Overview of Grain Drying and Storage Problems in India
Total Page:16
File Type:pdf, Size:1020Kb
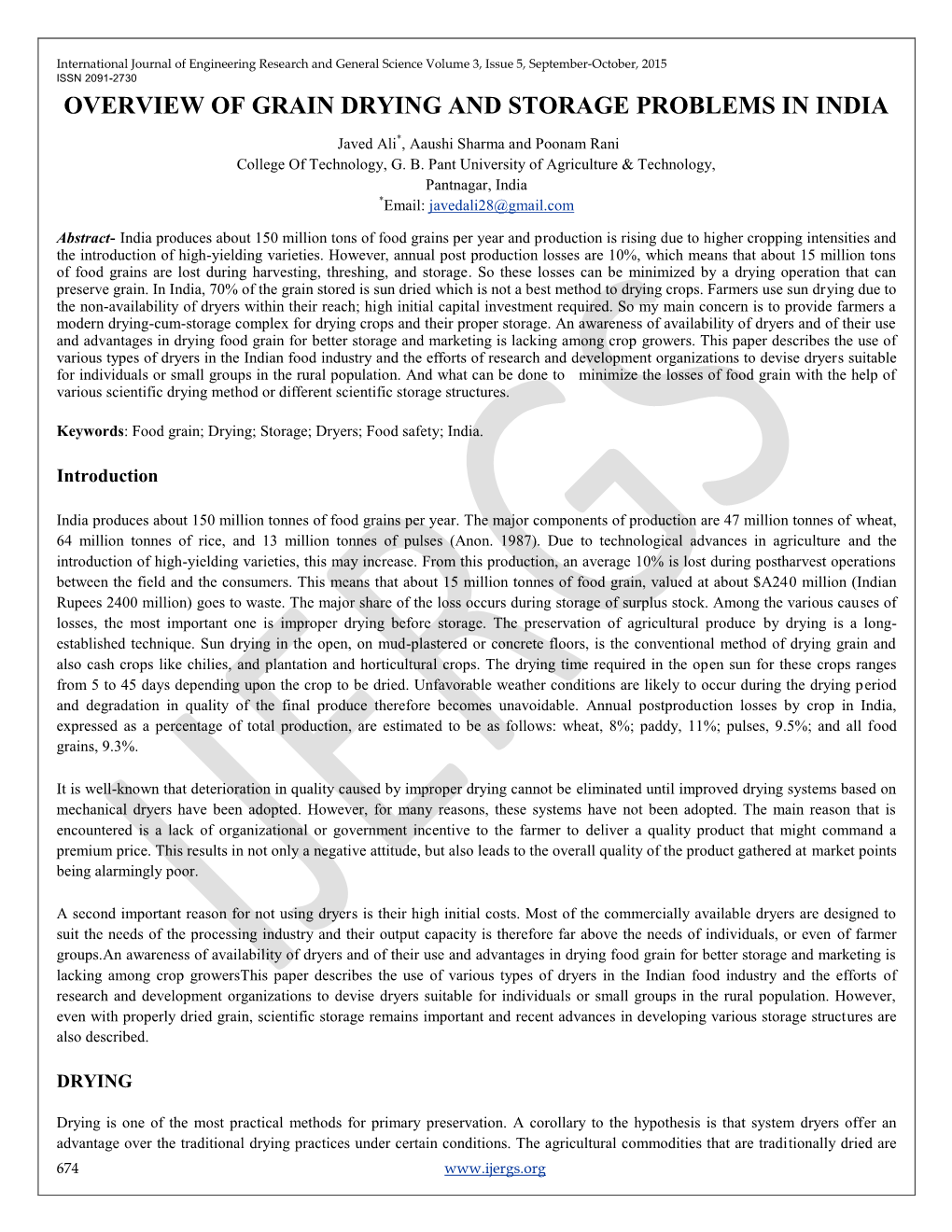
Load more
Recommended publications
-
Grain Crop Drying, Handling and Storage
363 Chapter 16 Grain crop drying, handling and storage INTRODUCTION within the crop, inhibiting air movement and adding Although in many parts of Africa certain crops can be to any possible spoilage problems. The crop must produced throughout the year, the major food crops therefore be clean. such as cereal grains and tubers, including potatoes, One of the most critical physiological factors in are normally seasonal crops. Consequently the food successful grain storage is the moisture content of the produced in one harvest period, which may last for only crop. High moisture content leads to storage problems a few weeks, must be stored for gradual consumption because it encourages fungal and insect problems, until the next harvest, and seed must be held for the respiration and germination. However, moisture next season’s crop. content in the growing crop is naturally high and only In addition, in a market that is not controlled, the value starts to decrease as the crop reaches maturity and the of any surplus crop tends to rise during the off-season grains are drying. In their natural state, the seeds would period, provided that it is in a marketable condition. have a period of dormancy and then germinate either Therefore the principal aim of any storage system must when re-wetted by rain or as a result of a naturally be to maintain the crop in prime condition for as long adequate moisture content. as possible. The storage and handling methods should Another major factor influencing spoilage is minimize losses, but must also be appropriate in relation temperature. -
Spoilage and Heating of Stored Agricultural Products
Spoilage and heating of stored agricultural products Prevention, detection, and control 1 Publication 1823E 1989 Spoilage and heating of stored agricultural products Prevention, detection, and control J.T. Millls Research Station, Winnipeg, Man. Research Branch Agriculture and Agri-Food Canada 2 ©Minister of Supply and Services Although the information contained Canada 1989 in this manual has been carefully researched, neither the author nor Available in Canada through Agriculture Canada can accept responsibility for any problems Authorized Bookstore Agents and that may arise as a result of its other bookstores application. Specific mention of a product type, brand name, or or by mail from company does not constitute endorsement by the Government of Canadian Government Publishing Canada or by Agriculture Canada. Centre Supply and Services Canada Recommendations for pesticide use Ottawa, Canada K1A 0S9 in this publication are intended as guidelines only. Any application of Price subject to change without a pesticide must be in accordance notice with directions printed on the product label of that pesticide as prescribed Cat. No. A53-1823/1988E ISBN 0 under the Pest Control Products Act. 660-13043-2 Always read the label. A pesticide should also be recommended by Staff editor provincial authorities. Because Sheilah V. Balchin recommendations for use may vary from province to province, your provincial agricultural representative should be consulted for specific advice. Canadian Cataloguing in Publication Data Mills, J.T. (John T.) Spoilage and heating of stored agricultural products: prevention, detection and control (Publication: 1823E) Includes index. Bibliography: p. 1. Farm produce -Storage - Diseases and injuries. I. Title. II. Series: Publication (Canada. -
Grain Drying Systems
GEAPS FDC July 28-31, 2002 Grain Drying Systems By Dr. Dirk E. Maier, Ph.D., P.E. Professor and Extension Agricultural Engineer Post-Harvest Education & Research Center Purdue University And Dr. Fred W. Bakker-Arkema, Ph.D. Professor Emeritus Biosystems Engineering Department Michigan State University Written for presentation at the 2002 Facility Design Conference of the Grain Elevator & Processing Society held July 28-31, 2002 in St. Charles, Illinois, U.S.A. 1 GEAPS FDC July 28-31, 2002 Table of Contents Table of Tables.................................................................................................................... 4 Table of Figures .................................................................................................................. 6 Table of Figures .................................................................................................................. 6 Introduction...................................................................................................................... 7 Introduction...................................................................................................................... 7 Basic Drying Concepts ................................................................................................. 8 Moisture Content................................................................................................................. 8 Moisture Shrink.................................................................................................................. -
On-Farm Grain Drying Methods
DIVISION OF AGRICULTURE RESEARCH & EXTENSION UJA--University of Arkansas System Agriculture and Natural Resources FSA1072 OnFarm Grain Drying Methods grain production more attractive Sammy Sadaka, Introduction resulting in more producers and Ph.D., P.E. When grain is harvested from the more production. This increased sup Assistant Professor field, it contains dry matter and water. ply is associated with a larger grain Extension Engineer While water is necessary for price swing between harvest and plant growth and grain production, nonharvest periods. Therefore, in Karl VanDevender, excess moisture after grain maturity addition to more control of harvest can lead to storagerelated problems. timing, there are potential economic Ph.D., P.E. Grain moisture content is expressed advantages to onfarm drying and Professor Extension as a percent of the grain weight. storage. Accordingly, several Arkansas Engineer For example, 100 pounds of 13% producers indicated their interest in moisture content rice contains 13 exploring the possible techniques of Griffiths Atungulu, Ph.D. pounds of water and 87 pounds of dry onfarm grain drying and storage. Assistant Professor matter rice. Grain moisture con This fact sheet provides an overview Grain Processing tent and temperature play a key role of the basics of onfarm grain drying Engineering in determining safe storage life (see and storage methods. https://www.uaex.uada.edu/publications/ pdf/FSA1058.pdf). As a ru le, dryer grain and cooler temperatures increase safe Grain Drying Basics storage durations. In contrast, wetter grain and warmer tempera Storage Moisture Content tures increase the potential for pests, The first step in drying grain is insects, mold and fungi to reduce determining the desired, or target, grain quality and market value. -
Sunflower Production
A-1331 (EB-25 Revised) SSunflunfl oowerwer PProductionroduction SEPTEMBER 2007 2 Foreword The fi rst edition of “Sunfl ower Production and Mar- unless otherwise specifi ed. This publication con- keting Extension Bulletin 25” was published in 1975. tains certain recommendations for pesticides that This publication provided general information for are labeled ONLY for North Dakota. The users of growers, seedsmen, processors, marketing agencies any pesticide designated for a state label must have and Extension personnel. Revised editions followed in a copy of the state label in their possession at the 1978, 1985 and 1994. Interest and knowledge about time of application. State labels can be obtained sunfl ower production and marketing in the U.S. has from agricultural chemical dealers or distributors. increased greatly in the past 30 years. Marketing and USE PESTICIDES ONLY AS LABELED. processing channels have stabilized and have become fairly familiar to growers since 1985, but pest prob- lems have shifted and new research information has Acknowledgements become available to assist in production decisions. The editor is indebted to the contributors for writing This publication is a revision of the “Sunfl ower Pro- sections of this publication. The editor also appreci- duction and Marketing Bulletin” published in 1994. ates the efforts made by previous contributors, as The purpose is to update information and provide a these previous sections often were the starting point production and pest management guide for sunfl ower for current sections. growers. This revised publication is directed primarily to the commercial production of sunfl ower, not to mar- keting and processing. It will attempt to give specifi c guidelines and recommendations on production prac- tices, pest identifi cation and pest management, based on current information. -
The Grain Storage Guide
'$# ($# )=1.A213<? 9.+ -:/*+ CONTENTS Section Summer 2003 1 Preparation 2 Moisture dear member 3 drying – heated air First published in 1999, HGCA’s Grain storage guide was widely accepted by the industry. We – printed 45,000 copies and it is now required 4 drying bulk or near-ambient reading by most assurance schemes. Principles laid down in the original publication remain 5 temperature sound – effective grain storage is crucial to successfully producing and marketing grain. 6 cooling However, legislation, technology and pesticides have all changed, so it is now time for an 7 insects update. 8 Mites New legal limits for ochratoxin A contamination in grain now apply. Treatments that can be used 9 Pest identification on stored grain as part of an integrated strategy have changed. However, check what treatments 10 Fungi your buyer will accept. Warmer winters mean that using ambient air to cool grain takes longer, 11 Pesticides so moisture content assumes greater importance. 12 Rodents & birds Two companion publications now provide more 13 oilseed rape detail on some aspects of grain storage. These are The rodent control guide and Grain 14 Monitoring sampling – a farmer’s guide . Any guide is bound to have a limited ‘shelf life’. References To avoid confusion, I suggest you throw away your old copy and now use this ‘updated’ guide. The Home-Grown Cereals Authority (HGCA) has provided funding for some of the projects on which this document is based but has Yours sincerely not conducted the research or written this guide. While the authors have worked on the best information available to them, neither the HGCA nor the authors shall in any event be liable for any loss, damage or injury howsoever suffered directly or indirectly in relation to the guide or the research on which it is based. -
Overview of On-Farm Natural Air-Drying of Grain
DIVISION OF AGRICULTURE RESEARCH & EXTENSION Agriculture and Natural Resources University of Arkansas System FSA1060 Overview of On-Farm Natural Air-Drying of Grain Sammy Sadaka Introduction occurs, the grain is said to be in Assistant Professor equilibrium with the drying air. The Freshly harvested grains are not Extension Engineer moisture content of the grain when no always dry to a safe moisture content moisture transfer is possible is suitable for marketing or long-term referred to as the equilibrium moisture Griffiths Atungulu storage. Therefore, they may need content (EMC) for a given air tempera Assistant Professor - Grain artificial drying, such as natural air- ture and relative humidity. In Processing Engineering drying, to achieve the target safe addition to temperature and relative storage moisture content. Natural air- humidity of air, the EMC value also drying is a technique for drying grain, depends on the grain type. It should e.g., corn, rice, soybeans, and wheat, be mentioned, that moisture might be to an equilibrium moisture content transferred from the air to the grain with the ambient air. This fact sheet during natural air-drying if the air provides an overview of this on-farm EMC is higher than the moisture natural air-drying technique. It content of the grain. This process is emphasizes the pros and cons as well known as rewetting. as some limitations of this technique. Under the two conditions discussed above, assume that air at Rationalization of temperature of 60°F and relative Natural Air-Drying humidity of 70% is being forced through long grain rice. This rice has Natural air-drying is a technique a moisture content of 18%. -
On-Farm Drying and Storage of Soybeans Sammy Sadaka
Arkansas Soybean Production Handbook CHAPTER DIVISION OF AGRICULTURE RESEARCH & EXTENSION 15 University of Arkansas System On-Farm Drying and Storage of Soybeans Sammy Sadaka Arkansas farmers harvested more than Fundamentals of 3.1 million acres of soybeans in 2013. With a state average of 43 bushels/acre, Arkansas soybean Soybean Drying production reached 133 million bushels. Soybean producers are increasingly interested in on-farm Drying Process drying and storage due to the various advantages they offer. For example, producers can afford to The ultimate goal of soybean drying is to get harvest soybeans early at higher moisture contents rid of the excess moisture in the kernel in order to than normal to reduce the possibility of harvest make it less accessible to living microorganisms, such losses. Additionally, they may harvest soybeans at as fungi and bacteria. In this process, moisture is faster rates if daily harvesting hours can be extended. evaporated from the kernel to the surrounding air. Moreover, on-farm storage may provide marketing Therefore, soybeans are dried in most cases by flexibility and advantage during the soybean passing relatively large volumes of air, either ambient selling process. or heated, through the grain. Figure 15-2 shows an example of an on-farm grain drying and storage site. The quality of the drying air determines the final moisture content of the bean kernels. In addition, the Figure 15-1. Newly harvested soybeans. Since soybean quality is highest at harvest, soybean producers should promptly dry newly harvested beans (Figure 15-1) to safe moisture levels in order to maintain their quality. -
Corn and Soybean Drying and Storage
Grain Storage Best Management Practices Michigan Webinar March 31, 2020 Kenneth Hellevang, Ph.D., P.E. Extension Engineer & Professor Agricultural & Biosystems Engineering Manage - to direct with a degree of skill Monitor: •Temperature •Moisture •Insects •Mold •Carbon dioxide Check Grain Frequently •2-weeks until cooled •2-3 weeks during winter •2-weeks spring & summer Manage: Aerate & Dry • Temperature • Moisture Senses only grain near cable Cable Temperature sensor Temperature indicator Fan Sensors & Fan Controllers Technology does not replace Management! Recommended Long-Term Storage Moisture Content Mold Growth > 70% RH Grain EMC Moisture @ 70ºF, 60% RH Barley 11.8% 12% Canola 8.0% 8% Corn 12.8% 13% Flaxseed 8.3% 8% Soybeans 10.2% 11% Sunflower Non-Oil 9.6% 10% Oil 7.4% 7- 8% Wheat 13.3% 13.5% “Approximate” Allowable Storage Time for Cereal Grains (Days) Cumulative * Exceeds 300 days Moisture ----- Grain Temperature (°F) ----- Content 30º 40º 50º 60º 70º 80º (%) Approximate Allowable Storage Time (Days) 14 * * * * 200 140 15 * * * 240 125 70 16 * * 230 120 70 40 17 * 280 130 75 45 20 18 * 200 90 50 30 15 19 * 140 70 35 20 10 20 * 90 50 25 14 7 22 190 60 30 15 8 3 24 130 40 15 10 6 2 26 90 35 12 8 5 2 28 70 30 10 7 4 2 30 60 25 5 5 3 1 “Approximate” Allowable Storage Time for Soybeans Cumulative * Exceeds 300 days Moisture --- Grain Temperature (°F) --- Content 30° 40° 50° 60° 70° 80° (%) Approximate Allowable Storage Time (Days) 11 * * * * 200 140 12 * * * 240 125 70 13 * * 230 120 70 40 14 * 280 130 75 45 20 15 * 200 90 50 30 15 -
Grain Storage and Seed Processing Plants, Drying Complexes, and Port Terminals
| GB | TURNKEY Grain storage and seed processing plants, drying complexes, and port terminals CONVEYING | DRYING | SEED PROCESSING | ELECTRONIC SORTING | STORAGE | TURNKEY | SERVICE Cimbria Inhouse 05.19 Inhouse Cimbria SOLUTIONS. TOGETHER. CONVEYING | DRYING | SEED PROCESSING | ELECTRONIC SORTING | STORAGE | TURNKEY | SERVICE CIMBRIA | TURNKEY | 3 | TURNKEY SOLUTIONS OUR COMPETENCIES AND MISSION Cimbria is one of the world’s leading manufacturers in the PLANT DESIGN processing, handling and storage of grain and seeds as well PROJECT MANAGEMENT as offering an increasing number of applications involving other types of products. We design, develop, manufacture and install AUTOMATION customer-specific solutions, regardless of whether this involves DOCUMENTATION individual machines, complete processing lines or large turnkey AFTER-SALES SERVICE projects. Our underlying approach always emphasises increasing quality and energy efficiency, as well as reducing operating costs. TRAINING | 4 | GRAIN AND SEED TECHNOLOGIES CIMBRIA - A ONE-STOP COMPANY Cimbria’s project and turnkey solutions comprise one of our six different business areas. With turnkey projects, we extract and leverage all the experience and expertise we have acquired from the other five business areas: transport, drying, seed processing, electronic sorting and storage. By choosing Cimbria as a business partner for large projects, our customers will thus gain a business partner with a range of skills and 70 years of experience in all areas involving the handling of crops. We master all disciplines involving research and development, are highly knowledgeable about the crops, engineering and manufacturing, as well as possessing substantial expertise in professional project management, consulting services, training, site supervision and implementation. From the point at which the order is issued until the warranty period expires, we place complete responsibility in the hands of a senior project manager. -
Appendix B. General Explanation and Census of Agriculture Report Form
Appendix B. General Explanation and Census of Agriculture Report Form DEVELOPMENT OF THE CENSUS internet form to evaluate the feasibility of the online REPORT FORMS submission system. Content test results helped determine final report form content and design. A Before the release of the 2012 Census of Agriculture’s sample copy of the report form and instruction sheet results, NASS had already begun preparations for the is included in this appendix. 2017 Census of Agriculture. The first team assembled was the 2017 Census Content Team, which evaluated DATA CHANGES the content and report form design for the census. They reviewed the 2012 report forms, solicited input Following are descriptions of the report form changes from both internal and external customers, and and their effect on the publication tables. developed criteria for determining acceptable content for inclusion in the 2017 Census of Agriculture. The Crop Data Changes team tested the effectiveness of the 2017 report forms for various modes of data collection (mail, telephone, Added items include: personal interview, and electronic data reporting) and made recommendations to NASS senior executives • Aronia berries for final determination. • Cherimoyas • Chickpeas Throughout development NASS sought the advice • Coffee – first time collected in States other than and input from the data user community. Integral Hawaii partners included the Advisory Committee on • Elderberries Agriculture Statistics, State Departments of • Indian or traditional corn Agriculture and other State government officials, • Raspberries, other Federal agency officials, land grant universities, agricultural trade associations, media, and various Deleted items include: community-based organizations. • Pineapples not harvested NASS conducted a three phase content test (OMB No. -
Harvesting of Rape Seed
HARVESTING OF RAPE SEED Harvesting in general usage includes an immediate post-harvest handling, all of the actions taken immediately after removing the crop - cooling, sorting, cleaning, packing - up to the point of further on-farm processing, or shipping to the wholesale or consumer market. 1. Agronomic requirements For high rape seed efficiency it is necessary to have appropriate harvest technology, good grain and yields, high oil, ground grain quality, but also the following grain features: . Uniformity of maturation, . Mean resistance to lodging, . Resistance to silique's cracking and seed shedding, . Ability of plant to form corn sealed with branches at silique's layer, . The optimum number of branches (4-7 per plant), . Location of the first yielding branch at 40-60 cm height above soil surface, . Resistance to fungal diseases, . Tolerance to delayed harvest date. 1.1. Appropriate crop condition before and during the harvest The time, when rape seed is harvesting, defines its yields too. Rapeseed ready for harvest is a drab brown, a far cry from the bright yellow fields of the crop in flower, and often has a distinct cabbage smell, a reminder that it’s a member of the Brassica family. For example some rape seed’s characteristics in relation of harvesting period are shown in table 1. Table 1. Seeds humidity Mass of 1000 Harvest period Yield, t/ha moisture, % seeds, g Lactic ripeness 68.2 2.38 2.91 Pasty ripeness 64.5 3.16 3.76 Beginning of 64.2 3.63 4.24 Waxy ripeness Middle of Waxy 32.0 4.00 4.72 ripeness Beginning of full 18.0 4.02 4.53 ripeness Swathing can began with the appearance of brown seeds when grain moisture is 30%.