An Experimental Investigation of Human/Bicycle Dynamics and Rider Skill In
Total Page:16
File Type:pdf, Size:1020Kb
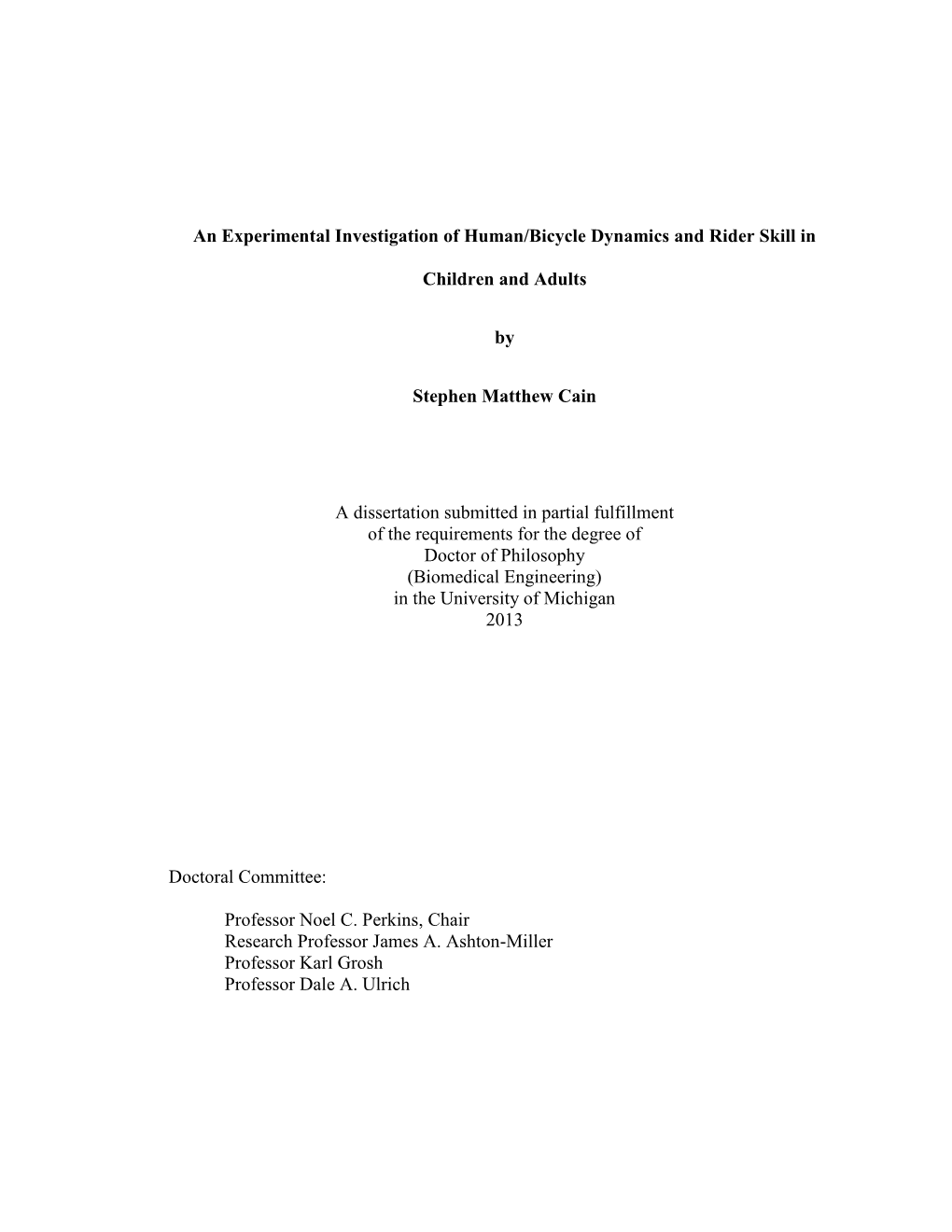
Load more
Recommended publications
-
Writing the Bicycle
Writing the Bicycle: Women, Rhetoric, and Technology in Late Nineteenth-Century America Sarah Overbaugh Hallenbeck A dissertation submitted to the faculty of the University of North Carolina at Chapel Hill in partial fulfillment of the requirements for the degree of Doctor of Philosophy in the Department of English and Comparative Literature. Chapel Hill 2009 Approved by: Jane Danielewicz Jordynn Jack Daniel Anderson Jane Thrailkill Beverly Taylor ABSTRACT Sarah Overbaugh Hallenbeck Writing the Bicycle: Women, Rhetoric, and Technology in Late Nineteenth-Century America (Under the direction of Jane Danielewicz and Jordynn Jack) This project examines the intersections among rhetoric, gender, and technology, examining in particular the ways that American women appropriated the new technology of the bicycle at the turn of the twentieth century. It asks: how are technologies shaped by discourse that emanates both from within and beyond professional boundaries? In what ways do technologies, in turn, reshape the social networks in which they emerge—making available new arguments and rendering others less persuasive? And to what extent are these arguments furthered by the changed conditions of embodiment and materiality that new technologies often initiate? Writing the Bicycle: Women, Rhetoric and Technology in Late Nineteenth- Century America addresses these questions by considering how women’s interactions with the bicycle allowed them to make new claims about their minds and bodies, and transformed the gender order in the process. The introduction, “Rhetoric, Gender, Technology,” provides an overview of the three broad conversations to which the project primarily contributes: science and technology studies, feminist historiography, and rhetorical theory. In addition, it outlines a “techno-feminist” materialist methodology that emphasizes the material ii and rhetorical agency of users in shaping technologies beyond their initial design and distribution phases. -
Teaching Kids to Ride
Accessories Bicycles Parts Specials Tools Search Teaching Kids To Ride Translations of this article: Belarusian Czech Georgian Latvian Select Language Tweet Like Share Powered by Translate Follow @sheldonbrowncom Polish Portuguese Serbian by Sheldon "Two Wheeler" Brown revised by John Allen Adult Beginners Balance Brakes Draisines ("no-pedal bikes") Patience Safety Equipment Scooters Stabilisers Running With Child Testimonials Traffic Training Wheels Tricycles Undersized Bike Teaching Kids To Ride One of the many tasks parents must undertake is teaching their children to ride bicycles. At every stage of the learning process, there are several possible approaches, and most parents will be unsure how to proceed. This article will try to cover the options and explain when to choose which. This article focuses on only the most basic skills: pedaling, steering and balancing, that make it possible for a child to operate a bicycle. There is much more to teach and to learn about cycling than this, but that is mostly beyond the scope of this particular article. Tricycles For most children, a tricycle is the first step in learning to ride. The most useful tricycles are the smallest ones, like the one shown in the photo. Ideally, a child should get a tricycle even before he or she learns to walk. A tricycle has only two things to teach a child: steering and pedaling. The steering usually comes first, because the child can stand on the back step with one foot and push along with the other. Some children will be able to master this even before learning to walk. Once the basic concept of steering has been learned, the child can start to use the pedals. -
Willy WATTS 14
VOLUME 4 BO. 3 <,JARTERLY JULY 1977 { Official Organ UNICYCLING SOCIETY OF AMERICA. Inc. c 1977 ~11 Rts Rea. Yearly Membership S5 Incl~des NeVl!lletter (4) ID Card - See Blank Pg.18 OFFICERS FELI.OW UNICYCLISTS: Due to o·trcwastances beyond our control (namely a big pile of dirt and construction lfOrk) the Southland Mall in Marion Pres. Paul Fox will not be available for our National Meet races on A.ug. 20. lttempts v.Pres. R.Tschudin to secure an alternate suita'Qle location nearby have failed. We are Sec. T. ni.ck Haines therefore planning to anit the Saturday morning races and utilize that FOUNDER M:El-!BE&S part of the day this year ror a general convention type get-together where clubs and inru.viduais can meet each other, swap ideas, and display Bernard Crandall their talents and cycles. · We still plan to hold the preliminary elimi Paul & Nancy Fox nations for the group an9- trick riding later in the day at the Catholic Peter Hangach High School parking lot·. We also have the use of the Coliseum again for Patricia Herron the Sunday afternoon final~. A pan.de is still in question and if we do Bill Jenack hold one it will be JllUCh s.horter than last year. It, is hoped that every Gordon Kruse member will make a ~ec~al-effort to attend the annual business meeting Steve McPeak Sunday rooming at th(' Hpltday Inn. We have a number of V9ry important Fr. Jas. J. Moran items on the agenda (see pag~ 14 for further infomation). -
The History of Cycling
The History of Cycling 1493 A student of Leonardo Da Vinci sketched an idea for a bicycle. 1817 Drais running machine, the 'Draisine'. It was also called the 'hobby horse' because it competed with horses for transport. It was popular in Europe and North America and didn't have any pedals. Instead the riders pushed against the ground with their feet to move along. 1860s The French velocipede was also called 'bone shaker', because it had such hard wooden wheels and was rough to ride on old roads and cobblestones. There was a major breakthrough when pedals were added to the front wheel of a running machine. Again, the 'bone shaker' was a huge craze in Europe and North America, where special schools were set up to teach people how to ride. 1870s The British penny farthing was named because it looked like two British coins, the large penny in front and the small farthing behind. The penny farthing used several new inventions to make it much better than the bone shaker. They used tubular steel frames that were light, strong and cheap. The wheels and pedals had ball bearings that allowed them to spin smoothly and lasted a long time. Wheels had previously used wooden spokes which were much stronger and heavier than needed. On the penny farthing they used wire spokes, which were a major breakthrough as the wheels were not only much lighter, but were also able to be repaired easily. Adding solid rubber tyres to the outside of the wheel gave the wheels more grip and made the ride smoother by absorbing some of the bumps. -
Electronic Training Wheels: an Automated Cycling Track Stand
Proceedings of Australasian Conference on Robotics and Automation, 2-4 Dec 2014, The University of Melbourne, Melbourne, Australia Electronic training wheels: An automated cycling track stand D. Wardle, T. Gregory, B. Cazzolato University of Adelaide, Australia [email protected], [email protected], [email protected] Abstract associated with children so the public response of train- ing wheels for adults would be poor. As a result, several A track stand is the act of balancing a bicycle more technical solutions have been created. while stationary, an inherently hard technique One of these more technical solutions is stabilisation to perform. Several devices exist that provide through conservation of angular momentum, which has lateral stabilisation of a bicycle, though few are been utilised by a design produced by Gyrowheel. The designed to assist a rider. In this paper the concept involves a battery powered rotor in the front design and derivation of dynamics are detailed wheel of the bicycle [Clawson, 2014], through conser- for a Single Gimbal Control Moment Gyroscope vation of angular momentum (and resulting gyroscopic (SGCMG) retrofitted to an adult-sized bicycle. precession) the bicycle wheel will impede angular veloc- A linear control system is designed with corre- ity about the roll or yaw axes. Active control and gy- sponding simulations of the modelled system. roscopic precession has been implemented on a design Linear theory shows that a minimum rotor mo- by Lam [2011], which employs a SGCMG mounted on a mentum is required for stabilisation. The phys- children's bicycle. The rotor spins at significant angular ical system is described with results showing velocity and is rotated by the gimbal to exert a torque the rider track stand time has significantly in- on the bicycle to keep the bicycle upright. -
The History of the Wheel and Bicycles
NOW & THE FUTURE THE HISTORY OF THE WHEEL AND BICYCLES COMPILED BY HOWIE BAUM OUT OF THE 3 BEST INVENTIONS IN HISTORY, ONE OF THEM IS THE WHEEL !! Evidence indicates the wheel was created to serve as potter's wheels around 4300 – 4000 BCE in Mesopotamia. This was 300 years before they were used for chariots. (Jim Vecchi / Corbis) METHODS TO MOVE HEAVY OBJECTS BEFORE THE WHEEL WAS INVENTED Heavy objects could be moved easier if something round, like a log was placed under it and the object rolled over it. The Sledge Logs or sticks were placed under an object and used to drag the heavy object, like a sled and a wedge put together. Log Roller Later, humans thought to use the round logs and a sledge together. Humans used several logs or rollers in a row, dragging the sledge over one roller to the next. Inventing a Primitive Axle With time, the sledges started to wear grooves into the rollers and humans noticed that the grooved rollers actually worked better, carrying the object further. The log roller was becoming a wheel, humans cut away the wood between the two inner grooves to create what is called an axle. THE ANCIENT GREEKS INVENTED WESTERN PHILOSOPHY…AND THE WHEELBARROW CHINA FOLLOWED 400 YEARS AFTERWARDS The wheelbarrow first appeared in Greece, between the 6th and 4th centuries BCE. It was found in China 400 years later and then ended up in medieval Europe. Although wheelbarrows were expensive to purchase, they could pay for themselves in just 3 or 4 days in terms of labor savings. -
Discovering Bicycling Leaders Manual
Leaders Manual 4-H Body Works Series Discovering Bicycling Learning is 3D! To help you get the most out of your learning, each project meeting has Dig It Dream It the following parts: Dream it! Plan for success Do it! Hands on learning Dig it! What did you learn? Do It What Skills Will You Learn? To complete this project, members must: Spend a minimum of 15 - 20 hours completing the project work. Complete the listed activities, OR a similar activity that focuses on the same skills, as you and your members may plan other activities. Plan and complete the Showcase Challenge Complete the Portfolio Page. Participate in your club’s Achievement (see the inside back cover for more information about 4-H Achievement). This project is being offered in Manitoba, with permission from Saskatchewan 4-H Council. Achievement (project completion) requirements for 4-H Manitoba apply to this project and are described above. The amount of time spent on project work may exceed the minimum 15 hours, depending on the project that you have chosen and the activities within the project. This project was selected to be offered by 4-H Manitoba because it provides members with the opportunity to meet Manitoba 4-H project learning objectives. These objectives include technical skills, communication, meeting management, leadership skills, as well as community involvement and real world experiences. Showcase Challenge and My Portfolio Page At the end of the member’s section are the “Showcase Challenge” and “My Portfolio Page”. The “Showcase Challenge” page gets members to think about their accomplishments and explain or demonstrate how they were successful. -
Owner's Manual
OWNER’S MANUAL ADULT / ELECTRIC / JUVENILE OWNER’S RESPONSIBILITY Consult last page of manual for Warranty Registration This manual contains important information regarding the safe operation and maintenance of your bicycle. Read all sections and appendices before you ride your new bicycle, and carefully follow the instructions. Instructions preceded by the words NOTE, CAUTION, or WARNING are of special significance. NOTE: Instructions which are of special interest. CAUTION: Indicates a potentially hazardous situation which, if not avoided, may result in minor or moderate injury, or is an alert against unsafe practices. WARNING: Indicates a potentially hazardous situation which, if not avoided, could result in serious injury or death. THEFT AND WARRANTY INFORMATION • Record all numbers shown on the bicycle. • Be sure to fill out warranty information online (or mail in if you do not have access to a computer). NOTE: The serial number is not on record where your bicycle was sold or manufactured, you must register it. Keep the following information along with a copy of your sales receipt. Serial Number: Model Name: Store Purchased From: Purchase Date: Color: Size: • Lock your bicycle securely whenever it is out of your sight. • Also, carefully follow the instructions in any additional literature supplied with the bicycle. WARNING: Before your first ride, check the brakes and all cam action retention devices. Service, if necessary, is described in the maintenance section of this manual. • Register your bicycle with your local law enforcement agency & National Bike Registry. • Report any theft immediately. • Add your bicycle to your homeowner’s or apartment insurance policy. Serial Number Locations WARNING: MUST READ BEFORE RIDING • Obtain, read, and follow Owner’s Manual. -
1990) Through 25Th (2014
CUMULATIVE INDEX TO THE PROCEEDINGS OF THE INTERNATIONAL CYCLE HISTORY CONFERENCES 1st (1990) through 25th (2014) Prepared by Gary W. Sanderson (Edition of February 2015) KEY TO INDEXES A. Indexed by Authors -- pp. 1-14 B. General Index of Subjects in Papers - pp. 1-20 Copies of all volumes of the proceedings of the International Cycling History Conference can be found in the United States Library of Congress, Washington, DC (U.S.A.), and in the British National Library in London (England). Access to these documents can be accomplished by following the directions outlined as follows: For the U.S. Library of Congress: Scholars will find all volumes of the International Cycling History Conference Proceedings in the collection of the United States Library of Congress in Washington, DC. To view Library materials, you must have a reader registration card, which is free but requires an in-person visit. Once registered, you can read an ICHC volume by searching the online catalog for the appropriate call number and then submitting a call slip at a reading room in the Library's Jefferson Building or Adams Building. For detailed instructions, visit www.loc.gov. For the British Library: The British Library holds copies of all of the Proceedings from Volume 1 through Volume 25. To consult these you will need to register with The British Library for a Reader Pass. You will usually need to be over 18 years of age. You can't browse in the British Library’s Reading Rooms to see what you want; readers search the online catalogue then order their items from storage and wait to collect them. -
4-H Bicycling Project – Reference Book
4-H MOTTO Learn to do by doing. 4-H PLEDGE I pledge My HEAD to clearer thinking, My HEART to greater loyalty, My HANDS to larger service, My HEALTH to better living, For my club, my community and my country. 4-H GRACE (Tune of Auld Lang Syne) We thank thee, Lord, for blessings great On this, our own fair land. Teach us to serve thee joyfully, With head, heart, health and hand. This project was developed through funds provided by the Canadian Agricultural Adaptation Program (CAAP). No portion of this manual may be reproduced without written permission from the Saskatchewan 4-H Council, phone 306-933-7727, email: [email protected]. Developed in January 2013. Writer: Leanne Schinkel Table of Contents Introduction Objectives .................................................................................................................................................... 1 Getting the Most from this Project ....................................................................................................... 1 Achievement Requirements for this Project ..................................................................................... 2 Safety and Bicycling ................................................................................................................................. 2 Online Safety .............................................................................................................................................. 4 Resources for Learning ............................................................................................................................ -
CTM English E2 First Bicycles Final.Cdr
The First Bicycles Course: English Adult Learning at Coventry Transport Museum The First Bicycles Course: English Teacher information This activity is designed for learners working at Entry 2 or above. The questions are based on information in this museum exhibition: Cycle Pioneers 1868-1900 Learners can answer the questions on the wipeable answer sheet. There is a vocabulary sheet at the front of the pack. In this activity, learners will practice: • using illustrations, captions and images to locate information • understanding the main points in texts • sequencing words in alphabetical order Introduction Go to this exhibition to answer the questions: Cycle Pioneers 1868-1900 You can answer the questions on the wipeable answer sheet. What are pioneers? Pioneers are the first people to do something. The Cycle Pioneers 1868 - 1900 exhibition tells you about the people who were first to design and develop bicycles. It also tells you about the history of the bicycle and how the bicycle started out. To understand the history of the bicycle, you can look at the captions and illustrations. Captions are labels or headings, and illustrations are pictures. You can use the captions and illustrations in the museum to help you understand the history of the bicycle. Vocabulary Parts of a Bicycle Brake Lever Handlebars Saddle Brakes Pedals Tyres Brakes These help the rider to slow down and stop a bicycle. The rider squeezes a lever on the handlebars to make the brakes work. The brakes squeeze on the wheels to make them stop. Handlebars A bar with a handle on each end. The rider holds each end of the handlebars to steer the bicycle. -
The Bicycle in America to 1900
Oberlin Digital Commons at Oberlin Honors Papers Student Work 1941 The Bicycle in America to 1900 William Herbert Mariboe Oberlin College Follow this and additional works at: https://digitalcommons.oberlin.edu/honors Part of the History Commons Repository Citation Mariboe, William Herbert, "The Bicycle in America to 1900" (1941). Honors Papers. 788. https://digitalcommons.oberlin.edu/honors/788 This Thesis is brought to you for free and open access by the Student Work at Digital Commons at Oberlin. It has been accepted for inclusion in Honors Papers by an authorized administrator of Digital Commons at Oberlin. For more information, please contact [email protected]. • 'THE BICYCLE IN AMERICA TO 1900 ' By William Herbert Mariboe A.B. Oberlin College, 1940 A thesis submitted to the Faculty of Oberlin College in partial fulfillment of the requirements for the Degree of Master of Arts in the Department of History 1941 t TABLE OF CONTENTS Introduction. • • • • • • • • . l History ot The Bicycle Era. • • • • • • • • • • 7 The Velocipede. • • • • • • • • .. • • • • • 9 High Bicycle Era. • • • • • • • • • • • • • 13 Progress Toward The Safety••••••••• 18 The "Safety" •••••••••••••••• 21 Manufacturing • • • • • • • • • • • • • • • 30 Advertising • • • • • • • • • • • • • • • • 40 Organizations• ••••••••••••••••• 51 League of American Wheelm.en •••••••• 52 L.A. W. and Law • • • • • • • • • • • • 56 L.A. W. and Good Roads. • • • • • • • • 59 The Club Movement •••••••••••• • 61 Racing. • . • • • . • . 66 Military Use. • • • • • • • • • • •