ON Semiconductor Is
Total Page:16
File Type:pdf, Size:1020Kb
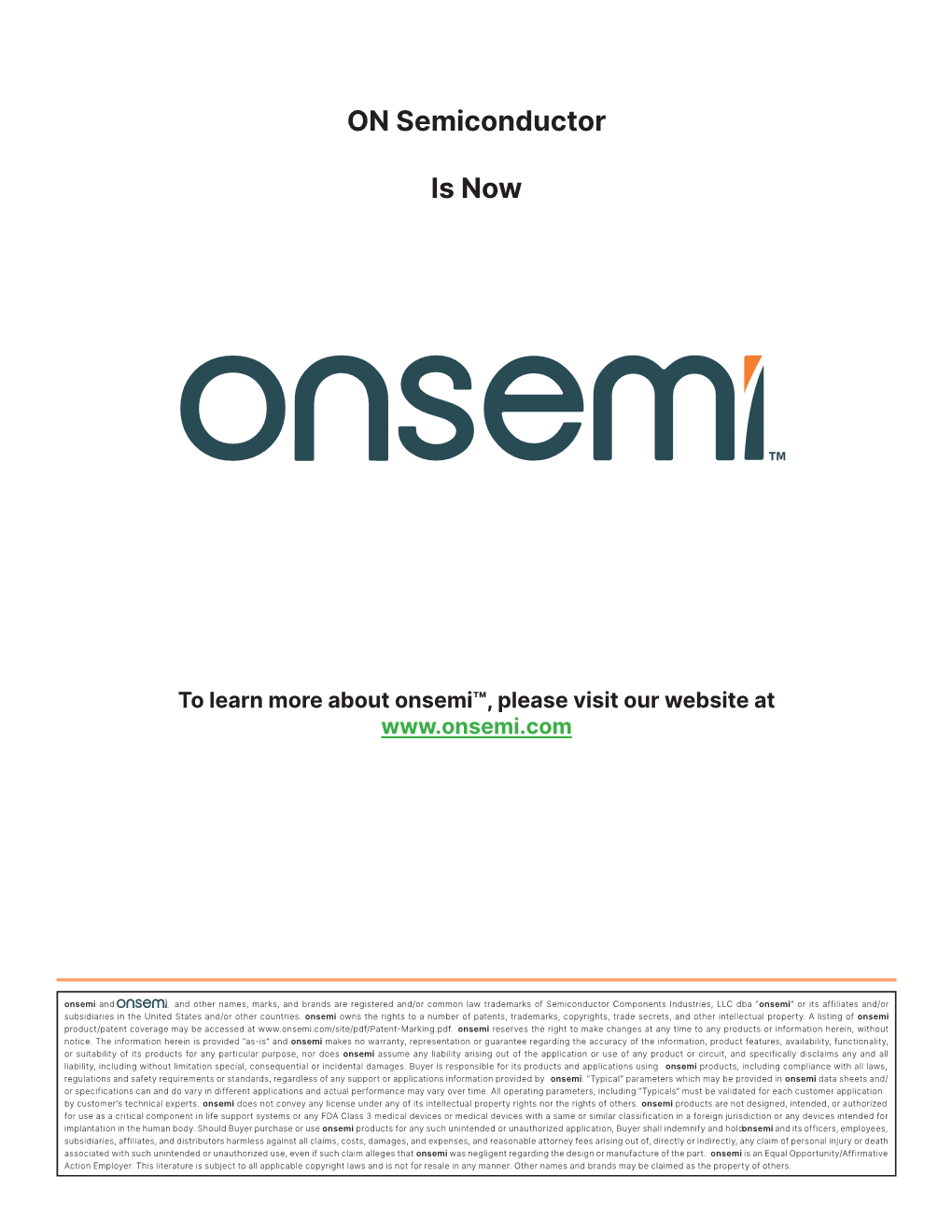
Load more
Recommended publications
-
Application Note AN-50 Linkswitch-PL Family
Application Note AN-50 LinkSwitch-PL™ Family Design Guide (Flyback Topology) Introduction The LinkSwitch-PL family of highly integrated monolithic off-line may be used in both the flyback or buck-boost topologies switcher ICs enables implementation of single-stage isolated or however only the flyback is covered in this document. Support, non-isolated, power factor corrected, constant current output with a separate PIXls spreadsheet, for the buck-boost topology is drivers for LED lighting applications. Non-isolated designs are planned and will be covered in a separate application note. compatible with low cost TRIAC based dimmers and provide In addition to this application note, the reader may also find the >300:1 dimming range. The low component count simplifies Reference Design Kits (RDKs) useful. Each contains a fully meeting space constraints of LED retrofit designs (e.g. A19 and functional engineering prototype board, engineering report and candelabra lamp sizes) while the >0.9 PF, low THD and harmonic device samples. Further details on downloading PI Expert, input currents allows a single driver design to be used worldwide. obtaining an RDK, reviewing additional Design Example Reports (DERs) and updates to this document can be found at www. Scope powerint.com. This application note is intended for engineers designing an Basic Circuit Configuration isolated or non-isolated AC to DC power supply driving a A typical application schematic is shown below for a TRIAC constant current LED load. It provides step-by-step guidance on dimmable, non-isolated LED driver. Circuit blocks required for the use of the PIXls design spreadsheet, part of the PI Expert™ interface with TRIAC based phase angle control dimmers are software suite, selection of key components and optimization of labeled Passive, Active Damper, and Bleeder and can be designs especially for TRIAC based dimmers. -
Designing LED Drivers for the Challenges of Phase Cut Dimmers
ON Semiconductor Is Now To learn more about onsemi™, please visit our website at www.onsemi.com onsemi and and other names, marks, and brands are registered and/or common law trademarks of Semiconductor Components Industries, LLC dba “onsemi” or its affiliates and/or subsidiaries in the United States and/or other countries. onsemi owns the rights to a number of patents, trademarks, copyrights, trade secrets, and other intellectual property. A listing of onsemi product/patent coverage may be accessed at www.onsemi.com/site/pdf/Patent-Marking.pdf. onsemi reserves the right to make changes at any time to any products or information herein, without notice. The information herein is provided “as-is” and onsemi makes no warranty, representation or guarantee regarding the accuracy of the information, product features, availability, functionality, or suitability of its products for any particular purpose, nor does onsemi assume any liability arising out of the application or use of any product or circuit, and specifically disclaims any and all liability, including without limitation special, consequential or incidental damages. Buyer is responsible for its products and applications using onsemi products, including compliance with all laws, regulations and safety requirements or standards, regardless of any support or applications information provided by onsemi. “Typical” parameters which may be provided in onsemi data sheets and/ or specifications can and do vary in different applications and actual performance may vary over time. All operating parameters, including “Typicals” must be validated for each customer application by customer’s technical experts. onsemi does not convey any license under any of its intellectual property rights nor the rights of others. -
The Principles of Dimming Leading Edge Dimming – Triac and Thyristor
The Principles Of Dimming An artificial light source such as a lamp or one or more lamps in a fitting (luminaire) will be specified for a purpose. Often this purpose will need a lot of light but may be too much at other times. This is nothing new, candle lamps used mechanical screens and oil lamps adjustable wicks. Aesthetic, artistic, mood setting, visual comfort, or energy saving are all valid reasons for changing lighting levels, or in other words dimming the lamps. Dimming an electric lamp is achieved by reducing the current and thereby the power to the lamp. Early dimmers used series resistance but this generates a lot of heat and is inefficient. All modern dimmers use semiconductor technology and digital control with typical losses of less than 2% of full load. Mains “chopping” or Phase Control The most widely used form of dimming is phase control. Phase control dimming uses a switching device to “chop” the supply such that only part of each half cycle Normal line voltage, full power for the load of the AC mains supply is applied to the load. For the remaining part the switch is open and no power is applied to the load. The amount of power to the load is therefore determined by the phase angle of the AC supply at which the switching occurs and thereby altering the ratio of off to on time from always open, no power, to allows closed, full power. The switching is synchronised to each half cycle to minimise the visual impact of momentarily turning the lamp off. -
Stage Lighting Technician Handbook
The Stage Lighting Technician’s Handbook A compilation of general knowledge and tricks of the lighting trade Compiled by Freelancers in the entertainment lighting industry The Stage Lighting Technician's Handbook Stage Terminology: Learning Objectives/Outcomes. Understanding directions given in context as to where a job or piece of equipment is to be located. Applying these terms in conjunction with other disciplines to perform the work as directed. Lighting Terms: Learning Objectives/Outcome Learning the descriptive terms used in the use and handling of different types of lighting equipment. Applying these terms, as to the location and types of equipment a stagehand is expected to handle. Electrical Safety: Learning Objectives/Outcomes. Learning about the hazards, when one works with electricity. Applying basic safety ideas, to mitigate ones exposure to them in the field. Electricity: Learning Objectives/Outcomes. Learning the basic concepts of what electricity is and its components. To facilitate ones ability to perform the mathematics to compute loads, wattages and the like in order to safely assemble, determine electrical needs and solve problems. Lighting Equipment Learning Objectives/Outcomes. Recognize the different types of lighting equipment, use’s and proper handling. Gain basic trouble shooting skills to successfully complete a task. Build a basic understanding of applying these skills in the different venues that we work in to competently complete assigned tasks. On-sight Lighting Techniques Learning Objectives/Outcomes. Combing the technical knowledge previously gained to execute lighting request while on site, whether in a ballroom or theatre. Approaches, to lighting a presentation to aspects of theatrical lighting to meet a client’s expectations. -
LIGHTING CONTROL HISTORY Their Immediate Technological Predecessors
not exist if preset boards had not been LIGHTING CONTROL HISTORY their immediate technological predecessors. AND The first type of control for electrical MODERN PROGRAMMING lighting was simply a bank of switches STRATAGIES that turned the lights on and off. Not surprisingly, artists in the theatre were not entirely satisfied with the “lights up, lights Modern lighting control methods are down,” nature of switches in controlling governed by complex computer systems lighting for sensitive scenes. Not long that make it possible to operate hundreds after the use of electric lighting became of lights at one time. They also make it widespread, resistance dimmers were possible to use the many digital lights and developed so that it was possible to fade in accessories developed over the past two and out of scenes. Fading indicates that decades. Although each manufacturer has the lighting change occurs over a period of its own particular method of handling time, which is an important element in technical issues, the core technology that lighting design. The term blackout is used makes all of them work is basically the to describe what happens when all of the same. This chapter is not intended to be stage lights go out instantly. (or as fast as an exhaustive review of every OEM system the cooling filaments will allow) on the market, but rather as an overview Although blackouts are frequently used to of the basic philosophy that is used in indicate a sudden end to the action on designing digital products for the control stage, they are not appropriate for most of stage lighting. -
Compatible Dimmers for Cree® LED Bulbs Cree® LED Bulbs Are Designed to Be Dimmed with Standard Incandescent Type Dimmers
Compatible Dimmers for Cree® LED bulbs Cree® LED bulbs are designed to be dimmed with standard incandescent type dimmers. They are also compatible with most Magnetic Low Voltage (MLV) and Electronic Low Voltage (ELV) dimmers. This list was generated from lab testing of samples and your results could vary.* bulbs per dimmer Phase Cut Company Name Series Part Number Load Type Edge Dial Control Rating (W) min max Cree LED bulbs are Cooper Architectural RAI10 Incandescent Leading Rotary 1000 2 19 different. Cree LED Cooper Aspire® 9530WS Incandescent/MLV Leading Slide 600 1 8 bulbs look and light like Cooper Aspire® 9532WS Incandescent/MLV Leading Slide 1000 1 19 an incandescent and Cooper Aspire® 9534WS Incandescent/MLV Leading Slide 600 1 8 Cooper Aspire® 9540WS Incandescent/MLV Leading Slide 1000 1 19 are priced affordably. Cooper Devine® DI06P-W Incandescent/MLV Leading Slide 600 1 8 Cooper Devine® DI10P Incandescent/MLV Leading Slide 1000 1 19 Cooper React® RI101 Incandescent Leading Rotary 1000 1 19 Cooper Skye® SI061-W Incandescent Leading Slide 600 1 8 Cooper Skye® SI06P Incandescent/MLV Leading Slide 600 1 8 www.creebulb.com Cooper Skye® SI10P Incandescent/MLV Leading Slide 1000 1 19 Cooper Skye® SLC03P LED/CFL/INC Leading Slide 600 1 8 Cooper Trace® TI061-W Incandescent Leading Toggle 600 1 8 Leviton Acenti® ACE06 ELV Trailing Button 600 1 15 Leviton Acenti® ATI06-1L Incandescent Leading Button 600 1 8 Leviton Decora® 6631-L Incandescent Leading Slide 600 2 8 Leviton Illumatech® IPE04 ELV Trailing Slide 300 1 7 Leviton Illumatech® -
LM3445 TRIAC Dimmable Offline LED Driver Datasheet
Product Sample & Technical Tools & Support & Reference Folder Buy Documents Software Community Design LM3445 SNVS570M –JANUARY 2009–REVISED NOVEMBER 2015 LM3445 TRIAC Dimmable Offline LED Driver 1 Features 3 Description The LM3445 is an adaptive constant off-time AC/DC 1• TRIAC Dim Decoder Circuit for LED Dimming buck (step-down) constant current controller designed • Application Voltage Range 80 VAC to 277 VAC to be compatible with TRIAC dimmers. The LM3445 • Capable of Controlling LED Currents Greater provides a constant current for illuminating high Than 1 A power LEDs and includes a TRIAC dim decoder. The • Adjustable Switching Frequency dim decoder allows wide range LED dimming using standard TRIAC dimmers. The high frequency • Low Quiescent Current capable architecture allows the use of small external • Adaptive Programmable Off-Time Allows for passive components. The LM3445 includes a bleeder Constant Ripple Current circuit to ensure proper TRIAC operation by allowing • Thermal Shutdown current flow while the line voltage is low to enable proper firing of the TRIAC. A passive PFC circuit • No 120-Hz Flicker ensures good power factor by drawing current directly • Low Profile 10-Pin VSSOP Package or 14-Pin from the line for most of the cycle, and provides a SOIC constant positive voltage to the buck regulator. • Patented Drive Architecture Additional features include thermal shutdown, current limit and VCC under-voltage lockout. 2 Applications Device Information(1) • Retro Fit TRIAC Dimming PART NUMBER PACKAGE BODY SIZE (NOM) • Solid State Lighting VSSOP (10) 3.00 mm × 3.00 mm LM3445 • Industrial and Commercial Lighting SOIC (14) 3.91 mm × 8.65 mm • Residential Lighting (1) For all available packages, see the orderable addendum at the end of the data sheet. -
AN2839: Implementing a Lamp Dimmer with an HC908Q Family
Freescale Semiconductor AN2839 Application Note Rev. 0, 9/2004 Implementing a Lamp Dimmer with an HC908Q Family MCU by: Jefferson Daniel de Barros Soldera Andre Luis Vilas Boas Alfredo Olmos Marcus Espindola Brazil Semiconductor Technology Center — BSTC/SPS Introduction Many homes have lamps that can be made brighter or dimmer by a control on the on/off switch. This application note describes how to implement a low-cost lamp brightness control or dimmer using a member of the M68HC08 MCU Family. The circuit controls the amount of energy that reaches the bulb during each half-cycle of the AC power line. Moreover, a microcontroller may grant extra automation features to the circuit, such as soft start and programmable timing. Additionally, an application in which a lamp is turned on for a specific amount of time is described. The dimmer circuit implementation requires few external components. Freescale™ and the Freescale logo are trademarks of Freescale Semiconductor, Inc. This product incorporates SuperFlash® technology licensed from SST. © Freescale Semiconductor, Inc., 2004. All rights reserved. Dimmer Features Dimmer Features • 110 V or 220 V, 60 Hz or 50 Hz supply voltage • Up to 100 W lamp dimming • Full wave AC phase control • No transformer for AC power isolation • Up/down touch control option • Customized programmable timer • Low-cost 8-pin MCU implementation Control Method Many homes have lamps that can be made brighter or dimmer by rotating or sliding a control on the on/off switch. Years ago, this was done using a device called a rheostat which consists of a large variable resistor. -
Dimming Leds with Phase-Cut Dimmers: the Specifier's Process
Dimming LEDs with Phase-Cut Dimmers: The Specifier’s Process for Maximizing Success October 2013 (Updated to include information on Burden Museum demonstration, August 2014) Prepared for: Solid-State Lighting Program Building Technologies Office Office of Energy Efficiency and Renewable Energy U.S. Department of Energy Prepared by: Pacific Northwest National Laboratory PNNL-22945 Dimming LEDs with Phase-Cut Dimmers: The Specifier’s Process for Maximizing Success NJ Miller ME Poplawski October 2013 Final report prepared in support of the DOE Solid-State Lighting Technology Demonstration GATEWAY Program Study Participants: Pacific Northwest National Laboratory U.S. Department of Energy Prepared for the U.S. Department of Energy under Contract DE-ACO5-76RL01830 Pacific Northwest National Laboratory Richland, Washington 99352 Preface This document is a report of observations and results obtained from a lighting demonstration project conducted under the U.S. Department of Energy (DOE) GATEWAY Demonstration Program. The program supports demonstrations of high-performance solid-state lighting (SSL) products in order to develop empirical data and experience with in-the-field applications of this advanced lighting technology. The DOE GATEWAY Demonstration Program focuses on providing a source of independent, third-party data for use in decision-making by lighting users and professionals; this data should be considered in combination with other information relevant to the particular site and application under examination. Each GATEWAY Demonstration compares SSL products against the incumbent technologies used in that location. Depending on available information and circumstances, the SSL product may also be compared to alternate lighting technologies. Though products demonstrated in the GATEWAY program may have been prescreened for performance, DOE does not endorse any commercial product or in any way guarantee that users will achieve the same results through use of these products. -
Application Note AN-1153
Application Note AN-1153 Low Cost Triac Dimmable CFL Ballast Using IRS2530D DIM8 TM By Andre Tjokrorahardjo Table of Contents Page Introduction ...................................................................................................2 Circuit Schematic .........................................................................................5 Electrical and Fault Protection Characteristics .............................................6 Functional Description .................................................................................7 Fault Conditions .......................................................................................... 14 Ballast Design ............................................................................................. 17 Bill of Materials ............................................................................................ 19 PCB Information and Layout ....................................................................... 21 Conclusion .................................................................................................. 23 www.irf.com AN-1153 1/23 INTRODUCTION It has often been a disadvantage with electronic ballasts that they have been unable to be dimmed with a standard (phase cut) type of dimmer, particularly in the case of small integral ballast-lamp combinations commonly used in the home to save energy. This is due to the fact that, where there is no power factor correction, the ballast circuit input consists of a rectification stage followed by a large storage capacitor -
Dimmer Buying Guide Table of Contents Dimmer/Bulb Compatibility 2 Wiring Options 3 Dimmer Styles 4-6 Basic Lighting Terms 7
Dimmer Buying Guide Table of Contents Dimmer/Bulb Compatibility 2 Wiring Options 3 Dimmer Styles 4-6 Basic Lighting Terms 7 Dimmers offer an ideal way to create ambiance in a room or adjust lighting for a specific task or activity. Leviton offers a wide range of dimmers to suit every bulb preference and lifestyle. Our selection of LED compatible dimmers helps ensure smooth, flicker-free dimming when used with the latest LED bulbs; and our line of Smart dimmers is the perfect way to control lighting by app or voice from within your home or while away. Dimmers easily replace standard switches and can be used in any room of the home such as family rooms, dining rooms, kitchens and bedrooms. There are several factors to consider when choosing a dimmer. This guide will provide insight into the options available so you can decide which is the right solution to enhance your living environment. Dimmer/Bulb Compatibility Choosing the right dimmer and bulb combination can be a confusing task, especially because there are so many different types of dimmers and bulbs on the market. Today, LED bulbs are the most common. Our LED Compatibility Selector Tool (leviton.com/led) makes it easy to find the best dimmer and LED bulb combinations to avoid potential issues such as lights flickering, limited dimming range, slow start-up, or inconsistent illumination. The chart below provides some helpful hints pertaining to the most common types of dimmers you may see on the market. It will give you a better understanding of the types of bulbs to use with them for the best dimming experience based on your application. -
Recommended Dimmer Switches for Ecosmart A19 60W All Glass Bulb
Recommended Dimmer Switches for Ecosmart A19 60W All Glass Bulb No flicering or shimmer observed and smooth dimming across range. Bulbs Per Dimmer Manufacturer Series Part Number Load Type Rating(W) min max LUTRON Maestro MACL-153MH-WH LED/CFL/INC 600W 1 8 LUTRON Maestro MS-OPS5MH-WH LED/CFL/INC 600W 1 8 LUTRON Maestro MS-OPS2H-WH LED/CFL/INC 600W 1 8 LUTRON Maestro MSCL-OP153MH-WH LED/CFL/INC 600W 1 8 LUTRON Maestro MACL-153MR-WH LED/CFL/INC 600W 1 8 LUTRON Maestro MACL-153MH-LA LED/CFL/INC 600W 1 8 LUTRON Maestro MRF2-6CL-WH LED/CFL/INC 600W 1 8 LUTRON Skylark CTCL-153PDH-IV LED/CFL/INC 600W 1 8 LUTRON Skylark CTCL-153PR-WH LED/CFL/INC 600W 1 8 LUTRON Skylark S-600PH-WH LED/CFL/INC 600W 1 8 LUTRON Skylark SCL-153PR-WH LED/CFL/INC 600W 1 8 LUTRON Skylark S2-LH-WH LED/CFL/INC 300W 1 8 LUTRON Credenza TT-300H-WH Incandescent 300W 1 8 LUTRON Diva DVW-603PGH-WH Incandescent 600W 1 8 LUTRON Diva DV-600PR-WH Incandescent 600W 1 8 LUTRON Diva DVWCL-153PH-WH Incandescent 600W 1 8 LUTRON Diva DVCL-153PR-WH Incandescent 600W 1 8 LUTRON Toggler TG-600PR-WH Incandescent 600W 1 8 LUTRON Toggler TGCL-153PH-WH LED/CFL/INC 600W 1 8 LUTRON Caseta PD-6WCL-WH-R LED/CFL/INC 600W 1 8 LEVITON SureSlide R70-06631-1LW LED/CFL/INC 600W 1 8 LEVITON SureSlide R62-06674-P0W LED/CFL/INC 600W 1 8 LEVITON SureSlide R12-06672-1LW LED/CFL/INC 600W 1 8 LEVITON SureSlide 6613-P LED/CFL/INC 600W 1 8 LEGRAND Pass & Seymour H703PTUTCCCV6 LED/CFL 450W 1 8 LEGRAND Pass & Seymour HCL453PTCCCV6 LED/CFL 450W 1 8 May produce some flicker or shimmer.