The Design of the Proposed 5AT High-Speed 4-6-0 Locomotive
Total Page:16
File Type:pdf, Size:1020Kb
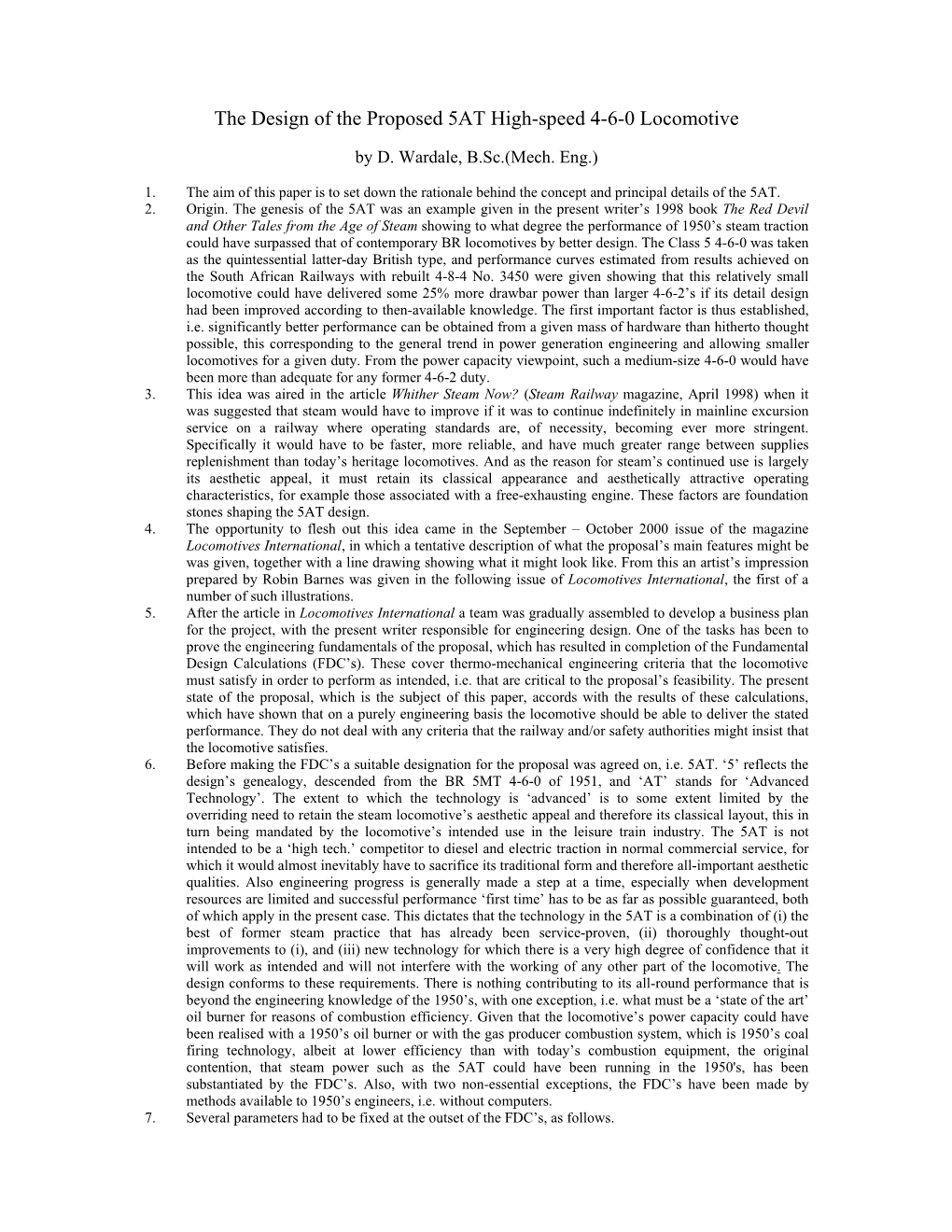
Load more
Recommended publications
-
Scale Models Brassmasters 4Mm SCALE KITS and FITTINGS
Brassmasters Scale Models PO Box 1137 Sutton Coldfield West Midlands B76 1FU www.brassmasters.co.uk 4mm SCALE KITS AND FITTINGS CATALOGUE AND PRICE LIST 1 May 2018 email : [email protected] TERMS OF TRADE All products listed in this catalogue are available direct by mail order or from our stand at selected exhibitions. Details of the exhibitions we attend are advertised in the model press and on our website. Payment Cash, postal order or cheque with order. Unfortunately, we are unable to accept foreign currency or non - Sterling cheques. Please make your postal orders/cheques payable to " BRASSMASTERS ". We can also accept payments in Sterling by electronic credit into the following UK bank account Name: Brassmasters Scale Models Sort code: 090127 Account number: 74795972 Please contact us first to ensure the items are in stock You may find it useful to download our excel Order Form (make sure you save it to your PC before completing your Please email us when you have made the payment We also accept credit card payments for both UK and overseas customers. Email us with your order and we will send you an iZettle invoice which can be paid using your card. For overseas customers only who do not want to pay via credit card, we can take payment via Paypal - please email us for the post & packing charge. Whilst every effort will be made to supply ex-stock, we will notify you if we cannot deliver your order within twenty- eight days. Please bear in mind that this is a part-time hobby business for us; we try to post out twice weekly, but we only collect our post from the PO Box once each week. -
3 Power Supply
3 Power supply Table of contents Article 44 Installation, etc. of Contact Lines, etc. .........................................................................2 Article 45 Approach or Crossing of Overhead Contact Lines, etc................................................ 10 Article 46 Insulation Division of Contact Lines............................................................................ 12 Article 47 Prevention of Problems under Overbridges, etc........................................................... 13 Article 48 Installation of Return Current Rails ........................................................................... 13 Article 49 Lightning protection..................................................................................................... 13 Article 51 Facilities at substations................................................................................................. 14 Article 52 Installation of electrical equipment and switchboards ................................................. 15 Article 53 Protection of electrical equipment................................................................................ 16 Article 54 Insulation of electric lines ............................................................................................ 16 Article 55 Grounding of Electrical Equipment ............................................................................. 18 Article 99 Inspection and monitoring of the contact lines on the main line.................................. 19 Article 101 Records........................................................................................................................ -
The Communication Cord
60163 TORNADO 2007 PRINCE OF WALES 3403 ANON New Steam for the Main Line Building Britain’s Most Powerful Steam Locomotive Recreating Gresley’s last design THE COMMUNICATION CORD No. 60 Winter 2021 The rather wonderful sight of one of the Trust’s two new boilers in the X-ray room at DB Meiningen for analysis of the welded seams. DB Meiningen THE RACE IS ON! by Graham Langer There can be no doubt that the Covid-19 push the P2 project over the line it will & Darlington Railway bi-centenary pandemic has had an extremely negative require a final herculean effort in both celebrations during 2025. We need all the impact on the heritage railway movement terms of fundraising and construction to help we can get from our Covenantors and it will probably be some years before ensure that we meet our deadlines, getting and supporters and one of the best ways the financial damage done can be mended No. 2007 Prince of Wales into steam during to achieve this is to bring new people to and The A1 Steam Locomotive Trust has 2022, into traffic by the end of 2023 and the party – after all, it’s not every day you not been entirely immune. If we are to “front and centre” during the Stockton get the chance to be part of history! TCC 1 CONTENTS EDITORIAL by Graham Langer FROM THE CHAIR by Steve Davies PAGE 1 The race is on! “Nothing great will ever be achieved without great men, he Covid-19 essential pipe runs, conduits and the commitment to the P2; second, please and men are great only if they are determined to be so.” situation, and myriad of other small components act as an ambassador on our behalf and PAGE 2 T So said Charles de Gaulle. -
Circulatic Steam Generator Installation Manual
STEAM GENERATORS CIRCULATIC® STEAM GENERATORS INSTALLATION MANUAL VAPOR POWER INTERNATIONAL 551 S. County Line Rd. Franklin Park, IL 60131 P: 630.694.5500 F: 630.694.2230 VaporPower.com Revised July 2005 Bulletin No. Printed in U.S.A. TWM5-AM-2 CIRCULATIC TABLE OF CONTENTS Section Page No. List of Figures ..................................................................................................................2 List of Tables ...................................................................................................................2 1.0 Introduction .....................................................................................................................3 2.0 Lifting and Handling .........................................................................................................4 3.0 Installation .......................................................................................................................8 4.0 Mounting .........................................................................................................................9 5.0 Clearances .................................................................................................................... 10 6.0 Combustion and Ventilation Air Requirements ............................................................... 12 7.0 Stack Installation ........................................................................................................... 13 8.0 Steam Output ............................................................................................................... -
Hurst Boiler & Welding Company, Inc
Hurst Boiler & Welding Company, Inc. P.O. Drawer 530 - Highway 319 North Coolidge, Georgia 31738 877-99HURST – Toll Free 229-346-3545 – Local 229-346-3874 – Fax www.hurstboiler.com SERIES 45 STEAM BOILER (8.5- 813 HP, STEAM 15 psig) SAMPLE SPECIFICATIONS The following sample specifications are provided by Hurst Boiler & Welding Co., Inc. to assist you in meeting your customer's specific needs and application. The sample specifications are typically utilized as the base template for the complete boiler specification. Contact your local Hurst Boiler & Welding Co., Inc. authorized representative for information on special insurance requirements, special code requirements, optional equipment, or general assistance in completing the specification. 1.0 – General Boiler Specifications 1.1 - The Steam Boiler shall be Hurst Boiler & Welding Co., Inc. Series 45, hp designed for 15 psig. The maximum operating pressure shall be psig and the minimum operating pressure shall be psig. 1.2 - The boiler shall have a maximum output of Btu/hr, or horsepower when fired with oil and/or natural gas, Btu/cu-ft. Electrical power available shall be Volt Phase Cycle. 2.0 – Boiler Design 2.1 - The boiler shall be a three-pass wetback horizontal firebox type boiler with four (4) square feet of fireside heating surface per rated boiler horsepower. Furnace volume shall not be less than cubic feet. It shall be mounted on a heavy steel frame with integral forced draft burner and burner controls. The complete packaged boiler approved as a unit by Underwriters Laboratories and shall bear the UL label. 2.2 - The boiler shall be completely preassembled and tested at the factory. -
O-Steam-Price-List-Mar2017.Pdf
Part # Description Package Price ======== ================================================== ========= ========== O SCALE STEAM CATALOG PARTS LIST 2 Springs, driver leaf........................ Pkg. 2 $6.25 3 Floor, cab and wood grained deck............. Ea. $14.50 4 Beam, end, front pilot w/coupler pocket...... Ea. $8.00 5 Beam, end, rear pilot w/carry iron.......... Ea. $8.00 6 Bearings, valve rocker....................... Pkg.2 $6.50 8 Coupler pockets, 3-level, for link & pin..... Pkg. 2 $5.75 9 Backhead w/fire door base.................... Ea. $9.00 10 Fire door, working........................... Ea. $7.75 11 Journal, 3/32" bore.......................... Pkg. 4. $5.75 12 Coupler pockets, small, S.F. Street Railway.. Pkg.2 $5.25 13 Brakes, engine............................... Pkg.2 $7.00 14 Smokebox, 22"OD, w/working door.............. Ea. $13.00 15 Drawbar, rear link & pin..................... Ea. $5.00 16 Handles, firedoor............................ Pkg.2. $5.00 17 Shelf, oil can, backhead..................... Ea. $5.75 18 Gauge, backhead, steam pressure.............. Ea. $5.50 19 Lubricator, triple-feed, w/bracket, Seibert.. Ea. $7.50 20 Tri-cock drain w/3 valves, backhead.......... Ea. $5.75 21 Tri-cock valves, backhead, (pl. 48461)....... Pkg. 3 $5.50 23 Throttle, nonworking......................... Ea. $6.75 23.1 Throttle, non working, plastic............... Ea. $5.50 24 Pop-off, pressure, spring & arm.............. Ea. $6.00 25 Levers, reverse/brake, working............... Kit. $7.50 26 Tri-cock drain, less valves.................. Ea. $5.75 27 Seat boxes w/backs........................... Pkg.2 $7.50 28 Injector w/piping, Penberthy,................ Pkg.2 $6.75 29 Oiler, small hand, N/S....................... Pkg.2 $6.00 32 Retainers, journal........................... Pkg. -
FLYING SCOTSMAN’ LNER 4-6-2 1:32 SCALE • 45 Mm GAUGE
‘FLYING SCOTSMAN’ LNER 4-6-2 1:32 SCALE • 45 mm GAUGE ENGINEERING SAMPLE SHOWN Sir Nigel Gresley was renowned for his Pacific express locomo- SPECIFICATIONS tives, the first of which, the A1 class, entered service in 1922. The A3 was a modification of the A1 and over time all of the sur- Scale 1:32 viving A1s were rebuilt as A3s. No. 4472 “Flying Scotsman” was Gauge 45 mm built in 1923 and went on to become one of the most famous Mini. radius 6ft 6in. (2 m) steam locomotives in the world setting many records along the way. After the war it was renumbered 103 then, after the nation- Dimensions 26.5 x 3.5 x 5.25 in. alisation, carried the number 60103, remaining in service on the Construction Brass & stainless steel East Coast mainline until 1963. During its service career it cov- Electric Version ered over 2,000,000 miles and travelled non-stop from London Power 0~24V DC to Edinburgh in 8 hours. It was sold into private ownership, was Full cab interior design sent to America and Australia and is today under restoration at Features The National Railway Museum in York. Constant lighting Live Steam Version We are currently developing a 1:32 scale live steam version of our very successful electric LNER A3 Class “Flying Scotsman”. Power Live steam, butane fired The model is gas-fired with slide valves and has all the features Boiler Copper the Gauge 1 fraternity have come to expect from an Accucraft Valve gear Walschaerts valve gear locomotive. -
Conventional Steam
DECEMBER 2019 Application Solutions Guide CONVENTIONAL STEAM Experience In Motion 1 Application Solutions Guide — The Global Combined Cycle Landscape TABLE OF CONTENTS THE GLOBAL CONVENTIONAL STEAM POWER FLOWSERVE PRODUCTS IN CONVENTIONAL PLANT LANDSCAPE . 3 STEAM POWER . 16 A Closer Look at Conventional Steam Conventional Steam Applications Power Technology . 5 Overview . 16 Basics . 5 Pumps for Conventional Steam Plants . 18 Plant Configurations and Sizes . 7 Valves for Conventional Steam Plants . 24 Flue Gas Desulfurization (FGD) . 8 Actuators for Conventional Steam Plants . 30 Conventional Steam Project Models . 11 Seals for Conventional Power Plants . 31 Seals for Wet Limestone Flue Gas THE CONVENTIONAL STEAM POWER- Desulfurization . 33 FLOWSERVE INTERFACE . 13 Business Impact and Focus Areas . 13 COMMUNICATING OUR VALUE . 34 The Big Picture . 13 Innovative Ways Flowserve Addresses The Flowserve Fit in Conventional Customer Challenges . 34 Steam Power . 13 APPENDIX . 35 PRODUCTS FOR STEAM POWER — Flowserve Value Proposition in Conventional Steam . 35 AT A GLANCE . 14 Sub-critical Versus Supercritical Pumps . 14 Power Plant . 36 Valves . 14 Reheat . 37 Seals . 14 Terminology . 38 Estimated Values by Plant Size . 15 Acronyms . 39 2 Application Solutions Guide — Conventional Steam THE GLOBAL CONVENTIONAL STEAM POWER PLANT LANDSCAPE Thermal power generation involves the conversion Combined cycle plants have become the preferred of heat energy into electric power. Fossil fuel power technology for gas-fired power generation for several plants as well as nuclear, biomass, geothermal reasons. The USC plant takes 40 to 50 months to and concentrated solar power (CSP) plants are all build; a combined cycle plant can be built in 20 to examples of thermal power generation. -
A Brief History of Front-End Research and Latest Developments
A Brief History of Front-End Research and Latest Developments Ir. J.J.G. Koopmans Ph.D. Paper presented during the conference on “Developments in modern Steam Traction” in the National Railway Museum in York, 11th of December 2006. 1 Introduction This paper will cover some of the historic highlights of the development of front-ends during the last 200 years. It is also intended to give a phenomenal description of the functioning of a front-end. Illustration and proof of the examples is provided by some of the results of the tests with the RTM 54 steam locomotive. Notion The discussion is about the use of exhausted steam to create artificial draught in the boiler of steam locomotives. Figure 1 Terence Cuneo's painting of the first steam locomotive The history of the front-end started with Richard Trevithick, who mounted a blast pipe from the cylinders to the chimney, and turned its orifice upwards. The 20th century painting by Terence Cuneo, present in the Welsh National Museum, shows this detail together with the feedwater heater around the blast pipe. The picture shows the joyous moment it represents, but this author has some reservations about the way Trevithick is represented, walking with a spanner in his hand. Locomotive owners and engineers have a common and lasting tendency to be on the locomotive themselves! Some 60- years later the first serious research on the subject was started by Prof. Zeuner1. He used a simplified model of a front-end. During the tests he found that certain dimensional ratios in the front-end gave an asymptotic limit to its performance. -
Generation Unit Basics Power System Elements
Power System Elements Generation Unit Basics PJM State & Member Training Dept. PJM©2018 10/2/2018 Objectives • Provide an overview of: ‒ Major components of a Generator ‒ Excitation ‒ Governor Control ‒ Rotational Speed ‒ Generator limitations ‒ VAR/voltage relationship ‒ MW’s and Power Angle PJM©2018 2 10/2/2018 Basic Operating Principles • Electromagnetic induction is the principle used for a generator to convert mechanical energy to electrical energy • D.C. excitation is applied to the rotor field winding producing a magnetic field ‒ Output voltage and VAR flow are controlled by changing the strength of the magnetic field • The field winding (rotor) spins, at synchronous speed, within the armature windings (stator) providing relative motion between the magnetic field and the stationary conductor windings (stator) ‒ A.C. output voltage is induced in the stator armature windings • The changing polarity of the rotor produces the alternating characteristics of the current PJM©2018 3 10/2/2018 PJM©2018 4 10/2/2018 A.C. Generator Components • Rotating Magnetic Field (Rotor) • Series of Stationary Conductors (Stator) • Source of D.C. Voltage (Exciter) PJM©2018 5 10/2/2018 Rotor • The generated voltage is proportional to the: ‒ Strength of the magnetic field ‒ Number of coils and number of windings on each coil ‒ Speed at which the rotor turns • Rotor winding is a multi-coil, single circuit, energized with DC power fed through the shaft from the collector rings ‒ The rotor is a low voltage, low power circuit; a major factor in building a generator -
Full Page Photo
THE LIFE AND TIMES OF A DUKE Martyn J. McGinty AuthorHouse™ UK Ltd. 500 Avebury Boulevard Central Milton Keynes, MK9 2BE www.authorhouse.co.uk Phone: 08001974150 © 2011. Martyn J. McGinty. All rights reserved No part of this book may be reproduced, stored in a retrieval system, or transmitted by any means without the written permission of the author. First published by AuthorHouse 04/25/2011 ISBN: 978-1-4567-7794-4 (sc) ISBN: 978-1-4567-7795-1 (hc) ISBN: 978-1-4567-7796-8 (e) Front Cover Photo: Th e Duke at Didcot (Courtesy P. Treloar) Any people depicted in stock imagery provided by Th inkstock are models, and such images are being used for illustrative purposes only. Certain stock imagery © Th inkstock. Th is book is printed on acid-free paper. Because of the dynamic nature of the Internet, any web addresses or links contained in this book may have changed since publication and may no longer be valid. Th e views expressed in this work are solely those of the author and do not necessarily refl ect the views of the publisher, and the publisher hereby disclaims any responsibility for them. Born out of Tragedy and Riddles, his lineage traceable, unerasable, back through the great houses of Chapelon, Giffard, Stephenson, Belpaire and Watt, the Duke was laid to rust by the sea, a few meagre miles from the mills that shaped the steel that formed the frames that bore the machine that Crewe built. Time passed and the Duke was made well again by kindly strangers. -
Ships Heat Generation Plant Heat Generation Plant Heat
SHIPS HEAT GENERATION PLANT Boilers Water Treatment 2014.07.14 Pag |1 - 94 REPORT: ALVARO SARDINHA BOILERS WATER TREATMENT MARINE ENGINEER DATE: 2014.07.14 [email protected] INDEX 1. Introduction 2. BoilerBoilerssss water treatment ––– three factors 3. Boilers water fundamental knowledge 444.4. Ships heat generation plant 555.5. BoilerBoilerss water treatment 666.6. Main problems in boilers caused by water 777.7. Unex boilerboilerssss water recommendations 888.8. Lessons learned 999.9. Water chemistry terms Pag |2 - 94 REPORT: ALVARO SARDINHA BOILERS WATER TREATMENT MARINE ENGINEER DATE: 2014.07.14 [email protected] 1. INTRODUCTION If boilers water doesn’t receive proper treatment, the boiler will suffer from carryover, sludging, scale and corrosion, leading to weak and dangerous machinery. Long before the boiler fails, water-related problems will cause: ● Growing safety hazard ● Increased maintenance cost ● Additional fuel required - higher energy costs ● Lower boiler efficiency Correct boiler water treatment and follow-up of the water and steam condition, are of utmost importance for keeping the heat generation systems in good condition. By implementing a rigorous program of boiler water treatment, a vessel can greatly extend equipment life, reduce maintenance and enable thermal efficiency to be maintained at the designed level. The present report characterizes a ship heat generation system, its water treatment procedures and maintenance required. The main objective is to document the system and to establish optimal and standard operation processes. It is also an important piece of digital information, part of the ship information system, shareable and available for present and future crews, and a helpful tool to support company management.