Residue STEAM
Total Page:16
File Type:pdf, Size:1020Kb
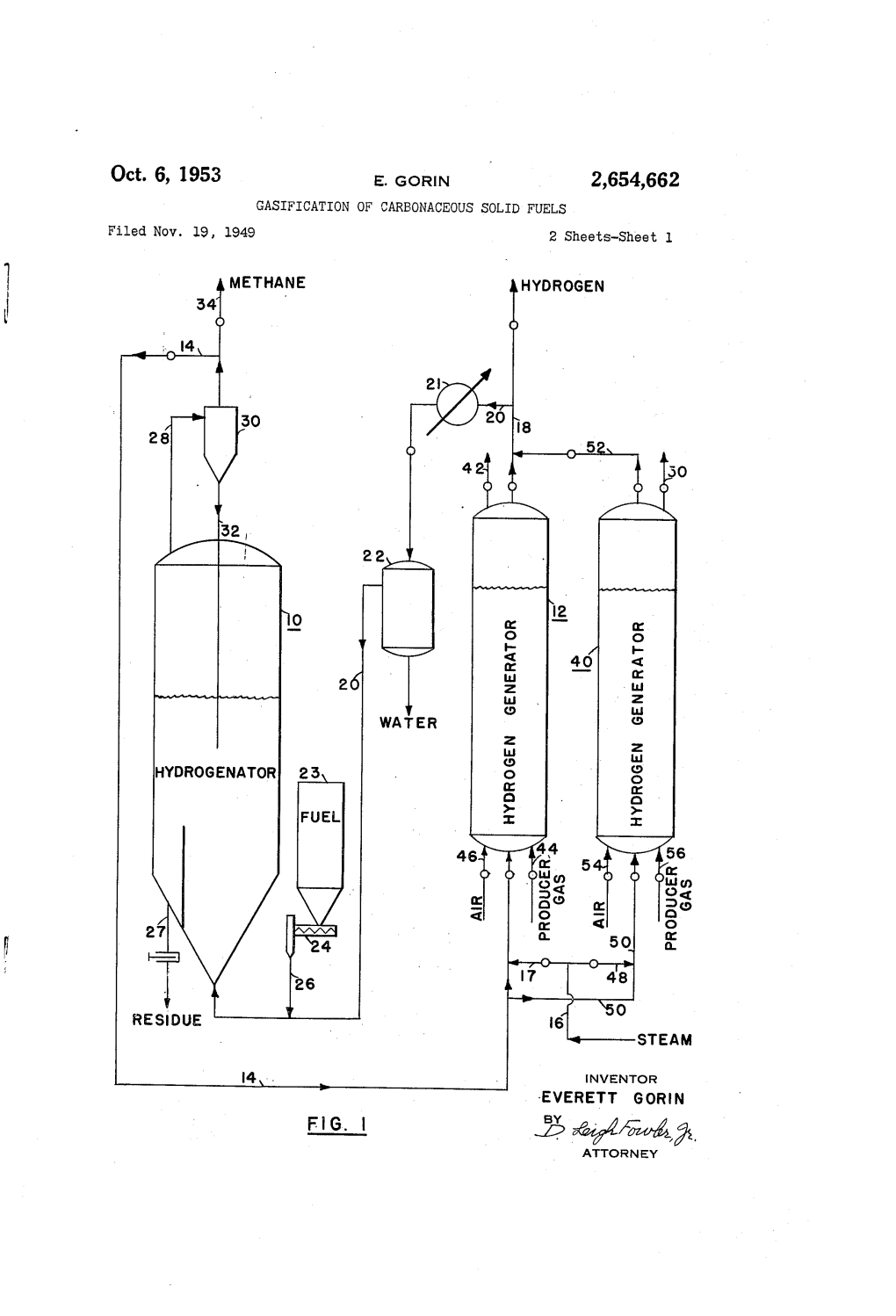
Load more
Recommended publications
-
Unit 3 Types of Fuels and Their Characteristics
Types of Fuels and UNIT 3 TYPES OF FUELS AND THEIR their Characteristics CHARACTERISTICS Structure 3.1 Introduction Objectives 3.2 Principles of Classification of Fuels 3.3 Solid Fuels and their Characteristics 3.3.1 Woods and their Characteristics 3.3.2 Coals and their Characteristics 3.3.3 Manufactured Solid Fuels and their Characteristics 3.4 Liquid Fuels and their Characteristics 3.4.1 Petroleum and its Characteristics 3.4.2 Manufactured Liquid Fuels and their Characteristics 3.5 Gaseous Fuels and their Characteristics 3.5.1 Natural Gas and its Characteristics 3.5.2 Manufactured Gases and their Characteristics 3.6 Summary 3.7 Key Words 3.8 Answers to SAQs 3.1 INTRODUCTION Fuel is a substance which, when burnt, i.e. on coming in contact and reacting with oxygen or air, produces heat. Thus, the substances classified as fuel must necessarily contain one or several of the combustible elements : carbon, hydrogen, sulphur, etc. In the process of combustion, the chemical energy of fuel is converted into heat energy. To utilize the energy of fuel in most usable form, it is required to transform the fuel from its one state to another, i.e. from solid to liquid or gaseous state, liquid to gaseous state, or from its chemical energy to some other form of energy via single or many stages. In this way, the energy of fuels can be utilized more effectively and efficiently for various purposes. Objectives After studying this unit, you should be able to • describe the classification of fuels, • explain the various types of fuels and their characteristics, and • know their applications in various fields. -
Solid Fuels and Firelighting Products
Nordic Ecolabelling of Solid fuels and firelighting products Version 3.2 • 06 March 2017 - 31 March 2024 Nordic Ecolabelling Content What is a Nordic Swan Ecolabelled solid fuel or firelighting product? 4 Why choose The Nordic Swan Ecolabel? 4 What can carry The Nordic Swan Ecolabel? 4 How to apply 5 1 Production and product description 6 2 Resources 6 2.1 Wood 8 2.2 Solid and liquid renewable raw materials other than wood in barbecue charcoal/briquettes and firelighting products and the tree species (salix/poplar/hybrid asp) grown as energy forest on arable land 10 2.3 Requirements for working conditions in the production of barbeque charcoal/briquettes 11 2.4 Chemicals 12 3 Energy consumption 14 4 Use and quality requirements 16 5 Quality and official requirements 20 Regulations for the Nordic Ecolabelling of products 22 Follow-up inspections 22 History of the criteria 22 New criteria 22 Terms and definitions 23 Appendix 1 Description of the solid fuel, material composition and production Appendix 2 Definition, class and type of raw materials Appendix 3 Declaration of tree species not permitted to be used in Nordic Ecolabelled products Appendix 4 Traceability and verification of renewable raw materials in barbecue charcoal/-briquettes and firelighting products and the tree species (salix/poplar/hybrid asp) grown as energy forest on arable land Appendix 5 Declaration for chemical products used in the manufacture of solid fuels or firelighting products Appendix 6 Declaration for constituent substances in chemical products Appendix 7 Reference values for the energy content of fuels Appendix 8 Analysis and test laboratories Appendix 9 Declaration of compliance with quality specifications for firewood O87 Solid fuels and firelighting products, version 3.2, 26 January 2021 This document is a translation of an original in Danish. -
Outline of Solid Fuel Manufacturing
Technical Information Sheet 1. Name of technology Biomass Waste Fuel (BWF) Manufacturing Technology Complete recycling of waste oil (waste ink, waste paint, etc.) which has been considered difficult for recycling and simply incinerated. 2. Type of technology A patented original treatment system (Patent No. 5078628) to manufacture BWF as an alternative fuel to coal 3. Description of technology [Objective and application of technology] Our original treatment method and facilities enable waste oil, for which incineration has been the only treatment method, to be recycled to BWF with higher combustion efficiency than coal and thereby contributing to the reduction in environmental impact by accelerating the recycling of various kinds of waste. In particular, BWF for cement factories enables combustion residue from incineration plants and oil mud from oil-water separation plants to be fully recycled, provided that BWF is used in appropriate plants with facilities for burning general coal. In our BWF manufacturing process, we receive materials after carrying out preliminarily sample inspections for thoroughly confirming material composition (to eliminate substances with hazardous properties such as heavy metal contamination). Also, we treat the materials using a reliable safety management system including special fire prevention equipment such as a nitrogen generating devices and sprinklers with twice the capacity generally required. Outline of solid fuel manufacturing Animal and plant Combustion Waste oil Waste plastic Slag Smoke dust Tonner -
Form SFCT1 SOLID FUEL CARBON TAX (SFCT) RETURN & DECLARATION Supplier’S Name Tax Reference No
This form should only be used for accounting periods from 1 May 2021 to 30 April 2022 Form SFCT1 SOLID FUEL CARBON TAX (SFCT) RETURN & DECLARATION Supplier’s Name Tax Reference No. Address (include Eircode) Accounting Period From DDMMYYYY To DDMMYYYY (see Note 1) Part A Declaration of tax-free and fully relieved supplies of solid fuel (One tonne equals 1,000 kilograms) Coal Peat briquettes Milled peat Other peat Purpose of supply Tonnes (one Tonnes (one Tonnes (one Tonnes (one decimal place) decimal place) decimal place) decimal place Electricity generation (excluding CHP cogeneration) (see Notes 2 & 3) Use by a Greenhouse Gas Not (GHG) emissions permit Applicable holder (see Note 4) Use as a raw material (see Note 5) First supply outside the State Part B Summary of taxable supplies (including self-supplies) of solid fuel and tax payable (see Note 6) (One tonne equals 1,000 kilograms) Tonnes Rate Description of solid fuel Tax Payable (one decimal place) € / tonne Coal for use by a GHG emissions 4.18 € permit holder (see Note 4) 0 to <30% Biomass 88.23 € Coal (see Note 7) 30% to <50% Biomass 61.76 € Biomass 50% or over 44.12 € 0 to <30% Biomass 61.42 € Peat briquettes 30% to <50% Biomass 42.99 € (see Note 7) Biomass 50% or over 30.71 € Milled peat 30.44 € Other peat (see Note 8) 45.65 € Total Tax Payable € 1 RPC014952_EN_WB_L_1 This form should only be used for accounting periods from 1 May 2021 to 30 April 2022 Part C DECLARATION I declare, in accordance with the law* governing SFCT, that: • the details on page 1 of this form represent -
Combustion of Solid Fuels and Indoor Air Quality in Primarily Developing Countries
1791 Tullie Circle, NE. Atlanta, Georgia 30329-2305, USA www.ashrae.org ASHRAE Position Document on COMBUSTION OF SOLID FUELS AND INDOOR AIR QUALITY IN PRIMARILY DEVELOPING COUNTRIES Approved by ASHRAE Board of Directors October 3, 2016 Reaffirmed by ASHRAE Technology Council June 26, 2019 Expires June 26, 2022 ASHRAE S H A P I N G T O M O R R O W ’ S B U I L T E N V I R O N M E N T T O D A Y COMMITTEE ROSTER The ASHRAE Position Document on “Combustion of Solid Fuels and Indoor Air Quality in Primarily Developing Countries” was developed by the Society’s Combustion of Solid Fuels and Indoor Air Quality in Primarily Developing Countries Position Document Committee formed on September 16, 2013 with Paul Francisco as its chair. Paul W. Francisco, Chair Kirk R. Smith University of Illinois University of California Champaign, IL, USA Berkeley, CA, USA Jill Baumgartner Dean Still McGill University Aprovecho Research Center Montreal, QC, Canada Cottage Grove, OR, USA Chandra Sekhar National University of Singapore Singapore, Singapore Cognizant Committees The chairperson of Environmental Health Committee also served as ex-officio members. Zuraimi Sultan, Ex-Officio Cognizant Committee Chair Environmental Health Committee National Research Council Canada Ottawa, ON, Canada ii HISTORY of REVISION / REAFFIRMATION / WITHDRAWAL DATES The following summarizes the revision, reaffirmation or withdrawal dates 10/03/2016 —BOD approves Position Document titled Combustion of Solid Fuels and Indoor Air Quality in Primarily Developing Countries 6/26/2019—Technology Council approves reaffirmation of Position Document titled Combustion of Solid Fuels and Indoor Air Quality in Primarily Developing Countries Note: Technology Council and the cognizant committee recommend revision, reaffirmation or withdrawal every 30 months. -
Health Problems and Burning Indoor Fuels
American Thoracic Society PUBLIC HEALTH | INFORMATION SERIES Health Problems and Burning Indoor Fuels Household air pollution means that the quality of the air inside your home is not healthy. There are a number of things that can pollute the air indoors. A common source of indoor air pollution worldwide is the fuel used for cooking and heating. When these fuels are burned, the process can cause pollution inside the home, particularly if there is not good outdoor air exchange (ventilation). This fact sheet focuses on air pollution caused by burning fuels in the home. How does burning fuel cause pollution in the home? What lung problems can indoor pollution from Burning of fuels inside homes generates a complex mixture burning fuels cause? of indoor air pollutants. The key air pollutants include soot Household air pollution is harmful to people of all ages, and and other small particles (called particulate matter) that can may start having a harmful impact on lung function soon be breathed in and damage the lungs. Liquefied petroleum after birth or even before a baby is born. The most common gas, natural gas, ethanol, and electricity are considered clean lung problem from household air pollution in adults is chronic fuels, but not all clean fuels are equal. Some studies find that bronchitis, a type of chronic obstructive pulmonary disease cooking with gas stoves, particularly if they are unvented, (COPD). Regular exposure to indoor air pollution can increase may increase indoor levels of nitrogen dioxide, causing air the risk for asthma, tuberculosis, interstitial lung diseases, pollution. heart disease, and lung cancer. -
THE GUIDE to SOLID FUELS This Leaflet Will Tell You All You Need To
THE GUIDE TO SOLID FUELS This leaflet will tell you all you need to know about: • The different solid fuels available and their suitability for the various types of appliances • Smoke control legislation • Buying solid fuel • Hints on getting the best from your fuel and appliance Choice of Fuel There are a great many different solid fuels for sale. Your choice will be based on a number of criteria, the most important of which will be the type of appliance you will be burning the fuel on and whether or not you live in a smoke control area (see page 4). Fuels for open fires Housecoal The most traditional fuel for open fires is housecoal. It is available in various sizes e.g. Large Cobbles, Cobbles, Trebles and Doubles. The larger sizes are usually a little more expensive than Doubles size. Housecoal comes from mines in Britain and other parts of the world, most notably Columbia and Indonesia. The coal may be sold by the name of the colliery it comes from e.g. Daw Mill, the port of entry e.g. Merseyport or a merchant’s own brand name, e.g. Stirling. Coal merchants also frequently sell the coal by grade – 1, 2 and 3 or A, B and C; 1 and A being the best quality. Wood Wood and logs can be burnt on open fires. They should be well-seasoned and preferably have a low resin content. You should not use any wood that has any kind of coating on the surface e.g. varnish or paint, as harmful gases may be emitted on burning. -
AN ORDINANCE for ZONING for SOLID FUEL-FIRED HEATING DEVICES (Sfhds)
MPCA Model Ordinance for Minnesota Local Governments Solid Fuel-Fired Heating Devices February 2017 ZONING: NEW AND EXISTING SFHDS ALLOWED AN ORDINANCE FOR ZONING FOR SOLID FUEL-FIRED HEATING DEVICES (SFHDs) ADD I. IF YOUR COMMUNITY HAS, WILL ALLOW, PROHIBITS, OR WILL PROHIBIT SFHDs: I. ADMINISTRATIVE PROVISIONS A. PURPOSE. Model Community adopts the regulations in this ordinance controlling the use, installation and operation of outdoor wood or other solid fuel-fired heating devices (SFHDs) to achieve the following purposes: 1. Health. To protect citizens from environmental hazards and to safeguard community health. In particular, to protect the health of citizens from fine particles in emissions generated by SFHDs. The Clean Air Act (CAA) required the U.S. Environmental Protection Agency (EPA) to establish standards for particulate matter. EPA’s daily and annual fine particle National Ambient Air Quality Standards (NAAQS) were developed to protect the public from adverse health effects associated with exposure to fine particle pollution exposure. Sensitive populations protected by the CAA include persons who already have heart or lung diseases, children, and older adults. They experience serious health effects such as heart attacks, strokes, acute and chronic bronchitis, asthma episodes, reduced lung function, and other respiratory illnesses as a result of inhaling fine particle smoke which imbeds in their respiratory and circulatory systems. In addition to health effects, scientific studies show inhalation results in increased hospital and emergency room visits, lost work and school days, and in rare cases, premature death. 2. Fire safety. To protect citizens and structures from fire safety risks from SFHDs that are not properly installed, do not have proper safety equipment such as spark arresters, or are installed in close proximity to other buildings. -
Tracking Access to Nonsolid Fuel for Cooking 2014/8
1 TRACKING ACCESS TO NONSOLID FUEL FOR COOKING 2014/8 Supported by A KNOWLEDGE NOTE SERIES FOR THE ENERGY & EXTRACTIVES GLOBAL PRACTICE THE BOTTOM LINE Tracking Access to Nonsolid Fuel for Cooking Some 4.3 million deaths each year in the developing world To support the achievement of these goals, a starting point are traceable to household Why is this issue important? must be set, indicators developed, and a framework established to air pollution caused by the Traditional home cooking practices are a major health track those indicators until 2030. The World Bank and International inefficient use of solid fuels for risk across the developing world Energy Agency have led a consortium of 15 international agencies household cooking and other to produce data on access to nonsolid fuel for the SE4ALL Global purposes. Although 1.6 billion The World Health Organization estimates that in 2012 about 4.3 mil- Tracking Framework. Launched in 2013, the framework defines people gained access to lion deaths occurred because of exposure to household air pollution access to modern cooking solutions is as the use of nonsolid fuels nonsolid fuels between 1990 caused by smoke from the incomplete combustion of fuels such as for the primary method of cooking. Nonsolid fuels include (i) liquid and 2010, reliance on solid fuels wood, coal, and kerosene. Inefficient energy use in the home also fuels (for example, kerosene, ethanol, or other biofuels), (ii) gaseous expanded in Sub-Saharan Africa poses substantial risks to safety, causing burns and injuries across fuels (such as natural gas, LPG, and biogas), and (iii) electricity. -
WHO Indoor Air Quality Guidelines: Household Fuel Combustion
WHO IAQ Guidelines: household fuel combustion – Review 2: Emissions WHO Indoor Air Quality Guidelines: Household fuel Combustion Review 2: Emissions of Health-Damaging Pollutants from Household Stoves Convening lead author: Rufus Edwards1 Lead authors: Sunny Karnani1, Elizabeth M. Fisher2, Michael Johnson3, Luke Naeher4, Kirk R. Smith5, Lidia Morawska6 Affiliations: 1Department of Epidemiology, School of Medicine, University of California, Irvine, USA 2Department Mechanical and Aerospace Engineering, School of Mechanical and Aerospace Engineering, Cornell University, New York State, USA 3Berkeley Air Monitoring Group, School of Public Health, University of California - Berkeley, CA 4Environmental Health Sciences, College of Public Health, University of Georgia, USA 5Environmental Health Sciences, School of Public Health, University of California - Berkeley, CA, USA 6International Laboratory for Air Quality and Health, School of Chemistry, Physics and Mechanical Engineering, Queensland University of Technology Brisbane, Australia Convening lead author: that author who led the planning and scope of the review, and managed the process of working with other lead authors and contributing authors, and ensuring that all external peer review comments were responded to. Lead authors: those authors who contributed to one or more parts of the full review, and reviewed and commented on the entire review at various stages. Disclaimer: The work presented in this technical paper for the WHO indoor air quality guidelines: household fuel combustion has been carried out by the listed authors, in accordance with the procedures for evidence review meeting the requirements of the Guidelines Review Committee of the World Health Organization. Full details of these procedures are described in the Guidelines, available at: http://www.who.int/indoorair/guidelines/hhfc ; these include declarations by the authors that they have no actual or potential competing financial interests. -
Public Consultation on the Development of New Solid Fuel Regulations for Ireland Summary of Responses
Public Consultation on the Development of New Solid Fuel Regulations for Ireland Summary of Responses April 2021 Table of Contents Table of Contents ..................................................................................................................... i 1 Introduction ....................................................................................................................... 3 2 Public Consultation Summary .......................................................................................... 4 3 Overall Summary .............................................................................................................. 6 3.1 Q1: Are you in favour of a national regulation on solid fuels, and if so, why? .......... 7 3.2 Q2 - What additional solid fuels should be subject to regulation, and why? ............ 9 3.3 Q3 - What specifications or standards should/could be applied to each type of solid fuel? 10 3.4 Q4 - What do you believe are the most appropriate, implementable and enforceable regulatory approaches for each type of solid fuel? ......................................... 10 3.5 Q5 - How can a transition to less polluting fuels and more efficient heating systems be supported? (Building upon the measures already set out in the Climate Action Plan) . 11 3.6 Q6-8 Timelines ....................................................................................................... 13 3.6.1 Q6 - What do you think is an appropriate timeframe for the implementation of a national regulation of solid fuel? .................................................................................... -
Solid Fuel Booklet
LC102 FIRE SAFETY in Solid Fuel-Burning Systems A solid fuel safety reference guide Introduction RAM Mutual Insurance provides reinsurance for township mutual insurance companies. These locally-owned and References operated companies provide fire insurance to their NFPA 211 ~ Standard for Chimneys, Fireplaces, policyholders. RAM, since its beginning in 1931, has Vents, and Solid Fuel-Burning Systems (2016 Edition) worked very closely with these township mutuals in fire loss prevention. This booklet is presented in the hope that it will NFPA 921 ~ Guide for Fire and Explosion be helpful in preventing tragic fire losses. Investigations (2017 Edition) Be sure to check with your insurance company before HEATING WITH WOOD ~ Minnesota Department of purchasing or installing any solid fuel-burning system. Be Energy (excerpts and clip art reprinted with permission) aware that insurance policies may void coverage if the hazard is increased by an improperly installed solid WOOD HEAT SAFETY (Copyright 1979) by Jay W. fuel-burning system. Most insurance companies will Shelton, Garden Way Publishing, Charlotte, VT 05445 ~ require that these systems be inspected for fire insurance The Preferred Parallel Installation and Preferred Series underwriting purposes. Solid fuel-burning systems in Installation diagrams on pages 39, 40 and 41, particular can pose a greater fire hazard than the use of respectively, are reprinted with permission. conventional oil or gas heating appliances. A violation of any of the installation or safety requirements may lead to Paul B. Stegmeir ~ Fire Safety and Hearth Products the endangerment of lives and property. Consultant, Lecturer, Writer This publication is a fire insurance underwriting guide for the proper installation, operation, and maintenance of solid To simplify information, trade names have been used in this fuel-burning systems.