The New Cullinan AG Milling Circuit – a Narrative of Progress by L
Total Page:16
File Type:pdf, Size:1020Kb
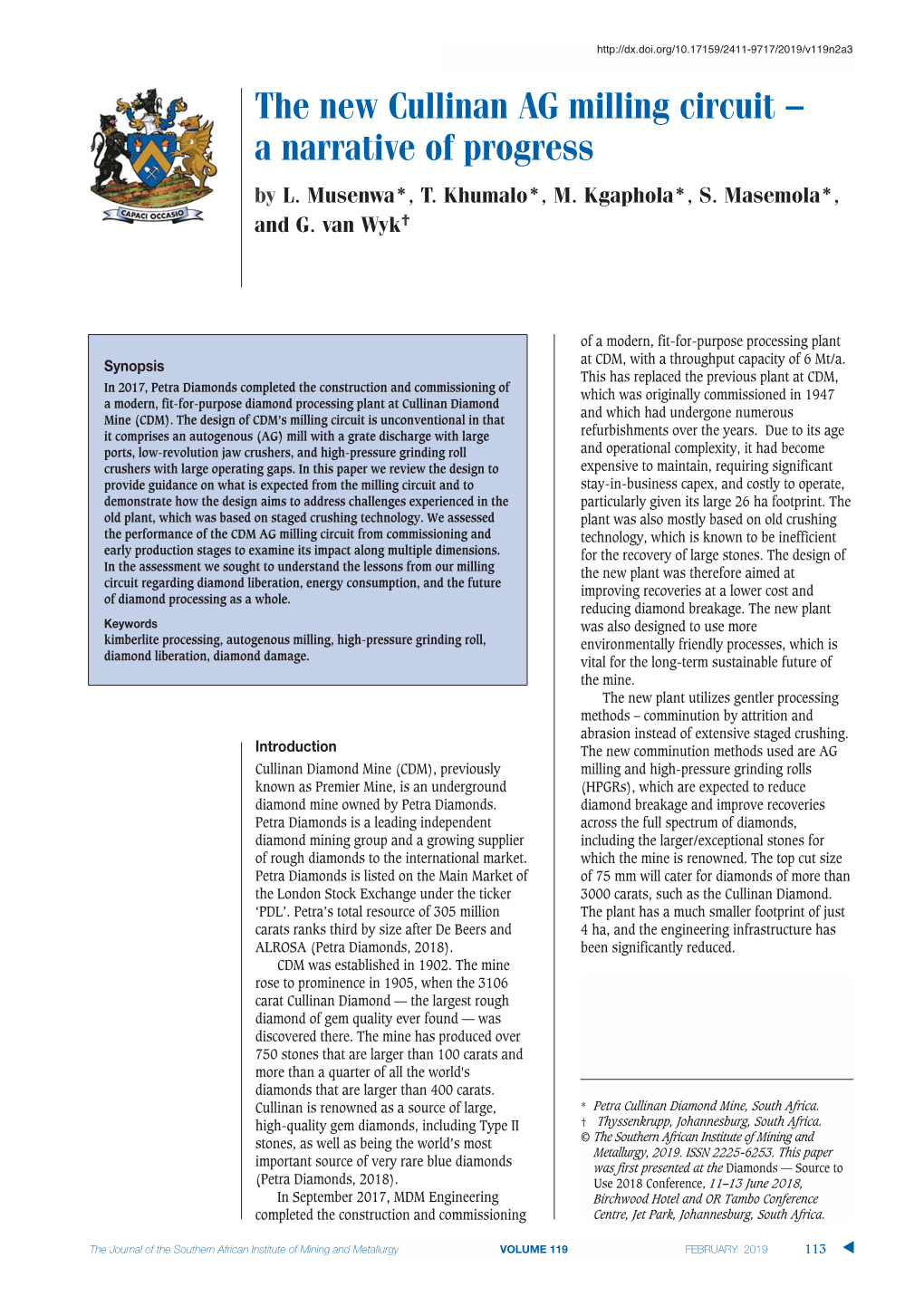
Load more
Recommended publications
-
ANNUAL REPORT and ACCOUNTS 2018 Gem Diamonds Is a Leading Producer of High-Value Diamonds
ANNUAL REPORT AND ACCOUNTS 2018 Gem Diamonds is a leading producer of high-value diamonds The Group, which has its head office in the United Kingdom, owns the Letšeng mine in Lesotho and the Ghaghoo mine in Botswana. The Letšeng mine is renowned for its regular On the cover, the 910 carat Lesotho production of large, exceptional white diamonds, making it the Legend recovered in January 2018, highest average dollar per carat kimberlite diamond mine in largest gem quality diamond ever recovered at Letšeng. the world. Since Gem Diamonds acquired the mine in 2006, Letšeng has produced some of the world’s most remarkable Welcome to the Gem diamonds. Among these diamonds recovered are the 910 carat Diamonds Annual Report Lesotho Legend, the 603 carat Lesotho Promise, the 550 carat and Accounts 2018 Letšeng Star and the 493 carat Letšeng Legacy. The Annual Report and Accounts have been prepared in accordance Gem Diamonds’ strategy is underpinned by three key priorities with: to deliver maximum value for all shareholders through its – applicable English and British Virgin Islands law; business cycle. Its current focus is on enhancing the efficiency – regulations and best practice as of the Group’s operations by improving day-to-day advised by the Financial performance, driving stringent cost control and capital Reporting Council and the discipline; and selling non-core assets. The selling of diamonds Department of Business, is supported by the Group’s sales, marketing and manufacturing Innovation and Skills in the United Kingdom; and capabilities. Financial, technical and administrative services are – International Financial supported by its South African subsidiary. -
Investor Presentation June 2017 Disclaimer
Investor Presentation June 2017 Disclaimer The following presentations are confidential and are being made only to, and are only directed at, persons to whom such Presentations may lawfully be communicated (“relevant persons”). Any person who is not a relevant person should not act or rely on these presentations or any of their contents. Information in the following presentation relating to the price at which relevant investments have been bought or sold in the past or the yield on such investments cannot be relied upon as a guide to the future performance of such investments. This presentation does not constitute an offering of securities or otherwise constitute an invitation or inducement to any person to underwrite, subscribe for or otherwise acquire securities in any company within the Group. Neither this documentation nor the fact of its distribution nor the making of the presentation constitutes a recommendation regarding any securities. This presentation if for information purposes only. The presentation contains forward-looking statements which are subject to risk and uncertainties because they relate to future events. These forward-looking statements include, without limitation, statements in relation to the Group’s projected growth opportunities. Some of the factors which may cause actual results to differ from these forward-looking statements are discussed in certain slides of the presentation and others can be found by referring to the information contained under the heading “Principal risks and uncertainties” in “The Strategic Report” in our Annual Report for the year ended 2015. The Annual Report can be found on our website (www.gemdiamonds.com). No statement in this presentation is intended as a profit forecast or profit estimate and no statement in the presentation should be interpreted to mean that earnings per share for the current or future financial years would necessarily match or exceed the historical published earnings. -
View Annual Report
127694 GemDiamonds COVER_127694 GemDiamonds COVER 30/04/2010 07:47 Page 1 GEM DIAMONDS ANNUAL REPORT 2009 ANNUAL REPORT 2009 www.gemdiamonds.com 127694 GemDiamonds COVER_127694 GemDiamonds COVER 30/04/2010 07:48 Page 2 GEM DIAMONDS ANNUAL REPORT 2009 Highlights 1 Board of Directors 2 Chairman’s Review 4 Chief Executive Officer’s Review 6 Chief Financial Officer’s Review 10 Annual Resource Statement 16 Sustainable Development Report 19 Directors’ Report 38 Remuneration Report 41 Corporate Governance Report 50 Annual Financial Statements 57 Advisors and Contacts ibc Contact Details GEM DIAMONDS LIMITED Registered Office Head Office Harbour House, 2nd Floor 2 Eaton Gate Waterfront Drive London SW1W 9BJ Road Town United Kingdom Tortola T: +44 203 043 0280 British Virgin Islands F: +44 203 043 0281 Advisors Financial Advisors and Sponsor Auditors and Reporting Accountants JPMorgan Cazenove Limited Ernst & Young LLP 20 Moorgate 1 More London Place London EC2R 6DA London SE1 2AF United Kingdom United Kingdom T: +44 20 7588 2828 T: +44 20 7951 2000 F: +44 20 7155 9000 F: +44 20 7951 1345 Legal Advisor Financial PR Advisor Linklaters Pelham Bell Pottinger Public Relations One Silk Street 12 Arthur Street London EC2Y 8HQ London, EC4R 9AB United Kingdom T: +44 20 7337 1500 T: +44 20 7456 2000 F: +44 20 7337 1550 F: +44 20 7456 2222 Front cover image: +10ct emerald cut D IF diamond, cut from Letšeng rough. Inside front cover image: Ellendale fancy yellow diamonds. 127694 GemDiamonds Pt1 3 column_127694 Gem Diamonds Pt1 30/04/2010 08:09 Page 1 GEM DIAMONDS ANNUAL REPORT 2009 Gem Diamonds is a global diamond mining company that has pursued a long term growth strategy through targeted acquisitions and the development of its existing assets. -
Annual Report and Accounts 2020 Contents
ANNUAL REPORT AND ACCOUNTS 2020 CONTENTS STRATEGIC REPORT 02 WELCOME TO THE GEM DIAMONDS About Gem Diamonds 03 ANNUAL REPORT AND ACCOUNTS 2020 2020 in review 04 The Annual Report and Accounts (this report) have been prepared in accordance with: Our business model 06 • applicable English and British Virgin Islands law; Chairperson’s statement 10 • regulations and best practice as advised by the Financial Market review 13 Reporting Council (FRC) and the Department of Business, Stakeholder engagement 15 Innovation and Skills in the United Kingdom (UK); • guidance from the International Integrated Our strategy 21 Reporting Council (IIRC) Integrated Reporting Principal risks and uncertainties 25 <IR> Framework which is publicly available at Viability statement 31 www.integratedreporting.org ; • information related to payments made to governments was compiled as required under the UK’s Report on PERFORMANCE REVIEW 32 Payments to Governments Regulations 2014 (as amended Chief executive’s review 33 December 2015) as applicable to companies involved in extractive activities. It is also intended to satisfy the Chief financial officer’s review 36 requirements of the Disclosure and Transparency Rules; Operational review 43 of the Financial Conduct Authority in the UK; Sustainability 48 • International Financial Reporting Standards (IFRS); and • the UK Corporate Governance Code 2018 which is GOVERNANCE 51 publicly available at www.frc.org.uk . The report covers Gem Diamonds Limited and its subsidiaries Chairperson’s introduction to corporate governance -
THE GLOBAL DIAMOND INDUSTRY Lifting the Veil of Mystery This Work Was Commissioned by AWDC and Prepared by Bain
THE GLOBAL DIAMOND INDUSTRY Lifting the Veil of Mystery This work was commissioned by AWDC and prepared by Bain. This work is based on secondary market research, analysis of financial informa- tion available or provided to Bain & Company and AWDC, and a range of interviews with customers, competitors and industry experts. Bain & Company and AWDC have not independently verified this information and make no representation or warranty, express or implied, that such information is accurate or complete. Projected market and financial information, analyses and conclusions contained herein are based (unless sourced otherwise) on the information described above and on Bain & Company’s and AWDC’s judgment, and should not be construed as definitive forecasts or guarantees of future performance or results. Neither Bain & Company nor AWDC nor any of their subsidiaries or their re- spective officers, directors, shareholders, employees or agents accept any responsibility or liability with respect to this document. This document is copyright Bain & Company, Inc. and AWDC and may not be published, copied or duplicated, in whole or in part, without the written permis- sion of Bain and AWDC. Copyright © 2011 Bain & Company, Inc. and Antwerp World Diamond Centre private foundation (AWDC) All rights reserved Diamond Industry Report 2011 | Bain & Company, Inc. Contents Note to readers..................................................................................................1 1. Introduction to diamonds.....................................................................................3 -
Letšeng's Unique Diamond Proposition
FEATURE ARTICLES LETŠENG’S UNIQUE DIAMOND PROPOSITION Russell Shor, Robert Weldon, A.J.A. (Bram) Janse, Christopher M. Breeding, and Steven B. Shirey The Letšeng-la-Terae diamond mine in Lesotho, a small nation surrounded by South Africa, is unique in that it produces some of the world’s largest and highest-value diamonds from a relatively small volume of kimberlite ore. The mine, operated by De Beers during the late 1970s and early 1980s, was difficult to sustain economically because of its remoteness and very low ore grade, which made production costs very high. Since 2000, sharply rising prices for large diamonds have permitted the mine to reopen prof- itably as a 70/30 venture between Gem Diamonds Ltd. of South Africa and the government of Lesotho. To improve recovery of large diamonds, Letšeng’s owners have implemented new processing technology that provides better identification of these crystals before processing and a crushing mechanism that re- duces their potential breakage. In recent years, several important diamonds recovered from Letšeng have been sold to London luxury jeweler Laurence Graff. hile the Premier (now Cullinan) mine in Until 2004, Letšeng had been shut down for more South Africa is usually cited as the tradi- than 20 years because its low grade and remote loca- Wtional source for very rare large diamonds, tion made mining unprofitable at existing diamond in recent years the Letšeng-la-Terae mine in Lesotho prices. Up until the past decade, De Beers and other has become the major producer of such stones (figure mining companies typically sacrificed large crystals 1). -
The Mineral Industries of Lesotho and Swaziland in 2007
2007 Minerals Yearbook LESOTHO AND SWAZILAND U.S. Department of the Interior March 2010 U.S. Geological Survey THE MINERAL INDUS T RIES OF LESO T HO AND SWAZILAND By Harold R. Newman LESOTHO leading diamond manufacturing and trading companies. SAFDICO bought the 603-carat Lesotho Promise from Gem With the exception of diamond mining, the mining and Diamonds for $12.4 million in 2006. Three of the largest quarrying sector was a marginal contributor to the gross diamonds ever mined have been recovered from the Letseng domestic product of Lesotho. Although Lesotho was believed Mine (Antwerp World Diamond Center, 2007). to have significant mineral deposits, attempts at exploitation Gem Diamonds reported that it was doubling the capacity of continued to be limited owing to lack of investment. Known the Letseng Mine from 2.6 million metric tons per year (Mt/yr) deposits included base metals, clays, diamond, dimension stone, of ore in 2007 to 5.3 Mt/yr by midyear 2008. Efforts directed sand and gravel, and uranium. Reserves of bituminous shale and at maximizing the quality and quantity of diamond recovered coal had been identified in several areas of the country. there were reportedly resulting in improvements in the grade The Ministry of Natural Resources through the Department recovered and the average price per carat. Grade from the of Mines and Geology is responsible for the regulation of the Satellite Pipe was running at 2.26 carats per hundred metric mining sector and coordination of development and operational tons of ore, which was 14% ahead of expectations. A total of activities in the energy, mining, and water sectors. -
143447 Gem Diamonds 2010 Cover 10Mm Spine
Annual Report 2010 GEM DIAMONDS ANNUAL REPORT 2010 Highlights 1 Board of Directors 2 Chairman’s Review 4 Business Review 5 Mineral Resource Management 16 Sustainable Development Report 17 Directors’ Report 45 Remuneration Report 48 Corporate Governance Report 56 Annual Financial Statements 63 Contacts and Advisors IBC Front cover image: 196 carat and 184 carat rough diamonds recovered at Letšeng during 2010. Inside front cover image: 4.68 carat blue diamond recovered from Letšeng and sold for a Letšeng record price of US$155 000 per carat. GEM DIAMONDS ANNUAL REPORT 2010 Gem Diamonds is a global diamond mining company that is pursuing a long term growth strategy through the development of its existing assets and targeted acquisitions. Under the depressed market conditions of late 2008 and early 2009, the Company focused its strategy on developing its cash generating assets and curtailing all non-essential capital and development expenditure. Following the steady improvement in the diamond market during 2010, the Company has completed the development of a growth strategy designed to take advantage of these improving conditions. The Company’s portfolio comprises producing kimberlite and lamproite mines in Lesotho and Australia, as well as development projects and exploration assets in Angola and Botswana. With Letšeng’s production of the world’s most remarkable white diamonds and Ellendale’s production of rare fancy yellow diamonds, Gem Diamonds remains focused on higher value diamonds. This segment of the market is expected to deliver attractive -
AN ECONOMIC REVIEW of the PAST DECADE in DIAMONDS by William E
AN ECONOMIC REVIEW OF THE PAST DECADE IN DIAMONDS By William E. Boya jian The diamond industry was buffeted by lthough the market for gem diamonds has long extreme price volatility during the last A enjoyed stability and gradual appreciation, it can decade, unlike any encountered since the nevertheless be sensitive to a variety of economic forces. Great Depression of the 1930s. Although At no time has this been more evident than in the period the industry is currently enjoying a re- that spanned the late 1970s to the mid-1980~~when market surgence of activity worldwide, partic- demand and prices climbed to incredible highs- before ularly in the Far East, today's market dif- falling precipitously to equally stunning lows. fers significantly from what it was 10 years ago. This article reviews the factors In November 1973, the American economy entered its that led to the enormous demand for dia- sixth post-World War I1 recession. In 1974 and 1975, De monds in the late 1970s, examines the Beers's rough diamond sales declined by 5% and 15%, causes of recession in the early 1980s, and respectively. Consumer confidence and consumer spend- provides an analysis of the comeback of ing in the United States bottomed out. The second half of diamond in 1986. Inasmuch as events the 1970s, however, heralded a period of rapid inflation, during this period ushered many changes during which many investors sought tangible assets as a into the diamond trade, an understanding hedge. Diamonds, with a tradition of steady, rising value, of how economic forces affect the supply. -
Gem Diamonds Half-Year 2016 Results
Gem Diamonds Half-Year 2016 Results 17 August 2016 Strong operational performance at Letšeng underpins half-year 2016 results Gem Diamonds Limited (LSE: GEMD) (Gem Diamonds, the Company or the Group) today announces its half-year results for the six months ended 30 June 2016 (H1 2016 or the Period). FINANCIAL RESULTS: Solid EBITDA1 achieved • Revenue of US$109.1 million (US$118.0 million in H1 2015) • Underlying EBITDA of US$43.5 million (US$46.1 million in H1 2015) • Attributable profit (before exceptional item) of US$13.4 million (US$15.4 million in H1 2015) • Basic EPS (before exceptional item) of 9.70 US cents (10.69 US cents in H1 2015) • After the exceptional item of a US$40.0 million non-cash impairment to the Ghaghoo asset, attributable loss of US$26.6 million and basic loss per share of 19.23 US cents • Ordinary dividend of 5 US cents per share (US$6.9 million) and special dividend of 3.5 US cents per share (US$4.9 million) were paid on 14 June 2016 • Cash on hand of US$66.5 million as at 30 June 2016 (US$53.2 million attributable to Gem Diamonds) 1 Underlying earnings before interest, tax, depreciation and mining asset amortisation OPERATIONAL RESULTS: Letšeng: Continues to perform well with steady prices achieved for high value diamonds • Waste tonnes mined of 15.3 million tonnes (11.4 million tonnes in H1 2015) • Ore treated of 3.3 million tonnes (3.1 million in H1 2015) • Carats recovered of 57 380 (50 019 in H1 2015) • Average value of US$1 899* per carat achieved (US$2 264* in H1 2015) • 20 diamonds achieved a sales value -
Gem Diamonds 2015 Results
RNS Number: Gem Diamonds Limited 15 March 2016 15 March 2016 GEM DIAMONDS FULL YEAR 2015 RESULTS Gem Diamonds Limited (the Company) is pleased to announce its Full Year Results for the year ending 31 December 2015 (the Period). FINANCIAL RESULTS • Revenue US$249.5 million, down 8% YoY • Underlying EBITDA US$103.5million, down 2% YoY • Profit for the year US$67.4 million, up 12% YoY • Attributable profit (post exceptional items) US$52.0 million, up 57% YoY • Earnings per share (pre exceptional items), 30.2 US cents, up 26% YoY DIVIDEND • Ordinary dividend of 5 US cents per share recommended • Special dividend of 3.5 US cents per share also recommended Commenting on the results today, Clifford Elphick, Chief Executive Officer of Gem Diamonds, said: “It is pleasing to see that the prices achieved for Letšeng's diamonds during 2015 have remained robust despite the sharp downturn in the global market. The world class, high quality diamonds, for which Letšeng is renowned, have contributed to the strong results at an average price of US$2 299 per carat for the year.” “Although 2015 was a challenging year for the diamond mining industry, it is encouraging to report that the Group has delivered a strong set of operational and financial results. The Group continued to implement its strategic objectives of capital discipline by investing in low cost high return capital projects. The increase in the recoveries of the important +100 carat diamonds from an average of 6 per year to 11 in 2015 demonstrates the success of the initiatives.” The key objectives for the development of Phase 1 at the Ghaghoo mine have been achieved. -
Diamond Localities
G&G Data Depository: Commercial diamond-producing localities active in the period 2000–2010, to accompany J. E. Shigley et al., “Gem Localities of the 2000s,” Fall 2010 G&G, pp. 188-216. Country State/province Nearest town Mine/deposit Deposit Annual Mined by Reference a or district name type production Africa Angola Gordon (2004), Chapman (2005), Egorov et al. (2005) Lunda Norte Lucapa Camatchia Kimberlite Medium Endiama, Escom Mining Lunda Norte Lucapa Camafuca Kimberlite Medium Endiama, Alrosa, Mwana Lunda Norte Lucapa Camatue Kimberlite Medium Tecmad Mining Services SARL, Resource & Investment NL Lunda Norte Lucapa Camazuanza Kimberlite Medium Endiama Lunda Norte Lucapa Calonda Alluvial Medium Endiama, ITM Mining Ltd. ITM Mining (2010a) Lunda Norte Lucapa Yetwene Alluvial Medium Endiama, ITM Mining Ltd. Endiama (2010c) Lunda Norte Lucapa Mafuto Alluvial Medium Endiama, ITM Mining Ltd. ITM Mining (2010d) Lunda Norte Lucapa Luarica Alluvial Medium Endiama, Trans Hex Endiama (2010b) Group Ltd. Lunda Norte Lucapa Luana Alluvial Medium Endiama, Trans Hex Trans Hex (2010) Group Ltd. Lunda Norte Nzaji Chitotolo Alluvial Medium Endiama, ITM Mining Ltd. ITM Mining (2010b) Lunda Norte Nzaji Chimbongo Alluvial Medium Endiama, Alrosa, Escom Mining Lunda Norte Nzaji Maludi Alluvial Medium Lunda Norte Dundo Faucama Alluvial Medium Endiama, Trans Hex Endiama (2010a) Group Ltd. Lunda Norte Dundo Cassanguidi Alluvial Medium Endiama, PangeaDF Lunda Norte Cuango- Tazua Alluvial Medium Endiama, Odebrecht ITM Mining (2010c) Luzamba Lunda Norte Canfunfo Luremo Alluvial Medium Endiama Lunda Sul Saurimo Catoca Kimberlite Very large Endiama, Alrosa, Leviev Zinchenko (2008), Read and Janse (2009), Robles-Cruz et al. (2009) Botswana Field et al. (2008) Central Francistown Orapa Kimberlite Huge Debswana Deines et al.