Investigation of Thermo Mechanical Effect on Structure and Properties of Aluminium Alloy 6082
Total Page:16
File Type:pdf, Size:1020Kb
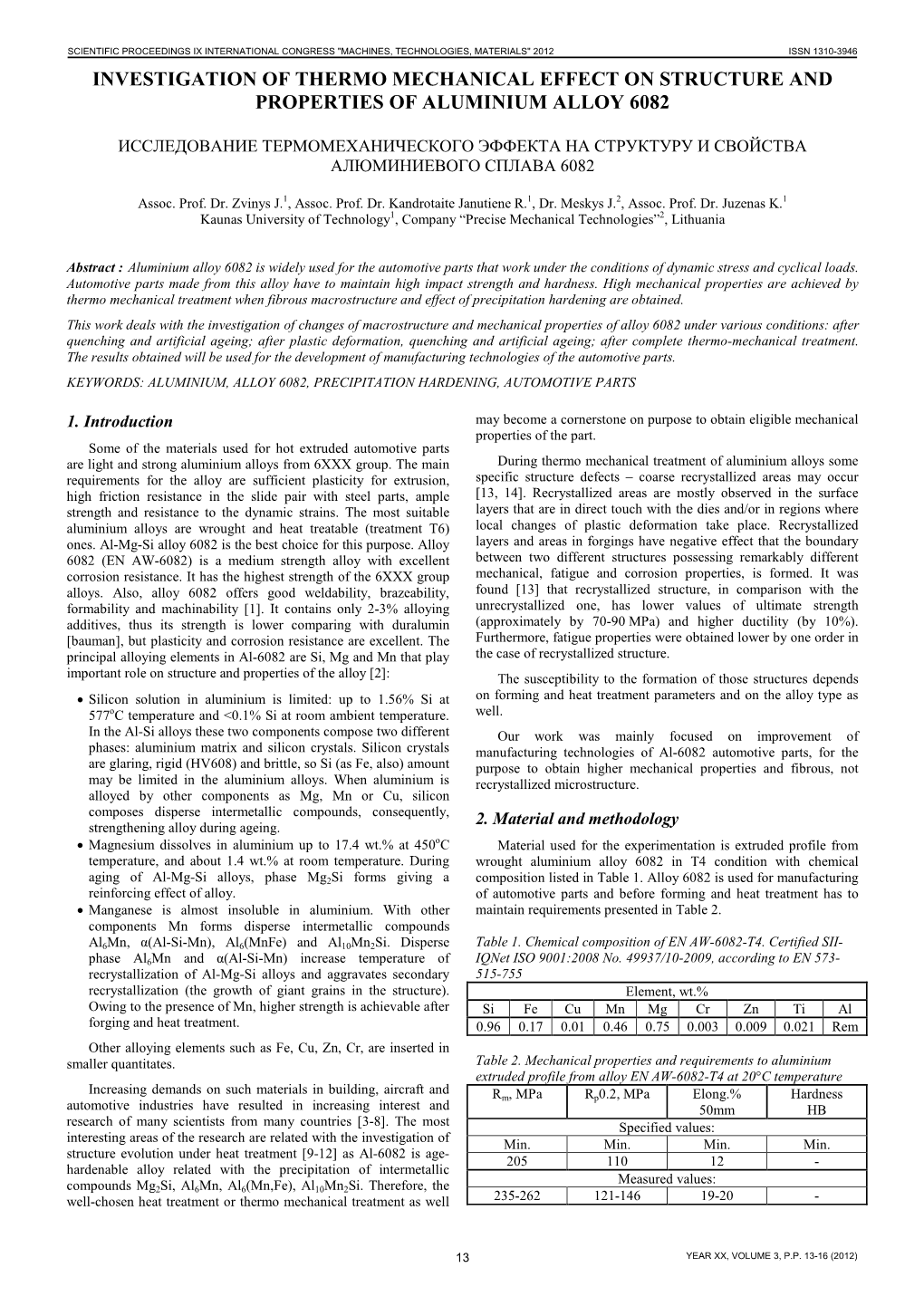
Load more
Recommended publications
-
Studies on Properties of Al–Sic Metal Matrix Composite Material for Making IC Engine Valves
Proceedings of the World Congress on Engineering 2018 Vol II WCE 2018, July 4-6, 2018, London, U.K. Studies on Properties of Al–SiC Metal Matrix Composite Material for Making IC Engine Valves Nilamkumar S. Patel, Ashwin D. Patel, Ritesh Kumar Ranjan, Vikas Rai Abstract-Automobile industries are using material substitution the matrix also helps to transfer load among the composite for to build lighter weight, and fuel efficient engines, offering is compound material which differs from alloy due to fact better properties materials of engine components, including that all the individual component retain its characteristic. engine poppet valves and valve seats. Valves and valve seats are very important components that are used at high operating II. EXPERIMENTAL SET-UP temperature to control the flow and volumetric efficient at desired level of engine performance. The present work Stir casting process is liquid state processing. It is simple describes that Al-SiC composite as possible alternate materials and flexible process. In this process, there is mixing of with its unique capacity to give required properties for engine matrix and reinforcement. poppet valves and valve seats. Al-SiC MMC is prepared by In this process, reinforcement particles are added into the powder metallurgy and various casting techniques. In the research a composite is developed by stir casting process by molten matrix metal. And then the proper mixture is done using aluminium alloy with silicon carbide Nano particles and by hand stirring as well as Mechanical stirring. And then substitute sintering operation at 600oC temperature for one this mixture is allowed to pour into the mould shape. -
A Review on Comparison of Aluminium Alloy LM-25 with Al/Sic
International Research Journal of Engineering and Technology (IRJET) e-ISSN: 2395-0056 Volume: 05 Issue: 01 | Jan-2018 www.irjet.net p-ISSN: 2395-0072 A review on comparison of Aluminium alloy LM-25 with Al/Sic Rahul Ushir1 , Kunal Gandhi2, Gaurav Dahe3, Vijay Bidgar4, Prof. Vishal Thakre5. 1,2,3,4 BE student Mechanical, SND COE & RC, YEOLA, Maharashtra, India 5Prof. Mechanical, SND COE & RC, YEOLA, Maharashtra, India ---------------------------------------------------------------------***--------------------------------------------------------------------- Abstract- Many industries suffered a great loss of materials and procedures to decrease the wear of devices manufacturing process due to collapse of manufacturing and designing segments. These incorporate change of mass machines due to wear and fail of lubrication. Friction is main properties of the materials, surface medications and cause of wear and energy dissipation. Improving friction can utilization of covering, and so on. In the course of the most make substantial saving. It is obvious that enormous amount recent couple of years, numerous endeavors have been made of the worlds resources are used to overcome friction in the to comprehend the wear conduct of the surfaces in sliding form or another. Lubrication is an effective means of contact and the instrument, which prompts wear. The controlling wear and reducing friction. Hence, for the survival applications of aluminium and its alloys for the machine of machine wear and friction must be decreased parts are increasing day to day in the industry. However, and/controlled carefully. little has been reported on the wear behaviour of aluminium and its alloys with the addition of grain refiner and modifier. Key words: Silicon Carbide(Sic) , aluminium LM25,scanning electron microscope ( SEM ) , metal PROBLEM DEFINITION: matrix composite ( MMCs) . -
Maec.19 70 (University of London) London
COMPLEX & INCREMENTAL STRESS CREEP OF A HIGH STRENGTH ALUMINIUM ALLOY AT ELEVATED TEMPERATURES (ALLOY: HIDUMINIUM RR58 SPECIFICATION DTD 731) by SURINDAR BAHADUR MATHUR Thesis presented in the Department of Mechanical Engineering for the Award of the Doctor of Philosphy in Mechanical Engineering of the University of London. Mechanical Engineering Department Imperial College of Science and Technology mAec.19 70 (University of London) London. ABSTRACT A theory for creep rates under complex and incremental stresses is deduced from experimental data concerning complex creep at elevated temperatures for the test material HIDUMINIUM RR 58 - Specification DID 731. The most important results are for tubular specimens tested at 150°C and 250°C under incremental loads. The analysis of results relates to steady state creep only. Modified relationships in stress equivalence and strain equivalence are proposed to account for thermal softening, polygonization, recrystallization and the resulting exaggerated flow in the direction of the applied shear. (The original equations are based on the hypothesis of Von Mises). A further relationship is suggested between the immediate total energy of distortion and the subsequent creep work rate. Results of the static tests and the results of the tests for creep behaviour under complex loading are presented and compared with the results of static torsion and simple incremental torsion creep tests on the basis of the proposed equations. An appendix describes the complex creep testing machine, furnace, extensometers -
The Effect of Cooling Rate on the Microstructure of A356 Aluminium Alloy
SVOA MATERIALS SCIENCE & TECHNOLOGY (ISSN: 2634-5331) Research https://sciencevolks.com/materials-science/ Volume 2 Issue 4 The Effect of Cooling Rate on the Microstructure of A356 Aluminium Alloy Maftah H. Alkathafi1*, Abdalfattah A. Khalil2, Ayad O. Abdalla3 Affiliations: 1Mechanical Engineering Department, Faculty of Engineering, Sirte University, Libya 2Materials Science Department, Faculty of Engineering, Omer Al-Mukhtar University, Libya. 3College of Mechanical Engineering Technology, Benghazi-Libya. *Corresponding author: Maftah H. Alkathafi* Mechanical Engineering Department, Faculty of Engineering, Sirte University, Libya Received: December 10, 2020 Published: December 31, 2020 Abstract: In this study a fast-cooling technology is employed for a cast iron mould to prepare cast A356 aluminium alloy by solidifica- tion of the molten metal. The cooling rate is achieved by pouring the molten alloy into a preheating permanent mould at different temperatures (25, 100, 200, 300 and 4000C) for cast samples with 40 mm inside diameter and 200 mm height. The samples considered are analyzed by optical microscopy, scanning electron microscopy (SEM), and EDS X-ray analysis (EDS). The effects of cooling rate on the morphology of α – aluminum and eutectic silicon of A356 alloy have been studied. The results showed that the dendritic structure of α-phase was broken and converted into a somewhat globular grain structure and the coarse acicular eutectic silicon trend to be broken and converted into short sticks or small rounded in other cases. Keywords: A356 Aluminum alloy, Grain refinement, Cooling rate, SEM, EDS, Microstructure. 1. Introduction Aluminium alloys have attractive physical and mechanical properties. They are lightweight, low costs production, easy to machine and have good recycling possibilities up to 95 % [1]. -
Aluminium Alloy - 6262 - T6 Extrusions
Aluminium Alloy - 6262 - T6 Extrusions SPECIFICATIONS CHEMICAL COMPOSITION Commercial 6262 BS EN 573-3:2009 Alloy 6262 EN 6262 Element % Present Magnesium (Mg) 0.80 - 1.20 Aluminium alloy 6262 is a heat treatable alloy with Copper (Cu) 0.15 - 1.40 very good corrosion resistance and strength. Additions of bismuth to the alloy mean that 6262 has excellent Silicon (Si) 0.40 - 0.80 machinability and surface finish. Lead (Pb) 0.40 - 0.70 High-speed steel or carbide tooling can be used to obtain smooth finishes. Heavy cutting requires oil Bismuth (Bi) 0.40 - 0.70 lubricant but light cutting can be done dry. Iron (Fe) 0.0 - 0.70 Alloy 6262 can be used in place of 2011 when higher corrosion resistance and better anodising response is Zinc (Zn) 0.0 - 0.25 required. Chromium (Cr) 0.04 - 0.14 Applications Titanium (Ti) 0.0 - 0.15 6262 is commonly used in the manufacture of: Manganese (Mn) 0.0 - 0.15 Screw machine products Camera parts Others (Total) 0.0 - 0.15 Nuts Other (Each) 0.0 - 0.05 Couplings Aluminium (Al) Balance Marine fittings Decorative hardware and appliance fittings Hinge pins Oil line fittings ALLOY DESIGNATIONS Valves and valve parts Aluminium alloy 6262 also corresponds to the following standard designations and specifications but may not PLEASE NOTE: Due to European Environmental be a direct equivalent: Protection Directives: AA6262 # 2000/53/CE-ELV – For the automotive sector Al 1.0Mg 0.6Si Pb # 2002/95/CE-RoHS – For the electrical and A96262 electronics sector This alloy has been replaced by Alloy 6026 which has a PLEASE NOTE: Due to European Environmental lower Lead content. -
Fatigue Behavior of 2618-T851 Aluminum Alloy Under Uniaxial and Multiaxial Loadings
Open Archive Toulouse Archive Ouverte (OATAO) OATAO is an open access repository that collects the wor of some Toulouse researchers and ma es it freely available over the web where possible. This is an author's version published in: https://oatao.univ-toulouse.fr/24572 Official URL : https://doi.org/10.1016/j.ijfatigue.2019.105322 To cite this version : BenaÕssa, Malek and Mabru, Catherine and Chaussumier, Michel Fatigue behavior of 2618-T851 aluminum alloy under uniaxial and multiaxial loadings. (2020) International Journal of Fatigue, 131 (105322). 1-9. ISSN 0142-1123 Any correspondence concerning this service should be sent to the repository administrator: [email protected] Fatigue behavior of 2618-T851 aluminum alloy under uniaxial and multiaxial loadings ⁎ Benaïssa Malek, Catherine Mabru, Michel Chaussumier Université de Toulouse, Institut Clément Ader (ICA), UMR CNRS 5312, UPS/INSA/ISAE/ Mines Albi, 3 Rue Caroline Aigle, 31400 Toulouse, France ABSTRACT Keywords: AA2618 aeronautical aluminum alloy has been largely used in the past, especially in well-known Concorde AA2618-T851 aircraft, developed during sixties decade. In more recent aircraft, this alloy has been largely replaced by others Multiaxial fatigue such as 7075 which present greater fatigue resistance. Forgotten for a time, AA2618 comes back in new aircrafts Roughness for structural parts submitted to fatigue loading at high temperature because of only a slight decrease of fatigue Crossland criterion resistance of this alloy compared to room temperature fatigue resistance. In this paper, a complete fatigue characterization of 2618-T851 aluminum alloy is presented: fatigue tests under uniaxial tensile or torsion cyclic loadings, with mean tensile or shear stress have been realized; fatigue tests under combined tensile-torsion, in or out-of-phase have also been conducted as well as some combined tensile-torsion-internal pressure fatigue tests. -
Tribological Behavior and Hardness Properties of Heat Treated Al 7075-Beryl-Graphene Hybrid Metal Matrix Composites
International Journal of Recent Technology and Engineering (IJRTE) ISSN: 2277-3878, Volume-8 Issue-3, September 2019 Tribological Behavior and Hardness Properties of Heat Treated Al 7075-Beryl-Graphene Hybrid Metal Matrix Composites Shanawaz Patil, Mohamed Haneef mirror frames, house members, serving trays and cooking Abstract— The emerging technologies and trends of the utensils. Even in the field of engineering applications, the present generation require downsizing the unwieldy structures to aluminum and its alloys plays vigorous role as an aerospace, lightweight structures. Aluminum matrix composites are tailored space, and automotive components material of increasing candidate materials for aerospace applications due to their outstanding greater strength to weight ratio and low wear rate. In value because of its properties which includes diverse range this study, Al7075 alloy-Beryl-Graphene hybrid composites are of uses are appearance, lightweight and has a low density of developed by using stir casting process. Graphene weight range 2.7 to 2.8 gm/cm3 which is almost one-third of steel percentage was varied from 0 wt. % to 2 wt. % in steps of 0.5 wt. %. (7.83 gmcm3)[-,5]. One of the foremost usually used metal Whereas for Beryl 6 wt. % is used thorough out the study. The alloy for structural application is Al7075 due to its enticing casted specimens were heat-treated at T6 solutionizing wide-ranging properties like low density, improved strength, temperature of 530±5oC for 8 hours. After the heat treatment the specimen are quenched in boiling Water and Ice. The ductility, toughness, and resistance to fatigue. Al7075 alloy microstructure of the newly developed hybrid MMCs has been has been extensively used in aircraft structure elements and investigated by TEM and SEM. -
A Survey of Al7075 Aluminium Metal Matrix Composites
International Journal of Science and Research (IJSR) ISSN (Online): 2319-7064 Index Copernicus Value (2013): 6.14 | Impact Factor (2013): 4.438 A Survey of Al7075 Aluminium Metal Matrix Composites Rajendra .S .K1, Ramesha .C .M2 1Research Scholar, Jain University, Bengaluru, Department of Industrial Engineering and Management, Dr. Ambedkar Institute of Technology, Bengaluru 2Department of Mechanical Engineering, M S Ramaiah Institute of Technology, Bengaluru Abstract:A composite material is a combination of two or more chemically distinct and insoluble phases; its properties and structural performance are superior to those of the constituents acting independently. Metals and ceramics, as well, can be embedded with particles or fibers, to improve their properties; these combinations are known as Metal-Matrix composites. Aluminum 7075 alloy constitutes a very important engineering material widely employed in the aircraft and aerospace industry for the manufacturing of different parts and components. It is due to its high strength to density ratio that it a sought after metal matrix composite. In this paper we present a survey of Al 7075 Metal Matrix Composites. Keywords: Metal Matrix Composites (MMC’s), Aluminium Metal Matrix, Beryl, Al7075, Aluminium alloy 1. Introduction Aluminium alloy 7075 is an aluminium alloy, with zinc as the primary alloying element. It is strong, with a strength The effects of research in Aluminium based Metal Matrix comparable to many steels, and has good fatigue strength and Composites (MMC’s) are far reaching these days. These average machinability, but has less resistance to corrosion composites find various applications in the automobile than many other Al alloys. Its relatively high cost limits its industry, the aerospace industry and in defence and marine use to applications where cheaper alloys are not suitable. -
THE VACUUM CHAMBERIN the INTERACTION REGIÓN of PARTIÓLE COLLIDERS: a HISTORICAL STUDY and DEVELOPMENTS IMPLEMENTED in the Lhcb EXPERIMENT at CERN
Departamento de Física Aplicada a la Ingeniería Industrial Escuela Técnica Superior de Ingenieros Industriales THE VACUUM CHAMBERIN THE INTERACTION REGIÓN OF PARTIÓLE COLLIDERS: A HISTORICAL STUDY AND DEVELOPMENTS IMPLEMENTED IN THE LHCb EXPERIMENT AT CERN Autor: Juan Ramón Klnaster Refolio Ingeniero Industrial por la E.T.S.I. Industriales Universidad Politécnica de Madrid Directores: Raymond J.M. Veness Ph; D. Mechanics of Materials and Plasticity University of Leicester (England) Linarejos Gámez Mejías Doctor Ingeniero Industrial por la E.T.S.I.I. Universidad Politécnica de Madrid 2004 Whatever you dream, you can do, begin it! Boldness has power, magic and genius in it Goethe Homo sum: humani nihil a me alienum puto (Je suis homme, et rien de ce que est humain ne m'est étraxiger) Terence Loving softly and deeply... Elsje Tout proche d'étre un Boudha paresseusement réve le vieux pin Issa En nuestra cabeza, en nuestro pecho es donde están los circos en que, vestidos con los disfraces del tiempo, se enfrentan la Libertad y el Destino Jünger This Thesis has been possible thanks to the support of many people that duñng last 15 months have helped me in different ways. I would like to thank my co- lleagues R. Aehy, P. Bryant, B. Calcagno, G. Corii, A. Gerardin, G. Foffano, M. Goossens, C. Hauvüler, H. Kos, J. Kruzelecki, P. Lutkiewicz, T. Nakada, A. Rossi, J.A. Rubio, B. Szybinski, D. Tristram, B. Ver- solatto, L. Vos and W. Witzeling for their contribu- tions in different moments. Neither would I have ever managed to finish it without those moments of peace shared with mes fréres d'Independance et Verité á VOr :. -
Microstructual and Thermal Analysis of Aluminum-Silicon and Magnesium-Aluminum Alloys Subjected to High Cooling Rates
University of Windsor Scholarship at UWindsor Electronic Theses and Dissertations Theses, Dissertations, and Major Papers 2012 Microstructual and Thermal Analysis of Aluminum-Silicon and Magnesium-Aluminum Alloys Subjected to High Cooling Rates Paul Marchwica University of Windsor Follow this and additional works at: https://scholar.uwindsor.ca/etd Recommended Citation Marchwica, Paul, "Microstructual and Thermal Analysis of Aluminum-Silicon and Magnesium-Aluminum Alloys Subjected to High Cooling Rates" (2012). Electronic Theses and Dissertations. 5572. https://scholar.uwindsor.ca/etd/5572 This online database contains the full-text of PhD dissertations and Masters’ theses of University of Windsor students from 1954 forward. These documents are made available for personal study and research purposes only, in accordance with the Canadian Copyright Act and the Creative Commons license—CC BY-NC-ND (Attribution, Non-Commercial, No Derivative Works). Under this license, works must always be attributed to the copyright holder (original author), cannot be used for any commercial purposes, and may not be altered. Any other use would require the permission of the copyright holder. Students may inquire about withdrawing their dissertation and/or thesis from this database. For additional inquiries, please contact the repository administrator via email ([email protected]) or by telephone at 519-253-3000ext. 3208. Microstructual and Thermal Analysis of AlSi and MgAl Alloys Subjected to High Cooling Rates By Paul C. Marchwica A Thesis Submitted to the Faculty of Graduate Studies through the Department of Mechanical, Automotive and Materials Engineering in Partial Fulfillment of the Requirements for the Degree of Master of Applied Science at the University of Windsor Windsor, Ontario, Canada 2012 © 2012 P. -
Contribution À La Caractérisation Thermique Et Mécanique De La Zone Soudée En FSW Nejah Jemal
Contribution à la caractérisation thermique et mécanique de la zone soudée en FSW Nejah Jemal To cite this version: Nejah Jemal. Contribution à la caractérisation thermique et mécanique de la zone soudée en FSW. Génie mécanique [physics.class-ph]. Arts et Métiers ParisTech, 2011. Français. NNT : 2011ENAM0046. pastel-00766216 HAL Id: pastel-00766216 https://pastel.archives-ouvertes.fr/pastel-00766216 Submitted on 17 Dec 2012 HAL is a multi-disciplinary open access L’archive ouverte pluridisciplinaire HAL, est archive for the deposit and dissemination of sci- destinée au dépôt et à la diffusion de documents entific research documents, whether they are pub- scientifiques de niveau recherche, publiés ou non, lished or not. The documents may come from émanant des établissements d’enseignement et de teaching and research institutions in France or recherche français ou étrangers, des laboratoires abroad, or from public or private research centers. publics ou privés. 2011-ENAM-0046 École doctorale n° 432 : Sciences des Métiers de l’Ingénieur Doctorat ParisTech T H È S E pour obtenir le grade de docteur délivré par l’École Nationale Supérieure d'Arts et Métiers Spécialité “ Génie Mécanique ” présentée et soutenue publiquement par Nejah JEMAL le 13 décembre 2011 Qualification du domaine de soudabilité en soudage par friction malaxage Directeur de thèse : Franck GIROT Co-encadrement de la thèse : Laurent LANGLOIS Co-encadrement de la thèse : Jean-Eric MASSE Jury M. Abdellatif IMAD, Professeur, LML, Polytech Lille Président T M. Christophe DESRAYAUD, Professeur, LCG, Ecole des Mines de Saint-Etienne Rapporteur M. Guillaume RACINEUX, Professeur, GeM, Ecole Centrale Nantes Rapporteur H M. -
O Rigin Al a Rticle
International Journal of Mechanical and Production Engineering Research and Development (IJMPERD) ISSN (P): 2249–6890; ISSN (E): 2249–8001 Vol. 9, Issue 6, Dec 2019, 627–642 © TJPRC Pvt. Ltd. THE EFFECT OF ADDING MAGNESIUM TO THE FILLER MATERIAL ON THE TENSILE PROPERTIES OF TIG WELDED AA 6082 ALUMINIUM ALLOY SUDHEESH. N1 & K. THIRUNAVUKKARASU 2 1Research Scholar, Department of Mechanical Engineering, Karpagam Academy of Higher Education, Coimbatore, India 2Senior Professor, Department of Mechanical Engineering, Karpagam Academy of Higher Education, Coimbatore, India ABSTRACT Aluminium 6082 is a moderate strength alloy with good weldability. Tungsten inert gas (TIG) welding is the most common welding process of this alloy. AA6082 is one of the major alloys used in automotive, shipbuilding, aircraft and structural applications. Tensile strength of welded joints is an important design parameter when it is used for these applications. ER 4043, which contains 5% silicon as major alloying element and ER5356, which contains 5% magnesium as major alloying element, are the most common filler materials used for the welding of AA6082 alloys. In the present investigation, magnesium is added to silicon- based ER 4043 filler wire at different percentage levels, and this new filler wire with altered chemical Original Article Original composition is used for welding of 6082 aluminium plates. The effect of adding magnesium to the filler wire is investigated by using design of experiments. From experiments it is found that this new filler wire is capable of providing higher tensile strength for the welded joint. It is found that the increase in the tensile strength is due to the formation of magnesium silicide intermetallic phase in the weld zone.