How to Achieve Six Sigma Benefits on a Tight Budget How, Why and When to Apply Basic Analysis Tools to Boost the Bottom Line Table of Contents Introduction
Total Page:16
File Type:pdf, Size:1020Kb
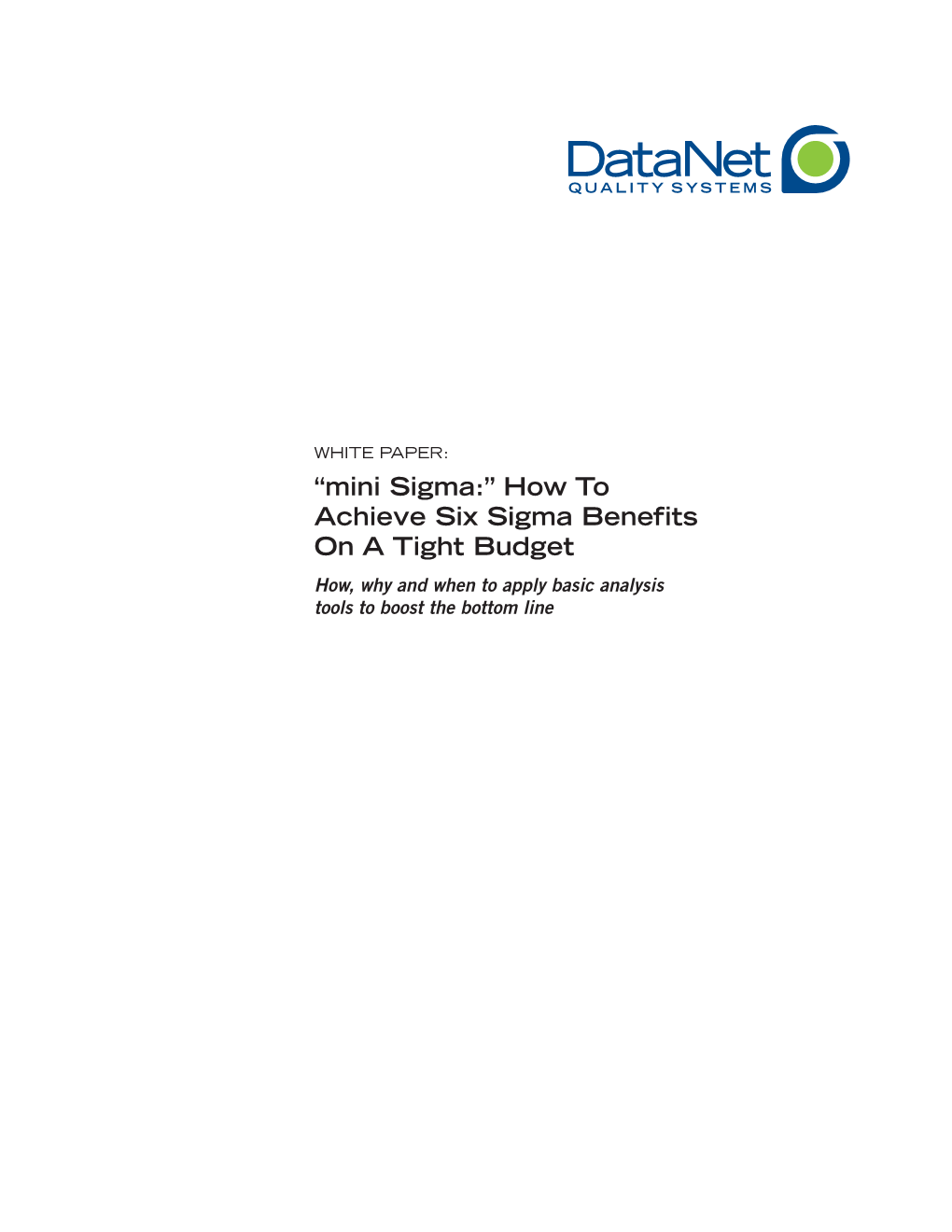
Load more
Recommended publications
-
Seven Basic Tools of Quality Control: the Appropriate Techniques for Solving Quality Problems in the Organizations
UC Santa Barbara UC Santa Barbara Previously Published Works Title Seven Basic Tools of Quality Control: The Appropriate Techniques for Solving Quality Problems in the Organizations Permalink https://escholarship.org/uc/item/2kt3x0th Author Neyestani, Behnam Publication Date 2017-01-03 eScholarship.org Powered by the California Digital Library University of California 1 Seven Basic Tools of Quality Control: The Appropriate Techniques for Solving Quality Problems in the Organizations Behnam Neyestani [email protected] Abstract: Dr. Kaoru Ishikawa was first total quality management guru, who has been associated with the development and advocacy of using the seven quality control (QC) tools in the organizations for problem solving and process improvements. Seven old quality control tools are a set of the QC tools that can be used for improving the performance of the production processes, from the first step of producing a product or service to the last stage of production. So, the general purpose of this paper was to introduce these 7 QC tools. This study found that these tools have the significant roles to monitor, obtain, analyze data for detecting and solving the problems of production processes, in order to facilitate the achievement of performance excellence in the organizations. Keywords: Seven QC Tools; Check Sheet; Histogram; Pareto Analysis; Fishbone Diagram; Scatter Diagram; Flowcharts, and Control Charts. INTRODUCTION There are seven basic quality tools, which can assist an organization for problem solving and process improvements. The first guru who proposed seven basic tools was Dr. Kaoru Ishikawa in 1968, by publishing a book entitled “Gemba no QC Shuho” that was concerned managing quality through techniques and practices for Japanese firms. -
Super Simple Lean Six Sigma Glossary
SUPER SIMPLE LEAN SIX SIGMA GLOSSARY The web is overflowing with Lean Six Sigma resources. Our glossary provides clear, straight-forward language, organized for quick access so you can easily find and understand terms that you’re searching for. For a better understanding of these terms and an advanced understanding of Lean Six Sigma, please check out our Green Belt and Black Belt Training & Certification courses. View online Lean Six Sigma Glossary including visuals & infographics at: https://goleansixsigma.com/glossary/ P300-10 COPYRIGHT 2019 GOLEANSIXSIGMA.COM. ALL RIGHTS RESERVED. 1 5S: 5S is a workplace organization technique composed for five primary phases: Sort, Set In Order, Shine, Standardize, and Sustain. 5 Whys: 5 Whys is a simple but effective method of analyzing and solving problems by asking “why” five times, or as many times as needed in order to move past symptoms and determine root cause. This approach is used in tandem with Cause- and-Effect or Fishbone diagrams. 8 Wastes (aka Muda): The 8 Wastes refer to a list of issues that get in the way of process flow and cause stagnation. The list consists of Defects, Overproduction, Waiting, Non-Utilized Talent, Transportation, Inventory, Motion, and Extra-Processing. The idea of process improvement is to identify and remove all forms of waste from a process in order to increase efficiency, reduce cost and provide customer value. A3: On a literal level, A3 refers to a ledger size (11x17) piece of paper. But in the Lean Six Sigma world, it is a tool to help see the thinking behind the problem-solving. -
Quality Control Tools for Continuous Improvement
QUALITY CONTROL TOOLS FOR CONTINUOUS IMPROVEMENT Yogesh K. More1 , Prof.J.N.Yadav2 1Mechanical Engineering Department, SITRC, Sandip Foundation, Nashik, (India) 2Assist.Prof.Mechanical Engineering Department, SITRC, Sandip Foundation, Nashik, (India) ABSTRACT The main aim of this paper is to understand the basic concept of Quality, Quality Control Tools to improve the quality as well as maintain the quality. Quality Control Tools are very important tool and they are widely used in various industries like Automobile, Production etc. The main seven quality control tools are Check Sheet, Pareto Diagram, Histogram, Cause and effect diagram, Control Chart, Run-Chart and Scatter-Diagram are generally used to improve the quality. All of these tools together can improve process and analysis that can be very helpful for quality improvements. These tools make quality improvements process easier, simple to implement. Keyword: Cause-and-effect diagram, Check Sheet, Control Chart, Histogram, Pareto Diagram, Run-Chart, Scatter-Diagram, Quality, Quality Control Tools. I. INTRODUCTION Quality improvement is a very essential topic in today‟s life. It can be express in many ways. Quality is the features and characteristics of product or services that can full fill the customer requirement or customer need. These can be achieving by using Quality Control Tools. The seven quality control tools are simple tools used for solving the problems related to the quality control. These tools were either developed in Japan or introduced to Japan by the Quality Gurus such as Deming and Juran. Kaoru Ishikawa of Japan had suggested seven simple tools that can be used for documentation, analysis and organization of data needed for quality control. -
Seven Quality Concepts 1
Running head: SEVEN QUALITY CONCEPTS 1 Seven Quality Concepts Benjamin Srock Embry-Riddle Aeronautical University Worldwide Campus Planning, Directing, and Controlling Projects PMGT-614 Jimmie Flores, Ph.D. July 2, 2017 Table of Contents History............................................................................................................................................. 3 Cause and Effect Diagrams ......................................................................................................... 3 Check Sheet ................................................................................................................................. 4 Control Charts.............................................................................................................................. 5 Histograms ................................................................................................................................... 6 Pareto Charts................................................................................................................................ 7 Scatter Plots ................................................................................................................................. 8 Flow Charts................................................................................................................................ 10 References ..................................................................................................................................... 12 SEVEN QUALITY CONCEPTS 3 -
Appendix A: Graphical Tools Available for Quality Improvement Activities May 2014
U.S. Medical Assistance Program Appendix A: Graphical Tools Available for Quality Improvement Activities May 2014 The How-To Guide on Quality Improvement, which is available here, reviews how a clinic can begin quality improvement (QI) activities, the Plan-Do-Study-Act (PDSA) model and where to find indicators and benchmark measures. Graphical tools are extremely useful when undertaking QI projects, both when identifying potential causes of issues and analyzing QI data. There are upwards of 148 quality improvement tools available (Tague Quality Toolbox book), but included below are a handful of basic tools that will help a clinic get started. The tools are organized by purpose: (1) cause analysis and (2) data collection and analysis. Each tool described below has a freely-available downloadable Excel template and a built-in graphical interface that can be customized for individual clinic use. Each Excel template, once downloaded, has an instruction page for how to input data and automatically creates the graph. The Excel templates originate from the American Society for Quality (http://asq.org/learn-about-quality/quality-tools.html) and from the Institute for Healthcare Improvement (http://www.ihi.org/resources/pages/tools/runchart.aspx). Cause Analysis Tools 1. Cause and Effect Diagram/ Fishbone Diagram. The Cause and Effect Diagram (also known as the Fishbone Diagram because of its resemblance to a fish skeleton) is a visual tool used for identifying causes of a problem. Once a problem is described the task is to identify the causes. -
Lean Six Sigma Glossary Brought to You By
Lean Six Sigma Glossary Brought To You By: View Online Lean Six Sigma Glossary Including Visuals & Infographics At: https://goleansixsigma.com/glossary/ The web is overflowing with Lean Six Sigma resources. Our glossary provides clear, straight-forward language, organized for quick access so you can easily find and understand terms that you’re searching for. For a better understanding of these terms and an overview of Lean Six Sigma, check out our Green Belt Training & Certification. P300 COPYRIGHT 2015 GOLEANSIXSIGMA.COM. ALL RIGHTS RESERVED. 1 5 Whys: 5 Whys is a simple but effective method of analyzing and solving problems by asking “why” five times, or as many times as needed in order to move past symptoms and determine root cause. This approach is used in tandem with Cause-and-Effect or Fishbone diagrams. 5S: 5S is a workplace organization technique composed for five primary phases: Sort, Set In Order, Shine, Standardize, and Sustain. 8 Wastes (aka Muda): The 8 Wastes; Defects, Overproduction, Waiting, Non-Utilized Talent, Transportation, Inventory, Motion, and Extra- Processing are a list of the most common reasons for excess cycle time in a process. The idea of process improvement is to identify and remove all forms of waste from a process in order to increase efficiency, reduce cost, and provide customer value. A3: On a literal level, A3 refers to a ledger size piece of paper, but in the Lean world it is a one page project report. This one-pager contains the problem, the analysis of the process, the identified root causes, potential solutions and action plan all on a large sheet of paper. -
Basic Quality Tools 1
Basic Quality Tools 1. Check Sheets 2. Histograms 3. Pareto Charts 4. Cause and Effect Diagram 5. Flowcharts 6. Control Charts 7. Scatter Diagrams 1 Many people only consider 7 basic tools. ASQ does not list Flowcharts as one of the basic tools. However, in order to improve processes and know where to measure, you also need to know how the process is designed, what are the variables that influence the process, and how they interact. 1 Check Sheets • A structured form for collecting and analyzing data. • A generic tool that can be adapted for a wide variety of purposes. • Used by teams to record and compile data • Easy to understand • Builds with each observation based on facts • Forces agreement on each definition • Generates patterns 2 2 When to Use a Check Sheet • When data can be observed and collected repeatedly by the same person or at the same location. • When collecting data on the frequency or patterns of events, problems, defects, defect location, defect causes, etc. • When collecting data from a production process. 3 3 Check Sheet Procedure 1. Decide what event or problem will be observed. Develop operational definitions. 2. Decide when data will be collected and for how long. 3. Design form. Set it up so data can be recorded simply by making check marks or Xs or similar symbols and so that data do not have to be recopied for analysis. 4. Label all spaces on the form. 5. Test the check sheet for a short trial period to be sure it collects the appropriate data and is easy to use. -
Health Care Quality Tools
Health care quality tools Quality tools help people understand and improve processes. There are many different tools, and the skill of quality professionals lies in their ability to take an application from one field or industry and apply it, or adapt it, to specific situations in other fields. If you're new to applying quality techniques in health care, don’t be scared off by the vast number of tools available, or the fact that the tools have roots in fields other than health care. Take a look at the tools listed below, “test-drive” a couple, and soon you’ll begin discovering how to apply them to your unique situation. Seven tools of quality improvement The basic “seven tools of quality improvement” help organisations generate ideas; analyse, develop, and evaluate processes; and collect data. 1. Flowchart/process map—Graphical tools for process understanding. A flowchart creates a map of the steps in a process, and documents the inputs and outputs for each step. 2. Check sheet—A simple data-recording device, custom-designed by the user to allow for easy data collection and interpretation. 3. Cause-effect diagram—A tool for analyzing a process by illustrating the main causes and sub-causes leading to an effect (or symptom). Also called an "Ishikawa diagram" after its inventor, Kaoru Ishikawa, and the "fishbone diagram," because the complete diagram resembles a fish skeleton. 4. Pareto chart—A graphic tool for ranking causes from most significant to least significant. It’s named for economist Vilfredo Pareto, who said most effects come from relatively few causes: that is, 80% of the effects come from 20% of the possible causes. -
Lean Six Sigma Terminology
Lean Six Sigma Terminology 1-Sample Sign Test – This is used to test the probability of a sample median being equal to hypothesized value. 2-Sample t-Test – Used for testing hypothesis about the location two sample means being equal. 5 Why's - The 5 why’s typically refers to the practice of asking, five times, why the failure has occurred in order to get to the root cause/causes of the problem. 5S plus Safety - A process and method for creating and maintaining an organized, clean and high performance workplace. Sort, Straighten, Shine, Standardize, Sustain plus Safety. Accuracy – The average difference observed between a gage under evaluation and a master gage when measuring the same parts over multiple readings. Affinity Diagram – A tool used to organize and present large amounts of data (ideas, issues, solutions, problems) into logical categories based on user perceived relationships and conceptual frame working. Often used in the form of “sticky notes” sent up to the front of the room in brainstorming exercises, and then grouped by facilitator and workers. Final diagram shows relationship between the issue and the category. Then categories are ranked, and duplicate issues are combined to make a simpler overview. Alpha Risk – The probability of accepting the alternate hypothesis Alternative Hypothesis – A tentative explanation which indicates that an event does not follow a chance distribution; a contrast to the null hypothesis. Analysis of Variance (ANOVA) – A statistical method for evaluating the effect that factors have on process mean and for evaluating the differences between the means of two or more normal distributions. -
Poka-Yoke for Mass Customization
LAPPEENRANTA UNIVERSITY OF TECHNOLOGY Faculty of Technology Management Department of Industrial Management POKA-YOKE FOR MASS CUSTOMIZATION The subject of this Master of Science Thesis was approved by the Council of the Faculty of Technology Management on 25th of February 2008 Supervisor: Prof. Janne Huiskonen Instructor: Matti Pilviö, M.Sc.(Eng.) Helsinki, May 9, 2008 Jussi Tapani Sissonen Rantakartanontie 5 C 99 00910 Helsinki ABSTRACT Author: Jussi Tapani Sissonen Subject of the thesis: Poka-yoke for mass customization Department: Department of Industrial Management Date: 2008 Location: Helsinki Master of Science Thesis. Lappeenranta University of Technology. 107 pages, 37 figures, 3 tables and 2 appendices Supervisor: Professor Janne Huiskonen Instructor: M.Sc.(Eng.) Matti Pilviö Keywords: poka-yoke, mistake-proofing, quality improvement, mass customization Producing high quality products and services is one of the key concerns in order to keep up with the competition in the global markets. Companies are putting a great effort on preventing customers having faulty products and services by any means. However, the total elimination of mistakes in manufacturing processes has always been a great challenge for quality management. In this thesis the applicability of poka-yoke methodology in reducing the number of quality failures in the case company has been studied. Poka-yoke stands for the mistake-proofing and is mainly developed for the purpose of eliminating human errors in manufacturing processes. Inspection techniques; judgment, informative and source inspection are in the core of this methodology. Mass customization and large configurability of products leads to situation where the root causes of quality problems may vary a lot. -
Introduction to Statistical Quality Control, 5Th Edition
Unit 6 - Quality Improvement 1 Definitions – Meaning of Quality and Quality Improvement The Eight Dimensions of Quality 1. Performance 2. Reliability 3. Durability 4. Serviceability 5. Aesthetics 6. Features 7. Perceived Quality 8. Conformance to Standards 2 •This is a traditional definition •Quality of design •Quality of conformance 3 This is a modern definition of quality 4 The Transmission Example 5 • The transmission example illustrates the utility of this definition • An equivalent definition is that quality improvement is the elimination of waste. This is useful in service or transactional businesses. 6 Terminology 7 Terminology cont’d • Specifications – Lower specification limit – Upper specification limit – Target or nominal values • Defective or nonconforming product • Defect or nonconformity • Not all products containing a defect are necessarily defective 8 History of Quality Improvement 9 10 11 12 Statistical Methods for Quality Control and Improvement 13 Statistical Methods • Statistical process control (SPC) – Control charts, plus other problem-solving tools – Useful in monitoring processes, reducing variability through elimination of assignable causes – On-line technique • Designed experiments (DOX) – Discovering the key factors that influence process performance – Process optimization – Off-line technique • Acceptance Sampling 14 Walter A. Shewart (1891-1967) • Trained in engineering and physics • Long career at Bell Labs • Developed the first control chart about 1924 15 16 17 A cake-baking process 18 Random Lot sample -
MAGNIFICENT SEVEN" TOOLS of QUALITY Rod Lashley STATKING Consulting, Inc
USING SAS/QC®TO AUTOMATE THE "MAGNIFICENT SEVEN" TOOLS OF QUALITY Rod Lashley STATKING Consulting, Inc. Fairfield, Ohio The goal of statistical process control (SPC) is to We will use data from Benjamin and Shaw (1993) improve process performance through the reduction as an example of the use of check sheets from the of variability. There are seven graphical tools to medical care industry. A medical group submits help the quality practitioner analyze his/her process patient insurance claim forms to a clearinghouse in order to see how the process may be improved. that checks the forms for validity and then sends the They are check sheets, Pareto charts, cause and forms on to the proper insurance carrier. The effect (Ishikawa) diagrams, defect concentration medical group is then reimbursed from the insurance diagrams, scatter diagrams, control charts and carrier for the covered services. Forms that are histograms. filled out incorrectly are returned to the medical group for correction. This slows the reimbursement By implementing these seven tools, process process. improvement teams can get immediate or on-line feedback of information about the production A SAS® data set named CLAIMS is created to process. All seven tools of quality can be house the data. The data and the data step code automated using SAS®, SAS/GRAPH®, and used to create the CLAIMS data set is shown in the SAS/QC® software. Thorough descriptions of these Appendix. Each observation in the data set tools can be found in Montgomery(1991) and represents a returned form. The variable REASON Burr(1993). This paper will show examples of how gives the field on the form that was incorrectly SAS software can be used to produce the seven entered.