Operating Manual
Total Page:16
File Type:pdf, Size:1020Kb
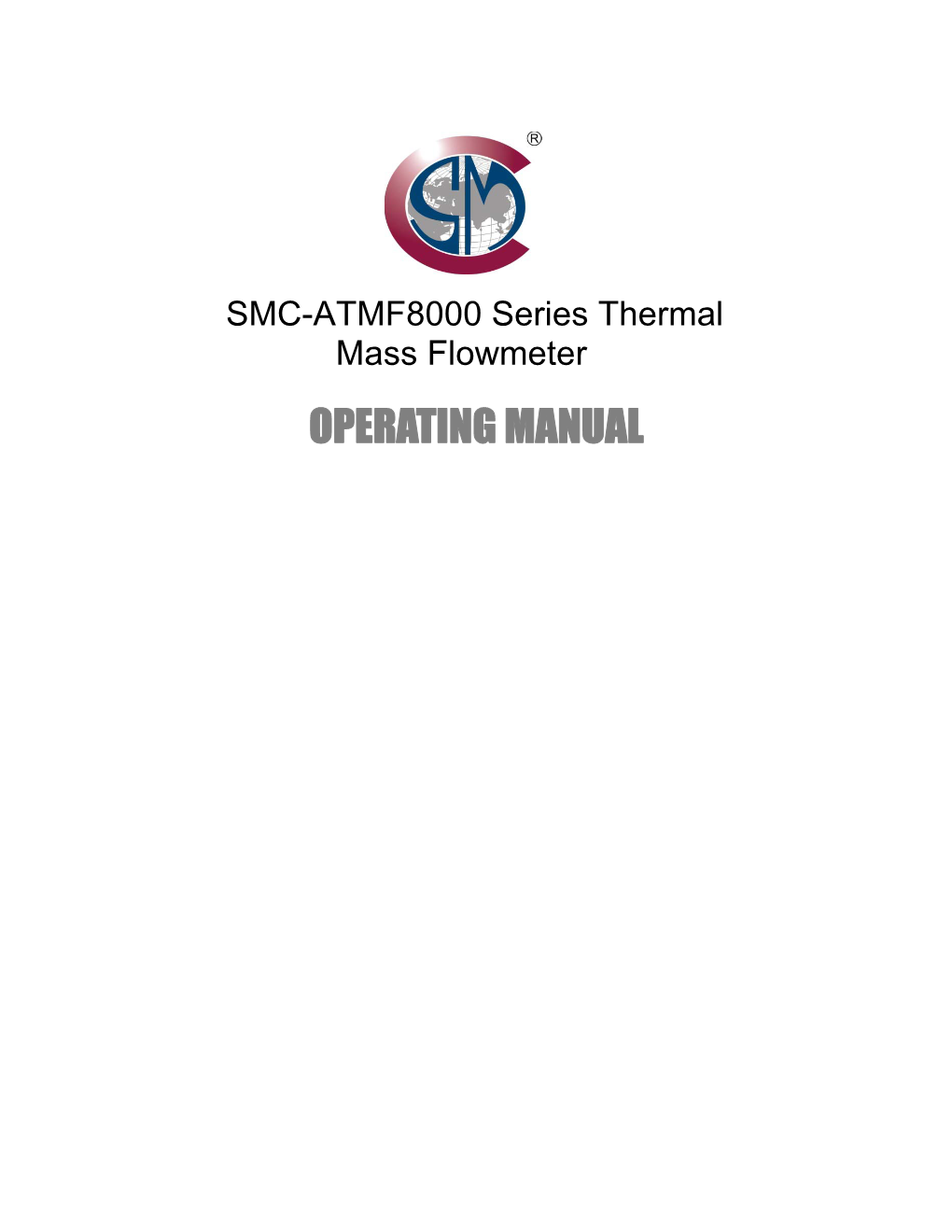
Load more
Recommended publications
-
8000 Plus Magazine Issue 17
THE BEST SELLIINIG IVI A<3 AZI INI E EOF=t THE AMSTRAD PCW Ten copies ofMin^g/jf^^ Office Professional to be ISSUE 17 • FEBRUARY 1988* £1.50 Could AMS's new desktop publishing package be the best yet? f PLUS: Complete buyer's guide to word processing, accounts, utilities and DTP software jgl- ) MASTERFILE 8000 FOR ALL AMSTRAD PCW COMPUTERS MASTERFILE 8000, the subject of so many Any file can make RELATIONAL references to up enquiries, is now available. to EIGHT read-only keyed files, the linkage being effected purely by the use of matching file and MASTERFILE 8000 is a totally new database data names. product. While drawing on the best features of the CPC versions, it has been designed specifically for You can import/merge ASCII files (e.g. from the PCW range. The resulting combination of MASTERFILE III), or export any data (e.g. to a control and power is a delight to use. word-processor), and merge files. For keyed files this is a true merge, not just an append operation. Other products offer a choice between fast but By virtue of export and re-import you can make a limited-capacity RAM files, and large-capacity but copy of a file in another key sequence. New data cumbersome fixed-length, direct-access disc files. fields can be added at any time. MASTERFILE 8000 and the PCW RAM disc combine to offer high capacity with fast access to File searches combine flexibility with speed. variable-length data. File capacity is limited only (MASTERFILE 8000 usually waits for you, not by the size of your RAM disc. -
Camcorder Accessories #2
Section2 PHOTO - VIDEO - PRO AUDIO Camcorder Accessories LCD Monitors and Accessories.............122 Power and Lighting ........................123-127 Camcorder Filters...........................128-129 Camcorder Lenses ..........................130-141 Camcorder Support........................142-157 Audio for Video ..............................158-178 Camcorder Bags .............................179-185 Underwater Housings ....................186-195 VARIZOOM VZ-TFT SERIES Active Matrix LCD Video Monitors VariZoom's VZ-TFT series monitors serve two purposes. First, they function as an external video display, allowing you to step back from the camera while recording (no more bending over to peek through a tiny viewfinder). Second, combined with a tripod-mounted camera and a VariZoom lens controller, they can emulate a studio-style rig costing thousands of dollars. Used on a hand-held camera, a VZ-TFT monitor lets you walk around with ease while accurately framing shots. Additionally, it is a highly compact and affordable alternative to bringing a conventional CRT video monitor into the field for video playback. Use them to review footage on an airplane or any other small space. Mounted on or near the camera, they provide instant playback of footage for small groups. For those who want audio monitoring and playback, the VZ-TFT-4 ACCESSORIES has a built-in speaker. ◆ Large, bright active matrix display has wide viewing angle VZ-TFT SERIES PRICING ◆ TFT Technology means no blurring/strobing of VZ-TFT-4 4˝ TFT Monitor with A/V cables and -
19, 2009 OUR 119Th YEAR – ISSUE NO
Ad Populos, Non Aditus, Pervenimus Published Every Thursday Since September 3, 1890 (908) 232-4407 USPS 680020 Thursday, November 19, 2009 OUR 119th YEAR – ISSUE NO. 47-2009 Periodical – Postage Paid at Rahway, N.J. www.goleader.com [email protected] SIXTY CENTS BOE: Health Insurance Hikes Could Lead to Layoffs in District By CHRISTINA M. HINKE last five years to combat rising pre- receive insurance as well as does Specially Written for The Westfield Leader miums, according to Board Presi- their replacement. Premiums in the WESTFIELD – The town’s board dent Ginny Leiz. Although she said Westfield school district are lower of education stressed concerns over she acknowledged the staff for sup- than average, Mr. Lawrie said, and rising healthcare costs as it heard an porting the board’s decision to the percentage of health insurance to update on the current school year’s, change carriers, she said she under- the operating budget is “typical.” 2009-2010, school budget, which was stood “it’s not easy [for the insured] The district offers staff an indem- presented on Tuesday. to change carriers.” nity or a point of service (POS) plan, Over the last eight school calen- Last year the district switched from with a majority of staff (about 70 dar years, health insurance costs have Cigna to Horizon Blue Cross Blue percent) opting for the POS, which is increased about 5 percent when com- Shield to save over $1 million, ac- offered at a lower cost than the in- pared to the district’s total operating cording to the district’s insurance demnity plan. -
White Paper the Canon Eos 5D Mark Ii Camera
WHITE PAPER THE CANON EOS 50D CAMERA: UNPRECEDENTED FLEXIBILITY OF DIGITAL PHOTOGRAPHY THE CANON EOS 5D MARK II CAMERA: HIGH PERFORMANCE FOR HIGH EXPECTATIONS I. Overview 4 II. Summary of New and Improved Features 8 EOS 50D vs. EOS 40D 9 EOS 5D Mark II vs. EOS 5D 10 EOS 5D Mark II vs. EOS-1Ds Mark III 11 III. Video Recording on EOS 5D Mark II 13 Features and Benefits 14 Positioning 16 Tech Info 18 Technology Highlight - New Video Shooting Capability 19 IV. Performance and Reliability 20 Advanced Sensor Designs 21 DIGIC 4 and 14-bit A/D Conversion 23 Image Recording and Processing 25 • RAW, sRAW, RAW+JPEG 25 • Intelligent Lithium-ion Battery on EOS 5D Mark II 26 Image Enhancement 26 • High ISO Noise Reduction 26 • Peripheral Illumination Correction 27 • Auto Lighting Optimizer 28 • Highlight Tone Priority 28 High Resolution, 3.0-inch Clear View LCD 29 Live View shooting with AF 30 Precise 9-point AF Systems 31 Improved Viewfinder Experience 33 Rugged Construction 33 EOS Integrated Cleaning System 34 Intuitive Button and Dial Arrangement 35 Increased Shutter Durability 35 Action-stopping Burst Modes 36 UDMA Compatibility 36 HDMI Connectivity 36 Technology Highlight - Live View Function 38 V. Controls and Convenience 39 Camera Settings and Displays 40 Creative Auto Mode 40 Image Quality Controls 42 Playback Controls and Displays 42 My Menu and User Settings 43 Custom Function Controls 43 AF Microadjustment 44 Quick Control Screen 45 Printing and Camera Direct Controls 45 VI. Intelligent Bundled Software 46 New Features in EOS Utility and DPP 47 VII. -
SCCM Part 1 R1 Copy
TURN YOUR INTO Turn for your future. VISION Changing lives and enriching communities for a better world. MISSION • We deliver superior products and services that benefit society, and shape future generations of leaders and thinkers. • We care for the safety and health of our people, and we believe in developing their talents through empowerment and enabling them to maximise their potential. • We grow our businesses to deliver sustainable and responsible shareholder returns while ensuring that we continue to protect our environment. • We must be bold in technological innovations to be market leaders in our core businesses. • We will leverage on the synergies within our business ecosystem to create unique product offerings. EDUCATION CHARTER • We inspire students and staff to lead, share and serve. • We create a community in which learning, teaching and research are encouraged, enabled and enjoyed. • We promote critical thinking, independent learning and creative problem solving. • We nurture individuals to be ethical and responsible global citizens. • We share our success with stakeholders and the community we serve. Do things differently. things Do incididunt. sed do eiusmod tempor tempor eiusmod do sed consectetur adipiscing elit, elit, adipiscing consectetur Lorem ipsum dolor sit amet, amet, sit dolor ipsum Lorem TABLE OF CONTENTS 1 ABOUT Introduction 2 Entrepreneurial Spirit & Working with Communities 3 2 COMPUTING AND CREATIVE MEDIA About 5 Why Choose KDU 6 Academic Faculty 8 Student Projects 11 Awards & Achievements 12 Facilities 14 Study Route 15 3 KDU PROGRAMMES Foundation Studies (Art & Technology) 16 Diploma in Computer Studies 18 Diploma in Sequential Art 20 Bachelor of Computer Science (Hons) 22 Bachelor of Game Development (Hons) 24 Bachelor of Software Engineering (Hons) 26 Bachelor of Information System (Hons) (Enterprise Information Systems) 28 Bachelor of Arts (Digital Media Production) 30 4 STUDENT LIFE 34 36 5 CAMPUS LIFE & FACILITIES COMPUTING & CREATIVE MEDIA 1 INTRODUCTION Welcome to KDU. -
Buy Cheap Cialis Online
Like us on Facebook! Visit us online at montrosemirror.com! Please Support our Advertisers! Remembering the legacy of Dr. Martin Luther King, Jr. © Issue No. 360 Jan. 20, 2020 www.montrosecounty.net OLATHE TRACK MOVES FORWARD; RE-1J SCHOOL DISTRICT SEES INCREASE IN STUDENT MEAL CONSUMPTION www.voahealthservices.org By Caitlin Switzer MONTROSE-Montrose County School District RE-1J Board of Education Vice President Sarah Fishering took the gavel for the regular meeting of Tuesday, Jan. 14, in the absence of Board President Gayle Johnson. With the exception of Johnson, all direc- tors were present for the meeting. www.tristategt.org STUDENT SPOTLIGHT Centennial Middle School Eighth Grader Allie Stam- baugh and Life Skills Educator Kim Huchel conduct- ed a life skills presentation on the culinary arts. Huchel said that teaching life skills to middle schoolers is a rewarding job; “You get to have kids in the kitchen.” Stambaugh put finishing touches on a meal of www.scottsprinting.com Centennial Middle School Eighth Grader Allie Stam- pineapple fried rice, all the while chatting comfort- baugh gave a life skills presentation on the culinary arts ably about the things she for the Montrose County School District RE-1J board of has learned as a life skills Continued pg 15 Education on Jan. 14. FOOD, COFFEE, COMPANY: THERE ARE NO OUTSIDERS AT MADA By Caitlin Switzer www.montrosecolorado.com MONTROSE- Step through the doors on a weekday, and the mood is friendly here, with a blend of Spanish and English speakers and a small, but dedi- cated crew of volunteers. With a mission that dates to 1972, the Mexican American Development Asso- ciation (MADA) at 17 North 6th Street offers a mul- titude of useful services for people experiencing www.alpinebank.com homelessness or insecure housing. -
Section 1115 Demonstration: Kansas Kancare
Section 1115 Demonstration: Kansas KanCare Public Comments Title Description Created At Be realistic and use • New systems are not functional as of December 24th: 2013-12-24 common sense o Providers already can’t bill for services because of the day service 12:29 unit conversion o Some CDDOs cannot access the new basis system • Not only are these new system not functional, but the state administration and MCOs cannot get the issues that have been ongoing for almost a year already resolved. These issues continue to happen repeatedly because all the state has to do to indicate resolution is to have passed it on to the MCO to resolve. This is also known as ‘passing the buck’. I heard many people saying over two years ago that this would happen and it is. • The MCOs are not likely to resolve the payment, pre-authorization and overwhelming administration issues the providers are facing simply because this is simply how they operate, how they do business, everywhere. Denying this is silly and not realistic. • It is saddening that after literally years of individuals with I/DD, their families, guardians, caregivers, providers, case managers, and CDDOs telling our state administration that this is not a good business model for I/DD long term services, that they can simply choose not to listen to those who know best how to provide these services, and just do as THEY choose. I haven’t spoken to anyone who knows how to serve these individuals that wants this, or honestly believes it will provide better outcomes. -
Isolette 8000 Plus
Instructions for use Isolette 8000 plus WARNING Incubator To properly use this medical device, Software 5.n read and comply with these instructions for use. This page has been left blank intentionally. 2 Instructions for use Isolette 8000 plus SW 5.n Contents Contents 1 Information about these instructions for use ............................................. 7 1.1 Typographical conventions ................................................................... 7 1.2 Trademarks ........................................................................................... 7 1.3 Information on safety instructions and precautionary statements ......... 8 2 For your safety and that of your patients .................................................. 11 2.1 Information on safety instructions and precautionary statements ....... 11 2.2 Basic safety instructions ..................................................................... 11 2.3 Target groups ..................................................................................... 14 2.4 Safety instructions for accessories ..................................................... 15 2.5 Electrical safety ................................................................................... 16 2.6 Explosion protection ........................................................................... 18 2.7 Use of oxygen ..................................................................................... 19 2.8 Use of humidity .................................................................................. -
The Voice Jael Kerandi (’21 BSB) Led Students Through Unprecedented Crises
CARLSONFALL 2020 SCHOOL OF MANAGEMENT The Voice Jael Kerandi (’21 BSB) led students through unprecedented crises THE MAGAZINE FOR ALUMNI AND FRIENDS FALL 2020 THE CARLSON SCHOOL OF MANAGEMENT MAGAZINE CARLSON FOR ALUMNI AND FRIENDS Opposite: Murals and tributes honor the DISCOVER life of George Floyd in south Minneapolis. 3 Start-Up News Cover and right: Jael Kerandi, the 7 3 People, 3 Questions first Black student body president, 8 Faces of Carlson led students through COVID-19 and protests with steady purpose. FOCUS : UNPRECEDENTED TIMES Photography by Nate Ryan. 10 Faculty Insights Below: Four savvy alumni are building 14 Close-Up: Alumni business models and products that can help their businesses—and 18 their customers— The Voice thrive, even during a global pandemic. How Jael Kerandi (’21 BSB) led fellow students through COVID-19 and the murder of George Floyd 18 24 A Port in the Storm Tomme Beevas (’11 CEMBA) is reinventing the way a restaurant can serve its community 30 Alumni Profiles ENGAGE 35 News & Notes 36 Executive Spotlight 38 Giving 42 Alumni Happenings 44 Class Notes 48 5 Things I’ve Learned 30 FALL 2020 | CARLSON SCHOOL OF MANAGEMENT 1 FROM THE DEAN Building Connections START-UP NEWS More Important Than Ever DISCOVER “No [person] is an island.” Our last magazine explored the world and our months, the Carlson School’s faculty and English poet John Donne’s place in it. The themes remain, but we’ve seen 1,532 staff responded admirably. “Our faculty 17th-century words remain immense change these last six months. Here in responded to this shift with resiliency and true. -
A Force at Razor's Edge
April 2010/$4 A Force at Razor’s Edge Cyber Menace Tankers in Unknown Territory MiG Alley Remembered F-35 LIGHTNING II USA DELIVERING ON THE PROMISE. THE PARTNERSHIPS WithW each flight test, the F-35 Lightning II continues to ddeliver unprecedented performance as the world’s only iniinternational 5th generation multirole fighter. While each vvariant is uniquely designed to operate from different bbases, all three variants – conventional, carrier and SSTOVL – set new standards in network-enabled mission ssystems, sensor fusion, supportability and maintainability. AllA while bringing together nnine international partners wwith a common commitment tto build the most capable, aaffordable multirole fighter that willw provide global security forfof decades to come. F-35 – COMMITMENT Redefining the multirole fighter. NORTHROP GRUMMAN BAE SYSTEMS PRATT & WHITNEY GE ROLLS-ROYCE FIGHTER ENGINE TEAM LOCKHEED MARTIN April 2010, Vol. 93, No. 4 2 Editorial: The Mullen Doctrine 56 Commissioned in Hanoi By Robert S. Dudney By Leo K. Thorsness The threshold for commitment of Art Cormier, Neil Black, and Bill forces is lower than it used to be. Robinson showed excellence in the Now it looks like it will go lower still. POW camps around Hanoi. 24 A Force at Razor’s Edge 61 MiG Alley By John A. Tirpak By John T. Correll There will be no margin for error, The American F-86 Sabres stopped said senior Air Force leaders at the MiG-15s—and their Russian AFA’s Air Warfare Symposium. pilots—at the Yalu. 30 Airpower On Demand 65 Chart Page Special: By Marc V. Schanz Defense Budget at a Glance 34 At AFA’s Air Warfare Symposium in By Tamar A. -
NO JOKE Official: Financial Aid Now Priority Women’S Rifle Team Heads to Nebraska This Weekend
T C U DAILY SKIFF DAILYSKIFF.COM ∙ FRIDAY, JANUARY 22, 2010 ∙ VOL. 107 ISSUE 88 NEWS NEWS The university will offer a new University faculty, staff and credit-earning Study Abroad op- students are finding new ways portunity in Ghana for students to provide relief for victims in of all majors. Haiti. Tomorrow Tomorrow CAMPAIGN FOR TCU CONAN VS. NBC NO JOKE Official: Financial aid now priority Women’s rifle team heads to Nebraska this weekend. By Thomas Koenig Sports, page 6 Staff Reporter The Campaign for TCU, which has already reached more than 86 percent TODAY’S HEADLINES of its $250 million goal, is changing its News: Executives visit priority from the construction of new campus, page 2 facilities to scholarships, a school offi- Opinion: Oil reliance cial said. unwise, page 3 The $100 million Scholarship Initia- Sports: Wade Phillips tive has recently gained priority over extends contract, page 6 new facilities, said David Nolan, associ- ate vice chancellor for university devel- opment. As of Tuesday night, the cam- paign had earned $216,498,370 since it CONTACT US began in 2005, Nolan said. Send your questions, COURTESY OF SAM WUNDERL According to the campaign’s Web compliments, complaints Supporters of “Tonight Show” host Conan O’Brien on Monday rally outside Universal Studios where the show is shot to protest NBC’s site, the campaign was originally broken or news tips to news@ move to push the show to a later timeslot. into four categories: Strengthening the dailyskiff.com. Follow us Vibrant TCU Community by improv- on Twitter at twitter.com/ ing the Living Learning Community, tcudailyskiff or look up Conan exit leaves student stranded Endowed Scholarships for recruiting “DailySkiff.com” on high-caliber students, Academic Pro- By Courtney Jay O’Brien and NBC was at a lengthy Amber Watts, an assistant pro- Facebook. -
Plans to Change Livermore Arts Commission Needs More Input
VOLUME LII, NUMBER 40 Your Local News Source Since 1963 SERVING DUBLIN • LIVERMORE • PLEASANTON • SUNOL THURSDAY, OCTOBER 1, 2015 Plans to Change Livermore Arts Commission Needs More Input Plans to change the role mission currently takes on art Gary said the issue is the number of members on staff, refining the Commis- of Livermore's Commission two roles. One to generate important to resolve. He the Commission from nine sion's mission would allow Find Out What's for the Arts were sent back to and create applications, the suggested staff meet with to seven; adjusting the num- it to focus on the review and staff for more work. other to review rank and the Livermore Cultural Arts ber of meetings from one a funding process of applica- Happening After reviewing the fund the applications. That Council (LCAC) to revisit month to four a year; allow- tions, setting art priorities for Check Out Section A changes and listening to places fund control in the the depth and scope of what ing mini grant applications the city, and reviewing and Section A is filled with public testimony, the city hands of those who generate LCAC and the Commis- of $1000 or less to be ap- making recommendations information about arts, council tabled the proposal the proposals. One of the sion accomplish. He said plied for and approved four regarding public art. people, entertainment and and directed staff to take a objectives of the changes he was open to providing a times a year; allowing grant According to Eric Ura- special events.