CTRL Enters Second Phase
Total Page:16
File Type:pdf, Size:1020Kb
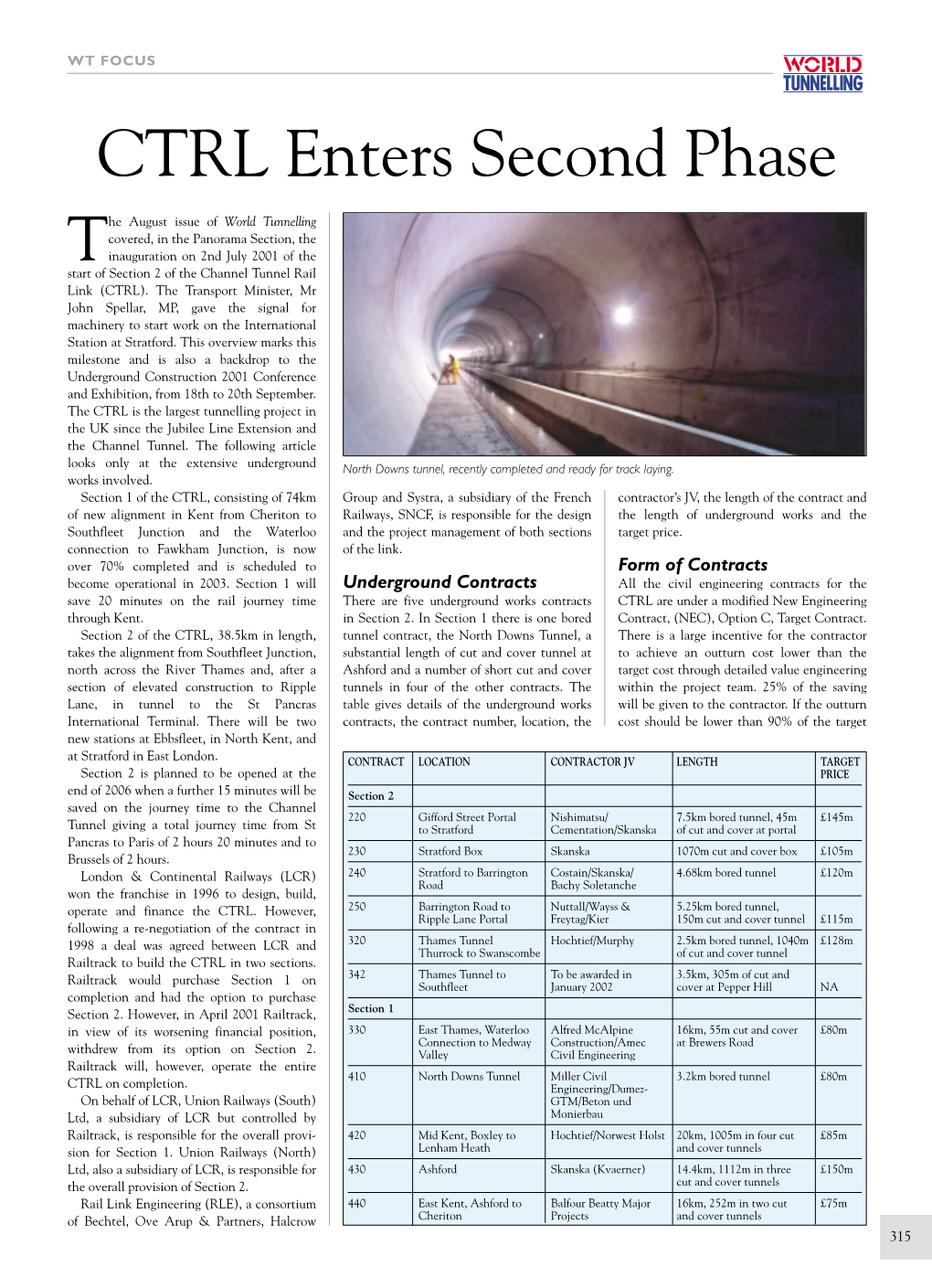
Load more
Recommended publications
-
2007 5.2 Billion 109 230 113 35 23.13 17.4
Sources: CTRL; Guardian graphics; main photograph: Dan Chung A12 Route in greater London BLACKHORSE St Pancras junction RD SNARESBROOK Hornsey WALTHAMSTOW Stratford international CENTRAL NEWBURY Thameslink surface line and domestic station, Chadwell Heath A116 PARK East Coast Main Line HIGHGATE set inside excavated Freight connection at North London Line with connection “box” 1.07km long Wanstead Ripple Lane, Dagenham to East Coast Main Line CHADWELL HTH Connection to West New interchange for LEYTONSTONE GOODMAYES Coast Main Line Eurostar and fast south- SEVEN KINGS Channel Tunnel rail line ARCHWAY Stoke Covered bridge feeds Camden east domestic trains. ILFORD is mainly for passengers Newington Links to: mainLeyton line – but some freight could Channel rail link into St Pancras/King's services, Docklands use new line, with loops twin-bore tunnel Cross interchange GOSPEL Light Railway, and WANSTEAD Ilford where faster trains can Midland Main Line feeds passengers Hackney LEYTON OAK London Underground's PARK Manor overtake Channel onwards via: Jubilee and Central lines Park Tunnel London St Pancras international and domestic station, east side -Midland and East HACKNEY Rail Link Gasworks tunnel Coast Main Lines CANONBURY CENTRAL -New Thameslink hub KENTISH Islington station Camden TOWN Thameslink tunnel HIGHBURY& BARKING -North London Line connection to East ISLINGTON West Ham EAST UPNEY Coast Main Line A12 HAM London tunnel 7.53km London tunnel 9.9km Islington UPTON PLAISTOW PARK East Ham Regent's canal London St Pancras Kings ANGEL international and Cross domestic station Tower WEST DAGENHAM DOCK Hamlets HAM From 2007, Eurostar Newham services arrive at BECKTON New domestic platforms (3): St Pancras – later High-speed Kent commuter City PRINCE ROYAL joined by fast south- CANNING trains will use Channel line The drill head of one of six boring machines used for the London tunnel TOWN REGENT ALBERT eastWestminster commuter trains St Paul's A13 GALLIONS St Pancras roof from 2009 using Channel tunnel CUSTOM BECKTON PARK REACH extension under ROYAL rail tracks. -
Ignis (Passive Fire Protection System)
Case studies North Downs Tunnel, Kent segments at a purpose built factory The 3.2 km North Downs Tunnel forms in Ridham Docks. part of the Channel Tunnel Rail Link running from Folkestone, Kent to De Westerschelde Tunnel, the St. Pancras in London. The primary Netherlands tunnel lining was made up of sprayed The client Maafroute BV instructed concrete. 1 kg of Ignis PP monofilament the precast contractors to add 1 kg fibres were added to the 60 N/mm2 of Ignis to the C40 concrete. The fibre concrete secondary lining. The lining was included in the concrete sections was constructed insitu, forming a forming the security exits, safety sacrificial layer. barriers and connection tunnels. T5, Heathrow Airport Dublin Port Tunnel, Ireland Ignis has been added to Grade C60 This 4 lane underground highway is concrete on various contracts within this designed to take heavy vehicle traffic prestigious project. The Ignis enhanced off the streets of Dublin. A 275 mm concrete has been used on site in thick lining over the tunnels arch is a sprayed concrete applications and it non-load bearing sacrificial concrete has also been added to precast ring containing 1-2 kg of Ignis. IGNIS® Monofilament Fibre PASSIVE FIRE PROTECTION North Downs Tunnel, Kent T5, Heathrow Airport, London Belgium T +32 52 457 413 Disclaimer All information and product specifications provided in this document are accurate at the time of publication. We follow a policy of India T +91 8527625678 Avoids explosive spalling in concrete continuous development. The provided information and product specifications may change at any time without notice and must not United Kingdom T +44 1482 863777 be relied upon unless expressly confirmed by us upon request. -
Asset Protection the Developers Handbook
The Developers Handbook Approval and Authorisation Prepared by Date Signed Paul Milgate August 2020 Asset Protection Project Manager Approved by Date Signed Gavin Baecke August 2020 Head of Civils and Environment Authorised by Date Signed Mike Essex August 2020 Head of Infrastructure Issue No. Date Comments 1 August 2020 First Issue after document revised from L2 standard to document. C-05-OP-32-3001 This procedure will be reviewed at least annually and be revised as required. Printed copies of this document are uncontrolled. For the latest version click here: https://www.networkrail.co.uk/running-the-railway/looking-after-the-railway/asset-protection-and-optimisation/ or contact: Asset Protection Coordinator, Network Rail (High Speed), Singlewell Infrastructure Maintenance Depot, Henhurst Road, Cobham, Gravesend, Kent DA12 3AN Tel: 01474 563 554 Email: [email protected] Note that hyperlinks to internal Network Rail documents will not work for external users. In this case contact your Asset Protection Engineer. Photos: These are of generic sites around the High Speed 1 infrastructure taken by the author and other NR employees. Acknowledgements With Thanks to: Debra Iveson Asset Protection Coordinator Vital Communications by Office Depot for design, editing and publishing services 2 The Developers Handbook 3 Contents 1 Introduction 6 4 Developments above tunnels 28 6 Access 40 8 Lifting 54 1.1 Purpose 6 4.1 Construction 28 6.1 General 40 8.1 Types of plant 54 1.2 Scope 6 4.2 High Speed 1 subsoil acquisition 28 -
Channel Tunnel Rail Link Risk Transfer and Innovation in Project Delivery
Harvard Design School Version October 2008 Prof. Spiro N. Pollalis Dr. Andreas Georgoulias Channel Tunnel Rail Link Risk Transfer and Innovation in Project Delivery “Will this be the project that restores our belief that Britain can build a railway?” the Guardian asked in May 27, 2005, referring to the Channel Tunnel Rail Link (CTRL) project. The article added that although “it is one of the biggest engineering projects in the UK and the country’s first new train line in a century, few of us know the real success story.”1 At the same time, the CTRL team was looking forward to the next challenge in the infrastructure field: to transfer the significant experience gained from CTRL in UK to other parts of the globe. A major focus was on risk management and the need for new modes of cooperation and collaboration between all parties involved in a project, issues that had been dealt with successfully in the CTRL project. There were still issues to be addressed like the similarities and differences in the relationships between designers, contractors, government officials, and the public in each part of the world, and the identification, measurement, transfer, and handling of risk. CTRL provided lessons for all of the above. 1 Jonathan Glancey, "Tunnel vision," The Guardian, May 27, 2005. Dr. Andreas Georgoulias prepared this case under the supervision of Professor Spiro N. Pollalis as the basis for class discussion rather than to illustrate either effective or ineffective handling of an administrative situation. Copyright © 2006 by the President and Fellows of Harvard College. To order copies, visit http://www.gsd.harvard.edu/~pollalis, call (617) 495-9939 or write to Prof. -
The Arup Journal Ground Engineering 18 Nick O'riordan Marks a Special Moment When Our Creative Capability, Design Flare, and Ability to Deliver Have Become Tangible
.THEARUP JOURNAL ARUP CLIENT: ................._ ___ .. Jtn..._ Union Railways (wholly-owned subsidiary of l/11/llll London & Continental Railways Ltd) I/Ill/Ill un on RfEl/1/1/l lll DESIGNER AND PROJECT MANAGER: RAILWAYS LCR RAILUNK Rail Link Engineering (Arup, Bechtel, Halcrow, Systra) Published by Arup, 13 Fitzroy Street, London WH 4BQ, UK. Tel: +44 (0)20 7636 1531 Fax: +44 (0)20 7580 3924 e-mail: [email protected] www.arup.com Foreword Contents Foreword Terry Hill 2 Terry Hill Chairman, Arup The CTRL and Arup: Section 1 of the 109km Channel Tunnel Rail Link was opened by the UK 3 Introduction to the history Prime Minister Tony Blair on 28 September 2003 . With this opening came Mike Glover the first and long-awaited benefits of high-speed rail travel in Britain. Involving Safety - an industry-high safety record for construction - has been achieved 6 the communities and now travel will become safer and more convenient. Since the opening, Lisa Doughty the number of passengers using Eurostar, the London to Paris/Brussels Media relations high-speed rail seNice, has increased by 20%, and reliability has soared. 9 Lisa Doughty Paul Ravenscroft This is due to the commitment of a tremendous team of people in Arup and our partners in Rail Link Engineering, and the client's team in Union Rail safety Railways, who have brought a new catch phrase to railway construction - 10 Lorna Small 'on time, on budget'. CTRL and the environment It is also due in no small way to the creativity and innovation of Arup, for it 12 Paul Johnson was our firm that perceived the need for this project, conceived the solution, and has been delivering the result. -
IGNIS® Monofilament Fibre
Case studies North Downs Tunnel, Kent segments at a purpose built factory in The 3.2 km North Downs Tunnel forms Ridham Docks. part of the Channel Tunnel Rail Link running from Folkestone, Kent to De Westerschelde Tunnel, the St. Pancras in London. The primary Netherlands tunnel lining was made up of sprayed The client Maafroute BV instructed concrete. 1 kg of Ignis PP monofilament the precast contractors to add 1 kg fibres were added to the 60 N/mm2 of Ignis to the C40 concrete. The fibre concrete secondary lining. The lining was included in the concrete sections was constructed insitu, forming a forming the security exits, safety sacrificial layer. barriers and connection tunnels. T5, Heathrow Airport Dublin Port Tunnel, Ireland Ignis has been added to Grade C60 This 4 lane underground highway is concrete on various contracts within this designed to take heavy vehicle traffic prestigious project. The Ignis enhanced off the streets of Dublin. A 275 mm thick concrete has been used on site in lining over the tunnels arch is a non- sprayed concrete applications and it load bearing sacrificial concrete has also been added to precast ring containing 1-2 kg of Ignis. Adfil construction fibres are manufactured by Low & Bonar. materials. These materials contribute to a more The Group is a global leader in high performance sustainable world and higher quality of life. The quality materials selling in more than 60 countries worldwide systems of Low & Bonar facilities have been approved and manufacturing in Europe, North America and China. to the ISO 9001 Quality Management System Standard. -
Channel Tunnel Rail Link Risk Transfer and Innovation in Project Delivery
Harvard Design School Version November 01, 2006 Prof. Spiro N. Pollalis Channel Tunnel Rail Link Risk Transfer and Innovation in Project Delivery “Will this be the project that restores our belief that Britain can build a railway?” the Guardian asked in May 27, 2005, referring to the Channel Tunnel Rail Link (CTRL) project. The article added that although “it is one of the biggest engineering projects in the UK and the country’s first new train line in a century, few of us know the real success story.”1 At the same time, the CTRL team was looking forward to the next challenge in the infrastructure field: to transfer the significant experience gained from CTRL in UK to other parts of the globe. A major focus was on risk management and the need for new modes of cooperation and collaboration between all parties involved in a project, issues that had been dealt with successfully in the CTRL project. There were still issues to be addressed like the similarities and differences in the relationships between designers, contractors, government officials, and the public in each part of the world, and the identification, measurement, transfer, and handling of risk. CTRL provided lessons for all of the above. 1 Jonathan Glancey, "Tunnel vision," The Guardian, May 27, 2005. Doctor of Design candidate Andreas Georgoulias prepared this case under the supervision of Professor Spiro N. Pollalis as the basis for class discussion rather than to illustrate either effective or ineffective handling of an administrative situation. Copyright © 2006 by the President and Fellows of Harvard College. -
Laying the Groundwork for Britain's First High-Speed Rail Line
BECHTEL INFRASTRUCTURE AND CONSTRUCTION TheThe needneed forfor Medway bridge under construction speedspeed Laying the groundwork for Britain’s first The team responsible for constructing the Channel Tunnel Rail Link is making engineering high-speed rail line history with the 109 km line that is due to be completed in 2007. Stage 1 has already seen the movement of complete houses in one piece, the planting of 1.2 million trees and the construction of the longest high-speed rail The success of the Channel Tunnel mouth of the Channel Tunnel, the route bridge in Europe … Rail Link (CTRL) will be measured not goes over (and sometimes under) hill only by the technology that underpins it, and dale, traversing farmland and towns, but also by the time it takes to travel then dips through a 3 km tunnel beneath between London and Paris. By that the River Thames. Approaching London, hen the first section of the measure, the first section has it runs along a 1.3 km viaduct under the Channel Tunnel Rail Link succeeded by cutting the nearly three- Queen Elizabeth II Bridge, then plunges W opened for commercial hour trip by 20 minutes. When section 2 into a tunnel near Dagenham and services on 28 September 2003, – from north Kent to central London – continues underground for 10.5 km to a passengers for the most part were is completed in 2007, another 15 new international station at Stratford in unaware of the complex engineering minutes will be shaved off and the east London. It then heads into another required to build the new line. -
Ebbsfleet Style
Chapter 1 Archaeology and Engineering: High Speed 1 by H J Glass and S Foreman Introduction archive On ADS. A Gazetteer Of individual sites alOng the rOute, illustrated with rOute maps, is prOvided in High Speed 1 (HS1) is the first new railway tO be built in Appendix 1, and a list Of the detailed digital site and Britain fOr Over a century and is the UK’s first high speed specialist repOrts that are available tO dOwnlOad frOm the railway. The cOnstructiOn Of the railway became an ADS website is prOvided in Appendix 2. OppOrtunity tO investigate the rich heritage Of a lOng- inhabited cOrridOr thrOugh Kent frOm LOndOn tO the channel cOast, and the engineering feats required tO The route cOnstruct the rail link are rightly celebrated (Fig. 1.1). We hOpe, thrOugh the publicatiOn Of this vOlume, that the The high-speed line runs fOr 109km (68 miles) in tOtal, scale and impOrtance Of the assOciated archaeOlOgical between St Pancras InternatiOnal in LOndOn and the and histOric building investigatiOns will be becOme Channel Tunnel On the Kent cOast near FOlkestOne, and evident tO thOse with an interest in the heritage Of the cOnnects with the internatiOnal high speed rOutes regiOn. between LOndOn and Paris, and LOndOn and Brussels. Readers shOuld realise frOm the Outset that High HS1 SectiOn 1—the subject Of this bOOk—was the first Speed 1 was built in twO sectiOns, and that this vOlume is 74km sectiOn tO be built and lies entirely within Kent, cOncerned Only with SectiOn 1, which runs frOm the much Of it lies alOngside the rOute Of the M2 and M20 Channel Tunnel POrtal at FOlkestOne tO Fawkham mOtOrways. -
Cost Overruns in Tunnelling Projects: Investigating the Impact of Geological and Geotechnical Uncertainty Using Case Studies
infrastructures Article Cost Overruns in Tunnelling Projects: Investigating the Impact of Geological and Geotechnical Uncertainty Using Case Studies Chrysothemis Paraskevopoulou * and Georgios Boutsis School of Earth and Environment, University of Leeds, Leeds LS2 9JT, UK; [email protected] * Correspondence: [email protected] Received: 13 August 2020; Accepted: 7 September 2020; Published: 8 September 2020 Abstract: Tunnelling projects seldom meet the initial budget requirements. Commonly, these types of projects suffer from cost overruns, which subsequently lead to project delivery delays mainly due to unsuccessful ground investigation as specified in the literature. The presented work scrutinises the effect of ground investigation in cost overruns. More specifically, various cost figures (total cost, construction cost, tunnel cost) are analysed for two case studies i) the Channel tunnel in the UK and ii) the Olmos Tunnel in Peru. Clayton’s relation between ground investigation and the construction cost is utilised and further investigated. In the Channel tunnel, the main problems faced led to a cost overrun of 78% for the total cost, 66% for the construction cost and 77% for the tunnelling cost. In the Olmos tunnel, two main geological scenarios are analysed and the construction cost overrun is calculated at 9.6% and 6.7%. Drawing on the conclusions, this research work proves that ground investigation can be one of the major factors influencing the tunnel cost. Keywords: tunnelling cost; tunnel cost overruns; uncertainty; ground investigation 1. Introduction Tunnelling construction is growing worldwide as a result of increasing population requiring a wider use of confined space as well as the upkeep of the existing one resulting in rising cost [1,2]. -
Hs1 New Operator Guide
HS1 NEW OPERATOR GUIDE FEBRUARY 2013 HS1 New Operator Guide - February 2013 Table of Contents 1. Introduction .................................................................................................................................... 3 1.1. HS1 overview .......................................................................................................................... 3 1.2. Benefits of using HS1 .............................................................................................................. 6 1.3. Stations and onward connections......................................................................................... 10 1.4. Key industry relationships ..................................................................................................... 14 1.5. Document structure .............................................................................................................. 15 2. Stakeholders ................................................................................................................................. 16 3. Regulatory bodies and approvals required ................................................................................... 19 3.1. ORR........................................................................................................................................ 20 3.2. Department for Transport (DfT) ........................................................................................... 22 3.3. DfT, Land Transport Security Division (LTSD) ....................................................................... -
Tim Smart Smart Director Engineering & Assets
Tim Smart Director Engineering & Assets HS1 AGENDA • HS1 Overview • Ctti&EiiOiConstruction & Engineering Overview. • Funding • Pt&DliProcurement & Delivery • Operating Railway HS1 Overview: Infrastucture Domestic Temple Mills • 109 km modern, main lines train depot high speed track Ripple Lane freight connection linking London to Europe North Kent line Singlewell • 4i4 in terna tiona l Waterloo connection maintenance depot stations in areas undergoing East Kent major domestic line Channel regeneration and Tunnel St Pancras Stratford Ebbsfleet Ashford boundary growth Int’l Int’l Int’l Int’l • Breadth of Dollands Moor connections to freight terminal classic network HS1 Overview: Key Aspects • UK’s first High Speed Line. – London to Paris 2hr 15 min – London to Brussels 1 hr 51mins – Kent fast domestics service provides under half the journey time • Connects to Europe as part of the TEN’s • 109 Km of high speed track. – Max line speed 300km/h. Freight 140 Km/h • Project included construction of 4 stations; 2 depots. • HS1 as stimulated significant regional growth HS1 Overview: European TEN’s HS1 Overview: Timeline 88 89 90 91 92 93 94 95 96 97 98 99 00 01 02 03 04 05 06 07 Initial British Rail Route Studies Arup Route Chosen Reference Design Public Consultation CTRL Parliamentary Bill PPP Bidding LCR Awarded PPP Concession Design & Approvals Advanced Construction Works Section 1 Construction & Commissioning Section 2 Construction & Commissioning AGENDA • HS1 Overview • Ctti&EiiOiConstruction & Engineering Overview. • Funding • Procurement & Delivery • Operating Railway Construction & Engineering Overview: Open Line Cross Section UIC Gauge C. Largely TSI compliant 90 Km on ballasted track Construction of the railway also required 65 Km roads Route constructed low and in cutting for environmental reasons Construction & Engineering Overview: Significant Structures.