Installation of Existing Lift Systems for the Handicapped on Light Rail Vehicles
Total Page:16
File Type:pdf, Size:1020Kb
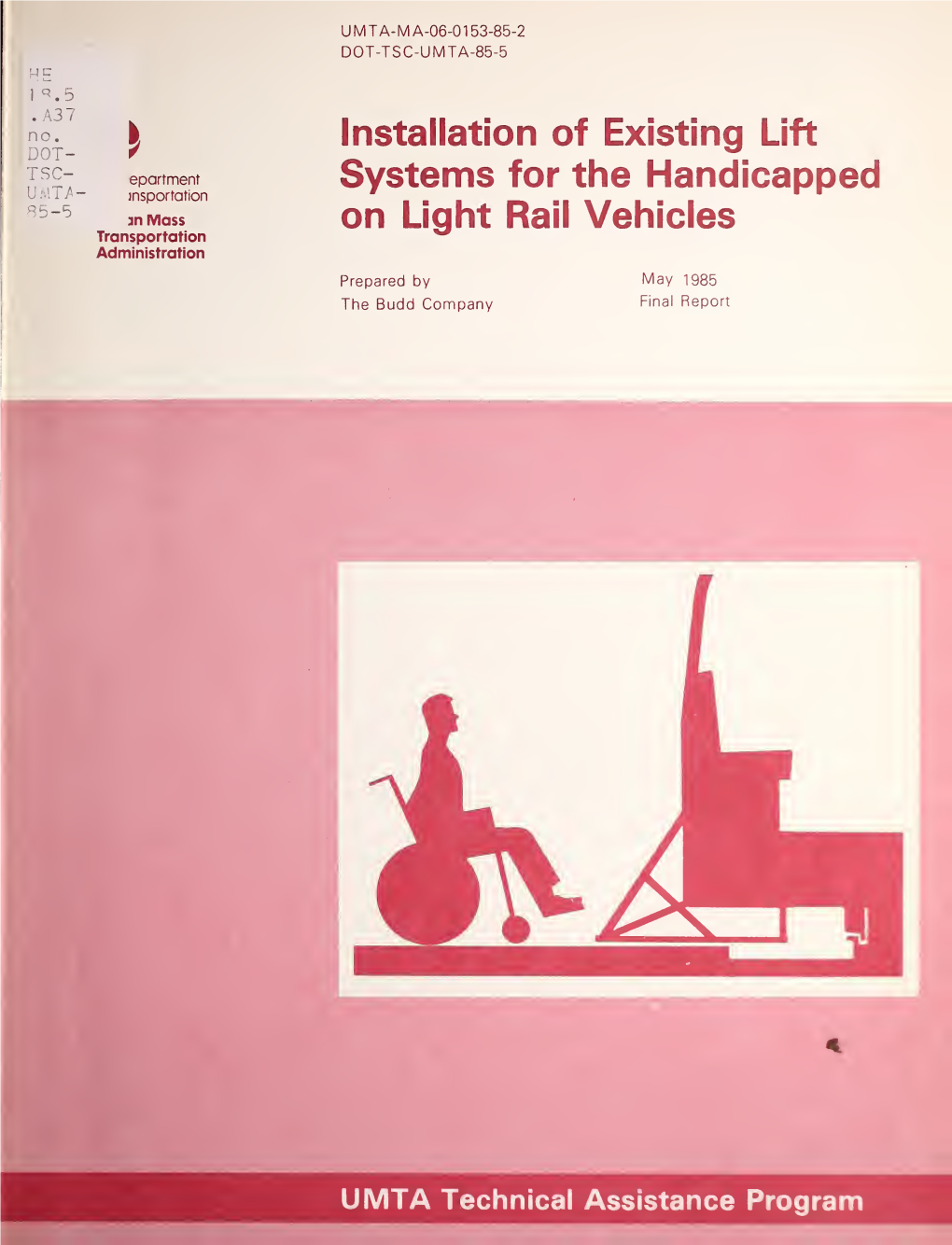
Load more
Recommended publications
-
Outside Lands Outside Lands History from the Western Neighborhoods Project 2 Where in West S.F.? (Previously Issued As SF West History)
OutsideSan Francisco HistoryLands from Western Neighborhoods Project Volume 14, No. 1 Jan–Mar 2018 100 Years of the Twin Peaks Tunnel I NS I DE 1 Inside the Outside Lands OUTSIDE LANDS History from the Western Neighborhoods Project 2 Where in West S.F.? (Previously issued as SF West History) January-March 2018: Volume 14, Number 1 3 OpenSFHistory Highlight John Martini remembers Fleishhacker Pool EDITOR: Woody LaBounty CONTRIBUTORS: Angus Macfarlane, John Martini, and Arnold Woods 6 Roosevelt History, Part One The Story of a Richmond District school Board of Directors 2018 by Angus Macfarlane Chelsea Sellin, President Jamie O’Keefe, Vice President Anisha Gupta, Secretary 10 Westward the Course of Empire Takes its David Gallagher, Treasurer Way–100 Years of the Twin Peaks Tunnel Richard Brandi, David Chang, Nicole Meldahl, Kyrie Whitsett, Arnold Woods by Arnold Woods Staff: Woody LaBounty, Dave Lucas 15 Thank You to Our Donors Advisory Board Those who supported us in 2017 Cammy Blackstone, Al Harris, Gretchen Hilyard, Brady Lea, Felicity O’Meara, Paul Rosenberg, Nate Tico, and Lorri Ungaretti 20 Historical Happenings The WNP Event Calendar Western Neighborhoods Project 4016 Geary Boulevard, Suite A 22 A Home for History San Francisco, CA 94118 New WNP digs at 1617 Balboa Street Tel: 415/661-1000 Email: [email protected] Website: www.outsidelands.org facebook.com/outsidelands twitter.com/outsidelandz instagram.com/westernneighborhoods/ Cover: Mayor Rolph driving the first streetcar out of the west portal of the Twin Peaks tunnel, February 3, 1918. (wnp15.174) © 2018 Western Neighborhoods Project. All rights reserved. Inside the Outside Lands Woody LaBounty estern Neighborhoods Project from the neighborhoods recon- (that’s us), the nonprofit with a nected, but just as many strangers mission to preserve and share became new friends in sharing their Wlocal history, now has a public space love of history and of the west side for exhibits, presentations, and com- of San Francisco. -
California State Rail Plan 2005-06 to 2015-16
California State Rail Plan 2005-06 to 2015-16 December 2005 California Department of Transportation ARNOLD SCHWARZENEGGER, Governor SUNNE WRIGHT McPEAK, Secretary Business, Transportation and Housing Agency WILL KEMPTON, Director California Department of Transportation JOSEPH TAVAGLIONE, Chair STATE OF CALIFORNIA ARNOLD SCHWARZENEGGER JEREMIAH F. HALLISEY, Vice Chair GOVERNOR BOB BALGENORTH MARIAN BERGESON JOHN CHALKER JAMES C. GHIELMETTI ALLEN M. LAWRENCE R. K. LINDSEY ESTEBAN E. TORRES SENATOR TOM TORLAKSON, Ex Officio ASSEMBLYMEMBER JENNY OROPEZA, Ex Officio JOHN BARNA, Executive Director CALIFORNIA TRANSPORTATION COMMISSION 1120 N STREET, MS-52 P. 0 . BOX 942873 SACRAMENTO, 94273-0001 FAX(916)653-2134 (916) 654-4245 http://www.catc.ca.gov December 29, 2005 Honorable Alan Lowenthal, Chairman Senate Transportation and Housing Committee State Capitol, Room 2209 Sacramento, CA 95814 Honorable Jenny Oropeza, Chair Assembly Transportation Committee 1020 N Street, Room 112 Sacramento, CA 95814 Dear: Senator Lowenthal Assembly Member Oropeza: On behalf of the California Transportation Commission, I am transmitting to the Legislature the 10-year California State Rail Plan for FY 2005-06 through FY 2015-16 by the Department of Transportation (Caltrans) with the Commission's resolution (#G-05-11) giving advice and consent, as required by Section 14036 of the Government Code. The ten-year plan provides Caltrans' vision for intercity rail service. Caltrans'l0-year plan goals are to provide intercity rail as an alternative mode of transportation, promote congestion relief, improve air quality, better fuel efficiency, and improved land use practices. This year's Plan includes: standards for meeting those goals; sets priorities for increased revenues, increased capacity, reduced running times; and cost effectiveness. -
Improving West Side Transit Access
STRATEGIC ANALYSIS REPORT SAR 15/16-1 Improving West Side Transit Access INITIATED BY COMMISSIONER KATY TANG SAN FRANCISCO COUNTY TRANSPORTATION AUTHORITY REPORT CREDITS Rachel Hiatt and Chester Fung (Interim Co-Deputy Directors for Planning) oversaw the study and guided the preparation of the report. Ryan Greene-Roesel (Senior Transportation Planner) managed the project and led all research and interviews, with assistance from Camille Guiriba (Transportation Planner) and interns Sara Barz, David Weinzimmer, Evelyne St-Louis, and Emily Kettell. TILLY CHANG is the Executive Director of the San Francisco County Transportation Authority. PHOTO CREDITS Uncredited photos are from the Transportation Authority photo library or project sponsors. Unless otherwise noted, the photographers cited below, identified by their screen names, have made their work available for use on flickr Commons: https://www.flickr.com/, with the license agreements as noted. Cover, top left: Daniel Hoherd 2 Cover, top right: Jason Henderson for SFBC Cover, bottom: James A. Castañeda 3 p. 1: Charles Haynes 4 p. 6: Tim Adams 1 p. 8: Daniel Hoherd 2 – Licensing information: 1 https://creativecommons.org/licenses/by/2.0/legalcode 2 https://creativecommons.org/licenses/by-nc/2.0/legalcode 3 https://creativecommons.org/licenses/by-nc-nd/2.0/legalcode 4 https://creativecommons.org/licenses/by-sa/2.0/legalcode REPORT DESIGN: Bridget Smith SAN FRANCISCO COUNTY TRANSPORTATION AUTHORITY 1455 Market Street, 22nd Floor, San Francisco, CA 94103 TEL 415.522.4800 FAX 415.522.4829 EMAIL [email protected] WEB www.sfcta.org STRATEGIC ANALYSIS REPORT • IMPROVING WEST SIDE TRANSIT ACCESS SAN FRANCISCO COUNTY TRANSPORTATION AUTHORITY • FEBRUARY 2016 WEST PORTAL STATION Contents 1. -
San Francisco Transit Effectiveness Project
A partnership between the San Francisco Controller’s Office and the Municipal Transportation Agency, which oversees Muni. San Francisco Transit Effectiveness Project BRIEFING BOOK Nelson Nygaard DPOTVMUJOHBTTPDJBUFT JULY 2006 TABLE OF CONTENTS TABLE OF FIGURES Introduction to the TEP ........................................... 1-1 Figure.1-1. Stakeholder.Input.Structure........................ 1-2. Introduction................................................................ 1-1 Figure.1-2. Muni.Transit.Vehicles.and.Lines................. 1-4 TEP.Goals.................................................................. 1-1 Figure.1-3.. Schematic.Diagram.of.Current.. Major.Tasks................................................................. 1-2 . Muni.Service.Network................................ 1-4 Who.is.Involved.......................................................... 1-2 Figure.5-1. Peer.Comparison:..Transit.Agency. Schedule...................................................................... 1-3 . (including.bus.and.rail).............................. 5-3 About.this.Briefing.Book............................................. 1-3 Figure.5-2. Percent.of.Passenger.Trips.Carried. Muni.System.Overview............................................... 1-4 . by.Each.Mode............................................ 5-5 Figure.5-3. Cost.Effectiveness.(Cost.per.passenger.trip)..5-6 Key Issues for the TEP ............................................. 2-2 Figure.5-4.. Average.System.Operating.Speed................ 5-8 Introduction............................................................... -
Chase Center Parking and Transportation
LOCATION / GENERAL INFORMATION WARRIORS WAY GARAGE NORTHWEST ENTRY PLAZA WARRIORS WAY RETAIL NORTH ESPLANADE UBER TOWER NORTHWEST RAMP ESPLANADE 3RD STREET GARDENS SPACE THRIVE CITY WEST RETAIL MAIN PLAZA ENTRANCE BAYFRONT PARK GATEHOUSE 3RD STREET TERRY FRANCOIS BOULEVARD (TFB) SOUTHWEST RAMP SOUTH EAST UBER TOWER ENTRANCE 16TH STREET RAMP SOUTHEAST SOUTHWEST PLAZA PLAZA LOADING DOCK ENTRANCE 16TH STREET MISSION STATEMENT ARENA ADDRESS SHIPPING ADDRESS Chase Center and the Golden State Warriors are committed to diversity, Chase Center Chase Center equity and inclusion, and believe our individual experiences, backgrounds 1 Warriors Way 400 16th Street and perspectives help drive innovation and create an environment of San Francisco, CA 94158 San Francisco, CA 94158 empowerment. We believe in strength in numbers – on the court and of the court – fostering a culture where every person is valued and heard, to build a more inclusive and open community for all. DRIVING DIRECTIONS From East Bay From South Bay From Peninsula From North Bay 1. Take the Bay Bridge (80 West ) 1. Take 101 North 1. Take 280 North 1. Take 101 South 2. Get off at the 5th Street Ext 2. Exit at Vermont 2. Exit at Mariposa 2. Exit Cesar Chavez East 3. Make Left on 5th Street 3. Continue Straight onto Mariposa 3. Make Right onto Mariposa 3. Continue on Cesar Chavez 4. Make Left onto Brannan Street 4. Stay on Mariposa till 3rd Street 4. Continue to Chase Center 4. Make left onto 3rd Street 5. Make Right onto 4th Street 5. Make Left on 3rd Street 5. Continue up 3rd Street 6. -
San Francisco Municipal Transportation Agency Board of Directors and Parking Authority Commission Minutes
SAN FRANCISCO MUNICIPAL TRANSPORTATION AGENCY BOARD OF DIRECTORS AND PARKING AUTHORITY COMMISSION MINUTES Tuesday, January 7, 2020 Room 400, City Hall 1 Dr. Carlton B. Goodlett Place REGULAR MEETING 1 P.M. SFMTA BOARD OF DIRECTORS Malcolm Heinicke, Chair Gwyneth Borden, Vice Chair Cheryl Brinkman Amanda Eaken Steve Heminger Cristina Rubke Art Torres Jeffrey Tumlin DIRECTOR OF TRANSPORTATION Roberta Boomer SECRETARY ACCESSIBLE MEETING POLICY The San Francisco Municipal Transportation Agency Board of Directors/Parking Authority Commission meeting will be held in Room 400, at 1 Dr. Carlton B. Goodlett Place (400 Van Ness Ave.), San Francisco, CA. The closest accessible BART station is the Civic Center Station at United Nations Plaza and Market Street. Accessible Muni transit serving this location are: Muni Metro lines J-Church, K-Ingleside, L Taraval, M Ocean View, N Judah and T Third at Van Ness and Civic Center Stations; F Market-Wharves; 19 Polk, 47 Van Ness; 49 Mission-Van Ness; 5 Fulton; 5R Fulton; 6 Haight-Parnassus, 7 Haight-Noriega 7R Haight-Noriega; 21-Hayes; 9 San Bruno; 9R San Bruno Rapid and 71 Haight-Noriega. For information about Muni accessible services, call 415.701.4485. The meeting room is wheelchair accessible. Accessible curbside parking spaces have been designated on the Van Ness Avenue and McAllister Street perimeters of City Hall for people with mobility impairments. There is accessible parking available within the underground Civic Center Garage at the corner of McAllister and Polk streets and within the Performing Arts Garage at Grove and Franklin streets. To obtain a disability-related accommodation, including auxiliary aids or services, or to obtain meeting materials in alternative format, please contact Roberta Boomer at 415.701.4505. -
Track & System Improvements
TWIN PEAKS TUNNEL Track & System Improvements The Twin Peaks Tunnel, which runs between West Portal and Castro TIMELINE stations, will undergo a major rehabilitation and replacement of its 40+ year old infrastructure, including fixtures that are original to the tunnel, When: circa 1917. The new tracks will improve safety and reliability for Muni trains and keep the tunnel in good working condition. Summer 2018 Planned work includes replacing tracks and track infrastructure, replacing Muni Metro Changes: the drainage system, repairing tunnel walls and ceilings, completing Bus substitute for M Ocean seismic upgrades to the original east entrance of the tunnel (Eureka Valley View and L Taraval; K station), and making structural repairs and inspections. Ingleside operating modified Construction is expected to start summer 2018 during a single closure up train route to 60 days long. Transit service will be modified during construction. Bus Routes Affected: Twin Peaks Tunnel opened for service on February 3, 1918. A vital 48, 57, Nx, L OWL, 91 OWL connection between downtown San Francisco and southern and western neighborhoods, the tunnel carries over 80,000 customers daily. sfmta.com/twinpeaks Taraval Bus Ingleside • SF Zoo via Dewey/Woodside to Castro • Trains will operate between Sloat/St. Francis Station (will not stop at Church or West and Balboa Park Station and continue as Portal Stations) J Church to Embarcadero • Transfer at Sloat/St. Francis for M Ocean Ocean View Bus View or Forest Hill Shuttle buses • Balboa Park via West Portal/Vicente to • Transfer to BART for faster trips Church Station (will not stop at Forest Hill downtown or Castro Stations) To downtown Taraval & WawonaDewey & Woodside Church Castro 48 Taraval & MUNI METRO 14th Ave SF Zoo • J, N, T, and S trains running increased service. -
Muni Metro Guide 1986
METRO GUIDE INTRODUCTION Welcome to Muni Metro! This brochure introduces you to Muni's light rail system, and offers a full descrip tion of its features. Five lines operate in the Muni Metro. Cars of the J, K, L, M and N lines run in the Market Street subway downtown, and branch off to serve dif ferent neighborhoods of the city. Tunnel portals are located at Duboce Avenue and Church Street and at West Portal. The light rail vehi cles feature high/low steps at center doors. In the subway, these steps remain flush with the car floor and station platforms. For street operation, the steps lower for easy access to the pavement. SUBWAY STATIONS MEZZANINE Muni Metro has nine subway stations: Embarcadero, The mezzanine is the Montgomery, Powell, Civic Center, Van Ness, Church, level immediately below Castro, Forest Hill, and West Portal. the street, where you pay your fare and enter STATION ENTRANCES the Metro system. At Embarcadero, Mont Orange Muni or BART/ gomery, Powell, and Muni signposts mark Civic Center Stations, subway entrances on Muni Metro shares the the street. Near the top mezzanine with BART, of the stairs, brown the Bay Area Rapid Transit system. BART and Muni signs list the different maintain separate station agent booths and faregates. Metro lines which stop Muni booths are marked with orange and BART with below. blue. Change machines may be used by all passen gers. Ticket machines issue BART tickets only. Though BART and Muni share the mezzanine level, they do not share the same platforms andrai/lines. Be sure to choose the right faregates. -
San Francisco Municipal Transportation Agency Board of Directors Policy and Governance Committee
SAN FRANCISCO MUNICIPAL TRANSPORTATION AGENCY BOARD OF DIRECTORS POLICY AND GOVERNANCE COMMITTEE NOTICE OF MEETING AND CALENDAR Tuesday, April 27, 2021 Due to the COVID-19 health emergency and to protect our Board Members, SFMTA staff, and members of the public, the Board’s Meeting Room at One South Van Ness Avenue is closed. Members of the public are encouraged to participate remotely. If you want to ensure your comment on any item on the agenda is received by the Committee in advance of the meeting, please send an email to [email protected] by 5pm on Monday, April 26 or call (415)646- 4470. REMOTE MEETING ACCESS WATCH ONLINE: Click here to join the meeting PUBLIC COMMENT CALL IN: 888-363-4734, ACCESS CODE: 7014320 REGULAR MEETING 9:00 A.M. COMMITTEE Cheryl Brinkman, Chair Gwyneth Borden Sharon Lai Jeffrey Tumlin DIRECTOR OF TRANSPORTATION Caroline Celaya Manager, Public Records Requests ORDER OF BUSINESS 1. Call to Order 2. Roll Call 3. Approval of Minutes March 23, 2021 Regular Meeting 4. Public Comment Members of the public may address the Committee on matters that are within the Committee's jurisdiction and are not on today's calendar. 5. Presentation, discussion and possible action regarding the SFMTA 2021 20-Year Capital Plan. ADJOURN The Ethics Commission of the City and County of San Francisco has asked us to remind individuals and entities that influence or attempt to influence local legislative or administrative action may be required by the San Francisco Lobbyist Ordinance [S.F. Campaign and Governmental Conduct Code section 2.100 et seq.] to register and report lobbying activity. -
Calworks Eligibility Handbook
CalWORKs Eligibility Handbook Table Of Contents CalWORKs Handbook ..............................................................................................................................1 50 - Intake...........................................................................................................................................1 50-3 Actions and Applications .........................................................................................................1 50-3.1 Appointments in Intake......................................................................................................12 50-3.2 Emergency Benefit Request: Immediate Needs, Expedited Services, and Homeless Assistance Assessment..................................................................................................................16 50-3.3 Applications for a Child Already on Aid...............................................................................27 50-11 Evidence..............................................................................................................................29 50-20 Social Security Number Requirements.................................................................................35 50-24 Form CW 5 - Veterans' Benefit Verification and Referral......................................................45 50-27 Inter-County Transfers - Incoming .......................................................................................48 50-28 Intraprogram Transfer Between Foster Care and CalWORKs................................................52 -
PRESS RELEASE** SFMTA Weekend Transit and Traffic Advisory for Weekend of Saturday, May 15, 2021
FOR IMMEDIATE RELEASE May 13, 2021 Contact: Erica Kato [email protected] **PRESS RELEASE** SFMTA Weekend Transit and Traffic Advisory for Weekend of Saturday, May 15, 2021 San Francisco—The San Francisco Municipal Transportation Agency (SFMTA) releases the following upcoming event-related traffic and transit impacts for this weekend, from Friday, May 14 through Sunday, May 16, 2021. For real-time updates, follow us on https://twitter.com/sfmta_muni or visit SFMTA.com/EmailText to sign up for real-time text messages or email alerts. For details of Muni re-routes, visit SFMTA.com/Updates. This website will be updated when it is closer to the event date. For additional notifications and agency updates, subscribe to our blog, Moving SF for daily or weekly updates. Federal Law Requires Face Masks on Muni To help stop the spread of COVID-19, federal law requires wearing a mask in Muni stations, when purchasing a ticket and while waiting for, boarding, riding or exiting transit. Masks are also required on paratransit and in taxis. Violations can result in denial of boarding or removal from Muni and may carry federal penalties. Face coverings like scarves and bandanas do not meet this requirement. For more information, please visit sfmta.com/COVID. UPDATED: Muni Service During the COVID-19 Shelter-In-Place Order On Saturday, May 15, the K Ingleside and N Judah metro lines will resume train service: • N Judah: Full route service restored between Ocean Beach (Judah at La Playa) and 4th at King streets. On weekdays, service will be provided between 5 a.m. -
SFMTA Taraval Signage
Modified Signage and Pavement Markings Requiring Vehicles to Stop Behind Light Rail Vehicles Stopped to Board or Alight Passengers Final Evaluation Report CTCDC Experiment 16-07 Submitted to: California Traffic Control Devices Committee Submitted by: San Francisco Municipal Transportation Agency March 2018 2 Table of Contents Contents Executive Summary ....................................................................................................................................... 3 Background ................................................................................................................................................... 4 Experimental Treatments ............................................................................................................................. 6 Experiment Locations.................................................................................................................................... 8 Evaluation Methodology ............................................................................................................................... 9 Results and Analysis .................................................................................................................................... 10 Recommendations ...................................................................................................................................... 13 CTCDC Experiment 16-07: Modified Signage and Pavement Markings Requiring Vehicles to Stop Behind Light Rail Vehicles Stopped to Board or