Design and Analysis of an Axial Fan Applicable for Kiln Shell Cooling
Total Page:16
File Type:pdf, Size:1020Kb
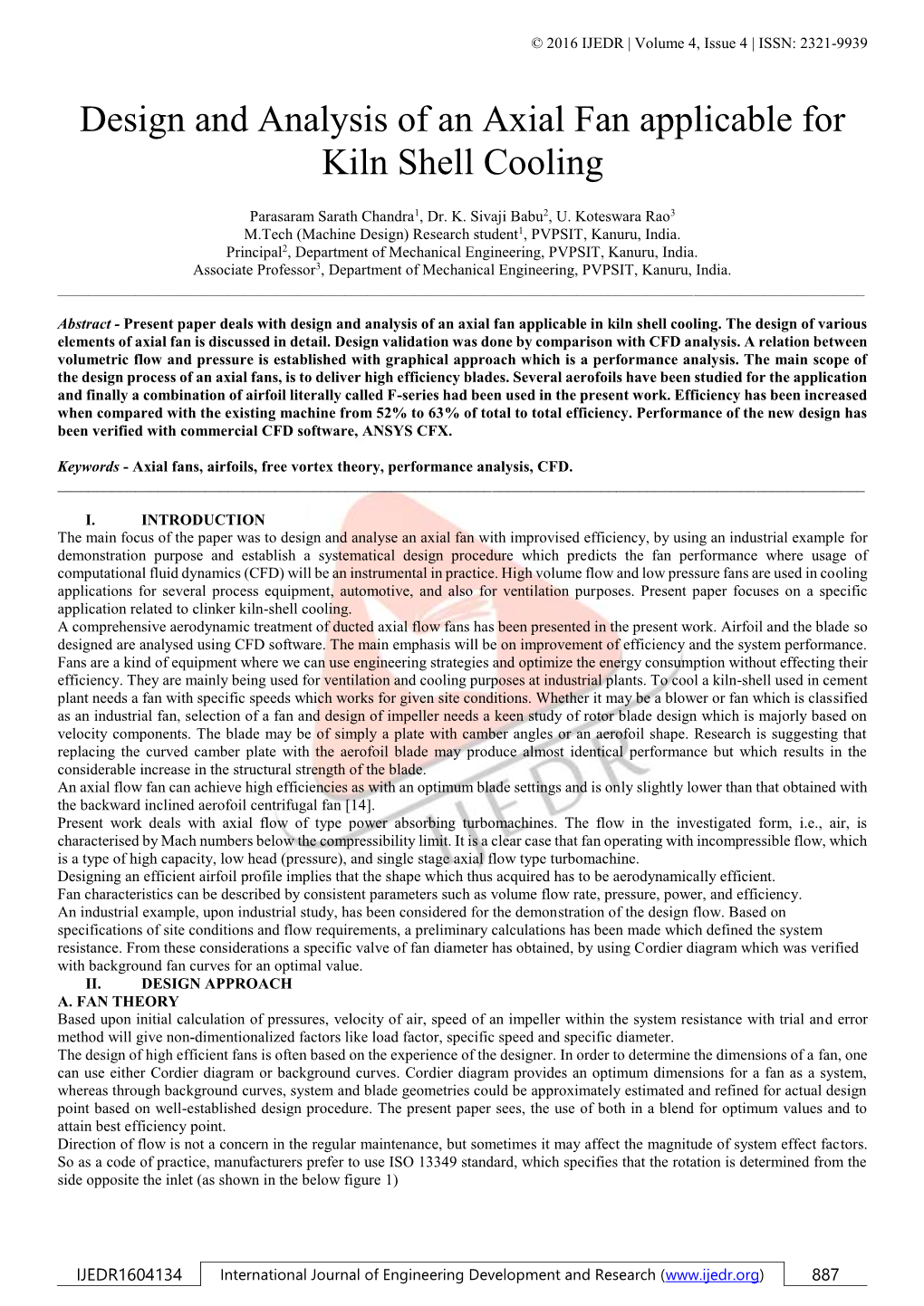
Load more
Recommended publications
-
Design, Construction and Performance Evaluation of Axial Flow Fans
DESIGN, CONSTRUCTION AND PERFORMANCE EVALUATION OF AXIAL FLOW FANS A THESIS SUBMITTED TO THE GRADUATE SCHOOL OF NATURAL AND APPLIED SCIENCES OF MIDDLE EAST TECHNICAL UNIVERSITY BY HAYRETTİN ÖZGÜR KEKLİKOĞLU IN PARTIAL FULFILLMENT OF THE REQUIREMENTS FOR THE DEGREE OF MASTER OF SCIENCE IN MECHANICAL ENGINEERING SEPTEMBER 2019 Approval of the thesis: DESIGN, CONSTRUCTION AND PERFORMANCE EVALUATION OF AXIAL FLOW FANS submitted by HAYRETTİN ÖZGÜR KEKLİKOĞLU in partial fulfillment of the requirements for the degree of Master of Science in Mechanical Engineering Department, Middle East Technical University by, Prof. Dr. Halil Kalıpçılar Dean, Graduate School of Natural and Applied Sciences Prof. Dr. M. A. Sahir Arıkan Head of Department, Mechanical Engineering Prof. Dr. Kahraman Albayrak Supervisor, Mechanical Engineering, METU Examining Committee Members: Assoc. Prof. Dr. Cüneyt Sert Mechanical Engineering. METU Prof. Dr. Kahraman Albayrak Mechanical Engineering, METU Assoc. Prof. Dr. Mehmet Metin Yavuz Mechanical Engineering, METU Assist. Prof. Dr. Özgür Uğraş Baran Mechanical Engineering, METU Assist. Prof. Dr. Ekin Özgirgin Yapıcı Mechanical Engineering, Çankaya University Date: 03.09.2019 I hereby declare that all information in this document has been obtained and presented in accordance with academic rules and ethical conduct. I also declare that, as required by these rules and conduct, I have fully cited and referenced all material and results that are not original to this work. Name, Surname: Hayrettin Özgür Keklikoğlu Signature: iv -
Axial Flow Fan Design
BASF Corporation BASIC GUIDELINES FOR PLASTIC CONVERSION OF METAL AXIAL FLOW FANS INTRODUCTION This guideline outlines in brief the basic steps recommended for the development of a plastic conversion of a metal fan. It is limited with respect to axial flow type fans, and does not necessarily address a single classification within that family. The field of fan design is quite extensive and complex, it is therefore impossible to address all aspects of axial fan design within the scope of this paper. It is suggested that these rules be utilized in general sense as a starting point in the development process especially when initial geometric data is lacking. It is also essential to integrate a testing program throughout the different development stages, to evaluate the performance of the various basic design changes and their impact on achieving the desired outcome. TABLE OF CONTENTS Topic Page 1.DEVELOPMENT GUIDELINES 1 - 14 2. PLASTICS IN MAJOR FAN APPLICATIONS 14 - 15 3. TECHNICAL SUPPORT FROM BASF CORPORATION 15 - 18 4. SUMMARY OF AN ACTUAL DEVELOPMENT PROGRAM 18 - 28 5. APPENDIX DOCUMENT STRUCTURE This document is structured around four main topics. The first one highlights basic rules that are recommended for developing baseline dimensions of axial flow in a metal to plastic conversion application. The second topic describes in summary the general methods used to optimize plastic fans. The third topic presents in brief BASF Corporationdesign support capabilities in this field, and finally the last topic goes over an actual fan development program at BASF facilities. 1 DEVELOPMENT GUIDELINES Axial Flow Fans Axial flow fans, while incapable of developing high pressures, they are well suitable for handling large volumes of air at relatively low pressures. -
Smith Diagram for Low Reynolds Number Axial Fan Rotors
Paper ID: ETC2017-069 Proceedings of 12th European Conference on Turbomachinery Fluid dynamics & Thermodynamics ETC12, April 3-7, 2017; Stockholm, Sweden SMITH DIAGRAM FOR LOW REYNOLDS NUMBER AXIAL FAN ROTORS R. Corralejo - P. Harley Dyson Ltd., Malmesbury, UK [email protected] ABSTRACT Compressor operation at low Reynolds numbers is commonly associated with a loss in- crease. A semi-analytical approach was used to investigate this region of the design spec- trum. To do this, an axial rotor with constant diameter endwalls was non-dimensionalised to understand the influence of different design parameters independently. Smith diagrams showing contours of efficiency on a plot of flow coefficient versus stage loading coefficient were produced at low and high Reynolds numbers. The results showed not only lower levels of efficiency at low Reynolds numbers but a much narrower high efficiency island, with losses rapidly increasing as the design moved away from the high efficiency region. Several points in the Smith diagram were selected, dimensionalised and simulated using CFD with and without a transition model. Good agreement between the CFD and the model was found, with discrepancies increasing towards low efficiency regions. Meanline correlations for the low Reynolds number regime were also provided. KEYWORDS: Axial fan, Reynolds number, Smith diagram, loss, deviation. NOMENCLATURE AR Aspect ratio (= h=c) ηT=T T/T isentropic efficiency (Eq. 18) c Chord ∆η Loss of efficiency CD Dissipation coefficient ρ Density Cd Discharge coefficient σ Solidity -
Axial Fan Design Using Multi-Element Airfoils to Minimize Noise
Axial Fan Design Using Multi-Element Airfoils to Minimize Noise Hurtado, Mark1 Virginia Tech 635 Prices Fork Road, 445 Goodwin Hall, Blacksburg, VA 24061 Burdisso, Ricardo2 Virginia Tech 635 Prices Fork Road, 445 Goodwin Hall, Blacksburg, VA 24061 ABSTRACT Axial fans are one of the most harmful sources of noise due to their close proximity to occupied areas and widespread use. The prolonged exposure to hazardous noise levels can lead to noise-induced hearing loss. Consequently, there is a critical need to reduce noise levels from ventilation fans. Since fan noise scales with the 4-6th power of the fan tip speed, minimizing the fan tip speed is an effective method to reduce fan noise. However, reducing the fan speed results in a decrease in aerodynamic performance. To this end, the present study uses multi-element airfoils to increase the aerodynamic characteristics of the fan blades to enable lower fan speeds and noise relative to fan blades with single element airfoils. Additionally, a control vortex design method has been implemented to increase the effectiveness of the blade outer sections, i.e. spanwise varying axial flow. The resulting blade geometry has been shown to reduce noise levels while maintaining the same volumetric flow rate. Keywords: Multi-element, Fan, Noise I-INCE Classification of Subject Number: 30 1. INTRODUCTION Axial ventilation fans are used extensively to control the temperature, humidity, and to remove and dilute contaminants from occupied areas. However, their close proximity to occupied areas and widespread use are a significant threat to the immediate and long term health and hearing. -
Fans & Blowers
FANS & BLOWERS "AC/DC/EC Cooling Fan & Blower Size: From Ø15mm to Ø280mm Flow: 0.3CFM to 1450CFM" Dynetics represents leading manufacturers with great technical expertise in cooling solutions with fans and blowers using a variety of technologies. Dynetics will help you to economically optimize your designs, to mass- produced products with an optimal price / performance ratio. For the units cooling and cross-flow fans, we have axial / radial fans and blowers from various suppliers such as Nidec Servo in the program. Many of our fans can be customized, e.g. with wire, plug, pulse generator, PWM connection for speed control, IP class protection, etc. For drive solutions we offer micro motors with gears, sensors, and motor control of eg. Nidec, Shinano Kenshi, Tsukasa, Mellor, NPM etc. Please visit our website: www.dynetics.eu In this issue 1. Selecting a fan or blower 2. What's new 2.1 Super silent multi-blade blower, 2.2 Low Noise and vibration: low cogging 2.3 Compact fans with more pressure 2.4 New AC / EC fans also available with IP65 protection 2.5 Nidec Servo's Gentle Typhoon 3. Blowers 4. Overview: Our range of blowers 5. Axial fans 5.1 Outlook More pressure and flow Small lightweight fans from Nidec Nidec Servo Axial AC and EC Fans 6. Overview: our range of axial fans 6.1 AC, EC, water resistant or fans with integrated bluetooth 7. Customising fans and blowers .1 Selecting a fan or blower Fan and blower selection The required airflow and ventilating resistance of equipment must be determined when selecting a fan or a blower. -
Computational Characterization of an Axial Rotor Fan
JOURNAL OF ENERGY SYSTEMS Volume 1, Issue 4 2602-2052 DOI: 10.30521/jes.346660 Research Article Computational characterization of an axial rotor fan Unai Fernandez-Gamiz University of the Basque Country (UPV/EHU), Faculty of Engineering of Vitoria-Gasteiz, Department of Nuclear Engineering and Fluid Mechanics, C/Nieves Cano 12, 01006, Vitoria-Gasteiz, Spain, [email protected], orcid.org/0000-0001-9194-2009 Mustafa Demirci Gazi University, Department of Energy Systems Engineering, Faculty of Technology, Ankara, Turkey, [email protected], orcid.org/0000-0002-7050-8323 Mustafa İlbaş Gazi University, Department of Energy Systems Engineering, Faculty of Technology, Ankara, Turkey, [email protected], orcid.org/0000-0001-6668-1484 Ekaitz Zulueta University of the Basque Country (UPV/EHU), Faculty of Engineering of Vitoria-Gasteiz, Department of Systems Engineering and Automatic Department, C/Nieves Cano 12, 01006, Vitoria-Gasteiz, Spain, [email protected], orcid.org/0000-0001-6062-9343 Jose Antonio Ramos University of the Basque Country (UPV/EHU), Faculty of Engineering of Vitoria-Gasteiz, Department of Electrical Engineering, C/Nieves Cano 12, 01006, Vitoria-Gasteiz, Spain, [email protected] ; orcid.org/0000-0001-9706-4016 Jose Manuel Lopez-Guede University of the Basque Country (UPV/EHU), Faculty of Engineering of Vitoria-Gasteiz, Department of Electrical Engineering, C/Nieves Cano 12, 01006, Vitoria-Gasteiz, Spain, [email protected], orcid.org/0000-0002-5310-1601 Erol Kurt Gazi University, Department of Electrical and Electronics Engineering, Faculty of Technology, Ankara, Turkey, [email protected], orcid.org/0000-0002-3615-6926 Arrived: 26.10.2017 Accepted: 28.12.2017 Published: 29.12.2017 Abstract: Axial flow fans are broadly applied in numerous industrial applications because of their simplicity, compactness and moderately low cost, such us propulsion machines and cooling systems. -
Metamodel Based Design Optimization in Industrial Turbomachinery
SAPIENZA UNIVERSITÀ DI ROMA DOCTORAL THESIS METAMODEL BASED DESIGN OPTIMIZATION IN INDUSTRIAL TURBOMACHINERY Author: Supervisor: Tommaso BONANNI Prof. Alessandro CORSINI A thesis submitted in fulfilment of the requirements for the degree of Doctor of Philosophy in Energy and Environment February 1, 2018 iii SAPIENZA UNIVERSITÀ DI ROMA Abstract Faculty Name Department of Astronautical, Electrical and Energy Engineering, XXX Cycle Doctor of Philosophy METAMODEL BASED DESIGN OPTIMIZATION IN INDUSTRIAL TURBOMACHINERY by Tommaso BONANNI Fans and Blowers community is experiencing, during those years, an incredible push in rethinking design approaches and strategies. The change in regulations on minimum ef- ficiency grades and market requirements on even more customized products demand a changing in the way design in fan technology is perceived. In this context, even if syn- thetic approaches for fan design and analysis are still valuable tools, they need to be flanked by metamodels in order to overcome the limitations and criticism introduced by empirical relationships developed in the past for specific applications. In addition, by replacing computation-intensive functions with approximate surrogate models, it is pos- sible to adopt advanced and nested optimization methods, such as those based on Evo- lutionary Algorithms, drastically improving the overall optimization computational time. Surrogate-based Optimizations based on Evolutionary Algorithm should become common practice in design optimization because of their capability of find optima in the design space, thanks to their intrinsic balance between exploitation and exploration. This work proposes methods for interweave elements of metamodeling techniques and multi-objective optimization problems with the synthetic approaches classically de- veloped by the turbomachinery community. The entire Thesis can be ideally divided into two parts; the first gives a brief survey on the classical fan design and analysis approaches and reports two synthetic in-house codes for axial fan performance prediction. -
Design of Axial Fan Using Inverse Design Method†
Journal of Mechanical Science and Technology Journal of Mechanical Science and Technology 22 (2008) 1883~1888 www.springerlink.com/content/1738-494x DOI 10.1007/s12206-008-0727-8 Design of axial fan using inverse design method† Kyoung-Yong Lee, Young-Seok Choi*, Young-Lyul Kim and Jae-Ho Yun Thermal and Fluid System Team, Korea Institute of Industrial Technology, 35-3 Hongcheon-ri, Ipjang-myeon, Cheonan-si, Korea (Manuscript Received April 16, 2008; Revised June 25, 2008; Accepted July 23, 2008) ------------------------------------------------------------------------------------------------------------------------------------------------------------------------------------------------------------------------------------------------------------------------------------ Abstract The axial fans for cooling condensers were designed by inverse design code TURBOdesign-1. The parameters of the inverse design were set by DOE (design of experiments). By changing the design parameters, such as the distribution of the blade loading, spanwise circulation distribution and stacking, 32 different fan designs were created for the screening of parameters. The overall performance and the local flow field of these fans were computed using a com- mercial CFD code. The results of the CFD computations were analyzed by DOE. The pressure rise and efficiency were selected as the main responses, and the main effects of the design parameters on the responses were discussed. The main design parameters for the optimum design of the fan were decided from the results of the screening procedure. We designed the optimum axial fan by RSM (response surface method). The design center fan was made by RP (rapid prototype) and the performance was tested using a fan tester based on AMCA standards. These procedures ensured proper screening of parameters and optimum design of the axial fan. -
Ing-Ind/09 3
From Design to Flow solutions In Industrial Fluid Machinery Team Research Assistant & PostDoc Giovanni Delibra, Paolo Venturini Ph.D. Candidates David Volponi, Alessio Castorrini Ph.D. students Tommaso Bonanni, Lorenzo Tieghi, Gino Angelini SSD: ING IND-09 Fluid Machinery R&D Environment Selection Smart environment is configured in order to give the user DESIGN the possibility to customize the experience selecting tools optimizing time and accuracy. VIRTUAL Configure TEST RIG Tool Chain B OPTIMIZATION C A D Duty Selection Design Verify Te s t CentrLab Fan Selector AxLab TM MixLab Design BigData Prototyping In Fluid ADM ALM Der. Design Machinery CFD & FSI BD Opt P-Track SSD: ING IND-09 Integrated tool for industrial design of turbomachinery blades DESIGN • Develepod in Python, based on an axisymmetric solution of DESIGN the indirect problem. • Designed to be Multi-Platform and Expandable. VIRTUAL • It allows to test innovative design solutions. TEST RIG • Save, Export, Share and Compare different Designs. OPTIMIZATION SSD: ING IND-09 VIRTUAL TEST RIG DESIGN The virtual test rig consists of different analysis tools: TM DESIGN • Reduced Order Solvers: AxLab, MixLab, CentrLab • Actuator Disk Model • Actuator Line Model VIRTUAL TEST RIG • Ljungstrom Heat Exchanger OPTIMIZATION MixLab AxLab CentrLab • Each tool is designed for performance analysis on different level; from a AADM quasi-3D steady state approach to transient problems. • Set of instruments for fan performance analysis in order to simplify fans performance prediction. ALM • Designed both for axial and centrifugal machinery SSD: ING IND-09 Reduced Order Solvers: AxLab – MixLab DESIGN MixLab TM DESIGN AxLab CentrLab VIRTUAL TEST RIG AxLab and MixLab software are python programs for performance analysis of ducted axial or mixed-flow fans. -
Impact of Different Aerodynamic Optimization Strategies on the Sound Emitted by Axial Fans
19th AIAA/CEAS Aeroacoustics Conference (34th AIAA Aeroacoustics Conference), 27 - 29 May 2013, Berlin Impact of Different Aerodynamic Optimization Strategies on the Sound Emitted by Axial Fans Konrad Bamberger1 and Thomas Carolus2 Institut für Fluid- und Thermodynamik, Universität Siegen, Paul-Bonatz-Str. 9-11, 57068 Siegen, Germany The correlation between the aerodynamic design strategy and the sound emission of low pressure axial fans is investigated by a case study. The four fans investigated are equal in terms of total-to-static design point, rotational speed, diameter, and tip clearance, but different regarding hub size and blade geometry. One fan (the baseline) is designed using the analytical blade element momentum method whereas the other fans are optimized by stationary CFD simulations embedded in an evolutionary optimization algorithm. Three different target functions are applied: Maximization of total-to-static and total-to-total efficiency at design point, and maximization of operating range. The distinction between the two efficiencies addresses two competing effects: While the fan optimized with respect to total-to-total efficiency has the lowest secondary flow effects, its aerodynamic load required to fulfill the same total-to-static pressure rise is higher. The characteristic curves of each fan are measured on a chamber test rig to validate the CFD results. The acoustic investigations are conducted in a semi-anechoic chamber. It is found that optimization with respect to total-to-total efficiency, i.e. minimization of losses, leads to the lowest sound power levels around the design point at low Mach numbers while the design optimized with respect to total-to-static efficiency is superior at high Mach numbers. -
MACHINERY Performance, Analvsis, J and Design
FLUID MACHINERY Performance, Analvsis, J and Design Terry Wright CRC Press Boca Raton London New York Washington, D.C. Library of Congress Cataloging-in-Publication Data Wright, Terry. 1938- Fluid machinery : performance, analysis, and design 1 Terry Wright. p. cm. Includes bibliographical references and index. ISBN 0-8493-2015-1 (alk. paper) "' 1. ~urbomachines.~'2. Fluid mechanics. I. Title. TJ267.W75 1999 62 1.406.-dc2 1 98-47436 CIP This book contains information obtained from authentic and highly regarded sources. Reprinted material is quoted with permission, and sources are indicated. A wide variety of references are listed. Reasonable efforts have been made to publish reliable data and information, but the author and the publisher cannot assume responsibility for the validity of all materials or for the consequences of their use. Neither this book nor any part may be reproduced or transmitted in any form or by any means, electronic or mechanical, including photocopying, microfilming, and recording, or by any information storage or retrieval system, without prior permission in writing from the publisher. The consent of CRC Press LLC does not extend to copying for general distribution, for promotion, for creating new works, or for resale. Specific permission must be obtained from CRC Press for such copying. Direct all inquiries to CRC Press LLC, 2000 N.W. Corporate Blvd., Boca Raton, Florida 3343 1. Trademark Notice: Product or corporate names may be trademarks or registered trademarks, and are used only for identification and explanation, without intent to infringe. ,/ O 1999 by CRC Press LLC No claim to original U.S. -
Aerodynamic and Aeroacoustic Behavior of Axial Fan Blade Sections at Low Reynolds Numbers
Aerodynamic and aeroacoustic behavior of axial fan blade sections at low Reynolds numbers Esztella Éva Balla Supervisor: János Vad, D.Sc. A thesis presented for the degree of Doctor of Philosophy Department of Fluid Mechanics Faculty of Mechanical Engineering Budapest University of Technology and Economics August 27, 2020 i Acknowledgement I am grateful to the Reviewers of this thesis for their hard work and valuable suggestions. Gratitude is expressed to Mr. Gábor Daku for conducting, and evaluating the hot-wire measurements, and also for processing the data of Schmitz, and applying the corrections established by Prandtl to the measurement results. I would like to thank the following colleagues giving assistance in the measurements, in alphabetical order of the family names: Mr. András Gulyás; Mr. Bálint Lőczi; Ms. Eszter Menyhért; Mr. József Tajti. Gratitude is expressed to Professor Alessandro Corsini for supervising my MSc thesis, and to Dr. Giovanni Delibra for his valuable advice on the thesis. My MSc thesis served as a basis for this dissertation. This work has been supported by the Hungarian National Research, Development and Innovation Centre under contract Nos. K 112277, 119943, and 129023. The research reported in this dissertation was supported by the Higher Education Excellence Program of the Ministry of Human Capacities in the frame of Water science & Disaster Prevention research area of Budapest University of Technology and Economics (BME FIKP-VÍZ) and by the National Research, Development and Innovation Fund (TUDFO/51757/2019-ITM, Thematic Excellence Program). Köszönetnyilvánítás Mindenek előtt a témavezetőmnek, Vad Jánosnak tartozok köszönettel, aki a munkához való hozzáállásával rendkívüli módon inspirált és motivált.