US5094991.Pdf
Total Page:16
File Type:pdf, Size:1020Kb
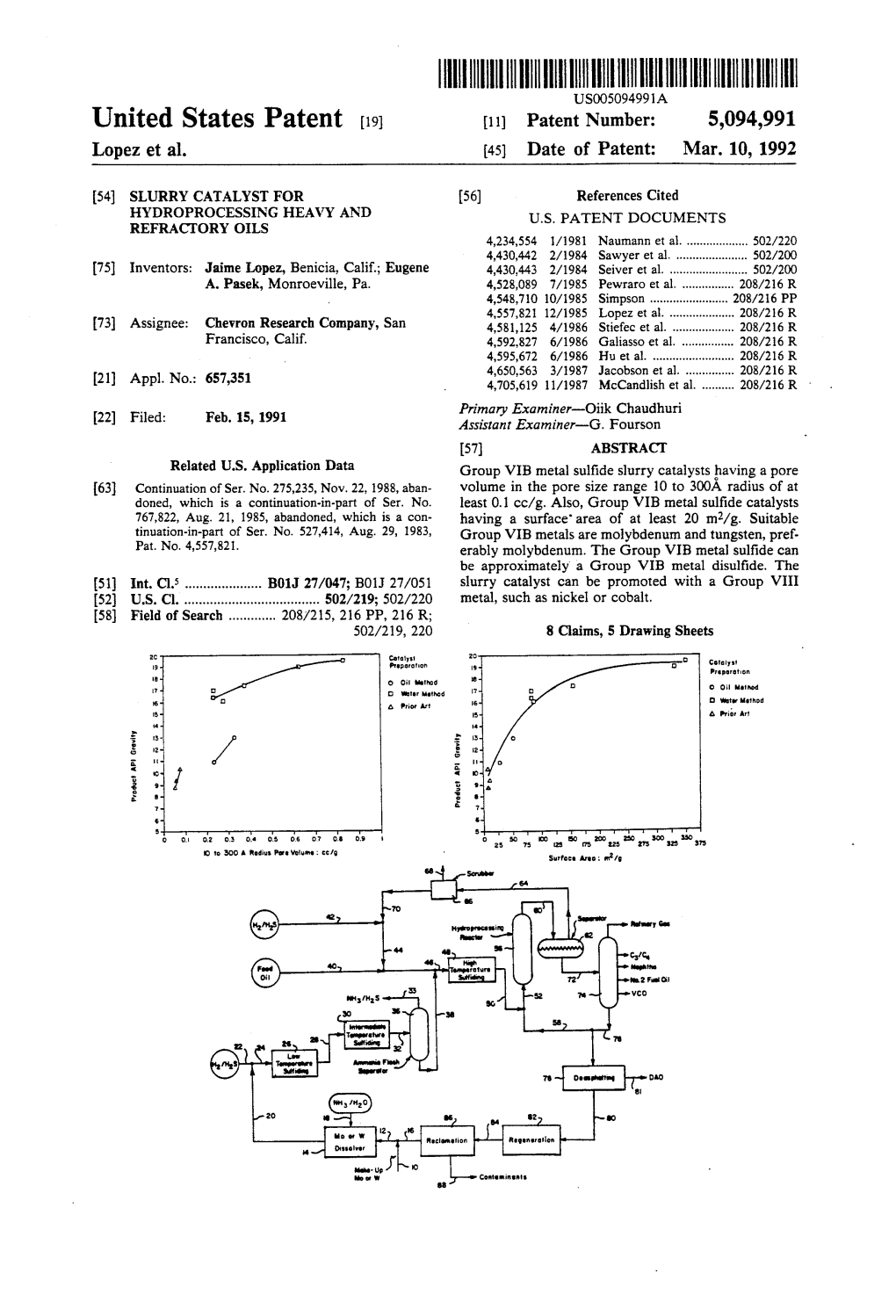
Load more
Recommended publications
-
Molybdates: an Alternative to Hexavalent Chromates in Corrosion
Molybdates: An Alternative to Hexavalent Chromates 3ytzt7n2 in Corrosion Prevention and Control qz ,+ B3 F Stiles C. Thompson Sverdrup Technology, Inc. 626 Anchors St. NW Fort Walton Beach, FL 32548 (904) 833-7600 Introduction Hexavalent chromates have been the preferred corrosion inhibitor in military systems for years. Chromate conversion coatings are specified in MIL-STD-808, “Finishes, Materials and Processes for Corrosion Prevention and Control in Support Equipment ”, for aluminum, magnesium, and plated steel. A number of primers are formulated with zinc or strontium chromate. Passivation treatments for stainless steels frequently specify chromic acid. Some anodic coatings specify baths containing chromic and sulfuric acid and a pcst treatment or rinse with aqueous sodium dichromate. Even water-based primers formulated for volatile organic I compound (VOC) compliance in such areas as southern California contain chromate-based corrosion inhibitors. Chromates are decreasing in industrial use, however, as concerns about their environmental risks and toxicity increase. One pollution prevention approach is to substitute analogs of chromates in similar applications. Molybdate is one such analog of lower toxicity. Federal Environmental Regulations A number of environmental regulations now control hexavalent chromate. Toxic Substances Control Act (TSCA). Under TSCA, the Environmental Protection Agency @PA) must be notified 90 days prior to manufacture. EPA may restrict or prohibit manufacture where there is unreasonable risk to the environment. EPA also has the authority to require testing for health or environmental effects. No current regulation specifies molybdate. Resource Conservation and Recovery Act (RCRA). RCRA regulates the treatment, storage, transportation, and disposal of hazardous waste (HW). The EPA HW number for hexavalent chromium is D007. -
A Titrimetric Determination of Thorium John J
Ames Laboratory ISC Technical Reports Ames Laboratory 6-1954 A titrimetric determination of thorium John J. Ford Iowa State College James S. Fritz Iowa State College Follow this and additional works at: http://lib.dr.iastate.edu/ameslab_iscreports Part of the Chemistry Commons Recommended Citation Ford, John J. and Fritz, James S., "A titrimetric determination of thorium" (1954). Ames Laboratory ISC Technical Reports. 92. http://lib.dr.iastate.edu/ameslab_iscreports/92 This Report is brought to you for free and open access by the Ames Laboratory at Iowa State University Digital Repository. It has been accepted for inclusion in Ames Laboratory ISC Technical Reports by an authorized administrator of Iowa State University Digital Repository. For more information, please contact [email protected]. A titrimetric determination of thorium Abstract A rapid, accurate method for thorium is proposed in which thorium is titrated with a standard solution of ethylenediaminetetraacetic acid (EDTA). Alizarin Red S serves as the indicator, a sharp change from pink to yellow marking the end point of the titration. The method is selective for thorium although several cations and anions interfere. A preliminary extraction of thorium nitrate by mentyl oxide provides an excellent separation of thorium from most interfering ions. Keywords Ames Laboratory Disciplines Chemistry This report is available at Iowa State University Digital Repository: http://lib.dr.iastate.edu/ameslab_iscreports/92 Physical 'cieuccs Re· dmg Room UNITED STATES ATOMIC ENERGY COMMISSION ISC-520 A TITRIMETRIC DETERMINATION OF THORIUM By John J. Ford James S. Fritz June 1954 Technical Information Service, Oak Ridge, Tennessee J Subject Category, CHEMISTRY. Work performed under Contract No. -
FALL2015.Pdf
Introducing… In Meso In Situ Serial Crystallography mitegen.com/imisx Easy Crystallizaon in LCP • Simple in situ X-ray Diffracon • Standard Goniometer Compable • Serial Crystallography Enabling • Advanced Dual-Sandwich Design Rethink what your LCP crystallizaon plate is capable of. EZ-Cut LCP LCP Tools Easy Access LCP Crystallizaon Plate Starter Kits, Syringes, Lipids & More Take your crystallizaon in LCP to the next level with MiTeGen’s new LCP line mitegen.com/lcp ACA - Structure Matters www.AmerCrystalAssn.org Table of Contents 2 President’s Column 2-4 News from Canada 4 From the Editor's Desk 5-6 Update on Structural Dynamics Chris Cahill 7 What's on the Cover ACA President 8-11 Poster Prizes in Philadelphia 12 Undergraduate Student Reception in Philadelphia Contributors to this Issue What's on the Cover 13-51 Philadelphia ACA Meeting Page 7 21 Index of Advertisers 53-54 2015 ACA Summer Course 56 What's New on the ACA History Website Spotlight on Stamps Juanma García-Ruiz Net RefleXions 15 Plenary Lecturer in Philadelphia 58-59 Puzzle Corner 59 YSSIG Activities 60-61 48th Erice International School of Crystallography 61-62 Updates from 2014-2015 AIP Science & Technology Fellows 62 CSD50 Symposium Daniel Rabinovich 64-65 News & Awards Spotlight on Stamps 65-66 Book Reviews 66-67 2015 Wisconsin Crystal-Growing Competition 68 Net RefleXions 69 CCDC Data Deposition Service Enhancement 70-71 ACA 2016 Denver Preview 72 Future Meetings Anastasiya Vinokur Net RefleXions Contributions to ACA RefleXions may be sent to either of the Editors: Please address matters pertaining to advertisements, membership Judith L. -
Tungsten Removal from Molybdate Solutions Using Chelating Ion-Exchange Resin: Equilibrium Adsorption Isotherm and Kinetics
J. Cent. South Univ. (2016) 23: 1052−1057 DOI: 10.1007/s11771-016-0354-y Tungsten removal from molybdate solutions using chelating ion-exchange resin: Equilibrium adsorption isotherm and kinetics ZHU Xian-zheng(朱先正), HUO Guang-sheng(霍广生), NI Jie(倪捷), SONG Qiong(宋琼) School of Metallurgy and Environment, Central South University, Changsha 410083, China © Central South University Press and Springer-Verlag Berlin Heidelberg 2016 Abstract: The equilibrium adsorption isotherm and kinetic of the sorption process for W and Mo on macro chelating resin D403 were investigated on single Na2MoO4 and Na2WO4 solutions. The sorption isotherm results show that the adsorption process of W obeys the Freundlich model very well whereas the exchange process with Mo approximately follows the Henry model. The kinetic experiments show that the intraparticle diffusion process was the rate-determining step for W sorption on the resin, and the corresponding activation energy is calculated to be 21.976 kJ/mol. Key words: tungsten; molybdate; ion-exchange resin; isotherms; kinetics tin (IV) oxide hydrate [14], that would preferentially 1 Introduction form precipitations with W under certain conditions. The separation was effective but a large number of The separation between W and Mo has been a precipitation agents were required and the impurity ions national difficulty due to their extremely similar accompanied with the added reagents were inevitable, physicochemical properties, resulting from the increasing the impurity-removal burden. lanthanide contraction [1]. Additionally, according to the Inspired by the different affinities towards O industrial requirement, WO3 impurity in final ammonium between W and Mo, we discovered a novel resin (D403) molybdate product should be restricted to below containing meglumine group which exhibited marvelous 150×10−6 (mass fraction) [2], making W removal from separation effects between Mo and W at pH above 8.0, at molybdate solutions particularly important. -
A High-Affinity Molybdate Transporter in Eukaryotes
A high-affinity molybdate transporter in eukaryotes Manuel Tejada-Jime´ nez, Angel´ Llamas, Emanuel Sanz-Luque, Aurora Galva´ n, and Emilio Ferna´ ndez* Departamento de Bioquı´micay Biologı´aMolecular, Facultad de Ciencias, Universidad de Co´rdoba, Campus de Rabanales, Edif. Severo Ochoa, 14071 Co´rdoba, Spain Edited by Bob B. Buchanan, University of California, Berkeley, CA, and approved October 29, 2007 (received for review May 17, 2007) Molybdenum is an essential element for almost all living beings, In contrast to bacteria, molybdate transporters in eukaryotes which, in the form of a molybdopterin-cofactor, participates in the are unknown, and genes similar to the bacterial molybdate active site of enzymes involved in key reactions of carbon, nitrogen, channel modB have not been found in sequenced eukaryotic and sulfur metabolism. This metal is taken up by cells in form of the genomes. Physiological data from the green alga Chlamydomo- oxyanion molybdate. Bacteria acquire molybdate by an ATP-binding- nas reinhardtii suggest the presence of at least two molybdate cassette (ABC) transport system in a widely studied process, but how transport systems that are related to the unlinked genetic loci Ni5 eukaryotic cells take up molybdenum is unknown because molybdate and Nit6 (10). Mutants defective at one of these loci are transporters have not been identified so far. Here, we report a phenotypically wild type but have a reduced molybdate transport eukaryotic high-affinity molybdate transporter, encoded by the activity; double mutants at both loci lack Moco and, thus, activity green alga Chlamydomonas reinhardtii gene MoT1. An antisense RNA of the molybdoenzyme nitrate reductase (11). -
Toxicity of Sodium Molybdate and Sodium Dichromate to Daphnia Magna Straus Evaluated in Acute, Chronic, and Acetylcholinesterase Inhibition Tests Teresa C
Ecotoxicology and Environmental Safety 45, 253}259 (2000) Environmental Research, Section B doi:10.1006/eesa.1999.1889, available online at http://www.idealibrary.com on Toxicity of Sodium Molybdate and Sodium Dichromate to Daphnia magna Straus Evaluated in Acute, Chronic, and Acetylcholinesterase Inhibition Tests Teresa C. Diamantino,*,-,1 Lucia Guilhermino,? Elisabete Almeida,- and Amadeu M. V. M. Soares* *Instituto do Ambiente e Vida, Departamento de Zoologia, Largo Marque' s de Pombal, Universidade de Coimbra, 3000 Coimbra, Portugal; -Instituto Nacional de Engenharia e Tecnologia Industrial, Estrada do Pac,o do Lumiar, 1699 Lisboa Codex, Portugal; and ?Instituto de Cie' ncias BimeH dicas de Abel Salazar, Departamento de Estudos de Populac,oJ es, LaboratoH rio de Ecotoxicologia/Centro de Investigac,a8 o Marinha e Ambiental, Universidade do Porto, Lg Prof. Abel Salazar, 2, 4050 Porto, Portugal Received March 18, 1999 spread application in numerous industrial processes, chro- As a result of a widespread application in numerous industrial mium is a contaminant of many environmental systems processes, chromium is a contaminant of many environmental systems. Chromium and their compounds are toxic to both (Cohen et al., 1993). Industrial uses of chromium include invertebrates and vertebrates and, for this reason, there has been metal "nishing industry, production of paints and pigments, a search for suitable and less toxic alternatives. Molybdenum tanning, wood preservation, chromium chemicals produc- compounds have been studied as alternative to chromium tion, pulp and paper production, and metal smelting (Paw- compounds for some industrial applications. The toxicity of lisz et al., 1997). One of the major uses of environmentally chromium is well known but the e4ects of molybdenum and hazardous chemicals is in the metal "nishing industry. -
Removal of Hazardous Oxyanions from the Environment Using Metal-Oxide-Based Materials
materials Review Removal of Hazardous Oxyanions from the Environment Using Metal-Oxide-Based Materials Ewelina Weidner and Filip Ciesielczyk * Institute of Chemical Technology and Engineering, Faculty of Chemical Technology, Poznan University of Technology, Berdychowo 4, PL-60965 Poznan, Poland; [email protected] * Correspondence: fi[email protected]; Tel.: +48-61-6653626 Received: 11 February 2019; Accepted: 14 March 2019; Published: 20 March 2019 Abstract: Scientific development has increased the awareness of water pollutant forms and has reawakened the need for its effective purification. Oxyanions are created by a variety of redox-sensitive metals and metalloids. These species are harmful to living matter due to their toxicity, nondegradibility, and mobility in aquatic environments. Among a variety of water treatment techniques, adsorption is one of the simplest, cheapest, and most effective. Since metal-oxide-based adsorbents poses a variety of functional groups onto their surface, they were widely applied in ions sorption. In this paper adsorption of harmful oxyanions by metal oxide-based materials according to literature survey was studied. Characteristic of oxyanions originating from As, V, B, W and Mo, their probable adsorption mechanisms and comparison of their sorption affinity for metal-oxide-based materials such as iron oxides, aluminum oxides, titanium dioxide, manganium dioxide, and various oxide minerals and their combinations are presented in this paper. Keywords: oxyanions; sorption; metal oxides; environment pollution; water purification; adsorbents; hazardous metals 1. Introduction Intensive industrial development has contributed to the increased pollution of the environment with hazardous metals and metalloids. The majority of these elements are redox sensitive and some of their oxidation states can form oxyanions in solution. -
Molybdenum, Ferromolybdenum, and Ammonium Molybdate, Phosphoric
MOLYBDENUM, FERROMOLYBDENUM, AND AMMONIUM MOLYBDATE A. Commodity Summary Almost all molybdenum is recovered from low-grade deposits of the mineral molybdenite, naturally occurring molybdenum disulfide (MoS2), mined either from a primary deposit, or as a byproduct of copper processing.1 In 1993, one mine extracted molybdenum ore, and nine mines recovered molybdenum as a byproduct. Two plants converted molybdenite concentrate to molybdic oxide, which was used to produced ferromolybdenum, metal powder, and other molybdenum compounds.2 Exhibit 1 presents the names and locations of molybdenum mines and processing facilities. EXHIBIT 1 SUMMARY OF MOLYBDENUM, MOLYBDIC OXIDE, AND FERROMOLYBDENUM PRODUCERSa Facility Name Location Cyprus-Climax - Henderson Empire, CO Cyprus-Climax Fort Madison, IA Cyprus-Climax Clear Water, MI Cyprus-Climax - Green Valley Tucson, AZ Cyprus-Climax Baghdad, AZ Kennecott Bingham Canyon, UT Molycorp Inc. Washington, PA Montana Resources Inc. Butte, MT Phelps Dodge Chino, NM San Manuel San Manuel, AZ San Manuel Morenci, AZ Thompson Creek Chalis, ID Thompson Creek Langeloth, PA a - Personal Communication between ICF Incorporated and John W. Blossom, U.S. Bureau of Mines, October 1994. Molybdenum metal is a refractory metal used as an alloying agent in steels, cast irons, and superalloys.3 Ferromolybdenum is an alloy of iron and molybdenum used primarily as an alternative additive in producing alloy steels, cast irons, and nonferrous alloys. The two most common grades of ferromolybdenum are low carbon- and high carbon ferromolybdenum. Ammonium molybdate is an intermediate in manufacturing both molybdenum metal and molybdic oxide, although it can also be sold as a product. Purified MoS2 concentrate also is used as a lubricant. -
Structure of the Molybdate/Tungstate Binding Protein Mop from Sporomusa Ovata
View metadata, citation and similar papers at core.ac.uk brought to you by CORE provided by Elsevier - Publisher Connector Structure, Vol. 8, 1127±1136, November, 2000, 2000 Elsevier Science Ltd. All rights reserved. PII S0969-2126(00)00525-6 Structure of the Molybdate/Tungstate Binding Protein Mop from Sporomusa ovata Ulrike G. Wagner,*³ Erhard Stupperich,² sten occur in the environment (typically at low submicromolar ³ 2Ϫ and Christoph Kratky* concentrations) as the soluble oxyanions molybdate (MoO4 ) 2Ϫ *Institut fuÈ r Chemie and tungstate (WO4 ), which have similar sizes, shapes, and Strukturbiologie H bonding properties to those of sulfate, phosphate, and van- Karl-Franzens-UniversitaÈ t adate. A-8010 Graz Bacteria have a high-affinity molybdenum uptake system Austria belonging to the ABC superfamily of transporters [4, 5]. Compo- ² Abteilung Angewandte Mikrobiologie nents of this system include a periplasmic binding protein UniversitaÈ t Ulm (ModA), an integral membrane protein (ModB), and an energizer D-89081 Ulm protein (ModC). The ModA, ModB, and ModC proteins from Germany various organisms (e.g., Escherichia coli, Haemophilus influen- zae, Azotobacter vinelandii, and Rhodobacter capsulatus) are very similar [5]. Molybdate transport is tightly coupled to utiliza- Summary tion in E. coli and Klebsiella pneumoniae, while other organisms appear to have a molybdenum storage protein. In all organisms Background: Transport of molybdenum into bacteria involves studied so far, molybdate transport genes are regulated by a a high-affinity ABC transporter system whose expression is repressor protein, ModE [5]. controlled by a repressor protein called ModE. While molyb- Earlier studies on the accumulation of molybdenum in cells date transport is tightly coupled to utilization in some bacteria, of Clostridium pasteurianum demonstrated that after entry into other organisms have molybdenum storage proteins. -
Oxidative Dehydrogenation of Propane with Cobalt, Tungsten and Molybdenum Based Materials
Revista Facultad de Ingeniería, Universidad de Antioquia, No. 84, pp. 97-104, 2017 Oxidative dehydrogenation of propane with cobalt, tungsten and molybdenum based materials Deshidrogenación oxidativa de propano con materiales a base de cobalto, tungsteno y molibdeno Maurin Salamanca-Guzmán1, 2*, Yordy Enrique Licea-Fonseca3, Adriana Echavarría-Isaza1, Arnaldo Faro4, Luz Amparo Palacio-Santos5 1 Grupo Catalizadores y Adsorbentes, Instituto de Química, Universidad de Antioquia. Calle 67 # 53-108. A. A. 1226. Medellín, Colombia. 2 Department of Chemistry, Bielefeld University. Universitätsstraße 25, D-33501. Bielefeld, Germany. 3 CENANO-DCAP, Instituto Nacional de Tecnologia. Av. Venezuela 82. CEP 20081-312. Rio de Janeiro, Brasil 4 Departamento de Físico-Química, Instituto de Química, Universidade Federal do Rio de Janeiro. Av. Athos da Silveira Ramos, 149. CEP 21941-909. Río de Janeiro, Brasil. 5 Departamento de Operações e Processos Industriais, Instituto de Química, Universidade do Estado do Rio de Janeiro. Rua São Francisco Xavier, 524. CEP 20550-900. Río de Janeiro, Brasil. ARTICLE INFO ABSTRACT: Oxidative dehydrogenation of propane is a reliable alternative for olefins Received January 20, 2017 production. This paper presents the results obtained on oxidative dehydrogenation of propane Accepted August 09, 2017 by using two materials based on cobalt, tungsten, and molybdenum. The materials were characterized by X-ray diffraction (XRD), Fourier transform infrared spectroscopy (FTIR), temperature programmed reduction (TPR), thermogravimetric analysis (TGA), and differential thermal analysis (DTA). The CoMo y material was calcined at 623 K, transforming itself to β-CoMoO4 phase (CoMo 623), the same phase is observed when the material is calcined at 873 K (CoMo y873). -
UC Berkeley UC Berkeley Previously Published Works
UC Berkeley UC Berkeley Previously Published Works Title Identifying the Unique Properties of α-Bi2Mo3O12 for the Activation of Propene Permalink https://escholarship.org/uc/item/3z33q49j Journal Journal of Physical Chemistry C, 120(51) ISSN 1932-7447 Authors Licht, RB Getsoian, A Bell, AT Publication Date 2016-12-29 DOI 10.1021/acs.jpcc.6b09949 Peer reviewed eScholarship.org Powered by the California Digital Library University of California Identifying the Unique Properties of α-Bi2Mo3O12 for the Activation of Propene Rachel B. Licht, Andrew “Bean” Getsoian, and Alexis T. Bell* Department of Chemical and Biomolecular Engineering University of California Berkeley, CA 94720-1462 and Chemical Sciences Division Lawrence Berkeley National Laboratory Berkeley, CA 94720 1 Abstract In order to understand the remarkable activity of -Bi2Mo3O12 for selective oxidation and ammoxidation of propene, the propene activation abilityα of four molybdenum-based mixed metal oxides – Bi2Mo3O12, PbMoO4, Bi2Pb5Mo8O32, and MoO3 – was investigated using Density Functional Theory. Propene activation is considered to occur via abstraction of a hydrogen atom from the methyl group of physisorbed propene by lattice oxygen. For each material, the apparent activation energy was estimated by summing the heat of adsorption of propene, the C-H bond dissociation energy, and the hydrogen attachment energy (HAE) for hydrogen addition to lattice oxygen; this sum provides a lower bound for the apparent activation energy. It was found that two structural features of oxide surfaces are essential to achieve low activation barriers: under-coordinated surface cation sites enable strong propene adsorption, and suitable 5- or 6-coordinate geometry at molybdenum result in favorable HAEs. -
The Crystal Chemistry of Novel Thorium and Uranium Compounds with Oxo-Anions from Group VI of Periodic Table (S, Se, Te, Cr, Mo and W)
The Crystal Chemistry of Novel Thorium and Uranium Compounds with Oxo-Anions from Group VI of Periodic Table (S, Se, Te, Cr, Mo and W) Von der Fakultät für Georessourcen und Materialtechnik der Rheinisch -Westfälischen Technischen Hochschule Aachen Zur Erlangung des akademischen Grades eines Doktors der Naturwissenschaften genehmigte Dissertation Vorgelegt von Magister für Technik und Technologie Bin Xiao aus Sichuan, China Berichter: Prof. Dr. rer.nat. Evgeny V. Alekseev Univ.-Prof. Dr. rer. nat. Georg Roth Univ.-Prof. Dr. rer. nat. Dirk Bosbach Tag der mündlichen Prüfung: 26. Januar 2016 Diese Dissertation ist auf den Internetseiten der Hochschulbibliothek online verfügbar Abstract This dissertation focus on the synthesis, phase studies and physicochemical properties of novel thori- um and uranium compounds with the Group VI (S, Se, Te, Cr, Mo, W) of the Periodic Table. All the studied compounds are listed in Table 2.2 from the page 15. I subdivided all the newly synthesized compounds into several chapters according to their structural and topological differences. First, for thorium molybdates and tungstates, almost all of these compounds are based on corner- sharing of ThOx (x = 6, 8 and 9) and MoO4 or WOx (x = 4, 5, 6) polyhedra. Interestingly, all these compounds can be seen as derived from a pure thorium molybdate compound (ThMo2O8) which was isolated from high-temperature solid-state synthesis method. Therefore, the polymorphs of this most basic ThMo2O8 compound is firstly introduced (see Chapter 3.1 from page 18). The thermodynamic, electronic and vibrational properties of all investigated ThMo2O8 polymorphs were studied using ab initio calculations. Then, two subfamilies of thorium molybdates, that is, rubidium thorium molybdate and cesium thori- um molybdate and their thermal and vibrational behaviors were discussed in details in Chapter 4.1 from page 37 and Chapter 4.2 from page 50, respectively.