Rail Accident Report
Total Page:16
File Type:pdf, Size:1020Kb
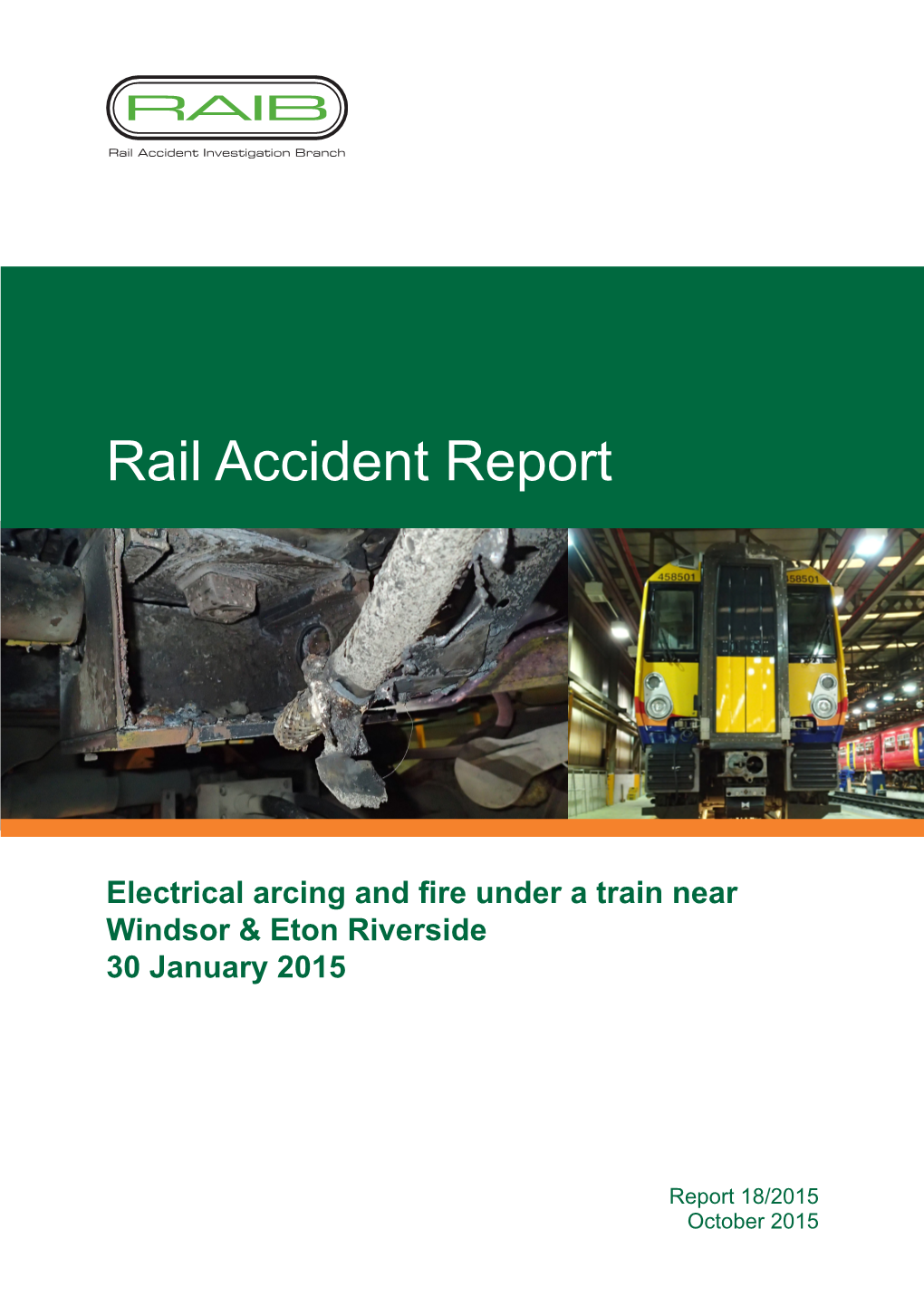
Load more
Recommended publications
-
Analysis of Electric Shoegear Dynamics 1P. F. Weston, E. Stewart
Analysis of Electric Shoegear Dynamics 1P. F. Weston, E. Stewart, C. Roberts, and S. Hillmansen The Birmingham Centre for Rail Research and Education, Department of Electronic, Electrical and Computer Engineering, The University of Birmingham, Birmingham, UK1 Abstract The mechanical interface between vehicle-mounted shoegear and the third rail is critically important to the smooth running of electrically powered railway vehicles. Research is being carried out into the static and dynamic interactions between shoegear and the third rail. This paper describes the instrumentation being developed for the shoegear of a class 375 railway vehicle in the UK. Introduction Many electrically powered railway vehicles operating in the UK pick up traction current from a third rail in parallel to the running rails. The interface between the vehicle-mounted shoegear and this third rail is critically important. Network Rail provides and maintains the conductor rail and associated lineside equipment, while train operating companies are responsible for the shoegear. The geometry and range of contact forces allowed between the shoegear and third rail are defined by standards that have evolved over many years of experience. In recent years however, a review of the shoegear and third rail standards in the UK has been initiated. This has been prompted by a) reported increase in the incidents of lost or damaged shoes, and b) anecdotal evidence that different shoegear designs perform differently in the presence of ice on the third rail. The contribution of the current research to this review is to design instrumentation to measure geometry, forces, and the dynamic response of the shoegear on the third rail. -
Method and Apparatus for Controlling Trains by Determining a Direction Taken by a Train Through a Railroad Switch
Europäisches Patentamt *EP001086874A1* (19) European Patent Office Office européen des brevets (11) EP 1 086 874 A1 (12) EUROPEAN PATENT APPLICATION (43) Date of publication: (51) Int Cl.7: B61L 3/06 28.03.2001 Bulletin 2001/13 (21) Application number: 99118757.6 (22) Date of filing: 23.09.1999 (84) Designated Contracting States: • Hungate, Joe B. AT BE CH CY DE DK ES FI FR GB GR IE IT LI LU Marion, IA 52302 (US) MC NL PT SE • Montgomery, Stephen R. Designated Extension States: Marion, IA 52302 (US) AL LT LV MK RO SI (74) Representative: Petri, Stellan et al (71) Applicant: WESTINGHOUSE AIR BRAKE Ström & Gulliksson AB COMPANY Box 41 88 Wilmerding, PA 15148 (US) 203 13 Malmö (SE) (72) Inventors: • Halvorson, David H. Cedar Rapids, IA 52405 (US) (54) Method and apparatus for controlling trains by determining a direction taken by a train through a railroad switch (57) An apparatus for determining the presence of are shown which are disposed on opposite sides of the a third rail disposed between parallel railroad tracks as rail vehicle. The radar detectors are coupled with an on- a train progresses along said parallel railroad tracks and board computing device and with other components of further for determining the relative direction of motion of an advanced train control system which can be used for said third rail with respect to said first two rails and fur- precisely locating the train on closely spaced parallel ther for determining the rate at which the third rail moves tracks and further for updating and augmenting position with respect to the first rails is disclosed, which is a low information used by the advanced train control system. -
Guidelines for Railroad Safety
Safety Bulletin #28 Railroads INDUSTRY WIDE LABOR-MANAGEMENT SAFETY COMMITTEE SAFETY BULLETIN #28 GUIDELINES FOR RAILROAD SAFETY These guidelines are recommendations for safely engaging in rail work, i.e., working onboard trains, in railroad yards, subways and elevated systems, or in the vicinity of railroad equipment. Railroads are private property requiring the railroad’s authorization to enter. Once authorization is given, everyone on scene must follow the railroad’s safety procedures to reduce hazards. There are strict rules governing rail work. These rules must be communicated to and followed by all cast and crew. Check with the Authority Having Jurisdiction (AHJ) and with the owner/operator for local regulations, specific guidelines, and required training. Additionally, each railroad property or transportation agency may have its own rules and training requirements. In many cases, everyone must receive training. PRIOR TO THE START OF RAIL WORK Prior to starting rail work, the Production, in conjunction with the railroad representative, will conduct a safety meeting with all involved personnel to acquaint cast and crew members with possible workplace risks. Consult with the appropriate Department Heads to determine if equipment, such as lighting, grip equipment, props, set dressing, electric generators or other equipment will be used. When using these items, ensure that they are properly secured and their use has been authorized by the railroad representative. Plan proper ventilation and exhaust when using electric generators. Electrical bonding may be necessary. Ensure conditions and weight loads of the work area and adjacent roads used for camera cars, camera cranes, horses, etc. are adequate for the intended work. -
Gauge-And-Scale.Pdf
GAUGE and SCALE FOR TOY AND MODEL TRAINS fredlub |SNCF231E | 11 maart 2019 1 Content 1 Content ........................................................................................................................... 2 2 Introduction.................................................................................................................... 4 3 Gauge and Scale explained............................................................................................. 6 What is Gauge ........................................................................................................................................... 6 Real trains ............................................................................................................................................. 6 Toy and model trains ............................................................................................................................ 6 The name of the gauge .......................................................................................................................... 7 A third rail? ........................................................................................................................................... 8 Monorail ................................................................................................................................................ 9 What is Scale ............................................................................................................................................. 9 Toy-like -
TN-11 Curvature and Rolling Stock
RP‐11 Curvature and Rolling Stock NMRA Technical Note TN‐11 Alex Schneider April 9, 2017 NMRA RP 11 Curvature and Rolling Stock Technical Note This Recommended Practice was published to coordinate the expectations of modelers with the capabilities of model manufacturers concerning the minimum radius that could be negotiated by various “classes” of equipment. In order to build a model railroad layout in the space available, curve radii must be reduced by much more than the scale factor of the scale selected, such as 1 to 87.1 for HO scale. However such reduction in radius can be achieved only by compromising some of the aspects of the prototype which limit track curvature. The values shown below reflect a judgment of the trade‐off between practical space requirements and the need to accommodate greater truck rotation and coupler swing by adjusting or eliminating underbody detail. Modelers pick up this RP to answer two basic questions: Equipment purchase: can a specific locomotive or car run on the minimum radius of my home or club layout? Layout design: what radius should I design to accommodate a type of locomotives or cars I intend to run, even if I have not yet purchased them? The tightest railroad curves built by the prototype were on streetcar lines, then somewhat broader on interurban and narrow gauge lines. Short four wheel cars were the most forgiving of tight curves and rigid frame locomotives, primarily steam, were the least. RP‐11 was last changed in 1992. The changes in this edition were driven by a need to offer specific recommendations for the most common sizes of HO sectional track, and to make the steps between classes narrower. -
Nvent Rail Heating System
Rail Heating Systems Ensuring safe, reliable operations with solutions that prevent ice buildup on critical rail infrastructure Innovative heating solutions from nVent allow for safe, reliable railway operations in harsh winter conditions. Snow and ice buildup on track poses a major operational challenge that can cause serious disruptions to rail service and adversely impact safety. nVent is an integral supplier of heating systems to freight and transit railroads, providing solutions that prevent costly delays and service disruptions during the winter. This offering brings together core nVent capabilities including the industrial heating expertise of nVent RAYCHEM and the extensive railway industry experience of nVent ERICO. Our comprehensive offering includes heating solutions for switches, contact rail (third rail), and overhead catenary wire. In addition, nVent offers heating system control solutions that allow for remote or on-site operation. We offer full system design with a wide range of options and configurations to provide heating solutions that meet the specific needs of a given site. When it comes to safe, reliable rail operations in challenging winter conditions, trust nVent. WE CONNECT AND PROTECT. SWITCH HEATING CONTACT RAIL HEATING CATENARY HEATING nVent.com | 3 Switch Heating Railway switches are mission critical to railway safety. Railway switches are a critical part of safe, reliable railway operations. During the winter months, snow and ice buildup on track can prevent switches from properly aligning and locking into place. With innovative nVent RAYCHEM heating cable technology along with the rail industry expertise and high quality components of nVent ERICO, nVent offers the following types of switch heating systems; • The nVent Self-Regulating Switch Heating System is an innovative solution that automatically adjusts power output to compensate for temperature changes, delivering the exact amount of power required to keep tracks clear. -
Reviews with Bob Keller and the CTT Staff
reviews With Bob Keller and the CTT Staff Product reviews in Classic Toy Trains magazine Inclusive from Fall 1987 through December 2010 issue Manufacturer Issue Product and reviewer 3rd Rail Jan 94 O gauge brass Pennsylvania RR S2 6-8-6 Turbine by 3rd Rail – Dick Christianson 3rd Rail May 94 O gauge brass Pennsylvania RR 2-10-0 by 3rd Rail – Tom Rollo 3rd Rail Jan 96 Update on review of O gauge S2 6-8-6 Turbine by 3rd Rail – Marty McGuirk 3rd Rail May 96 O gauge brass Union Pacific 4-8-8-4 Big Boy by 3rd Rail – Marty McGuirk 3rd Rail Sep 97 O gauge brass Union Pacific 4-6-6-4 Challenger by 3rd Rail – Bob Keller 3rd Rail Jan 98 O gauge brass Pennsylvania RR 2-10-4 by 3rd Rail – Bob Keller 3rd Rail Nov 98 O gauge brass Pennsylvania RR Q2 4-4-6-4 by 3rd Rail – Bob Keller 3rd Rail Jan 99 O gauge Santa Fe Dash 8 by 3rd Rail – Bob Keller 3rd Rail Mar 99 O gauge Southern Pacific 4-8-8-2 cab-forward by 3rd Rail – Bob Keller 3rd Rail Nov 99 O gauge Pennsylvania RR S1 6-4-4-6 by 3rd Rail – Bob Keller 3rd Rail Sep 00 CTT Online review: Pennsylvania RR 2-10-2 – Bob Keller 3rd Rail Jul 01 O gauge brass UP & SP 2-8-0s by 3rd Rail – Bob Keller 3rd Rail Jan 02 O gauge brass Erie 0-8-8-0 by 3rd Rail – Bob Keller 3rd Rail Jul 02 O gauge brass Union Pacific 4-6-6-4 Challenger by 3rd Rail – Bob Keller 3rd Rail Oct 02 O gauge die-cast metal NYC Mercury 4-6-2 Pacific by 3rd Rail – Bob Keller 3rd Rail Nov 02 O gauge brass NYC 4-8-4 Northern by 3rd Rail – Bob Keller 3rd Rail May 04 O gauge brass Pennsylvania RR Q1 4-6-4-4 locomotives – Bob Keller 3rd Rail July 08 O gauge brass C&O 4-8-4 by Third Rail – Bob Keller Academy Models Dec 02 1:48 scale tanks by Academy Models – Bob Keller Ace Trains Sep 00 O gauge 4-4-4T and car set by Ace Trains – Neil Besougloff Ace Trains Jan 01 Southern (UK) Ry. -
Stray Current Corrosion in Electrified Rail Systems -- Final Report
Stray Current Corrosion in Electrified Rail Systems -- Final Report Dr. Thomas J. Barlo, formerly of Northwestern University Dr. Alan D. Zdunek May 1995 _______________________________________________________________________ Contents • List of Tables and Figures • Executive Summary • Introduction • Objectives and Approach • Literature Review • Transit Operator Interviews • Discussion • Conclusions • Recommendations • Acknowledgement • References _______________________________________________________________________ EXECUTIVE SUMMARY Despite a relatively mature technology for its control, corrosion caused by stray current from electrified rapid-transit systems costs the United States approximately $500 million annually. Part of that cost is the result of corrosion of the electrified rapid-transit system itself, and part is the result of corrosion on neighboring infrastructure components, such as buried pipelines and cables. Detailed costs to either the transit systems or the neighboring infrastructure are not available, and, therefore, this limited study was undertaken for the Infrastructure Technology Institute (1) to assess the scope of stray-current corrosion on the electrified-rail systems based upon information in the literature and from interviews with selected transit-system operators, and (2) to determine whether new or additional corrosion monitoring or mitigation techniques are needed. The literature review was conducted through the Infrastructure Technology Institute Library Services Program, the Transportation Library, and -
Electrification and the Chicago, Milwaukee & St. Paul Railroad
University of Missouri, St. Louis IRL @ UMSL Theses Graduate Works 11-20-2009 Unfulfilled Promise: Electrification and the Chicago, Milwaukee & St. Paul Railroad Adam T. Michalski University of Missouri-St. Louis, [email protected] Follow this and additional works at: http://irl.umsl.edu/thesis Recommended Citation Michalski, Adam T., "Unfulfilled Promise: Electrification and the Chicago, Milwaukee & St. Paul Railroad" (2009). Theses. 181. http://irl.umsl.edu/thesis/181 This Thesis is brought to you for free and open access by the Graduate Works at IRL @ UMSL. It has been accepted for inclusion in Theses by an authorized administrator of IRL @ UMSL. For more information, please contact [email protected]. Unfulfilled Promise: Electrification and the Chicago, Milwaukee & St. Paul Railroad by Adam T. Michalski B. S., Urban Studies, University of Minnesota, Twin Cities, 2004 A Thesis Submitted to the Graduate School of the University of Missouri – St. Louis In partial Fulfillment of the Requirements for the Degree Master of Arts in History December 2009 Advisory Committee Carlos A. Schwantes, Ph. D. Chairperson Daniel L. Rust, Ph. D. Kevin J. Fernlund, Ph. D. Michalski Adam, 2009, UMSL, p. ii Copyright © 2009 by Adam T. Michalski All Rights Reserved Michalski Adam, 2009, UMSL, p. iii CONTENTS LIST OF ABBREVIATIONS iv GLOSSARY v Chapter 1. INTRODUCTION 1 2. THE PROMISE OF ELECTRICITY IN EVERYDAY LIFE 5 3. EARLY ELECTRIFICATION OF STEAM RAILROADS 26 4. THE MILWAUKEE ELECTRIFICATION 50 5. THE MILWAUKEE ELECTRIFICATION’S BENEFITS AND DRAWBACKS -
Chapter 3 Adoption of Project Plan 3.1 Route Selection
Chapter 3 Adoption of Project Plan 3.1 Route selection 3.1.1 Basic issues in the route selection Study Team has adopted line profiles to reflect the existing roads so that land acquisition for railway construction is minimized as far as possible. A prerequisite is to guarantee the convenience of users and create pedestrian spaces at the nods between roads and railway stations. Study Team has formed construction plans around stations to facilitate smooth transfer between different traffic modes. In regard to the structure style, Study Team proposed a plan that paid attention to the landscapes that match with the development of Hanoi city in the future and those to cut the total cost including the cost for construction and maintenance of facilities. Therefore, it is proposed that the route selection will be the one to facilitate project promotion from the viewpoints of cost and implementation of construction work and yield various merits from an early stage. In view of the fact that the line passes the city center, Study Team will construct stations at the crossing points with other transport modes to establish railway network and ensure the convenience of users, while limiting the station-to-station distance to 1,500 m or less in the midtown area. The location of stations in suburban areas will be determined in consideration of land utilization plans and natural conditions. To cut the travel time and maintenance cost, Study Team guarantees as appropriate line profiles as possible avoiding level crossings and minimizes curved sections, thereby aiming at raising the security level of train operation and rapidity between the city center and suburban areas to be connected in about 30 minutes. -
Investigation Into the Computational Techniques of Power System Modelling for a DC Railway
Computers in Railways X 735 Investigation into the computational techniques of power system modelling for a DC railway A. Finlayson1, C. J. Goodman2 & R. D. White1 1Atkins Rail, UK 2University of Birmingham, UK Abstract The use of computer simulation techniques is now a fundamental part of the design process for electrified railways and at the feasibility stage clients will often request detailed calculations to be performed for the basic design. This will establish a level of confidence in both the project and basic design parameters that will justify the capital expenditure further on in the project life-cycle. This paper will address how the total impedance of a railway network may be represented, where the impedances of the traction return circuit and traction power system are either combined together to form one impedance or studied independent of one another. The accuracy of the modelling in this manner, particularly how it affects the accuracy of rail voltage results shall be assessed. It will also examine how much impedance is typically in the rails and what proportion this needs to be before it has an unacceptable effect on the numerical results. To assess this, a range of proportions will be studied, for example 70% of the total impedance to be modelled in the conductor with 30% modelled in the rails, 60%/40%, etc. In this way, a proper scientific assessment of the combined or split calculation methods can be made via simplified case studies. Keywords: DC railway, modelling, simulation, computational techniques, accuracy, numerical method, rail voltage, stray current. 1 Introduction DC electrified railway systems across the world are growing, both in passenger and freight traffic, as an alternative solution to increasing road congestion. -
Railway Electrification Systems & Engineering
First Edition, 2012 ISBN 978-81-323-4395-0 © All rights reserved. Published by: White Word Publications 4735/22 Prakashdeep Bldg, Ansari Road, Darya Ganj, Delhi - 110002 Email: [email protected] Table of Contents Chapter 1 - Railway Electrification System Chapter 2 - Traction Power Network Chapter 3 - Railway Electric Traction Chapter 4 - Electric Locomotive Chapter 5 - Pantograph (Rail) Chapter 6 - Electric Multiple Unit Chapter 7 - Trolley Pole Chapter 8 - Third Rail Chapter 9 - Overhead Lines Chapter 10 - Ground-Level Power Supply Chapter 1 Railway Electrification System Electric locomotives under the wires in Sweden Overhead wire and catenary in Bridgeport, Connecticut, United States A railway electrification system supplies electrical energy to railway locomotives and multiple units so that they can operate without having an on-board prime mover. There are several different electrification systems in use throughout the world. Railway electrification has many advantages but requires significant capital expenditure for installation. Characteristics of electric traction The main advantage of electric traction is a higher power-to-weight ratio than forms of traction such as diesel or steam that generate power on board. Electricity enables faster acceleration and higher tractive effort on steep gradients. On locomotives equipped with regenerative brakes, descending gradients require very little use of air brakes as the locomotive's traction motors become generators sending current back into the supply system and/or on-board resistors, which convert the excess energy to heat. Other advantages include the lack of exhaust fumes at point of use, less noise and lower maintenance requirements of the traction units. Given sufficient traffic density, electric trains produce fewer carbon emissions than diesel trains, especially in countries where electricity comes primarily from non-fossil sources.