There's an Intruder at Your Project – Vapor Intrusion: How It Can Affect
Total Page:16
File Type:pdf, Size:1020Kb
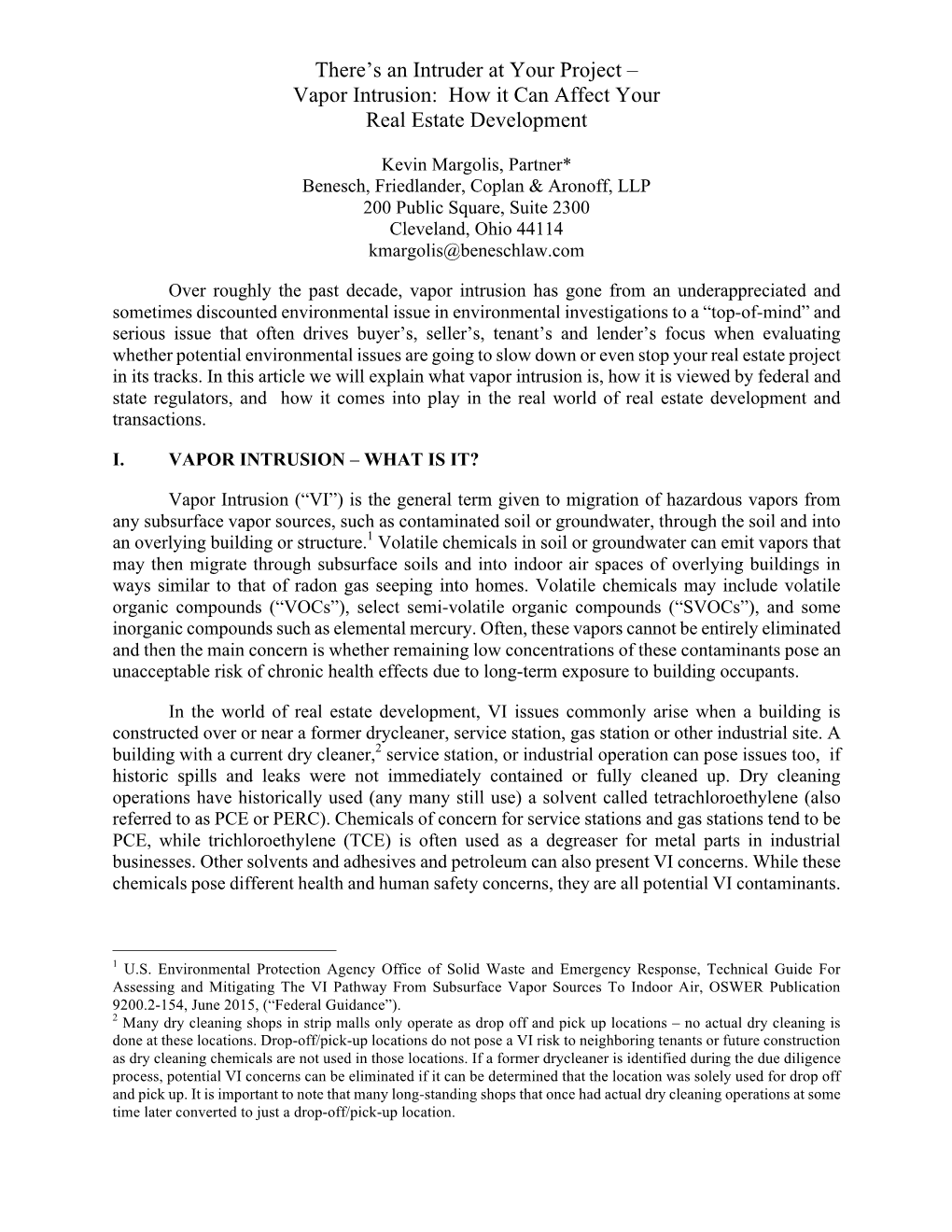
Load more
Recommended publications
-
Evaluating Vapor Intrusion Pathways
Evaluating Vapor Intrusion Pathways Guidance for ATSDR’s Division of Community Health Investigations October 31, 2016 Contents Acronym List ........................................................................................................................................................................... 1 Introduction ........................................................................................................................................................................... 2 What are the potential health risks from the vapor intrusion pathway? ............................................................................... 2 When should a vapor intrusion pathway be evaluated? ........................................................................................................ 3 Why is it so difficult to assess the public health hazard posed by the vapor intrusion pathway? .......................................... 3 What is the best approach for a public health evaluation of the vapor intrusion pathway? ................................................. 5 Public health evaluation.......................................................................................................................................................... 5 Vapor intrusion evaluation process outline ............................................................................................................................ 8 References… …...................................................................................................................................................................... -
EPA's Vapor Intrusion Database: Evaluation and Characterization of Attenuation, Factors for Chlorinated Volatile Organic Compo
EPA 530-R-10-002 March 16, 2012 EPA’s Vapor Intrusion Database: Evaluation and Characterization of Attenuation Factors for Chlorinated Volatile Organic Compounds and Residential Buildings Office of Solid Waste and Emergency Response U.S. Environmental Protection Agency Washington, DC 20460 March 16, 2012 EPA’s Vapor Intrusion Database [This page intentionally left blank.] ii March 16, 2012 EPA’s Vapor Intrusion Database Disclaimer This document presents technical information regarding the concentrations of chlorinated volatile organic compounds (VOCs) in and underneath North American buildings that have been investigated for potential vapor intrusion. This document does not confer legal rights, impose legal obligations, or implement any statutory or regulatory provisions. This document does not change or substitute for any statutory or regulatory provisions. U.S. Environmental Protection Agency (EPA) personnel (and others) are free to use and accept other technically sound information, either on their own initiative, or at the suggestion of responsible parties or other interested parties. Interested parties are free to raise questions and objections about the appropriateness of the information presented in this document. Finally, this is a living document and may be updated periodically. Mention of trade names or commercial products does not constitute endorsement or recommendation for use. iii March 16, 2012 EPA’s Vapor Intrusion Database Authors and Contributors The U.S. Environmental Protection Agency (EPA), Office of Solid Waste and Emergency Response (OSWER), Washington, DC, was responsible for the preparation of EPA’s Vapor Intrusion Database: Evaluation and Characterization of Attenuation Factors for Chlorinated Volatile Organic Compounds and Residential Building. Dr. Helen E. -
Understanding Vapor Intrusion Regulation and the Potential for Litigation
ARTICLE The ‘Volatile’ World of Vapor Intrusion: Understanding Vapor Intrusion Regulation and the Potential for Litigation CHRISTINE G. ROLPH* VALERIE E. TORRES** JOHN W. EVERETT*** I. INTRODUCTION Vapor intrusion is breathing new life into decades-old controversies and regulatory actions. State environmental agencies in recent years have reopened hundreds of sites for vapor intrusion assessment that were previously subject to final closure.1 Meanwhile, at least one court has permitted plaintiffs to pursue an action for alleged damage due to vapor intrusion even when an action arising from the same soil and groundwater contamination was settled more than twenty-five years prior.2 Vapor intrusion has become a hot topic amongst legal practitioners, as well as a significant concern for the regulated community. The attention and concern arises largely from the uncertainty surrounding vapor intrusion—an uncertainty that * Christine G. Rolph is a partner in the Environment, Land and Resources Department of Latham & Watkins LLP in Washington, D.C. ** Valerie E. Torres is counsel in the Environment, Land and Resources Department of Latham & Watkins LLP in San Diego, California. *** John Everett, a former associate at Latham & Watkins in San Diego, is currently Deputy Attorney General in the Environment Section of the Office of the California Attorney General. The opinions expressed in the article are his and do not necessarily reflect those of the Office of the California Attorney General. 1. See INTERSTATE TECH. & REGULATORY COUNCIL, ITRC STATE SURVEY: RE- VISITING “CLOSED” SITE FOR VAPOR INTRUSION CONCERNS (Oct. 2007), available at http://www.itrcweb.org/vaporintrusionresources/ReOpeningCasesVIStateSurvey Oct07sh.pdf. 2. See Aiken v. -
Vapor Intrusion Issues at Brownfield Sites
Background Document Vapor Intrusion Issues at Brownfield Sites December 2003 Prepared by The Interstate Technology & Regulatory Council Brownfields Team ABOUT ITRC Established in 1995, the Interstate Technology & Regulatory Council (ITRC) is a state-led, national coalition of personnel from the environmental regulatory agencies of some 40 states and the District of Columbia; three federal agencies; tribes; and public and industry stakeholders. The organization is devoted to reducing barriers to, and speeding interstate deployment of, better, more cost-effective, innovative environmental techniques. ITRC operates as a committee of the Environmental Research Institute of the States (ERIS), a Section 501(c)(3) public charity that supports the Environmental Council of the States (ECOS) through its educational and research activities aimed at improving the environment in the United States and providing a forum for state environmental policy makers. More information about ITRC and its available products and services can be found on the Internet at http://www.itrcweb.org. DISCLAIMER This document is designed to help regulators and others develop a consistent approach to their evaluation, regulatory approval, and deployment of specific technologies at specific sites. Although the information in this document is believed to be reliable and accurate, this document and all material set forth herein are provided without warranties of any kind, either express or implied, including but not limited to warranties of the accuracy or completeness of information contained in the document. The technical implications of any information or guidance contained in this document may vary widely based on the specific facts involved and should not be used as a substitute for consultation with professional and competent advisors. -
Technical Guide for Addressing Petroleum Vapor Intrusion at Leaking Underground Storage Tank Sites
EPA 510-R-15-001 Technical Guide For Addressing Petroleum Vapor Intrusion At Leaking Underground Storage Tank Sites U.S. Environmental Protection Agency Office of Underground Storage Tanks Washington, D.C. June 2015 Contents Recommendations .......................................................................................................................... 1 Background ................................................................................................................................. 1 Overview Of Petroleum Vapor Intrusion (PVI) ........................................................................... 2 Scope And Applicability .............................................................................................................. 3 Recommended Actions For Addressing PVI ............................................................................... 3 Supporting Technical Information ................................................................................................ 10 1. Petroleum Vapor Intrusion (PVI) ....................................................................................... 11 2. Typical PVI Scenarios ......................................................................................................... 33 3. Site Characterization And Conceptual Site Model (CSM) ................................................. 39 4. Lateral Inclusion Zone ....................................................................................................... 44 5. Vertical Separation Distance ............................................................................................ -
Group Says State Hides Oil-Spill Info
Daily News January 25, 2006 GROUP SAYS STATE HIDES OIL-SPILL INFO GREENPOINT residents and environmental activists charged yesterday that the state is hiding critical information about potential cancer-causing gases generated by a massive underground oil spill. The latest salvo in the long-running case came just before tonight's community meeting where state Department of Environmental Conservation officials are expected to update residents about the cleanup of the decades-old 17-million-gallon plume. "We detected alarmingly high levels of [methane gas and benzene vapors] in July," said Riverkeeper investigator Basil Seggos. "In the right concentrations, methane gas is explosive and benzene vapors can cause cancer." State officials insisted tests conducted for them came up clean. Seggos charged the DEC has done little to assess the gas and vapor levels, and has not shared what health information it has with the public. Believing the state was not doing its job, Riverkeeper filed a federal lawsuit against ExxonMobil in 2004 to force the oil giant to mop up the plume, which was discovered in 1978. "Nobody knows what they've found," said JoAnn McErlean, a Greenpoint plaintiff represented in a second suit backed by environmental crusader Erin Brockovich. No cancer clusters have been documented in Greenpoint, but McErlean said when she and her neighbors compiled their medical histories for the lawsuit, she learned of unusual cancer cases and women with reproductive problems. "People are upset at the way DEC has approached this job," said state Assemblyman Joseph Lentol (D-Greenpoint). "We'd been told that they were getting the oil out of the ground as quickly as possible," he said. -
Brownfields Technology Primer: Vapor Intrusion Considerations For
Brownfields Technology Primer: Vapor Intrusion Considerations for Redevelopment Solid Waste and EPA 542-R-08-001 Emergency Response March 2008 (5203P) www.epa.gov/brownfields www.brownfieldstsc.org Brownfields Technology Primer: Vapor Intrusion Considerations for Redevelopment U.S. Environmental Protection Agency Office of Solid Waste and Emergency Response Brownfields and Land Revitalization Technology Support Center Washington, DC 20460 BROWNFIELDS TECHNOLOGY PRIMER VAPOR INTRUSION CONSIDERATIONS FOR REDEVELOPMENT Notice and Disclaimer Preparation of this document was funded by the U.S. Environmental Protection Agency (EPA) under Contract No. 68-W-02-034. It was prepared for EPA’s Brownfields and Land Revitalization Technology Support Center (BTSC), which responds to requests from EPA regional offices, states, localities, and tribes to provide support for brownfield sites related to the use of technology for site investigations and cleanups. The document is intended as a primer only, not guidance. EPA recommends that users refer to existing guidance documents (some references are provided herein) regarding vapor intrusion characterization and mitigation techniques. The primer was subjected to the Agency’s administrative and expert review and was approved for publication as an EPA document. Mention of trade names or commercial products does not constitute an endorsement or recommendation for use. An electronic version of the primer can be downloaded from BTSC’s website at http://www.brownfieldstsc.org. A limited number of hard copies are available free of charge by mail from EPA’s National Service Center for Environmental Publications at the following address (please allow 4 to 6 weeks for delivery): EPA/National Service Center for Environmental Publications P.O. -
Guidance for Communicating Vapor Intrusion at Environmental Restoration Sites
Naval Facilities Engineering Command And Navy and Marine Corps Public Health Center Guidance for Communicating Vapor Intrusion at Environmental Restoration Sites October 2014 Distribution Statement A: Approved for public release; Distribution is unlimited. This page is intentionally left blank CONTENTS Acronyms iv 1. Purpose/Statement of Intent 1 2. Background 1 3. Objectives of Vapor Intrusion Communication 2 4. Audience and Stakeholders 2 5. Key Messages 3 6. Communication Strategy 4 7. Considerations for Residential Buildings 7 8. References and Resources 8 APPENDICES A Examples - Fact Sheets and Notification Letters B Examples - Open House Posters C Frequently Asked Questions (FAQs) iii Acronyms and Abbreviations CERCLA Comprehensive Environmental Response, Compensation, and Liability Act CO Commanding Officer DON Department of the Navy ERP Environmental Restoration Program FAQs Frequently asked questions and answers NAVFAC Naval Facilities Engineering Command NIRIS Navy Installation Restoration Information Solution NMCPHC Navy and Marine Corps Public Health Center OSHA Occupational Safety and Health Administration RPM Remedial Project Manager PPV Public Private Venture USEPA U.S. Environmental Protection Agency VI Vapor Intrusion VOC Volatile Organic Compound iv 1. PURPOSE/STATEMENT OF INTENT This guidance, prepared by Naval Facilities Engineering Command (NAVFAC) and Navy and Marine Corps Public Health Center (NMCPHC), is designed to provide Navy Environmental Restoration Program (ERP) Remedial Project Managers (RPMs) with recommendations for notifying and relaying information regarding vapor intrusion (VI) investigations to Base personnel and potentially affected occupants of industrial, office, or residential buildings. Ensuring a safe work environment for Base employees is a top priority for Department of the Navy (DON) officials. RPMs should use this guidance to assist project teams and Base officials with communicating plans and results of VI investigations and potential future actions in a timely and responsible manner. -
2008 More Tests on Toxic Underground Plume in Southern Tier Town
Associated Press Financial Wire January 11, 2008 More tests on toxic underground plume in Southern Tier town State health and environmental officials will conduct another round of testing for signs of hazardous chemicals flowing in the ground below homes in Endicott. The area includes more than 12 blocks of residential and commercial property near a former Canada Dry bottling plant. Officials declined Thursday to say how many structures would be tested, or when, until residents in the area are notified. Letters were mailed from Albany on Wednesday, said Lori O'Connell, a spokeswoman for the state Department of Environmental Conservation. A public meeting is scheduled for Jan. 23 at Union-Endicott High School to discuss the plans, she said. Samples collected outside homes last summer gave scientists a more complete picture of a subterranean plume of trichloroethylene (TCE) in the ground and penetrating into homes as a toxic vapor. To date, TCE vapors have affected more than 700 properties, mostly in Endicott and the town of Union near a former IBM Corp. Click for Enhanced Coverage Linking Searchesmanufacturing site. The vapors were first detected in 2003. Exposure to TCE, a metal cleaning solvent, has been linked to illnesses ranging from kidney cancer to brain damage. Collecting samples inside and under homes this winter will determine whether the vapors are moving through foundations and collecting in buildings through a process called vapor intrusion. Scientists will use the data to "determine whether actions are needed to address exposure," according to the mailing to residents. Last week, a group of 94 residents and businesses filed a lawsuit against IBM over more than $100 million in claims they say are linked to the TCE pollution from the company's former microelectronics plant in Endicott. -
Oswer Technical Guide for Assessing and Mitigating the Vapor Intrusion Pathway from Subsurface Vapor Sources to Indoor Air
OSWER Publication 9200.2-154 OSWER TECHNICAL GUIDE FOR ASSESSING AND MITIGATING THE VAPOR INTRUSION PATHWAY FROM SUBSURFACE VAPOR SOURCES TO INDOOR AIR U.S. Environmental Protection Agency Office of Solid Waste and Emergency Response June 2015 June 2015 Assessing and Mitigating the Vapor Intrusion Pathway from Subsurface Vapor Sources to Indoor Air DISCLAIMER This document presents current technical recommendations of the U.S. Environmental Protection Agency (EPA) based on our current understanding of vapor intrusion into indoor air from subsurface vapor sources. This guidance document does not impose any requirements or obligations on the EPA, the states or tribal governments, or the regulated community. Rather, the sources of authority and requirements for addressing subsurface vapor intrusion are the relevant statutes and regulations. Decisions regarding a particular situation should be made based upon statutory and regulatory authority. EPA decision-makers retain the discretion to adopt or approve approaches on a case-by-case basis that differ from this guidance document, where appropriate, as long as the administrative record supporting its decision provides an adequate basis and reasoned explanation for doing so. i June 2015 Assessing and Mitigating the Vapor Intrusion Pathway from Subsurface Vapor Sources to Indoor Air TABLE OF CONTENTS DISCLAIMER........................................................................................................................... i TABLE OF CONTENTS ......................................................................................................... -
Virginia Unified Risk Assessment Model VURAM User Guide
Virginia Unified Risk Assessment Model – VURAM User Guide For Risk Assessors Updated October 2018 Table of Contents I. NOTICE .......................................................................................................................................................5 II. Disclaimer..................................................................................................................................................5 III. Acknowledgements..................................................................................................................................5 IV. Contacts Table .........................................................................................................................................5 1.0 Virginia Unified Risk Assessment Model (VURAM).................................................................................6 1.1 Software Requirements ......................................................................................................................6 1.2 User Guide ..........................................................................................................................................6 1.3 Recommended Use.............................................................................................................................7 1.4 Model Limitations ...............................................................................................................................7 1.5 Prerequisites for Computation ...........................................................................................................8 -
Vapor Intrusion Technical Guidance
NEW JERSEY DEPARTMENT OF ENVIRONMENTAL PROTECTION SITE REMEDIATION AND WASTE MANAGEMENT PROGRAM VAPOR INTRUSION TECHNICAL GUIDANCE Indoor Air Soil Gas Ground Water May 2021 Version 5.0 New Jersey Department of Environmental Protection Site Remediation and Waste Management Program Vapor Intrusion Technical Guidance May 2021 Version 5.0 2 ACKNOWLEDGEMENTS The New Jersey Department of Environmental Protection (Department) Vapor Intrusion Technical Guidance (Version 4.1) document was previously prepared by the Department/Stakeholder Vapor Intrusion Guidance Committee in cooperation with the Department Vapor Intrusion Committee. The updated Vapor Intrusion Technical Guidance (Version 5.0) was completed by the Department with assistance from the Stakeholder Vapor Intrusion Guidance Committee. Department/Stakeholder Vapor Intrusion Guidance Committee Carey Compton, Chair, New Jersey Department of Environmental Protection Nicole Kalaigian, New Jersey Department of Environmental Protection John Boyer, New Jersey Department of Environmental Protection Retiree Ken Bird, Woodard & Curran Consultants Brian Blum, Langan Consultants Scott Drew, Geosyntec Consultants John Engdahl, Speedway Erica Snyder, New Jersey Department of Environmental Protection Diane Groth, New Jersey Department of Environmental Protection Retiree Andrew Sites, New Jersey Department of Environmental Protection Retiree Peter Sorge, JM Sorge, Inc., Environmental Consultants Chad VanSciver, New Jersey Department of Environmental Protection Additional Technical Assistance: Gunnar