Study on Frequent Lines
Total Page:16
File Type:pdf, Size:1020Kb
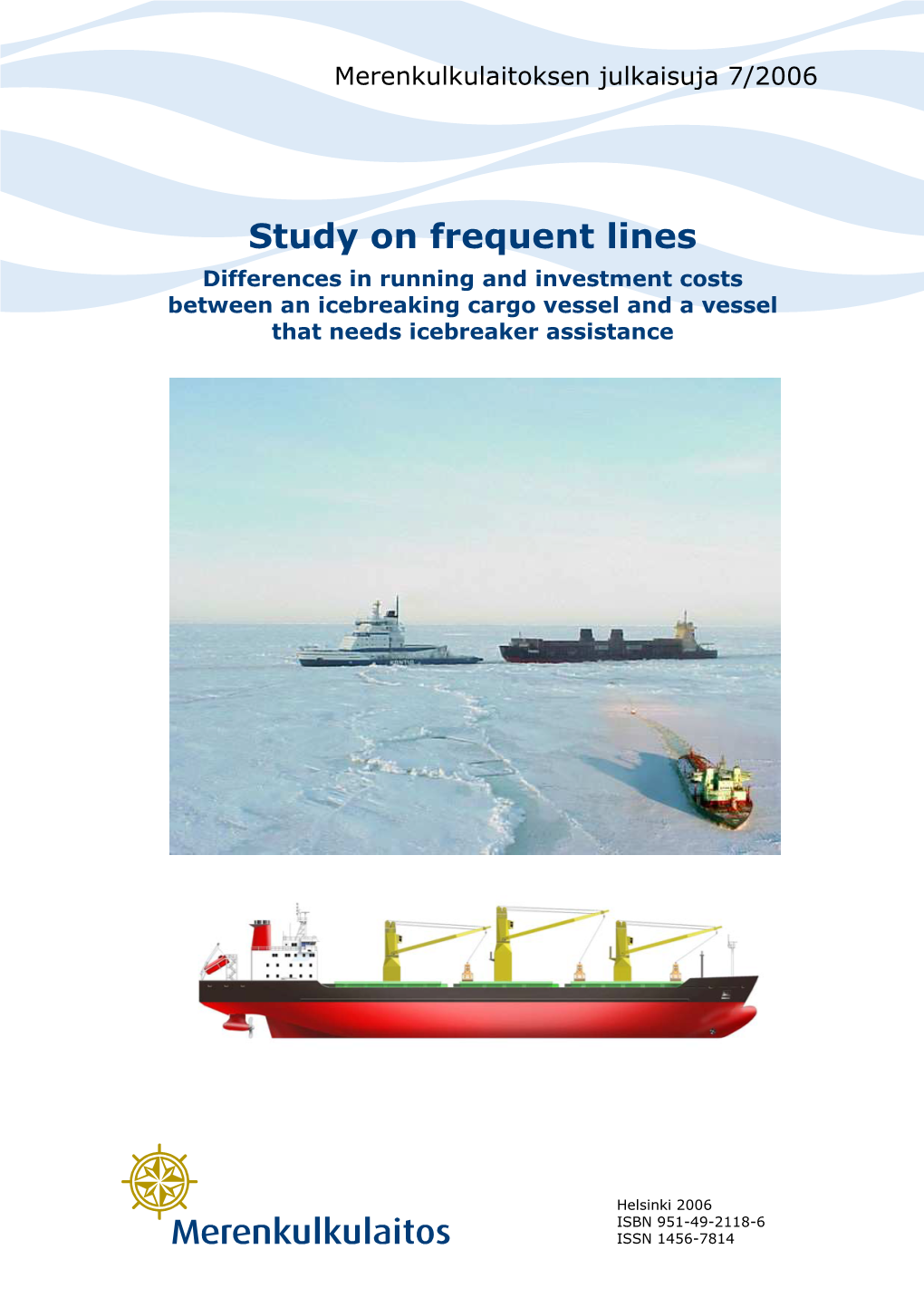
Load more
Recommended publications
-
The Problem of Propeller Design for High Ice Class Transportation Ships А.V
Fifth International Symposium on Marine Propulsors smp’17, Espoo, Finland, June 2017 The problem of propeller design for high ice class transportation ships А.V. Pustoshny, G.K. Darchiev, I.G. Frolova. Krylov State Research Centre, St. Petersburg, Russia ABSTRACT Some of these problems were expected to be solved by Development of large-capacity merchant vessels of so-called DAS (double acting ship) concept invented in high ice classes for Arctic has raised a range of Finland. According to this concept the vessels challenges for propeller designers. Usual propeller equipped with electric podded propulsors should sail design approaches are often not applicable for high ice- bow-first in open water and stern-first in ice. However, class merchant vessels. from the Russian experience with 3 series of heavy- tonnage merchant DAS of different types it is seen that In particular, the requirements regarding vibration the concept evolves not exactly as it was initially levels related to propeller cavitation, which are envisaged by its inventors. In deviation from the traditionally specified for merchant ships, cannot be original declarations of inventors high ice class DAS directly implemented in case of propellers designed for are built without bow bulb to enable both bow- and operation in ice because general measures to reduce stern-first operation in ice, the vessels require cavitation like skew or tip unloading prove to be either additional strengthening of stern (according to not feasible or limited by the requirement to ensure presently discussed Lloyd’s opinion stern and safe propeller operation in ice conditions. The propulsor should be one ice class higher) and special measures against cavitation are also restricted by maneuvering tactics in ice. -
Fuel and Economic Efficiency of an Ice-Going Vessel on the Northern Sea Route
Janne Esa Fuel and economic efficiency of an ice-going vessel on the Northern Sea Route School of Engineering Thesis submitted for examination for the degree of Master of Science in Technology. Espoo 25.5.2015 Thesis supervisor: Professor Pentti Kujala Thesis advisor: Lauri Kuuliala, M.Sc. (Tech.) aalto university abstract of the school of engineering master’s thesis Author: Janne Esa Title: Fuel and economic efficiency of an ice-going vessel on the Northern Sea Route Date: 25.5.2015 Language: English Number of pages: 9+90 Department of Applied Mechanics Major: Marine Technology Code: K3005 Supervisor: Professor Pentti Kujala Advisor: Lauri Kuuliala, M.Sc. (Tech.) In this thesis fuel and economic efficiency of an ice-going vessel were studied. The study was carried out for a double acting ship (DAS) and an ice-bow vessel operating year-around on the Northern Sea Route (NSR). For comparison these efficiencies were investigated for an open water vessel operating on the Suez Canal route (SCR) and a vessel using the NSR during operable months, i.e., from July until December and rest of the year using the SCR. These are the months permitted by current NSR regulations. The fuel consumption of the vessel was studied with the transit-simulation. For DAS and the ice-bow ship first the speed was solved in different ice conditions. For open water and assisted ships the power demand was calculated. DAS and ice-bow ship were assumed to use full power in ice and the speeds in open water and ice channel were assumed to be constant. -
Autical Queries--Deck
Coast Guard ICE Polar Icebreakers Operations Past, present, and future. by CDR T HOMAS WOJAHN Ice Operations Program Manager, U.S. Coast Guard Division of Ice Operations and Mobility The United States has extensive economic, environ - All icebreakers returned to the Coast Guard in the mental, and security interests in the polar regions. 1960s when it was determined that—with its long his - Much of the state of Alaska lies within the Arctic circle, tory of operations in the ice-covered waters of Alaska, and the U.S. maintains geopolitical relations with Antarctica, Greenland, the Great Lakes, and the East other Arctic nations. In the Antarctic, the U.S. partici - Coast—it was the best service to execute all of the pates in a number of international agreements, such as nation’s icebreaking missions. Upon the return of the the 1961 Antarctic Treaty. Over the decades, repeated last wind-class vessel, the USCG fleet included eight high-level reviews have reaffirmed the importance of heavy icebreakers, the seven wind-class icebreakers, U.S. presence and leadership in the polar regions. and the Glacier, which was built for the Navy in 1955. For the past 140 years, the U.S. Coast Guard has con - In 1955, the USCG returned to Antarctica to facilitate ducted a variety of missions in these regions, and for the first Operation Deep Freeze (resupply of the U.S. the past 40 years has been the sole operator of heavy Antarctic program) in support of science and national U.S. icebreakers in the harshest marine environments security missions on the continent, which have con - in the world. -
Anssi Hepo-Oja & Viktor Mäki-Kuutti MEKAANISEN JA
Anssi Hepo-oja & Viktor Mäki-Kuutti MEKAANISEN JA SÄHKÖISEN PROPULSIOJÄRJESTELMÄN ESITTELY Merenkulun koulutusohjelma Merikapteeni 2012 MEKAANISEN JA SÄHKÖISEN PROPULSIOJÄRJESTELMÄN ESITTELY Hepo-oja, Anssi; Mäki-Kuutti, Viktor Satakunnan ammattikorkeakoulu Merenkulun koulutusohjelma Helmikuu 2012 Ohjaaja: Rantala, Pauli Sivumäärä: 52 Liitteitä: 2 Asiasanat: propulsiojärjestelmä, asennustavat, ruoripotkurityypit, laivarakennusteol- lisuus ____________________________________________________________________ Opinnäytetyön tarkoituksena oli esitellä kaksi erilaista propulsiojärjestelmää: sähköi- nen ja mekaaninen järjestelmä. Emme pohdi niiden paremmuutta, vaan halusimme tutustua näihin järjestelmiin itse sekä tuoda ne tutuiksi myös muille opiskelijoille ja merenkulkijoille. Opinnäytetyössä kerromme, minkälaisissa alustyypeissä kyseisiä propulsiojärjestel- miä käytetään, selvitämme niiden asennustapoja, esittelemme erilaisia ruoripotkuri- tyyppejä sekä arvioimme näiden potkurijärjestelmien tulevaisuuden näkymiä. Aineisto opinnäytetyöhön on kerätty haastattelemalla alan asiantuntijoita, ABB:n ja Rolls-Roycen internetsivuilta sekä valmistajilta saamistamme materiaaleista. Tutustuessamme aiheeseen vakuutuimme siitä, että laivanrakennusteollisuus ja uudet innovaatiot laivanrakennusteollisuudessa ovat Suomessa kansainvälistä huippua nyt ja tulevaisuudessa. Kiitämme ABB:tä sekä Rolls-Roycea hyvästä yhteistyöstä. INTRODUCTION TO MECHANICAL AND ELECTRIC PROPULSION SYSTEMS Hepo-oja, Anssi; Mäki-Kuutti, Viktor Satakunnan ammattikorkeakoulu, Satakunta -
Venäjän LNG-Sektorista Ja Aker Arcticin Toimista Jamalin Niemimaalla
SHIP CONSULTING ICE MODEL OFFSHORE Design & Engineering & Project Development & Full Scale Testing Development Aker Arctic Technology Oy Venäjän LNG-sektorista ja Aker Arcticin toimista Jamalin niemimaalla Mauri Lindholm KAASUALAN NEUVOTTELUPÄIVÄT, 23.-24.5.2019 22 May, 2019 Slide 1 Johdanto ¡ Tämä esitys keskittyy Venäjän maakaasun vientiin, erityisesti sen LNG-tuotantoon ja -kuljetuksiin nyt ja tulevaisuudessa ¡ Ajan mittaan Venäjä on nousemassa LNG:n viejänä suurimpien vientimaiden joukkoon samalla kun joidenkin perinteisten LNG- viejien osuus on laskemassa ¡ Myös uusia jakelukanavia tarvitaan yhä useampien tuotanto- ja energialaitosten sekä erilaisten laivojen alkaessa käyttää maakaasua pääasiallisena polttoaineenaan ¡ Itämeren piiriin syntyvillä uusilla laitoksilla ja jakelupisteillä on merkitystä kaasun saatavuuteen ja jakeluun myös Suomessa ¡ Suomalaisyrityksiä on mukana suunnittelemassa ja rakentamassa kuljetuksiin tarvittavia aluksia sekä niiden toimintaan tarvittavia apualuksia ¡ Lisäksi esitellään Aker Arcticin toimintaa, joka liittyy akrtisten laivojen kehittämisen ja suunnitteluun. Kaikissa Venäjän LNG- kuljetuksissa tarvitaan jäävahvistettuja laivoja, joiden tulee pystyä toimimaan kylmissä olosuhteissa. 24 May, 2019 Slide 2 Sisällöstä ¡ Aker Arctic Technology Oy:stä lyhyesti ¡ Venäjän LNG-hankkeista ¡ Itämeren kaasukartta ¡ Arktisista LNG;n kuljetuslaivoista ja apulaivoista ¡ LNG:n jakelualuksista Enin osa lähdeaineistosta on vieraskielistä, siksi myös seuravien sivujen sisältö on englanniksi. Kuvien alkuperä: useista eri -
Lloyd's Register – Written Evidence (ARC0048)
Lloyd’s Register – Written evidence (ARC0048) 1. Summary The objectives of this submission of evidence to the Select Committee on the Arctic are: To offer supporting data and insights on transit and destination shipping in the Arctic and, in addition, the characteristics of the UK registered Arctic shipping fleet. To contribute evidence on the technological challenges for future Arctic shipping activities To contribute evidence on the regulatory framework that will govern Arctic shipping To contribute advice, and views, on Arctic shipping to support consideration of the “UK dimension” by the Select Committee Considering each objective in turn: Key points on supporting data and insights on transit and destination shipping in the Arctic: 1. Very small numbers of ships use Arctic transits for voyages between ocean basins (i.e. Pacific and Atlantic basins) as an alternative shipping route to transits through the Panama or Suez canal 2. Shipping in the Russian Arctic is likely to increase, but will be mainly export shipping for dedicated natural resources projects. Transit of commercial ships through the Russian Arctic is likely to occur during the summer season only 3. The UK registered ice-classed fleet is small, with 119 ice classed ships, and just 8 ships potentially suitable for transiting the Russian Northern Sea Route independently in an average summer season Figure 1.1 % of Ice Classed UK Fleet Figure 1.2 Ice Classes assigned to UK flagged ships 1 Key points on the technological challenges for future Arctic shipping activities: 1. Technological challenges remain for efficient Arctic shipping with a significant build and operating cost premium associated with current generation of Arctic capable ships 2. -
Accelerated Icebreaker Development
Accelerated icebreaker development Imagine a ship owner having the right to refuse to take delivery of a new container vessel if it does not sail at 2 knots in 1.5-meter thick ice. Would anyone guarantee the performance of a new, innovative vessel in advance? 2 generations 1|13 his is not a theoretical example but a real- organization has a long history in researching and life situation. Aker Arctic Technology Inc. developing maritime ice technologies and a unique is probably one-of-a-kind in giving such a set of groundbreaking achievements to go with it. guarantee. The owner is Norilsk Nickel, the Tworld’s largest exporter of nickel and palladium and “Computer simulations estimate how much power a in need of an ice-breaking container ship. vessel will need to meet specific ice conditions,” says Uuskallio, adding that these need to be verified in As a so-called double acting ship, this type of vessel model testing. is designed to lead the way in open water and thin ice, then turn around and proceed astern (back- Model testing is done in our ice tank, which is 75 wards) in heavy ice conditions, sucking the ice in meters long and 8 meters wide, with a water depth under the ship with its Azipod® thrusters. Such ships of up to 2.1 meters. We can also do tests in Aalto can operate independently in severe ice conditions University’s ice tank, which is 40 by 40 meters and without icebreaker assistance, while performing more suitable for testing maneuverability. better in open waters compared with traditional ice- breaking vessels. -
Finnish Solutions for the Entire Icebreaking Value Chain
FINNISH SOLUTIONS FOR THE ENTIRE ICEBREAKING VALUE CHAIN AN AMERICAN-FINNISH PARTNERSHIP 2 3 4 FINNISH SOLUTIONS FOR THE ENTIRE ICEBREAKING VALUE CHAIN TABLE OF 6 ICEBREAKING SOLUTIONS DELIVERED ON TIME AND ON BUDGET CONTENTS 8 THE POLAR MARITIME NETWORK IN FINLAND 12 RESEARCH 12 AALTO UNIVERSITY 14 DESIGN 14 AKER ARCTIC 18 BUILD 18 RAUMA MARINE CONSTRUCTIONS 22 OPERATE 22 ARCTIA 26 EQUIPMENT & SYSTEM SUPPLIERS / DIGITAL SERVICE PROVIDERS 28 LAMOR 30 ABB 32 NESTIX 34 WÄRTSILÄ 38 TRAFOTEK 40 MARIOFF 42 STARKICE 44 ICEYE 46 CRAFTMER 48 PEMAMEK 50 STEERPROP 52 NAVIDIUM 54 DANFOSS 56 POLARIS: THE FIRST LNG-POWERED ICEBREAKER IN THE WORLD 58 BENEFITS OF AN AMERICAN-FINNISH PARTNERSHIP PHOTO BY TIM BIRD 4 5 Finnish companies have designed about 80 percent of the world’s icebreakers, and about 60 percent of them have been built by Finnish shipyards. We have a creative and FINNISH agile polar maritime network that is known for delivering on schedule and on budget. We are also known for delivering sustainable, innovative and effective solutions SOLUTIONS for demanding tasks in Arctic conditions. Finland is the only nation in the world that offers ice- proven products and services with a solid, cost-effective FOR THE ENTIRE value chain. This value chain covers R&D, education, ship design, engineering, building, operation, program management and life cycle support services. Globally ICEBREAKING recognized Finnish companies and shipyards offer icebreaking solutions for the U.S polar icebreaker program that can be considered as a complete package or VALUE CHAIN configured as individual options to suit specific needs. -
The Development of the New Double Acting Ships for Ice Operation
POAC 2001, OTTAWA 12-17.8.2001 THE DEVELOPMENT OF THE NEW DOUBLE ACTING SHIPS FOR ICE OPERATION Kimmo Juurmaa, Tom Mattsson, Göran Wilkman Kvaerner Masa-Yards Arctic Technology, Helsinki, Finland THE DEVELOPMENT OF THE NEW DOUBLE ACTING SHIPS FOR ICE OPERATION Kimmo Juurmaa, Tom Mattsson, Göran Wilkman Kvaerner Masa-Yards Arctic Technology, Helsinki, Finland ABSTRACT Most of the traditional icebreakers have had good capability to run astern in ice even the vessels are not designed for that. The development during the last 10 years has made it possible that running astern could be considered as the main way of operation in heavy ice conditions. The key to this development is the use of azimuthing podded propulsion, which gives the vessel the benefits of both electric propulsion and excellent maneuverability. These are now combined for the first time. Kvaerner Masa-Yards together with ABB Azipod has developed the concept for more and more demanding projects. Without the participation of ship owners the development could have slowed down, because reality is the final testing ground. The Azipod propulsion has been earlier described in a number of papers. This paper concentrates on the recent development of the Double acting principal including the multy pod applications at the speed range where the Double acting principal is still beneficial. Results from the latest model tests will be discussed. INTRODUCTION Traditionally ice breaking ships have been quite poor in open water. The total efficiency has been 20-40 % less than a good open water vessel. This has been mainly due to the bow forms, which have been developed to break thicker and thicker ice. -
Aker Arctic Technology
AKER ARCTIC TECHNOLOGY Swedoceans Seminarium 23.3.2021 Reko-Antti Suojanen Managing Director COPYRIGHT Copyright of all published material including photographs, drawings and images in this document remains vested in Aker Arctic. Accordingly, neither the whole nor any part of this document shall be reproduced in any form nor used in any manner without express prior written permission and applicable acknowledgements. No trademark, copyright or other notice shall be altered or removed from any reproduction. Agenda 1. Aker Arctic as company 2. Icebreaker types 3. Latest ships 4. Development and technical points 5. Ships 6. Future 23 March 2021 3 Aker Arctic Technology Inc World’s most experienced designer for icegoing ships Own Ice Model Test basin Experienced Naval Unique know-how As reference 60% of Various Architecture for ice classed world icebreaker vessel types - Power determination - Operational studies vessels designs - Hull form - Ice class approvals development - Offshore structures 23 March 2021 www.akerarctic.fi Design and 01 Naval Architecture Engineering 02 Hydrodynamics 03 Icebreaking design 04 Hull structural 05 Systems 06 Machinery 23 March 2021 6 Aker Arctic comprehensive partner From early stage planning to delivery of the ships. • Feasibility fleet Design development, • Testing and hull Basic design • Special • Delivery of vessel and vessel consept and tender design (class approval) icebreaking requirements design equipments • Trials and • Ice model testing commisioning • Budget definition • Yard support services • Open -
Improved Double-Acting Ship Solutions for Transportation Systems
Aker Arctic Technology Inc Newsletter March 2011 Arctic PassionNews 1 / 2011 Improved Solutions for Ice management Double-Acting transportation protects ships Ship systems and floaters at Better open water features and Choose right on page 4 work more on page 3 How does it work on page 9 Arctic Passion News March 2011 In this issue Towards risk assessment Page 2 From the Managing Director Page 3 Improved based safety ruling Double-Acting Ship Page 4 Complete solutions for transportation needs Dear reader, These ongoing processes have put an Page 9 Ice management unfortunate time-out in short term for protects ships and tankers When writing these words for the further investments in new harsh Page 14 Ice pressure previous Arctic Passion News the environment operations as the industry is on fixed structures Macondo well was still leaking and the waiting for authorities' attitudes in the Page 15 What's up industry shocked from the consequences post-Macondo world. On the other hand Page 16 Trip to Norway of the accident. The leak was rather the new situation has changed the quickly stopped and the well closed. BP overall situation dramatically; the trend has to be praised on the fact how well appears to be that now the operator Announcements they managed to work in finding the himself needs to start thinking on his solutions to cut the deepwater leak. Now risks in any planned activity and create the investigation committees have his own risk assessment and his own published their reports and authorities in decision-making on acceptable risk all oil producing nations are reviewing levels, which then need to be their rules, practices and safety demonstrated to the authorities. -
System Project Guide for Passenger Vessels
System Project Guide For Passenger Vessels Preface This project guide provides system data and information for preliminary project evaluation of an electrical propulsion system in accordance of power plant benefits resulting from the selection. More detailed information is available in our platform-specific “Product Introduction” publications. Furthermore, our project and sales departments are available to advise on more specific ques- tions concerning our products and regarding the installation of the system components. Our power plant and propulsion system offering is constantly reviewed and refined according to the technology development and the needs of our customers. Therefore, we reserve the right to make changes to any data and information herein without notice. All information provided in this publication is meant to be informative only. All project-specific issues shall be agreed separately and therefore any information given in this publication shall not be used as part of agreement or contract. Helsinki, February 2011 ABB Oy, Marine Merenkulkijankatu 1/ P.O. Box 185 00981 Helsinki Finland Tel. +358 10 22 11 http://www.abb.com/marine Azipod is registered trademark of ABB Oy. © 2005 ABB Oy. All rights reserved Disclaimer The data, examples and diagrams in this manual are included solely for the concept or product description and are not to be deemed as a statement of guaranteed properties. All persons responsible for applying the equipment addressed in this manual must satisfy themselves that each intended application is suitable and acceptable, including that any applicable safety or other operational requirements are complied with. In particular, any risks in applications where a system failure and/ or product failure would create a risk for harm to property or persons (including but not limited to personal injuries or death) shall be the sole responsibility of the person or entity applying the equipment, and those so responsible are hereby requested to ensure that all measures are taken to exclude or mitigate such risks.