Software Technology Steel Spur Gears
Total Page:16
File Type:pdf, Size:1020Kb
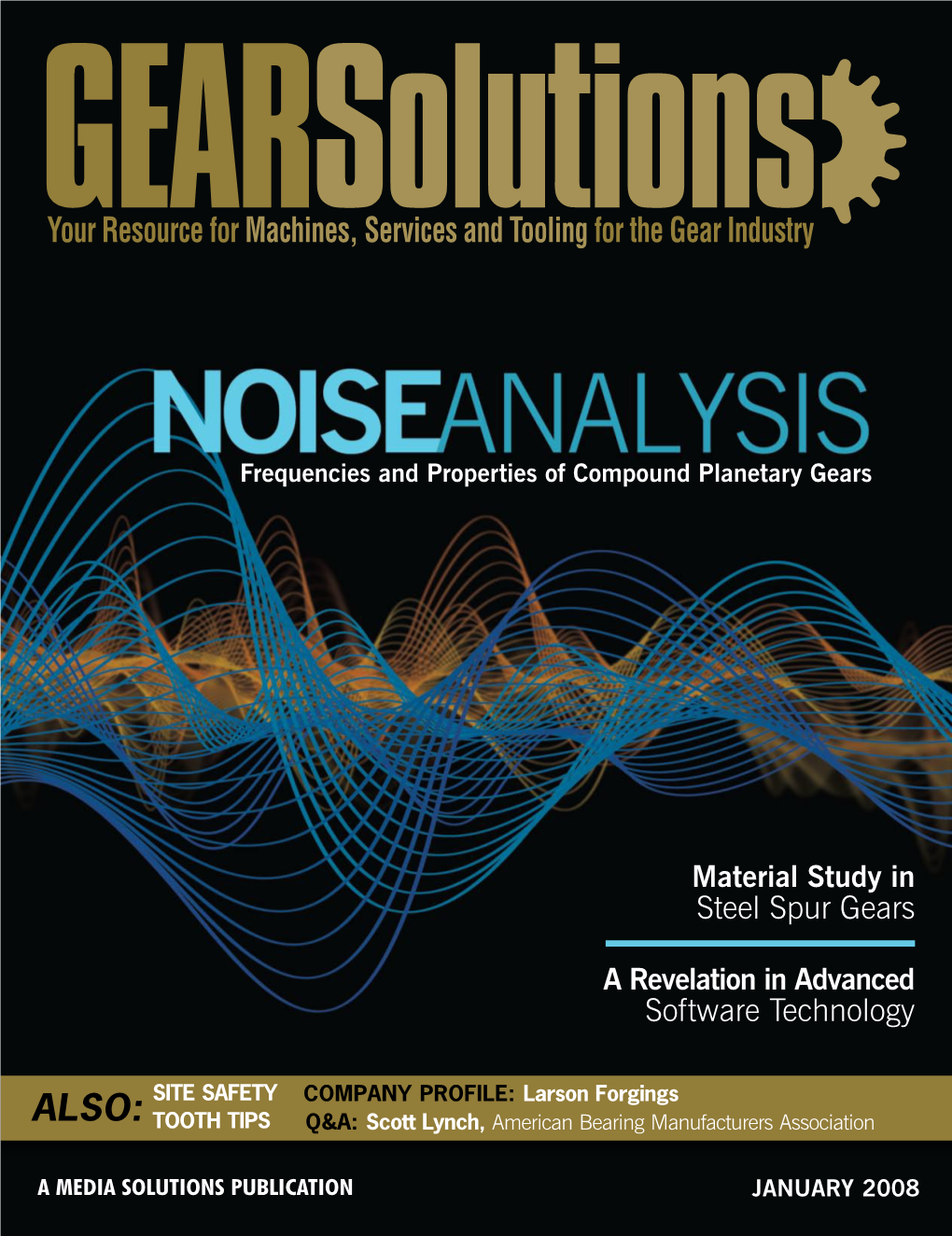
Load more
Recommended publications
-
Century American Machinery and Machine Tool Building
From Depression to Globalization: Reconfiguring 20th Century American Machinery and Machine Tool Building Philip Scranton, Rutgers University Prologue Practical Machinist: 06-14-2003, 11:51 AM Let's talk about Machine Tool Making. 1. The industry is Capital Intensive. A machine tool maker has a huge amount invested in plant and equipment. 2. The industry is Labor Intensive. Almost all the workers are highly skilled and not only that, each worker has to have significant experience working in the specific shop making that company's machines. 3. The Industry is cyclic. Some years there is a big backlog of orders. Some years, there is hardly anything for the skilled and valued workers to do. 4. The "Technical" competition is Brutal. As soon as a new machine design is fit for production, some competitor brings out a newer design with faster spindle speeds or faster motions or some other feature that he touts relentlessly in the trade publications. A Machine tool can be rendered obsolete by the time the first article is being crated up on a maker's loading dock. 5. The reverse of this can happen. A machine tool maker can devise a highly sophisticated design that just doesn't sell. Giddings and Lewis has had this happen to them several times and Davenport Machine had it happen with a servo-controlled, multi-spindle automatic bar machine. 6. During slow times, a machine tool manufacturer can be in competition with slightly used machine of his own manufacture. This is happening right now. None of the above points have anything to do with the government, and the best of the foreign competition suffers all of the above situations. -
IMTS 2004 Sneak Preview
ShowBasics 2 6/10/04 2:07 PM Page 19 IMTS IMTS COVERAGE SNEAK PREVIEW There’s a bustle of activity as exhibitors prepare for America’s most significant manufacturing trade show. The red carpets are ready, the lights are being tested, and the crowds are gathering with anticipation. Amid the excitement, Gear Technology has managed to sneak under the usher’s ropes to provide you with this advance look at some of the gear-related products and technologies that will be featured at IMTS 2004. New LMT-Fette Tool for Chamfering/ Chromium: The Base of Balzers’ Deburring in the Hob Machine New Tool Coating LMT-Fette will introduce a new chamfer- Balzers Inc. will unveil a tool coating that can be used on hobs and ing/deburring tool for use in hob machines, a features increased wear resistance. The coating, Balinit® Alcrona, is new tool steel and two new coatings. the first of the new G6 coating generation developed by Balzers. The new tool is called Chamfer Cut. It Titanium has been the base of benchmark coatings such as TiAlN, allows gear manufacturers to produce con- TiCN or AlTiN. With Alcrona, Balzers has developed a coating based sistent chamfering and deburring of paral- on chromium. The coating’s formula is in its name; Alcrona is AlCrN, lel-axis gears, both spur and helical. an aluminium chromium nitride. Darryl Witte, product manager–gear Dennis T. Quinto, Balzers’ technical director, calls Alcrona the tools, says Chamfer Cut will allow gear “cornerstone” for its new generation of PVD coatings and says it’ll manufacturers to reduce the many hours that open “a new productivity dimension in machining.” manual deburring takes and reduce high Quinto emphasizes Alcrona’s wear resistance, which he calls “unri- costs associated with specialized chamfer machines and their tools. -
May/June 2002 Gear Technology
Now there are no limits to how good aU iiiiiiiiii:!~our gears can be. Chances are there's a Gleason Malu metrology product for any and all of your gear and gear tool measuring requirements: bevel or cylindrical, internal or external, plastic or formed, hobs or shaper cutters. Call today or log-on Now you have single to learn more ••• sourc,e ac,cess... to everything www ..-Ieason ...com from Double Flank Roll Testers to accurately identify proce 5 variations on the shop floor. on the fly' to the PR[MAR Universal Gear Inspection System: the 1000 U niversity Ave .• p.o. Box. 229'70 latest in single setup complete measuring Rochester, NY 14692-2970 U.S.A. technology, Phone: 585/473-1000 Fax: 585/4614348 Web site: wwwgleason.eom E-mail: [email protected] TH.ELAT£5T INNOVATION fNHOBBING. SUPERIOR QUAUTY. SERVICE AND Dfl.lVER Y. MAV/JUNE 2002 The Journal 0/ Gear Malzu/acturi'ng FEATURES Carbiide H!obbing Case Study A gear manufacturer starts from scratch with new technology ,.., , 12 FOCUS ON GEAR DESIGN Gear Oesiign Spec;ial Section , 21 Optimizing IPlastic Gear Geometry: An Introductiont'D ,G,earOptimizat~ion A close look at working tooth depth and other parameter , , 22 Program for Involut,e Equat.ion to. Develop, Spur Gears, on Pm/E Software A program for modeling spur gears with profile shift ,.., , ,., 27' 21' lnereased Load 'Cap,ady of Worm Gears by Optimizing the Worm Wheel Bnm~e A study of bronze alloy content.. " 33 DEPARTMENTS IPublisher~s Page, lndu trial Evolution 7 Revo~lutions Ice-blast gear cleaning 9 Industry N'ews Wllat's happeningin the gear industry 18 Technical,Call,endar DOIl'I mi s these important upcoming events 31 IProduct INews The latest product for the gear industry 38 1CD'~RO'MIIB'UyersGuide FRE.EListing Forms Sign up for fr~e listings in our 2003 directory 40 Advertiser Index NEW! Phone numbers and web addresses to make it easier to get information " 44, ICl'assi,lieds Services, Help Wanted, websites and more 45, Clrver art ,CQu:rtesy' 'D. -
United States Patent (19) 11) Patent Number: 4,790,545 Dzewaltowski Et Al
United States Patent (19) 11) Patent Number: 4,790,545 Dzewaltowski et al. 45) Date of Patent: Dec. 13, 1988 (54) WORKPART CENTERING MECHANISM Assistant Examiner-Daniel W. Howell FOR A CHUCK Attorney, Agent, or Firm-Edward J. Timmer (75) Inventors: Victor F. Dzewaltowski; Walter C. 57 ABSTRACT Dodd, both of Springfield, Vt. A workpart chuck is provided with a centering member 73 Assignee: Bryant Grinder Corporation, that is movable toward the axis of rotation of the chuck Springfield, Vt. as the chuck rotates the workpart in an eccentric non centered position. As the centering member moves the 21 Appi. No.: 142,549 workpart, a sensing device senses the extent of changing (22 Filed: Jan. 11, 1988 eccentric movement of the workpart and generates an electrical signal that is indicative of the extent of such 51) Int. Cl." .............................................. B23B 15/00 eccentric movement. The workpart is moved toward 52 U.S. Cl. ...................................... 279/1 L; 33/550; the chuck axis until the signal reaches a predetermined 33/642; 33/644; 33/645; 82/45; 279/1 R value indicative that the workpart is rotating about its 58 Field of Search ............... 279/1 L, 1 M, 1 J, 1 R, axis; i.e., the workpart axis and chuck axis are substan 279/6, 11; 82/45, 2.5; 51/277; 33/550, 640, tially coaxial. The centering member is offset slightly 641, 642, 644, 645; 409/174 relative to the chuck axis of rotation to assure that ex (56) References Cited cessive movement of the centering member placing the workpart center beyond the chuck axis of rotation will U.S. -
Cbn Grinding a Tempting Technology
Reprinted from MANUFACTURING ENGINEERING, February 1994 Issue Don’t let initial cost and perceived risk scare you CBN GRINDING A TEMPTING TECHNOLOGY or years, CBN grinding This material also offers was on the fringes of the potential for improved F machining technolo- production through better gy. Manufacturing engi- finish, greater part consis- neers used it only when tency, and tighter toler- they had to, usually because ances. CBN can offer a sig- a metal was too difficult to nificant time saving in high cut or finish any other way. speed production because The picture is changing wheel dressing is less fre- today with about 25% of all quent. CBN grinding is not industrial grinding in Japan limited to traditional fin- done with CBN, 15% in ishing operations. Its Europe, and 10% in the US. potential for fast material Although CBN use in the US removal means it can is statistically low, interest is sometimes eliminate quite high. Predictions are machining steps. In some that its use will expand dra- cases, grinding can do in matically for three reasons: one setup what would oth- conversion from other erwise require milling, abrasives, chiefly alum- grinding, heat treating, and inum oxide; introduction of polishing. Grinding drill CBN compatible grinders; bits from bar stock is one and new applications as such application. harder, more complex work ‘Today, high-speed materials are introduced. Landis CBN machines, shown doing pin journal grinding, are grinding (16,000-40,000 According to data from gaining acceptance in the US automotive industry. sfm, 80-200 m/s) accounts GE Superabrasives (Worthington OH), total use. -
IMTS 2000 Offers Ten Pavilions with More Than 1,800 on the Main Concourse, Room N426
_------------,IMTSFOCUS------------- The World Of Manufacturing or eight. days every other year, the sponsor of the 200 largest trade shows. That wasn't always the size or scope of International Manufacturing Technology Show (IMTS), the show. Its inception, while impressive for the time" was hum- the Association for Manufacturing Technology (AMT), ble by today's standards. strives to tum Chicago's McCormick Place into a "pIO- The Birt/' of IMTS. The first Machine Tool Show. ponsored ductivity marketplace," the largest and most complete display and by AMT's predecessor, the National Machine Tool Builder's demonstration of manufacturing technology ever seen in the Association, opened for a five-day run at the Public Auditorium Americas. If the growth of the show is any indicator, that effort in Cleveland, Ohio, on September 19, 1927. This precursor to has been very successful. indeed. With over] .4 million square feet llVITS was heralded as a neutral forum where engineers" product of exhibit space taking up all five levels and all three exhibit halls users, distributors and producers could freely discuss questions of of McComllck Place, each level would rank as one of the nation's mutual interest and seek solutions to manufacturing problems. The show's 12,000 visitors and 184 exhibitors filled the Public SHOW OATES: September 6-13,2000 Auditorium to capacity. Helping to bring in the visitors, the Society of Automotive Engineers, the Machine Tool Congress, LOCATION: McCormick Place, Chicago, Illinois, USA the Association of Woedworking Machinery Manufacturers, the Associated Machine Tool Dealers. the Foundry Equipment EXHIBit HALL HOURS: Manufacturers Association, the Screw Machine Products • Lakeside Center and North Building,. -
Eligible Company List - Updated 2/1/2018
Eligible Company List - Updated 2/1/2018 S10009 3 Dimensional Services Rochester Hills, MI Supplier Employees Only S65830 3BL Media LLC North Hampton, MA Supplier Employees Only S69510 3D Systems Rock Hill, SC Supplier Employees Only S65364 3IS Inc Novi, MI Supplier Employees Only S70521 3R Manufacturing Company Goodell, MI Supplier Employees Only S61313 7th Sense LP Bingham Farms, MI Supplier Employees Only D18911 84 Lumber Company Eighty Four, PA DCC Employees Only S42897 A & S Industrial Coating Co Inc Warren, MI Supplier Employees Only S73205 A and D Technology Inc Ann Arbor, MI Supplier Employees Only S57425 A G Manufacturing Harbour Beach, MI Supplier Employees Only S01250 A G Simpson (USA) Inc Sterling Heights, MI Supplier Employees Only F02130 A G Wassenaar Denver, CO Fleet Employees Only S80904 A J Rose Manufacturing Avon, OH Supplier Employees Only S19787 A OK Precision Prototype Inc Warren, MI Supplier Employees Only S62637 A Raymond Tinnerman Automotive Inc Rochester Hills, MI Supplier Employees Only S82162 A Schulman Inc Fairlawn, OH Supplier Employees Only S78336 A T Kearney Inc Chicago, IL Supplier Employees Only D80005 A&E Television Networks New York, NY DCC Employees Only S64720 A.P. Plasman Inc. Fort Payne, AL Supplier Employees Only S36205 AAA National Office (Only EMPLOYEES Eligible) Heathrow, FL Supplier Employees Only S31320 AAF McQuay Inc Louisville, KY Supplier Employees Only S14541 Aarell Process Controls Group Troy, MI Supplier Employees Only F05894 ABB Inc Cary, NC Fleet Employees Only S10035 Abbott Ball Co -
A Revelation in Advanced Software Technology
A REVELATION IN Bryant Grinder has always been at the forefront of grinding machine ADVANCED SOFTWARE technology. Founded in Springfield, Vermont, in 1909, the company TECHNOLOGY has the distinction of having introduced the first computer numeri- By George Nelson cally controlled (CNC) grinding machine. Today, Bryant is leading the HERE ARE DETAILS ON A NEW SOFTWARE PACKAGE THAT INCREASES PRODUCTIVITY, DECREASES PROGRAMMING, SETUP, machine tool industry again with the introduction of its REVELATIONS™ AND CYCLE TIMES, AND LEADS TO GREATER PROFITABILITY. CNC software. 36 GEAR SOLUTIONS • JANUARY 2008 • gearsolutionsonline.com gearsolutionsonline.com • JANUARY 2008 • GEAR SOLUTIONS 37 • Single screen flowchart programming, and single screen for set-up and run. • Supports any number of axes in any combination; any number of wheel, work and dresser spindles; all standard types of E E VERSATILEgrinds and dresses including contour and profile;FEATURES multi-path operations, including simultaneous operations in multiple paths; any number of programmable devices including loaders, gauges, wheel balancing; and any number of programmable trigger ES inputs from the machine: switches, positions, registers. TIL • Any combination or sequence of grinds, dresses, devices or other operations in any cycle. R • Grinds and dresses can contain any combination of nested operations: feeds, reverse feeds, dwells, and others. U • Skip dressing and any other desired program branching. • Wheel, work, and dresser RPM adjustable at any point in a programmed cycle, as are oscillation parameters. T SA • Recognizes and translates G-code programs, and programmer can view and edit ladder from the PC. • Servo parameters viewed and programmed from the PC. R • Ethernet connection to customer LAN for remote programming, and telemaintenance via Ethernet for real-time trouble- WITH REVELATIONS™ SOFTware, ONE BUTTON CONVERTS THE INTUITIVE FLOWCHART TO TIGHT, EFFICIENT G-CODE. -
Online Auction Sale Range of CNC Machining Centres, Lathes, Grinders and Ancillary Equipment Bidding Ends
For Impressive Performances www.kingsland.com [email protected] www.mtimagazine.com 31 August 2015 Now available on the App Store for iOS Android App on Inter-Plast Andrzej Bodziachowski company was established in 1995 and is one of the biggest companies in Poland selling used CNC metal working machines. We own properties in the form of 1.5 ha of area partially built over with modern halls of 6000 m2. There are over 100 machines in stock. We would like to invite you to co-operate with us. Andrzej Bodziachowski CNC Bed Type Milling Machine CNC Bed Type SORALUCE Milling Machine SORAMILL SP 8000 CME BF 01 rotary table, swarf conveyor Year of production: Year of production: 1996 1994 CNC HEIDENHAIN TNC 426 CNC HEIDENHAIN Table: 8000 x 800 mm TNC 360 Working travel X/Y/Z: 6500/1600/1200 mm Table: 1400 x 600 mm Rotary table diameter: Working travel X/Y/Z: 1000 mm 1200/600/600 mm Tool holder: ISO 50 160 000 EUR 109 000 EUR Range of spindle speeds: 20-2000 rpm CNC Vertical Machining CNC Vertical Center Machining Center STAMA MC 540 DAEWOO Year of production: 1996 CNC SIEMENS 840 C MYNX - 540 Index head with three side coolant through spindle rotary table:1640 x 280 mm Year of production: 2005 Vertical rotary table: CNC SIEMENS 810 D 1200 x 630 mm Working travel X/Y/Z: Working travel X/Y/Z: 1020/510/625 mm 4000/550/550 mm Table: 1200 x 500 mm Spindle speeds: 36-8000 rpm Range of spindle speeds: 46 000 EUR 35 900 EUR Tool holder: SK 40 49 000 EUR 41 000 EUR 8000 rpm Tool magazine: 60 pcs Tool magazine: 24 pcs CNC Lathe CNC Lathe TRAUB TNC MAX MULLER 42/65 EGY MDW 40 Y axis, sub-spindle, driven tool magazine, measurement Year of production: 1998 tools, bar feeder LNS Year of production: 1995 CNC SIEMENS Turning diameter over bed: CNC TX-8 F 1200 mm Max. -
Dana Corporation Allowed Class 5B General Unsecured Claims As of 1/31/08
Dana Corporation Allowed Class 5B General Unsecured Claims As of 1/31/08 CLAIM # ORIGINAL CREDITOR NAME TRANSFEREE NAME ALLOWED AMOUNT 12557 137 NORTH BRANFORD RD LLC HAIN CAPITAL HOLDINGS LLC $143,000.00 406 3M $238,616.34 54-F-1-19713 641 PLUMBING AND ELECTRIC ARGO PARTNERS $7,574.69 73-F-1-15699 A GHIENDONI HAULAGE LTD $60,641.74 94-F-1-17196 A L COMPRESSED GASES INC LONGACRE MASTER FUND LTD $28,906.71 2168 A SCHULMAN INC MADISON INVESTMENT TRUST - SERIES 39 $98,535.24 560 A STAMP INDUSTRIES $75,057.43 3481 A&C MOLD $21,500.00 3904 AAA COOPER TRANSPORTATION $5,800.59 94-F-1-17199 ABB INC ASM CAPITAL LP $136,816.00 6160 ABB INC ASM CAPITAL LP $33,209.18 54-F-1-19740 ABBOTTS PRINT SHOP INC ARGO PARTNERS $7,533.57 6158 ABC PLASTIC MOULDING $10,444.00 1024 ABC SECURITY GUARD SERVICE INC LIQUIDITY SOLUTIONS INC $9,653.40 941 ABF FREIGHT SYSTEMS INC $17,891.83 774 ABRASIVE MACHINE TECHNOLOGIES $25,554.22 90-F-1-16886 ABS QUALITY EVALUATIONS INC $5,092.50 54-F-1-19746 ABS QUALITY EVALUATIONS INC $5,079.66 12691 ABSOLUTE MACHINING INC MADISON INVESTMENT TRUST - SERIES 39 $157,795.88 95-F-1-17892 ABSORB TECH $17,636.96 5390 ACCU MOLD INC AMROC INVESTMENTS LLC $19,253.60 1231 ACCUCAM INC $29,470.78 3872 ACCUCAST TECHNOLOGY LLC $47,687.47 6570 ACCULUBE $40,056.70 54-F-1-19761 ACCUTREX PRODUCTS INC SPCP GROUP LLC $58,169.09 10299 ACE METAL STAMPING CO AMROC INVESTMENTS LLC $6,381.50 8883 ACE QUALITY CONTROL SERVICE $6,312.00 8884 ACE QUALITY CONTROL SERVICE $5,318.00 814 ACHESON COLLOIDS $21,168.00 3909 ACME SPIRALLY WOUND PAPER PROD INC SIERRA -
EXTENSIONS of REMARKS 25025' by Mr
July 19·, 1973 ·EXTENSIONS OF REMARKS 25025' By Mr. STARK: for other purposes; to· the Committee on the By Mr. WINN: . H.R. 9424. A bill to govern the disclosure · Judiciary. H. Con. Res. 270. Concurrent resolution of certain financial information by financial By Mr. ROE: expressing the sense of the Congress that no institutions to governmental agencies, to pro H.R. 9434. A bill to encourage considera person should be ·considered for appointment tect the constitutional rights of citizens of tion of nonstructura.l alternatives to flood. as ambassador or minister if such· person or the United States and to prevent unwar damage prevention; to the Committee on members of his immediate family have con ranted invasions of privacy by prMcribing Public Works. tributed more than $5,000 to a candidate for procedures and standards governing disclo H.R. 9435. A bill to amend the Internal President in the last election; to the Com sure of such information, and for other pur Revenue Code of 1954 to allow an income mittee on Foreign Affairs. poses; to the Committee in Banking and Cur tax deduction for depreciation on capital ex By Mr. GUDE (for himself, Mr. FRA rency. penditures incurred in connecting residential SER, Mr. BROWN o! California, Mr. By Mrs. BURKE of California: sewerlines to municipal sewage systems; to BURTON, Mr. CORMAN, Mr. COUGH H.R. 9425. A bill to require that funds be the Committee on Ways and Means. LIN, Mr. DAVXS of Georgia, Mr. DRI made available for replacement housing in By Mr. ROONEY of Pennsylvania (for NAN, Mr. -
September/October 1988 Gear Technology
Th,eIoumalot Gear' Manufacturin',g SEPTEMBER/O'CTOBER 198B Accurate gear inspection depends on retlat8d dataevaluation. Profit depends on speed. Maag CNC ~1 •• '" three, in the lab and on the shop floor. • Maag mechanical machines 'combine the speed and automatic checldng the reliability of a base circle disc design for profile and lead gear inspection. • Onlly Maag multi-axis electronic machines measure internal and external spur, helical and cluster gears with up to 15 sets of teeth, all in a single setup, with accuracy of .000040 in. • Maag's unique easy-to-use menu programming and software automatically bring the stylus to the moth surface. If you'd like to know how to spot your bad apples quicker, contact American Pfauter, 92,5Estes Ave., Elk 'Grove v.mage, IL 60007. Phone (312) 640-7500. 11111 !I.f" A .• 11-_..1••..:.,:., Iuou,n,· menea. r;nNllnnf'iii MIKRON brings you hob speeds upto 2,000 rpm and high rigidity with the A33/2 gear hObblng machine The model A33/2 is a completely automatic gear hobbing machine with programmable controller. Users realize the full advantages of modem TiN coated hobs while hobbing gears of from 0.151" to 4" (4mm -100mm) outside diameter. The Mikron A33/2 is step-by-step expandable and is available in both automatic and manual load models. It can be fitted with an automatic deburring device and is also suited for skiving with tungsten carbide hobs because of the high rigidity achieved by its horizontal design. write or phone for complete details on this flexible, expandable system and other Mikron hobblng.