017 Abstract: The World Health Organization (WHO) reported that there are 285 million visually- impaired people worldwide. Among these individuals, there are 39 million who are totally blind. There have been several systems designed to support visually-impaired people and to improve the quality of their lives. Unfortunately, most of these systems are limited in their capabilities. In this paper, we present a comparative survey of the wearable and portable assistive devices for visually- impaired people in order to show the progress in assistive technology for this group of people. Thus, the contribution of this literature survey is to discuss in detail the most significant devices that are presented in the literature to assist this population and highlight the improvements, advantages, disadvantages, and accuracy. Our aim is to address and present most of the issues of these systems to pave the way for other researchers to design devices that ensure safety and independent mobility to visually-impaired people. Keywords: assistive devices; visually-impaired people; obstacles detection; navigation and orientation systems; obstacles avoidance 1. Introduction The World Health Organization (WHO) Fact reported that there are 285 million visually- impaired people worldwide. Among these individuals, there are 39 million who are blind in the world [1]. -
MUSCULOSKELETAL PHYSICAL THERAPY for SACROILIAC JOINT PAIN Anas Alhakami*1, Mohammed Qasheesh2, Senthilkumar Cennappan Bose3
International Journal of Physiotherapy and Research, Int J Physiother Res 2020, Vol 8(4):3533-36. ISSN 2321-1822 Case Report DOI: https://dx.doi.org/10.16965/ijpr.2020.144 MUSCULOSKELETAL PHYSICAL THERAPY FOR SACROILIAC JOINT PAIN Anas Alhakami*1, Mohammed Qasheesh2, Senthilkumar Cennappan Bose3. *1 Senior Musculoskeletal Physical Therapist, King Faisal Medical City for Southern Regions, Kingdom of Saudi Arabia. 2 Assistant Professor and Head-Physical Therapy, Jazan University,Kingdom of Saudi Arabia 3 Lecturer-Physical Therapy, Jazan University, Kingdom of Saudi Arabia. ABSTRACT This case report describes a clinical case of a 53 years aged male with Low Back Pain(LBP) at Sacro Iliac Joint(SIJ). Patient referred to physical therapy department with LBP over the past 3 weeks. Pain extended to posterior aspect of left thigh and worsening with prolonged standing, sitting and with stair climbing. Moreover, he found difficulty to ride his car or going from sit to stand. He had a history of road traffic accident 30 years ago that led to severe pain in his lower back area, he was a farmer as well and was working hardly more than 8 hours daily by lifting heavy objects. Patient came to the department by walking with assistive cane. By palpation, there was a local tenderness at the posterior aspect of the SIJ. Range of motion was limited by pain in lumbar flexion, extension, rotation and bilateral side bending movements. Pain scored 7 out of 10 on Numerical Pain Rating Visual Analogue Scale. Functional disability scored 19 out of 24 on Roland-Morris Disability questionnaire. -
Assistive Multi-Purpose Mobility Device with Folding Temporary Seat
Assistive Multi-Purpose Mobility Device with Folding Temporary Seat A Major Qualifying Project Proposal Submitted to the Faculty of WORCESTER POLYTECHNIC INSTITUTE in partial fulfillment of the requirements for the Degree of Bachelor of Science by _________________________ Xinping Deng _________________________ Daniel Haley _________________________ Taylor Roseen Date: 4/30/15 Approved: ______________________________ Professor Allen H. Hoffman, Co-Advisor ______________________________ Professor Holly K. Ault, Co-Advisor Abstract Crutches and canes are widely used around the world as a means of providing stability and support for those who need them; the elderly population in particular utilizes these devices the most. There are numerous products on the market that attempt to add a seat to the crutch or cane in an effort to alleviate the stress of standing for too long. However, these products are oftentimes too cumbersome, heavy, or just simply unsafe. The goal of this project is to design and build a device that can be used as either a crutch or a cane that gives stability and helps support the weight of the user while standing and walking, additionally offering the ability for the user to rest comfortably and safely in a seated position when necessary. A first generation prototype was successfully manufactured using an existing forearm crutch and machined aluminum and steel components. The prototype underwent load and dimension tests in addition to students conducting overall usability tests. i Table of Contents Abstract ......................................................................................................................................................... -
Electronic Smart Canes for Visually Impaired People
NATIONAL AND KAPODISTRIAN UNIVERSITY OF ATHENS SCHOOL OF SCIENCE DEPARTMENT OF INFORMATICS AND TELECOMMUNICATION BSc THESIS Electronic Smart Canes for Visually Impaired People Dimitra P. Marini Supervisor: Georgios Kouroupetroglou, Associate Professor ATHENS MARCH 2018 ΕΘΝΙΚΟ ΚΑΙ ΚΑΠΟΔΙΣΤΡΙΑΚΟ ΠΑΝΕΠΙΣΤΗΜΙΟ ΑΘΗΝΩΝ ΣΧΟΛΗ ΘΕΤΙΚΩΝ ΕΠΙΣΤΗΜΩΝ ΤΜΗΜΑ ΠΛΗΡΟΦΟΡΙΚΗΣ ΚΑΙ ΤΗΛΕΠΙΚΟΙΝΩΝΙΩΝ ΠΤΥΧΙΑΚΗ ΕΡΓΑΣΙΑ Έξυπνα Ηλεκτρονικά Μπαστούνια για Άτομα με Απώλεια Όρασης Δήμητρα Π. Μαρίνη Επιβλέπων: Γεώργιος Κουρουπέτρογλου, Αναπληρωτής Καθηγητής ΑΘΗΝΑ ΜΑΡΤΙΟΣ 2018 BSc THESIS Electronic Smart Canes for Visually Impaired People Dimitra P. Marini S.N.: 1115201100044 SUPERVISOR: Georgios Kouroupetroglou, Associate Professor ΠΤΥΧΙΑΚΗ ΕΡΓΑΣΙΑ Έξυπνα Ηλεκτρονικά Μπαστούνια για Άτομα με Απώλεια Όρασης Δήμητρα Π. Μαρίνη Α.Μ.: 1115201100044 ΕΠΙΒΛΕΠΩΝ: Γεώργιος Κουρουπέτρογλου, Αναπληρωτής Καθηγητής ABSTRACT The purpose of this paper is to present and describe existing devices and smart-stick technologies for blind and visually impaired people. This state-of-the-art review includes the most recent research results of international scientific literature (published in scientific journals, conferences, etc.), patents and commercially available products. These technologies are classified according to their basic characteristics and are then accompanied by of the research trials conducted (where reference is made to the respective sources) and their results. In order to achieve this goal, after an extensive search in the international scientific literature, the most important and most recent technologies of smart sticks were selected and the operating principle of each of them was briefly described. Subsequently, the devices were classified according to the technologies they use and their basic characteristics, along with the additional information on the relative user trials and their results. The positive and negative aspects of each device as well as whether it covers the needs and requirements of visually impaired people are easily distinguishable. -
Ph.D. Dissertation Template
A HIGHLY ACCURATE AND RELIABLE DATA FUSION FRAMEWORK FOR GUIDING THE VISUALLY IMPAIRED Wafa Elmannai Under the Supervision of Dr. Khaled Elleithy DISSERTATION SUBMITTED IN PARTIAL FULFILMENT OF THE REQUIREMENTS FOR THE DEGREE OF DOCTOR OF PHILOSOPHY IN COMPUTER SCIENCE AND ENGINEERING THE SCHOOL OF ENGINEERING University of Bridgeport CONNECTICUT May 2018 i A HIGHLY ACCURATE AND RELIABLE DATA FUSION FRAMEWORK FOR GUIDING THE VISUALLY IMPAIRED © Copyright by 2018 iii A HIGHLY ACCURATE AND RELIABLE DATA FUSION FRAMEWORK FOR GUIDING THE VISUALLY IMPAIRED ABSTRACT The world has approximately 285 million visually impaired (VI) people according to a report by the World Health Organization. Thirty-nine million people are estimated to be blind, whereas 246 million people are estimated to have impaired vision. An important factor that motivated this research is the fact that 90% of VI people live in developing countries. Several systems have been designed to improve the quality of the life of VI people and support the mobility of VI people. Unfortunately, none of these systems provides a complete solution for VI people, and the systems are very expensive. Therefore, this work presents an intelligent framework that includes several types of sensors embedded in a wearable device to support the visually impaired (VI) community. The proposed work is based on an integration of sensor-based and computer vision-based techniques in order to introduce an efficient and economical visual device. The designed algorithm is divided to two components: obstacle detection and collision avoidance. The system has been implemented and tested in real-time scenarios. A video dataset of 30 videos and an average of 700 frames per video was fed to the system for the testing purpose. -
A Flexible Object Orientated Design Approach for The
A FLEXIBLE OBJECT ORIENTATED DESIGN APPROACH FOR THE REALISATION OF ASSISTIVE TECHNOLOGY STEVEN BATTERSBY A thesis submitted in partial fulfilment of the Requirements of Nottingham Trent University For the degree of Doctor of Philosophy February 2013 This work is the intellectual property of the author. You may copy up to 5% of this work for private study, or personal, non-commercial research. Any re-use of the information contained within this document should be fully referenced, quoting the author, title, university, degree level and pagination. Queries or requests for any other use, or if a more substantial copy is required, should be directed in the owner(s) of the Intellectual Property Rights. Abstract This thesis contributes to a growing body of research conducted by the Interactive Systems Research Group (ISRG) at Nottingham Trent University within the fields of accessibility and accessible technologies. Core to this research is the exploration of how interactive technologies can be developed and applied as platforms for education, rehabilitation and social inclusion. To this end the group has been actively evolving the User Sensitive and Inclusive Design (USID) methodology for the design, development and evaluation of accessible software and related technologies. This thesis contributes to the further development of the USID method with a focus on its application for the design of assistive technology. Video Games are increasingly being recognised as an important resource for the development and improvement of the quality of life of those with a disability and/or impairment. Creating universally accessible games and related technologies is however no simple feat. Review of literature quickly highlights that the predominant barrier to the adoption of console gaming and also video gaming in general, by those with a disability or impairment, is that of the human-machine hardware interface. -
Standards Presentation to California Occupational Safety and Health Standards Board
STANDARDS PRESENTATION TO CALIFORNIA OCCUPATIONAL SAFETY AND HEALTH STANDARDS BOARD Petition to add new Title 8 Section related to Musculoskeletal Injury Prevention through the use of Ergonomic Disposable Large Capacity Poly Bags with Secondary Handle Application prepared by Mark Sale on June 1st 2017 Contact email [email protected] Ph. 808 557-7600 Table of Contents 1. Petition to add new Title 8 Section related to Musculoskeletal Injury Prevention through the use of Ergonomic Disposable Large Capacity Poly Bags with Secondary Handle. 2. Report following pilot study at Stanford Hospital and Clinics performed by Dr. Georgi Popov and economist Elyce Biddle Evaluation of Benefits of Litelift Ergonomic Bags. 3. Excerpt from Risk Assessment: A Practical Guide to Assessing Operational Risks, by Dr. Georgi Popov and Elyce Biddle. 4. Comparison of traditional bag vs. two-handled bags per NiOSH Lifting Guidelines. 5. Excerpts from case summaries taken from search results in www.dir. ca.gov for trashbag injuries (see also linen bag injuries, dumpster injury, recycle injury). 6. Ergonomic of Study of Custodial, Housekeeping and Environmental Service Positions at the University of California, May 2011. 7. Prevention through Design (PtD): Combining Risk Assessment, Productivity and Sustainability, Drs. Popov and Ney, University of Central Missouri. Continuing documentation; Automative Waste Collection - How to Make Sure It Makes Sense for Your Community, a related work resulting in the implementation of automated waste collection. 8. Bureau of Labor Statistics show janitors (those most likely tobe tasked with carrying trash bags) are at the highest risk of injury and days away from work. 9. CAL/OSHA DIR descriptions of "Safe Lifting and Carrying" 1. -
A Review of Intent Detection, Arbitration, and Communication
A Review of Intent Detection, Arbitration, and Communication Dylan P. Losey Aspects of Shared Control for Department of Mechanical Engineering, Rice University, Physical Human–Robot Houston, TX 77251 e-mail: [email protected] Interaction Craig G. McDonald Department of Mechanical Engineering, As robotic devices are applied to problems beyond traditional manufacturing and indus- Rice University, trial settings, we find that interaction between robots and humans, especially physical Houston, TX 77251 interaction, has become a fast developing field. Consider the application of robotics in e-mail: [email protected] healthcare, where we find telerobotic devices in the operating room facilitating dexterous surgical procedures, exoskeletons in the rehabilitation domain as walking aids and Edoardo Battaglia upper-limb movement assist devices, and even robotic limbs that are physically inte- Centro di Ricerca “E. Piaggio”, grated with amputees who seek to restore their independence and mobility. In each of University of Pisa, these scenarios, the physical coupling between human and robot, often termed physical Pisa 56126, Italy human robot interaction (pHRI), facilitates new human performance capabilities and cre- e-mail: [email protected] ates an opportunity to explore the sharing of task execution and control between humans and robots. In this review, we provide a unifying view of human and robot sharing task Marcia K. O’Malley execution in scenarios where collaboration and cooperation between the two entities are necessary, and where the physical coupling of human and robot is a vital aspect. We Professor define three key themes that emerge in these shared control scenarios, namely, intent Fellow ASME detection, arbitration, and feedback. -
Volume 3 Issue 10– October 2014
Volume 3 Issue 10– October 2014 Editorial Board American Journal of Engineering Research (AJER) Dr. Moinuddin Sarker, Qualification :PhD, MCIC, FICER, Dr. June II A. Kiblasan MInstP, MRSC (P), VP of R & D Qualification : Phd Affiliation : Head of Science / Technology Specialization: Management, applied Team, Corporate Officer (CO) sciences Natural State Research, Inc. 37 Brown House Road (2nd Floor) Country: PHIILIPPINES Stamford, CT-06902, USA. Dr. Jonathan Okeke Dr. Narendra Kumar Sharma Qualification: PHD Chimakonam Affiliation: Defence Institute of Physiology Qualification: PHD and Allied Science, DRDO Affiliation: University of Calabar Specialization: Proteomics, Molecular Specialization: Logic, Philosophy of biology, hypoxia Maths and African Science, Country: India Country: Nigeria Prof. Dr. Shafique Ahmed Arain Qualification: Postdoc fellow, Phd Dr. ABDUL KAREEM Affiliation: Shah abdul Latif University Qualification: MBBS, DMRD, FCIP, FAGE Khairpur (Mirs), Affiliation: UNIVERSITI SAINS Malaysia Specialization: Polymer science Country: Malaysia Country: Pakistan Dr. sukhmander singh Qualification: Phd Dr. Alcides Chaux Affiliation: Indian Institute Of Qualification: MD Technology, Delhi Affiliation: Norte University, Paraguay, Specialization : PLASMA PHYSICS South America Specialization: Genitourinary Tumors Country: India Country: Paraguay, South America Dr. Nwachukwu Eugene Nnamdi Dr. Md. Nazrul Islam Mondal Qualification: Phd Qualification: Phd Affiliation: Michael Okpara University of Affiliation: Rajshahi University, Agriculture, Umudike, Nigeria Bangladesh Specialization: Health and Epidemiology Specialization: Animal Genetics and Country: Bangladesh Breeding Country: Nigeria Volume-3 Issue-10 S.No. Manuscript Title Page No. A Review of the Fatigue Analysis of Heavy Duty Truck Frames 01. Ahmad O. Moaaz|| Nouby M. Ghazaly 01-06 COMING SOON!... (A New theory on "j-66 human") 02. M.Arulmani||V.R.Hema Latha 07-13 A JOURNEY TO "WHITE PLANET"?.. -
Permanent Disability Form
Accessibility Services Office Use Only Date Submitted:_________________________ Referred to:____________________________ Appointment Date:_______________________ Accessibility Services 3377 Bayview Avenue, Toronto, Ontario, M2M 3S4 Phone: 416-226-6620 Fax: 416-619-1203 Email: [email protected] DISABILITY ASSESSMENT DOCUMENTATION FORM Alternate format of this form is available by contacting the Accessibility Office Tyndale University College & Seminary is committed to creating an environment where students with disabilities are able to participate and integrate into its strong community. The Student Accessibility Office ensures students are provided appropriate and reasonable accommodations based on the functional limitations of their disability so they can have an equal access to their education while at Tyndale. The goal of the Student Accessibility Office is to provide students with disabilities a safe and comfortable environment where services are offered that respect their dignity and confidentiality while offering individualized accommodations so they can fully participate in their learning. This form will be used by Accessibility Services to verify a student has a disability, and/or to understand the impact of the disability and any resultant academic restrictions it places on the student. To receive support from Accessibility Services a student must “communicate his or her needs in sufficient detail and cooperate in consultations to enable the person responsible for accommodation to respond to the request.” (Ontario Human Rights Code (OHRC) Guidelines, 1994, p.17). The OHRC Guidelines (1994) also states that the University, as the body responsible for accommodating, must have sufficient information “to properly assess the impact of the disability on the specific academic task and know how to make the requested accommodation.” This form must be based on a current and thorough assessment from an appropriate registered practitioner who is qualified to diagnose the condition (e.g.