Bridge Rail for Messina Strait Bridge
Total Page:16
File Type:pdf, Size:1020Kb
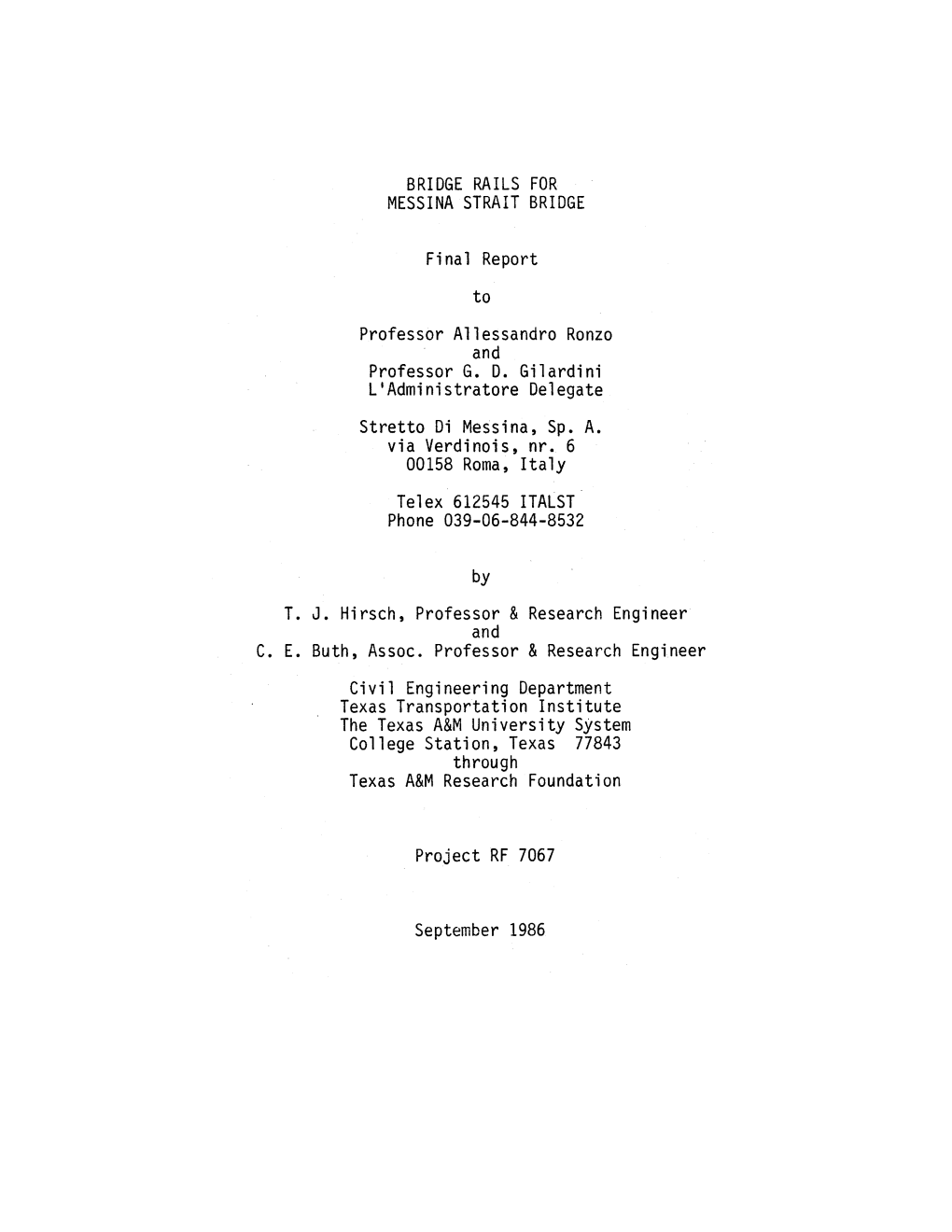
Load more
Recommended publications
-
IMPREGILO GROUP Origins
PROGRESS, OUR GREATEST WORK 2008 Annual Report 2008 The value of a group is tied to its history and concessions market, particularly for motorway IMPREGILO GROUP origins. networks, renewable energy plants and energy 2008 Annual Report Impregilo group was set up at the beginning of the transportation. It is also active in the plant and 1990s but its origins lie much further back as it is engineering and environmental services sectors. the legacy of Girola, Lodigini, Impresit and Cogefar. Dams, hydroelectric plants, motorways, railways, These prestigious Italian companies were at the underground train systems, tunnels, bridges, forefront of international civil engineering from the viaducts, desalination plants, fume treatment plants early twentieth century. and waste-to-energy plants: a wealth of experience gained in Italy and abroad thanks to its constant Active in all five continents, the companies that commitment to meeting deadlines, protecting the merged to become Impregilo engaged in the environment and deploying innovative technologies. IMPREGILO GROUP construction of the main motorway, railway and hydroelectric works underpinning development in Impregilo is a group looking to the future. It is Italy and in many other countries around the world, responsible and sensitive to its stakeholders’ and helped strengthen Italy’s international standing. expectations and has proved itself well capable of exploiting and anticipating market developments This rich history of tradition and success has made over its more than a hundred years of experience. Impregilo, listed on the Italian stock exchange, the leading general contractor in Italy and one of the Today, thanks to its business and organisational major international general construction companies. -
Interim Financial Report
(Translation from the Italian original which remains the definitive version) Interim financial report 30 June 2018 This document is available at: www.salini-impregilo.com Salini Impregilo S.p.A. Company managed and coordinated by Salini Costruttori S.p.A. Salini Impregilo S.p.A. Share capital €544,740,000 Registered office in Milan, Via dei Missaglia 97 Tax code and Milan Company Registration no. 00830660155 R.E.A. no. 525502 - VAT no. 02895590962 1 CONTENTS Company officers ................................................................................................................................................................... 3 Key events of the period......................................................................................................................................................... 4 Directors’ report - Part I ................................................................................................................. 5 Financial highlights ............................................................................................................................................................ 6 Performance ...................................................................................................................................................................... 9 Directors’ report - Part II .............................................................................................................. 20 Performance by geographical segment .......................................................................................................................... -
Annual Report 2017 Report 2017
ANNUAL ANNUAL REPORT 2017 REPORT 2017 I ANNUAL REPORT 31 DECEMBER 2017 TABLE OF CONTENTS CEO’S LETTER TO THE SHAREHOLDERS 4 COMPANY OFFICERS 12 OUR VISION AND GLOBAL PRESENCE 14 KEY EVENTS OF THE YEAR 16 DIRECTORS’ REPORT - PART I 22 FINANCIAL HIGHLIGHTS 24 PERFORMANCE 32 DIRECTORS’ REPORT - PART II 54 PERFORMANCE BY GEOGRAPHICAL SEGMENT 58 RISK MANAGEMENT SYSTEM 88 MAIN RISK FACTORS AND UNCERTAINTIES 96 EVENTS AFTER THE REPORTING DATE 126 OUTLOOK 128 REPORT ON CORPORATE GOVERNANCE AND THE OWNERSHIP STRUCTURE 130 ALTERNATIVE PERFORMANCE INDICATORS 132 OTHER INFORMATION 136 2017 CONSOLIDATED NON-FINANCIAL STATEMENT 138 CONSOLIDATED FINANCIAL STATEMENTS AS AT AND FOR THE YEAR ENDED 31 DECEMBER 2017 210 NOTES TO THE CONSOLIDATED FINANCIAL STATEMENTS 220 Statement of financial position 266 Statement of profit or loss 367 CONSOLIDATED FINANCIAL STATEMENTS OF SALINI IMPREGILO GROUP - INTRAGROUP TRANSACTIONS 388 CONSOLIDATED FINANCIAL STATEMENTS OF SALINI IMPREGILO GROUP - EQUITY INVESTMENTS 404 CONSOLIDATED FINANCIAL STATEMENTS OF SALINI IMPREGILO GROUP - LIST OF COMPANIES 416 STATEMENT ON THE CONSOLIDATED FINANCIAL STATEMENTS 438 SEPARATE FINANCIAL STATEMENTS OF SALINI IMPREGILO S.P.A. AS AT AND FOR THE YEAR ENDED 31 DECEMBER 2017 440 NOTES TO THE SEPARATE FINANCIAL STATEMENTS 450 Statement of financial position 482 Statement of profit or loss 545 Proposal to the shareholders of Salini Impregilo S.p.A. 566 SEPARATE FINANCIAL STATEMENTS OF SALINI IMPREGILO - INTRAGROUP TRANSACTIONS 568 SEPARATE FINANCIAL STATEMENTS OF SALINI IMPREGILO - EQUITY INVESTMENTS 588 STATEMENT ON THE SEPARATE FINANCIAL STATEMENTS 608 REPORTS 610 CEO’S LETTER TO THE SHAREHOLDERS Directors’ Report 6 ANNUAL REPORT 2017 Dear Shareholders, effective as shown not just by the numbers and the attained results, but also by the market’s acknowledgement. -
Italy-9-Index.Pdf
© Lonely Planet 925 Index A Alpe di Fanes 339-41 Brescia 285-7 AbbaziaABBREVIATIONS di Pomposa 463-4 Alpe di Siusi 338 Cagliari 839 AbbaziaACT di SanAustralian Galgano 544Capital Alta Badia 339, 340 Catania 795 Territory Abbazia di Sant’Antimo 550 Alta Murgia National Park 85 Catanzaro 750 NSW New South Wales Abruzzo 619-29, 622 alte vie hiking trails 316 Cuma 658-9 NT Northern Territory Abruzzo Lazio e Molise National Altipiano della Paganella 322-4 Fiesole 511 Qld Queensland Park 85 Alto Adige 313-16, 329-42, 318-19 Filicudi 786 SA South Australia abseiling 800, 866 Alto Lario 305 Herculaneum 671-2 Tas Tasmania AC Milan 276 Altopiano del Golgo 869-70 itineraries 32 Vic Victoria Accademia Carrara 283 Amalfi 685-7, 686 Lecce 723-4 WA Western Australia accommodation 871-5 Amalfi Coast 87, 681-91, 12 Lipari 780 agriturismo 21, 22, 579, 872 Ampezzo 424 Metaponto 733 B&Bs 872 amusement parks Naples 643 camping 698, 872-3 Aquafàn 471 Nora 844 convents 873 Aquaparadise 309 nuraghi 851, 852, 857, 859, 863, farmstays 579 CanevaWorld 309 865, 867, 868 hostels 873 Delfinario Rimini 471 Ostia Antica 179 hotels 873-4 Fiabilandia 471 Paestum 691-2, 11 internet resources 874-5 Gardaland 309 Perugia 569 language 907 Italia in Miniatura 471 Pietrabbondante 632 monasteries 873 Movieland 309 Pompeii 674-5 mountain huts 874 Anacapri 663-4, 664 Pozzuoli 657-8 pensioni 873-4 Ancona 601-5, 602 Rimini 470 rental accommodation 874 Andalo 322 Saepinum 630-1 villa rentals 874-5 animals 81-3, see also individual Selinunte 822 Acquafredda di Maratea 740 species -
Orthotropic Steel Deck Bridges in the U.S
ORTHOTROPIC STEEL DECK BRIDGES IN THE U.S. Brian M. Kozy1 and Justin Ocel2 Abstract This paper summarizes some of the recent developments in the U.S. on the subject of orthotropic steel deck (OSD) bridges. The Federal Highway Administration published a manual to provide up-to-date technical guidance on the proper design, construction and maintenance of OSDs for bridges and the AASHTO bridge design specifications have been greatly revised and expanded. The rib-to-deck weld continues to be an area of difficulty in OSD construction; due to competing desire for fabrication economy and fatigue longevity in the detail. Preliminary results from FHWA research on this detail are presented. Background Many of the world’s notable major bridge structures utilize the orthotropic steel plate system as one of the basic structural building blocks for distribution of traffic loads in decks and for the stiffening of slender plate elements in compression. Examples include the new San Francisco Oakland Bay Bridge, Self-Anchored Suspension Span in California and the proposed Strait of Messina Bridge in Italy. Stiffened steel plates have been used for many years in a wide range of steel construction applications. They are particularly prevalent in the ship building industry and for hydraulic applications such as tanks, gates, and locks. The first orthotropic steel deck (OSD) bridge was developed by German engineers in the 1930's and the first such deck was constructed in 1936. In the United States, a similar system was built and often referred to as a “battle deck” because it was considered to be as strong as a battleship. -
XXIV Liberation, Redemption, Autonomy
XXIV Liberation, Redemption, Autonomy: Contemporary Utopias in Southern Italian Popular Music Marcello Messina1 Introduction Alongside the passionate interest, shown by Southern Italian intellectuals and artists, for the renegotiation of the official historical narratives (Messina 2015), the celebra- tions for the 150th anniversary of the Unification of Italy have at times reawakened the need to imagine a better future. These exercises in utopianism have constructed, from time to time, a future characterized by the liberation from the mafia, or by the bridge of the economic gap with the rest of the country, or even by the overcoming of national unity towards autonomy or independence-based solutions. Taking Co- nelli’s (2013) and Polizzi’s (2013) works on Southern Italy (aka Mezzogiorno) and post- coloniality as fundamental premises, this work seeks to interpret this phenomenon in the light of the theoretical tools provided by postcolonial studies, and in particular by the concept of postcolonial utopia, formulated, among others, by Ashcroft (2012). A key element is memory, whereby historical chronicles become, in a way, the allegory of present power relations and the discussion of the past serves to open up a debate about the present (Slemon 1988). Ashcroft argues that memory is also fun- damental “in the formation of utopian concepts of a liberated future” (2012: 2), and 1 I would like to thank Raquel Ishii, Jairo Souza, Cristina Perissinotto and Albert Göschl for their precious insights. liberation, redemption, autonomy 377 continues by mentioning two other characteristics of postcolonial utopias, namely the obsession with place and the problematic relationship with the concept of nation (2012: 3-4). -
Safety and Reliability of Bridge Structures
SAFETY AND RELIABILITY OF BRIDGE STRUCTURES Safety and Reliability of Bridge Structures Edited by Khaled M. Mahmoud Bridge Technology Consulting New York City, USA Front Cover: Kanchanaphisek Bridge, Samut Prakan Province, Thailand Photo courtesy of Parsons Brinckerhoff, USA Back Cover: (From top to bottom) Grimselsee Bridge, Bern, Switzerland Rendering courtesy of Christian Menn, Switzerland Kingston-Rhinecliff Bridge, Kingston, New York, USA Photo courtesy of New York State Bridge Authority, USA Cover Design: Khaled M. Mahmoud Bridge Technology Consulting, New York City, USA CRC Press/Balkema is an imprint of the Taylor & Francis Group, an informa business © 2009 Taylor & Francis Group, London, UK Typeset by Vikatan Publishing Solutions (P) Ltd., Chennai, India Printed and bound in the USA by Edwards Brothers, Inc, Lillington, NC All rights reserved. No part of this publication or the information contained herein may be reproduced, stored in a retrieval system, or transmitted in any form or by any means, electronic, mechanical, by photocopying, recording or otherwise, without written prior permission from the publisher. Although all care is taken to ensure integrity and the quality of this publication and the information herein, no responsibility is assumed by the publishers nor the author for any damage to the property or persons as a result of operation or use of this publication and/or the information contained herein. Published by: CRC Press/Balkema P.O. Box 447, 2300 AK Leiden, The Netherlands e-mail: [email protected] www.crcpress.com – www.taylorandfrancis.co.uk – www.balkema.nl ISBN: 978-0-415-56484-7 (Hbk) ISBN: 978-0-203-86158-5 (Ebook) Table of contents Preface IX 1 Bridge safety, analysis and design The safety of bridges 3 T.V. -
Compared Cost Evaluation Among Traditional Versus Innovative Strait Crossing Solutions
Available online at www.sciencedirect.com Procedia Engineering Procedia Engineering 2 (2010) 000–000 www.elsevier.com/locate/procedia Procedia Engineering 4 (2010) 293–301 www.elsevier.com/locate/procedia ISAB-2010 Compared cost evaluation among traditional versus innovative strait crossing solutions G. Martire, B. Faggiano, F.M. Mazzolani* DIST – Department of Structural Engineering, University of Naples Federico II, P.le Tecchio 80, 80125, Naples, Italy Received 4 August 2010; accepted 4 August 2010 Abstract Among the traditional solutions in use to cross waterways Cable Supported Bridges (CSB), such as suspension and cable stayed ones, nowadays represent one of the most widely realized. However this structural typology feature several problems, in particular when large spans have to be surpassed. Submerged Floating Tunnel (SFT) is instead an innovative technical solution in the field of waterway crossings, particularly suitable and advantageous in case of long waterway crossings. As a matter of fact, thanks to its modularity, the SFT structural performance is not greatly affected by the crossing length; also, its cost varies linearly with its length, differently from Cable Supported Bridges. At the stage of selection of the structural solutions to be adopted a decisive role is played by economic aspects. In particular, the building cost of each available solution has to be assessed in order to come to the final choice. Therefore simple procedures for the evaluation of the realization cost of the crossing solutions are needed; such a kind of procedures, considering only the costs related to quantity of steel, are already available for traditional Cable Supported Bridges. The scope of the present study is to provide a similar procedure for Submerged Floating Tunnels, thus allowing for quickly comparing the cost-effectiveness of the latter solutions with the one of traditional CSB solutions. -
Suspended Bridges Subjected to Moving Loads and Support Motions Due to Earthquake
ARTICLE IN PRESS JOURNAL OF SOUND AND VIBRATION Journal of Sound and Vibration 319 (2009) 218–227 www.elsevier.com/locate/jsvi Suspended bridges subjected to moving loads and support motions due to earthquake Ladislav Fry´baa,Ã, Jong-Dar Yaub,1 aInstitute of Theoretical and Applied Mechanics, v.v.i., Academy of Sciences of the Czech Republic, Prosecka 76, CZ – 190 00 Prague 9, Czech Republic bDepartment of Architecture and Building Technology, Tamkang University, 5 Lane 199, Kinghua Street, Taipei, Taiwan Received 5 December 2006; received in revised form 8 January 2008; accepted 9 May 2008 Handling Editor: A.V. Metrikine Available online 3 July 2008 Abstract The paper deals with the vibration of suspended bridges subjected to the simultaneous action of moving loads and vertical support motions due to earthquake. The basic partial integro-differential equation is applied to the vertical vibration of a suspended beam. The dynamic actions of traffic loads are modelled as a row of equidistant moving forces, while the earthquake is considered by vertical motions of supports. The governing equation is solved first analytically to receive an ordinary differential equation and next numerically. Moreover, the designed world’s largest suspended bridge— Messina Bridge—is investigated (central span of length 3.3 km). The paper studies the effect of various lags of the earthquake arrival because the earthquake may appear at any time when the train moves along a large-span bridge. The modified Kobe earthquake records have been applied to calculations. The results indicate that the interaction of both the moving and seismic forces may substantially amplify the response of long-span suspended bridges in the vicinity of the supports and increase with the rising speed of trains. -
Experimental Investigation of Effect of Windshield Barriers on the Aerodynamic Properties of the Multi-Box Bridge Decks
Experimental Investigation of Effect of Windshield Barriers on the Aerodynamic Properties of the Multi-box Bridge Decks by Xi Chen A thesis submitted to the Faculty of Graduate and Postdoctoral Studies in partial fulfilment of the requirements for the degree of Masters of Applied Science In Civil Engineering Department of Civil Engineering University of Ottawa Ottawa, Canada June 2015 © Xi Chen, Ottawa, Canada, 2015 Acknowledgements I would like to express my deepest appreciation to Dr. Elena Dragomirescu for her untiring and sincere teachings. She patiently guided me from choosing the topic to submitting the thesis. I'm also grateful to Dr. Muslim Majid for the advices and assistance when I was preparing the experiments. Thanks to Dr. Bas Baskaran and Mr. Steve Ko who lend the equipment needed for the experiment. Particular I am thankful to Mr. Vincent Ferraro, Mr. Un Yong Jeong, Mr. Dave Menard and Mr. Ryan Rosborough for making available the wind tunnel facility used in this experiment and for modifying the experimental model and technique support. My deepest thanks go to Fan Feng, Zhida Wang, Songyu Cao, Xiangwen Zuo and all my friends for their various kinds of helps during the experiment procedure. Finally, I would like to acknowledge with gratitude, the support and love from my family and my girlfriend. Their understanding and unwavering support kept me going and helped me overcoming difficulties. ii Abstract With the development of aerodynamic investigation methods, long-span bridge projects gradually became more open to adopt challenging geometric optimizations and countermeasure implementations. Thus the bridge girder decks improved as well, changing from the compact box-deck girders shapes, to twin-box and multi-box deck sections. -
13 English Texts 21/11/11 10.12 Pagina 170
17.English Texts_13_English Texts 21/11/11 10.12 Pagina 170 170 ENGLISH TEXTS TITLE OF THE ISSUE Studies on Italian Architecture of the Twentieth Century EDITORIAL In an era without memory, that easily accepts rapid infatuations and equally sudden abandonment, Marcello In 2006, when Marcelo Rebecchini (who created this cultivated memory even at the risk of resembling a magazine, together with Giuseppe Nicolosi, Edoardo conservative. Instead, he was curious to understand. Salzano and Umberto De Martino, almost 50 years ago) Though he was also severe in his criticism of those who decided, regretfully, to end his university teaching career “for praise form as an end in itself, self-satisfied theorisers of a having reached the maximum age limit”, there was one thing that fantastic, eccentric architecture, openly ignoring reality and a subtly gnawed at him, a sort of regret, a future nostalgia, a its problems. In these figures he saw the refusal of any sensation that he defined with a smile and almost ethical involvement. apologetically as “inconvenient”: it was the sensation of one Not by accident he greatly admired Stendhal; his was an who fears, during the passage of testimony, that he has not antique admiration, almost adolescent, from his high school done enough to leave at least “some sign”, a “tangible years. A passion cultivated throughout his entire life. His record” of his passage, something that continues to speak last book, dedicated to Stendhal, was published of the school as it was once and as he experienced it, the posthumously. lessons he learned, the discipline that he cultivated and As Stendhal was not an admirer of the Baroque and transmitted for so many years. -
A Journey to the Heart of the Island
Sicily A journey to the heart of the island Discovering the colours, flavours and rites of the biggest island in the Mediterranean sea Regione Siciliana POR Sicilia UNIONE EUROPEA Assessorato Turismo, 2000-2006 Fondo Europeo Trasporti e Comunicazioni Misura 4.18 a/b Sviluppo Regionale www.regione.sicilia.it/turismo A journeySicily to the heart of the island Discovering the colours, flavours and rites of the biggest island in the Mediterranean sea index Knowing Sicily A paradise made of sea and sun island Treasure oasi Green pag 04 pag 12 pag 22 pag 54 Language ......................... 6 Among shores, The early settlements ..... 24 Regional parks ............... 56 cliffs and beaches .......... 14 Documents and Exchange . 6 The Greek domination .... 26 Reserves and The fishing villages, the protected areas .............. 58 The weather and what The Roman civilization ... 32 fishing tourism and wearing ............................ 6 The Arab-Norman period .. 34 Outdoor sports................ 60 the sea cooking .............. 16 Festivities ......................... 7 Frederick II and the Country tourism Minor Islands and marine Swabians ....................... 38 and baths ...................... 62 Trasportation .................... 7 protected areas: a paradise Medieval Sicily ............... 42 Roads ............................... 8 for diving and snorkelling .. 18 The explosion of Emergency numbers ........ 8 Marina Charters, tourist 02 harbours and the Baroque..................... 45 Geography ........................ 8 aquatic sports ................. 20 Bourbon’s age ................ 48 History ............................ 10 The Florio’s splendour .... 50 The museums ................ 52 The memory of the Island An island opened all the year Master in hosting Maps of the provinces pag 64 pag 76 pag 86 pag 100 The non-material Religious celebrations .... 78 The routes of wine ......... 88 Palermo ........................ 102 heritage register ............. 66 Theatre and Gastronomy ...................