Poka-Yoke for Mass Customization
Total Page:16
File Type:pdf, Size:1020Kb
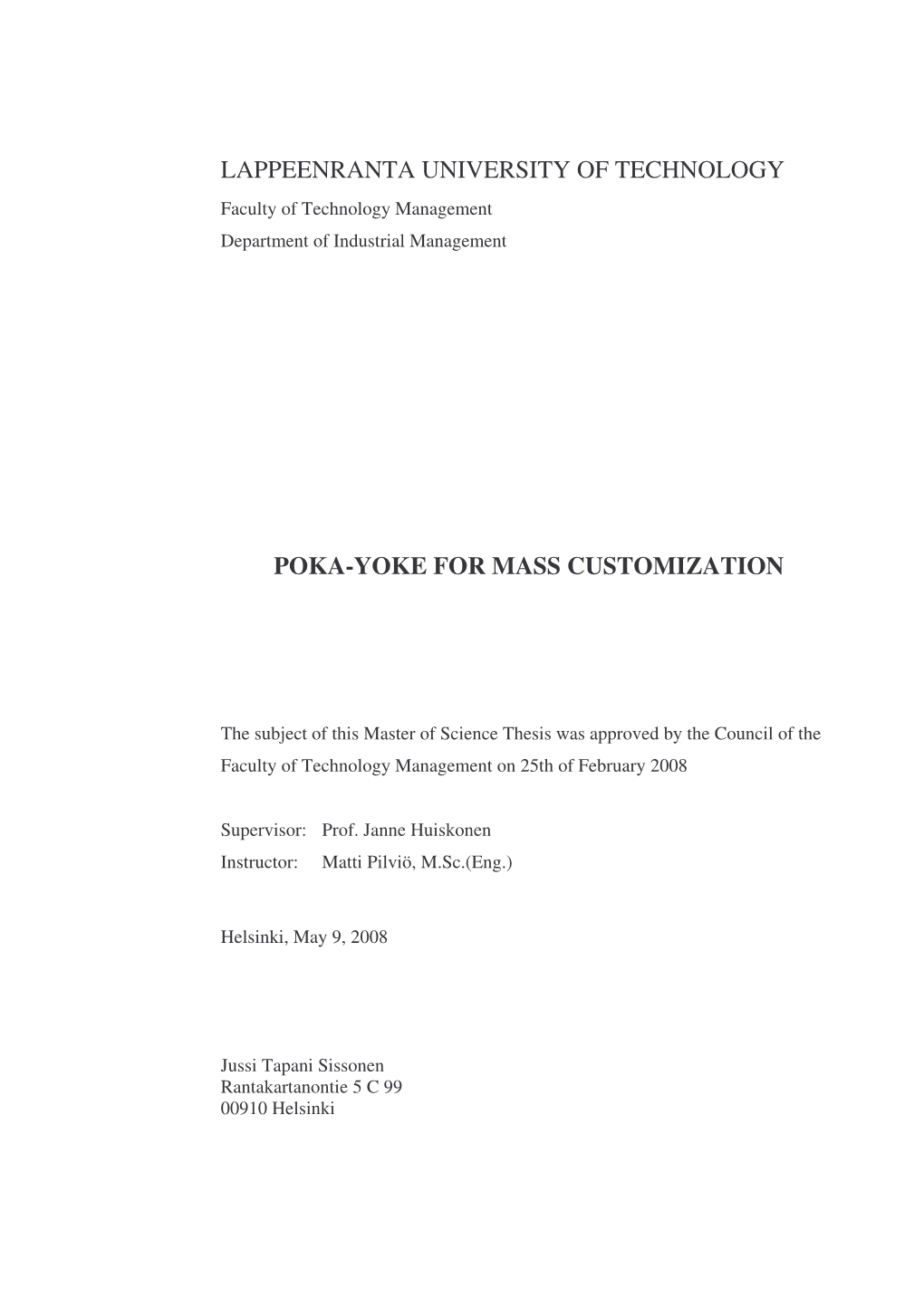
Load more
Recommended publications
-
Root Cause Analysis in Context of WHO International Classification for Patient Safety
Root cause analysis in context of WHO International Classification for Patient Safety Dr David Cousins Associate Director Safe Medication Practice and Medical Devices 1 NHS | Presentation to [XXXX Company] | [Type Date] How heath care provider organisations manage patient safety incidents Incident External organisation Healthcare Patient/Carer or agency professional Department of Health Incident report Complaint Regulators Health & Safety Request Risk/complaint Request additional manager additional Healthcare information information commissioners and purchasers Local analysis and learning Industry Feed back External report Root Cause AnalysisWhy RCA? (RCA) To identify the root causes and key learning from serious incidents and use this information to significantly reduce the likelihood of future harm to patients Objectives To establish the facts i.e. what happened (effect), to whom, when, where, how and why To establish whether failings occurred in care or treatment To look for improvements rather than to apportion blame To establish how recurrence may be reduced or eliminated To formulate recommendations and an action plan To provide a report and record of the investigation process & outcome To provide a means of sharing learning from the incident To identify routes of sharing learning from the incident Basic elements of RCA WHAT HOW it WHY it happened happened happened Human Contributory Unsafe Acts Behaviour Factors Direct Care Delivery Problems – unsafe acts or omissions by staff Service Delivery Problems – unsafe systems, procedures -
Guidance for Performing Root Cause Analysis (RCA) with Pips
Guidance for Performing Root Cause Analysis (RCA) with Performance Improvement Projects (PIPs) Overview: RCA is a structured facilitated team process to identify root causes of an event that resulted in an undesired outcome and develop corrective actions. The RCA process provides you with a way to identify breakdowns in processes and systems that contributed to the event and how to prevent future events. The purpose of an RCA is to find out what happened, why it happened, and determine what changes need to be made. It can be an early step in a PIP, helping to identify what needs to be changed to improve performance. Once you have identified what changes need to be made, the steps you will follow are those you would use in any type of PIP. Note there are a number of tools you can use to perform RCA, described below. Directions: Use this guide to walk through a Root Cause Analysis (RCA) to investigate events in your facility (e.g., adverse event, incident, near miss, complaint). Facilities accredited by the Joint Commission or in states with regulations governing completion of RCAs should refer to those requirements to be sure all necessary steps are followed. Below is a quick overview of the steps a PIP team might use to conduct RCA. Steps Explanation 1. Identify the event to be Events and issues can come from many sources (e.g., incident report, investigated and gather risk management referral, resident or family complaint, health preliminary information department citation). The facility should have a process for selecting events that will undergo an RCA. -
Extension of the Lean 5S Methodology to 6S with an Additional Layer to Ensure Occupational Safety and Health Levels
sustainability Article Extension of the Lean 5S Methodology to 6S with An Additional Layer to Ensure Occupational Safety and Health Levels Mariano Jiménez 1,2 , Luis Romero 2,* , Jon Fernández 2, María del Mar Espinosa 2 and Manuel Domínguez 2 1 Department of Mechanical Engineering, Technical School of Engineering—ICAI, Comillas Pontifical University, 25, 28015 Madrid, Spain 2 Design Engineering Area, Industrial Engineering School, National Distance Education University (UNED), 38, 28015 Madrid, Spain * Correspondence: [email protected] Received: 12 June 2019; Accepted: 11 July 2019; Published: 12 July 2019 Abstract: This paper proposes an expansion of the Lean 5S methodology, which includes the concept of Safety–Security as 6S. Implementation was done by a standardized process tested in a pilot area that is part of the Integrated Industrial Manufacturing System Laboratory at the Higher Technical School of Engineering (ICAI). The additional 6S phase (Safety-Security) thoroughly reviews all areas of an industrial plant by analyzing the risks at each workstation, which let employees be fitted out with protection resources depending on each of their personal characteristics and to guarantee the safety of the workstation by strictly complying with occupational safety and health and machinery use standards, which must hold a CE certificate of compliance. The main objective was to increase the scope of 5S methodology to respond to the occupational safety and health needs for machines required in optimizing production processes. It is important to remember that companies must guarantee that their employees use personal protection equipment (PPE) at their work posts or stations that protect them properly from risks to their health and safety and that cannot be prevented or sufficiently limited by using collective means of protection or by adopting work organization measures. -
Root Cause Analysis in Surgical Site Infections (Ssis) 1Mashood Ahmed, 2Mohd
International Journal of Pharmaceutical Science Invention ISSN (Online): 2319 – 6718, ISSN (Print): 2319 – 670X www.ijpsi.org Volume 1 Issue 1 ‖‖ December. 2012 ‖‖ PP.11-15 Root cause analysis in surgical site infections (SSIs) 1Mashood Ahmed, 2Mohd. Shahimi Mustapha, 3 4 Mohd. Gousuddin, Ms. Sandeep kaur 1Mashood Ahmed Shah (Master of Medical Laboratory Technology, Lecturer, Faculty of Pharmacy, Lincoln University College, Malaysia) 2Prof.Dr.Mohd. Shahimi Mustapha,(Dean, Faculty of Pharmacy, Lincoln University College, Malaysia) 3Mohd.Gousuddin, Master of Pharmacy (Lecturer, Faculty of Pharmacy, Lincoln University College, Malaysia) 4Sandeep kaur,(Student of Infection Prevention and control, Wairiki Institute of Technology, School of Nursing and Health Studies, Rotorua: NZ ) ABSTRACT: Surgical site infections (SSIs) are wound infections that usually occur within 30 days after invasive procedures. The development of infections at surgical incision site leads to extend of infection to adjacent tissues and structures.Wound infections are the most common infections in surgical patients, about 38% of all surgical patients will develop a SSI.The studies show that among post-surgical procedures, there is an increased risk of acquiring a nosocomial infection.Root cause analysis is a method used to investigate and analyze a serious event to identify causes and contributing factors, and to recommend actions to prevent a recurrence including clinical as well as administrative review. It is particularly useful for improving patient safety systems. The risk management process is done for any given scenario in three steps: perioperative condition, during operation and post-operative condition. Based upon the extensive searches in several biomedical science journals and web-based reports, we discussed the updated facts and phenomena related to the surgical site infections (SSIs) with emphasis on the root causes and various preventive measures of surgical site infections in this review. -
Root Cause Analysis: the Essential Ingredient Las Vegas IIA Chapter February 22, 2018 Agenda • Overview
Root Cause Analysis: The Essential Ingredient Las Vegas IIA Chapter February 22, 2018 Agenda • Overview . Concept . Guidance . Required Skills . Level of Effort . RCA Process . Benefits . Considerations • Planning . Information Gathering • Fieldwork . RCA Tools and Techniques • Reporting . 5 C’s Screen 2 of 65 OVERVIEW Root Cause Analysis (RCA) A root cause is the most reasonably identified basic causal factor or factors, which, when corrected or removed, will prevent (or significantly reduce) the recurrence of a situation, such as an error in performing a procedure. It is also the earliest point where you can take action that will reduce the chance of the incident happening. RCA is an objective, structured approach employed to identify the most likely underlying causes of a problem or undesired events within an organization. Screen 4 of 65 IPPF Standards, Implementation Guide, and Additional Guidance IIA guidance includes: • Standard 2320 – Analysis and Evaluation • Implementation Guide: Standard 2320 – Analysis and Evaluation Additional guidance includes: • PCAOB Initiatives to Improve Audit Quality – Root Cause Analysis, Audit Quality Indicators, and Quality Control Standards Screen 5 of 65 Required Auditor Skills for RCA Collaboration Critical Thinking Creative Problem Solving Communication Business Acumen Screen 6 of 65 Level of Effort The resources spent on RCA should be commensurate with the impact of the issue or potential future issues and risks. Screen 7 of 65 Steps for Performing RCA 04 02 Formulate and implement Identify the corrective actions contributing to eliminate the factors. root cause(s). 01 03 Define the Identify the root problem. cause(s). Screen 8 of 65 Steps for Performing RCA Risk Assessment Root Cause Analysis 1. -
White Paper the PDCA Cycle and Management System Standards
The PDCA cycle and Management System Standards ISO uses a very simple but powerful tool for quality system standards. This tool is the Plan- Do-Check-Act (PDCA) cycle shown in the figure below. It is also known as the Deming cycle after J.W. Deming, who proposed the concept in the 50s. The entire logic, structure, and sequence of standards like ISO 9001 and ISO 13485 are based on this cycle. Every process or activity needs to pass through these four phases. Plan Phase Perhaps, planning tasks are the most important ones in a management system. ISO recognizes this fact, as well as the fact that the plan phase should be the very first thing we do. To better understand this phase, activities like “establish” and “determine” should be associated to planning. Other words we can use instead are “identify” or “define”. Let´s see what an organization needs to plan. ACT PLAN First, the organization needs to establish its high- level planning. This will set direction and provide a framework for the entire system. We are talking about the organization´s purpose. And also, in CHECK DO terms of quality, about: policy, system´s scope, and objectives. The output of the high-level planning process will provide the necessary guide to the next step. The PDCA Cycle Next the organization needs to identify the processes that will be part of the quality system. It also needs to define how to apply or operate these processes, their sequence and how they interact. Also, the organization must identify risks related to the processes and how to control them according to those risks. -
The Concept and Implementation of Kaizen in an Organization
Global Journal of Management and Business Research: A Administration and Management Volume 19 Issue 1 Version 1.0 Year 201 Type: Double Blind Peer Reviewed International Research Journal Publisher: Global Journals Online ISSN: 2249-4588 & Print ISSN: 0975-5853 The Concept and Implementation of Kaizen in an Organization By Lubna Rahman Lina & Hafiz Ullah University of Dhaka Abstract- For continuous improvement in an organization, Japanese philosophy Kaizen is very popular. Flawless concepts of kaizen methodology and proper implementation of tools can lead to a successful kaizen program in a company. From the reviews of various case studies, it has revealed that most of the companies have implemented kaizen efficiently and observe better performance. Besides, some companies also failed to implement kaizen due to the lacking of proper knowledge about the concepts of kaizen. Keywords: kaizen, 5 why technique, 5s, 7 QC tools, 7 wastes, jidoka, PDCA cycle, poka-yoke. GJMBR-A Classification: JEL Code: M00 TheConceptandImplementationofKaizeninanOrganization Strictly as per the compliance and regulations of: © 2019. Lubna Rahman Lina & Hafiz Ullah. This is a research/review paper, distributed under the terms of the Creative Commons Attribution-Noncommercial 3.0 Unported License http://creativecommons.org/licenses/by-nc/3.0/), permitting all non-commercial use, distribution, and reproduction in any medium, provided the original work is properly cited. The Concept and Implementation of Kaizen in an Organization α σ Lubna Rahman Lina & Hafiz Ullah Abstract - For continuous improvement in an organization, over the longer term, without having to go through any Japanese philosophy Kaizen is very popular. Flawless radical innovation. It can be a much gentler and concepts of kaizen methodology and proper implementation employee-friendly way to institute the changes that must of tools can lead to a successful kaizen program in a occur as a business grows and adapts to its changing company. -
Agile and Devops Overview for Business
NELKINDA SOFTWARE CRAFT Ƅ TRAINING Agile and DevOps Overview for Business Duration: 2 Days Available Languages: English Audience Everyone who is steering or involved in software delivery: Business, Management, Operations, Development, for example: CxOs, managers, directors, team leads, systems administrators, development managers, business analysts, requirements engineers, architects, product owners, scrum masters, IT operations sta', IT stakeholders, developers, testers Goals Agile and DevOps are the big drivers of organizational transformation today. What do they mean? Where do they come from? What are their goals? How can they help my organization and my team? How can I use and implement them? And are there any side-e'ects or challenges to consider? Learn the answers to these questions in a holistic perspective from the CxO level to the code about what Agile and DevOps mean for organizations of all sizes. Contents • Business Case for Improving the Software Development Life Cycle ◦ Evolution of the Software Development Life Cycle (SDLC) ◦ Business Drivers of the SDLC Evolution ◦ Principles of Agile, DevOps, Extreme Programming (XP), and Software Craft ◦ Goals and Objectives of Agile, DevOps (Development Operations), XP, and Software Craft ◦ The Pipeline for Value Delivery • Essential Principles ◦ Manifesto for Agile Software Development ("Agile Manifesto") ◦ The Values and Principles of XP ◦ Manifesto of Software Craft ◦ The Two Values of Software ◦ The Deming (PDCA, plan-do-check-act) Cycle ◦ The XP Feedback Loops ◦ Parkinson's Law and Timeboxing ◦ Conway's Law, Organizational Structure and Cross-functional responsibility ◦ KPIs (Key Performance Indicators) and Drivers: Story-Point Velocity, Cycle Time, WIP (Work In Progress) limit ◦ Heisenberg's Uncertainty Principle of Agile Estimation 1/3 https://nelkinda.com/training/DevOps-Driven-Agile © Copyright 2015-2020 Nelkinda Software Craft Private Limited. -
Implementation of Lean Tools in Apparel Industry to Improve Productivity and Quality
Current Trends in Fashion Technology & Textile Engineering ISSN: 2577-2929 Review Article Curr Trends Fashion Technol Textile Eng Volume 4 - Issue 1 - July 2018 Copyright © All rights are reserved by Prakash C DOI: 10.19080/CTFTTE.2018.04.555628 Implementation of Lean Tools in Apparel Industry to Improve Productivity and Quality Mothilal B and Prakash C* Department of Fashion Technology, Sona College of Technology, India Submission: April 19, 2018; Published: July 02, 2018 *Corresponding author: Prakash C, Department of Fashion Technology, Sona College of Technology, India, Tel No: ; Fax: +91-427- 4099888; Email: Abstract The rapid change in apparel styles, deviation of order quantities and increasing quality levels at the lowest possible cut-rate, demand the market. To increase the productivity of the apparel industries we need to reduce the wastage of the manufacturing and time to manufacture the product.apparel manufacturing Lean is the tool industry to reduce to the be focusedwastage on in moreall process effective of apparel and efficient manufacturing, manufacturing reducing processes cost and for value survival added in anto theimmensely product. competitive This paper proposes the lean tool for the apparel industry to reduce the overall wastage of the industries. Keywords: Abbreviations:Apparel FMEA: industry; Failure Eco-efficiency; Mode and Effect Industrial Analysis; wastes; SFPS: Single Lean Failuretools Points; TPM: Total Productive Maintenance; OEE: Overall Equipment Effectiveness; PDCA: Plan-Do-Check-Act or Plan-Do-Check-Adjust; PDSA: Plan-Do-Study-Act Introduction Tapping D [1] observed that lean strategy is to eliminate wastes Lean tools from the process. Any excess in equipment’s, materials, parts, and working period beyond the requirement is generally referred as of waste (muda), the improvement of quality, and production waste. -
Root Cause Analysis in Health Care Tools and Techniques
Root Cause Analysis in Health Care Tools and Techniques SIXTH EDITION Includes Flash Drive! Senior Editor: Laura Hible Project Manager: Lisa King Associate Director, Publications: Helen M. Fry, MA Associate Director, Production: Johanna Harris Executive Director, Global Publishing: Catherine Chopp Hinckley, MA, PhD Joint Commission/JCR Reviewers for the sixth edition: Dawn Allbee; Anne Marie Benedicto; Kathy Brooks; Lisa Buczkowski; Gerard Castro; Patty Chappell; Adam Fonseca; Brian Patterson; Jessica Gacki-Smith Joint Commission Resources Mission The mission of Joint Commission Resources (JCR) is to continuously improve the safety and quality of health care in the United States and in the international community through the provision of education, publications, consultation, and evaluation services. Joint Commission Resources educational programs and publications support, but are separate from, the accreditation activities of The Joint Commission. Attendees at Joint Commission Resources educational programs and purchasers of Joint Commission Resources publications receive no special consideration or treatment in, or confidential information about, the accreditation process. The inclusion of an organization name, product, or service in a Joint Commission Resources publication should not be construed as an endorsement of such organization, product, or service, nor is failure to include an organization name, product, or service to be construed as disapproval. This publication is designed to provide accurate and authoritative information in regard to the subject matter covered. Every attempt has been made to ensure accuracy at the time of publication; however, please note that laws, regulations, and standards are subject to change. Please also note that some of the examples in this publication are specific to the laws and regulations of the locality of the facility. -
Bringing Lean to Life: Making Processes Flow in Healthcare
NH S Improving Quality BRINGING LEAN TO LIFE Making processes flow in healthcare IMPROVEMENT. PEOPLE. QUALITY. STAFF. DATA. SATcEknPoSw.leLdgEeAmNen. tsPATIENTS. PRODUCTIVITY. IDEAS. This document has been written in partnership by: RZEoë LDord ESIGN. MAPPING. SOLUTIONS. EXPERIENCE. Email: [email protected] Lisa Smith SEmHail:A [email protected] OCESSES. TOOLS. MEASURES. INVOLVEMENT. STRENGTH. SUPPORT. LEARN. CHANGE. TEST. IMPLEMENT. PREPARATION. KNOW-HOW. SCOPE. INNOVATION. FOCUS. ENGAGEMENT. DELIVERY. DIAGNOSIS. LAUNCH. RESOURCES. EVALUATION. NHS. PLANNING. TECHNIQUES. FRAMEWORK. AGREEMENT. UNDERSTAND. IMPLEMENTATION. SUSTAIN. Bringing Lean to Life - Making processes flow in healthcare Contents Introduction - what is the problem in healthcare? 4 Identifying waste 18 What is Lean? 6 Making value flow 21 A3 thinking 7 Understanding pull 22 An example A3 report 8 Understanding Takt time 23 The importance of data and measures 10 Using 5S to improve safety 24 Example statistical process control (SPC) charts 11 Plan, Do, Check, Adjust (PDCA) cycle 25 Current state value stream mapping 12 Continuous improvement 26 Analysing your current state and designing your 14 Value stream mapping symbols 27 future state value stream map Standard work to produce high quality every time 15 Visual management 16 3 4 Bringing Lean to Life - Making processes flow in healthcare Introduction - what is the problem in healthcare? We all come to work to do our very best - to The processes are to blame, not the people This booklet provides a basic introduction and achieve what we are capable of and to add real overview of Lean; the culture, principles and value for our patients and ensure clinical Often, there is ambiguity in how certain tasks tools to understand to enable you to tackle and expertise is supported by process excellence to should be performed – so people work it out for resolve issues within healthcare. -
Review Paper on “Poka Yoke: the Revolutionary Idea in Total Productive Management” 1,Mr
Research Inventy: International Journal Of Engineering And Science Issn: 2278-4721, Vol. 2, Issue 4 (February 2013), Pp 19-24 Www.Researchinventy.Com Review Paper On “Poka Yoke: The Revolutionary Idea In Total Productive Management” 1,Mr. Parikshit S. Patil, 2,Mr. Sangappa P. Parit, 3,Mr. Y.N. Burali 1,Final Year U.G. Students, Mechanical Engg. Department,Rajarambapu Institute of Technology Islampur (Sangli),Shivaji University, Kolhapur (India) 2,P.G. Student, Electronics Engg. Department, Rajarambapu Institute of Technology Islampur (Sangli), Shivaji University, Kolhapur (India) Abstract: Poka-yoke is a concept in total quality management which is related to restricting errors at source itself. It deals with "fail-safing" or "mistake-proofing". A poka-yoke is any idea generation or mechanism development in a total productive management process that helps operator to avoid (yokeru) mistakes (poka). The concept was generated, and developed by Shigeo Shingo for the Toyota Production System. Keywords— Mistake-proofing, Total quality management, Total productive management. I INTRODUCTION In today’s competitive world any organisation has to manufacture high quality, defect free products at optimum cost. The new culture of total quality management, total productive management in the manufacturing as well as service sector gave birth to new ways to improve quality of products. By using various tools of TQM like KAIZEN, 6 sigma, JIT, JIDCO, POKA YOKE, FMS etc. organisation is intended to develop quality culture.[2,6] The paper is intended to focus basic concept of poka yoke, types of poka yoke system, ways to achieve simple poka yoke mechanism. It also covers practical study work done by various researchers .