Using Fuel Cells to Power Electric Propulsion Systems
Total Page:16
File Type:pdf, Size:1020Kb
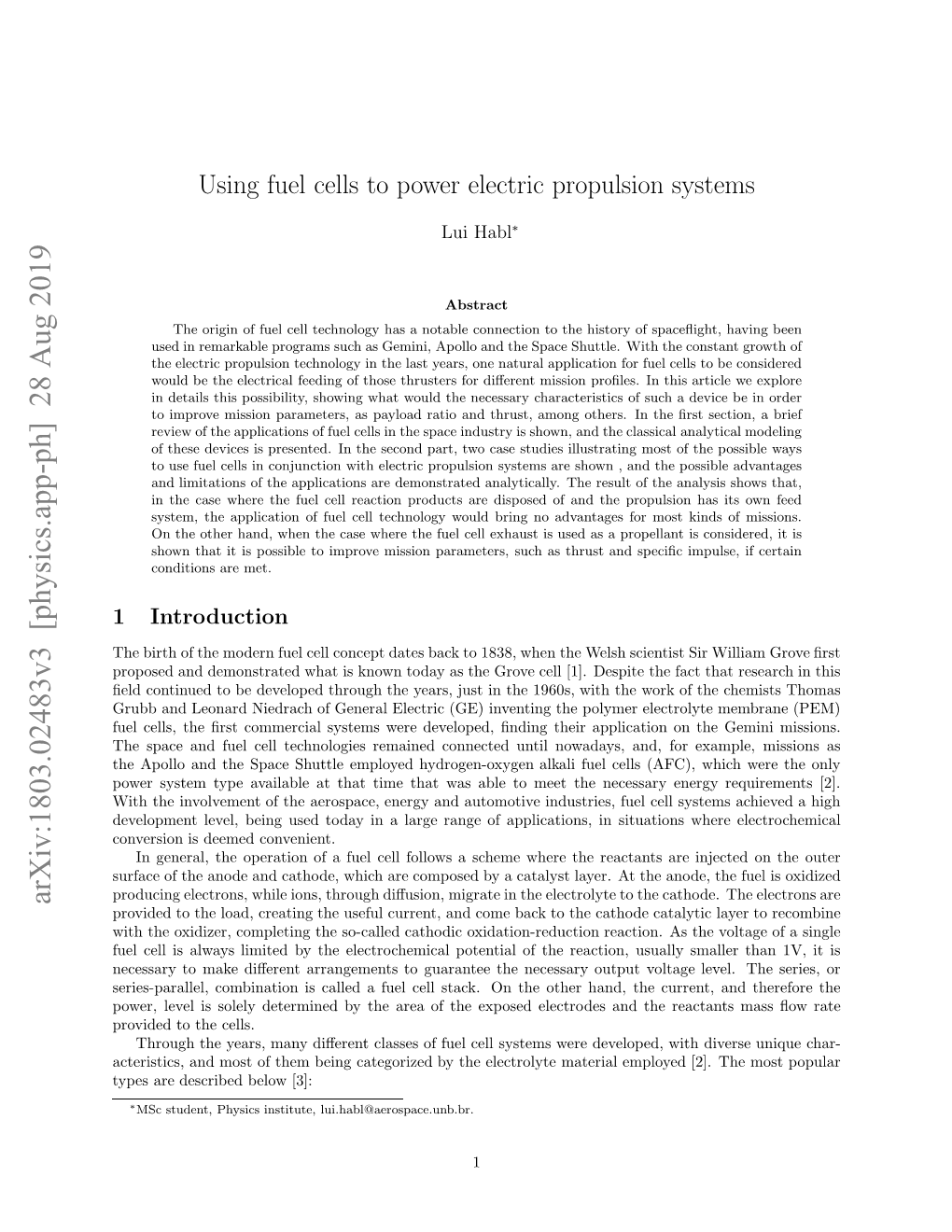
Load more
Recommended publications
-
Fuel Cell Energy Generators PLATINUM CATALYSTS USED in ALTERNATIVE ENERGY SOURCE
Fuel Cell Energy Generators PLATINUM CATALYSTS USED IN ALTERNATIVE ENERGY SOURCE By D. S. Cameron Group Research Centre, Johnson Matthey and Co Limited The steam, in turn, is produced by burning Improvements in the preparation and fossil fuels (coal or hydrocarbons), or by utilisation of platinum metal catalysts nuclear fission. Unfortunately, the processes have now made megawatt scale fuel cell of converting fuel into heat, heat into steam, systems economically viable. The high and steam into electricity involve efficiency thermal efficiency and low pollution losses at every stage. The Carnot cycle characteristics of this novel power source shows that the thermal efficiency of any heat are likely to result in it forming an engine is limited to E where: increasing proportion of the generating capacity utilised for both peaking and intermediate applications. This paper T, and TI being the temperatures, in degrees briejly reviews the development of fuel kelvin, at which heat is supplied to, and cells; it also describes how they work, rejected by, the system. In practice, upper including the function of the catalyst, temperatures are limited to about 500'C and indicates the more important of the (773 K), lower temperatures are at least 30°C many factors which have to be considered (303 K), and efficiencies are limited to a when selecting a commercial system. maximum of 60 per cent. Indeed most modern large power stations are able to achieve only 38 to 40 per cent efficiency. Fuel cells have already achieved acceptance Fuel cells convert fuel directly into elec- as reliable, lightweight power sources for trical energy by an electrochemical route space applications, for example in the Apollo which is not limited by the Carnot cycle. -
Introduction to Materials for PEMFC Electrodes Final
University of Birmingham Introduction to Materials for PEMFC Electrodes Mardle, Peter; Du, Shangfeng License: None: All rights reserved Document Version Peer reviewed version Citation for published version (Harvard): Mardle, P & Du, S 2020, Introduction to Materials for PEMFC Electrodes. in A-G Olabi (ed.), Encyclopedia of Smart Materials. Elsevier. Link to publication on Research at Birmingham portal General rights Unless a licence is specified above, all rights (including copyright and moral rights) in this document are retained by the authors and/or the copyright holders. The express permission of the copyright holder must be obtained for any use of this material other than for purposes permitted by law. •Users may freely distribute the URL that is used to identify this publication. •Users may download and/or print one copy of the publication from the University of Birmingham research portal for the purpose of private study or non-commercial research. •User may use extracts from the document in line with the concept of ‘fair dealing’ under the Copyright, Designs and Patents Act 1988 (?) •Users may not further distribute the material nor use it for the purposes of commercial gain. Where a licence is displayed above, please note the terms and conditions of the licence govern your use of this document. When citing, please reference the published version. Take down policy While the University of Birmingham exercises care and attention in making items available there are rare occasions when an item has been uploaded in error or has been deemed to be commercially or otherwise sensitive. If you believe that this is the case for this document, please contact [email protected] providing details and we will remove access to the work immediately and investigate. -
A Multi-Pronged, Noninvasive Probing of Electrodeposition In
A MULTI-PRONGED, NONINVASIVE PROBING OF ELECTRODEPOSITION IN LI-ION BATTERIES A Thesis by MICHAEL ANDREW KALAN Submitted to the Office of Graduate and Professional Studies of Texas A&M University in partial fulfillment of the requirements for the degree of MASTER OF SCIENCE Chair of Committee, Partha P. Mukherjee Committee Members, Sarbajit Banerjee Hong Liang Head of Department, Andreas A. Polycarpou May 2017 Major Subject: Mechanical Engineering Copyright 2017 Michael Andrew Kalan ABSTRACT Lithium ion batteries hold the potential to play a key role in meeting our future and increasing energy storage needs. Lithium ion batteries have the highest energy density of all battery systems currently available. Since their introduction to the modern battery market in the mid 90’s they have evolved and become the choice system for meeting energy needs in portable electronic devices. Lithium ion batteries, however, face many challenges preventing them from being utilized to their fullest potential. They suffer from self-discharge, degradation over repeated charging, not operating well at extreme low or high temperatures, and can suffer from the deposition of metallic lithium during charging. This deposition builds up on the surface of the graphite electrode and can lead to the formation of structures called dendrites. These dendrites can cause problems like internal short-circuits, ultimately resulting in the battery catching on fire. The focus of this work is to study the electrodeposition of lithium on graphite electrodes. Two main tools are used over the course of this study: modeling and experimentation. The first half of this work discusses the approach through computational modeling. -
Silicon-Based Anode Materials for Lithium-Ion Batteries
Silicon-based anode materials for lithium-ion batteries Binghui Xu Bachelor of Engineering A thesis submitted for the degree of Doctor of Philosophy at The University of Queensland in 2015 School of Chemical Engineering Abstract While lithium-ion batteries (LIBs) have found wide applications in customer electronics, such as cellular phones and lap-top computers, the performance of the currently LIBs does not meet the market requirements for massive energy storage, such as electric vehicles and smart grids. One of the critical issues is the low energy capacity of the electrode materials. Graphite has been a common anode for LIBs, but the maximum capacity (372 mAh·g-1) of graphite has hindered its application in advanced LIBs. Substituting graphite with materials of high capacity has become an active research area. Graphene can store more Li+ than graphite because Li+ can not only be stored on both sides of graphene sheets, but also on the edges and covalent sites. Being electric conducting and mechanically strong, graphene is also an attractive support for other high capacity materials, such as silicon (Si). Si possesses the highest known theoretical capacity (4200 mAh·g-1, fully lithiated). However, Si suffers from a critical problem, namely severe volume change during charging/discharging, resulting in poor reversibility and rapid capacity decay. This PhD project aims to improve the stability and suitability of Si nanoparticles (SiNPs) for LIBs. The first aspect in this thesis is to demonstrate a novel approach to wrapping SiNPs in a reduced graphene oxide (RGO) aerogel framework. The aerogel-typed RGO architecture not only provided a porous network to accommodate the volume change of entrapping SiNPs, but also facilitated electrolyte transport and electron transfer. -
Head , Electrochemical Systems National Aeronautics and Space Administration Washington, D
Head , Electrochemical Systems national Aeronautics and Space Administration Washington, D. C. , Summary By 1975, Grove-type fuel cells may reach 70% gross thermal efficiency, with 3-5%,‘for parasitic power. Cell-degradation rates OP /pss should be 4 microvolts/h ? and system specific weight 60-80 lbs/kw of average load, with maintenfince-free life up to 1 year. A better cathodic catalyst, optimized electrode structure, Tn&Y;t-m$,-rices I (if used at all) will be needeq. Better solutions to chemical engir.eering prJblems are even more urgent.’ The best approach appears to be abandon- i ment of the Grove cell and use of modern electrochemical knowledge in developing novel systems concepts. Tklese may result in even greater %.. %.. weight and volume savings as well as simpler controls, lower parasitic power and longer life, particularly for larger power systems. Peak ,sower and heat-load demands might best be met by special auxiliaries instead of overdesign of the basic equipment. In turn, pseudo-primary fuel cells may satisfy peak- loads in conjunction with primary solar or nuclear systems. 1 Introduction Among the known fuel-cell reactants, hydrogen and oxygen thus fur appear to be best suited for space use. Energy densities of the reactants the highest that can br attainvd. '.chr? reactants arP rsla'bivuly ca~i.1~ stored and handled, presenting no difficult compatibility problems. Although efficiency losses at the cathode leave room for improvement of low-temperature cathodic catalysts, reactivities of both reactants are high enough to permit equipment to ope te at "low" temperatures (about 100°C) and reasonable thermal efficiencies. -
1990-10: Ancestors of Batteries
The ancestors of today's batteries Radio technology has always been very dependent on batteries . The history of batteries goes back 200 years, twice that of radio itself. During this long period, some very interesting ways of producing an electric current have evolved. There is a common belief that the Operation could be restored by either ing the positive electrode were em- first practical battery was invented by removing the bubbles physically or rest- ployed, as in the Leclanche and Edison Georges Leclanche in 1868, but in fact ing the battery, but these remedies were cells. Leclanche's battery was a relative late- both inconvenient. comer in a long line of developments — The 19th century was the age of indi- Grove's cell some successful, some bizarre, others vidual rather than corporate research, In 1839, Sir William Grove intro- dangerous, but most now forgotten. and experimenters were soon at work duced a cell that performed excellently, The history of the battery actually improving on Volta's pile. Various elec- but was expensive and produced a poi- starts in 1790, when Luigi Galvani of trolytes and electrode materials were sonous gas. Grove's cell consisted of a Bologna was experimenting with mus- tried. Zinc was found to be the most glass jar containing dilute sulphuric acid cles from frog's legs. The story goes satisfactory negative electrode and its and a semicircular amalgamated zinc that he hung them on copper hooks, use was universal. As acids will attack electrode, surrounding a porous earth- suspended from an iron railing. When commercial grade zinc, in some in- enware pot. -
Titelei 1..18
521 Subject Index A – Characteristics 479 AC Techniques Alkaline Manganese Batteries 464 – Bode Plot 285 – Characteristics 467 – Conductivity 14f. Amperometric Titrations 491 – Electron transfer Processes 284 – Biamperometric (“dead-stop”) methods –,– Influence of mass transport 287 492 – Equivalent Circuit for an electrode Anions 6 –,– Diffusion Limited Reaction 282 Anodic Stripping Voltammetry (ASV) 501 –,– Electron transfer Limited 284 – Differential pulse ASV 500 –,– Mixed Control 286 Anolyte 6 – Impedance in the presence of Anode 6, 9, 158 adsorption 289ff – Dimensionally stable 405 – Measurement of film coverage 291 Anthraquinone Process 420 – Nyquist Plot 284f. Applications of high-temperature melts in – Randles Circuit 284 electrochemical processes 394 – Warburg Impedance 282f. – Extraction of uranium Activity Coefficient 46ff. – Deposition of specialised metal alloys – Dependence on concentration 48ff. Apollo Cell 472 – In concentrated solutions 51 Asymmetry Effect 46 – Measurement 139f. Asymmetry Parameter 164, 166ff. – Of neutral molecules 60 Asymmetry Potential 150f. Adiponitrile or Monsanto Process 424 Atomic Force Microscopy (AFM) Adsorption see Scanning Probe Methods – Dependence of current on 212 Avogadro constant 2, 7 – Enthalpies 211 – Influence on current-voltage curves B 293 Bands – Isotherms 208 – Metal Electronic 134 –,– Langmuir 208f. – Conduction 134 –,– Temkin 209 – Valence 135 – Of dipoles 210 Batteries – Of ions 208 – Air batteries 484 – Of intermediates in electrochemical –,– Aluminium-air batteries 484 reactions 212 –,– Zinc-air batteries 484 Air batteries 484 –,– Secondary types 485 – Aluminium-air batteries 484 – Costs of energy storage in 449 – Zinc-air batteries 484 –,– Table of Values 459 –,– Secondary types 485 – Current-voltage characteristics of 446 Alkaline Fuel Cells (AFC) 473ff. – Discharge Characteristics in 447 – Apollo Cell 472 – Efficiency of batteries 486 Electrochemistry. -
Electrochemistry and Fuel Cells: the Contribution of William Robert Grove
Indian Journal of History of Science, 50.3 (2015) 476-490 DOI: 10.16943/ijhs/2015/v50i4/48318 Historical Notes Electrochemistry and Fuel Cells: The Contribution of William Robert Grove Jaime Wisniak* (Received 19 January 2015) Abstract William Robert Grove (1811-1896), a British lawer, judge, and researcher, discovered the voltaic cell that carries his name (more powerful than the Daniell one), the fuel cell, and carried fundamental research in the area of electrochemistry and allied phenomena. His general analysis of physical phenomena may be considered an expression of the first law of thermodynamics and the negation of perpetual motion. Key words: Daniell cell, Electrochemistry, Energy conversion, First law of thermodynamics, Flame electricity, Gas fuel cell, Grove cell, Perpetual motion, Polarization. 1. INTRODUCTION to Grove being appointed to the first professorial chair of the Institution (1841-1846). William Robert Grove1 was born on July 11, 1811, in Swansea in South Wales, the only son The financial needs for growing a long of Anne Bevan and John Grove, a magistrate and family forced him to return to the practice of law; deputy lieutenant of Glamorgan. After receiving in 1853 he became a Q.C. (Queen Council), in 1871 he was appointed a judge to the Court of private education he registered at Brasenose Common Pleas, and in 1880 he was appointed to College (one of the constituent colleges of the the Queen’s Bench. In 1887, after retirement, he University of Oxford), receiving a B.A. degree in appointed a member of the Privy Council. 1832. He then moved to London to pursue a legal career at Lincoln’s Inn and was called to the bar William Grove passed away on August 1, 1896, after a long illness and was buried at Kensal in 1835. -
(Zinc-Carbon) Batteries • Alkaline Manganese Dioxide Batteries
CHAPTER 3 Batteries Expected Outcomes •What is a battery? •Performance of batteries •Types of batteries •Advantages & Disadvantages •Electric vehicles Batteries Contents • What is a battery? • Performance of batteries • Types of batteries • Advantages & Disadvantages • Electric vehicles What is a battery? • An electric battery is a device consisting of one or more electrochemical cells (battery cells) that convert stored chemical energy into electrical energy. • Each cell contains a positive terminal, or cathode, and a negative terminal, or anode. Electrolytes allow ions to move between the electrodes and terminals, which allows current to flow out of the battery to perform work. Types of battery cells Wet cell- A wet cell battery has a liquid electrolyte. e.g. , Grove cell, Bunsen cell etc. http://www.upsbatterycenter.com/blog/what-is-a-dry-cell-battery/ 12/19/2015 A dry cell uses a paste electrolyte, with only enough moisture to allow current to flow. e.g., Zinc–carbon battery or Leclanche cell. Principle of operation • A battery consists of some number of voltaic cells. Each cell consists of two half-cells connected in series by a conductive electrolyte containing cathode and anode. The electrode to which anions (negatively charged ions) migrate; the other half- cell includes electrolyte and the positive electrode to which cations (positively charged ions) migrate. • Cations are reduced (electrons are added) at the cathode during charging, while anions are oxidized (electrons are removed) at the anode during discharge. Major types of batteries • Primary batteries is a portable voltaic cell that is not rechargeable. When the supply of reactants is exhausted, energy cannot be readily restored to the battery. -
246. the Grove-Bunsen Cell
Notes from the Oesper Collections The Grove and Bunsen Cells William B. Jensen Department of Chemistry, University of Cincinnati Cincinnati, OH 45221-0172 The previous two issues of Museum Notes have de- scribed the secondary Edison nickel-iron alkaline stor- age cell (1) and the primary Daniel gravity cell (2) respectively. This issue will deal with two more closely related primary cells of historical importance found among the collection of voltaic cells donated to the Oesper Collections some years ago by the Chemistry Department of Oberlin College – the Grove nitric acid cell and the Bunsen carbon cell. First described by the British scientist and jurist, William Robert Grove (fig- ure 1), in 1839 (3) both of these cells are based on the net cell reaction (4): Zn(s) + H2(SO4)(aq) + 2H(NO3)(aq) → Zn(SO4)(aq) + 2NO2(g) + 2H2O(l) + ΔEel Figure 1. William Robert Grove (1811-1896). in which Zn(0) is oxidized to Zn(II) at the anode, N(V) is reduced to N(IV) at the cathode, and the resulting net cell potential is roughly 1.9 V. Like the Daniel cell described in the previous is- sue, the Grove nitric acid cell was a two-fluid system that employed separate electrolytes for the cathode and anode and a ceramic spacer. In his prototype Grove had employed the bowls from broken clay pipes as his spacers, with an inert platinum (Pt) cathode and nitric acid [H(NO3)] electrolyte inside the pipe bowl, and a Zn anode and dilute sulfuric acid [H2(SO4)] electrolyte outside the pipe bowl (5). -
Composite Gel Polymer Electrolyte for Lithium Ion Batteries Roya Naderi South Dakota State University, [email protected]
South Dakota State University Open PRAIRIE: Open Public Research Access Institutional Repository and Information Exchange Theses and Dissertations 2016 Composite Gel Polymer Electrolyte for Lithium Ion Batteries Roya Naderi South Dakota State University, [email protected] Follow this and additional works at: http://openprairie.sdstate.edu/etd Part of the Materials Science and Engineering Commons, and the Power and Energy Commons Recommended Citation Naderi, Roya, "Composite Gel Polymer Electrolyte for Lithium Ion Batteries" (2016). Theses and Dissertations. Paper 1061. This Thesis - Open Access is brought to you for free and open access by Open PRAIRIE: Open Public Research Access Institutional Repository and Information Exchange. It has been accepted for inclusion in Theses and Dissertations by an authorized administrator of Open PRAIRIE: Open Public Research Access Institutional Repository and Information Exchange. For more information, please contact [email protected]. COMPOSITE GEL POLYMER ELECTROLYTE FOR LITHIUM ION BATTERIES BY ROYA NADERI A thesis submitted in partial fulfillment of the requirements for the Master of Science Major in Electrical Engineering South Dakota State University 2016 iii This thesis is dedicated to my parents, Bahador Naderi and Homeira Sam-Daliri for their love, encouragement, support and always teaching me “Educate for betterment of the world, education is waste of time if can’t make our lives easier!” iv ACKNOWLEDGEMENTS The work presented in this thesis was supported by NASA EPSCoR (Award #: NNX14AN22A), and by the State of South Dakota. First and foremost, my deepest gratitude would be extended to Dr. Qiao as my supervisor and graduate coordinator for providing me the opportunity of working in his research group as a research assistant and his enormous help throughout this project. -
Battery Life and How to Improve It
Battery Life and How To Improve It Battery and Energy Technologies Technologies Battery Life (and Death) Low Power Cells High Power Cells For product designers, an understanding of the factors affecting battery life is vitally important for managing both product Chargers & Charging performance and warranty liabilities particularly with high cost, high power batteries. Offer too low a warranty period and you won't Battery Management sell any batteries/products. Overestimate the battery lifetime and you could lose a fortune. Battery Testing Cell Chemistries FAQ That batteries have a finite life is due to occurrence of the unwanted chemical or physical changes to, or the loss of, the active materials of which Free Report they are made. Otherwise they would last indefinitely. These changes are usually irreversible and they affect the electrical performance of the cell. Buying Batteries in China Battery life can usually only be extended by preventing or reducing the cause of the unwanted parasitic chemical effects which occur in the cells. Choosing a Battery Some ways of improving battery life and hence reliability are considered below. How to Specify Batteries Battery cycle life is defined as the number of complete charge - discharge cycles a battery can perform before its nominal capacity falls below Sponsors 80% of its initial rated capacity. Lifetimes of 500 to 1200 cycles are typical. The actual ageing process results in a gradual reduction in capacity over time. When a cell reaches its specified lifetime it does not stop working suddenly. The ageing process continues at the same rate as before so that a cell whose capacity had fallen to 80% after 1000 cycles will probably continue working to perhaps 2000 cycles when its effective capacity will have fallen to 60% of its original capacity.