M.R.No: Dated: Sri/M/S. for Chief Admn Officer/Con/SC. F O R M 'A' 1. NAME OF
Total Page:16
File Type:pdf, Size:1020Kb
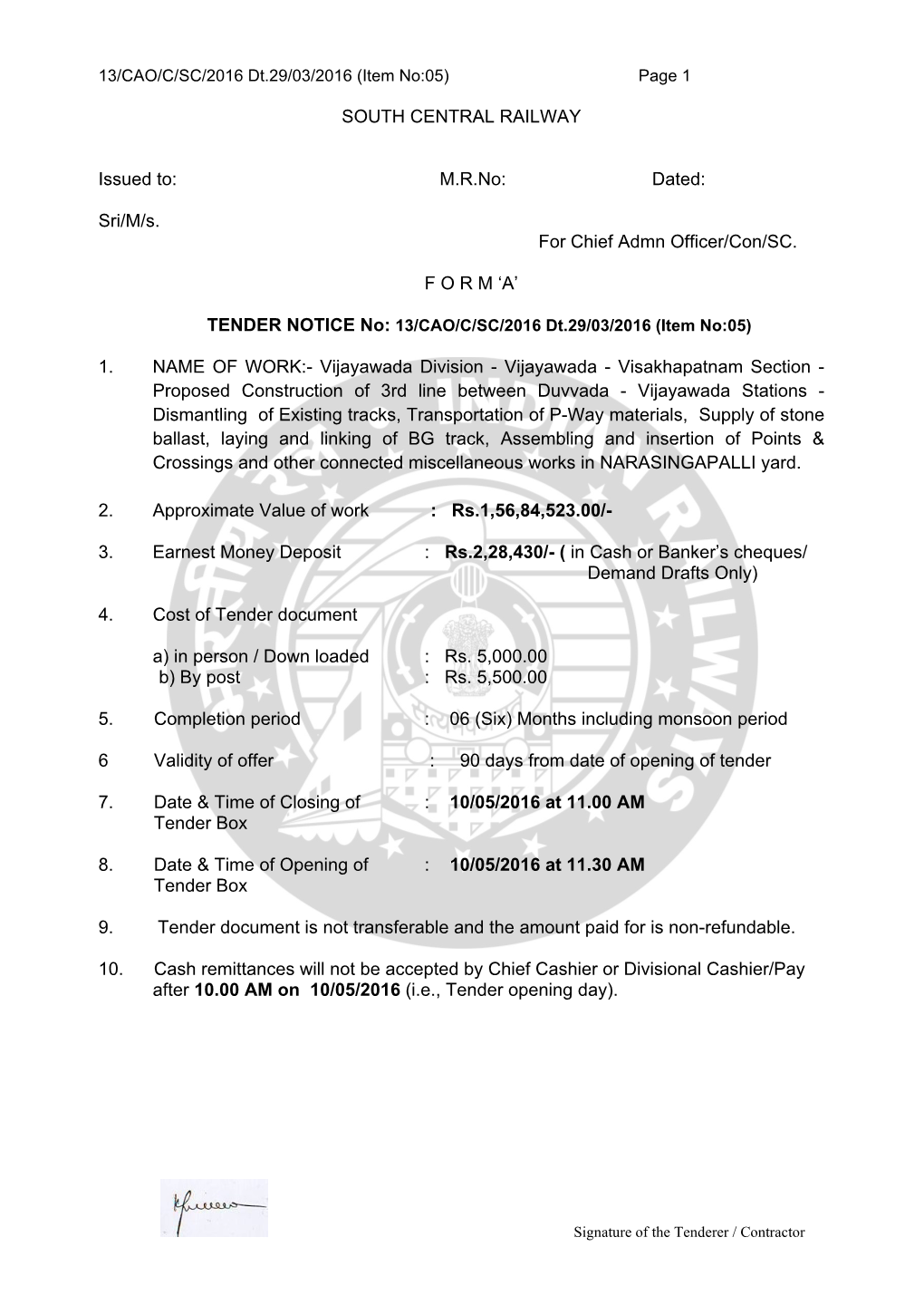
Load more
Recommended publications
-
LHA Recuritment Visakhapatnam Centre Screening Test Adhrapradesh Candidates at Mudasarlova Park Main Gate,Visakhapatnam.Contact No
LHA Recuritment Visakhapatnam centre Screening test Adhrapradesh Candidates at Mudasarlova Park main gate,Visakhapatnam.Contact No. 0891-2733140 Date No. Of Candidates S. Nos. 12/22/2014 1300 0001-1300 12/23/2014 1300 1301-2600 12/24/2014 1299 2601-3899 12/26/2014 1300 3900-5199 12/27/2014 1200 5200-6399 12/28/2014 1200 6400-7599 12/29/2014 1200 7600-8799 12/30/2014 1177 8800-9977 Total 9977 FROM CANDIDATES / EMPLOYMENT OFFICES GUNTUR REGISTRATION NO. CASTE GENDER CANDIDATE NAME FATHER/ S. No. Roll Nos ADDRESS D.O.B HUSBAND NAME PRIORITY & P.H V.VENKATA MUNEESWARA SUREPALLI P.O MALE RAO 1 1 S/O ERESWARA RAO BHATTIPROLU BC-B MANDALAM, GUNTUR 14.01.1985 SHAIK BAHSA D.NO.1-8-48 MALE 2 2 S/O HUSSIAN SANTHA BAZAR BC-B CHILAKURI PETA ,GUNTUR 8/18/1985 K.NAGARAJU D.NO.7-2-12/1 MALE 3 3 S/O VENKATESWARULU GANGANAMMAPETA BC-A TENALI. 4/21/1985 SHAIK AKBAR BASHA D.NO.15-5-1/5 MALE 4 4 S/O MAHABOOB SUBHANI PANASATHOTA BC-E NARASARAO PETA 8/30/1984 S.VENUGOPAL H.NO.2-34 MALE 5 5 S/O S.UMAMAHESWARA RAO PETERU P.O BC-B REPALLI MANDALAM 7/20/1984 B.N.SAIDULU PULIPADU MALE 6 6 S/O PUNNAIAH GURAJALA MANDLAM ,GUNTUR BC-A 6/11/1985 G.RAMESH BABU BHOGASWARA PET MALE 7 7 S/O SIVANJANEYULU BATTIPROLU MANDLAM, GUNTUR BC-A 8/15/1984 K.NAGARAJENDRA KUMAR PAMIDIMARRU POST MALE 8 8 S/O. -
Signature of the Tenderer / Contractor 13/CAO/C/SC/2016 Dt.29/03/2016 (Item No:03) Page 2
13/CAO/C/SC/2016 Dt.29/03/2016 (Item No:03) Page 1 SOUTH CENTRAL RAILWAY Issued to: M.R.No: Dated: Sri/M/s. For Chief Admn Officer/Con/SC. F O R M ‘A’ TENDER NOTICE No:13/CAO/C/SC/2016 Dt.29/03/2016 (Item No:03) 1. NAME OF WORK: VIJAYAWADA Division - Vijayawada - Visakhapatnam Section: Proposed Third Line with Electrification between DUVVADA - VIJAYAWADA stations: Earthwork in embankment including blanketting to GE- 0014 Specifications and extension of Minor bridges, Construction of Relay, Battery and Equipment room and other connected miscellaneous works at Narasingapalli yard. 2. Approximate Value of work : Rs. 3,65,29,006.48 3. Earnest Money Deposit : Rs. 3,32,650 /- ( in Cash or Banker’s cheques / Demand Drafts) 4. Cost of Tender document a) in person / Down loaded : Rs. 10,000.00 b) By post : Rs. 10,500.00 5. Completion period : 9 (Nine) Months including monsoon period 6 Validity of offer : 90 days from date of opening of tender 7. Date & Time of Closing of : 10/05/2016 at 11.00 AM Tender Box 8. Date & Time of Opening of : 10/05/2016 at 11.30 AM Tender Box 9. Tender document is not transferable and the amount paid for is non-refundable. 10. Cash remittances will not be accepted by Chief Cashier or Divisional Cashier / Pay after 10.00 AM on 10/05/2016 (i.e., Tender opening day). Signature of the Tenderer / Contractor 13/CAO/C/SC/2016 Dt.29/03/2016 (Item No:03) Page 2 NAME OF WORK: NAME OF WORK: VIJAYAWADA Division - Vijayawada - Visakhapatnam Section: Proposed Third Line with Electrification between DUVVADA - VIJAYAWADA stations: Earthwork in embankment including blanketting to GE- 0014 Specifications and extension of Minor bridges, Construction of Relay, Battery and Equipment room and other connected miscellaneous works at Narasingapalli yard. -
Incentives Releases Made As on 26.02.2018
Details of Transaction SlNo Beneficiary Name District Date of release Payment Amount Wolkem India Ltd SyNo 235 1 Butchayyapeta V Kasimkota M VSKP Visakhapatnam Pavala vaddi 313599 8/16/2017 Dist Nano Polymers India P Limited Plt No 2 424 Growth Centre Gundlapalli V Prakasam Power 402090 8/16/2017 Maddipadu M Prakasam Dist Dynamic Exports SyNo 102 Plt No A/1 3 Indl Estate Pernamitta SN Padu Prakasam Prakasam Power 86490 8/16/2017 Dist Sree Sai Venkateswara GranitesSyNo3- Ananthapuram 4 AChinnapalamada GPTadipatri Power 48390 8/16/2017 u MAnanthapuramu District Sree Jayadeep 5 GranitesSyNo263Chukkalur GpTadipatri Ananthapuramu Power 139170 8/16/2017 MAnanthapuram District M/s SRKGranites SyNo434 UKothapalli 6 Kurnool Pavala vaddi 67869 8/16/2017 V Dhone Mandal Kurnool District M/s AG Granites SyNo449/B 7 Kurnool Pavala vaddi 276351 8/16/2017 UKothapalli V Dhone M Kurnool District Thirumala Granites SyNo 77/1 8 Budawada V Chimakurthy M Prakasam Prakasam Power 840920 8/16/2017 Dist Manasvi Pharma Plot No219 & 220 9 Industrial Development Ara Thumukunta Ananthapuramu SD 55680 8/16/2017 Hindupur Mandal Anantapur District Manasvi Pharma Plot No219 & 220 10 Industrial Development area Thumukunta Ananthapuramu Land Cost 174000 8/16/2017 Hindupur Mandal Anantapur District SR Poly PacksSyno30-dRayalachervu v 11 Ananthapuramu Pavala vaddi 391930 8/16/2017 Yadiki mAnanthapuram Apple Polymers-1 SyNo 556/5m 12 Vavilathota Road Muthirevula M Chittoor Power 99560 8/16/2017 Chittoor Dist Alif GranitesSyno284-1Nakkaladdi 13 Ananthapuramu Power 39230 8/16/2017 -
Vizag Industrial Scan's
RNI Certificate No.69375/98 JulyPostal 16-31, Registered 2021 No.VSP-127/2020-2023 VIZAG INDUSTRIAL SCAN 1 VOLUME 24 ISSUE 06, PAGES: 12 July 16-31, 2021 www.viscan.in ANNUAL SUBSCRIPTION Rs.999/- Vizag Container Traffic up 10% RINL welcomes PLI Aditya Sabharwal bers in Q1FY22 by record- 34500 TEUs (aver- for Speciality Steel espite skyrocketing age) per month for Q1. container freight Similarly VCT also D VIS News Service scheme is a welcome step of Rs. 6322 crores, the rates coupled with the ad- witnessed the highest toward making India a truly scheme is expected to vent of the second wave ever number of rail he Union Cabinet, ‘Atmanirbhar Bharat’ as bring in investment of ap- container traffic at Vizag’s volumes and number chaired by the Prime T it will have multiple cascad- proximately Rs. 40,000 container terminal, of rakes handled in the Minister, Mr Narendra ing positive effect . It will crores and capacity addi- VCTPL witnessed an up- month of June ’21 i.e. Modi, recently approved not only promote production tion of 25 MT for special- ward swing. 71 Rakes with volumes the Production Linked In- of quality specialty steel for ity steel. The scheme will of over 10500 TEUs. centive (PLI) Scheme for The terminal in fact ing the highest EXIM import substitution for the specialty saw some impressive num- ‘Laden’ volumes of over Contd. on Page ..3 steel. The Incentives worth Rs.6,322 New Retail parks policy industry overall crores over 5 years wel- to spur growth: Valaven comed the scheme and said that end users but also provide give employment to about Vinita Chaudhary the Andhra Pradesh Gov- this would enhance the opportunity for the produc- 5,25,000 people of which ernment recently released imed to catalyse production quality of spe- ers to export finished prod- 68,000 will be direct em- the Retail Park Policy Agrowth, provide ciality steel while also help ucts for long term ployment. -
S.No District Student Name Course Institute Name Address Mobile Number Aadhar No D No 14-33-37/5,Rama Lakshmi Sri Sai Institute of Medical Colony,Maharanipeta,K.G.H
S.No District student Name Course Institute Name Address Mobile Number Aadhar No D No 14-33-37/5,Rama Lakshmi Sri Sai Institute of Medical Colony,Maharanipeta,K.G.H. Diploma in Radiographic Assistant Technology , Dilshuknagar , OPP,Visakhapatnam - 530002,Andhra 4288 Visakhapatnam Janjam Vijay Kumar (Two Years) Course Hyderabad Pradesh 8121827308 288806519855 C/o Beulah Institute of Health Sciences,Baji Junction,D No-2- Diploma in Medical Lab Technician Beulah Institute of Health Sciences, 121,Gopalapatnam,Visakhapatnam- 4289 Visakhapatnam Gude Pavani (Two Years) Course Gopalapatnam, Visakhapatnam 530027,Andhra Pradesh 6309737450 293569095348 D No 541/4 Sec-5, Lakshmiparvathi Modukuri Santhosh Diploma in Cath Lab Technician Andhra Medical College , Nagar,Visakhapatnam-530040,,Andhra 4290 Visakhapatnam Kranthi Kumar (Two Years) Course Visakhapatnam , Visakhapatnam Pradesh 7780790344 311463583293 Satya Venkata Lakshmi Diploma in Medical Lab Technician Andhra Medical College , D No 40-2-436, 4291 Visakhapatnam N (Two Years) Course Visakhapatnam , Visakhapatnam Kailasapuram,Visakhapatnam-530024 9542308737 330120955090 Diploma in Multipurpose Health H No-1-143,Gannela(V&P),Araku Assistant (Male) (Two Years) Lakshmi Prasanna Institute of Health Valley(M),Visakhapatnam-531149,Andhra 4292 Visakhapatnam Bariki Ramesh Kumar Course Sciences , Paderu , Visakhapatnam Pradesh 9492345022 334880573099 Diploma in Multipurpose Health Santhi MPHW(M) Training Institute, Assistant (Male) (Two Years) Narsipatnam, Visakhapatnam Dist. Kinaparthi(V&P),Koyyuru(M),Visakhapatn 4293 Visakhapatnam Surla Durgaprasad Course A.P am District-531084,Andhra Pradesh 9014737905 345793638509 D V L N Diploma in Multipurpose Health Mother Theresa MPHA (M) Training Murthy,Boyalakintada,Gavaravaram(Bo),D V L N Murthy Assistant (Male) (Two Years) Institute , Chodavaram , evarapalli(M),Visakhapatnam District- 4294 Visakhapatnam Dhanyamraju Course Visakhapatnam Dist, A.P. -
FORM 1 (FULLY MECHANISED OPENCAST COLOUR GRANITE QUARRY-4.965 Ha)
SRI ANGARA RAJESH SURVEY NO. 218 & 286, THOTAKURAPALEM VILLAGE, RAVIKAMATHAM MANDAL, VISAKHAPATNAM DISTRICT, ANDHRA PRADESH FORM 1 (FULLY MECHANISED OPENCAST COLOUR GRANITE QUARRY-4.965 ha) SUBMITTED BY STUDIES AND DOCUMENTATION BY Sri Angara Rajesh TEAM Labs and Consultants Flat No. 501, D. No. 7-18-5/16, (MoE&F O.M. - S. NO: 25, List A-1) Vinayghar Beach Apartment, B-115 to 117 & 509, Annapurna Block, Kirlampudi Layout, Chinna Waltair, Aditya Enclave, Ameerpet, Visakhapatnam – 530 017. Hyderabad-500 038 Mobile No. +91 98855 62539 Phone: 040-23748 555/616, Telefax: 040-23748666 Email: [email protected] SUBMITTED TO STATE LEVEL ENVIRONMENTAL IMPACT ASSESSMENT AUTHORITY, ANDHRA PRADESH GOVERNMENT OF INDIA Sri Angara Rajesh Form-1 APPENDIX I (See paragraph – 6) FORM 1 (I) Basic Information S. No Item Details 1 Name of the Project/s Sri Angara Rajesh – Colour Granite Quarry 2 S. No in the Schedule 1(a) 3 Proposed capacity/area/length/tonnage to be Fully mechanized opencast method for handled/command area/lease area/number of Colour granite maximum production of wells to be drilled 38538 m3/annum. Quarry lease area is 4.965 ha. 4 New/Expansion/Modernization New Quarry Cost estimated for the project Rs. 52 Lakhs 5 Existing Capacity/Area etc. -- 6 Category of Project i. e 'A' or 'B' B (Quarry Lease area is <5Ha) 7 Does it attract the general condition? If yes, No please specify 8 Does it attract the Specific condition? If yes, No. please specify. 9 Location Plot/Survey/Khasra No. Survey No. 218 & 286, Thotakurapalem Village Village, Ravikamatham Mandal, Tehsil Visakhapatnam District, Andhra Pradesh District State 10 Nearest railway station/airport along with Railway Station: Narasingapalli - 11.8 km - distance in kms. -
Assessment of the Need for Common Effluent Treatment Plants
Assessment of the Need for Common Effluent Treatment Plants Central Pollution Control Board (Ministry of Environment & Forests, Govt. of India) CONTENTS Page 1.0 Introduction 1 2.0 Methodology 2 3.0 Findings 4-20 Annexure I 21 Format for collection of basic information for the study Annexure II 22-84 List of industrial areas/estates ASSESSMENT OF THE NEED FOR COMMON EFFLUENT TREATMENT PLANTS 1. INTRODUCTION Small scale industrial units (SSIs) have a very important role in industrial development in the country. Government actively promotes growth of SSI units to induce a balanced economic growth and distribute the benefits of industrial development in an equitable manner. SSI units generally find it difficult to establish and operate individual effluent treatment plant due to their limited size and scale of operations. However, as SSI units are generally located as clusters in industrial areas/estates, the concept of Common Effluent Treatment Plant (CETP) for the entire effluent from the industrial area has been developed to achieve satisfactory treatment through their collective efforts. The monitoring and enforcement of a CETP as a single pollution source also become easier for regulatory agencies as compared to monitoring of large number of SSI units individually. Central Government has several financial support schemes to promote establishment of CETPs. Ministry of Environment, Forests & Climate Change has a ‘CETP Scheme’ since 1991. This scheme promotes establishment of CETPs for treatment of effluents generated from SSI units located in clusters by providing a financial assistance in the form of subsidy on capital up to 75% (50% central subsidy plus 25% state subsidy). -
Andhra Pradesh Pollution Control Board List of Industries Category Wise Red
Andhra Pradesh Pollution Control Board List of Industries Category Wise Red Srikakulam District M/s. Dr. Reddy’s Laboratories Limited (CTO Unit-VI), IDA, Pydibheemavaram (V), 1 Ranasthalam (M), Srikakulam District United Millennium Breweries Limited, (Formerly M/s. GMR Beverages & Industries 2 Limited), Bantupalli (V), Ranasthalam (M). Srikakulam District 3 Nagarjuna Agri Chem Limited, Arinama Akkivalasa(V), Etcherla (M). 4 SAMKRG Pistons Limited, (Unit-II), Varisham (V), Ranasthalam (M). 5 Smart Chem Technologies Limited, Ponnada (V), Etcherla (M), Srikakulam District 6 Varam Power Projects, Chilakapalem (V), Etcherla (M), Srikakulam District. 7 Andhra Organics Limited, IDA, Pydibheemavaram (V), Ranasthalam (M). 8 Aurobindo Pharma Limited, Pydibheemavaram (V), Ranasthalam (M). Frinze Laboratories Limited, (Formerly DR Organics Limited), Pisini (V), Ranasthalam 9 (M), Srikakulam District Parry Sugar Industries Limited (Formelry GMR Industries Limited), (Distillery Division), 10 Sankili (V), Regidi Amadalavalasa (M), Srikakulam District Trimex Sands Private Limited (Trimax Industries Limited), Vatsavalasa (V), Gara (M), 11 Srikakulam District Trimex Sands Private Limited (Sand Mining), Vatsavalasa (V), Gara (M), Srikakulam 12 District Synpure Labs India Private Limited, Plot No.45,IDA, Pydibheemavaram (V), Ranasthalam 13 (M), Srikakulam District Trans World Garnet India Limited (Sand Mining), Mofaz Bandru,Ippili & Srikakulam 14 Villages of Gara(M), Srikakulam District 15 Saraca Laboratories Limited, Boyapalem (V), Ranasthalam (M). Ekasila Chemicals Limited, Plot No. 23 to 26, IDA, Pydibheemavaram (V), Ranasthalam 16 (M), Srikakulam District Parry Sugar Industries Limited (Formerly M/s. GMR Industries Limited) (Sugar 17 Division), Sankali (V), Regidi Amadalavalasa (M), Srikakulam District SAMKRG Pistons & Rings Limited (Plant-III), Allinagaram (P.O), Arinama Akkivalasa (V), 18 Etcherla (M), Srikakulam District Vysyaraju Venkata Raju (Mining of Colour Granite) R. -
District Survey Report Srikakulam District
1 DISTRICT SURVEY REPORT SRIKAKULAM DISTRICT Prepared by Dr.S.V.Ramana Rao M.Sc.,Ph.D.,PGDMC&J., Assistant Director of Mines and Geology, Tekkali Submitted to Director of Mines and Geology, Government of Andhra Pradesh June, 2018 DMG, GoAP 2 Index Sl.No. Contents Page No. 1.0 Salient Features of Srikakulam District 9 1.1 Introduction 9 1.2 Boundaries and Topography: 10-11 1.3 Classification of Geographical Area of Srikakulam District 12 1.4 Natural Resources 12 1.5 Development Activities 12 A)Agriculture 12-13 B)Irrigation 13 1.6 Details of Irrigation Projects 14-15 A) Education 15 B) Culture of Srikakulam 15 C) Transportation of Srikakulam 16 D) People of Srikakulam 16 E) Language of Srikakulam 16 F) Srikakulam Weather 16 2.0 Tourists Places of Srikakulam 17 A) Arasvilli 17 B) Srikurmam 18 C) Salihundam 18 D) Srimukhalingam 19 E) Kalingapatnam 19 DMG, GoAP 3 F) Kaviti 19 G) Baruva 20 H) Telineelapuram 20 I) Mandasa 20 J) Rajam 21 3.0 Ground Water in Srikakulam District, Andhra Pradesh 21-24 3.1 Tekkali Office Jurdisction 24-26 4.0 Geology 27 4.1 Eastern Ghats Super Group 27-28 4.2 Khondalite 29 4.3 Charnockite 29 4.4 Migmatite 30-31 4.5 Intrusives 32 4.6 Structures 32 4.7 Metamorphism 33 4.8 Geochronoology 34 A) Upper Gondwana Formations 34 B) Quaternary Formations 34 C) Recent formations 34 5.0 Economic Deposits 35 5.1 General 35 5.2 Granite Deposits 35-40 A) Blue Granite 35-40 DMG, GoAP 4 B) White Granites 40-42 C) Other Varieties of Granite 42-43 D) Porpiiyroblastic Granite Gneiss 43 5.3 Other Deposits 44-45 A) Quartz and Quartzite 44-45 B) Lime Shell 46 C) Beach Sands 46 D) Clay 47 E) Manganese Ore 48 F) Lime Kankar 49 G) Laterite 50 6.0 Minor Minerals 51 A) Ponduru - Rapaka Quarries 51 B) Singupuram Quarry 52 C) Etcherla and Salihundam Quarries 52 6.1 Statement Showing the mineral based industries in the Srikakulam 52-76 District 6.2 Statement Showing the mineral based industries in the Tekkali 77-79 6.3 List of Colour Granite MDLs in O/o Asst.