Consumption on the Woolen System and Worsted Combing 1999 Summary Issued June 2000
Total Page:16
File Type:pdf, Size:1020Kb
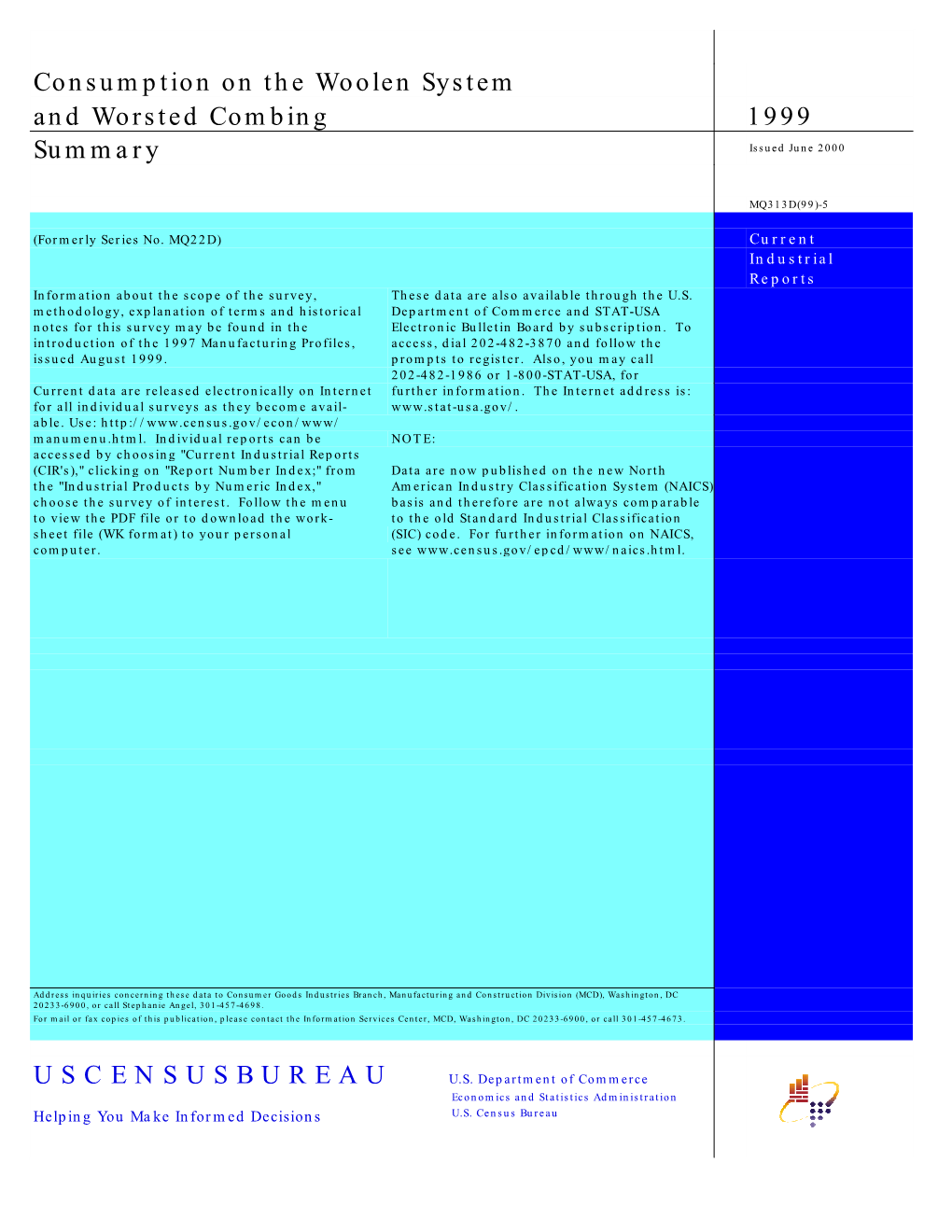
Load more
Recommended publications
-
A Research on Yarn and Fabric Characteristics of Acrylic/Wool/Angora Blends
(REFEREED RESEARCH) A RESEARCH ON YARN AND FABRIC CHARACTERISTICS OF ACRYLIC/WOOL/ANGORA BLENDS AKRİLİK/YÜN/ANGORA LİFİ KARIŞIMLARINDAN ÜRETİLEN İPLİK VE KUMAŞLARIN ÖZELLİKLERİ ÜZERİNE BİR ARAŞTIRMA Gamze SÜPÜREN MENGÜÇ * Ege University, Emel Akın Vocational Training School, 35100, Bornova-İzmir, Turkey Received: 05.01.2016 Accepted : 09.03.2016 ABSTRACT Acrylic fibers are one of the most commonly used synthetic fibers and due to its low thermal conductivity, good shape retention and durability properties, they have a large application area in knitted garment industry. Acrylic fibers are also used in blends to benefit from more prominent features of other fibers. Wool with having good wrinkle resistance, moisture absorption and warmth is a good blend material for acrylic. In order to get superior tactile properties, luxury animal fibers can also be used in acrylic blends, despite there are spinning difficulties and production limitations for these fibers. In this study, acrylic fiber and its blends with wool and Angora rabbit fiber were investigated for their yarn and fabric properties. According to the experimental results and the statistical analyses, it was concluded that, blending acrylic fiber with wool and Angora rabbit fiber, increases the CVm, thin/thick places and neps of the yarn. Yarns containing 100% acrylic and 70% acrylic/10% wool/20% angora have the highest tensile strength. In case of yarn friction coefficients, 70% acrylic /20% wool /10% angora containing yarn has the highest coefficient of yarn to pin and yarn to yarn friction values. However, 70% acrylic/30% angora and 100% acrylic yarns have lower values, supplying smoother yarn surface. -
Textile Industry Needs Christopher D
The Journal of Cotton Science 21:210–219 (2017) 210 http://journal.cotton.org, © The Cotton Foundation 2017 ENGINEERING & GINNING Textile Industry Needs Christopher D. Delhom, Vikki B. Martin, and Martin K. Schreiner ABSTRACT lthough the immediate customer of the gin is Athe cotton producer, the end user of the ginned The immediate customers of cotton gins are lint is the textile mill, retailers, and eventually the the producers; however, the ultimate customers consumer. Thus, it is essential for the ginner to are textile mills and consumers. The ginner has satisfy both the producers and the textile industry. the challenging task to satisfy both producers and Consequently, the ginner needs to be aware of the the textile industry. Classing and grading systems needs of the textile industry. are intended to assign an economic value to the The intent of the cotton classing and grading bales that relates to textile mill demands and the system is to assign an economic value to the bale that quality of the end product. International textile documents its properties as it relates to the quality of mills currently are the primary consumers of U.S. the end product. Since the last edition of the Cotton cotton lint where it must compete against foreign Ginners Handbook in 1994, the customers of U.S. origins. International textile mills manufacture cotton have changed radically, shifting from primar- primarily ring-spun yarns, whereas domestic mills ily domestic to international mills. International mills manufacture predominantly rotor spun yarns. Pro- have been accustomed primarily to hand-harvested ducers and ginners must produce cottons to satisfy cotton that has been processed at slow ginning all segments of the industry, i.e., domestic and in- rates. -
Determination of Dehairing, Carding, Combing and Spinning Difference from Lama Type of Fleeces
International Journal of Applied Science and Technology Vol. 2 No. 1; January 2012 Determination of dehairing, carding, combing and spinning difference from Lama type of fleeces Franka1, E.N., Hicka, M.V.H. and Adotb, O. a.- SUPPRAD2 Program, Catholic University of Córdoba, Argentina b.- SUPPRAD Program. Habitat Foundation, Buenos Aires, Argentina Abstract Mixed fleeces as Llama fleeces, require a special textile process known as dehairing. This process behaves differently according to the Lama type of fleeces dehaired. Dehairing generates structural modifications on textile raw material as it eliminates the longer and straighter (coarser) fibres. This has a marked effect on the following worsted or woolen spinning processes. This work was designed for to test these effects with the objective to report how the type of fleeces affects dehairing, worsted or woolen combing and spinning performances. From a textile behavior point of view, a higher fiber diameter variation was detected in double coated fleeces than in luster fleeces. Luster fleeces have a lower bulk potential than double coated fleeces and a lower comb yield due to the higher dehairing effect. It is also this type that produces less ends protruding from the yarn, which may account in part for their diminished prickle effect. Key words: Lama fibre, textile trials, bristle, prickle, coarse fibres. 1. Introduction A characteristic peculiar to the fibre of South American Camelids (SAC) is the presence of a mixed fleece. This is the reason for their textiles processing requiring „dehairing‟ to achieve a superior quality product, because this process consists in the removal of the coarser fibers (Russel, 1990). -
Start Spinning: Everything You Need to Know to Make Great Yarn Ebook
START SPINNING: EVERYTHING YOU NEED TO KNOW TO MAKE GREAT YARN PDF, EPUB, EBOOK Maggie Casey | 120 pages | 01 Apr 2008 | Interweave Press Inc | 9781596680654 | English | Loveland, CO, United States Start Spinning: Everything You Need to Know to Make Great Yarn PDF Book To make two-ply yarn, take two singles strands or both ends of the same strand , attach them both to your spindle, and twist them around each other in the opposite direction from how you originally spun them. When you spin, you put twist into fibres so that they hold together to form a continuous thread. Navajo Plying - Making a three-ply yarn 8. Designed to appeal to the beginning spinner, tips and hints are provided that illustrate how easy, enjoyable, and relaxing spinning can be. When I was in Kenya, women spun Romney wool chiefly "in the grease," but it often locked in large amounts of dirt in the process. Spin spin spin! Covers fiber characteristics, preparation and spinning, choosing a wheel, and crafting the finished yarn into useful and attractive pieces. I Made It! Leave the original loop of fiber anchored on the spindle hook. Description If you are a knitter or crocheter looking to take the step from just using manufactured yarn to making your own this is a great book to get you started. A bunch of loose fibers will fall apart if you pull on their ends. Launching a Patreon! First and foremost, you want a balanced drop spindle that spins true. Either one will do just fine to learn on. It is also much easier to learn to spin wool than silk, or cotton and other vegetable fibres. -
Mechanical Properties of Unidirectional Epoxy Matrix Composites Reinforced with Scutched Flax and Tow By-Product
ECCM16 - 16TH EUROPEAN CONFERENCE ON COMPOSITE MATERIALS, Seville, Spain, 22-26 June 2014 MECHANICAL PROPERTIES OF UNIDIRECTIONAL EPOXY MATRIX COMPOSITES REINFORCED WITH SCUTCHED FLAX AND TOW BY-PRODUCT N. Martina*,c, P. Daviesb, C. Baleya aLIMATB, EA 4250, Univ. Bretagne-Sud, 56100 Lorient, France bMarine Structures Laboratory, IFREMER, 29280 Plouzané, France cVan Robaeys Frères, 83 rue Saint-Michel, 59122 Killem, France *[email protected] Keywords: Flax fibers, Scutching, Flax by-products, Composite materials Abstract The decortication of flax by scutching yields scutched flax and tows. In this study, we have compared the properties of composite materials made of scutched flax and flax tows from the same batch. A series of unidirectional epoxy composites were manufactured by wet moulding. Mechanical properties of single fibers and composite materials were measured by tensile tests. The tensile properties of single fibers were in the same range. The tensile properties of the unidirectional composites show a similar evolution of properties versus fiber volume fraction. The results show that tows could be used to reinforce high performance composite materials. 1. Introduction A wide range of plant fibers have been studied for composite reinforcement including hemp, jute, sisal and flax [1]. Among them, flax fibers have excellent specific mechanical properties and are being evaluated as a replacement for E-glass fibers [2,3]. Flax (Linum usitatissimum) is the major plant fiber cultivated in northern Europe, mainly for the textile sector. The structure and composition of flax plants is complex [4,5]. The stems contain fiber bundles embedded in cortex tissues at the periphery. In these bundles, single fibers are grouped together by middle lamellae. -
Solutions for Textile Industry
Solutions for Textile Industry Textile MARKETS & APPLICATIONS Textile 3 Textile Preparation Process Page 4 to 9 Spinning & Yarn Finishing Page 10 to 17 Fabric production Page 18 to 21 The widest range of solutions for Textile processing and machinery Bonfiglioli also provides solutions for: Being one of the leading companies in drive technology and a reliable long-term partner with extensive know-how in the textile machine sector, Bonfiglioli drive FOOD & BEVERAGE specialists work side by side with your machine experts to develop tailored and PROCESSING forward-thinking integrated solutions for your requirements. This covers the entire drive including solutions for Industry 4.0 Applications. LOGISTICS & INDUSTRIAL CRANES Our drive system portfolio has the suitable features to respond to the demanding environment typical of the textile sector, characterized by air polluted by fibers, high ambient temperatures and management of occasionally mains failures. PACKAGING PROCESSES This, combined with a comprehensive range of Professional Services, enables us to fulfill your requirements with tailored solutions aimed at minimizing the WAREHOUSE & Total Cost of Ownership of plants through significant reduction of maintenance MATERIAL HANDLING efforts, energy consumption, and process downtimes. www.bonfiglioli.com Products for all types of textile applications: • Bale opening • Synthetic Yarn extrusion • Doubling & Twisting • Cleaning & Blending • Roving • Dyeing • Carding • Ring spinning • Direct warper/Beaming machine • Pre drawing • Air-jet spinning • Weaving • Lapping • Rotor spinning • Warp knitting • Combing • Winding • Cutting machine 4 Preparation Process Cleaning & Blending 1 Page 6 Synthetic Yarn Extrusion Page 9 4 Carding Page 7 2 www.bonfiglioli.com Textile 5 Combing Page 8 3 6 Preparation Process Cleaning & Blending 1 Bonfiglioli product range presents the suitable features to operate in the harsh environment conditions, such as high dust and humidity, typical of the preparation phase. -
Consumption on the Woolen System and Worsted Combing
CORE Metadata, citation and similar papers at core.ac.uk Provided by SNHU Academic Archive Consumption on the Woolen System and Worsted Combing: 2002 Issued June 2003 Summary MQ313D(02)-5 Current Industrial Reports Current data are released electronically on Internet and STAT-USA by subscription. The Internet for all individual surveys as they become avail- address is: www.stat-usa.gov/. Follow the able. Use: http://www.census.gov/mcd/. prompts to register. Also, you may call Individual reports can be accessed by choosing 202-482-1986 or 1-800-STAT-USA, for "Current Industrial Reports (CIR)," clicking on further information. "CIRs by Subsector;" then choose the survey of interest. Follow the menu to view the PDF file or For general CIR information, explanation of to download the worksheet file (WK format) to general terms and historical note, see the your personal computer. appendix. These data are also available on Internet through the U.S. Department of Commerce Address inquiries concerning these data to Consumer Goods Industries Branch, Manufacturing and Construction Division (MCD), Washington, DC 20233- 6900, or call Robert Lee, 301-763-4637. For mail or fax copies of this publication, please contact the Information Services Center, MCD, Washington, DC 20233-6900, or call 301-763-4673. U S C E N S U S B U R E A U U.S. Department of Commerce Economics and Statistics Administration Helping You Make Informed Decisions U.S. CENSUS BUREAU Table 1. Summary of Fibers Consumed in Woolen Spinning and Worsted Combing: 1998 to 2002 [Thousands -
Transatlantic Trade in Woollen Cloth 1850-1914: the Role of Shoddy
University of Nebraska - Lincoln DigitalCommons@University of Nebraska - Lincoln Textile Society of America Symposium Proceedings Textile Society of America 1990 Transatlantic Trade In Woollen Cloth 1850-1914: The Role Of Shoddy David T. Jenkins University of York Follow this and additional works at: https://digitalcommons.unl.edu/tsaconf Part of the Art and Design Commons Jenkins, David T., "Transatlantic Trade In Woollen Cloth 1850-1914: The Role Of Shoddy" (1990). Textile Society of America Symposium Proceedings. 607. https://digitalcommons.unl.edu/tsaconf/607 This Article is brought to you for free and open access by the Textile Society of America at DigitalCommons@University of Nebraska - Lincoln. It has been accepted for inclusion in Textile Society of America Symposium Proceedings by an authorized administrator of DigitalCommons@University of Nebraska - Lincoln. -25- TRANSATLANTIC TRADE IN WOOLLEN CLOTH 1850-1914: THE ROLE OF SHODDY conditions. The nature and scale of the problem did not permit easy and DAVID T. JENKINS rapid solutions. The raw materials, technology and labour skills required for all-wool worsted production were quite different and a Department of Economics and Related Studies, University of York, York, rapid conversion to French methods of wool preparation and spinning was Y01 5DD, England. not quickly feasible. The British industry instead pursued a policy, initially rather slowly, of adapting its existing machinery and THE WORSTED CLOTH TRADE innovating new products, notably worsted coatings. In the two decades The factors affecting European trade and competition in worsted before the First World War it did recoup some of its previous trade cloth in foreign markets, notably the United States, in the second half losses but its level of trade did not recover to that of earlier years.2 of the nineteenth century are well recorded. -
Spinning Machinery
panty portion of support pantyhose. Future development HFP of Heberlein Maschinenfabrik AG had been develop- of air covering machine might be focused on the improve- ed as an interlacer and has been put to practical use. Since ment of nozzle in order to get even entanglement appro- it is effective for air covering, it has been supplied to air priate strength and less air consumption. covering machines of ICBT International land Guidici. In addition, a new type nozzle, called "BCF-JET", used for 7. Other Related Machineries and Equipments thick carpet yarn of 1,000 - 12,000 dtex was also ex- hibited. The shape of a slit of V-Jet exhibited by Fiber- An exhibition of machinery and equipments related to guide Limited is featured by easy processing of yarn, and manufacturing machine for chemical and synthetic fiber less accumulation of dirt. It has been put to practical use varied widely from spinnerets to measuring instrument. for air covering as well as non-sizing texturing and air Such as suction guns, false-twisting friction disk unit, mixing texturing. magnet spindles, air jet nozzles, yarn guides, rubber apron/roller etc. and measuring instruments. (3) Measuring Instruments for Filament Yarn Some exhibits are briefly summarized as follows: There were many other exhibits from manufacturers of testing instruments introducing a variety of measuring (1) Suction Guns instruments, on-line measurements, quality control An air sucker is generally used for yarn suction in systems according to the importance of quality control package mounting onto take-up winders and other similar complying with diversity of end-uses and high quality. -
This Lightweight Scarf Feels Like a Dream. the Mohair and Silk Yarns
Weave Weave Weave This lightweight scarf feels like a dream. The mohair This lightweight scarf feels like a dream. The mohair This lightweight scarf feels like a dream. The mohair and silk yarns used in the warp and as the weft give and silk yarns used in the warp and as the weft give and silk yarns used in the warp and as the weft give this scarf its softness, while the other yarns add a lot this scarf its softness, while the other yarns add a lot this scarf its softness, while the other yarns add a lot of fl air and interest. of fl air and interest. of fl air and interest. YARNS YARNS YARNS Tahki Stacy Charles lace, DK, and worsted weight Tahki Stacy Charles lace, DK, and worsted weight Tahki Stacy Charles lace, DK, and worsted weight yarns. yarns. yarns. WEAVE ON WEAVE ON WEAVE ON THE CRICKET THE CRICKET THE CRICKET LOOM BY LOOM BY LOOM BY SCHACHT SCHACHT SCHACHT STRUCTURE WARPING STRUCTURE WARPING STRUCTURE WARPING Balanced plain weave. We measured Luna, Stella, Balanced plain weave. We measured Luna, Stella, Balanced plain weave. We measured Luna, Stella, EQUIPMENT Crystal and Eclipse yarns seper- EQUIPMENT Crystal and Eclipse yarns seper- EQUIPMENT Crystal and Eclipse yarns seper- Schacht 10” Cricket Loom; ately on a warping board. See Schacht 10” Cricket Loom; ately on a warping board. See Schacht 10” Cricket Loom; ately on a warping board. See 8-dent Cricket rigid heddle reed; “warping plan” below. Thread 8-dent Cricket rigid heddle reed; “warping plan” below. Thread 8-dent Cricket rigid heddle reed; “warping plan” below. -
Judging Wool and Mohair
AS3‐4.058 Judging Wool and Mohair Contents WOOL ........................................................................................ 3 Shrinkage and Yield .................................................................... 4 Scoring ........................................................................................ 4 Bulkiness ............................................................................ 5 Length ................................................................................ 5 Soundness and Purity ......................................................... 5 Quality ................................................................................ 7 Character ............................................................................ 7 Color ................................................................................... 7 MOHAIR .................................................................................... 7 Grading ....................................................................................... 7 Scoring ........................................................................................ 7 Fineness and Uniformity .................................................... 7 Staple Length.................................................................... 10 Character .......................................................................... 10 Softness ............................................................................ 10 Luster .............................................................................. -
Spininnovation
No. 24 07.2008 € INNOVATION 5,– SPIN THE MAGAZINE FOR SPINNING MILLS COREflex® – Core Yarn Attachment for Ring Spinning Machines ACP Quality Package Premium Parts – News HP-GX 5010 New Top Weighting Arms Mill Reports: – Nahar, India – Danmao, China Berkol – Part of Bräcker Wilhelm Stahlecker GmbH CONTENTS Editorial 3 COREflex® – Spinning Soft Core Yarn on Ring and Compact Spinning Machines 5 Yarn Quality Improved by ACP Quality Package 9 Premium Parts – News – Metal Washer for Magnetic Navals – CR-Coating for B 174 and B 20 SOLIDRINGS – ProFiL®Navels 15 The Theory of Compacting 19 BERKOL® – Becomes Part of Bräcker AG, Switzerland 21 NAHAR – A Saga from Farm to Fashion 23 Experience with EliTe® and EliTwist®CompactSet – A Practical Assessment , Nahar Industries, India 25 Manufacture of the SUESSEN Technology Components 27 Produce More and Better High Grade Worsted Fashion Fabric – Danmao Spinning Mills, China 31 HP-GX 5010 – The Top Weighting Arm for Worsted Spinning 36 Wilhelm Stahlecker GmbH (WST) – Centre for Research and Development 40 SUESSEN Customer Survey 2007 44 News 46 Advertisement: – Graf, Switzerland 47 – SUESSEN Product Range 48 Impressum No. 24 – July 2008 Published by Reprint of articles with reference Price : € 5.– Spindelfabrik Suessen GmbH permitted – Voucher copies desired Publication : once per year Dammstrasse 1, D-73079 Süssen, All rights reserved Information & Advertising Contact: Germany Spindelfabrik Suessen GmbH SPINNOVATION, Germany Editor in Chief : Peter Stahlecker fax + 49 (0) 71 62 15-367 Title registered® at German Patent Front Cover : e-mail: [email protected] Office EliCoreTwist® – EliTwist®CompactSet internet: www.suessen.com Copyright © 2008 with COREflex ® 2 SPINNOVATION No.