Catalytic Production of Hydrogen from Methanol
Total Page:16
File Type:pdf, Size:1020Kb
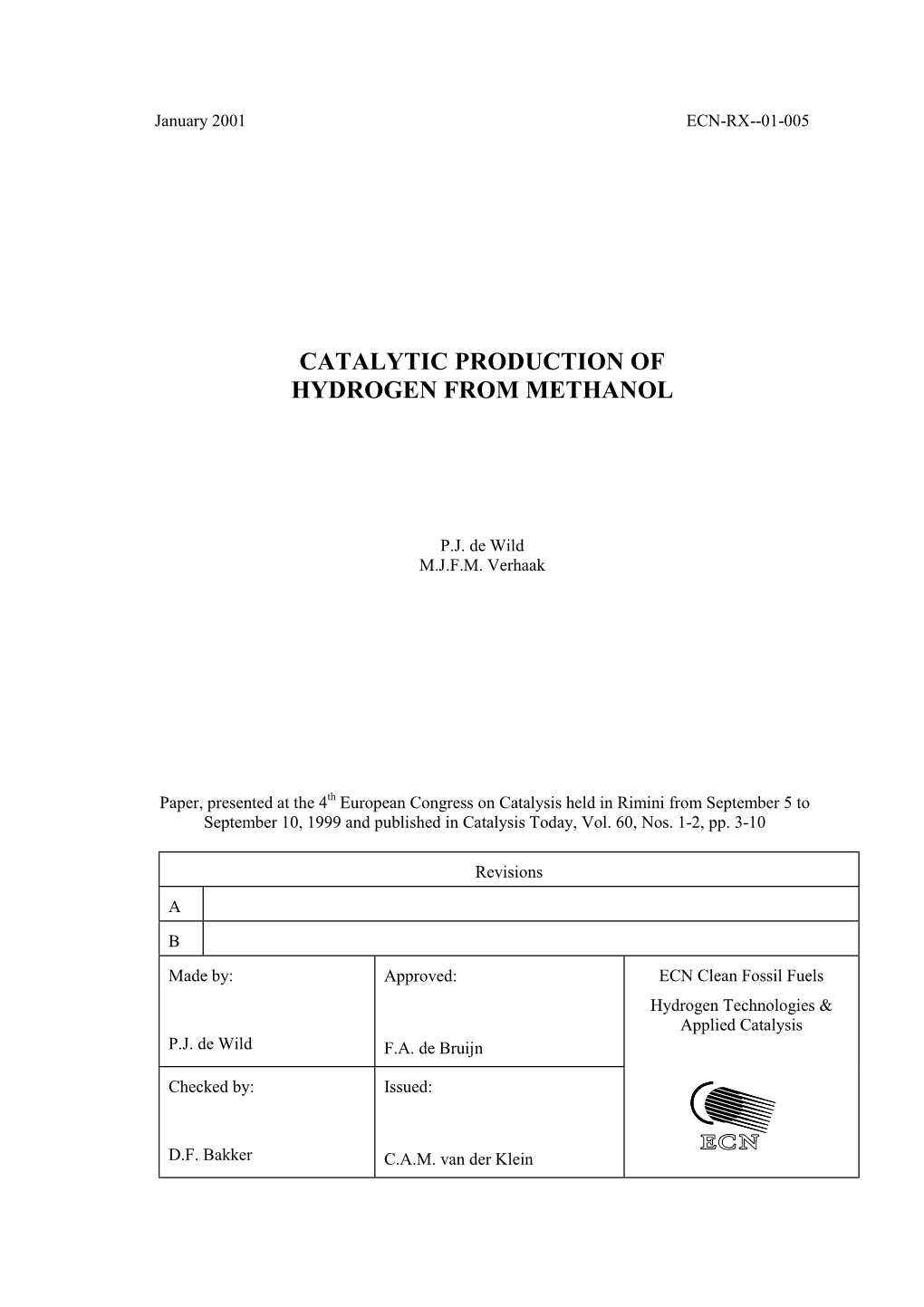
Load more
Recommended publications
-
Final REPORT Work Package 3
Final REPORT Work Package 3 Grant Agreement number: 303461 Project acronym: LIQUIDPOWER Project title: Fuel Cell Systems and Hydrogen Supply for Early Markets Funding Scheme: Collaborative Project (CP) Name, title and organization of the scientific representative of the project's coordinator: Ms Kristina Fløche Juelsgaard, Dantherm Power A/S Tel: +45 51580749 Fax: +45 96 14 38 05 E-mail: [email protected] Report prepared by: Tihamer Hargitai, managing director Catator AB (Sweden) Fredrik A Silversand, executive chairman Michael Steffen, Head of division, fuel processing Zentrum für BrennstoffzellenTechnik ZBT Ulrich Gardemann, project manager, fuel processing GmbH (Germany) 1 Final REPORT Work Package 3 Introduction – R&D methanol reformer for onsite H2 supply The objectives of this work package are the R&D of a methanol reforming system with higher outlet pressure, capacity and purity as well as reduced costs providing low cost hydrogen fuel suitable for LT-PEM fuel cells in the addressed markets. This is to be verified by conducting of laboratory testing of the developed components and complete system. In order to reach these objectives we have been through the following tasks: Task 3.1 Definition of suitable catalyst with improved performance & reduced costs Concerning the active material within the catalyst formulation there are two catalyst types which are considered for the methanol steam reforming, namely copper-based (Cu) and precious metal-based (PM) catalysts. Main issues for the selection are efficiency, lifetime and costs. Copper-based catalysts are state of the art for steady state methanol steam reforming systems on an industrial scale. The main advantages are the high activity at moderate temperatures of around 250 – 300 °C and the relatively low costs. -
The Operation of Polymer Electrolyte Membrane Fuel Cell Using Hydrogen Produced from the Combined Methanol Reforming Process
Research Article J. Electrochem. Sci. Technol., 2016, 7(2), 146-152 Journal of Electrochemical Science and Technology The Operation of Polymer Electrolyte Membrane Fuel Cell using Hydrogen Produced from the Combined Methanol Reforming Process Sang Sun Park1, Yukwon Jeon2, Jong-Man Park2, Hyeseon Kim1, Sung Won Choi2, Hasuck Kim3, and Yong-Gun Shul2,* 1lotte chemical, #24-1 Jang-dong, Yuseong-Gu, Daejeon-city. 305-726, Republic of Korea 2Department of Chemical and Biomolecular Engineering, Yonsei University, 50 Yonsei-ro, Seodaemun-gu, Seoul 120-749, Republic of Korea 3Department of Energy Systems Engineering, Daegu Gyeongbuk Institute of Science &Technology (DGIST), 50-1 Sang-Ri, Hyeonpung-Myeon, Dalseong-Gun, Daegu 711-873, South Korea ABSTRACT A combined system with PEMFC and reformer is introduced and optimized for the real use of this kind of system in the future. The hydrogen source to operate the PEMFC system is methanol, which needs two parts of methanol reforming reac- tion and preferential oxidation (PROX) for the hydrogen fuel process in the combined operation PEMFC system. With the optimized methanol steam reforming condition, we tested PROX reactions in various operation temperature from 170 to 270 oC to investigate CO concentration data in the reformed gases. Using these different CO concentration, PEMFC per- formances are achieved at the combined system. Pt/C and Ru promoted Pt/C were catalysts were used for the anode to com- pare the stability in CO contained gases. The alloy catalyst of PtRu/C shows higher performance and better resistance to CO than the Pt/C at even high CO amount of 200 ppm, indicating a promotion not only to the activity but also to the CO tolerance. -
A Computational Analysis of a Methanol Steam Reformer Using Phase Change Heat Transfer
energies Article A Computational Analysis of a Methanol Steam Reformer Using Phase Change Heat Transfer Hyemin Song 1, Younghyeon Kim 1, Dongjin Yu 1 , Byoung Jae Kim 2 , Hyunjin Ji 3 and Sangseok Yu 2,* 1 Mechanical Engineering, Graduate School, Chungnam National University, 99 Daehangno, Yuseong-gu, Daejeon 34134, Korea; [email protected] (H.S.); [email protected] (Y.K.); [email protected] (D.Y.) 2 School of Mechanical Engineering, Chungnam National University, 99 Daehangno, Yuseong-gu, Daejeon 34134, Korea; [email protected] 3 Agency for Defense Development, Yuseong P.O.Box 35-44, Daejeon 305-600, Korea; [email protected] * Correspondence: [email protected]; Tel.: +82-42-821-5646; Fax: +82-42-822-5642 Received: 18 May 2020; Accepted: 17 August 2020; Published: 21 August 2020 Abstract: A methanol steam reformer converts methanol and steam into a hydrogen-rich mixture through an endothermic reaction. The methanol reformer is divided into a reaction section and a heat supply section that transfers thermal energy from 200 to 300 ◦C. This study presents the behavior of the methanol steam reforming reaction using the latent heat of the steam. A numerical analysis was separately conducted for two different regimes assuming constant heat flux conditions. A methanol steam reformer is an annulus structure that has a phase change heat transfer from an outer tube to an inner tube. Different from the steam zone temperature in the tube, the latent heat of steam condensation decreases, and there is a gradual between-wall temperature decrease along the longitudinal direction. Since the latent heat of steam condensation is very sensitive to the requested heat from the reformer, it is necessary to consider a refined design of a methanol reformer to obtain a large enough amount of heat by steam condensation. -
Development of a Novel Palladium Membrane-Based Alkaline Direct Methanol Fuel Cell
Development of a Novel Palladium Membrane-based Alkaline Direct Methanol Fuel Cell A Major Qualifying Project Report: submitted to the Faculty of the WORCESTER POLYTECHNIC INSTITUTE Chemical Engineering Department in partial fulfillment of the requirements for the Degree of Bachelor of Science by Brian Walker Date: April 25th, 2013 Advisor: Ravindra Datta Acknowledgements I would like to thank the entire fuel cell lab group at Worcester Polytechnic Institute for assisting me in the completion of this project. I would like to especially thank my advisor, Professor Ravi Datta and graduate student Susan Yen for working with me throughout the duration of this project and offering excellent advice and insight into the concepts and tasks encountered while working on this project. Abstract The conventional direct methanol fuel cell (DMFC) operates with Nafion® membrane at ambient temperatures using dilute methanol feeds, and provides relatively poor performance because of slow kinetics and methanol crossover, despite high catalyst loading. The alternative is to reform methanol in a reformer and use it in conjunction with a hydrogen-oxygen PEM fuel cell, which results in a bulky unit. In this project, the overall goal was to design a high temperature DMFC based on alkaline electrolyte that could utilize concentrated methanol feeds directly. It uses a palladium membrane that serves both as the anode and as a membrane that precludes methanol crossover as well as CO2 reaction with the alkaline electrolyte. This novel fuel cell is designed as a planar cell, with the SiC ceramic support oriented as a circular wafer. This support had a dense palladium and silver membrane plated on one of its circular faces, operating as the anode. -
Catalvtic Heat Exchamzers for Small-Scale I Production of Hy( ~ D D
Rapport SGC 129 ) Catalvtic Heat Exchamzers for small-scale i production of hy( ~ d d ‘Svenskt Gastekniskt Center - Februari 2002 al gas s m -600“C I —.... I p.” L Hydrodesul- 1- Iwl J furisatwn UzlnO LT-sh ijfk r So”c Steam refomning of natural gas d 4 separation F25“C Fredrik Silversand CATATOR AB SGC:S FORORD FUD-projekt inom Svenskt Gastekniskt Center AB avrapporteras normalt i rapporter som ar fritt tillgangliga for envar intresserad. SGC svarar for utgivningen av rapporterna medan uppdragstagarna for respective proj ekt eller rapportforfattarna svarar for rapporternas inne- h~ll. Den som utnyttjar eventuella beskrivningar, resultat e dyl i rap- porterna gor detta belt pa eget ansvar. Delar av rapport f%- &erges med angivande av kallan. En forteckning over hittills utgivna SGC-rapporter firms pa SGC’S hemsida vvww.sgc.se. Svenskt Gastekniskt Center AB (SGC) ar ett samarbetsorgan for foretag verksamma inom energigasomr~det. Dess framsta uppgift ar att samordna och effektivisera intressenternas insatser inom omr~dena forskning, utveckling och demonstration (FUD). SGC har foljande delagare: Svenska Gasforeningen, Sydgas AB, Sydkraft AB, Goteborg Energi AB, Lunds Energi AB och Oresundskraft AB. Foljande parter har gjort det mojligt att genomfora detta utvecklingspro- jekt: Sydgas AB Catator AB SWEP International AB Statens Energimyndighet Summary A feasibility study concerning heat-exchanger reactors in small-scale production of hydrogen has been performed on the request of Svenskt Gastekniskt Center AB and SWEP International AB. The basic idea is to implement different catalysts into brazed plate-type heat exchangers. This can be achieved by installing catalytic cylinders in the inlet-and outlet ports of the heat exchangers or through treatment of the plates to render them catalytically active. -
Review of Small Stationary Reformers for Hydrogen Production
IEA/H2/TR-02/002 REVIEW OF SMALL STATIONARY REFORMERS FOR HYDROGEN PRODUCTION Dr. Joan M. Ogden Research scientist Center for Energy and Environmental Studies Princeton University Princeton, NJ 08544 Phone: (609) 258-5470 Email: [email protected] A report for the International Energy Agency Agreement on the Production and Utilization of Hydrogen Task 16, Hydrogen from Carbon-Containing Materials Preface The following report was prepared in support of efforts to develop a new International Energy Agency (IEA) task on the production of hydrogen from carbon-containing materials. The draft report was completed and the results presented during a Task Development Workshop in March 2001. The discussion in this report is based on technology developments that had been reported or were known prior to March 2001. No updates have been made to reflect advancements that have taken place since that time. An update to this report will be a likely outcome of the new IEA Agreement on the Production and Utilization of Hydrogen Task 16, Hydrogen from Carbon-Containing Materials, which officially began in April 2002 and will be active for three years. REVIEW OF SMALL STATIONARY REFORMERS FOR HYDROGEN PRODUCTION TABLE OF CONTENTS I. INTRODUCTION ............................................................................................................. 1 II. HYDROGEN SUPPLY OPTIONS FOR THE TRAN SPORTATION SECTOR ............. 3 A. MOTIVATION FOR HYDROGEN AS A TRANSPORTATION FUEL: ENVIRONMENTAL AND ENERGY SUPPLY CHALLENGES FACING THE TRANSPORTATION SECTOR .................................... 3 B. REVIEW OF PAST STUDIES OF HYDROGEN REFUELING INFRASTRUCTURE .................... 4 C. HYDROGEN INFRASTRUCTURE DEMONSTRATIONS........................................................ 6 D. DISTRIBUTED VERSUS CENTRALIZED HYDROGEN PRODUCTION ................................... 6 E. ROLES FOR SMALL REFORMERS IN DEVELOPMENT OF A HYDROGEN ENERGY SYSTEM 6 III. -
Methanol Electrolysis for Hydrogen Production Using Polymer Electrolyte Membrane: a Mini-Review
energies Review Methanol Electrolysis for Hydrogen Production Using Polymer Electrolyte Membrane: A Mini-Review Sethu Sundar Pethaiah 1,*, Kishor Kumar Sadasivuni 2,* , Arunkumar Jayakumar 3 , Deepalekshmi Ponnamma 2 , Chandra Sekhar Tiwary 4 and Gangadharan Sasikumar 5 1 Gashubin Engineering Pte Ltd., 8 New Industrial Road, Singapore 536200, Singapore 2 Center for Advanced Materials, Qatar University, P.O. Box 2713, Doha 2713, Qatar; [email protected] 3 SRM Institute of Science and Technology, SRM Nagar, Kattankulathur 603203, India; [email protected] 4 Materials Science and Engineering, Indian Institute of Technology, Gandhinagar, Gujarat 38235, India; [email protected] 5 Sustainable Solutionz, Chennai 600017, India; [email protected] * Correspondence: [email protected] (S.S.P.); [email protected] (K.K.S.); Tel.: +65-68443430 (S.S.P.); Fax: +65-62889803 (S.S.P.) Received: 3 September 2020; Accepted: 3 November 2020; Published: 11 November 2020 Abstract: Hydrogen (H2) has attained significant benefits as an energy carrier due to its gross calorific value (GCV) and inherently clean operation. Thus, hydrogen as a fuel can lead to global sustainability. Conventional H2 production is predominantly through fossil fuels, and electrolysis is now identified to be most promising for H2 generation. This review describes the recent state of the art and challenges on ultra-pure H2 production through methanol electrolysis that incorporate polymer electrolyte membrane (PEM). It also discusses about the methanol electrochemical reforming catalysts as well as the impact of this process via PEM. The efficiency of H2 production depends on the different components of the PEM fuel cells, which are bipolar plates, current collector, and membrane electrode assembly. -
Hydrogen Production Via Aqueous-Phase Reforming for High
Open Research Europe Open Research Europe 2021, 1:81 Last updated: 23 SEP 2021 REVIEW Hydrogen production via aqueous-phase reforming for high- temperature proton exchange membrane fuel cells - a review [version 1; peer review: 1 approved with reservations] Paranjeet Lakhtaria 1, Paulo Ribeirinha1, Werneri Huhtinen 2, Saara Viik2, José Sousa1,3, Adélio Mendes1 1LEPABE - Laboratory for Process Engineering, Environment, Biotechnology and Energy, Faculty of Engineering, University of Porto, Rua Dr. Roberto Frias, Porto, 4200-465, Portugal 2VTT Technical Research Center of Finland Ltd, Tietotie 4 C, P.O. Box 1000, FI-02044 VTT, Espoo, Finland 3Departamento de Química, Escola de Ciências da Vida e do Ambiente, Universidade de Trás-os-Montes e Alto Douro, Quinta de Prados, Vila Real, 5000-801, Portugal v1 First published: 20 Jul 2021, 1:81 Open Peer Review https://doi.org/10.12688/openreseurope.13812.1 Latest published: 20 Jul 2021, 1:81 https://doi.org/10.12688/openreseurope.13812.1 Reviewer Status Invited Reviewers Abstract Aqueous-phase reforming (APR) can convert methanol and other 1 oxygenated hydrocarbons to hydrogen and carbon dioxide at lower temperatures when compared with the corresponding gas phase version 1 process. APR favours the water-gas shift (WGS) reaction and inhibits 20 Jul 2021 report alkane formation; moreover, it is a simpler and more energy efficient process compared to gas-phase steam reforming. For example, Pt- 1. Adolfo Iulianelli, University of Calabria, based catalysts supported on alumina are typically selected for methanol APR, due to their high activity at temperatures of circa Rende, Italy 200°C. However, non-noble catalysts such as nickel (Ni) supported on Any reports and responses or comments on the metal-oxides or zeolites are being investigated with promising results in terms of catalytic activity and stability. -
Reformers for the Production of Hydrogen from Methanol and Alternative Fuels for Fuel Cell Powered Vehicles
Electrochemical Technology ANL-92/31 Program Electrochemical Technology Program Electrochemical Technology Program Electrochemical Technology Pronram Electrochemical Technology Reformers for the Production of Program Electrochemical Technology Hydrogen from Methanol and Program Electrochemical Technology Alternative Fuels for Program Fuel Cell Powered Vehicles Electrochemical Technology Program Electrochemical Technology Program by R. Kumar, S. Ahmed, Electrochemical Technology M. Krumpelt, and K. M. Myles Program Electrochemical Technology Program Electrochemical Technology Program Electrochemical Technology Program Electrochemical Technology Program Electrochemical Technology Program Electrochemical Technology Program Electrochemical Technology Program Argonne National Laboratory, Argonne, Illinois 60439 operated by The University of Chicago for the United States Department of Energy under Contract W-31-109-Eng-38 Chemical Technology Division Chemical Technology Division Chemical Technology Division Chemical Technology Division Chemical Technology Division Chemical Technology Division Chemical Technology Division Chemical Technology Division Argonne National Laboratory, with facilities in the states of Illinois and Idaho, is owned by the United States government, and operated by The University of Chicago under the provisions of a contract with the Department of Energy. DISCLAIMER- This report was prepared as an account of work sponsored by an agency of the United States Government. Neither the United States Government nor any agency -
Development of a Methanol Reformer for Fuel Cell Vehicles
Development of a methanol reformer for fuel cell vehicles Bård Lindström KTH-Kungliga Tekniska Högskolan Department of Chemical Engineering and Technology Chemical Technology Stockholm 2003 PhD Thesis TRITA-KET R172 ISSN 1104-3466 ISRN KTH/KET/R-172-SE ISBN 91-7283-406-4 To Amanda and my parents Abstract Vehicles powered by fuel cells are from an environmental aspect superior to the traditional automobile using internal combustion of gasoline. Power systems which are based upon fuel cell technology require hydrogen for operation. The ideal fuel cell vehicle would operate on pure hydrogen stored on-board. However, storing hydrogen on-board the vehicle is currently not feasible for technical reasons. The hydrogen can be generated on-board using a liquid hydrogen carrier such as methanol and gasoline. The objective of the work presented in this thesis was to develop a catalytic hydrogen generator for automotive applications using methanol as the hydrogen carrier. The first part of this work gives an introduction to the field of methanol reforming and the properties of a fuel cell based power system. Paper I reviews the catalytic materials and processes available for producing hydrogen from methanol. The second part of this thesis consists of an experimental investigation of the influence of the catalyst composition, materials and process parameters on the activity and selectivity for the production of hydrogen from methanol. In Papers II-IV the influence of the support, carrier and operational parameters is studied. In Paper V an investigation of the catalytic properties is performed in an attempt to correlate material properties with performance of different catalysts. -
Development of an Integrated Catalytic Methanol Reformer
DEVELOPMENT OF AN INTEGRATED CATALYTIC METHANOL REFORMER ETSU F/02/00060/REP Contractor C J B Developments Ltd Prepared by R A J Dams S C Moore P Hayter M Verhaak The work described in this report was carried out under contract as part of the New and Renewable Energy Programme, managed bythe Energy Technology Support Unit (ETSU) on behalf of the Department of Trade and Industry. The views and judgements expressed in this report are those of the contractor and do not necessarily reflect those of ETSU or the Department of Trade and Industry. First published 1996 CONTENTS 1. EXECUTIVE SUMMARY 1 2. BACKGROUND 2 3. OBJECTIVES 4 4. CATALYST DEVELOPMENT 4 5. BENCH-SCALE REFORMER CONSTRUCTION AND OPERATION 6 6. EVALUATION OF RESULTS 10 7. CONCLUSIONS 10 8. RECOMMENDATIONS 11 Figure 1 Figure 2 Table 1 1. EXECUTIVE SUMMARY As part of a successful collaboration with Vickers Shipbuilding and Engineering Limited (VSEL), CJB Developments Limited (CJBD) developed a methanol reformer to supply hydrogen-rich gas for a Solid Polymer Fuel Cell (SPFC) power system with an output of 10kW. The methanol reformer used a packed bed pelleted proprietary catalyst. The endothermic heat of reaction was supplied by combusting the fuel cell off-gases. Although the reformer performed successfully in terms of the objectives of the breadboard power system, it was clear that for an on-board fuel cell vehicle application the start-up time and response to transient changes in load was not adequate. Consequently, CJBD investigated different forms of construction of reformer and as a result formed a collaboration with ECN of the Netherlands and VSEL to develop, in the longer term, an all metal methanol reformer using metal substrates coated with both reforming and combustion catalysts. -
Imm Compact Methanol Reformer
1 Utilization of methanol as hydro- gen supply for fuel cells - sustainable IMM COMPACT METHANOL and compact 2 IMM compact methanol steam REFORMER – HYDROGEN SUPPLY reformer produces enough hydrogen to power a 6.5 kW fuel cell FOR MOBILITY Mobile fuel cell applications require compact Fraunhofer Institute for and simple hydrogen supply considering also Catalyst coated reformer Micro engineering and the still limited availability of compressed Microsystems IMM hydrogen. For many portable and mobile IMM has developed a highly compact applications, methanol is a viable alternative methanol reformer which has several Carl-Zeiss-Strasse 18-20 to compressed hydrogen owing to its higher advantages compared to conventional 55129 Mainz | Germany power density and easy transportation. technology, which originate from our Methanol can be produced from renewable unique catalyst and reactor technology: Contact sources, but also from carbon dioxide from industrial processes such as cement fabrica- Robust catalyst, no pre-treatment Prof. Dr. Gunther Kolb tion or even from the atmosphere. necessary, no performance drop after Phone: +49 6131 990-341 Its conversion to hydrogen (named refor- longer shut-down. [email protected] ming) is easiest compared to many other Higher activity compared to conventio- alcohol or hydrocarbon fuels, which require nal technology allows minimum catalyst www.imm.fraunhofer.de much higher operating temperature of the demand (and cost). reforming process. Catalyst coating similar to automotive The hydrogen content of reformed me- exhaust cleaning reduces catalyst thanol (reformate) is with 75 % (dry basis) demand further. highest of all fuels. Stable catalyst operation at partial load The reformate is then fed to a fuel cell allows system modulation.