Mapping Outcomes of Liquid Marble Collisions†
Total Page:16
File Type:pdf, Size:1020Kb
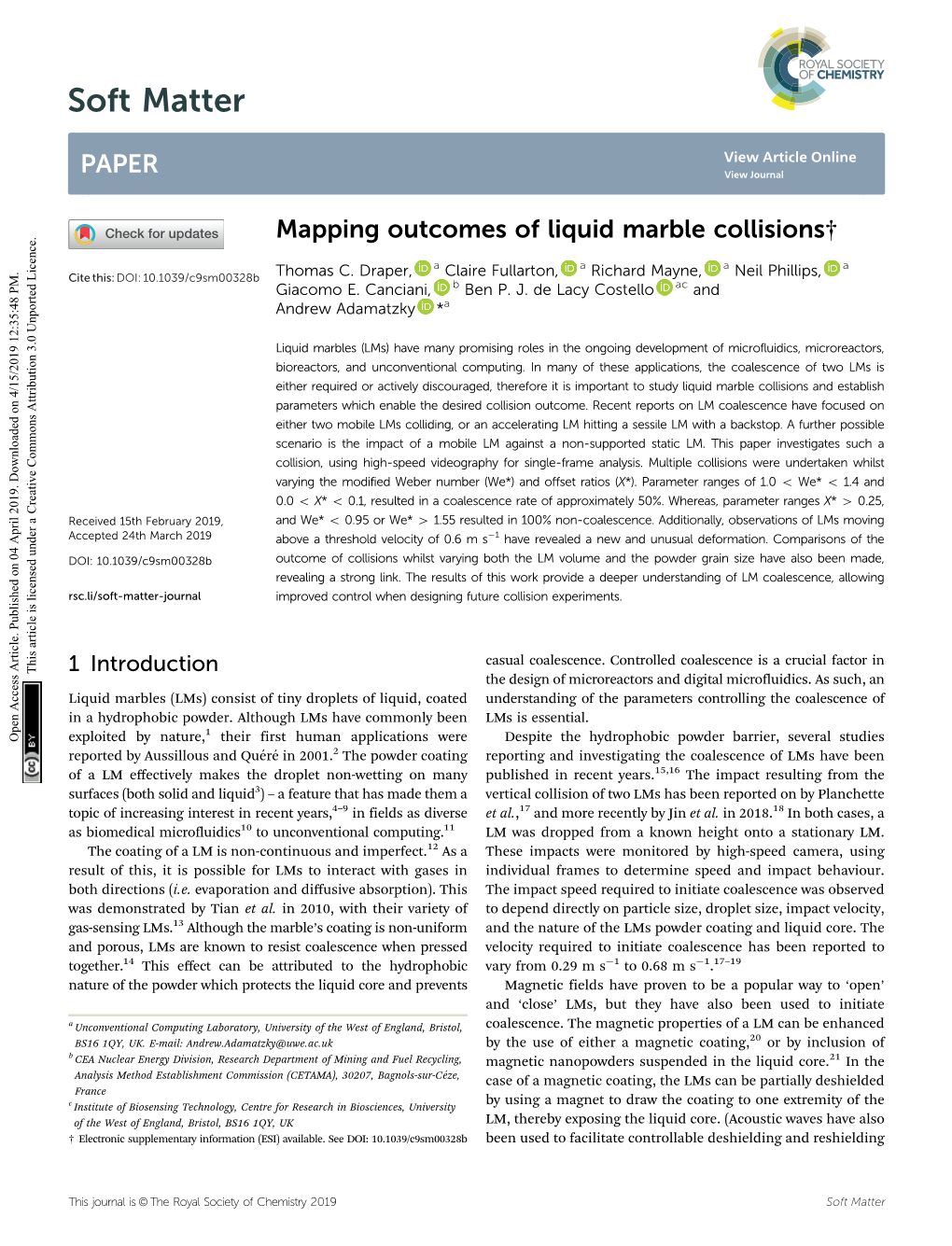
Load more
Recommended publications
-
Liquid Marbles As Bioreactors for the Study of Three-Dimensional Cell Interactions
Biomed Microdevices (2017) 19:31 DOI 10.1007/s10544-017-0171-6 Liquid marbles as bioreactors for the study of three-dimensional cell interactions Raja K. Vadivelu1 & Harshad Kamble2 & Ahmed Munaz2 & Nam-Trung Nguyen2 # Springer Science+Business Media New York 2017 Abstract Liquid marble as a bioreactor platform for cell- developing bioassays that could substantially contribute to based studies has received significant attention, especially therapeutic applications. Especially, insights for improving for developing 3D cell-based assays. This platform is partic- the survival and adherence of transplanted cells. ularly suitable for 3D in-vitro modeling of cell-cell interac- tions. For the first time, we demonstrated the interaction of Keywords Liquid marble . Bioreactor . Spinal cord injury . olfactory ensheathing cells (OECs) with nerve debris and Post-injury model . Post-transplantation model . Digital meningeal fibroblast using liquid marbles. As the transplanta- microfluidics . 3D cell interaction tion of OECs can be used for repairing nerve injury, degenerating cell debris within the transplantation site can adversely affect the survival of transplanted OECs. In this 1 Introduction paper, we used liquid marbles to mimic the hostile 3D envi- ronment to analyze the functional behavior of the cells and to Repairing injured tissues using cellular therapy is attractive. form the basis for cell-based therapy. We show that OECs Recently, this approach has been increasingly adopted in clin- interact with debris and enhanced cellular aggregation to form ical practice. Over the past two decades, cell-based therapy has a larger 3D spheroidal tissue. However, these spheroids indi- been improving significantly, especially in post-transplantation cated limitation in biological functions such as the inability of survival of cells in the host niche (Wan et al. -
Capillarity: Revisiting the Fundamentals of Liquid Marbles
Microfluidics and Nanofluidics (2020) 24:81 https://doi.org/10.1007/s10404-020-02385-9 REVIEW Capillarity: revisiting the fundamentals of liquid marbles Pradip Singha1 · Chin Hong Ooi1 · Nhat‑Khuong Nguyen1 · Kamalalayam Rajan Sreejith1 · Jing Jin1 · Nam‑Trung Nguyen1 Received: 11 June 2020 / Accepted: 1 September 2020 © Springer-Verlag GmbH Germany, part of Springer Nature 2020 Abstract Liquid marble, an emerging platform for digital microfuidics, has shown its potential in biomedical applications, cosmet- ics, and chemical industries. Recently, the manipulation and fundamental aspects of liquid marbles have been reported and attracted attention from the microfuidics community. Insights into their physical and chemical properties allow liquid marbles to be utilised in practical applications. This review summarises and revisits the efect of capillarity on the formation of liquid marbles and how it afects the efective surface tension as well as their robustness. The paper also systematically discusses the applied aspect of capillarity of the carrier liquid for transporting foating liquid marbles. Keywords Liquid marble · Surface tension · Capillarity · Digital microfuidics 1 Introduction et al. 2017; Samiei et al. 2016). Droplets can be manipulated with active approaches, such as electrowetting (Teng et al. Microfuidics is the science and technology dealing with the 2020), dielectrophoresis (Velev et al. 2003), thermocapil- manipulation of fuid in sub-millimeter/micrometer scale. lary efect (Chen et al. 2005), acoustic vibration (Chen et al. Microfuidics enables the implementation of liquid handling 2017; Zang et al. 2015), and magneto-wetting (Nguyen et al. process on a single device (Whitesides 2006). Microfuid- 2010a). However, evaporation, handling, contamination, ics has a broad range of applications from lab on a chip for and surface modifcation remain current challenges. -
Multifunctional Organically Modified Graphene with Super-Hydrophobicity
Nano Research 1 DOINano 10.1007/s12274-014-0408-0Res Multifunctional organically modified graphene with super-hydrophobicity 1 1 1 1 1 1 Huawen Hu , Chan C. K. Allan , Jianhua Li , Yeeyee Kong , Xiaowen Wang , John H. Xin (), and Hong Hu1 () Nano Res., Just Accepted Manuscript • DOI: 10.1007/s12274-014-0408-0 http://www.thenanoresearch.com on January 4 2014 © Tsinghua University Press 2014 Just Accepted This is a “Just Accepted” manuscript, which has been examined by the peer-review process and has been accepted for publication. A “Just Accepted” manuscript is published online shortly after its acceptance, which is prior to technical editing and formatting and author proofing. Tsinghua University Press (TUP) provides “Just Accepted” as an optional and free service which allows authors to make their results available to the research community as soon as possible after acceptance. After a manuscript has been technically edited and formatted, it will be removed from the “Just Accepted” Web site and published as an ASAP article. Please note that technical editing may introduce minor changes to the manuscript text and/or graphics which may affect the content, and all legal disclaimers that apply to the journal pertain. In no event shall TUP be held responsible for errors or consequences arising from the use of any information contained in these “Just Accepted” manuscripts. To cite this manuscript please use its Digital Object Identifier (DOI®), which is identical for all formats of publication. TABLE OF CONTENTS (TOC) Multifunctional organically modified graphene with super-hydrophobicity Huawen Hu, Chan C.K. Allan, Jianhua Li, Yeeyee Kong, Xiaowen Wang, John H. -
Liquid Marble Based Digital Microfluidics: Fundamental Physics and Applications
Liquid marble based digital microfluidics: fundamental physics and applications Nam-Trung Nguyen Queensland Micro and Nanotechnology Centre Griffith University, Nathan Campus Email: [email protected] Lab webpage: https://ntnlab.com 4BIO SUMMIT: EUROPE 2018 1 Queensland Micro- and Nanotechnology Centre (QMNC) www.griffith.edu.au/qmnc • ~ 30 Academic members • ~ 60 PhD students • A$3.0 Mil annual external funding • Class 100 and 1000 clean rooms Microtechnology Nanotechnology (Top-down) (Bottom-up) Micro/nanosystems (Multidisciplinary) 4BIO SUMMIT: EUROPE 2018 2 Micro/nanofluidics as tool for cellular and molecular scales Human E-coli Hand bacterium Red blood Hemoglobin Hair strand HIV cell 1Å 1nm 10nm 100nm 1mm 10mm 100mm 1mm 1cm 10cm 1m Nanofluidic tools Microfluidic tools Petri dish Well plate Liquid marble 4BIO SUMMIT: EUROPE 2018 Cell Stretcher Chip 3 Droplet versus liquid marble Droplet Liquid marble • Wetting behavior strongly depends • Non wetting on the surface property • Behavior independent from surface • Liquid-gas-solid system • Liquid-solid-gas system • We used 1 um PTFE powder 4BIO SUMMIT: EUROPE 2018 4 Applications of liquid marble based digital microfluidics 4BIO SUMMIT: EUROPE 2018 5 Liquid marble as bioreactor for cell spheroids (3D cell culture) R.K. Vadivelu, C.H. Ooi, R.Q. Yao, J.T. Velasquez, E. Pastrana, J. Diaz-Nido, F. Lim, J. Ekkberg, N.T. Nguyen, J. St John, Generation of three-dimensional multiple spheroid model of olfactory ensheathing cells using floating liquid marbles, Scientific Reports, 2015, Vol. 5, pp. 15083 4BIO SUMMIT: EUROPE 2018 6 Sessile versus floating liquid marble 4BIO SUMMIT: EUROPE 2018 7 Quality of cell spheroids grown in liquid marbles Spheroids of different sizes: (A) 60 μ m diameter spheroid, (B) 100 μm, (C) 150 μm. -
Self-Propelled Aero-Gan Based Liquid Marbles Exhibiting Pulsed Rotation on the Water Surface
materials Communication Self-Propelled Aero-GaN Based Liquid Marbles Exhibiting Pulsed Rotation on the Water Surface Tudor Braniste 1 , Vladimir Ciobanu 1 , Fabian Schütt 2, Hidenori Mimura 3, Simion Raevschi 4, Rainer Adelung 2, Nicola M. Pugno 5,6 and Ion Tiginyanu 1,7,* 1 National Center for Materials Study and Testing, Technical University of Moldova, Stefan cel Mare Av. 168, 2004 Chisinau, Moldova; [email protected] (T.B.); [email protected] (V.C.) 2 Institute for Materials Science, Kiel University, Kaiserstr. 2, 24143 Kiel, Germany; [email protected] (F.S.); [email protected] (R.A.) 3 Research Institute of Electronics, Shizuoka University, 3-5-1 Johoku, Naka-ku, Hamamatsu 432-8011, Japan; [email protected] 4 Department of Physics and Engineering, State University of Moldova, Alexei Mateevici Str. 60, 2009 Chisinau, Moldova; [email protected] 5 Laboratory for Bioinspired, Bionic, Nano, Meta Materials & Mechanics, Department of Civil, Environmental and Mechanical Engineering, University of Trento, 38123 Trento, Italy; [email protected] 6 School of Engineering and Materials Science, Queen Mary University of London, Mile End Road, London E1 4NS, UK 7 Academy of Sciences of Moldova, Stefan cel Mare Av. 1, 2001 Chisinau, Moldova * Correspondence: [email protected] Abstract: We report on self-propelled rotating liquid marbles fabricated using droplets of alcoholic solution encapsulated in hollow microtetrapods of GaN with hydrophilic free ends of their arms and Citation: Braniste, T.; Ciobanu, V.; hydrophobic lateral walls. Apart from stationary rotation, elongated-spheroid-like liquid marbles Schütt, F.; Mimura, H.; Raevschi, S.; were found, for the first time, to exhibit pulsed rotation on water surfaces characterized by a threshold Adelung, R.; Pugno, N.M.; speed of rotation, which increased with the weight of the liquid marble while the frequency of pulses Tiginyanu, I. -
Liquid Marble Actuator for Microfluidic Logic Systems
www.nature.com/scientificreports OPEN Liquid Marble Actuator for Microfuidic Logic Systems Thomas C. Draper 1, Claire Fullarton 1, Neil Phillips1, Ben P. J. de Lacy Costello2 & Andrew Adamatzky1 Received: 15 June 2018 A mechanical fip-fop actuator has been developed that allows for the facile re-routing and distribution Accepted: 10 September 2018 of liquid marbles (LMs) in digital microfuidic devices. Shaped loosely like a triangle, the actuating Published: xx xx xxxx switch pivots from one bistable position to another, being actuated by the very low mass and momentum of a LM rolling under gravity (~4 × 10−6 kg ms−1). The actuator was laser-cut from cast acrylic, held on a PTFE coated pivot, and used a PTFE washer. Due to the rocking motion of the switch, sequential LMs are distributed along diferent channels, allowing for sequential LMs to traverse parallel paths. This distributing efect can be easily cascaded, for example to evenly divide sequential LMs down four diferent paths. This lightweight, cheap and versatile actuator has been demonstrated in the design and construction of a LM-operated mechanical multiplication device — establishing its efectiveness. The actuator can be operated solely by gravity, giving it potential use in point-of-care devices in low resource areas. Liquid Marbles (LMs) are small droplets of liquid that have been coated in a nano- or micro-powder1. Also known (less theatrically) as particle-coated droplets, the liquid is typically aqueous and the powder coating has a degree of hydrophobicity — resulting in non-wetting of said powder. Due to the hydrophobic nature of this pow- der, the minimal energy profle of the water droplet results in a near-spherical coated droplet, that does not wet hydrophilic surfaces. -
Manipulation of Liquid Marbles
Microfluid Nanofluid (2015) 19:483–495 DOI 10.1007/s10404-015-1595-z REVIEW Manipulation of liquid marbles Chin Hong Ooi1 · Nam-Trung Nguyen1 Received: 19 October 2014 / Accepted: 11 May 2015 / Published online: 23 May 2015 © Springer-Verlag Berlin Heidelberg 2015 Abstract A liquid marble is a liquid droplet coated proposed for inhibiting the wetting of liquid droplets on a with hydrophobic powder which enables the marble to solid surface. These solutions can be broadly classified into be manipulated like a soft solid. Recently, liquid marbles two categories, namely superhydrophobic surfaces and liq- have been used in applications such as microbioreactors uid marbles. By studying one of the best examples of natu- for three-dimensional cell cultures and could be a new plat- rally hydrophobic surfaces—the lotus leaf, the relationship form for digital microfluidics. Despite its potential signifi- of surface microstructures and superhydrophobicity was cance, there is a lack of a systematic, thorough review and well understood (Barthlott and Neinhuis 1997). Numerous discussion on the manipulation schemes for liquid marbles. techniques are available for creating superhydrophobic sur- This paper presents past and recent manipulation schemes faces. Another approach to anti-wetting is engineering the for liquid marbles. This paper discusses the major work- liquid droplet instead of the surface, leading to the devel- ing principles, their advantages and drawbacks. Finally, opment of liquid marbles. The scope of this paper is the the paper concludes with recent applications and the chal- manipulation schemes of liquid marbles, and hydrophobic lenges of this research area. surfaces will not be discussed further. -
Electrically Deformable Liquid Marbles
Electrically Deformable Liquid Marbles Edward Bormashenko 1, Roman Pogreb 1, Tamir Stein 1, 2, Gene Whyman 1, Marcelo Schiffer 1 and Doron Aurbach 2 1Ariel University Center of Samaria, Applied Physics Department, P.O.B. 3, Ariel 40700, Israel 2Bar-Ilan University, Chemistry Department, Ramat-Gan 52900, Israel Short title: Electrically Deformable Liquid Marbles Corresponding author's address: Edward Bormashenko, Ariel University Center of Samaria, P.O.B. 3, Ariel 40700, Israel Phone: +972-3-906-6134 Fax: +972-3-906-6621 E-mail: [email protected] 1 Abstract Liquid marbles, which are droplets coated with a hydrophobic powder, were exposed to a uniform electric field. It was established that a threshold value of the electric field, 15 cgse, should be surmounted for deformation of liquid marbles. The shape of the marbles was described as a prolate spheroid. The semi-quantitative theory describing deformation of liquid marbles in a uniform electric field is presented. The scaling law relating the radius of the contact area of the marble to the applied electric field shows a satisfactory agreement with the experimental data. Keywords: liquid marbles, liquid marble deformation under electric field, liquid-substrate interaction, contact radius-electric field interrelation 2 Introduction Liquid marbles, defined as droplets enwrapped with micrometrically scaled hydrophobic particles, have inspired intensive experimental research in the past decade [1–25]. Various powders have been used for manufacturing liquid marbles, including poly(tetrafluoroethylene), polyvinylidene fluoride, polyethylene, lycopodium, aerogels, and others [1–24]. Marbles enwrapped by graphite were reported recently [25]. Liquid marbles are separated from solid or liquid support by "air pockets" in a way similar to Leidenfrost drops [26]. -
Liquid Marbles As Miniature Reactors for Chemical and Biological Applications
processes Review Liquid Marbles as Miniature Reactors for Chemical and Biological Applications Nhat-Khuong Nguyen , Chin Hong Ooi * , Pradip Singha , Jing Jin , Kamalalayam Rajan Sreejith, Hoang-Phuong Phan and Nam-Trung Nguyen Queensland Micro- and Nanotechnology Centre, Griffith University, 170 Kessels Road, Nathan 4111 QLD, Australia; khuong.nguyen@griffithuni.edu.au (N.-K.N.); pradip.singha@griffithuni.edu.au (P.S.); jing.jin3@griffithuni.edu.au (J.J.); sreejith.kamalalayamrajan@griffithuni.edu.au (K.R.S.); h.phan@griffith.edu.au (H.-P.P.); nam-trung.nguyen@griffith.edu.au (N.-T.N.) * Correspondence: c.ooi@griffith.edu.au Received: 3 June 2020; Accepted: 5 July 2020; Published: 7 July 2020 Abstract: The need for miniaturised reaction systems has led to the development of various microreactor platforms, such as droplet-based microreactors. However, these microreactors possess inherent drawbacks, such as rapid evaporation and difficult handling, that limit their use in practical applications. Liquid marbles are droplets covered with hydrophobic particles and are a potential platform that can overcome the weaknesses of bare droplets. The coating particles completely isolate the interior liquids from the surrounding environment, thus conveniently encapsulating the reactions. Great efforts have been made over the past decade to demonstrate the feasibility of liquid marble-based microreactors for chemical and biological applications. This review systemically summarises state-of-the-art implementations of liquid marbles as microreactors. This paper also discusses the various aspects of liquid marble-based microreactors, such as the formation, manipulation, and future perspectives. Keywords: liquid marble; particle-laden droplet; micromixer; microreactor; microbioreactor; digital microfluidics; liquid marble manipulation and applications; non-wetting phenomena 1. -
Revisiting the Surface Tension of Liquid Marbles
Self-Propulsion of Liquid Marbles: Leidenfrost-Like Levitation Driven by the Marangoni Flow Edward Bormashenko*a,b, Yelena Bormashenkob, Roman Grynyova, Hadas Aharonib, Gene Whymana and Bernard P. Binksc aAriel University, Physics Department, P.O.B. 3, 40700, Ariel, Israel bAriel University, Chemical Engineering and Biotechnology Department , P.O.B. 3, 40700, Ariel, Israel cSurfactant & Colloid Group, Department of Chemistry, University of Hull, Hull. HU67RX. UK *Corresponding author: Edward Bormashenko Ariel University, Physics Department, Chemical Engineering and Biotechnology Department P.O.B. 3, Ariel 40700, Israel Phone: +972-3-906-6134 Fax: +972-3-906-6621 E-mail: [email protected] Contains ESI 1 ABSTRACT Self-propulsion of liquid marbles filled with aqueous alcohol solutions and placed on a water surface is reported. The characteristic of velocity of the marbles is ca. 0.1 m/s. The phenomenon of self-propulsion is related to the Marangoni solutocapillary flow caused by the condensation of alcohol, evaporated from the liquid marble, on a water surface. The Marangoni flow in turn enhances the evaporation of alcohol from marbles. Addition of alcohol to the water supporting the marbles suppresses the self- propulsion. The propulsion of liquid marbles is mainly stopped by water drag. The velocity of the center of mass of marbles grows with the increase of the concentration of alcohol in a marble. The velocity of marbles’ self-propulsion is independent on their volume. INTRODUCTION Autonomous locomotion (self-propelling) of droplets driven by various physico-chemical mechanisms attracted widespread attention of researches in the last decade.1-9 Various mechanisms of self-propelling have been introduced including the use of gradient surfaces1-3, involving the Leidenfrost effect5-7, exploiting micro- structured surfaces5-7. -
Deformation of a Floating Liquid Marble
Volume 11 Number 23 21 June 2015 Pages 4553–4732 Soft Matter www.softmatter.org ISSN 1744-683X PAPER Nam-Trung Nguyen et al. Deformation of a fl oating liquid marble Soft Matter PAPER Deformation of a floating liquid marble a b b a Cite this: Soft Matter, 2015, Chin Hong Ooi, Raja K. Vadivelu, James St John, Dzung Viet Dao and a 11,4576 Nam-Trung Nguyen* A rigid spherical particle floating on a liquid is a known problem with well-defined solutions. Under the combined effect of gravity and surface tension, the rigid particle deforms the liquid surface. However, in the case of a floating soft particle such as a liquid marble, not only the liquid surface but also the Received 27th December 2014, particle itself deforms. In this paper, we investigate the deformation of a floating liquid marble and Accepted 10th April 2015 characterise its height as well as aspect ratio. The experimental results show that theoretical models for DOI: 10.1039/c4sm02882a a rigid spherical particle suit well for small liquid marbles. Larger marbles require an oblate liquid spheroid model. We will discuss the limitations of the two models and characterise the deformation of www.rsc.org/softmatter these marbles. 1. Introduction Due to the hydrophobic nature of the liquid marble coating, a large contact angle is formed similar to the Cassie–Baxter6 or Archimedes’ principle applies to a floating object stating that Extrand7 rough surface configuration. Dupin et al.8 and Fujii the buoyancy force is equal to the weight of the liquid volume et al.9 used latex-based coatings to float a liquid marble which displaced by the submerged volume of the object. -
Liquid Marbles Based on Magnetic Upconversion Nanoparticles As
Angewandte Communications Chemie International Edition: DOI: 10.1002/anie.201604781 Photodynamic Therapy Hot Paper German Edition: DOI: 10.1002/ange.201604781 Liquid Marbles Based on Magnetic Upconversion Nanoparticles as Magnetically and Optically Responsive Miniature Reactors for Photocatalysis and Photodynamic Therapy Dan Wang, Lin Zhu, Jian-Feng Chen,* and Liming Dai* Abstract: Magnetic liquid marbles have recently attracted particles show great potential for actuation and manipulation extensive attention for various potential applications. However, by magnetic forces.[3b,6a,9] conventional liquid marbles based on iron oxide nanoparticles Photon-induced reactions have recently emerged as are opaque and inadequate for photo-related applications. important processes in chemical and biomedical studies,[10] Herein, we report the first development of liquid marbles and some light-responsive liquid marbles have been repor- coated with magnetic lanthanide-doped upconversion nano- ted.[6c,11] However, owing to the light absorption and/or [6c] particles (UCNPs) that can convert near-infrared light into scattering by the powder (e.g., graphene, WO3 nanoparti- [11a] [11b] [11c] visible light. Apart from their excellent magnetic and mechan- cles, TiO2 nanoparticles, carbon black) attached to ical properties, which are attractive for repeatable tip opening the droplet surface, visible light can hardly pass through the and magnetically directed movements, the resultant UCNP- surface to reach the droplet inside the liquid marble. On the based liquid