Performance of Steam Assisted Gravity Drainage in Thin Oil Sand Reservoirs: Well Pair Configuration
Total Page:16
File Type:pdf, Size:1020Kb
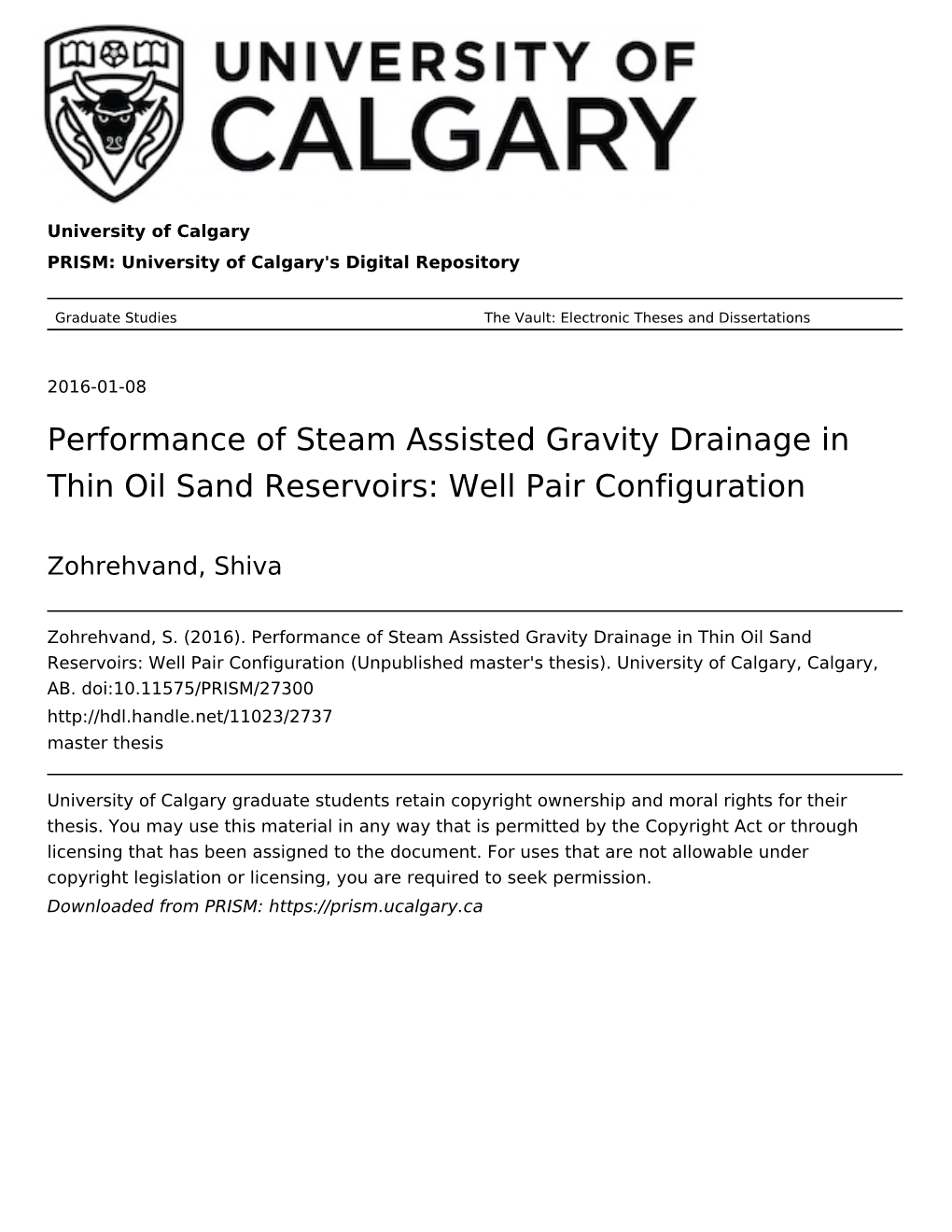
Load more
Recommended publications
-
A Comprehensive Guide to the Alberta Oil Sands
A COMPREHENSIVE GUIDE TO THE ALBERTA OIL SANDS UNDERSTANDING THE ENVIRONMENTAL AND HUMAN IMPACTS , EXPORT IMPLICATIONS , AND POLITICAL , ECONOMIC , AND INDUSTRY INFLUENCES Michelle Mech May 2011 (LAST REVISED MARCH 2012) A COMPREHENSIVE GUIDE TO THE ALBERTA OIL SANDS UNDERSTANDING THE ENVIRONMENTAL AND HUMAN IMPACTS , EXPORT IMPLICATIONS , AND POLITICAL , ECONOMIC , AND INDUSTRY INFLUENCES ABOUT THIS REPORT Just as an oil slick can spread far from its source, the implications of Oil Sands production have far reaching effects. Many people only read or hear about isolated aspects of these implications. Media stories often provide only a ‘window’ of information on one specific event and detailed reports commonly center around one particular facet. This paper brings together major points from a vast selection of reports, studies and research papers, books, documentaries, articles, and fact sheets relating to the Alberta Oil Sands. It is not inclusive. The objective of this document is to present sufficient information on the primary factors and repercussions involved with Oil Sands production and export so as to provide the reader with an overall picture of the scope and implications of Oil Sands current production and potential future development, without perusing vast volumes of publications. The content presents both basic facts, and those that would supplement a general knowledge base of the Oil Sands and this document can be utilized wholly or in part, to gain or complement a perspective of one or more particular aspect(s) associated with the Oil Sands. The substantial range of Oil Sands- related topics is covered in brevity in the summary. This paper discusses environmental, resource, and health concerns, reclamation, viable alternatives, crude oil pipelines, and carbon capture and storage. -
Heavy Oil Vent Mitigation Options - 2015”
Environment Canada Environmental Stewardship Branch “Heavy Oil Vent Mitigation Options - 2015” Conducted by: New Paradigm Engineering Ltd. Prepared by: Bruce Peachey, FEIC, FCIC, P.Eng. New Paradigm Engineering Ltd Ph: (780) 448-9195 E-mail: [email protected] Second Edition (Draft) April 30, 2015 Acknowledgements and Disclaimer Acknowledgements The author would like to acknowledge funding provided by Environment Canada, Environmental Stewardship Branch, and the support of a wide range of equipment vendors, producers and other organizations whose staff have contributed to direction, content or comments. This second edition is an upgrade to the initial report for Environment Canada and reflects additional work and content developed by New Paradigm Engineering Ltd. Our intent is to continue to provide in-kind updates, as necessary to keep information current and to reflect any additional information we are made aware of. Disclaimers This document summarizes work done under this contract in support of Environment Canada’s efforts to understand the potential sources of methane venting from primary, or cold, heavy oil operations in Western Canada and the potential mitigation options and barriers to mitigation to reduce those emissions. Any specific technologies, or applications, discussed or referred to, are intended as examples of potential solutions or solution areas, and have not been assessed in detail, or endorsed as to their technical or economic viability. Suggestions made as recommendations for next steps, or follow-up actions are based on the authors’ learnings during the project, but are not intended as specific input to any government policy or actions, which might be considered in crafting future emissions policies. -
Canada's Oil Sands and Heavy Oil Deposits
14 APPENDED DOCUMENTS 14.1 Appendix 1: CANADA'S OIL SANDS AND HEAVY OIL DEPOSITS Vast deposits of viscous bitumen (~350 x 109m3 oil) exist in Alberta and Saskatchewan. These deposits contain enough oil that if only 30% of it were extracted, it could supply the entire needs of North America (United States and Canada) for over 100 years at current consumption levels. The deposits represent "plentiful" oil, but until recently it has not been "cheap" oil. It requires technologically intensive activity and the input of significant amounts of energy to exploit it. Recent developments in technology (horizontal drilling, gravity drainage, unheated simultaneous production of oil and sand, see attached note) have opened the possibility of highly efficient extraction of oil sands at moderate operating cost. For example, the average operating costs for a barrel of heavy oil was CAN$10- 12 in 1989; it was CAN$5-6 in 1996, without correcting for any inflation. This triggered a “mini-boom” in heavy oil development in Alberta and Saskatchewan until the price crash of 1997-1998. However, reasonable prices have triggered more interest in the period 2000-2001, and heavy oil and oil sands development is accelerating. At present, heavy oil production is limited by a restricted refining capacity (upgraders designed specially for the viscous, high sulfur, high heavy metal content crude oil), not by our ability to produce it in the field. Currently (2002), nearly 50% of Canada's oil production comes from the oil sands and the heavy oil producing, high porosity sandstone reservoirs which lie along the Alberta-Saskatchewan border. -
Alberta Energy Regulator Index of Aer Orders and Approvals Ogs
INDEX OF AER ORDERS AND APPROVALS OAK OAK FIELD 0659 September 2021 Page 1 of 1 FIELD DESIGNATION 0659 2011-05-01 OAK FIELD POOL DESIGNATION 0659 304001 2009-09-01 BLUESKY A 0659 432001 2010-04-01 ROCK CREEK A 0659 606001 2001-02-01 KISKATINAW A 0659 606002 2001-02-01 KISKATINAW B 0659 606003 2013-07-01 KISKATINAW C 0659 658001 2001-02-01 WABAMUN A ALBERTA ENERGY REGULATOR INDEX OF AER ORDERS AND APPROVALS OGS OGSTON FIELD 0664 September 2021 Page 1 of 2 FIELD DESIGNATION 0664 2012-04-01 OGSTON FIELD POOL DESIGNATION 0664 304001 2010-04-01 BLUESKY A 0664 773502 2008-05-01 KEG RIVER SAND B 0664 797502 2008-06-01 GRANITE WASH B 0664 797503 2008-06-01 GRANITE WASH C 0664 797504 2008-06-01 GRANITE WASH D 0664 797505 2010-04-01 GRANITE WASH E 0664 797506 2008-06-01 GRANITE WASH F 0664 797507 2008-06-01 GRANITE WASH G 0664 797508 2008-06-01 GRANITE WASH H 0664 797509 2008-06-01 GRANITE WASH I 0664 797510 2008-06-01 GRANITE WASH J 0664 797511 2008-06-01 GRANITE WASH K 0664 797512 2008-06-01 GRANITE WASH L 0664 797514 2008-06-01 GRANITE WASH N 0664 797515 2008-06-01 GRANITE WASH O 0664 797516 2008-06-01 GRANITE WASH P 0664 797517 2008-06-01 GRANITE WASH Q 0664 797518 2008-06-01 GRANITE WASH R 0664 797519 2008-06-01 GRANITE WASH S 0664 797520 2008-06-01 GRANITE WASH T 0664 797521 2015-12-01 GRANITE WASH U 0664 797522 2008-06-01 GRANITE WASH V 0664 797523 2008-06-01 GRANITE WASH W 0664 797524 2008-06-01 GRANITE WASH X 0664 797525 2008-06-01 GRANITE WASH Y 0664 797526 2008-06-01 GRANITE WASH Z 0664 797527 2008-06-01 GRANITE WASH AA 0664 797528 2008-06-01 GRANITE WASH BB 0664 797529 2008-06-01 GRANITE WASH CC 0664 797530 2013-07-01 GRANITE WASH DD ALBERTA ENERGY REGULATOR INDEX OF AER ORDERS AND APPROVALS OGS OGSTON FIELD 0664 September 2021 Page 2 of 2 SPACING PATTERN SU 2462 16 Jan 1996 SU 2462A 15 Apr 1998 SUBSURFACE DISPOSAL SCHEMES App 9171E 17 Nov 2015 Class II Cardinal Energy Ltd. -
Alberta Oil Sands Industry Quarterly Update
ALBERTA OIL SANDS INDUSTRY QUARTERLY UPDATE WINTER 2013 Reporting on the period: Sep. 18, 2013 to Dec. 05, 2013 2 ALBERTA OIL SANDS INDUSTRY QUARTERLY UPDATE Canada has the third-largest oil methods. Alberta will continue to rely All about reserves in the world, after Saudi to a greater extent on in situ production Arabia and Venezuela. Of Canada’s in the future, as 80 per cent of the 173 billion barrels of oil reserves, province’s proven bitumen reserves are the oil sands 170 billion barrels are located in too deep underground to recover using Background of an Alberta, and about 168 billion barrels mining methods. are recoverable from bitumen. There are essentially two commercial important global resource This is a resource that has been methods of in situ (Latin for “in developed for decades but is now place,” essentially meaning wells are gaining increased global attention used rather than trucks and shovels). as conventional supplies—so-called In cyclic steam stimulation (CSS), “easy” oil—continue to be depleted. high-pressure steam is injected into The figure of 168 billion barrels TABLE OF CONTENTS directional wells drilled from pads of bitumen represents what is for a period of time, then the steam considered economically recoverable is left to soak in the reservoir for a All about the oil sands with today’s technology, but with period, melting the bitumen, and 02 new technologies, this reserve then the same wells are switched estimate could be significantly into production mode, bringing the increased. In fact, total oil sands Mapping the oil sands bitumen to the surface. -
Environmental Assessment – Joint Review Panel in the MATTER of FRONTIER OIL SANDS PROJECT Teck Resources Limited
Environmental Assessment – Joint Review Panel IN THE MATTER OF FRONTIER OIL SANDS PROJECT Teck Resources Limited CEAA Reference No. 65505 SUBMISSIONS ON IMPACTS OF THE FRONTIER OIL SANDS PROJECT ON WOOD BUFFALO NATIONAL PARK Filed by: Canadian Parks and Wilderness Society (CPAWS) CPAWS Northern Alberta Chapter P.O. Box 52031 Edmonton, AB T6G 2T5 Tel.: (780) 328-3780 Email: [email protected] PART I: INTRODUCTION The Canadian Parks and Wilderness Society is a nationwide charity dedicated to the protection and sustainability of Canada’s public land and water, and ensuring that parks are managed to protect the nature within them. CPAWS Northern Alberta’s role as an organization is to provide landscape-scale, science-based support and advice for the conservation and protection of Alberta’s wilderness. CPAWS Northern Alberta has championed the protection of Alberta’s diverse natural heritage since its establishment in 1968, and regularly collaborates with government, industry, and Indigenous communities on these issues. CPAWS Northern Alberta also strives to educate and bring awareness to Alberta’s residents and visitors about the importance of protecting Alberta’s wilderness. These are the submissions of CPAWS Northern Alberta ("CPAWS") to the Joint Review Panel ("JRP") in relation to the impacts of the Frontier Oil Sands Project (the "Project") on Wood Buffalo National Park ("Park" or “WBNP”). By separate filing on behalf of CPAWS, the Pacific Centre for Environmental Law and Litigation has filed evidence and submissions in relation to the greenhouse gas emissions associated with the Project. In relation to the submissions and evidence contained herein regarding the impacts of the Project on the Park, CPAWS has retained Mr. -
Final Sea Report
VOLUME 1: MILESTONE 3 - FINAL SEA REPORT Strategic Environmental Assessment of Wood Buffalo National Park World Heritage Site It will be iniS May 2018 FINAL REPORT: Strategic Environmental Assessment of Wood Buffalo National Park COVERING LETTER Independent Environmental Consultants 70 Valleywood Drive, Suite 200 Markham, ON, L3R 4T5 Tel/Fax: 844-736-7369 PSX16-0057 30 May 2018 Parks Canada Government of Canada 145 McDermot Avenue Winnipeg MB R3B 0R9 Attention: Katherine Cumming National Manager of Impact Assessment, Natural Resource Conservation Branch RE: Final Strategic Environmental Assessment of Potential Cumulative Impacts of all Developments on the Outstanding Universal Value of Wood Buffalo National Park World Heritage Site Independent Environmental Consultants (IEC) is pleased to submit this final Strategic Environmental Assessment (SEA) report. This two-volume report is being submitted in accordance with completion of Milestone 3 of the above noted Contract. Yours very truly, Independent Environmental Consultants Donald M. Gorber, PhD, P. Eng. President Page i FINAL REPORT: Strategic Environmental Assessment of Wood Buffalo National Park ACKNOWLEDGEMENT The journey to complete this Strategic Environmental Assessment has involved the gathering of a significant volume of available information, including both western science and Indigenous Traditional Knowledge. All of this has been accomplished through phone discussions with government staff, researchers, industrial associations and Non-Government Environmental Organizations, -
Index of Aer Orders and Approvals Oak
INDEX OF AER ORDERS AND APPROVALS OAK OAK FIELD 0659 October 2020 Page 1 of 1 FIELD DESIGNATION 0659 2011-05-01 OAK FIELD POOL DESIGNATION 0659 304001 2009-09-01 BLUESKY A 0659 432001 2010-04-01 ROCK CREEK A 0659 606001 2001-02-01 KISKATINAW A 0659 606002 2001-02-01 KISKATINAW B 0659 606003 2013-07-01 KISKATINAW C 0659 658001 2001-02-01 WABAMUN A ALBERTA ENERGY REGULATOR INDEX OF AER ORDERS AND APPROVALS OGS OGSTON FIELD 0664 October 2020 Page 1 of 2 FIELD DESIGNATION 0664 2012-04-01 OGSTON FIELD POOL DESIGNATION 0664 304001 2010-04-01 BLUESKY A 0664 773502 2008-05-01 KEG RIVER SAND B 0664 797502 2008-06-01 GRANITE WASH B 0664 797503 2008-06-01 GRANITE WASH C 0664 797504 2008-06-01 GRANITE WASH D 0664 797505 2010-04-01 GRANITE WASH E 0664 797506 2008-06-01 GRANITE WASH F 0664 797507 2008-06-01 GRANITE WASH G 0664 797508 2008-06-01 GRANITE WASH H 0664 797509 2008-06-01 GRANITE WASH I 0664 797510 2008-06-01 GRANITE WASH J 0664 797511 2008-06-01 GRANITE WASH K 0664 797512 2008-06-01 GRANITE WASH L 0664 797514 2008-06-01 GRANITE WASH N 0664 797515 2008-06-01 GRANITE WASH O 0664 797516 2008-06-01 GRANITE WASH P 0664 797517 2008-06-01 GRANITE WASH Q 0664 797518 2008-06-01 GRANITE WASH R 0664 797519 2008-06-01 GRANITE WASH S 0664 797520 2008-06-01 GRANITE WASH T 0664 797521 2015-12-01 GRANITE WASH U 0664 797522 2008-06-01 GRANITE WASH V 0664 797523 2008-06-01 GRANITE WASH W 0664 797524 2008-06-01 GRANITE WASH X 0664 797525 2008-06-01 GRANITE WASH Y 0664 797526 2008-06-01 GRANITE WASH Z 0664 797527 2008-06-01 GRANITE WASH AA 0664 797528 2008-06-01 GRANITE WASH BB 0664 797529 2008-06-01 GRANITE WASH CC 0664 797530 2013-07-01 GRANITE WASH DD ALBERTA ENERGY REGULATOR INDEX OF AER ORDERS AND APPROVALS OGS OGSTON FIELD 0664 October 2020 Page 2 of 2 SPACING PATTERN SU 2462 16 Jan 1996 SU 2462A 15 Apr 1998 SUBSURFACE DISPOSAL SCHEMES App 9171E 17 Nov 2015 Class II Cardinal Energy Ltd. -
Alberta Energy Annual Report 2013
Energy Annual Report 2013-2014 Energy Annual Report 2013-2014 Preface 3 Minister’s Accountability Statement 4 Minister’s Message 5 Management’s Responsibility for Reporting 7 Ministry Overview 9 The Energy Story 11 Energy Highlights 14 Non-Renewable Resource Revenue 16 Results Analysis 19 Review Engagement Report 20 Performance Measures Summary Table 21 Goal One 23 Goal Two 31 Goal Three 40 Appendix A: Performance Measure Methodologies 48 Financial Statements Ministry of Energy Financial Statements 53 Department of Energy Financial Statements 73 Alberta Energy Regulator Financial Statements 91 Alberta Utilities Commission Financial Statements 109 Alberta Petroleum Marketing Commission Financial Statements 123 Post-closure Stewardship Fund Financial Statements 141 Statutory Report 145 Other Information 145 2013-2014 Energy Annual Report 1 2 2013-2014 Energy Annual Report Preface The Public Accounts of Alberta are prepared in accordance with the Financial Administration Act and the Fiscal Management Act. The Public Accounts consist of the annual report of the Government of Alberta and the annual reports of each of the 19 ministries. The annual report of the Government of Alberta contains ministers’ accountability statements, the consolidated financial statements of the province and Measuring Up report, which compares actual performance results to desired results set out in the government’s strategic plan. This annual report of the Ministry of Energy contains the minister’s accountability statement, the audited consolidated financial statements -
Bp and Shell: Rising Risks in Tar Sands Investments Contents
BP AND SHELL: RISING RISKS IN TAR SANDS INVESTMENTS CONTENTS Summary and recommendations to investors 3 Will the tar sands bubble burst? 4 Heroic prospects or desperate measures? 6 A transcontinental infrastructure project 9 A transnational finance project 15 Risk 1 – Regulation: tightening constraints 17 Risk 2 – Operational: mounting technological and cost pressures 21 Risk 3 – Reputational: weakening public acceptance 24 Conclusion 27 Appendices 28 ACKNOWLEDGEMENTS This report was written and researched by James Marriott of PLATFORM, Lorne Stockman and Charlie Kronick of Greenpeace UK. The authors would like to thank the following for their comments and contributions to the report: Colin Baines of The Cooperative Group, Niall O’Shea of The Co-operative Asset Management, Mark Hoskins and Peter Holden of Holden & Partners, Kirsty Hamilton, Andrew Dlugolecki, Nick Robins, Paul Dickinson of Carbon Disclosure Project, Marc Brammer of Innovest, Ben Watson of Fairs Pensions, Matt Crossman of Rathbone Greenbank Investments, Miles Litvinoff of Ecumenical Council for Corporate Responsibility, Hyewon Kong and Seb Beloe of Henderson Global Investors, Stephanie Maier of EIRIS, James Leaton of WWF UK, Kenny Bruno and Steve Kretzman of Oil Change International, Mika Minio, Greg Muttitt, Kevin Smith of PLATFORM and John Sauven, Mike Hudema and Anna Rognaldsen of Greenpeace. SUMMARY AND RECOMMENDATIONS TO INVESTORS THIS REPORT DETAILS THE RANGE OF EXISTING AND EMERGING RISKS THAT BP AND SHELL FACE FROM THEIR EXPANSION OF PRODUCTION IN THE CANADIAN TAR SANDS. WE BELIEVE THESE RISKS ARE SIGNIFICANT FOR BP AND SHELL SHAREHOLDERS AND THAT INVESTORS SHOULD QUESTION THE COMPANIES MORE DEEPLY ON THEIR TAR SANDS STRATEGIES AND CALL FOR GREATER TRANSPARENCY REGARDING THE ASSESSMENT OF THE MID TO LONG TERM VIABILITY OF THESE PROJECTS. -
Alberta Oil Sands Industry Quarterly Update
ALBERTA OIL SANDS INDUSTRY QUARTERLY UPDATE SPRING 2014 Reporting on the period: Dec. 06, 2013 to Mar. 17, 2014 2 ALBERTA OIL SANDS INDUSTRY QUARTERLY UPDATE Canada has the third-largest oil methods. Alberta will continue to rely All about reserves in the world, after Saudi to a greater extent on in situ production Arabia and Venezuela. Of Canada’s in the future, as 80 per cent of the 173 billion barrels of oil reserves, province’s proven bitumen reserves are the oil sands 170 billion barrels are located in too deep underground to recover using Background of an Alberta, and about 168 billion barrels mining methods. are recoverable from bitumen. There are essentially two commercial important global resource This is a resource that has been methods of in situ (Latin for “in developed for decades but is now place,” essentially meaning wells are gaining increased global attention used rather than trucks and shovels). as conventional supplies—so-called In cyclic steam stimulation (CSS), “easy” oil—continue to be depleted. high-pressure steam is injected into TABLE OF CONTENTS The figure of 168 billion barrels directional wells drilled from pads of bitumen represents what is for a period of time, then the steam considered economically recoverable is left to soak in the reservoir for a All about the oil sands with today’s technology, but with period, melting the bitumen, and 02 new technologies, this reserve then the same wells are switched estimate could be significantly into production mode, bringing the increased. In fact, total oil sands Mapping the oil sands bitumen to the surface. -
Reducing the Environmental Impact of Bitumen Extraction
REDUCING THE ENVIRONMENTAL IMPACT OF BITUMEN EXTRACTION WITH ES-SAGD PROCESS A Thesis by ALBINA MUKHAMETSHINA Submitted to the Office of Graduate and Professional Studies of Texas A&M University in partial fulfillment of the requirements for the degree of MASTER OF SCIENCE Chair of Committee, Berna Hascakir Committee Members, Robert Lane Yuefeng Sun Head of Department, A. Daniel Hill December 2013 Major Subject: Petroleum Engineering Copyright 2013 Albina Mukhametshina ABSTRACT Steam Assisted Gravity Drainage (SAGD) is a proven enhanced oil recovery technique for oil sand extraction. However, the environmental and economic challenges associated with excessive greenhouse gas emissions due to the combustion of significant amount of natural gas and consumption of large amount of fresh water for steam generation limit the application of this technology. To address these issues, various SAGD modifications have been developed, among those, SAGD with solvent co- injection is one of the most prospective techniques. In this experimental study, the effectiveness of base SAGD and Expanding Solvent SAGD (ES-SAGD) was tested on a Peace River bitumen. All experiments were conducted using a two-dimensional cylindrical physical model. In order to investigate the influence of in-situ asphaltene precipitation on the performance of ES-SAGD process, three different types of solvent were considered as hydrocarbon additives; asphaltene soluble (toluene), asphaltene insoluble (n-hexane), and solvent with intermediate solubility parameter (cyclohexane). Different strategies for solvent injection were examined. In all experiments, temperature profiles at 47 different positions, produces oil and water were monitored continuously. Viscosity and API gravity of original and produced oil samples were measured.