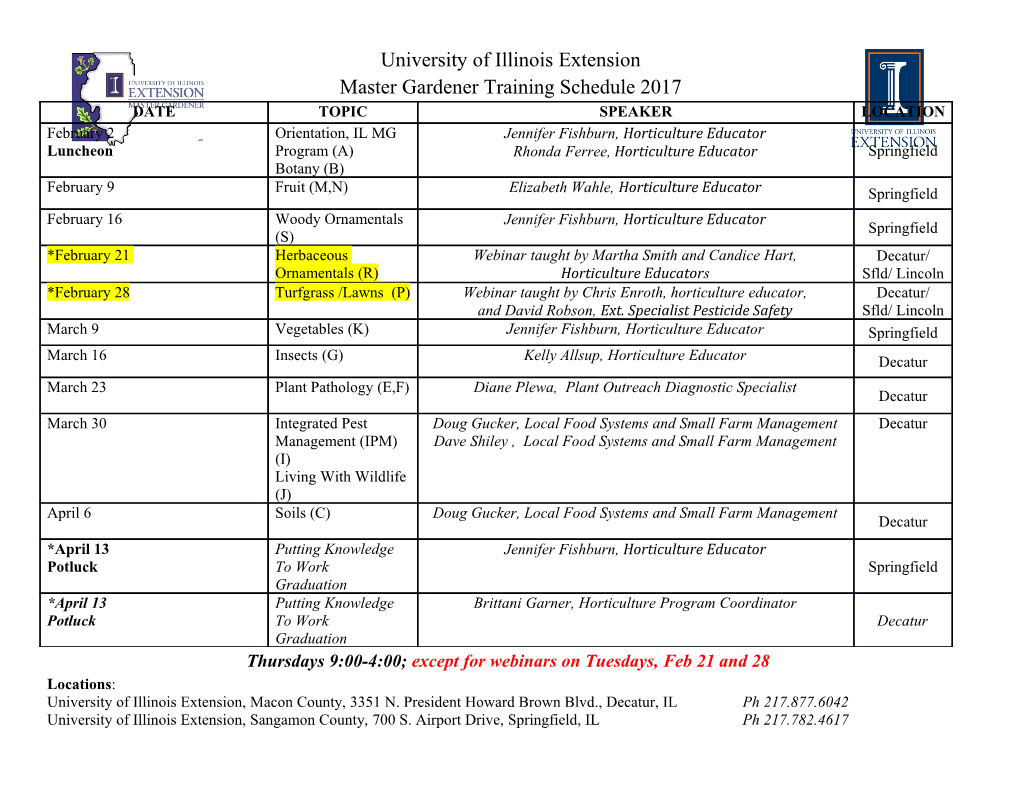
Oct. 6, 1953 E. GORIN 2,654,662 GASIFICATION OF CARBONACEOUS SOLID FUELS Filed Nov. l9, l949 2. Sheets-Sheet l METHANE HYDROGEN 34 4. N 156 REsidUE STEAM NVENTOr EVERETT GoRN ATTOrNY Oct. 6, 1953 E. GORN 2,654,662 GASFICATION OF CARBONACEOUS SOLID FUELS Filed Nov. 19, 1949 2. Sheets-Sheet 2 TO HYDROGEN GENERATOR HGH B.T. U. GAS HYDROGENATOR HYDROGEN RESIDUE were NVENOr STEAM EVERETT GORN S&4/rive.2.ATOrNEY Patented Oct. 6, 1953 2,654,662 UNITED STATES PATENT OFFICE 2,654,662 GASIFICATION OF CARBONACEOUS SOLD FUELS Everett Gorin, Castle Shannon, Pa., assignor to Pittsburgh Consolidation Coal Company, Pitts burgh, Pa., a corporation of Pennsylvania Applicatiora November 19, 1949, Serial No. 128,436 1. Claim. (C. 48-197) 2 This invention relates to the gasification of solid fuels to a gas containing primarily methane carbonaceous solid fuels, and particularly to the and/or hydrogen as desired. In one of the two production of hydrogen or high B. t. u. gas from vessels, a bed of carbonaceous Solid fuels in Such fuels. granular form is maintained, while in the In application Serial No. 99,562, filed June 16, other vessel a bed of granular barium oxide is 1949, a process for the gasification of car 5 confined. The temperature in the oxide vessel bonaceous solid fuels by reaction between steam must be between 1700 and 2300 F., while that and solid fuels in the presence of barium oxide in the solids fuel vessel must be at least 1400 F. is described. In accordance with that process, and preferably not above 1800 F. The pressures barium oxide is mixed with carbonaceous Solid in the two vessels, while preferably, but not fuels in certain critical proportions and under 10 necessarily the same, must at least equal and certain critical conditions of temperature and preferably exceed one atmosphere When the tem pressure and then subjected to reaction with perature in the oxide vessel is in the range 1700 steam. A gaseous product is obtained which to 2050 F., and when the temperature in the contains methane and hydrogen in varying rela oxide vessel is in the range 2050 to 2300 F., the tive proportions depending upon the particular 15 pressure must exceed that given by the empirical temperature and pressure conditions. As a re relation Sult of the reaction between the Steam and the carbonaceous Solid fuels, an inert solid residue (1) p=1--4.9X10-2 (t-2050) or ash is formed in admixture With the barium Oxide. In order to reuse the barium oxide which 20 where p is the minimum reaction pressure in at is converted to barium carbonate during the re mospheres and it is the temperature in the oxide action, it is necessary to separate the barium Wessel in F. oxide from the ash and regenerate it at elevated Steam and a gas containing methane are cir temperatures. While various means are avail culated through the vessel containing the barium able for separating this ash from the barium 25 oxide, and under the conditions of temperature oxide, it would be desirable to conduct the con and pressure recited, the methane is converted version of the carbonaceous Solid fuels to gas in to a gas containing a high percentage of hydro a system in which the Oxide and solid fuels are gen. The amount of barium oxide maintained not in admixture during the reaction, and yet in in the methane-steam reaction vessel must be which substantially all the benefits of the use of 30 Sufficient to absorb Substantially all of the Carbon the oxide in the process are secured, namely, high dioxide produced during the reaction in that ves yields of hydrogen or methane as desired and sel. Preferably, there are at least 800 parts by under Substantially thermoneutral conditions. Weight of barium oxide present for each 100 parts The primary object of this invention is to pro by weight of carbon contained in the gas circu vide an improved two-vessel System for convert 35 lating through the bed of barium oxide. ing carbonaceous Solid fuels into gas under Sub All or part of the hydrogen from the methane stantially thermoneutral conditions. Another Steam reaction Vessel (hereinafter sometimes re object of this invention is to provide a two-vessel ferred to as the hydrogen generator) is circu System for making a high B. t. u. fuel gas which 40 lated through the bed of carbonaceous solid fuels is rich in methane. A further object of the pres confined in the other vessel. Under the condi ent invention is to provide a two-vessel Systern tions of temperature and pressure existing in that for converting carbonaceous solid fuels into a gas vessel, the fuel is hydrogenated and a high Which is rich in hydrogen. Still another object B. t. u. gas containing methane in substantial of this invention is to provide a two-vessel SyS quantities is produced. If it is desired to pro tem for gasifying carbonaceous solid fuels in 45 duce only a high B. t. u. gas from the system, in which the gaseous products are substantially preference to substantially pure hydrogen, then free of carbon dioxide. part of the methane-containing gas is recycled to For a better understanding of my invention, the hydrogen generator for manufacturing hy reference should be had to the following descrip 50 drogen, all of which is then returned to the solid tion and to the accompanying drawings, in fuel hydrogenerator vessel. If it is desired to Which: produce hydrogen-rich gas, then only a part of Figure 1 is a diagrammatic illustration of an the hydrogen produced in the hydrogen genera apparatus comprising a two-vessel System tor is circulated to the hydrogenerator and all of adapted to carry out the preferred embodiment 55 tothe the methane hydrogen produced generator. in the latter is recycled of my invention; and AS stated above, the temperatures and pres Figure 2 is an illustration, partly diagrammatic sures of the two reaction zones do not necessarily and partly cross-sectional of a modified embodi have to be the same. But for practical reasons, ment of a portion of the system shown in Fig it is desirable to maintain the same pressure in ure 1. 60 both vessels. Preferably, the temperature in the In accordance with my invention, a two-vessel Solid fuel vessel is not higher than that in the system is employed to convert carbonaceous steam-methane reaction zone. It may be less but 2,654,662 4. 3. On the barium oxide or on an independent porous preferably not more than 200 F. lower. By op Support, i. e., Ni, Co, or Fe on a-alumina, Cu erating under these preferred temperature Con on silica, gel, etc. The barium oxide may be sup ditions the amount of recycled gas can be kept ported on a refractory basic oxide such as MgO at a minimum. The barium oxide employed in the hydrogen 5, to provide greater physical strength. generator is progressively converted to barium I have found that by operating the two vessels carbonate by the carbon dioxide produced. It in the above manner, either hydrogen or a high therefore is necessary to regenerate the oxide B. t. u. gas containing methane in substantial from the carbonate from time to time. This may quantities may be produced at will and under readily be done by separately heating the car- O conditions such that the overall process is exo bonate to its decomposition temperature in the thermic. In the barium oxide vessel heat is sup Same or different vessels. If the regeneration is plied for the endothermic steam-methane re effected in the same vessel, then it is necessary action by the exothermic reaction between the to operate a second vessel for carrying out the barium oxide and the carbon dioxide produced steam-methane reaction while the first vessel is 15 in the reaction. In the solid fuel vessel, the re on its regeneration cycle. Alternatively, the action between hydrogen and the fuel evolves carbonate 11ay be continuously withdrawn from heat. This desirable heat balance can readily the hydrogen generator and regenerated in a be achieved by recycling either methane or hydro separate vessel fron which it is continuously res. gen as the case may be. 20 In one of the embodiments of my new process, cycled to the generator. Eutilize the heat evolved in the solid fuel hydroge The reactions in the two zones may be carried later to preheat the steam which is circulated out using either fixed or fluidized beds. The use to the hydrogen generator. Thus a more than of fluidized beds is preferred when (1) the solid adequate Supply of heat is assured for the meth fuel used is a coking coal, and (2) it is desired ane steam reaction. to obtain precise temperature control in the oxide 25 In the following description of a specific em regeneration step. bodiment of my invention, by way of example The use of a fixed or moving bed is preferred Only, my new process is applied to the carbo when it is desired to obtain a niaximum con centration of hydrogen leaving the methiane naceous solid residue obtained by the low tem Steam Zone and a maximum concentration of 30 perature distillation or carbonization of hydro methane leaving the coal or char hydrogenation carbonaceous solid fuels, such as the high vola ZOne. This is not only desirable in Order to ob tile bituminous coal found in the Pittsburgh tain a higher purity product but also to minimize Sean.
Details
-
File Typepdf
-
Upload Time-
-
Content LanguagesEnglish
-
Upload UserAnonymous/Not logged-in
-
File Pages6 Page
-
File Size-