Strength Properties of Light Weight Aggregate
Total Page:16
File Type:pdf, Size:1020Kb
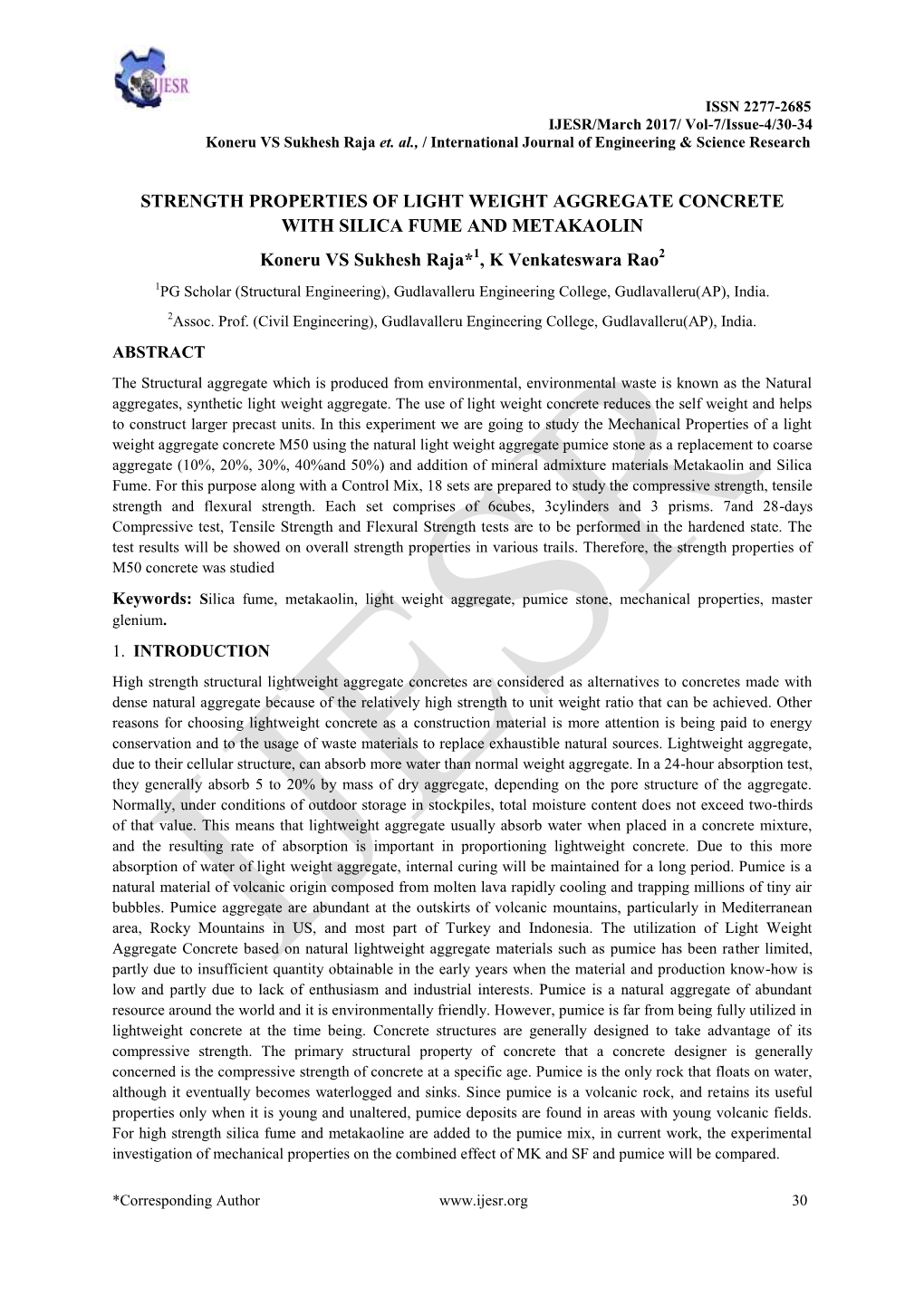
Load more
Recommended publications
-
How to Make Concrete More Sustainable Harald Justnes1
Journal of Advanced Concrete Technology Vol. 13, 147-154, March 2015 / Copyright © 2015 Japan Concrete Institute 147 Scientific paper How to Make Concrete More Sustainable Harald Justnes1 A selected paper of ICCS13, Tokyo 2013. Received 12 November 2013, accepted 16 February 2015 doi:10.3151/jact.13.147 Abstract Production of cement is ranking 3rd in causes of man-made carbon dioxide emissions world-wide. Thus, in order to make concrete more sustainable one may work along one or more of the following routes; 1) Replacing cement in con- crete with larger amounts of supplementary cementing materials (SCMs) than usual, 2) Replacing cement in concrete with combinations of SCMs leading to synergic reactions enhancing strength, 3) Producing leaner concrete with less cement per cubic meter utilizing plasticizers and 4) Making concrete with local aggregate susceptible to alkali silica reaction (ASR) by using cement replacements, thus avoiding long transport of non-reactive aggregate. 1 Introduction SCMs, also uncommon ones like calcined marl 2. Replacing cement in concrete with combinations of The cement industry world-wide is calculated to bring SCMs leading to synergic reactions enhancing about 5-8% of the total global anthropogenic carbon strength dioxide (CO2) emissions. The general estimate is about 3. Producing leaner concrete with less cement per cubic 1 tonne of CO2 emission per tonne clinker produced, if meter utilizing plasticizers. fossil fuel is used and no measures are taken to reduce it. 4. Making concrete with local aggregate susceptible to The 3rd rank is not because cement is such a bad mate- alkali silica reaction (ASR) by using cement re- rial with respect to CO2 emissions, but owing to the fact placements, thus avoiding long transport of non- that it is so widely used to construct the infrastructure reactive aggregate and buildings of modern society as we know it. -
Silica Fume and Metakaolin As Supplementary Cementing Materials- a Review
ISSN(Online): 2319-8753 ISSN (Print): 2347-6710 International Journal of Innovative Research in Science, Engineering and Technology (A High Impact Factor, Monthly, Peer Reviewed Journal) Visit: www.ijirset.com Vol. 6, Issue 10, October 2017 Silica Fume and Metakaolin as Supplementary Cementing Materials- A Review Syed Abuthahir 1, Nirmalkumar2 P.G. Student, Department of Civil Engineering, Kongu Engineering College, Perundurai, Erode, India1 Professor, Department of Civil Engineering, Kongu Engineering College, Perundurai, Erode, India2 ABSTRACT:The replacement of cement by various mineral admixtures as supplementary cementing materials for concrete has gained a global attention in recent years. This replacement becomes efficient not only by increasing the strength and durability of the concrete but also reduces the usage of the ordinary cement thereby curtailing the environmental hazardous due to cement manufacturing industries. This paper reviews the work carried out on the use of silica fume (SF) and Metakaolin (MK) as supplementary cementing materials as a partial replacement for cement. The literature demonstrates that both SF and MK are effective and causes significant improvement in various properties of the concrete in both fresh and harden state. KEYWORDS: Metakaolin, Silica Fume, Compressive Strength, Durability Properties. I.INTRODUCTION Major of the construction company relies on the concrete. Cement is major constituent of concrete. The annual global production of ordinary portland cement is about 3 Gt. Cement becomes a dominant binder due to its versatility, durability, and its demand increases dramatically. Even though it is a vital material, it production directly affects the environment by releasing 0.87t of carbon dioxide for every tonne of cement produced. -
Item 421 Hydraulic Cement Concrete
421 Item 421 Hydraulic Cement Concrete 1. DESCRIPTION Furnish hydraulic cement concrete for concrete pavements, concrete structures, and other concrete construction. 2. MATERIALS Use materials from prequalified sources listed on the Department website. Provide coarse and fine aggregates from sources listed in the Department’s Concrete Rated Source Quality Catalog (CRSQC). Use materials from non-listed sources only when tested and approved by the Engineer before use. Allow 30 calendar days for the Engineer to sample, test, and report results for non-listed sources. Do not combine approved material with unapproved material. 2.1. Cement. Furnish cement conforming to DMS-4600, “Hydraulic Cement.” 2.2. Supplementary Cementing Materials (SCM). Fly Ash. Furnish fly ash, ultra-fine fly ash (UFFA), and modified Class F fly ash (MFFA) conforming to DMS-4610, “Fly Ash.” Slag Cement. Furnish Slag Cement conforming to DMS-4620, “Slag Cement.” Silica Fume. Furnish silica fume conforming to DMS-4630, “Silica Fume.” Metakaolin. Furnish metakaolin conforming to DMS-4635, “Metakaolin.” 2.3. Cementitious Material. Cementitious materials are the cement and supplementary cementing materials used in concrete. 2.4. Chemical Admixtures. Furnish admixtures conforming to DMS-4640, “Chemical Admixtures for Concrete.” 2.5. Water. Furnish mixing and curing water that is free from oils, acids, organic matter, or other deleterious substances. Water from municipal supplies approved by the Texas Department of Health will not require testing. Provide test reports showing compliance with Table 1 before use when using water from other sources. Water that is a blend of concrete wash water and other acceptable water sources, certified by the concrete producer as complying with the requirements of both Table 1 and Table 2, may be used as mix water. -
Mechanical Properties of Glass Powder and Metakaolin in Concrete
ISSN 2321 3361 © 2020 IJESC Research Article Volume 10 Issue No.8 Mechanical Properties of Glass Powder and Metakaolin in Concrete Mukund Kumar1, Ajay Kumar Singh2 M.Tech Scholar1, Assistant Professor2 Department of Civil Engineering SSTC-SSGI, Bhilai, India Abstract: The production of Portland cement releases significant amount of greenhouse gas, One ton of cement clinker production releases approximately one ton of carbon dioxide. Today many researches are going to utilize mineral admixtures for the replacement of cement, fine aggregate and coarse aggregate using industrial waste like Metakaolin, Fly ash, GGBS, copper sag and glass. Glass has a unique property; it can be recycled many times without changing its chemical properties. Million tones of glass discarded every year from houses and industries and for dumping they need grounds. The addition of glass powder and metakaolin increases the durability properties of concrete. The use of metakaolin and glass powder will give us advantage to save natural resources and in addition to that it will be economical to use it in concrete. In this research work the metakaolin was used to replace the cement in 10%, 20% and 30% and glass powder was used to replace the fine aggregate in 10%, 20%, 30% and 40%. The compressive strength test was carried out on specimen for 7 days and 28 days, compressive strength, split tensile strength and durability test for 28 days. Keywords: Glass Powder, Metakaolin, Compressive Strength, Split Tensile Strength, Flexural Strength, Durability Test. I. INTRODUCTION used. Sand passing through IS 4.75mm Sieve was used for casting all the specimens. The curosity of the concrete researchers in using waste or recycled materials in concrete is increasing because of the Corse Aggregate: emphasis placed on sustainable construction. -
Selecting Measures to Prevent Deleterious Alkali-Silica Reaction in Concrete
Selecting Measures to Prevent Deleterious Alkali-Silica Reaction in Concrete Rationale for the AASHTO PP65 Prescriptive Approach October 2012 Notice This document is disseminated under the sponsorship of the U.S. Department of Transportation in the interest of information exchange. The U.S. Government assumes no liability for the use of the information contained in this document. The U.S. Government does not endorse products or manufacturers. Trademarks or manufacturers' names appear in this report only because they are considered essential to the objective of the document. Quality Assurance Statement The Federal Highway Administration (FHWA) provides high-quality information to serve Government, industry, and the public in a manner that promotes public understanding. Standards and policies are used to ensure and maximize the quality, objectivity, utility, and integrity of its information. FHWA periodically reviews quality issues and adjusts its programs and processes to ensure continuous quality improvement. 1. Report No. 2. Government Accession No. 3. Recipient’s Catalog No. FHWA-HIF-13-002 4. Title and Subtitle 5. Report Date October 2012 Selecting Measures to Prevent Deleterious Alkali-Silica Reaction in Concrete: Rationale for the AASHTO PP65 Prescriptive Approach 6. Performing Organization Code 7. Author(s) 8. Performing Organization Report No. Thomas, M.D.A., Fournier, B., Folliard, K.J. 9. Performing Organization Name and Address 10. Work Unit No. The Transtec Group, Inc. 6111 Balcones Drive Austin, TX 78731 11. Contract or Grant No. DTFH61-06-D-00035 12. Sponsoring Agency Name and Address 13. Type of Report and Period Covered Office of Pavement Technology Federal Highway Administration 1200 New Jersey Avenue, DE Washington, DC 20590 14. -
Structural Behavior of Metakaolin Infused Concrete Structure
Nigerian Journal of Technology (NIJOTECH) Vol. 36, No. 2, April 2017, pp. 331 – 338 Copyright© Faculty of Engineering, University of Nigeria, Nsukka, Print ISSN: 0331-8443, Electronic ISSN: 2467-8821 www.nijotech.com http://dx.doi.org/10.4314/njt.v36i2.2 STRUCTURAL BEHAVIOR OF METAKAOLIN INFUSED CONCRETE STRUCTURE J. O. Akinyele1,*, S. O. Odunfa2, A. A. Famoye3 and S. I. Kuye4 1,2,3 DEPARTMENT OF CIVIL ENGINEERING, FEDERAL UNIVERSITY OF AGRICULTURE, ABEOKUTA, OGUN STATE, NIGERIA 4 DEPT. OF MECHANICAL ENGINEERING, FEDERAL UNIVERSITY OF AGRICULTURE, ABEOKUTA, OGUN STATE NIGERIA E-mail addresses: 1 [email protected], 2 [email protected], 3 [email protected], 4 [email protected] ABSTRACT This work researched into the use of metakaolin as a partial substitute for cement in concrete, metakaolin was obtained by the calcination of kaolin clay to about 700 0C Cement was replaced with the metakaolin at 0, 5, 10, 15, 20, 25, 30, and 35% at water cement ratio of 0.5. Tests such as chemical analysis, compressive strength, flexural or modulus of rupture and bond strength were carried out on the concrete samples. Chemical analysis results showed that the metakaolin is a class “N” pozzolan, while the mechanical test showed that the strength of concrete increased from 5% to 20% replacement, and the strength peaked at 20%, but decreased above this value; concrete made with metakaolin performed better than the control sample at all the percentage replacements used in this work. Keywords: Metakaolin, Calcination, Pozzolan, Chemical test, Mechanical test 1. INTRODUCTION materials to produce materials with higher strength, The continuous increase in the cost of cement and the denser microstructure, lower porosity, higher resistance effect of air pollution being experienced during the to ions with improved durability properties [3]. -
Eco-Efficient Self-Compacting Concrete with Reduced Portland Cement Content and High Volume of Fly Ash and Metakaolin
Eco-efficient self-compacting concrete with reduced Portland cement content and high volume of fly ash and metakaolin Marcos A. S. Anjos 1a , Aires Camões 2b e Carlos Jesus 2c 1 Department of Building Technology, Instituto Federal de Educação, Ciência e Tecnologia do Rio Grande do Norte, Campus-Natal, Tirol, P – 59056-000 Natal, RN, Brazil 2C-TAC, Department of Civil Engineering, University of Minho, Campus de Azurém, 4800-058 Guimarães, Portugal [email protected] ; [email protected]; [email protected] keywords: Eco-efficient concrete, high-volume fly ash and metakaolin. Abstract. The eco-efficient, self-compacting concrete (SCC) production, containing low levels of cement in its formulation, shall contribute for the constructions' sustainability due to the decrease in Portland cement use, to the use of industrial residue, for beyond the minimization of the energy needed for its placement and compaction. In this context, the present paper intends to assess the viability of SCC production with low cement levels by determining the fresh and hardened properties of concrete containing high levels of fly ash (FA) and also metakaolin (MK). Hence, 6 different concrete formulations were produced and tested: two reference concretes made with 300 and 500 kg/m 3 of cement; the others were produced in order to evaluate the effects of high replacement levels of cement. Cement replacement by FA of 60% and by 50% of FA plus 20% of MK were tested and the addition of hydrated lime in these two types of concrete were also studied. To evaluate the self-compacting ability slump flow test, T500 , J-ring, V-funnel and L-box were performed. -
Study on Mechanical Properties of Metakaolin-Based Concretes and Corrosion of Carbon Steel Reinforcement in 3.5% Nacl
Int. J. Electrochem. Sci., 15 (2020) 2883 – 2893, doi: 10.20964/2020.04.25 International Journal of ELECTROCHEMICAL SCIENCE www.electrochemsci.org Study on Mechanical Properties of Metakaolin-Based Concretes and Corrosion of Carbon Steel Reinforcement in 3.5% NaCl Jian Zhang, Jin Yang*, Zhuoxuan Ying Jiyang College, Zhejiang Agricultural and Forestry University, Zhuji 311800, China *E-mail: [email protected] Received: 30 November 2019 / Accepted: 23 January 2020 / Published: 10 March 2020 One of the techniques to improve the concrete durability is to use cement materials blended with silica fume, slag and fly ash. The use of calcined clay cement in the metakaolin form as a pozzolan for mortar and concrete has received remarkable interest in recent years. Here, in this study, corrosion behavior and mechanical property of carbon steel rebar in metakaolin cement-based concretes were investigated. To evaluate the effect of high-reactivity metakaolin in the corrosion resistance of the ordinary Portland cement (OPC) concrete, 5 wt%, 10 wt%, 15 wt% and 20 wt% metakaolin replacement levels were done in concrete production. Corrosion rate, electrochemical mass loss, compressive strength, tensile strengths, open circuit potential, and electrochemical impedance spectroscopy (EIS) of the samples were studied and discussed. The electrochemical mass loss of concrete samples revealed that 15 wt% metakaolin sample had smaller mass losses which exhibited an improvement in anticorrosive properties that had led to better corrosion behavior of the carbon steel rebar. The mechanical results of concrete samples indicated a gradually increase in compressive and tensile strengths with the increase in the cement blended with metakaolin. Furthermore, the EIS findings showed that 15 wt% metakaolin sample indicated a higher value of passive film resistance compared to other samples, indicating that more enhancement of corrosion resistance on the surface of the carbon steel rebar. -
Alkali-Activated Metakaolin and Fly Ash As Unfired Ceramic Bonding
minerals Article Alkali-Activated Metakaolin and Fly Ash as Unfired Ceramic Bonding Systems Jozef Vlˇcek 1,2,*, Michaela Topinková 1,2 , Miroslava Klárová 1,2, Petra Maierová 1,2 , Hana Ovˇcaˇcíková 1,2,* , Vlastimil Matˇejka 3 , Alexandr Martaus 1 and Veronika Blah ˚ušková 1 1 Institute of Environmental Technology, CEET, VSB—Technical University of Ostrava, 738 01 Ostrava, Czech Republic; [email protected] (M.T.); [email protected] (M.K.); [email protected] (P.M.); [email protected] (A.M.); [email protected] (V.B.) 2 Department of Thermal Engineering, Faculty of Materials Science and Technology, VSB—Technical University of Ostrava, 708 00 Ostrava, Czech Republic 3 Department of Chemistry, Faculty of Materials Science and Technology, VSB—Technical University of Ostrava, 708 00 Ostrava, Czech Republic; [email protected] * Correspondence: [email protected] (J.V.); [email protected] (H.O.); Tel.: +420-597-321-527 (J.V.) Abstract: Metakaolin (MK) prepared by the calcination of kaolin at 550 ◦C and fly ash (FA) from the combustion of black coal in a granulating boiler were used to prepare unfired ceramic bonding systems via the alkali activation process. A long-term stability of the mechanical properties of the prepared samples similar to the unfired ceramic systems was observed. The optimal metakaolin and fly ash ratio, the type of the activator (NaOH or water glass) and its concentration were evaluated after the hydration in: a) laboratory conditions; b) hydration box; and c) under the hydrothermal activation. Raw materials and the samples prepared by alkali activation process were characterized by XRD, XRF, TG/DTA, and FTIR methods. -
Mechanical Behaviour of High Metakaolin Lightweight Aggregate Concrete
Computational Methods and Experimental Measurements XV 85 Mechanical behaviour of high metakaolin lightweight aggregate concrete A. Al-Sibahy & R. Edwards Department of Mechanical, Aerospace and Civil Engineering, University of Manchester, UK Abstract The work described in this paper forms part of a much larger investigation of the behaviour of a new developed type of lightweight aggregate concrete which would be suitable for use as load bearing concrete masonry units. The experimental work investigated the effect of high metakaolin (MK) content on the mechanical behaviour of newly modified lightweight aggregate concrete. 15% metakaolin and waste glass were used as a partial replacement for both ordinary Portland cement and natural sand. A medium grade expanded clay type Techni Clay was used as a coarse aggregate in the concrete mixes. Equal amounts of waste glass with particles sizes of 0.5-1 and 1-2 mm were used throughout this study. Unit weight, compressive and splitting tensile strengths were measured at various ages in accordance with the relevant British/EN standards. Fresh concrete properties were observed to justify the workability aspect. An assessment was carried out to indentify the pozzolanic activity of metakaolin material. The tests results were compared with the obtained results of controlled and lower metakaolin contents concretes which were previously studied. The tests results showed that metakaolin material had an explicit role in improving the strength and unit weight of modified lightweight concrete mixes. Compressive and splitting tensile strengths increase with an increase in the metakaolin content, while a counteractive behaviour was recorded for the unit weight aspect. The metakaolin material showed higher pozzolanic activity which was overcame there duction of compressive strength due to the negative effect of glass aggregate. -
Trends and Developments in Green Cement and Concrete Technology
International Journal of Sustainable Built Environment (2012) 1, 194–216 Gulf Organisation for Research and Development International Journal of Sustainable Built Environment SciVerse ScienceDirect www.sciencedirect.com Review Article Trends and developments in green cement and concrete technology Mohammed S. Imbabi ⇑, Collette Carrigan, Sean McKenna School of Engineering, King’s College, The University of Aberdeen, AB24 3UE Scotland, UK Received 20 February 2013; accepted 13 May 2013 Abstract The cement industry faces a number of challenges that include depleting fossil fuel reserves, scarcity of raw materials, perpetually increasing demand for cements and concretes, growing environmental concerns linked to climate change and an ailing world economy. Every tonne of Ordinary Portland Cement (OPC) that is produced releases on average a similar amount of CO2 into the atmosphere, or in total roughly 6% of all man-made carbon emissions. Improved production methods and formulations that reduce or eliminate CO2 emissions from the cement manufacturing process are thus high on the agenda. Emission reduction is also needed to counter the impacts on product cost of new regulations, green taxes and escalating fuel prices. In this regard, locally available minerals, recycled materials and (industry, agriculture and domestic) waste may be suitable for blending with OPC as substitute, or in some cases replacement, bind- ers. Fly ash, Blast furnace slag and silica fumes are three well known examples of cement replacement materials that are in use today that, like OPC, have been documented and validated both in laboratory tests and in practice. The first is a by-product of coal combustion, the second of iron smelting and the third of electric arc furnace production of elemental silicon or ferro silicon alloys. -
2016-UNEP Report-Complete6.Pdf
Eco-efficient cements: Potential, economically viable solutions for a low-CO2, cement- based materials industry Karen L. Scrivener, Vanderley M. John, Ellis M. Gartner Foreword Across the world, countries face ever-increasing demands for resources. Cement-based materials currently represent more than one-third of the total materials extracted from the earth, on average, each year. They are the backbone of our modern built environment, especially in urban areas. Driven by economic development, a growing middle class and rising populations, many countries are facing problems associated with rapid urbanisation, resource depletion and scarcity, and more broadly, unsustain- able patterns of consumption and production. As a key sector contributing to meeting needs for housing, schools, hospitals, public and commercial developments, the building and construction sector is a large con- sumer of materials and natural resources. Cement-based materials will remain essential to supply the growth and improvement of our built environment, particularly by those residing in the developing world. However, with current technology, the much needed increase in cement production will imply a substantial increase in CO2 gen- eration. This is a classical dilemma between the social aspect of sustainability — expansion of the built environment — and the environmental aspect — global warming. This makes it absolutely critical to find solutions and to identify more resource efficient pathways for the growth of our homes, towns, and cities. To help identify some of these new solutions, in 2015 the Sustainable Building and Climate Initiative of the United Nations Environmental Program (UNEP-SBCI) convened an international group of academic and industry experts, from both developed and developing countries, to investigate new, low-CO2, low-cost eco-efficient solutions.