Floating Installation Instructions
Total Page:16
File Type:pdf, Size:1020Kb
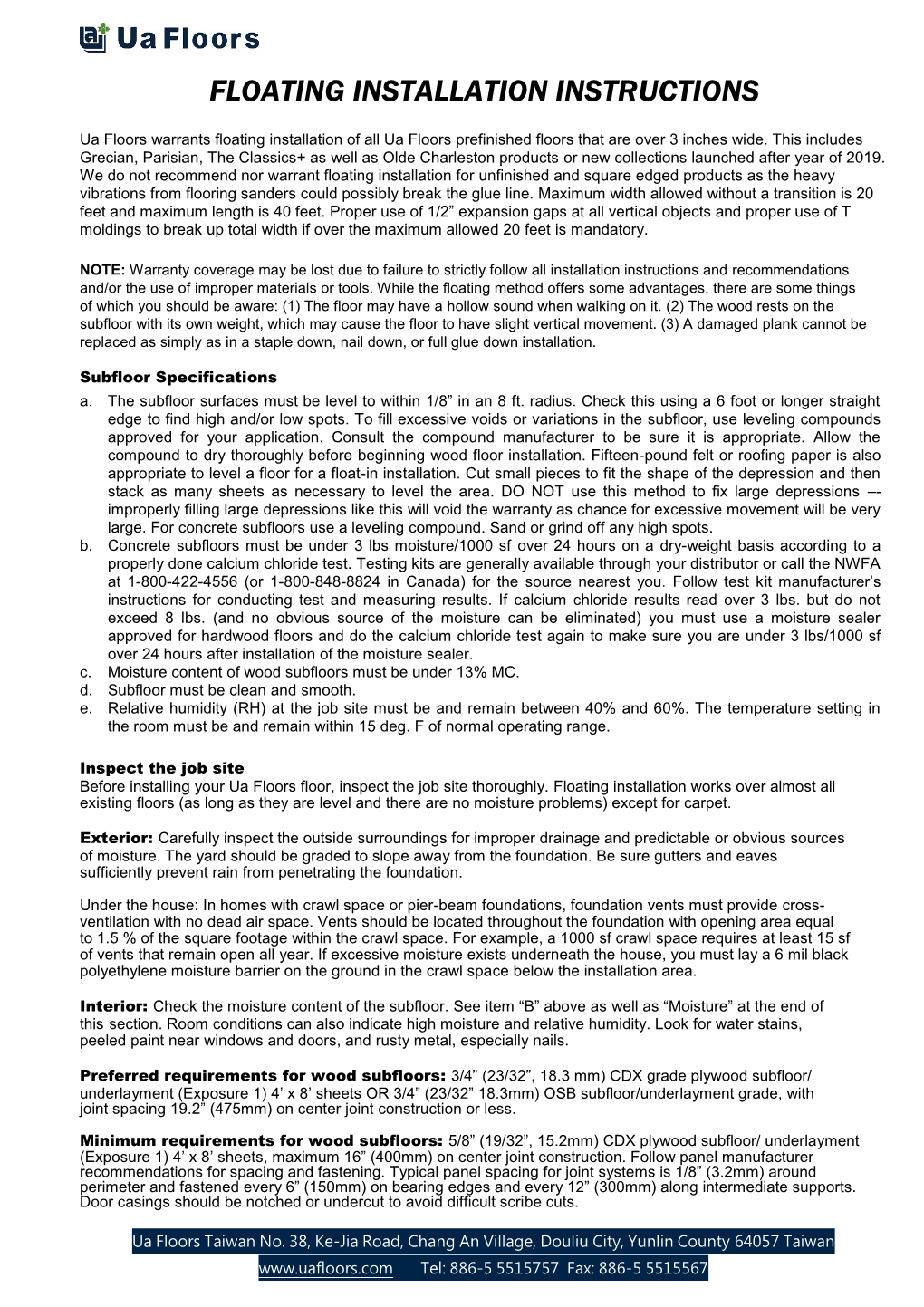
Load more
Recommended publications
-
Iafor the International Academic Forum Introduction
A Study of Comfort Elements Combine with Local Mascot The Case of Yunlin Townships Wen-Ying Chiu, National Yunlin University of Science and Technology, Taiwan Wen-Shan Chang, National Yunlin University of Science and Technology, Taiwan The Asian Conference on the Social Sciences 2017 Official Conference Proceedings Abstract Yunlin County, which located in south-west of Taiwan, west of the Taiwan Strait and consists of twenty townships. Due to its plain ground and fertile soil environment advantages which suits for agriculture, it has been being the main supplier of rice and vegetables, which had made a great contribution to Taiwan. Although there is an official mascot “KIMONCHAN” representing Yunlin County, there is no mascot for township individually. The mascot should contain affinity which let people feel close, harmless and being kind. The purpose of this study is looking for a method to combine those elements and to improve those to create a new harmless mascot for the townships. At the beginning of the research, the researchers will use Secondary Qualitative Study for the collection of mascot design. And analysis the color, and comfort elements, and combine the two data collection. After the completion of the data collection, researchers use focus groups to conduct interviews on design background students to get those who have Basic Aesthetics and Design Sensitivity for the mascot’s opinion and the image of Yunlin local towns. The contents of the interview after the integration of the mascot in accordance with the results of the prototype design, prototype design is complete, the use of prototype for the comfort of the in-depth interview. -
List of Insured Financial Institutions (PDF)
401 INSURED FINANCIAL INSTITUTIONS 2021/5/31 39 Insured Domestic Banks 5 Sanchong City Farmers' Association of New Taipei City 62 Hengshan District Farmers' Association of Hsinchu County 1 Bank of Taiwan 13 BNP Paribas 6 Banciao City Farmers' Association of New Taipei City 63 Sinfong Township Farmers' Association of Hsinchu County 2 Land Bank of Taiwan 14 Standard Chartered Bank 7 Danshuei Township Farmers' Association of New Taipei City 64 Miaoli City Farmers' Association of Miaoli County 3 Taiwan Cooperative Bank 15 Oversea-Chinese Banking Corporation 8 Shulin City Farmers' Association of New Taipei City 65 Jhunan Township Farmers' Association of Miaoli County 4 First Commercial Bank 16 Credit Agricole Corporate and Investment Bank 9 Yingge Township Farmers' Association of New Taipei City 66 Tongsiao Township Farmers' Association of Miaoli County 5 Hua Nan Commercial Bank 17 UBS AG 10 Sansia Township Farmers' Association of New Taipei City 67 Yuanli Township Farmers' Association of Miaoli County 6 Chang Hwa Commercial Bank 18 ING BANK, N. V. 11 Sinjhuang City Farmers' Association of New Taipei City 68 Houlong Township Farmers' Association of Miaoli County 7 Citibank Taiwan 19 Australia and New Zealand Bank 12 Sijhih City Farmers' Association of New Taipei City 69 Jhuolan Township Farmers' Association of Miaoli County 8 The Shanghai Commercial & Savings Bank 20 Wells Fargo Bank 13 Tucheng City Farmers' Association of New Taipei City 70 Sihu Township Farmers' Association of Miaoli County 9 Taipei Fubon Commercial Bank 21 MUFG Bank 14 -
Chi-Chi, Taiwan Earthquake Event Report
TM Event Report Chi-Chi, Taiwan Earthquake .8E 7km depth N 120 23.8 6 M7. m. a. 47 1: 99 19 , 1 2 r e b m e t p e S Chi-Chi Reconnaissance Team Weimin Dong, Ph.D. Laurie Johnson, AICP RMS Team Leader, Earthquake Engineer RMS Event Response Coordinator, Urban Planner Guy Morrow, S.E. Craig Van Anne, M.S. RMS, Structural Engineer OYO RMS, Fire Protection Engineer Akio Tanaka Shukyo Segawa OYO RMS, Geophysicist OYO Corporation, Geophysicist Hideo Kagawa Chin-Hsun Yeh, Ph.D. Engineering & Risk Services, National Center for Research in Earthquake Structural Engineer Engineering, Associate Research Fellow Lun-Chang Chou, Ph.D. Kuo-Liang Wen, Ph.D. National Science and Technology Program for National Science and Technology Program for Hazards Mitigation, National Taiwan University Hazards Mitigation, National Taiwan University Yi-Ben Tsai, Ph.D. Wei-ling Chiang, Ph.D. National Central University, Professor National Central University, Professor Wenko Hsu Institute for Information Industry, Engineer, Special Systems Division The reconnaissance team members arrived in Taiwan on Wednesday, September 23, two days after the earthquake, and initially spent 20 man-days in the field. OYO RMS, OYO, and ERS reconnaissance team members jointly presented preliminary findings at a seminar in Tokyo on October 11. RMS joined Pacific Gas & Electric (PG&E) and members of the Technical Council on Lifeline Earthquake Engineering (TCLEE) on October 10 in a week-long mission to further investigate power disruption and associated business interruption impacts, and collect additional loss data. Many of the team members, particularly our Taiwanese colleagues, have continued investigations of this earthquake. -
CHAPTER 132 Geomorphological Analysis of a Beach and Sandbar System Chen-Shan Kung1, Marcer Stive2 and Geffery Toms3 Abstract At
CHAPTER 132 Geomorphological Analysis of a Beach and Sandbar System Chen-Shan Kung1, Marcer Stive2 and Geffery Toms3 Abstract At Yunlin county a major development of over 10,000 ha of reclamation is being planned for port related industries. The development is taking place along a coast that bordered by Choshui river and the Wai-San-Ting sandbar. Detailed modeling using MIKE21 package with wave, flow and sediment transport modules were used to assess the morphological changes. Four such "relict" deltas were identified according to its ancient river courses. The decay of the sandbars was mostly independent due to the major discontinuities at sandbar headlands and tidal channels. The analysis of the complex morphological processes has provided an important insight into the probable impacts of coastal developments and guided the expensive and time-consuming model operations. Introduction At Yunlin county a major development of over 10,000 ha of reclamation is being planned for accommodating large scale port related industries and including a power plant and other developments. The reclamation, which covers shallow coastal areas along a 40 km length of coast, will be served by two new deep water ports. The development is taking place along a stretch of coast that bordered in the North by Choshui river and in the South by the unique shoreline attached Wai-San- Ting sandbar. Wai-San-Ting, over 20 km long, is Taiwan's largest coast bar feature and morphologically is very active (Figure 1). Typhoons and a predominant NNE wind and wave climate approaching at very oblique angle to shore together with strong tidal currents are the main iSinotech Engineering Consultants Inc., 171 Nanking E. -
The Handy Guide for Foreigners in Taiwan
The Handy Guide for Foreigners in Taiwan Research, Development and Evaluation Commission, Executive Yuan November 2010 A Note from the Editor Following centuries of ethnic cultural assimilation and development, today Taiwan has a population of about 23 million and an unique culture that is both rich and diverse. This is the only green island lying on the Tropic of Cancer, with a plethora of natural landscapes that includes mountains, hot springs, lakes, seas, as well as a richness of biological diversity that encompasses VSHFLHVRIEXWWHUÀLHVELUGVDQGRWKHUSODQWDQGDQLPDOOLIH$TXDUWHU of these are endemic species, such as the Formosan Landlocked Salmon (櫻 花鉤吻鮭), Formosan Black Bear (台灣黑熊), Swinhoe’s Pheasant (藍腹鷴), and Black-faced Spoonbill (黑面琵鷺), making Taiwan an important base for nature conservation. In addition to its cultural and ecological riches, Taiwan also enjoys comprehensive educational, medical, and transportation systems, along with a complete national infrastructure, advanced information technology and communication networks, and an electronics industry and related subcontracting industries that are among the cutting edge in the world. Taiwan is in the process of carrying out its first major county and city reorganization since 1949. This process encompasses changes in DGPLQLVWUDWLYHDUHDV$OORIWKHVHFKDQJHVZKLFKZLOOFUHDWHFLWLHVXQGHUWKH direct administration of the central government, will take effect on Dec. 25, 7RDYRLGFDXVLQJGLI¿FXOW\IRULWVUHDGHUVWKLV+DQGERRNFRQWDLQVERWK the pre- and post-reorganization maps. City and County Reorganization Old Name New Name (from Dec. 25, 2010) Taipei County Xinbei City Taichung County, Taichung City Taichung City Tainan County, Tainan City Tainan City Kaohsiung County, Kaohsiung City Kaohsiung City Essential Facts About Taiwan $UHD 36,000 square kilometers 3RSXODWLRQ $SSUR[LPDWHO\PLOOLRQ &DSLWDO Taipei City &XUUHQF\ New Taiwan Dollar (Yuan) /NT$ 1DWLRQDO'D\ Oct. -
Application of Multiple Sensors in Monitoring Land Subsidence in Central Taiwan
12th International Conference on Hydroscience & Engineering Hydro-Science & Engineering for Environmental Resilience November 6-10, 2016, Tainan, Taiwan. Application of Multiple Sensors in Monitoring Land Subsidence in Central Taiwan Wei-Chia Hung1, Yuan-Kang Cheng2, Jyun-Jen Huang2, Fang-Cyong Chen2, Chun-Ling Kuo2, Chao-Chun Chien2, Carl Wang1 Yi-An Chen1, Huan-Chin Chiu1, Chun Chang-Lee1 1. Green Environmental Engineering Consultant Co. LTD. Hsinchu, Taiwan 2. Water Resources Agency, Ministry of Economic Affairs Taipei, Taiwan ABSTRACT significant subsidence area in 2015. The most serious subsidence area is Choushui River Alluvial Fan(CRAF), the maximum settlement rate is Over pumping of groundwater has resulted in a large-scaled land around 7.1 cm per year in 2015. In particular, THSR passes through the subsidence in Taiwan. The subsidence has already endangered the subsidence center. Land subsidence will result in a major safety operation of Taiwan High Speed Rail (THSR). How to effectively concern about THSR. How to effectively monitor subsidence has monitor land subsidence become a major issue in Taiwan. In this paper, become a major issue in Taiwan. we would like to introduce the multiple-sensors monitoring system applied to study the extent of subsidence in central Taiwan and its CRAF is the most important agricultural area in western, central mechanism, including GPS (Global Positioning System), PSI Taiwan, with elevations ranging from 0 to 100 m. CRAF covers a total 2 (Persistent Scatterer Interferometry), levelling, multi-layer compaction area of 2,000 km and is bounded by Wu River (north), Pekang Creek monitoring well, extensometer and piezometer. These sensors (south), Douliu Mound (east) and Taiwan Strait (west). -
Report 3 on Kaohsiung Earthquake on February 6Th, 2016, in Taiwan Feb 10, 9:30 Am by National Sceince and Technology Center for Disaster Reduction
Report 3 on Kaohsiung Earthquake on February 6th, 2016, in Taiwan Feb 10, 9:30 am by National Sceince and Technology Center for Disaster Reduction Summary On February 6, 2016 at 3:57 am local time, a magnitude‐6.4 in‐land and shallow earthquake hit southern part Taiwan and caused casualties (37 died and 525 wounded) and losses (over a dozens of buildings totally or partially collapsed). The epicenter is located at Meinong, Kaohsiung City and with a focal depth of 16.6 Kilometers. According to the shake records, the strongest intensity reached scale 6 (334.1 gal). Source: Central Weather Bureau 1. Emergency Operation Right after the strong quake, the Ministry of the Interior activated quick damage survey at and elevated level of emergency operation to level 1 at 4:15 am to collect situations, and coordinate search and rescue efforts. Based on the disposal report released by the Central Emergency Operation Center on Feb 10, 9:00 pm, the latest situations are 2. Casualties: 43 died, 546 injured ( 84 hospitalized, 29 severely wounded) Area Death Injury Remarks 1. The Weiguan Jinlong building, located at No.6, Guoguang 5th St., Yongkang Dist., Tainan City, was completed in 1995 and it is a mixed‐use reinforced‐concrete complex for residential apartments and commercial units. The building collapsed and buried hundreds of residents. According to the latest report, 41 died (18 males and 23 females) and 101 were sent to hospitals. 95 residents escaped from the ruined building right after the quake and urban‐search‐and‐rescue (USAR) teams have found 214. -
National Taiwan University Hospital Yunlin Branch
GLOBAL NETWORK GOLD FORUM EVENT 2018 Sharing of “good practice” examples Chen Guan-Ju M.D. Healthcare Service Name: National Taiwan University Hospital Yunlin Branch Country/Region: Taiwan Self-Audit Score 2016 (Standards 1-8): 138/144 Size/ number of beds: 941 beds Number of Staff: 1661 persons Specialisation: community medicine, acute and critical care, integrated cancer treatment ⚫ After the launch of smoking cessation support group in 2015, the Smoking Cessation Support (st.4): abstinence rate among members was 40% in 2015, 48% in 2016 and reached 57% in 2017, which was higher than the target 25% Integrating a helpful eating program in the stop set by our government. tobacco process Abstinence rates of smoking support in 2016 and 2017 60% ⚫ A smoking cessation supporting group has been organized in our 50% hospital since 2015. (Figure 1) 40% 30% n:24 20% 10% 0% 2016 2017 3-month abstinence rates 40% 58% 6-month abstinence rates 50% 58% ⚫ In the group, many activities and lessons such as breathing method in Kung Fu, Chinese chess, exercise and cooking with Community Engagement (st.7): new veggies were offered to aid smoking cessation. ⚫ Cooking with new veggies is an eating program which taught Cooperating with local OB-GYN clinics to members how to prepare their food during the course of smoking promote smoking cessation cessation therapy. ⚫ The concept of new veggies was to combine low salt, low oil, and low sugar intake, with vegetables and fruit to avoid body ⚫ It has been our hospital’s responsibility for long to take care of the weight gain after stopping tobacco. -
T.N.K Pass Taichung Pass Yilan Pass Tainan Pass K.P.P Pass Taitung Pass
T.N.K Pass The Taipei Pass integrates transportation and tourist attractions in Taipei City, New Taipei City and Keelung, providing a diversity of options and combinations as well as transportation and attrac- tion discounts - the BEST way for you to travel and save across Greater Taipei! Taichung Pass Taichung is Central Taiwan's smart travel ticket! The Taichung City Government has integrated the tourism resources of seven counties and cities including Miaoli County, Taichung City, Changhua County, Nantou County, Yunlin County, Chiayi City and Chiayi County! You’ll find select tourist routes, exclusive discounts on the region’s best tourist attractions and amazing discounts on transportation! Yilan Pass Yilan City is a gorgeous ocean side location! The Yilan County government has introduced Yilan Pass to heighten and expand your travel experiences across our beautiful, seaside county! The Yilan Pass provides you discounts on dining, travel, shopping and accom- 日月潭 modations so you can enjoy your trip across Yilan even more! 北北基 T.N.K Taichung Pass T.N.K Pass Yilan Pass Tainan Pass Tainan Pass - fun on demand! The Tainan K.P.P Pass Tainan Pass Taitung Pass Pass integrates eating, accommodations, Taitung Pass and shopping into a travel platform that Put a microcosm of Taitung at your fingertips! Taiwan Pass Details by City & County offers you select tourist destinations across Find food, swinging music and creative arts Tainan and the most unique shopping K.P.P Pass https://khh.travel/ around every corner in our green valley home! opportunities in the city! A must-have for The Taitung Pass is your tour guide, enabling you Yilan Pass http://www.yilancard.com/ backpackers visiting our green, beautiful to embrace Taitung's simplicity and sincerity and https://www.ttfuncard.com/ Taitung Pass region! Tainan Pass - a complete visitor’s meet welcoming artisans and delicious eateries. -
NASA Finds Small Strength in Newly Formed Tropical Depression 08W 14 June 2018
NASA finds small strength in newly formed Tropical Depression 08W 14 June 2018 sustained winds near 29 mph (25 knots/46 kph). At 9:55 a.m. EDT (1355 UTC) on May 19, the Moderate Resolution Imaging Spectroradiometer or MODIS instrument that flies aboard NASA's Terra satellite gathered infrared data on 08W as it approached Taiwan's southwestern coast. Infrared data provides temperature information. MODIS revealed a few very powerful thunderstorms around the center where cloud top temperatures were as cold as minus 80 degrees Fahrenheit (minus 62.2 Celsius). NASA research has shown that cloud tops with temperatures that cold were high in the troposphere and have the ability to generate heavy rain. The Central Weather Bureau of Taiwan issued an Extremely Heavy Rain Advisory is in effect from tonight, June 14, through Friday morning June 15 for Tainan City, Kaohsiung City, Pingtung County, Hengchun Peninsula, Taitung County, Lanyu and On May 19, NASA's Terra satellite showed a few very Ludao Islands. powerful thunderstorms (yellow) northwest of the center where cloud top temperatures were as cold as minus 80 A Heavy Rain Advisory or Extremely Heavy Rain degrees Fahrenheit (minus 62.2 Celsius). Credit: Advisory is in effect from tonight, June 14, through NASA/NRL Friday morning June 15 for Taichung City Mountain Area, Nantou County, Yunlin County, Chiayi City, Chiayi County, Yilan County, Hualien County and Penghu County. Tropical Depression 08W formed around the same time as Tropical Storm 07W, and both are in the Strong Wind Advisory is in effect from tonight, June Northwestern Pacific Ocean basin. -
Welcome to the Central Bank of China
401 INSURED FINANCIAL INSTITUTIONS 2021/3/31 39 Insured Domestic Banks 5 Sanchong City Farmers' Association of New Taipei City 62 Hengshan District Farmers' Association of Hsinchu County 1 Bank of Taiwan 14 BNP Paribas 6 Banciao City Farmers' Association of New Taipei City 63 Sinfong Township Farmers' Association of Hsinchu County 2 Land Bank of Taiwan 15 Standard Chartered Bank 7 Danshuei Township Farmers' Association of New Taipei City 64 Miaoli City Farmers' Association of Miaoli County 3 Taiwan Cooperative Bank 16 Oversea-Chinese Banking Corporation 8 Shulin City Farmers' Association of New Taipei City 65 Jhunan Township Farmers' Association of Miaoli County 4 First Commercial Bank 17 Credit Agricole Corporate and Investment Bank 9 Yingge Township Farmers' Association of New Taipei City 66 Tongsiao Township Farmers' Association of Miaoli County 5 Hua Nan Commercial Bank 18 UBS AG 10 Sansia Township Farmers' Association of New Taipei City 67 Yuanli Township Farmers' Association of Miaoli County 6 Chang Hwa Commercial Bank 19 ING BANK, N. V. 11 Sinjhuang City Farmers' Association of New Taipei City 68 Houlong Township Farmers' Association of Miaoli County 7 Citibank Taiwan 20 Australia and New Zealand Bank 12 Sijhih City Farmers' Association of New Taipei City 69 Jhuolan Township Farmers' Association of Miaoli County 8 The Shanghai Commercial & Savings Bank 21 Wells Fargo Bank 13 Tucheng City Farmers' Association of New Taipei City 70 Sihu Township Farmers' Association of Miaoli County 9 Taipei Fubon Commercial Bank 22 MUFG Bank 14 -
Transformation of Taiwan's Reserve Force
Transformation of Taiwan’s Reserve Force Ian Easton, Mark Stokes, Cortez A. Cooper, Arthur Chan C O R P O R A T I O N For more information on this publication, visit www.rand.org/t/RR1757 Library of Congress Cataloging-in-Publication Data is available for this publication. ISBN: 978-0-8330-9706-4 Published by the RAND Corporation, Santa Monica, Calif. © Copyright 2017 RAND Corporation R® is a registered trademark. Cover: Photo by REUTERS/Patrick Lin. Limited Print and Electronic Distribution Rights This document and trademark(s) contained herein are protected by law. This representation of RAND intellectual property is provided for noncommercial use only. Unauthorized posting of this publication online is prohibited. Permission is given to duplicate this document for personal use only, as long as it is unaltered and complete. Permission is required from RAND to reproduce, or reuse in another form, any of its research documents for commercial use. For information on reprint and linking permissions, please visit www.rand.org/pubs/permissions. The RAND Corporation is a research organization that develops solutions to public policy challenges to help make communities throughout the world safer and more secure, healthier and more prosperous. RAND is nonprofit, nonpartisan, and committed to the public interest. RAND’s publications do not necessarily reflect the opinions of its research clients and sponsors. Support RAND Make a tax-deductible charitable contribution at www.rand.org/giving/contribute www.rand.org Preface This report provides an overview of Taiwan’s reserve force structure and describes its roles, missions, capabilities, and challenges.